一种改进的内排屑深孔钻头
BTA深孔钻结构及加工原理要点

BTA深孔钻的结构特点及加工原理要点bta深孔钻是内排屑深孔钻的一种典型结构,它是在单刃内排屑深孔钻的基础上改进而成,其切削刃呈双面错齿状,切屑从双面切下,并经双面排屑孔进入钻杆排出孔外。
bta深孔钻切削力分布均匀,分屑、断屑性能好,钻削平稳可靠,钻削出的深孔直线性好。
1、BTA深孔钻的结构特点BTA深孔钻具有以下结构特点:(1)刀体上分布有外刃刀片、中刃刀片、内刃刀片、导向块和双面排屑孔,并通过刀体上的浅牙多头矩形螺纹与空心钻杆联接。
(2)钻芯部分由内刀刃代替了麻花钻的横刃,从而克服了麻花钻横刃较长、轴向阻力较大的缺点;由于钻芯相对于钻孔轴心线偏移了一段距离,加工时钻芯处刀刃低于中心处刀刃,因此会形成一个导向芯柱,使钻头具有较好的导向性,钻孔时不易偏斜,该导向芯柱增长到一定长度后会自行折断并随切屑一起排出。
(3)主刀刃采用非对称的分段、交错排列形式,可保证分屑可靠,并避免用整体硬质合金刀片磨削卷屑槽、分屑槽时易产生裂纹的情况。
(4)刀片材料可采用几种不同牌号的硬质合金,以适应各部分结构对耐磨性和强度的不同要求,如钻芯部分切削速度低、切削力大,在切屑挤压作用下易发生崩刃,可选用韧性较好的硬质合金刀片;钻头外缘部分则可选用耐磨性较好的硬质合金刀片。
2、BTA深孔钻的加工原理BTA深孔钻在普通车床上的工作情况:被加工工件由车床大拖板上的v形铁定位并用螺栓压板夹紧。
钻孔加工时,钻杆由主轴内的专用夹头夹紧并在主轴带动下旋转,工件则由大拖板带动作进给运动。
机床工作台上安装了进液器,并通过o形密封圈与工件左端面密封连接。
加压切削液由进液器的进液口注入,经过钻杆外径与孔壁间的缝隙流入切削区,对进行冷却,切屑随同切削液一起由钻杆内孔通过专用夹头的出液口从排液箱排出。
切削液可采用浓度5%的乳化液;切削用量可选用:v=60~90m/min,s=0.035~0.23mm/r。
由于钻杆细长,容易变形,因此在机床导轨上安装了活动中心支承,可对钻杆的任意位置进行支承。
深孔加工技术改进

2. 活塞杆的深孔加工
( 1 )加工零件特点 图 1 所示零件为某型天
是又连续换了一只高速钢钻头,又导致切削部位过 热烧蚀、退火。此时,已钻到800mm深处,就再也 无法进行下去了。 该工件完工日期迫在眉睫,即使花上几千元联 系外协加工,也没有哪个单位愿意承接。我们冷静 下来查找原因,现场分析,提出以下导致钻头损坏 的原因: 一是内排屑油压过小,钻杆排屑孔小且不圆,
T工 艺
echnique
栏目主持 赵宇龙
深孔加工技术改进
中国船舶重工集团公司第722研究所 (湖北武汉 430079) 杨德群 徐家品
孔的加工是机械加工中最常见的加工形式。当 长径之比大于 5 时,则为深孔加工。随着机械工业 的迅速发展、新型材料的出现、加工精度要求越来 越高,孔加工难度越来越大,深孔加工往往成为 “卡脖子”工序。因而充分了解和认识深孔加工的 原理及特点,对提高深孔加工的效率,保证产品质 量都是十件采用 45 钢 实体棒料经调质处理至硬度 220 ~ 255H B W 后制作 而成。加工前的毛坯尺寸为 150mm × 3 010mm , 要求在毛坯上加工一深盲孔,孔径为 65m m 、深 2 800mm,长径之比达43倍。 (2)原始工艺装备:最初 所采用的工艺装备:一是 55mm 钻 杆 , 其 内 孔 为 2 8 m m ; 二 是
64.95m m ,小于所钻出的孔径尺寸,硬质合
金导向起不到支承导向的作用,其间隙过大, 钻杆颤动,钻头的硬质合金撞击工件内壁,导 致硬质合金头崩刃或撞掉。
3. 加工改进措施
( 1 )工艺装备改进:在对已加工的孔进行了 认真的测量后,证明已钻的 800m m 深的孔及其孔 径大小不一,都偏大,最小为 65.20m m ,最大为
深孔加工技术知识点
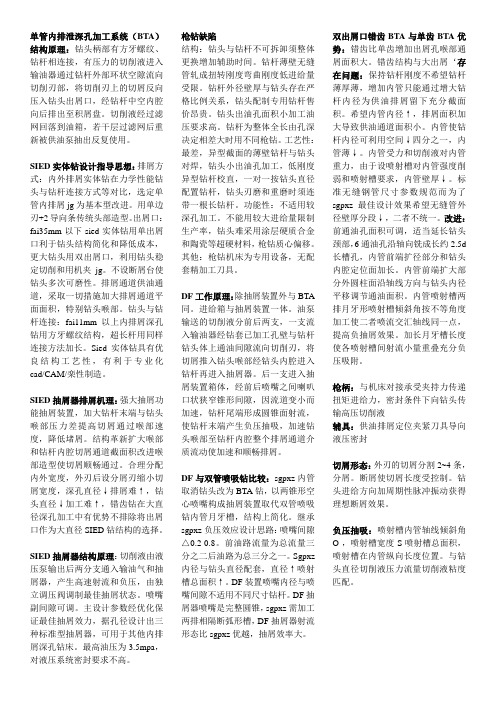
单管内排泄深孔加工系统(BTA)结构原理:钻头柄部有方牙螺纹、钻杆相连接,有压力的切削液进入输油器通过钻杆外部环状空隙流向切削刃部,将切削刃上的切屑反向压入钻头出屑口,经钻杆中空内腔向后排出至积屑盘。
切削液经过滤网回落到油箱,若干层过滤网后重新被供油泵抽出反复使用。
SIED实体钻设计指导思想:排屑方式:内外排屑实体钻在力学性能钻头与钻杆连接方式等对比,选定单管内排屑jg为基本型改进。
用单边刃+2导向条传统头部造型。
出屑口:fai35mm以下sied实体钻用单出屑口利于钻头结构简化和降低成本,更大钻头用双出屑口,利用钻头稳定切削和用机夹jg。
不设断屑台使钻头多次可磨性。
排屑通道供油通道,采取一切措施加大排屑通道平面面积,特别钻头喉部。
钻头与钻杆连接:fai11mm以上内排屑深孔钻用方牙螺纹结构,超长杆用同样连接方法加长。
Sied实体钻具有优良结构工艺性,有利于专业化cad/CAM/栾性制造。
SIED抽屑器排屑机理:强大抽屑功能抽屑装置,加大钻杆末端与钻头喉部压力差提高切屑通过喉部速度,降低堵屑。
结构革新扩大喉部和钻杆内腔切屑通道截面积改进喉部造型使切屑顺畅通过。
合理分配内外宽度,外刃后设分屑刃缩小切屑宽度,深孔直径↓排屑难↑,钻头直径↓加工难↑,错齿钻在大直径深孔加工中有优势不排除将出屑口作为大直径SIED钻结构的选择。
SIED抽屑器结构原理:切削液由液压泵输出后两分支通入输油气和抽屑器,产生高速射流和负压,由独立调压阀调制最佳抽屑状态。
喷嘴副间隙可调。
主设计参数经优化保证最佳抽屑效力,据孔径设计出三种标准型抽屑器,可用于其他内排屑深孔钻床。
最高油压为3.5mpa,对液压系统密封要求不高。
枪钻缺陷结构:钻头与钻杆不可拆卸须整体更换增加辅助时间。
钻杆薄壁无缝管轧成扭转刚度弯曲刚度低进给量受限。
钻杆外径壁厚与钻头存在严格比例关系,钻头配制专用钻杆售价昂贵。
钻头出油孔面积小加工油压要求高。
钻杆为整体全长由孔深决定相差大时用不同枪钻。
BTA内排屑深孔钻断屑机理及槽型设计

BTA内排屑深孔钻断屑机理及槽型设计
汽轮机低压加热器管板是核电设备的重要组成部分,加热器管板上的深孔加工难度较高。
BTA(Boring and Trepanning Association)内排屑深孔钻因生产效率高、加工质量好被广泛的应用于低压加热器管板的深孔加工,但由于被加工材料的韧性高,断屑和排屑较难,针对上述问题,本文提出了一种以车代钻的试验方法,主要从深孔钻钻削模型、各个切削刃不同角度下对切削力和断屑的影响规律等方面展开研究。
首先,针对BTA深孔钻封闭的使用环境,建立以车代钻的试验模型:不改变外刃、中间刃和中心刃的尺寸和角度,并保证各刃相对于深孔钻的位置不变,通过在工件端面进行切削加工,来模拟各个切削刃的加工过程。
其次,以钻削力为研究对象:通过对深孔钻外刃、中间刃和中心刃分别设计角度正交实验,分析了各切削刃的不同角度对切削力的影响规律,利用极差分析以切削力为研究对象,得到了各个切削刃的最佳角度组合。
再次,以断屑效果为研究对象:切屑的卷曲半径是切屑弯曲的重要指标,分析了各个切削刃的切屑形态,通过极差分析分析了各切削刃的不同刃倾角、后角和偏角对切屑的卷曲半径影响规律,发现各角度的变化对中心刃切屑的卷曲半径影响有限。
最后,针对深孔钻中心刃断屑难的问题,利用有限元仿真,建立了中心刃钻削模型,分析了不同槽宽(2n参数下的切削力、切削热和切屑的形态,得到了中心刃最佳的(2n参数对断屑的影响规律。
单位内部认证车工3级考试(试卷编号171)

单位内部认证车工3级考试(试卷编号171)1.[单选题]圆弧指令中的K表示( )。
A)圆心坐标在X轴上的分量B)圆心坐标在Y轴上的分量C)圆心坐标在Z轴上的分量答案:C解析:2.[单选题]选择定位基准时,粗基准可以使用( )。
A)一次B)二次C)多次答案:A解析:3.[单选题]数控机床开机时,一般要进行回参考点操作,其目的是( )。
A)建立机床坐标系B)建立工件坐标系C)建立局部坐标系答案:A解析:4.[单选题]在表面粗糙度的评定参数中,属于轮廓算术平均偏差的是( )。
A)RaB)RzC)Ry答案:A解析:5.[单选题]几何形状误差包括宏观几何形状误差,微观几何形状误差和( )。
A)表面波度B)表面粗糙度C)表面不平度答案:A解析:6.[单选题]车削中缩短基本时间是提高劳动生产率很重要的一个方面,下面方法中正确的是( )。
A)缩短工件装夹时间D)减少回转刀架及装夹车刀时间答案:C解析:7.[单选题]数控机床( )时,要使用解除模式。
A)自动状态B)手动数据输入C)回零D)X、Z超程答案:D解析:8.[单选题]用硬质合金车刀精车时,为了提高工件表面光洁程度,应尽量提高( )。
A)进给量B)切削厚度C)切削速度D)切深度答案:C解析:9.[单选题]以下选项中错误的是( )。
A)平面加工,工序余量为双边余量B)毛坯尺寸公差按双向对称偏差形式标注C)“入体原则”规定被包容尺寸最大加工尺寸为基本尺寸D)对于包容表面的工序余量等于本工序尺寸减去前工序尺寸答案:A解析:10.[单选题]复位键作用是除去一个程序,但不是在计算机中清除一个程序,缩写( )。
A)DELB)RESC)DGND)ALM答案:B解析:11.[单选题]国家鼓励制定( )国家标准或者行业标准的企业标准,在企业内部适用。
A)严于B)松于C)等同于解析:12.[单选题]CNC系统一般可用几种方式得到工件加工程序,其中MDI是( )。
A)利用磁盘机读入程序B)从串行通信接口接收程序C)利用键盘以手动方式输入程序D)从网络通过Modem接收程序答案:C解析:13.[单选题]镗削不通孔时,镗刀的主偏角应取( )。
麻花钻钻孔中常见问题的原因和解决办法

麻花钻钻孔中常见问题的原因和解决方法1、孔径增大、误差大产生原因:1、钻头左、右切削刃不对称,摆差大2、钻头横刃太长3、钻头刃口崩刃4、钻头刃带上有积屑瘤5、钻头弯曲6、进给量太大7、钻床主轴摆差大或松动解决方法:1、刃磨时保证钻头左右切削刃对称,摆差在允许范围内2、修磨横刃,减小横刃长度3、及时发现崩刃情况,并更换钻头4、将刃带上的积屑瘤用油石修到合格5、校直或更换6、降低进给量7、及时调整和维修钻床2、孔径小产生原因:1、钻头刃带已严重磨损2、钻出的孔不圆解决方法:1、更换合格钻头2、3、钻孔时产生振动或不圆产生原因:1、钻头后角太大2、无导向套或导向套与钻头配合间隙过大3、钻头左右切削刃不对称,摆差大4、主轴轴承松动5、工件夹紧不牢6、工件外表不平整,有气孔沙眼7、工件内部有缺口,交叉孔解决方法:1、减小钻头后角2、钻杆伸出过长时必须有导向套,采用合适间隙的导向套或先大中心孔在钻孔3、刃磨时保证钻头左右切削刃对称,摆差在允许范围内4、调整或更换轴承5、改良夹具与定位装置6、更换合格毛坯7、改变工序顺序或改变工件结构4、孔位超差,孔歪斜产生原因:1、钻头的钻尖已磨钝2、钻头左右切削刃不对称,摆差大3、钻头横刃太长4、钻头与导向套配合间隙过大5、主轴与导向套中心线不同心,主轴与工作台面不垂直6、钻头在切削时振动7、工件外表不平整,有气孔砂眼8、工件内部有缺口、交叉孔9、导向套低端面与工件外表间的距离远,导向套长度短10、工件夹紧不牢11、工件外表倾斜12、进给量不均匀解决方法:1、重磨钻头2、刃磨时保证钻头左右切削刃对称,摆差在允许范围内3、修磨横刃,减小横刃长度4、采用合适间隙的导向套5、校正机床夹具位置。
检查钻床主轴的垂直度6、先打中心孔再钻孔,采用导向套或改为工件回转的方式7、更换合格毛坯8、改变工序顺序或改变工件结构9、加长导向套长度10、改良夹具与定位装置11、正确定位安装12、使进给量均匀5、钻头折断产生原因:1、切削用量选择不当2、钻头崩刃3、钻头横刃太长4、钻头已钝,刃带严重磨损呈正锥形5、导向套底端面与工件外表间的距离太近,排屑困难6、切削液供给不足7、切屑堵塞钻头的螺旋槽,或切屑卷在钻头与导向套之间8、导向套磨损或成倒锥形,退刀时,钻屑夹在钻头与导向套之间9、快速行程终了位置距工件太近,快速行程转向工件进给时误差大10、孔钻通时,由于进给阻力迅速下降而进给量突然增加11、工件或夹具刚性不足,钻通孔时弹性恢复,使进给量突然增加12、进给丝杠磨损,动力头重锤重量不足。
650型定向井悬挂短节深孔加工工艺优化设计

隙 ,减振块不 起作用。当钻 削力失去平衡发生振 动 ,钻 头偏离 导块 方 向时 ,减振块 才起 作用 ,达 到
减振 、消振 、保 护 刀刃 的 目的 。同时 ,有助 于提 高 孔 的形状 精度 。 2 .珩磨 工具 的改 进
率 。系统最大钻孔 深度为 250mn 0 J ,转速为 1 8— 6Ormn O i,进给量 为 0 0 — . / . 1 05眦nr /,可 以满足
13 6 1 8 5
规加工手段很难达到用户使用要求 ,即便一些石油
专业厂家能够加工制造 ,但因其生产成本高、效率 低 ,也不能满足用户需求。为了降低生产成本 ,大 港油 田集团新世纪机械制造有限公司和大港油 田公 司第五采油厂对定 向井专用工具 并取得了一定的成效。 60型悬挂短节是定向井工具 中的易损件。该 5 5 0型 ( % 6 英寸)悬挂短节内孔加工工艺进行 了探索 和实践 ,
实践证 明,对传统加工工艺改进后 ,减小了刀具切 削力、钻削过程中的振动 ,提高了钻头耐用度 、钻 孔效率和钻孔精度。
3 工设备 .加
该悬挂短节的加工试验在改制的 C 20 W68 C车 床深孔加工系统上进行。该系统采用的 D F油路系
维普资讯
维普资讯
石
一
油
机
械
3 一 O
C IA ER LU A HN R H T OE MM C IE Y N P
20 06年
第3 4卷
第8 期
.加 工 制造 .
60型 定 向井 悬 挂短 节 深 孔 加 工 工 艺优 化 设 计 5
佘泽华 韩福强 董在 刚 魏福锁 李 辉
(. 1 大港油田集 团新世 纪机械 制造 有限公 司 2 .大港油田公 司第五采 油厂 )
喷吸钻的原理与应用

猛
不 同的切削速度 ,采用不 同的刀 片材料 ,并可分别磨 出
所需 要 的不 同参 数 的断 屑 台。
采取 较 大顶 角 ( 一般 取 2 a= 15 2 。~10 ) 4 。 ,以 利 断 屑。采
用支撑板 以增大切 削过程 的稳
的深孔 , 精度可达 II I1 ,加工表面粗糙度值 = TO—T7
定性 ,其位置根 据钻头受 力状
态安排 。
图 2 钻头
.
喷 吸 钻 的特 殊 处 在 于 有 内 、外钻 管,外钻管上 的反压 缝 隙 n ( 1 的大小 直接 影 图 )
中心刀 片 2 周 边 刀片 .
3 .支撑 板 4 .中间 刀片
d 压 向切削区 ,对钻 头切 削部分及导 向进行冷却与润 qL
一
图 3 冷却系统
1 .电动 机 2 .过滤 器 3 屑槽 .排 4 .压力 表 5 球 阀 6 高 压泵 . .
个动力头 ,这样虽然提高 了孔 的直线度 ,但增加 了改
续使用时有停滞 的危险 。所 以对 专门进行深 7I工 的机 L ̄ J
床来说 ,最好选用 含 E P添加剂的切削油作为切削液 。 ( )高压泵 2 压力和流量是选 配高压泵的 两个基 本
内 、外钻管之间的环形面积要大 于钻头小孔 的面积
2 结构特点 .
喷吸钻 主要 由钻 头 、内钻 管、外 钻管 三部分组 成。 钻头与钻管靠方形螺纹联接 ,如 图 1 所示 。内 、外钻 管
由连接器连接 。
之和 , 钻头小孔 的面积之和又要大 于反压缝 隙的环形
面积 ,使切削液向切削区的流动过程 中,经过 的通 道面 积逐 步缩小 ,流速加快 ,呈雾状 喷出 ,有利于钻 头的冷 却。
- 1、下载文档前请自行甄别文档内容的完整性,平台不提供额外的编辑、内容补充、找答案等附加服务。
- 2、"仅部分预览"的文档,不可在线预览部分如存在完整性等问题,可反馈申请退款(可完整预览的文档不适用该条件!)。
- 3、如文档侵犯您的权益,请联系客服反馈,我们会尽快为您处理(人工客服工作时间:9:00-18:30)。
目前,国内内排屑深孔钻刀片材料主要选 用硬质合金。 硬质合金的种类和牌号很多,除 普通硬质合金 (YG 类、YT 类、YW 类)外,发展了 许多新型硬质合金,如细晶粒和超细晶粒硬质 合 金 (YG6X、YD15)、 表 面 涂 层 硬 质 合 金 (YB120)、添加稀土元素的硬质合金(YW1R)等 等。 国内常用于内排屑深孔钻的刀片材料的牌 号主要是 YG8、YT15、YT798 和 YW1 等。
几何参数设计的不合理性主要表现在: (1)锋角 f 较小,钻尖较高 因锋角较小, 各刀齿在钻头锥面上沿半 径依次排列时, 刀齿间的轴向高度差相对较 大。 故在入钻、出钻阶段,中心齿要单独承受 较大的轴向力和径向力,使切削振动较大,定 心效果差,易产生硬质合金崩刃现象。 钻尖高度是指钻头的钻尖点到导向块前 端的轴向距离, 见图 1 中的 h。 钻尖高度越 大,入钻和出钻的时间就越长,不稳定钻削时 间也越长。 由于位于钻尖的中心齿切削速度 较低,切削力大,挤压摩擦严重,卷屑、断屑困 难,定心、导向较差。入钻时单刃独立作业,容 易产生摇晃,导致断齿或崩刃。 另外,出钻时 不易形成“切削帽”,钻尖首先钻穿工件,失去 孔底的反锥尖定心作用(见图 2),钻削力突 然失去平衡,钻头晃动突然加剧,非常容易崩 刃(特别是外齿)。
采用我公司自制的深孔钻床, 工件材料 为 45Cr1Mo1V 合金钢, 硬度 HRC 28~32,钻 头直径为准59 mm。 采用主铀(工件)转速 n= 43 r/min, 钻 头 转 速 n= 43r/min, 进 给 量 vf= 0.01~0.03 mm/r。 随着进给量增加,新型深孔 钻头切削力增加较为缓慢,如当 f=0.03 mm/r 时, 新型深孔钻头比普通型的深孔钻头的扭 矩轴向力和扭矩减小,机床电流负荷降低 10 %;由此可以看出,新型深孔钻头在大进给量 的切削过程中,切削更轻快平稳。
图 10 8 吋潜孔冲击器结构
塞的重量比为 1:1 左右,以保证最佳的能量传 递。 钻头与前接头的连接为花键连接。 冲击器 与钻杆的连接多数为锥形螺纹连接。
凿 岩 机 械 气 动 工 具 ,2009(1)
19
削力变化较大, 刀片选择与钻削材料不协调 等缺陷。这些缺陷造成钻头钻削稳定性不够, 耐用度差,钻孔效率和钻孔质量低。
20
定心反锥
定心 环形凸筋
图 2 加工孔底的形状
(2) 中 间 齿 、 外 齿 的 刀 尖 角 较 小 , 尖 角 突 出,强度降低,一旦尖角出现磨损,齿间的搭 接量就遭到破坏,容易造成崩齿,导致上述现 象及扭钻事故。
(3)内刃偏角小。钻削时孔底反锥高度较 低,定心作用减弱,容易引发切削振动,钻孔 质量差,或影响钻头使用寿命。
(2)改中间齿为尖齿。 为了提高钻削稳定
凿 岩 机 械 气 动 工 具 ,2009(1)
性,我们将中间齿设计为尖齿(见图 1)。 切削
时,中间齿在孔底形成环形凸筋,与内折线刃
在孔底形成的反锥(见图 2)同时起到定心、稳
定钻削的作用。
(3)增加减振块。 普通深孔钻大都采用两
个导向块,与钻头外齿副刃基本上在 180°内布
钻头刃型数对屑形的影响: (1)圆弧刃半径 R R 过小,形成分屑点尖角小,切屑易分开, 外刃出带状屑,圆弧刃出扇面块状屑。 R 过大,形成分屑点尖角大,圆弧刃屑易 连成一体,形成短的螺旋扇面形屑。 R 适中,外刃流屑方向与相临圆弧刃后流 向夹角较小,时连时分,此时正是生成“c”字形 屑的条件。 最佳角与材料韧性、切屑厚度等因 素有关,不是常数。 可通过试验找出最佳值。 (2)内、外刃高度差 Δh 圆弧刃较深时,外刃与圆弧刃形成自然分 屑点,外刃出带状屑,圆弧刃出块状屑。 圆弧刃 较浅时, 外刃与圆弧刃形不成自然分屑点,切 屑连成一体生成短的螺旋扇面形屑。 圆弧刃深度用内外刃垂直高度差 Δh 来控 制,较为合适的 Δh 值,应根据材料情况和进给 量由试验确定。 (3)外刃锋角 外刃锋角 f 过小时( f<125°)难以磨出适宜 尖角。 切屑易卷在容屑槽内,不宜排除。 实验表
普通的准50-准72 mm 深孔钻头,可分为 3 刃或 5 刃结构,外齿、内齿和中间齿不在同一 锥面上,因此有比较好的分屑效果,因此得到
技术中心,对钻头的设计,开展了系统的研究 广泛的应用。但存在几何参数设计不合理,切
!!!!!!!!!!!!!!!!!!!!!!!!!!!!!!!!!!!!!!!!!!!!!!!!!!!!!!!!!!!!!!!!!!!!!!
该钻头钻削一般钢材时 vc= 70 ~100 m /s , f = 0.15 ~ 0.30 mm /r 目前,常采用静力学中“稳定度”的概念作 为合理布置导向块位置的理论依据。 稳定度在 这里是指以所要考察的那个导向块作为支点, 使非考察的那个导向块压向孔壁的力矩与使 非考察的那个导向块脱离孔壁的力矩的比值。 这样,一个钻头就有两个稳定度,对于整个钻 头的稳定度,应该把两者中最小的作为该钻头 的稳定度 s,s 值越大,钻削稳定性越好,即 s > 1 时,钻头处于稳定状态;s = 1 时,钻头处于临界 状态;s<1 时,钻头处于不稳定状态。 其它参数不再赘述,详见图 3。 改进后的钻头,应用效果良好。
(4)导向块位置的影响。深孔钻利用外齿 副刃和两个导向块三点定圆自行导向进行切 削。导向块必须始终保持与已加工孔壁接触, 并有一定的压力存在, 才能保证加工过程的 稳定性。
2 提高钻头稳定性途径的研究
消除或减小前述各因素的影响即可提高 钻削稳定性。 本文主要从深孔钻头结构等方 面进行了改进研究 (改进的钻头详见图 1)。 与普通钻头相比进行了以下改进。
高的强度、硬度、耐磨性和红硬性;内排 屑深孔钻钻削时切削力大,切削温度高,钻削 刀刃的磨料磨损、 扩散磨损乃至氧化磨损都 较严重, 尤其当工件中存在一些硬质化合物 时,磨损更加严重,所以要求刀具材料的硬度 高于被加工材料的硬度, 能在高温下保持高 的硬度,有好的耐磨性和耐用度。
抗冲击性强;内排屑深孔钻削时刀具易崩 刃和扭断,故刀片材料应具有强抗冲击性。
法对铸造钢坯进行加工后轧制, 因此我们制 造了 10 余台内排屑深孔钻床,每天要消耗大 量的准50-准72 mm 焊接齿内排屑普通深孔钻 头。普通的内排屑焊接齿深孔钻头,普遍存在
的内排屑深孔钻头(以下简称钻头)。 本文基 于钻头的研制和实验,予以介绍。
1 普通钻头存在的问题
一些技术设计问题,致使钻头早期破损失效, 消耗大、效率低。因此钻孔成了制约轧钢生产 的“瓶颈”工序。为此,我们钎钢钎具工程研究
刃上方与之成 90°的位置(见图 3)。在正常切削
时,切削合力指向两导向块之间,使导向块紧
贴己加工孔壁,起导向作用,而减 振块位于后
端, 刃齿有倒锥使与己加工孔壁有一定的间
隙,不起作用;当钻削力失去平衡发生振动,产
生偏离导向块方向的位移时, 减振块才起作
用,可以减振、消振,保护刀刃和提高加工孔的
形状精度。
(1)增大了钻头锋角,降低钻尖高度。 这 是通过加大偏心量、 将中心齿的内刃磨成两 条折线刃来实现的。 其特点是:可以有效地降 低钻尖高度(图 1 中的钻尖由 h1 降低到 h2), 缩短入钻和出钻的时间。入钻时,中心齿和中 间齿几乎同时切入工件, 入钻后很快就可以 进入正常切削状态;出钻时,切削帽减薄,各 刀齿上切削力几乎同时消失, 有效地提高了 入钻和出钻过程的钻削稳定性。另外,内折线 刃还增大了中心齿的散热体积和钻尖强度。
内排屑深孔钻削是在封闭或半封闭的状 况下进行,切削热不易传散,排屑困难,工艺 系统刚性差。 当钻削中产生切屑不断或排屑 不畅引起堵塞时,常会崩刃或扭断钻杆;当钻 削中冷却液进不到切削区,造成冷却润滑不 良时,刀具温度急剧上升,加速刀具磨损,随 着钻孔的深度增加,刀具悬伸量增大,钻削时
22
的工艺系统刚性也随之降低。所有这些,对合 理选择内排屑深孔钻刀具的刀片材料提出了 一些特别的要求:
(5)减 小 导 向 块 与 刀 体 之 间 的 高 度 , 提 高 导向块的抗弯强度。
(6)为 了 增 大 冷 却 流 液 面 积 , 在 刀 体 上 铣 有半圆形输液槽,从而可使流液面积增大 20% ~ 30%,增大冷却液流量,以增强钻削过程中的 冷却润滑效果。
3 刀具几何参数
切削塑性金属时,断屑是需要解决的主要 矛盾。 为有利于断屑,应尽可能增大切屑的基 本变形和附加变形。 此外,随着切屑在前刀面 上流动,其底层受到挤压,晶粒被拉长,造成切 屑底部膨胀,促使切屑进一步弯曲变形,引起 切屑卷曲。
(4)除 外 齿 与 外 缘 一 侧 为 尖 角 外 , 其 余 刀
5
中间尖齿
15°
146°
中心齿
减震块
5°
5°
6°
外刀齿
图 3 改进的深孔钻头 凿 岩 机 械 气 动 工 具 ,2009(1)
齿都进行了倒角, 同时带有 6°~12°的侧后角, 消除了尖角,增大了刀齿的散热体积,同时也 增强了刀齿强度,不易崩刃,有利于提高钻头 的耐用度。
置,稳定度 s > l,当切削力波动不大时,可以保
证钻削过程稳定。 但是,由于作导向的已加工
孔表面有圆度误差,以及工件材质不均,特别
是入钻和出钻, 难免在钻削过程中引起振动,
尤其是扭振,使钻头以某一个导向块为支点转
动。 这种情况,普通深孔钻无法抑制。 为此,我
们在钻头体后端增设一减振块,布置 在外齿刀
内排屑深孔钻刀片材料的合理选择,同常 规切削加工相似,对不同材料的钻削,钻头刀 片材料的选择也有所不同。
对普通碳钢和合金结构钢的钻削, 刀片 材料牌号的选择一般为: 导向块用 YT15,钻 头外刃刀齿用 YT789, 中间刀齿和中心刀齿 用 YT789 或 YG8。
5 实验验证
为了验证新型钻头的切削性能,进行了批 量零件的钻削试验, 以测试新型钻头的耐用 度、加工质量以及加工效率。