车轮系统设计指南
汽车研发:车轮的设计、开发方法及流程!

汽车研发:车轮的设计、开发⽅法及流程!车轮于汽车⽽⾔,主要⽤于⾏驶像⼈⼀样,主要⽤来⾛路但是⼤长腿乃是众多美⼥与“野兽”梦寐以求的许多“野兽”们看美⼥第⼀眼就是看腿美不美像下⾯这两双⼤长腿估计“野兽们”看到后就⾛不动路了吧哈哈哈哈哈哈那说到车轮呢今天漫谈君就和⼤家聊⼀聊车轮的设计、开发⽅法及流程汽车车轮是汽车的重要部件,既是⼀个外观装饰件,⼜是⼀个安全件。
车轮的设计既要安全、轻量化,⼜要美观,与整车风格相配,符合时代发展潮流,同时还要满⾜个性化需求。
⼀车轮系统01定义车轮系统是汽车的⾏⾛部件,汽车⼯作时,车轮将汽车发出的作⽤⼒传给路⾯,同时将地⾯给予的反作⽤⼒传回汽车,汽车依据车轮传递的⼒和⼒矩实现约定的承载和完成规范的运动。
02基本功能1)⽀撑汽车,承受汽车的重⼒,使汽车能够承载,⽀承垂直载荷;2)传递驱动⼒、转向⼒和制动⼒,使驾驶⼈员能够对汽车的的运⽤进⾏操控(提供加速和制动所需的纵向⼒和转弯所需侧向⼒);3)减⼩⾏驶阻⼒和能量消耗,提⾼运输效率;4)缓和⾏驶冲击,改善⾏驶条件,同时保护汽车和路⾯。
03车轮系统的组成⼆车轮总成01车轮车轮⼀般由轮辋、轮辐、轮毂等构成。
可分为辐板式车轮和辐条式车轮。
1)轮辋:车轮上安装和⽀撑轮胎的部件。
2)轮辐:车轮上车轴和轮辋之间的⽀撑部件。
3)轮毂:轮胎内廓⽀撑轮胎的圆桶形的、中⼼装在轴上的⾦属部件。
02轮胎1)结构轮胎主要由内胎、外胎和垫带等组成。
垫带:⽤以保护内胎着合⾯不受轮辋磨损的环形带。
帘布层:帘布层是外胎的⾻架,也称胎体。
其主要作⽤是承受载荷,保持外胎的形状和尺⼨,使外胎具有⼀定的强度。
帘线:组成胎体帘布层、带束层、缓冲层等各种部件⽤的线绳。
2)轮胎规格表⽰⽅法3)轮胎的分类普通斜交车轮的帘布层和缓冲层各相邻层帘线交叉,且与胎⾯中⼼线呈⼩于90°⾓排列。
⼦午线车轮的帘布层与胎⾯中⼼线呈90°⾓或接近90°⾓排列。
4)轮胎花纹5)轮胎⽓压调节系统功能A. 汽车在松软地⾯上⾏驶时,可降低轮胎⽓压,增⼤车轮的接地⾯积,减⼩其单位⾯积载荷,从⽽提⾼汽车的通过性;B. 当轮胎穿孔⽽漏⽓时,轮胎⽓压调节系统可为车轮充⽓⽽使汽车继续⾏驶,不需马上更换轮胎;C. 使轮胎保持所需要的⽓压,有效提⾼汽车⾏驶安全性和燃油经济性。
上汽车轮设计规范

上汽车轮设计规范1. 引言上汽车轮设计规范是为了确保汽车轮的设计满足安全、可靠、经济、美观等方面的要求而制定的标准。
本规范适用于上汽公司在汽车轮设计和制造过程中的各个阶段,以确保最终产品符合设计和制造标准,满足客户需求。
2. 轮胎尺寸车轮的尺寸应根据车型和使用环境选择合适的规格。
轮胎尺寸的确定需要考虑到车辆的动力性能、操纵稳定性、驾驶舒适度和燃油经济性等因素。
同时,还需要考虑制动系统和悬挂系统等其他因素对轮胎尺寸的要求。
3. 轮毂结构车轮毂的结构应具备足够的强度和刚度,以承受汽车行驶中的各种荷载和力矩。
同时,车轮毂的设计还需要考虑到轮胎安装、动力传递、悬挂系统和制动系统等其他部件的要求。
车轮毂的材料应选择高强度、耐腐蚀和耐磨损的材料,以确保车轮的使用寿命和性能稳定性。
常见的车轮毂材料有铝合金、镁合金和钢材等。
4. 轮辐结构车轮辐是车轮毂与车轮毂之间的连接部件,其设计应考虑强度、刚度和轻量化等要求。
车轮辐的设计应符合下列要求:•辐条之间的距离应足够大,以确保轮胎的散热和制动系统的散热;•辐条的断面形状应选择合适的形状,以提高辐条的强度和耐久性;•辐条的材料应选择高强度和刚度的材料,以确保辐条的使用寿命和性能稳定。
5. 车轮均衡性车轮的均衡性是指车轮在旋转时的平稳性。
车轮的均衡性对驾驶稳定性、悬挂系统和悬挂零件的寿命等方面都有重要影响。
车轮的均衡性需要在设计和制造过程中进行有效的控制和调整。
为了确保车轮的均衡性,应采取以下措施:•在车轮设计过程中考虑轮毂和辐条的重量分布;•采用合适的车轮均衡技术,如质量均衡和动平衡;•在制造过程中进行车轮动平衡测试和调整,以消除轮胎和车轮组合体的不平衡。
6. 轮胎安装要求车轮的安装需要特别注意以确保安全和可靠性。
以下是车轮安装的一些重要要求:•轮胎与车轮轮毂之间的安装应采用适当的装配工具和技术,避免造成损坏或失效;•安装时应检查轮胎和车轮轮毂之间的间隙,以确保安装的正确性;•安装后应进行定位和校正,以确保轮胎与车轮轮毂的匹配性;•安装后应进行扭矩检查,以确保螺栓和螺母的紧固力合适。
汽车车轮动平衡测量系统的设计与实现
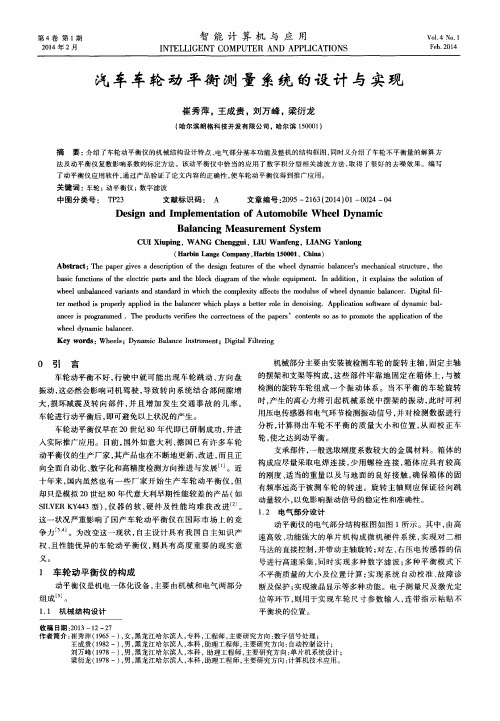
wh e e l dy n a mi c b a l a ne e r . Ke y wo r d s:W he e l s ; Dy na m i c Ba l a n c e I ns t u me r n t ; Di g i t a l Fi l t e ing r
崔 秀 萍 ,王成 贵 , 刘 万峰 , 梁 衍龙
( 哈尔滨朗格 科技开发有 限公司 。哈尔滨 1 5 0 0 0 1 )
摘 要 : 介绍 了车轮动平衡仪 的机械结构设计特点 、 电气部分基本功能及整机 的结构框 图, 同时又介绍 了车轮不平衡量 的解算方
法及动平衡仪 复数影 响系数 的标定方法 。该动平衡仪 中恰当的应用 了数字积分型相 关滤波方法 , 取得 了很 好的去 噪效果。编 写 了动平衡仪应用软件 , 通过产 品验证 了论文 内容的正确性 , 使车轮动平衡仪得 到推广应用 。
关键词 : 车轮; 动平衡仪 ; 数 字滤波
中图 分 类 号 : T P 2 3
文献标识码 : A
文章编号 : 2 0 9 5—2 1 6 3 ( 2 0 1 4) o 1 — 0 0 2 4— 0 4
车轮的设计原理

车轮的设计原理
车轮的设计原理有以下几个方面:
1. 结构设计:车轮通常由轮毂、轮辐和轮胎组成。
轮毂是车轮的中心部分,连接车轴,承载了车辆重量和扭矩。
轮辐连接轮毂和轮胎,起到支撑和保护轮胎的作用。
轮胎则是车轮与地面的接触部分,提供摩擦力和缓冲效果。
2. 材料选择:车轮需要承受较大的载荷和冲击力,因此常使用高强度的材料,如钢铁、铝合金等。
轮毂和轮辐需要具备足够的刚性和韧性,以抵抗外力的作用;而轮胎则需要具备耐磨、耐撕裂和耐高温等特性。
3. 动力传递:车轮是汽车传递动力的关键部件之一。
在传统燃油车中,车轮通过传动系统与发动机相连,将动力传递给地面,推动车辆行驶。
在电动车中,车轮通常由电动机直接驱动。
4. 减震效果:车轮设计中也考虑了减震效果,以提供更舒适的行驶感受。
轮胎通常具有弹性和吸震功能,可以减少车辆行驶过程中产生的颠簸和震动。
同时,一些车辆还配备了悬挂系统,通过悬挂装置在车轮与车身之间提供缓冲和支撑作用。
5. 高速平衡:车轮在高速行驶时会面临高速旋转带来的平衡问题。
车轮通常采取动平衡和静平衡措施,以确保在高速行驶中的稳定性和安全性。
综上所述,车轮设计的原理包括结构设计、材料选择、动力传
递、减震效果和高速平衡等方面,以提供稳定、安全和舒适的行驶体验。
指南车原理

差动式指南车方案—五十年代的指南车与宋代指南车的轮距等于轮径等结构大体相仿的条件下,选择自由度为二的差动轮系作为指南车的传动系统,是从事机械原理研究的人自然会想到的设计。
五十年代的指南车如图4 所示,此车就是采用了差动轮系方案。
五十年代的指南车图4图中A,B为指南车的轮子,D等于指南车的轮子直径,2L为指南车的宽度。
当指南车沿直线行走时,轮子A带动锥齿轮a转动,锥齿轮a带动锥齿轮c和c′转动;同理轮子D带动锥齿轮b转动,锥齿轮b带动锥齿轮d和d′转动。
由于直线行走时,锥齿轮c′和d′沿相反的方向转动,且转动速度一样,所以锥齿轮e的转臂不动,锥齿轮e绕固定轴旋转。
当指南车转弯时,齿轮的传动方式一样,但是锥齿轮c′和d′沿相同的方向转动,且转动速度一样,这就会导致锥齿轮e的转臂转动,同时锥齿轮e静止与自身的旋转轴。
当车身转过一定角度θ,左轮和右轮会有相应角度差ΦA- ΦB(见章节二),这个角度差ΦA- ΦB通过齿轮组最后使得木仙人相对于车辆转动-θ的角度,而相对于地面静止,所以木仙人就一直指向一个固定的方向。
五、指南车设计方案的比较和选择我们设计的是一种面向广大儿童的指南车玩具,所以设计的尺寸大小应该控制在140mm×140mm×140mm的空间范围内。
在选择指南车方案的过程中,应该考虑方案的可靠性、复杂程度、制作成本和安全性。
指南车设计方案比较1.定轴式指南车需要有一套自动控和自动离合的装置,常常是用齿轮的啮合和分离来实现的。
但是在啮合的过程中有可能会存在啮合点不正确而导致齿轮啮合不进去的现象,所以可靠性下降。
而差动式指南车不存在此现象。
2.定轴式指南车的行车轨迹只能是直线和定点转动的圆弧,如图5所示。
这是由于定轴式指南车固有的结构设计所导致的。
如节四所介绍的宋代指南车,当车转弯时,由辕A控制中心大平轮G与一个小平轮啮合,而与另一个小平轮分离,这时候,分离的小平轮不能够有转动,否则就会带来指南的误差,而正因如此,指南车在转弯时只能绕着分离的小平轮所对应的那个大轮子的着地点作圆周旋转。
汽车车轮侧滑量检测系统的设计

汽车车轮侧滑量检测系统的设计
本系统主要应用于汽车车轮侧滑量的检测。
为保证汽车转向车轮无横向滑移的直线滚动,要求车轮外倾角和车轮前束有适当配合,当车轮前束值与车轮外倾角匹配不当时,车轮就可能在直线行驶过程中不作纯滚动,产生侧向滑移现象。
当这种滑移现象过于严重时,将破坏车轮的附着条件,丧失定向行驶能力,引发交通事故并导致轮胎的异常磨损。
侧向滑移量的大小与方向可用汽车车轮侧滑检验台来检测。
侧滑台结构图:
系统的硬件配置:
2个位移传感器
2组光电开关
模拟量输入模块
开关量输入模块
系统工作原理:
当车轮踏上侧滑板时,第一组光电开关关闭(光电开关在没被挡住的情况下为常开状态),等离开侧滑板时,第二组光电开关关闭,此时记录车轮的侧滑量,一组车轮测试完成。
车轮依次踏上侧滑板,按照上述方式记录侧滑量,完成整个车的侧滑量测试。
功能结构图:
系统功能:
汽车定位:系统提供3种不同的汽车定位系统,分别为单桥定位,双桥定位。
轮胎压力与温度检测系统设计

轮胎压力与温度检测系统设计近年来,随着汽车行业的不断发展,车辆的安全性也越来越受到关注。
轮胎是汽车行驶的重要组成部分,它的压力和温度对行车安全有着至关重要的影响。
针对这一问题,不同的汽车制造商推出了各种类型的轮胎压力与温度检测系统。
本文就轮胎压力与温度检测系统的设计进行探讨。
一、轮胎压力与温度的重要性轮胎的压力是行车安全的重要保障之一,不仅会影响油耗、轮胎的耐久性和车辆的稳定性,还会影响对路面的附着力。
当轮胎的气压低于规定值时,会导致车辆行驶不稳、制动距离增大、轮胎磨损加速等问题。
同时,过高的气压也会导致轮胎的磨损加剧。
轮胎的温度也同样重要。
当轮胎长时间运转,特别是在高速公路等需要长时间高速行驶的路段,轮胎温度会逐渐升高。
如果温度过高,轮胎的橡胶会老化、硬化,从而导致开裂,这样会降低轮胎的寿命。
而轮胎温度过低时,会使橡胶变硬、降低柔性,从而降低轮胎与路面之间的附着力,影响车辆的行驶安全。
因此,轮胎压力与温度检测系统的设计对于车辆行驶安全至关重要。
二、轮胎压力与温度检测系统的设计1. 检测技术轮胎压力与温度检测系统的检测技术主要有两种:一种是通过传感器进行检测,另一种是通过胎压监测装置(TPMS,Tire pressure monitoring system)进行检测。
通过传感器实现的轮胎压力与温度检测系统,其传感器安装在每个轮胎上,实时监控各个轮胎的压力和温度,通过无线信号传输至车内显示屏,提醒驾驶员。
这种系统的优点是响应快、准确性高,并且可以监测到每个轮胎的状态。
然而,由于传感器需要安装在每个轮胎上,因此系统成本较高。
另外一种胎压监测装置(TPMS)则是利用车轮上的气门嘴探测胎压,将所测数据传到车载电脑系统内,由系统自动识别那个轮胎胎压不足。
这种系统优点是成本较低,缺点是无法监测轮胎的温度。
2. 系统设计轮胎压力与温度检测系统的设计要充分考虑安全性、稳定性和用户体验。
系统由传感器、控制器和车内显示屏组成。
车轮设计指导书

双王铝业有限公司产品设计指导书编号:版本号:修改次数:受控状态:实施日期:2014年07 月30 日分发号:批准日期审核日期编制日期一、目的1、规范设计人员产品设计,提高设计质量。
2、为研发中心产品设计人员提供参考。
二、范围1、本指导书适用于研发中心产品设计人员。
2、本指导书适用于铝合金压铸车轮的设计。
目录✧车轮产品结构基本知识一、车轮结构各部位名称二、车轮的种类三、车轮的基本装配知识✧产品设计工作流程✧产品结构设计一、确定车轮的参数二、5度深槽轮辋轮辋设计三、气门孔尺寸和位置四、车轮安装盘设计五、车轮轮辐结构设计六、轮辐掏料结构设计七、车轮中心孔结构设计八、螺栓孔结构设计九、装饰盖结构设计十、车轮机加余量的常规性设计十一、各种规格车轮的重量设计标准十二、常用PCD与中心孔对应表✧车轮飞轮结构设计车轮产品结构基本知识一、车轮结构各部位名称1、轮辋:与轮胎装配配合,支撑轮胎的车轮部分。
2、轮辐:与车轴轮毂实施安装连接,支撑轮辋的车轮部分。
3、偏距:轮辋中心面到轮辐安装面间的距离。
有正偏距、零偏距、负偏距之分。
4、轮缘:保持并支撑轮胎方向的轮辋部分。
5、胎圈座:与轮胎圈接触,支撑维持轮胎半径方向的轮辋部分。
6、槽底:为方便轮胎装拆,在轮辋上留有一定深度和宽度的凹坑。
7、气门孔:安装轮胎气门嘴的孔。
1 轮辋宽度10 螺栓孔节圆直径2 轮辋名义直径11 螺栓孔直径3 轮缘12 轮辐安装面4 胎圈座13 安装面直径5 凸峰14 后距6 槽底15 轮辐7 气门孔16 轮辋8 偏距17 轮辋中心线9 中心孔18二、车轮的种类按轮辋和轮辐结合形式的不同,车轮可分为如下结构,其代表型结构用图例来表示:1、整体式:轮辐和轮辋是由一个整体组成的。
2、组合式:由2个以上的零件组合而成的车轮,其组成的零件可以分开,按其组合形式可分为三类:(1)、两片式车轮:由轮辋和轮辐结合起来的结构;(2)、三片式车轮:由两个轮辋零件和一个轮辐结合起来的结构。
- 1、下载文档前请自行甄别文档内容的完整性,平台不提供额外的编辑、内容补充、找答案等附加服务。
- 2、"仅部分预览"的文档,不可在线预览部分如存在完整性等问题,可反馈申请退款(可完整预览的文档不适用该条件!)。
- 3、如文档侵犯您的权益,请联系客服反馈,我们会尽快为您处理(人工客服工作时间:9:00-18:30)。
车轮系统设计指南编制:校对:审核:批准:汽车工程研究院一.简要说明1.1车轮及车轮附件综述车轮是汽车的行走部件,汽车工作时,车轮将汽车发出的作用力传给路面,同时将地面给予的反作用力传回汽车,汽车依据车轮传递的力和力矩实现约定的承载和完成规范的运动。
轮胎和车轮组合工作,成对使用。
轮胎是弹性元件,镶嵌于车轮外缘,具有弹性、柔性和韧性,以及优良的变形能力和地面贴附能力;工作时可以分散汽车对路面的压力、降低汽车运动的能量损失,同时实现充分传力、经久耐用;车轮是刚性制件,在中心支撑轮胎,具有相应的强度、刚度,以及联结、传力机构,保证轮胎能够工作和展现轮胎特性。
轮胎和车轮共同体现其所具有的基本功能。
这些基本功能如下:①支撑汽车,承受汽车的重力,使汽车能够承载;②传递驱动力、转向力和制动力,使驾驶人员能够对汽车的运动进行操控;③减小行驶阻力和能量消耗,提高运输效率;④缓和行驶冲击,改善承载条件,同时保护汽车和路面。
轮胎及车轮与汽车的多种性能相关。
整车动力性、牵引性、经济性、平顺性、通过性、制动性及操纵稳定性等通过轮胎及车轮的特性配合实现匹配和优化,安全性和可靠性在很大程度上取决于所用轮胎和车轮的制造质量和使用寿命;车轮参数是整车设计的基础;轮胎是价格较高的易损件,对整车制造成本和汽车使用运营费用影响较大。
因此,汽车对轮胎和车轮的特性有诸多要求,其中主要要求如下:①足够的负荷能力和速度级别;②良好的附着特性和缓冲特性;③耐磨耗、耐刺扎、耐老化和良好的气密性;④良好的均匀性和质量平衡;⑤较小的滚动阻力和行驶噪音;⑥特定的外观或装饰;⑦质量小、价格低、拆装方便、互换性好。
轮胎和车轮需要配套,二者必须组成符合规定的配套总成才能装车使用。
轮胎和车轮还需要借助系统其它部件的组合应用才能完成正常的工作。
按照习惯专业划分,轮胎和车轮系统包含轮边可以从车桥上拆卸的所有独立部件,常见的应用部件如下:①轮胎(外胎,有些轮胎还有内胎、垫带等);②车轮(轮辋及轮辐总成,有些车轮还有挡圈、锁圈、座圈、密封圈等);③气门嘴(有些气门嘴是独立总成,有些气门嘴与内胎一体);④车轮螺母;⑤平衡配重(有些汽车省略不用);⑥轮罩(有些汽车省略不用);⑦轮胎防滑链(特别工况下使用);⑧专用装置(特定轮胎或车轮使用)。
轮胎及车轮通常展示汽车的典型特征,同时也能显现汽车的基本特性。
不同汽车可能使用不同的轮胎及车轮规格,也可以具有不同的轮数。
汽车装用轮胎及车轮的规格和数目大致反映汽车的工作能力和基本用途。
由于轮胎及车轮系统在整车中结构相对独立、制造工艺具有特殊性(轮胎属化工类产品),轮胎及车轮产品都具有高度标准化、系列化和通用化的显著特点,生产基本专业化。
现代汽车轮胎和车轮的开发、制造、使用和服务趋向社会化,轮胎和车轮工业同整车工业逐步分离是未来发展的总趋势。
我公司目前计划内的产品使用的轮胎是半钢子午线轮胎,规格从155到255,扁平率从40到80之间。
使用的车轮从13英寸到18英寸,包括钢圈和铝圈两种。
1.2设计目的车轮的设计首先必须满足总布置的需要,只有首先确认了车轮,才能在这一基础上进行整车的布置工作,同时,要满足负荷和速度的要求。
因此,车轮的设计目的就是通过合理的选择车轮的型号以满足整车布置、负荷和速度的需要,同时满足一定的外观需求。
1.3适用范围适用于轿车轮胎的选择。
1.4总成构成图图1.1 轮胎构成图图1.2轮辋结构图图1.3 总成构成图二、设计原则2. 1 车轮总成的设计原则(1)功能要求1、支撑汽车,承受汽车的重力,使汽车能够承载;2、传递驱动力、转向力和制动力,使驾驶人员能够对汽车的运用进行操控;3、减小行驶阻力和能量消耗,提高运输效率;4、缓和行驶冲击,改善行驶条件,同时保护汽车和路面。
(2)顾客要求1、使用寿命要尽量的长;(要求轮胎的耐磨性较好和车轮的强度高)2、外观要与整车相配合;3、拆卸、安装方便;(3)性能要求1、轮胎的速度级别和负荷指数必须满足整车的最高车速和最大载荷的要求;2、车轮的负荷能力必须满足整车的负荷要求;3、轮胎的花纹与整车工况相适应。
2.2 车轮设计参数2.2.1 决定尺寸的因素⑴与制动器的配合关系;⑵与车身的配合关系;⑶轮胎与轮辋的配合关系;⑷总布置要求的尺寸。
2.2.2 决定重量的因素⑴是采用钢圈还是铝圈;⑵对轮胎强度的要求;⑶对车轮总成承载能力的要求。
以P195/75—14的轮胎为例:人造橡胶(30种) 2.49kg碳黑(8种) 2.27kg天然橡胶(8种) 2.04kg化学物质,石蜡,石油,染料(40种) 1.36kg带束层钢丝线 0.68kg聚酯和尼龙线 0.45kg胎圈钢丝 0.23kg总重 9.52kg(固特异轮胎有限公司)2.3 环境条件2.3.1 零件的工作温度范围轮胎:-50℃~90℃2.3.2 零件工作的压力范围轮胎:2.0~3.0BAR2.5.3 组成该零件的部件12.5.3.2 该部件和该零件的装配模式/组装1.装配气门嘴前,先检查车轮上的气门孔是否光滑无毛刺,然后将气门嘴橡胶体表面涂上甘油或将气门嘴在甘油中浸一下,用专用工具以200~600N的力拉或压使气门嘴上的定位环通过车轮的孔后即安装到位(允许用肥皂水替代甘油)。
2.装配轮胎之前,将胎圈沿周向涂上甘油或肥皂水,同时注意:轮辋上有轻点标记时,将轮胎的均匀性测试标记对准轮辋的轻点标记。
轮辋上无轻点标记时,将轮胎的动平衡测试标记对准气门嘴位置。
轮辋上无轻点标记,且轮胎上无动平衡测试标记、而有静平衡测试标记时,将气门嘴对准静平衡测试标记。
轮胎的均匀性、动平衡、静平衡测试标记说明参轮胎图纸。
3.严格按照规定压力对轮胎充气,充气过程中气压不得超过额定气压的10%。
备胎总成分装时额定充气压力3.5atm,单独存放。
四轮定位工位前检查四轮轮胎气压并调整气压:标准atm±10%;4.轮胎充气后拧上气门嘴防护帽进行动平衡试验,按需在轮辋内外侧边缘装配合适重量的卡式平衡块I、II(A11-3100217~A11-3100239、A11-3100217BA~A11-3100239BA),要求总成不平衡度小于100g· cm,约相当于图示位置的平衡块5g。
注意:每个车轮单侧最多允许使用一个平衡块,且最大质量不大于65g。
在装配过程中避免对平衡块打击过重,若感到打击过重者则及时更换平衡块。
更换下来的平衡块不允许重复使用。
5.安装车轮及轮胎总成时,先将车轮螺母拧到轮毂上用手预紧,之后使用专用工具按对角线方法拧紧,拧紧力矩110%%P10N.m。
禁止使用冲击扳手以免拧得过松或过紧。
车轮螺母不允许涂润滑脂。
6.安装卡式装饰罩应用手拍打或使用橡胶工具将之敲入。
2.5.4.5 装配后工作能力的分析2.6 测试基本参数参见《铸造铝合金车轮》标准;轮胎试验数据的确定1.强度试验:破坏能的计算:W=F×P/2000W——破坏能,J;F——作用力,N;P——行程,mm;2.轮胎气压和温度关系PV=mR(273+T)/uP-----轮胎气压,Pa R------阿佛加得罗常量,8.31J/K/molV-----轮胎体积,m3m-----气体质量,gu------气体摩尔质量,g/molT-----温度,℃3.耐久性:GB/T 4502-19984.脱圈阻力试验:GB/T 4504-19985.强度试验:GB/T 4503-19966.高速性能试验:GB/T 7034-1998车轮品质的评价指标车轮试验载荷及寿命的计算方法① 轮试验载荷的计算F1=Q (前)·g ·[μ·R (动)+e]F2=0.5F1Q(前)——前轮允许的载荷;μ=0.9;R(动)——车速60km/h 时车轮的动力半径;e ——车轮的偏距;② 使用寿命的计算n N50= N1·N2·N3···Nn∑n (logN0—logNi) F1Slog= n —1 F2K=△1/△2=(logN2/N1)/(logF2/F1)N2=N1 (F1/F2)n Slog=0.15~0.3 N1 N2 寿命(N )logK :一般焊接件≥4~5弯曲扭件≥4~8扭转件≥102.6.2 测试的基本内容4.1 使用性能及耐久性能4.1.1 弯曲疲劳性能在规定的条件下,应满足下列要求:13寸:当M=2100N·m时,旋转120万次;当M=3600N·m时,旋转12万次,试验方法按QC/T221并进行检验;14寸:当M=2300N·m时,旋转120万次;当M=3700N·m时,旋转12万次,试验方法按QC/T221并进行检验;15寸:当M=2574N·m时,旋转120万次;当M=3800N·m时,旋转12万次,试验方法按QC/T221并进行检验;16寸:当M=2574N·m时,旋转120万次;当M=4000N·m时,旋转12万次,试验方法按QC/T221并进行检验;a)车轮的任何部位不允许出现可见的新裂纹或任何可见裂纹的扩展;b)任一紧固螺母的紧固力矩不得低于原始紧固力矩的60%;c)车轮在完成要求转数后能继续承受载荷。
4.1.2 径向疲劳性能在规定的条件下,应满足下述要求:13寸:当Fr=11025N时,旋转50万转,试验方法按QC/T221并进行检验;14寸:当Fr=11500N时,旋转50万转,试验方法按QC/T221并进行检验;15寸:当Fr=14625N时,旋转50万转,试验方法按QC/T221并进行检验;16寸:当Fr=14625N时,旋转50万转,试验方法按QC/T221并进行检验;a)车轮的任何部位不允许出现可见的新裂纹或任何可见裂纹的扩展;b)任一紧固螺母的紧固力矩不得低于原始紧固力矩的60%;c)车轮在完成要求转数后能继续承受载荷;d)车轮轮辋不能漏气。
4.1.3 冲击性能在规定条件下,车轮在经受冲击后应满足下述要求:在规定条件下,车轮在经受冲击后应满足下述要求:13寸:锤重=(540±2%)kg,落下高度为(230±2)mm,试验方法按:GB/T15704;14寸:锤重=(560±2%)kg,落下高度为(230±2)mm,试验方法按:GB/T15704;15寸:锤重=(580±2%)kg,落下高度为(230±2)mm,试验方法按:GB/T15704;16寸:锤重=(580±2%)kg,落下高度为(230±2)mm,试验方法按:GB/T15704;4.1.4 车轮平衡在规定的条件下,车轮的动平衡量应符合表1中的要求,也可根据用户要求进行调整。