滚齿误差及原因
齿轮加工误差产生的原因和消除方法

螺旋线偏差的说明:1、螺旋线偏差的评定范围Lβ除另有规定外,系指在轮齿两端处各减去下面两个数值中较小的一个以后的“齿线长度”,此两个数值为5%的齿宽或等于一个模数的长度。
2、使偏差量增加的偏向齿体外的正偏差,必须计算入误差值。
3、除另有规定外,对于负偏差,其允许值为评定范围Lβ规定的公差的3倍数。
4、螺旋线偏差是在齿轮端面基圆切线方向测量,如果在齿面的法向测量,应将测量值除以cosβb后再与公差值比较。
5、被测齿面的平均螺旋线是设计螺旋线的纵坐标减去一条斜直线的纵坐标后得到的曲线。
这条斜直线使得在评定范围内,实际螺旋线对平均螺旋线偏差的平方和最小。
因此,平均螺旋线的位置和倾斜可以用“最小二乘法”求得。
6、除另有规定外,螺旋线偏差应在沿齿轮圆周均布的不少于三个轮齿的两侧面的齿高中部进行测量。
齿廓(齿形)的说明:1、齿廓偏差在齿轮端平面内且垂直于渐开线齿廓的方向计算,若在齿面的法向测量,应将测量值除以cosβb后再与公差数值进行比较。
2、设计齿廓系指符合设计规定的齿廓,当物其他限定时,是指端面齿廓。
设计齿廓可以设备修正的理论渐开线,包括修缘齿形。
凸齿形等。
3、被测齿面的平均齿廓是设计齿廓线的纵坐标减去一条斜直线的纵坐标后得到的曲线。
这条斜直线使得在齿廓评定范围内,实际齿廓线对平均齿廓线偏差的平方和为最小。
因此,平均齿廓线的位置和倾斜可以用“最小二乘法”求得。
4、齿廓评定范围La系指可用长度L AE中的一部分,除另有规定,其长度等于从E点开始延伸刀有效长度L AE的92%。
对于L AE剩下的8%为靠近齿顶处的L AE与La之差。
在评定齿廓总偏差和齿廓形状偏差时,应遵守下述规则:①、使偏差量增加的偏向齿体外的正偏差,必须计算入误差值。
②、除另有规定外,对于负偏差,其允许值为评定范围La规定的公差的3倍数。
5、有效长度L AE系指可用长度对应于有效齿廓的那部分。
对于齿顶,其有与可用长度同样的限定(A点)。
插齿滚齿剃齿的误差分析

★★★★★插齿★★★★★插齿误差产生原因及消除方法见表01
表01 插齿时产生误差的原因与消除方法
(续表01)
★★★★★滚齿★★★★★滚齿误差产生原因及消除方法见表02
表02 滚齿误差产生原因及消除方法
(续表02)
★★★★★剃齿★★★★★剃齿轮齿接触的偏差及其修正方法见表03
表03 轮齿接触的偏差及其修正方法
剃齿误差产生原因及其消除方法见表04
表04 剃齿误差产生原因及其消除方法
(续表04)
磨齿
典型磨齿机的磨齿误差和纠正方法如下:
1) 蜗杆砂轮磨齿机(YE7272—AZA):齿形误差(见表30)和齿向误差(表31)。
表30 齿形误差
表31 齿向误差
2)锥面砂轮磨齿机(Y7163、ZSTZ630C2)见表32
表32 锥面砂轮磨齿机的缺陷项目、原因及纠正措施
3)大平面砂轮磨齿机见表33
表33 大平面砂轮磨齿机的缺陷项目
4)蝶形砂轮磨齿机(Y7032A、SD32X、HSS30BC) 表34
表34 蝶形砂轮磨齿机的缺陷项目
锥齿轮加工误差分析
表35 误差原因及消除。
关于齿轮滚齿误差产生的种类及原因分析

角左 右 对称 ,检 测 出的 齿形 图如 图: { 叶 的l 、2 .【 J j 1 是 刀 刃u的
图2
压 力 角 存在 误 差 ;如 果 左 右不 对 称 .检 洲 出 的齿 形 图 像 l 冬 j : { 中 的 1 、2 ,但 齿形 的方 向 是 平 行 的 .9 1 I J 是 刀 县 刀 口的 压 力 角干 ¨ 机I 术
其 检 测 出的 齿 形 图 的 形状 也 不 同 若 是 l 刳s _ 中的 齿 形 } l l l 线 变 成
s 形 ,则 是加 工 中 刀具和 工 件装 夹 部存在 误差
2 . 2形误 差 产 生的 原 因
图2 中1 、2 主 要是 刀具 的压 力角 偏差 较 大
如果 刀具 的压 力
3 4 ;
I 恤
2 O 1 6 年・ 第1 2 期
在 齿轮 制造工 艺 中.保证齿
轮 齿 部 精 度 的 方 法 有 挤 齿 、 滚
齿 、剃 齿 、磨 齿 、珩 齿 、 研齿 等。一般 小模数 齿轮 只能通过滚 齿 的方 法达 到齿 轮精 度要求 在 滚齿过 程 中,由于存在 刀具 、机
刀刃在切削工件时有时有 多切 、有
时有 少 切 .导 致 实 际 齿 形 从 齿 根到
齿顶一段 低于标准渐开线 .一段 高 于标 准渐 开线 ( 见图 3 中3 )。
技 术 创 新
图5 主 要 是 工件 孔 中心 与 工作 台 刚转 中心 不 重合 ,可 通过 齿 形 图 、跳 动 和 双 啮 合 检 测 出 。压 力 角偏 大 的 位 置 是 双啮 合和 齿 跳 的 高 点 、压 力 角偏 小 的 位 置是 双 啮 合 和 齿 跳 的 低 点 ;且 双 啮 合 和齿 跳 的 高 、低 点 误 差 大 ( 垂 直 中心 线 的 上 下位 置 齿 形 ),
滚齿误差及原因

滚齿误差及原因分析对策图表王津盛目录一、齿距误差 (2)相邻齿距误差大单个齿距误差大整个齿距误差大二、齿形误差 (5)各齿齿形误差形式一致窜刀后齿形变化左右侧上齿形形状不一致但同侧齿形形状一致差各齿齿形形状不同三、齿向误差 (12)单侧齿向多切锥度齿向两侧齿廓多切螺线角误差各齿齿向不一致两侧齿向中凹齿向波动齿面单个凹坑走刀纹不均匀台阶齿向四、径向跳动 (24)工件一圈有一次峰值工件一圈有二次峰值五、齿面粗糙度 (26)撕裂振纹单齿面粗糙六、齿厚 (27)每个齿轮之间变化周期变化随时间变化合制加工上下件不一致一.齿距误差当产生齿距误差时应该如何去分析图1 齿距误差的类型A、两相邻齿距误差大(采用多头滚刀)两相邻齿距间产生变动量大的原因见表1。
当被加工齿轮的齿数与多头滚刀的头数成倍数时或用多头滚刀进行高速滚削加工时,在用多头滚刀滚齿时会产生这类误差;表1B、两相邻齿距间变动量大(采用单头滚刀)C、单个齿距变动量大单头滚刀滚削下齿距变动量大的原因见表2。
若是齿廓的两侧左右齿面齿距变动量均大,则有可能是工作台主轴回转精度差。
表2D、全部齿距变动量大表3*注意:当因为大走刀量造成齿距超差时,考核方法应排除其影响,见有关资料介绍。
二、齿形误差产生齿形误差的缘由如下:a、滚刀的齿形误差b、滚刀一转螺旋线齿距累积误差c、滚刀安装偏心d、齿形棱度作为误差出现图2 齿形误差的形式齿顶抬高 A 、 每个齿的齿形相同(a ) 齿顶抬高 (b ) 齿顶低头 (c ) 靠近PCD 处中凹(d ) 靠近A 、B 、C 、齿的齿形均一致表4 分 类 滚刀精度低a 、滚刀精度太低;b 、滚刀切削刃刃磨不正确;B、滚刀窜刀后齿形改变(每个齿的齿形均相同)窜刀后齿形发生变化表5分类原滚刀精度低a、滚刀精度低b、滚刀切削刃刃磨不正确C、每个齿的左右齿廓上的齿形不同(同一齿侧方向上的齿形一致)通常把这种误差考虑为A类,已在前面叙述过。
倘若状况较严重时,可使用下表表6分类原屑瘤a、因切屑瘤形成的新切削刃造成齿面撕裂顺滚直齿时:多头滚刀顺滚时:撕裂现象出现滚刀安装精度低a、刀架回转角调整不当;b、滚刀切削刃刃磨不当a、基准齿轮侧隙过大D、每个齿的齿形均不同(当滚削齿数同多头滚刀的头数成倍数关系时)这种类型的齿形误差产生的原因与本节开头A内容的相同即使滚削齿轮的齿数与滚刀头数不成倍数关系,在大轴向走刀下,也会出现。
滚齿时产生缺陷的原因与消除方法

4、对鱼鳞:采用适当的预先热处理方法,若对齿面为最终加工时,必须避免;若后面还有剃磨等工艺时,可以不避免
控制工件两端面的平行度或安装时的径向跳动量齿圈跳动超差主要是在安装工件时它的内孔中心对于轴齿轮就是轴颈中心与工作台的回转中心不重合或偏心太大
滚齿时产生缺陷的原因与消除方法
缺陷名称
产生原因
消除办法
齿数不正确
1、机床:分齿挂轮调整的不正确;滚刀与工件的转向不配合。
2、刀具:滚刀的模数、头数、螺旋线方向等选择不当;
3、工件:齿轮毛坯尺寸不对
1、重新调整分齿挂轮与介轮;
2、选择合适的滚刀;
3、更换齿轮毛坯
齿向误差超差
主要是滚齿机刀架的垂直走刀方向与齿坯内孔中心线方向偏离,对于斜齿轮还要加上附加转动不正确的原因。归纳为:
1、机床:垂直走刀导轨与工作台的轴心线不平行;上下顶尖不同心;工作台有轴向窜动或径向跳动;分齿蜗杆、蜗轮有间隙或蜗轮副传动有周期性误差;走刀传动丝杆螺距有误差;分齿挂轮调整误差太大;差动挂轮不对,计算误差太大或刀架转动不对(加工斜齿轮时);
1、机床:工作台径向跳动;心轴对工作台回转中心不重合或长期使用磨损;心轴本身摆差太大;使用顶针加工时,上下顶针有偏摆或松动;夹具定位端面与工作台回转中心不垂直;垫圈两平面不平行或夹紧螺母端面对螺纹中心不垂直;
2、工件:内孔定心时,由于内孔与心轴配合间隙过大,引起安装偏心;外径定心时,由于外圆本身的径向跳动或椭圆度较大;工件夹紧刚性差
3、振纹:机床刀具、工件系统的好坏直接影响着振动发生的强弱(如滚刀安装不好,刃磨质量不好,刀轴尾支承间隙过大,齿坯的装夹等);
滚齿机加工原理及误差分析
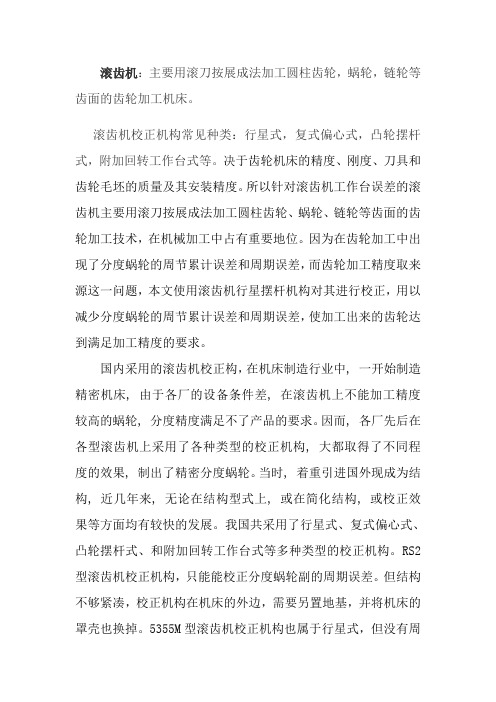
滚齿机:主要用滚刀按展成法加工圆柱齿轮,蜗轮,链轮等齿面的齿轮加工机床。
滚齿机校正机构常见种类:行星式,复式偏心式,凸轮摆杆式,附加回转工作台式等。
决于齿轮机床的精度、刚度、刀具和齿轮毛坯的质量及其安装精度。
所以针对滚齿机工作台误差的滚齿机主要用滚刀按展成法加工圆柱齿轮、蜗轮、链轮等齿面的齿轮加工技术,在机械加工中占有重要地位。
因为在齿轮加工中出现了分度蜗轮的周节累计误差和周期误差,而齿轮加工精度取来源这一问题,本文使用滚齿机行星摆杆机构对其进行校正,用以减少分度蜗轮的周节累计误差和周期误差,使加工出来的齿轮达到满足加工精度的要求。
国内采用的滚齿机校正构,在机床制造行业中, 一开始制造精密机床, 由于各厂的设备条件差, 在滚齿机上不能加工精度较高的蜗轮, 分度精度满足不了产品的要求。
因而, 各厂先后在各型滚齿机上采用了各种类型的校正机构, 大都取得了不同程度的效果, 制出了精密分度蜗轮。
当时, 着重引进国外现成为结构, 近几年来, 无论在结构型式上, 或在简化结构, 或校正效果等方面均有较快的发展。
我国共采用了行星式、复式偏心式、凸轮摆杆式、和附加回转工作台式等多种类型的校正机构。
RS2 型滚齿机校正机构,只能能校正分度蜗轮副的周期误差。
但结构不够紧凑,校正机构在机床的外边,需要另置地基,并将机床的罩壳也换掉。
5355M型滚齿机校正机构也属于行星式,但没有周期误差校正凸轮, 机构是封闭的。
其结构复杂, 构件将近85 种, 使用不方便, 需将机床的双蜗杆传动改成单蜗杆传动, 此时, 必需拆除一根蜗杆。
由于校正机构安装位置不够妥当,使得一部分齿轮外露。
这种结构不太适用于大型滚齿机。
FO-10滚齿机行星式校正机构,该机构有一定的简化, 它省去了四根摆杆和一根长套筒, 结构就比较紧凑一些。
它装在机床分度挂轮箱处, 不需另置地基, 但其构件的种数仍然较多, 达45种, 放大比为0.182毫米每秒。
这种机构的轮廓尺寸较大。
滚齿常见缺陷及解决办法

滚齿机的加工误差分析与修正
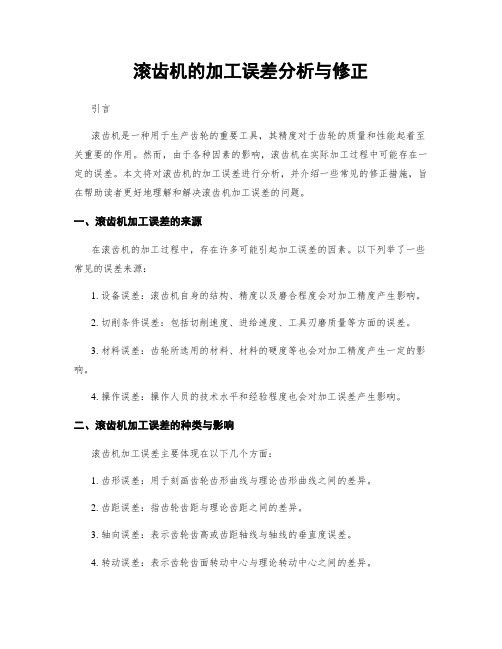
滚齿机的加工误差分析与修正引言滚齿机是一种用于生产齿轮的重要工具,其精度对于齿轮的质量和性能起着至关重要的作用。
然而,由于各种因素的影响,滚齿机在实际加工过程中可能存在一定的误差。
本文将对滚齿机的加工误差进行分析,并介绍一些常见的修正措施,旨在帮助读者更好地理解和解决滚齿机加工误差的问题。
一、滚齿机加工误差的来源在滚齿机的加工过程中,存在许多可能引起加工误差的因素。
以下列举了一些常见的误差来源:1. 设备误差:滚齿机自身的结构、精度以及磨合程度会对加工精度产生影响。
2. 切削条件误差:包括切削速度、进给速度、工具刃磨质量等方面的误差。
3. 材料误差:齿轮所选用的材料、材料的硬度等也会对加工精度产生一定的影响。
4. 操作误差:操作人员的技术水平和经验程度也会对加工误差产生影响。
二、滚齿机加工误差的种类与影响滚齿机加工误差主要体现在以下几个方面:1. 齿形误差:用于刻画齿轮齿形曲线与理论齿形曲线之间的差异。
2. 齿距误差:指齿轮齿距与理论齿距之间的差异。
3. 轴向误差:表示齿轮齿高或齿距轴线与轴线的垂直度误差。
4. 转动误差:表示齿轮齿面转动中心与理论转动中心之间的差异。
这些加工误差在一定程度上会影响齿轮的传动性能和寿命,因此非常值得我们关注和解决。
三、滚齿机加工误差的修正措施为了确保滚齿机加工出的齿轮达到要求的精度,我们可以采取以下一些修正措施:1. 设备维护:定期检查和维护滚齿机的机械部件,保证其正常工作状态和精度。
2. 切削条件调整:优化切削参数,如切削速度、进给速度等,以减小加工误差。
3. 工具选择与刃磨:选择合适的切削刀具,并定期对刀具进行质量检查和刃磨操作,确保刀具的几何精度和尺寸精度。
4. 材料选择:选择适当的齿轮材料,材料的硬度、耐磨性等特性应符合实际使用要求。
5. 操作培训:加强操作人员的培训和技术指导,提高其对滚齿机操作技术和知识的掌握程度。
这些修正措施可以辅助我们降低滚齿机加工误差,提高齿轮的加工质量和性能。
- 1、下载文档前请自行甄别文档内容的完整性,平台不提供额外的编辑、内容补充、找答案等附加服务。
- 2、"仅部分预览"的文档,不可在线预览部分如存在完整性等问题,可反馈申请退款(可完整预览的文档不适用该条件!)。
- 3、如文档侵犯您的权益,请联系客服反馈,我们会尽快为您处理(人工客服工作时间:9:00-18:30)。
滚齿误差及原因
滚齿误差及原因分析对策图表
王津盛
目录
一、齿距误差 (2)
相邻齿距误差大
单个齿距误差大
整个齿距误差大
二、齿形误差 (5)
各齿齿形误差形式一致
窜刀后齿形变化
左右侧上齿形形状不一致但同侧齿形形状一致差
各齿齿形形状不同
三、齿向误差 (12)
单侧齿向多切
锥度齿向
两侧齿廓多切
螺线角误差
各齿齿向不一致
两侧齿向中凹
齿向波动
齿面单个凹坑
走刀纹不均匀
台阶齿向
四、径向跳动 (24)
工件一圈有一次峰值
工件一圈有二次峰值
五、齿面粗糙度 (26)
撕裂
振纹
单齿面粗糙
六、齿厚 (27)
每个齿轮之间变化
周期变化
随时间变化
合制加工上下件不一致
一.齿距误差
当产生齿距误差时应该如何去分析
图1 齿距误差的类型
A、两相邻齿距误差大(采用多头滚刀)
两相邻齿距间产生变动量大的原因见表1。
当被加工齿轮的齿数与多头滚刀的头数成倍
数
时或用多头滚刀进行高速滚削加工时,在用多头滚刀滚齿时会产生这类误差;
表1
B、两相邻齿距间变动量大(采用单头滚刀)
C、单个齿距变动量大
单头滚刀滚削下齿距变动量大的原因见表2。
若是齿廓的两侧左右齿面齿距变动量均大,则有可能是工作台主轴回转精度差。
表2
D、全部齿距变动量大表3
*注意:
当因为大走刀量造成齿距超差时,考核方法应排除其影响,见有关资料介绍。
二、齿形误差
产生齿形误差的缘由如下:
a、滚刀的齿形误差
b、滚刀一转螺旋线齿距累积误差
c、滚刀安装偏心
d、齿形棱度作为误差出现
图2 齿形误差的形式
A、每个齿的齿形相同
(a)齿顶抬高
(b)齿顶低头
(c)靠近PCD处中凹
齿顶抬高
齿顶低头
(d)
靠近PCD处中凹
A 、B、C、 D齿的齿形均一致
表4
B、滚刀窜刀后齿形改变(每个齿的齿形均相同)A、B、C和D具有同样的齿形
刀后齿形发生变化
表5
C、每个齿的左右齿廓上的齿形不同(同一齿侧方向上的齿形一致)
通常把这种误差考虑为A类,已在前
面叙述过。
倘若状况较严重时,可使用下
表
A、B、C和D齿上
的齿形形状一样。
但各个齿的右侧和左侧齿形却不相同。
表6
D、每个齿的齿形均不同(当滚削齿数同多头滚刀的头数成倍数关系
时)
这种类型的齿形误差产生的原因与本
节开头A内容的相同
用
双头滚刀滚齿时,每隔一个齿的齿形
形
状是相同的
例: A齿和C齿的齿形相同,
齿和D齿的齿形相同,排列下去。
用
3头滚刀滚齿时,每隔两个齿的齿形
是
相同的
例: A齿和D齿的齿形相同,
齿和E齿的齿形相同,排列下去。
即使滚削齿轮的齿数与滚刀头数不成
倍数关系,在大轴向走刀下,也会出现。
图6
E、每个齿的齿形不同(当滚削齿数与滚刀头数不成倍数时)
各个齿的齿形不同的原因见下表。
A 、B、C和D齿上的齿形
均不相同
表7
fu
:加工表面的凹凸差(μ)f:进给率(mm/转)
α: 滚刀压力角(°)
DφPCD:滚刀分度圆直径(mm)
三、齿向误差
本节主要研究各种齿向误差的原因
齿向倾斜不平行
A单侧齿面上多切
部位处齿向倾斜
B 齿向倾斜成
锥形
C两侧齿面上多切部
位处齿向倾斜
D两齿廓上齿向倾
斜方向平行
E 每个齿的齿向
F 两侧齿面上齿
向中凹
G 齿向上出现波浪
H 齿向上有个凹
坑
I 不规则走刀纹
J 阶梯齿向
图5 齿向误差型式
A、单侧齿面上多切部位齿向折线
图5.1.9 多切部分
表8
B、锥度齿向
若在加工起始和结束时的齿厚不相同,就会产生这种齿向误差。
倘若有此误
差发生,则齿轮上的所有齿上均出现类似
的现象
齿轮上的所有齿上出现类
似的现象
图10
表9
C
、 两侧齿面上多切部位齿向折线
图11 表10 分
类
原 因 说 明 优先级
滚刀径向 支承力不
够 a 、 主轴主支撑轴承间隙过大;
b 、 滚刀小支架上的轴承间
隙过大;
1
在两侧齿面多切处上
齿槽变大
D 、 两侧齿面上齿向平行倾斜(螺旋角误差或导程误差)
图12 表11
分 类
原 因 说 明 优先级
工件夹
紧不当
a 、 工件的夹紧力不够
(调整不当或操作
者失误)
b 、 嵌入刃口磨钝(刀口式
夹具)
c 、 上下顶针的夹紧力不够(刀口式夹具)
1
作用在a 、 工件顶尖孔里有粘着
1
或
E、齿轮上每齿齿向不一致
图5.1.13
表12
图13
表12
F、两侧齿面上齿向中凹
图14
表13
分类原因说
明
优先级
尾架薄弱a、尾架轴承间隙过大(活
动顶尖)
(因轴承的损坏等造成
尾架起动条件不匹配)
1
G 、齿向波动
波动 图15 表14 分类
原 因
说 明 优先级 传动
链 a 、 滚刀与主电机之间的传动
链上存在偏心; (侧隙不匹配) b 、 最后一级传动齿轮上的侧
隙不匹配;
c 、 工作台基准大齿轮与小齿
1
H、齿向上单个凹坑
凹坑
齿向
图16
表15
分类原因说
明
优先级
夹铁屑a、逆滚时滚刀里面卡
入铁屑;
1
滚刀刀尖崩刃a、崩刃的碎片嵌入到
工件齿面上;
1
轴向滑动a、轴向滑动面或轴向 1
I 、刀具走刀纹不均匀
轴向进给量
不均匀刀纹
正常 图17 表16 分
类
原 因
说 明 优先级
尾架顶
尖
a 、 尾架轴承间隙过大(活动顶尖);
b 、 推力轴承损坏 1
工作台轴
承 a 、 工作台轴承允差过大; b 、 工作台推力轴承间隙过
1
J 、 台阶齿向
台阶 图18 表17 分
类
原 因
说 明
优先级 滚刀主
轴侧隙
a 、 最后一级传动齿轮侧隙过大;
b 、 滚刀芯轴上的键存在间隙; 1
滚刀主
轴间隙
a 、 推力轴承预载力不够;
b 、 推力轴承受损;
c 、 滚刀窜刀滑板夹紧力不够;
2
轴向镶
条
a、轴向镶条间隙过大;
b、刀架滑板平衡油缸出故障;
2 传动链
a、滚刀驱动齿轮侧隙与工
作台基准齿轮的侧隙不匹配
b、切削起始点位置设置不
当;
3
工件形
状
a、工件形状不适合;
b、工件刚性不够;
c、工件中心支架压紧力不均
匀
3
刀刃夹
具刃口
a、刀口拨爪打滑(刀刃式夹
具);
3 工作台a、推力轴承座不稳定; 3 K、走刀波纹度
f:工件每转走刀量mm/rev
D H:滚刀外径mm
β:工件螺旋角°。