薄板对接焊缝超声波探伤方法的试验
超声波检测焊缝的几种常用方法
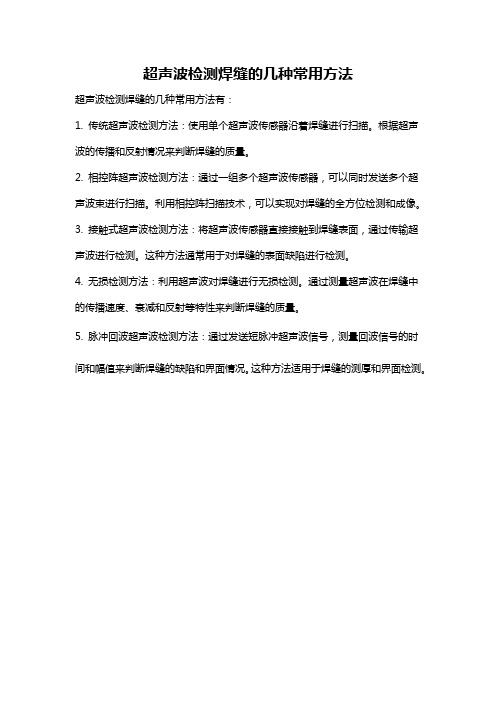
超声波检测焊缝的几种常用方法
超声波检测焊缝的几种常用方法有:
1. 传统超声波检测方法:使用单个超声波传感器沿着焊缝进行扫描。
根据超声波的传播和反射情况来判断焊缝的质量。
2. 相控阵超声波检测方法:通过一组多个超声波传感器,可以同时发送多个超声波束进行扫描。
利用相控阵扫描技术,可以实现对焊缝的全方位检测和成像。
3. 接触式超声波检测方法:将超声波传感器直接接触到焊缝表面,通过传输超声波进行检测。
这种方法通常用于对焊缝的表面缺陷进行检测。
4. 无损检测方法:利用超声波对焊缝进行无损检测。
通过测量超声波在焊缝中的传播速度、衰减和反射等特性来判断焊缝的质量。
5. 脉冲回波超声波检测方法:通过发送短脉冲超声波信号,测量回波信号的时间和幅值来判断焊缝的缺陷和界面情况。
这种方法适用于焊缝的测厚和界面检测。
浅谈钢制小径薄壁管环向对接接头的超声波检测工艺

浅谈钢制小径薄壁管环向对接接头的超声波检测工艺摘要:在承压类特种设备的制造和安装过程中,当钢制小径薄壁管环向对接接头因为受到结构或位置限制而不能优先选择射线检测方法时,超声波检测无疑是更为合理的检测方法。
本文较为详细地介绍了钢制小径薄壁管环向对接接头超声波检测的一般性工艺方法,包括探头和试块的选用、仪器探头系统的校准,以及DAC曲线的制作方法等方面内容,可做为承压类特种设备中钢制小径薄壁管环向对接接头采用超声波检测时的参考。
关键词:钢制小径薄壁环向对接接头超声波检测一般性工艺方法1、前言在承压类特种设备的无损检测中,时常遇见公称直径150mm以下,壁厚为4~8mm的小径薄壁管(一般为无缝管)的环向对接接头。
通常情况下,对该类对接接头,采用射线检测是最为可靠的检测手段。
但由于对接接头的位置以及检测现场条件等因素的限制,当不能优先选择射线检测方法时,选择超声波检测更为合理。
下面,依据JB/T4730.3-2005《承压设备无损检测》超声检测部分的第 6.1章节,浅谈一下钢制小径薄壁管(材质仅限于碳素钢和低合金钢)环向对接接头的横波接触法超声检测工艺,仅作参考。
2、探伤仪、探头、试块和耦合剂的选用2.1探伤仪必须满足JB/T4730.3-2005标准中3.2.2.1条关于仪器的要求。
2.2探头必须满足JB/T4730.3-2005标准中3.2.2.2条关于探头的要求。
小径管曲率半径小,管壁厚度薄,常规横波斜探头与管材接触面积小,耦合不良,波束扩散严重,检测灵敏度很低。
因而,在选用探头时,应从以下几个方面考虑:(1)曲面耦合:小径管表面为曲率半径较小的曲面,为了实现良好的耦合,一般将探头楔块加工成与管子外径相吻合的曲面,以减少耦合损失。
(2)晶片尺寸:探头楔块加工成曲面后,探头边缘声束将会产生散射。
晶片尺寸越大,散射越严重。
为了减少这种散射的不利影响,晶片尺寸不宜太大。
此外,为了尽量减少近场区的不利影响,也应该选择较小尺寸的晶片。
8~10mm薄壁对接焊缝超声检测方法及缺陷识别技巧
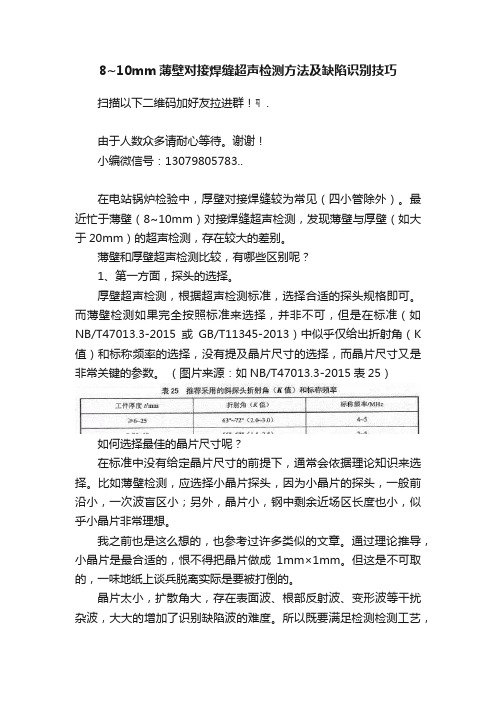
8~10mm薄壁对接焊缝超声检测方法及缺陷识别技巧扫描以下二维码加好友拉进群!☟.由于人数众多请耐心等待。
谢谢!小编微信号:130****5783..在电站锅炉检验中,厚壁对接焊缝较为常见(四小管除外)。
最近忙于薄壁(8~10mm)对接焊缝超声检测,发现薄壁与厚壁(如大于20mm)的超声检测,存在较大的差别。
薄壁和厚壁超声检测比较,有哪些区别呢?1、第一方面,探头的选择。
厚壁超声检测,根据超声检测标准,选择合适的探头规格即可。
而薄壁检测如果完全按照标准来选择,并非不可,但是在标准(如NB/T47013.3-2015或GB/T11345-2013)中似乎仅给出折射角(K 值)和标称频率的选择,没有提及晶片尺寸的选择,而晶片尺寸又是非常关键的参数。
(图片来源:如NB/T47013.3-2015表25)如何选择最佳的晶片尺寸呢?在标准中没有给定晶片尺寸的前提下,通常会依据理论知识来选择。
比如薄壁检测,应选择小晶片探头,因为小晶片的探头,一般前沿小,一次波盲区小;另外,晶片小,钢中剩余近场区长度也小,似乎小晶片非常理想。
我之前也是这么想的,也参考过许多类似的文章。
通过理论推导,小晶片是最合适的,恨不得把晶片做成1mm×1mm。
但这是不可取的,一味地纸上谈兵脱离实际是要被打倒的。
晶片太小,扩散角大,存在表面波、根部反射波、变形波等干扰杂波,大大的增加了识别缺陷波的难度。
所以既要满足检测检测工艺,又要快速找出缺陷,实则有些困难。
但是难不倒喜欢瞎捣鼓的人,分别试验了5Z6×6K2.5、5Z6×6K3、5Z8×8K2.5、2.5Z8×8K2.5、5Z8×8K3、5Z9×9K3等规格的探头,发现除了5Z9×9K3(实测K值有2.87、3.01、3.21等均可,实测前沿约11mm)外,其他规格的探头干扰波太多,实在是在下辨别缺陷的水平有限,太难了。
焊缝超声波探伤(第二节平板对接焊缝的超声波探伤方法)
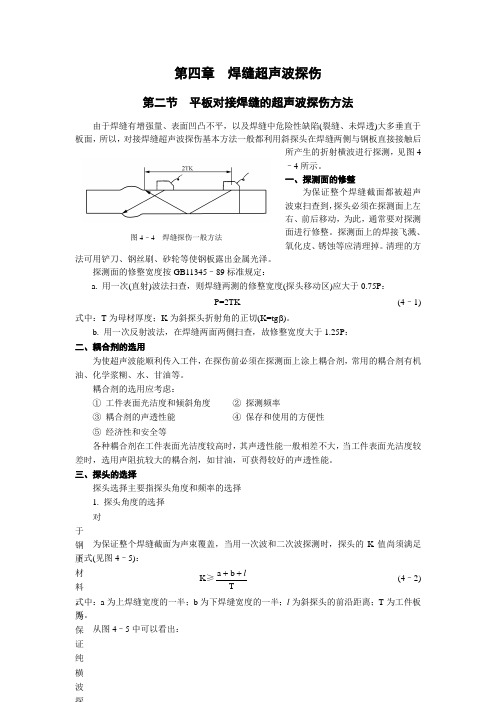
第四章 焊缝超声波探伤第二节 平板对接焊缝的超声波探伤方法由于焊缝有增强量、表面凹凸不平,以及焊缝中危险性缺陷(裂缝、未焊透)大多垂直于板面,所以,对接焊缝超声波探伤基本方法一般都利用斜探头在焊缝两侧与钢板直接接触后所产生的折射横波进行探测,见图4–4所示。
一、探测面的修整为保证整个焊缝截面都被超声波束扫查到,探头必须在探测面上左右、前后移动,为此,通常要对探测面进行修整。
探测面上的焊接飞溅、氧化皮、锈蚀等应清理掉。
清理的方法可用铲刀、钢丝刷、砂轮等使钢板露出金属光泽。
探测面的修整宽度按GB11345–89标准规定:a. 用一次(直射)波法扫查,则焊缝两测的修整宽度(探头移动区)应大于0.75P :P=2TK (4–1)式中:T 为母材厚度;K 为斜探头折射角的正切(K=tg β)。
b. 用一次反射波法,在焊缝两面两侧扫查,故修整宽度大于1.25P : 二、耦合剂的选用为使超声波能顺利传入工件,在探伤前必须在探测面上涂上耦合剂,常用的耦合剂有机油、化学浆糊、水、甘油等。
耦合剂的选用应考虑:① 工件表面光洁度和倾斜角度 ② 探测频率③ 耦合剂的声透性能④ 保存和使用的方便性⑤ 经济性和安全等各种耦合剂在工件表面光洁度较高时,其声透性能一般相差不大,当工件表面光洁度较差时,选用声阻抗较大的耦合剂,如甘油,可获得较好的声透性能。
三、探头的选择探头选择主要指探头角度和频率的选择 1. 探头角度的选择对于钢质材料,为保证纯横波探测,探头的入射角应在第一临界角(27.5°)和第二临界角(57°)之间,即27.5°<α<57°。
国内过去使用的探头均以入射角标称,如、30°、40°、45°、50°、55°等。
近年来,考虑到为使缺陷定位计算方便,故均改用K 值探头(K=tg β)如K=0.8、K=1、K=1.5、K=2、K=2.5、K=3等。
薄壁焊缝的超声板波检测方法研究1

作者简介何清,(66—),男,在职博士研究生文章编号:100520930(2005)20124206 中图分类号:TH82 文献标识码:A薄壁焊缝的超声板波检测方法研究何 清, 陈国光, 田晓丽(中北大学机械电子工程系,山西太原030051)摘要:针对高压薄壁焊接钢筒工件的内部质量检测问题,通过对五种常规无损检测方法的比较,确定了采用超声波板波法的优点.本介绍了板波的原理、特点、速度与入射角的关系、模式的能流分部并绘制了能流分部图.以高压薄壁焊接钢筒检测为例进行了现场试验,并以X 射线检测复测来确认板波检测的可靠性,对比试验结果证明,超声波板波法可有效的发现高压薄壁焊接钢筒焊缝内部缺陷,并可实现快速在线检测,具有广阔的应用前景.关键词:超声检测;板波;薄壁;钢筒高压薄壁焊接钢筒的形成过程为:薄板→卷圆→焊接→辊压→成型.由于钢筒焊接过程中可能会在焊接区形成各种缺陷,而钢筒使用过程中又承受较大压力,因此需要对其焊缝进行100%检测.对于焊缝,目前已有多种检测手段,比较常见的有:射线检测、涡流检测、磁粉检测、渗透检测、超声检测等技术.常见的五种方法中,磁粉、渗透、涡流、主要是检测表面或近表面缺陷,对于焊缝内部缺陷的检测采用较多是射线和超声检测,而射线检测成本高、效率低、不适合批量检测,超声检测是采用较多的另一种检测方法,但对于薄板焊缝的检测,还没有一种成熟的技术和方法可供借鉴,针对这种情况,在理论分析和实践的基础上,我们提出了采用超声板波法进行检测,从而达到了对钢筒焊缝的检测目的.图1 板波的产生Fig 11 Gene ra ti on of p late wave1 超声板波检测原理1.1 板波的产生机理众所周知,超声波以一定的入射角倾斜入射到薄板中,在板厚与波长相当的薄板中传播的波称为板波.要产生较强的板波,就要使探头楔块中的振动与薄板中的振动产生共振,当楔块中的纵波波长λL 与薄板中的板波波长λP 相对应时楔块中的振动就会与薄板中的振动产生共振,从而产生较强的板波,如图1所示.1.2 板波的特点板波的传播按照质点振动轨迹的不同,分为对称型(S 型)和非对称型(A )两种.如图2所示.增刊2005年10月 应用基础与工程科学学报JOURNA L OF BAS I C SC I ENCE AND E N GI N EER I NGSupp lemen tO ctober 2005:19.对称型(S 型)板波的特点是:薄板中心质点作纵向振动,上下表面质点作椭园运动,振动相位相反并对称于中心.图2 薄板中板波传播示意图F ig .2 Ske tch map of pla t e wave trans m issi on in thin p late非对称型(A 型)板波的特点是:薄板中心质点作横向振动,上下表面质点作椭园运动,并相位相同不对称[1].1.3 板波的反射板波在薄板中传播时,遇到板的端部或缺陷同样会产生反射,而且会产生波型转换.反射波经过探头转换成电脉冲,在探伤仪的示波屏上显示出来.反射的声能大小,决定于声阻抗变化之差,声阻抗的有效值又等于传声介质的密度值与超声波在介质中传播速度的乘积,而在缺陷的边缘声阻抗变化最大,因而缺陷反射回波就在这里形成.图3 钢板中相速度和频率×板厚的关系F ig .3 R elati on bet ween phase velocit y and frequency ×platesi ckness in steel plate1.4 板波的速度与入射角当介质一定时,板波的传播速度C 与频率(f)和板厚(d )以及入射角(α)有关[2].在一定的情况下可以有多种速度与波型存在,当频率与板厚(f ×d )值确定时,随声波入射角的不同,所得到的板波类型和模数也不同,而当声波入射角一定时,随频率与板厚(f ×d )值的改变,所得到的板波速度也随之改变.如图3—图5所示.图 钢板中群速度和频率×板厚的关系F R y f q y ×521何清等:薄壁焊缝的超声板波检测方法研究4图5 钢板中入射角和频率×板厚的关系F i g .5 Re lation bet ween entrance angle and frequency ×pla t e sickness in stee l p late当超声波束斜入射于介质时,其入射角与板波的相速度有如下关系:sin α=C L CP其中C L 为逶声斜楔中的纵波波速;C P 为薄板中的板波相速度.2 试验方案研究由钢板中入射角和频率×板厚的关系曲线图和以上公式可知:当板厚和频率确定后,可使用的探头角度较多(见表1).选用那种角度最佳,也就是选用那种角度做为入射角,即能将板材和焊缝中的缺陷检出而又不漏检.此入射角就为最佳入射角.因此,必须对所选的角度做能流分布测试.表1 从板波曲线族中查到频率、板厚、入射角、板波模数Table 1 frequency 、p late si ckness 、entrance angle 、module of pla te wav e found infam ily of curve s of p late wave模数f ×dαV P 1.8×3αV P 2.0×3αV P 2.5×3αV P S0A067°13295067°13295067°132950S130°535031°5500040°4200A145°390048°370052°3250S2A225°680025°620028°30°54005900能流分布试验方法:首先从被检板材上截取一段,规格为300×80和300×200两种,并在试板上加工不同深度的沟槽和不同深度平底孔(见表2).621应用基础与工程科学学报表2 试板人工缺陷Table 2 a rtificial defect of test pla t e规格/mm 300×80300×80300×80300×80300×80300×80300×80300×80规格槽深0.20.40.60.8 1.01.2 1.4 1.6规格/mm 300×200300×200300×200300×200300×200300×200300×200300×200孔深/mm 0.250.530.750.80.971.27 1.47 1.65孔径/mm118118118118118118118118 其次选择不同频率、不同角度的探头或可变角度探头,在试板两面上选择有孔和沟槽的面为正面,反之为反面.并在正反面上做各种不同深度缺陷情况下的回波试验.通过试验绘制不同角度的能流分布图.表3 试板人工缺陷Table2 result频率/入射角25MHz /40°20MHz /25°18MHz /25°线切糟深m m正面db反面db正面db反面db正面db反面db0122832383747380144440403548380164646413954420184649404052441474542405349112494841405252114474647456157116505151516561根据表3数据绘制,如图6—图8所示.横坐标为槽深和孔深(mm )、纵坐标为波幅高度(bd).图6 8M z 5°能流分部图F 6 y f 8M z 5°721何清等:薄壁焊缝的超声板波检测方法研究1.H 2ig .Ene rg l o w d istribu ti o n cha rt 1.H 2图7 2.0MHz 25°能流分部图F ig .7 Ene rgy fl o w distributi on cha rt 2.0MHz 25°图8 2.5MHz 40°能流分部图Fig .8 Ene rgy fl o w distributi on cha rt 2.5MHz 40°从分布图中可知:不同角度的探头能流分布不同,有些在板的两表面能量较强、中心能量较弱;有些在板的两表面较弱、中心能量较强,为了保证在检测过程中的不漏检,此角度的探头不可采用.因此在选择探头角度时,要选择板的两表面和中心能量都较强的探头角度,做为最佳入射角.通过能流分别试验,对产品直焊缝的超声板波检测采用的最佳入射角为f =2.5MHz 、а=40°,并采用纵、横两个方向检测.在试验过程采用对比试验的方法,首先用超声板波法对30根薄壁管的直焊缝进行100%检测,对有缺陷的地方做好标记,其次再用射线法对原30根薄壁管进行100%检测.对比结果两者完全一致.3 结论通过以上论述,采用超声波板波法来对薄板焊缝进行检测是完全可行和可靠的.目前已采用超声波板波法对1000多件产品的直焊缝进行100%在线检测.从检测结果看,从未发现漏检.因此超声波板波法检测薄壁管直焊缝是完全满足产品质量要求的,是可行有效的检测手段,并适用于在线批量生产检测.821应用基础与工程科学学报参考文献[1] 李家伟,陈积懋.无损检测手册[M ].北京:机械工业出版社,2002L i J i awei,Chin J i mao.No l oss checking m anual[M ].Beijing:M achine I ndustry Publis h i ng C omp any,2002[2] 王文忠,王小艾.无损检测标准应用手册[M ].昆明:云南科技出版社,2003Wang Wenzhong,Wang Xiaoai .No l o ss check i ng st andard a pp licat ed m anual [M ].Kunm i ng:Techonology Publishing C omp any of Yun Nan,2003Res earch on Ultra son i c Pl a te Testi n gof Th i n 2w a llW el ded SeamHE Q ing, CHE N G uoguang, TI A N Xiaoli(Depart m ent of Mechantroni c Engi neeri ng,North University of China,Taiyuan 030051,China )Abstra ctA i m at the p r oble m of inter na l quality te sting of high 2pressur e thin 2wall welded steel cylinder p i pe workpiece,the advantagesof the method of using ultrasonic plate wave are obtainedthr ough the c omparis on of five gener a l nondestructive testing m ethods by the paper .The theory 、characteristics 、the r e lati on bet ween ve l ocity and incidence angle 、the ener gy flo w distribution of mode ar e given in this paper .I n addition,ene r gy flow distributi on chart is also plotted .Taking an exa mple of the te sting of high 2pressur e thin 2wall welded steel cylinder pipe,field tests are m ade and the r e liability of plate wave testing is affir med by X 2r ay testing r epetition measure ment .Comparing the conclusi on of experi ment is to survey that the internal defects of welded sea m of high 2p r essur e thin 2wa ll we lded steel cylinde r p i pe can be f ound effic iently thr ough the m ethod of ultr a s onic p late wave which also can be used to r apid online te sting .Ther ef or e,thism ethod takes on br oad application p r ospect .Keyword s:ultrasonic testing;plate wave;thin 2wall;steel cylinder p i pe921何清等:薄壁焊缝的超声板波检测方法研究。
小径薄壁管焊接接头超声波探伤方法探讨

小径薄壁管焊接接头超声波探伤方法探讨摘要:针对小直径薄壁钢管焊缝的超声检测,提出了以焊缝的普通根波和管壁反射波为参照波,对比判断焊缝的缺陷,并对其进行了分析。
关键词:变形波;超声波探伤;比较法1小径管对接焊缝超声波探伤所具有的特点1.1较小直径的管道具有较薄的管壁和较宽的焊缝从电力部发布的工业标准(主要是《电力建设施工及验收技术规范》)的要求可以看出,一般小直径管焊缝比管壁厚宽2-3倍,且常规焊接缝无法实现,如,小直径管壁厚4mm,焊接缝宽12mm。
由于其具有较高的尺寸精度要求,因此必须采用超声波探伤技术来完成对管道焊缝质量的控制。
按常规超声检测方法进行,利用一次波对焊缝根部缺陷进行了探测,那么探头入射角β正切值就会介于2.7-3.2之间,很难在焊缝的中部,中部、上部分缺陷得到了有效鉴定,很容易引起表面波,继而给缺陷定位与量化带来负面影响。
1.2对超声近声场区域进行有效处理的必要性超声检测时,由于声束近场区轴向最大声压较多,在探测中,一定要把近场区最大压力限制在三个或更大,以确保缺陷的发现。
特别适用于管径较小时,因管壁较厚,这个问题就更为严重了。
本文介绍了通过采用适当大小的换能器来减小近场区内的最大声压和利用声波传播理论进行分析计算而得到的解决方法。
该方法可以使近场区的面积达到最小,是比较行之有效的途径。
1.3在管道内部和外部存在较大的表面声能量损耗而小径管因管径小曲率大,其内、外表面超声波均可出现较明显聚束、发散等现象,应格外加以重视。
对于大直径的管子,则需进行特殊处理才能满足探伤要求。
介绍小直径钢管超声检测专用试片DL—1。
该试片由两个相同厚度的钢板焊接而成。
使用对应圆弧形状,增大接触区域。
2小径管超声波探伤过程中较为常见的技术性问题2.1选择测针超声波检测小直径管接焊缝过程中,要尽可能选择较大探针,为了使声束在所有焊缝截面上都能尽量被扫描。
由于采用了适当的探头位置和较长的时间来探测整个焊缝,所以能够准确地发现焊缝中存在的裂纹等微小缺陷。
薄板超声波探伤
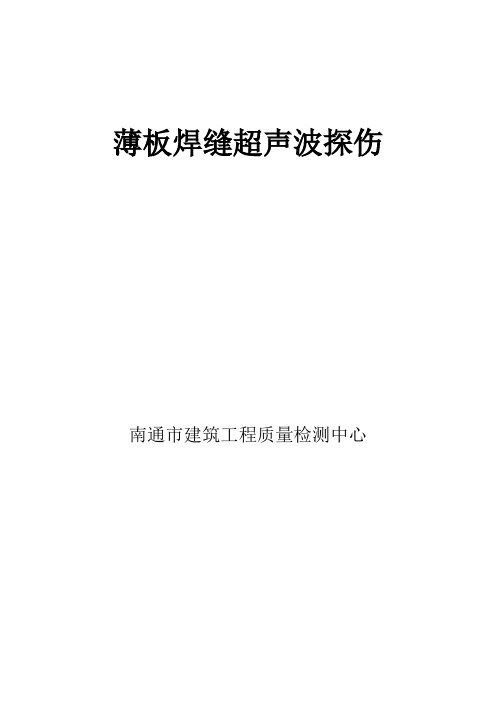
薄板焊缝超声波探伤南通市建筑工程质量检测中心薄板焊缝超声波探伤南通市建筑工程质量检测中心226006[摘要]:为适应轻型钢结构发展的检测需要,本文针对现行国家标准的盲区,讨论了薄板焊缝超声波探伤的可行性,初步研究了相应的探伤方法。
[关键词]:超声波探伤,近场区长度,薄板焊缝,探头,试块现行的GB11345-89《钢焊缝手工超声波探伤方法和探伤结果分级》标准中规定适用范围为“母材厚度不小于8mm的铁素体类钢全焊透熔化焊缝的脉冲反射法手工超声波焊缝检验”。
但是随着轻型钢结构地兴起和发展,在现今的钢结构工程中经常会遇到构件母材板厚小于8mm的情况。
在很多地区,建筑工程质量检测机构又未开展X射线探伤的检测项目,对这类薄板(厚度小于8mm的板材,主要是4mm~7mm)焊缝无法进行行之有效地检测。
而即使采用X射线对薄板焊缝进行探伤也存在对人和环境危害大,对裂纹、未熔合等危害性缺陷漏检率高等缺点。
因此研究薄板焊缝超声波探伤的可行性和探伤方法就显得很重要了。
1薄板焊缝超声波探伤的可行性1.1 薄板焊缝不宜进行超声波探伤的理论依据根据声学理论基础,在不考虑介质衰减的情况下,液体介质中超声波波源附近会有由于波的干涉而出现的一系列声压极大极小值的区域,称为超声场的近场区,又叫菲涅耳区。
在近场区进行超声波探伤对定量是不利的,处于声压极小值处的较大缺陷回波可能较低,而处于声压极大值处的较小缺陷回波可能较高,这样就容易引起误判,甚至漏检。
由于薄板焊缝的母材板厚较薄,基本都处于超声场的近场区,因此为避免误判、漏检,薄板焊缝不宜进行超声波探伤。
1.2 实际声场与理想声场的比较理想声场中讨论的是液体介质,波源做活塞振动,辐射连续波等理想条件下的情况。
实际探伤时往往是固体介质,波源非均匀激发,辐射脉冲波的声场,简称实际声场。
在近场区内,实际声场与理想声场存在明显区别。
理想声场轴线上声压存在一系列极大极小值,且极大值为2P 0,极小值为零。
薄板对接焊缝超声波探伤方法的试验
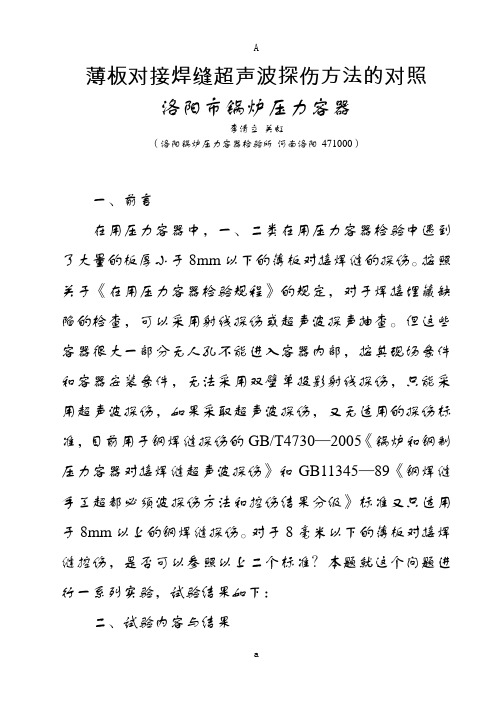
薄板对接焊缝超声波探伤方法的对照洛阳市锅炉压力容器李清立关虹(洛阳锅炉压力容器检验所河南洛阳471000)一、前言在用压力容器中,一、二类在用压力容器检验中遇到了大量的板厚小于8mm以下的薄板对接焊缝的探伤。
按照关于《在用压力容器检验规程》的规定,对于焊接埋藏缺陷的检查,可以采用射线探伤或超声波探声抽查。
但这些容器很大一部分无人孔不能进入容器内部,按其现场条件和容器安装条件,无法采用双壁单投影射线探伤,只能采用超声波探伤,如果采取超声波探伤,又无适用的探伤标准,目前用于钢焊缝探伤的GB/T4730—2005《锅炉和钢制压力容器对接焊缝超声波探伤》和GB11345—89《钢焊缝手工超都必须波探伤方法和控伤结果分级》标准又只适用于8mm以上的钢焊缝探伤。
对于8毫米以下的薄板对接焊缝控伤,是否可以参照以上二个标准?本题就这个问题进行一系列实验,试验结果如下:二、试验内容与结果1、对比试块人工缺陷的选择参照GB/T4730—2005、标准以及ZBE98001—88《常压钢质油罐焊缝超声波探伤》标准,我们制作了板厚为6mm 的薄板试块,人工缺陷为 2×0.5×0.5×20和0.6×300长横槽三种,通过,我们选用了板厚6mm 的2×201)。
用CTS —22型超声波探伤仪。
5P9×9K2探头,制作的距离一波幅曲线。
如图(2)和表(1)。
图(1)表(1)4020 20 40 60 P图(2)2、距离——波幅曲线灵敏度的确定为了使检验8mm以下薄板焊缝时,不离开国家现有标准。
我们参照GB/T4730—2005标准和GB11345—89标准的精神,确定距离——波幅曲线灵敏度,见表(2)表(2)3、缺陷的定位8mm以下的薄板焊缝超声波探伤,在焊板一侧进行探伤时,为了能扫查整个焊缝截面,一般要采用多次反射法,如图(3)所示,根据几何三角形原理,多次反射法缺陷位置的确定可由下式计算。
- 1、下载文档前请自行甄别文档内容的完整性,平台不提供额外的编辑、内容补充、找答案等附加服务。
- 2、"仅部分预览"的文档,不可在线预览部分如存在完整性等问题,可反馈申请退款(可完整预览的文档不适用该条件!)。
- 3、如文档侵犯您的权益,请联系客服反馈,我们会尽快为您处理(人工客服工作时间:9:00-18:30)。
薄板对接焊缝超声波探伤方法的对照
洛阳市锅炉压力容器
李清立关虹
(洛阳锅炉压力容器检验所河南洛阳471000)
一、前言
在用压力容器中,一、二类在用压力容器检验中遇到了大量的板厚小于8mm以下的薄板对接焊缝的探伤。
按照关于《在用压力容器检验规程》的规定,对于焊接埋藏缺陷的检查,可以采用射线探伤或超声波探声抽查。
但这些容器很大一部分无人孔不能进入容器内部,按其现场条件和容器安装条件,无法采用双壁单投影射线探伤,只能采用超声波探伤,如果采取超声波探伤,又无适用的探伤标准,目前用于钢焊缝探伤的GB/T4730—2005《锅炉和钢制压力容器对接焊缝超声波探伤》和GB11345—89《钢焊缝手工超都必须波探伤方法和控伤结果分级》标准又只适用于8mm以上的钢焊缝探伤。
对于8毫米以下的薄板对接焊缝控伤,是否可以参照以上二个标准?本题就这个问题进行一系列实验,试验结果如下:
二、试验内容与结果
1、对比试块人工缺陷的选择
参照GB/T4730—2005、标准以及ZBE98001—88《常压钢质油罐焊缝超声波探伤》标准,我们制作了板厚为6mm 的薄板试块,人工缺陷为 2×长横孔,0.5×0.5×20和0.6×300长横槽三种,通过,我们选用了板厚6mm 的 2长横孔的薄板试块。
见图(1)。
用CTS —22型超声波探伤仪。
5P9×9K2探头,制作的距离一波幅曲线。
如图(2)和表(1)。
2×20 b=15
402
0 20 40 60 P
图(2)
2、距离——波幅曲线灵敏度的确定
为了使检验8mm以下薄板焊缝时,不离开国家现有标准。
我们参照GB/T4730—2005标准和GB11345—89标准的精神,确定距离——波幅曲线灵敏度,见表(2)
表(2)
3、缺陷的定位
8mm以下的薄板焊缝超声波探伤,在焊板一侧进行探伤时,为了能扫查整个焊缝截面,一般要采用多次反射法,如图(3)所示,根据几何三角形原理,多次反射法缺陷位置的确定可由下式计算。
P=(no—d)k (1)
P
d= no —(2)
k
P——为水平距离。
Mm
式中:
O——钢板厚度。
Mm
K——探头K值
d——缺陷离探伤面的距离。
mm
n——多次反射的次数。
n>1。
且为偶数。
图(3)
当多次反射次数n>1且为奇数时,缺陷深度的计算应用下式:
P
d= o —(n o —(3)
k
缺陷定位试验。
我们制作了4mm和6mm二种板厚不同深度的2长横孔试块,还制作了4mm和6mm二种板
厚,并含根部未焊透的焊板试块。
试验采用了CTS—22型超声波探伤仪,探头为5P9×9K2,利用CSK—1B试块探伤仪和探头各参数,利用CSK —ⅢA试块调节扫插线,用板厚o=6mm×20的对比试
块制作探伤用的距离——波幅曲线,见表(3)和图(4)。
用图(4)所示的距离—波幅曲线调节探伤灵敏度。
对二种
2×20长横孔试块和二种板厚的对接焊
缝的未焊透进行探测定位结果见表(4)和表(5)。
表(3)
O=6mm 2×20
5P9×9K2 6=15
dB
60
2—6 dB
40
2—12 dB
20 2—18 dB
0 20 40 60 P(mm)
图(4)
表(4)(mm)
表(5)(mm)
4、缺陷定量
对4mm、6mm两种焊板中的根部未焊透气孔进行了定量试验,先采用X射线拍片探伤底片见图(5)和图(6),然后按图(4)距离——波幅曲线调节探伤灵敏度,进行超都必须波探伤缺陷幅度的测定,将探头置于出现最大反射
波高的位置时,读出该幅度的分贝值。
缺陷指示长度采用6dB法测定。
其结果见表(6)。
125mm 15 2 7mm
1# 4# 3# 2#
图(5)O=6mm 大量板射线底片缺陷分析
7mm 77mm
2# 1#
图(6)O=4mm 大量板射线底片缺陷分析
表(6)(mm)
焊板
厚度O 缺陷性质
射线探伤结果超声探伤结果
缺陷高度缺陷长度幅值(dB)指示长度
6 1#未焊透
2#未焊透
3#气孔
4#气孔
1~2
2
1.5
125
7
50—60
64
44
44
124
6
4
1#未焊透
2#未焊透1~2
0.8—1.2
77
7
50~60
46
76
6
三、结束语:
1、通过以上试验,利用厚度为6mm2×20的长横
孔的薄板试验,参照GB/T4730—2005标准距离—波幅曲线灵敏度,对板厚为8mm以下的薄板(厚度)焊缝进行超都必须波探伤是可行的。
2、6mm薄板试块使用方便,重量轻,适用于高空,制作容易,一次调节可用于多种厚度焊接,定位误差小,本试验误差为1mm左右。
3、 1.5mm以上气孔和0.8mm
深以上未焊透的反射波达到和超过了定量线。