车间常见质量问题与解决方法
车间的问题与解决建议
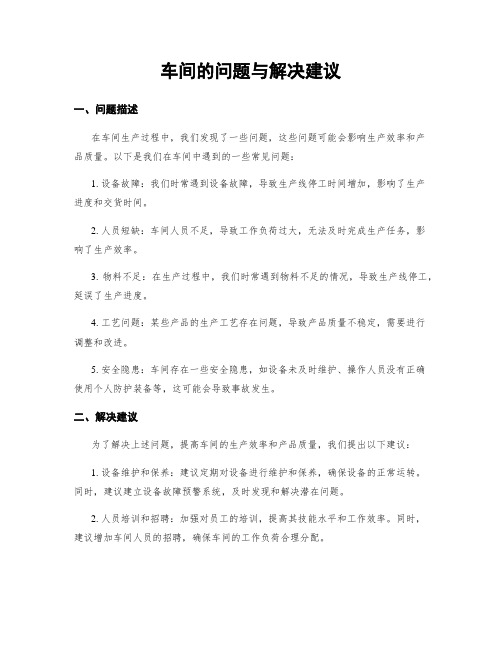
车间的问题与解决建议一、问题描述在车间生产过程中,我们发现了一些问题,这些问题可能会影响生产效率和产品质量。
以下是我们在车间中遇到的一些常见问题:1. 设备故障:我们时常遇到设备故障,导致生产线停工时间增加,影响了生产进度和交货时间。
2. 人员短缺:车间人员不足,导致工作负荷过大,无法及时完成生产任务,影响了生产效率。
3. 物料不足:在生产过程中,我们时常遇到物料不足的情况,导致生产线停工,延误了生产进度。
4. 工艺问题:某些产品的生产工艺存在问题,导致产品质量不稳定,需要进行调整和改进。
5. 安全隐患:车间存在一些安全隐患,如设备未及时维护、操作人员没有正确使用个人防护装备等,这可能会导致事故发生。
二、解决建议为了解决上述问题,提高车间的生产效率和产品质量,我们提出以下建议:1. 设备维护和保养:建议定期对设备进行维护和保养,确保设备的正常运转。
同时,建议建立设备故障预警系统,及时发现和解决潜在问题。
2. 人员培训和招聘:加强对员工的培训,提高其技能水平和工作效率。
同时,建议增加车间人员的招聘,确保车间的工作负荷合理分配。
3. 物料管理:建议建立健全的物料管理体系,确保物料的供应充足。
可以与供应商建立长期合作关系,提前预定所需物料,以避免物料短缺的情况发生。
4. 工艺改进:对存在问题的产品生产工艺进行分析和改进,确保产品的质量稳定。
可以借鉴其他企业的成功经验,引进先进的生产工艺和设备。
5. 安全管理:加强车间的安全管理,制定并执行相关的安全操作规程。
定期组织安全培训,提高员工的安全意识和操作技能。
同时,建议建立安全巡检制度,及时发现并解决安全隐患。
三、预期效果通过采取上述解决建议,我们预期能够达到以下效果:1. 提高生产效率:设备维护和保养、人员培训和招聘等措施能够减少停工时间,提高生产效率,保证生产进度的顺利进行。
2. 提升产品质量:通过工艺改进和物料管理的措施,能够提高产品的质量稳定性,减少次品率,满足客户的需求。
车间的问题与解决建议
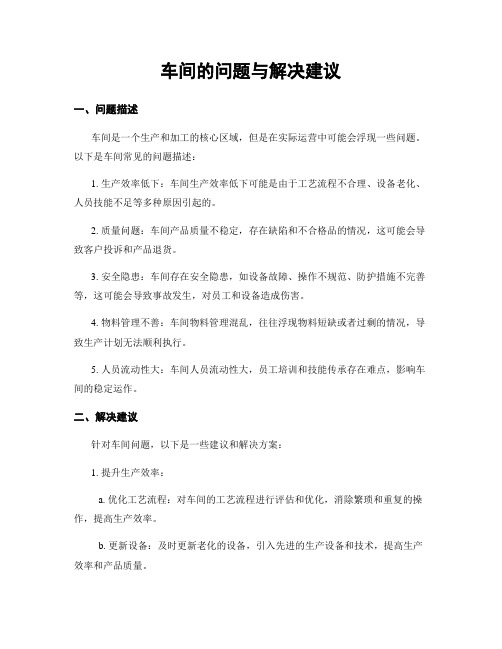
车间的问题与解决建议一、问题描述车间是一个生产和加工的核心区域,但是在实际运营中可能会浮现一些问题。
以下是车间常见的问题描述:1. 生产效率低下:车间生产效率低下可能是由于工艺流程不合理、设备老化、人员技能不足等多种原因引起的。
2. 质量问题:车间产品质量不稳定,存在缺陷和不合格品的情况,这可能会导致客户投诉和产品退货。
3. 安全隐患:车间存在安全隐患,如设备故障、操作不规范、防护措施不完善等,这可能会导致事故发生,对员工和设备造成伤害。
4. 物料管理不善:车间物料管理混乱,往往浮现物料短缺或者过剩的情况,导致生产计划无法顺利执行。
5. 人员流动性大:车间人员流动性大,员工培训和技能传承存在难点,影响车间的稳定运作。
二、解决建议针对车间问题,以下是一些建议和解决方案:1. 提升生产效率:a. 优化工艺流程:对车间的工艺流程进行评估和优化,消除繁琐和重复的操作,提高生产效率。
b. 更新设备:及时更新老化的设备,引入先进的生产设备和技术,提高生产效率和产品质量。
c. 培训员工:加强员工培训,提升技能水平,提高工作效率和质量。
2. 提高产品质量:a. 强化质量控制:建立完善的质量控制体系,从原材料采购到生产过程的每一个环节都要进行严格的质量控制。
b. 增加检测设备:引入更多的检测设备,提高产品的检测准确性和稳定性,确保产品质量符合标准。
3. 加强安全管理:a. 安全培训:加强员工的安全培训,提高员工的安全意识和操作规范性。
b. 安全设施完善:完善车间的安全设施,确保设备正常运行和员工的人身安全。
c. 定期检查维护:定期对设备进行检查和维护,确保设备的安全性和可靠性。
4. 改进物料管理:a. 建立物料管理系统:建立物料管理系统,实现物料的准确统计、库存管理和供应链协同。
b. 优化供应链:与供应商建立良好的合作关系,确保物料供应的及时性和稳定性。
5. 稳定人员队伍:a. 建立培训计划:制定员工培训计划,确保新员工快速适应工作,老员工能够持续提升技能。
车间的问题与解决建议

车间的问题与解决建议一、问题描述车间是生产过程中的重要环节,但在实际操作中可能会遇到一些问题。
以下是车间常见的问题描述:1. 生产效率低下:车间生产效率不高,无法满足客户需求,导致交货延迟和订单滞留。
2. 质量问题:车间产品存在质量问题,包括产品不合格、损坏和缺陷等,给企业声誉和客户满意度带来负面影响。
3. 安全隐患:车间存在安全隐患,如设备不安全、操作不规范等,容易导致事故和人员伤害。
4. 物料管理不善:车间物料管理不规范,导致物料丢失、过期和浪费,增加了成本和生产延误。
5. 人员流动率高:车间人员流动率高,员工稳定性差,影响团队协作和生产稳定性。
二、解决建议为了解决车间存在的问题,以下是一些建议:1. 提高生产效率:a. 优化生产流程:重新评估生产流程,找出瓶颈环节,进行改善和优化,提高生产效率。
b. 自动化设备:引入自动化设备和机器人技术,减少人工操作,提高生产效率和质量。
c. 培训员工:提供培训机会,提升员工技能和操作水平,减少操作失误和生产延误。
2. 提升质量控制:a. 强化质检流程:建立完善的质检流程,严格把控产品质量,确保产品符合标准和客户要求。
b. 增加质检设备:引入先进的质检设备,提高产品质量检测的准确性和效率。
c. 建立质量意识:加强员工质量意识培养,通过培训和奖惩机制激励员工对质量的重视。
3. 加强安全管理:a. 安全培训:定期进行安全培训,提高员工的安全意识和操作规范。
b. 安全设备更新:定期检修和更新设备,确保设备安全可靠,减少事故风险。
c. 设立安全巡检制度:建立安全巡检制度,定期检查车间安全隐患,及时整改。
4. 改善物料管理:a. 建立物料管理制度:制定严格的物料管理制度,包括采购、入库、出库和库存管理等环节,减少物料损失和浪费。
b. 引入物料追溯系统:使用物料追溯系统,追踪物料流向,提高物料管理的可视化和精细化程度。
5. 提高员工稳定性:a. 建立激励机制:制定激励政策,包括薪酬福利、培训机会和晋升通道等,提高员工满意度和稳定性。
工厂生产过程中的常见问题及解决方法
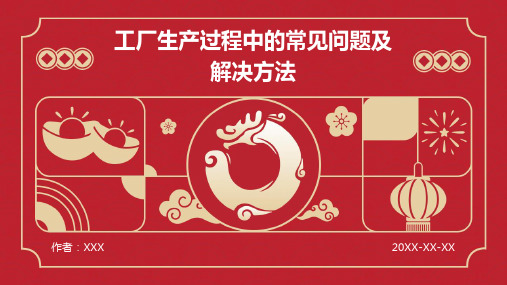
建立完善的质量检测体系,及时处理质量问题
总结词
确保产品质量
详细描述
建立完善的质量检测体系,对原材料、半成品和成品进 行严格的质量检测。采用统计过程控制(SPC)等工具 ,及时发现并处理质量问题。对质量数据进行追溯和分 析,找出潜在问题并采取改进措施。
采用新技术新工艺,降低原材料及能源消耗成本
总结词:降低成本
详细描述
通过对生产流程进行详细分析,可以发现哪些环节存在瓶颈,如物料供应、设备运转、人员操作等,针对这些瓶 颈制定相应的优化措施,可以提高生产效率。
设备运转效率低下
总结词
设备运转效率低下会直接影响生产效率和产品质量。
详细描述
设备老化、维护不当、故障频繁等问题都会导致设备运转效率低下,为了解决 这一问题,需要定期对设备进行维护和保养,及时更换老化部件,提高设备运 转效率。
噪音是工厂车间中常见的污染问题,长期暴露在噪音污染环境下会给员
工的身心健康带来严重影响。
02 03
详细描述
工厂车间的机械设备运行时会产生噪音,长期暴露在这种环境下会对员 工的听力造成损害,同时还会引起心脑血管疾病、神经系统疾病等健康 问题。
解决方法
采用低噪音设备、对设备进行定期维护和润滑、提高工厂布局合理性等 措施来降低车间噪音污染。此外,还可以为员工配备耳塞、耳机等个人 防护用品。
人员操作不熟练
总结词
人员操作不熟练会导致生产效率低下和产品质量不稳定。
详细描述
员工技能培训不足、操作不规范等问题都会导致人员操作不 熟练,为了解决这一问题,需要加强员工技能培训,制定操 作规范,提高员工操作熟练度和产品质量稳定性。
02 产品质量问题
CHAPTER
产品不良率较高
车间的问题与解决建议
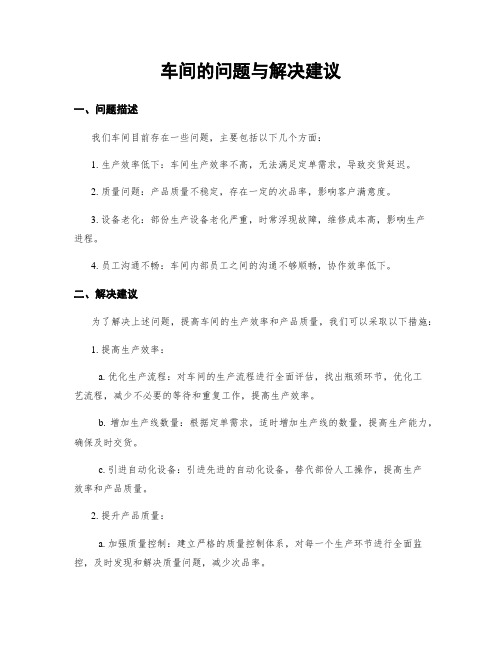
车间的问题与解决建议一、问题描述我们车间目前存在一些问题,主要包括以下几个方面:1. 生产效率低下:车间生产效率不高,无法满足定单需求,导致交货延迟。
2. 质量问题:产品质量不稳定,存在一定的次品率,影响客户满意度。
3. 设备老化:部份生产设备老化严重,时常浮现故障,维修成本高,影响生产进程。
4. 员工沟通不畅:车间内部员工之间的沟通不够顺畅,协作效率低下。
二、解决建议为了解决上述问题,提高车间的生产效率和产品质量,我们可以采取以下措施:1. 提高生产效率:a. 优化生产流程:对车间的生产流程进行全面评估,找出瓶颈环节,优化工艺流程,减少不必要的等待和重复工作,提高生产效率。
b. 增加生产线数量:根据定单需求,适时增加生产线的数量,提高生产能力,确保及时交货。
c. 引进自动化设备:引进先进的自动化设备,替代部份人工操作,提高生产效率和产品质量。
2. 提升产品质量:a. 加强质量控制:建立严格的质量控制体系,对每一个生产环节进行全面监控,及时发现和解决质量问题,减少次品率。
b. 增加员工培训:加强对员工的培训,提高他们的技能水平和质量意识,确保产品符合客户要求。
c. 引进质量管理工具:采用先进的质量管理工具,如六西格玛、PDCA等,提升质量管理水平,持续改进产品质量。
3. 更新设备:a. 定期维护保养:对现有设备进行定期维护保养,延长设备寿命,减少故障发生率。
b. 替换老化设备:根据设备的使用年限和性能状况,适时替换老化严重的设备,提高生产效率和稳定性。
c. 引进新技术设备:关注行业最新技术发展,适时引进新技术设备,提高生产效率和产品质量。
4. 加强员工沟通与协作:a. 建立沟通渠道:建立一个有效的沟通渠道,使员工能够及时交流信息和解决问题。
b. 增加团队建设活动:组织定期的团队建设活动,增强员工之间的团队合作意识和沟通能力。
c. 建立奖惩机制:建立奖惩机制,激励员工积极参预团队合作,提高协作效率。
车间的问题与解决建议
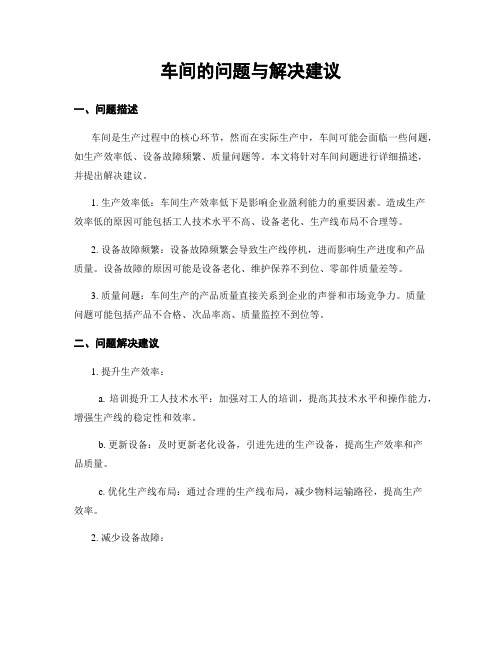
车间的问题与解决建议一、问题描述车间是生产过程中的核心环节,然而在实际生产中,车间可能会面临一些问题,如生产效率低、设备故障频繁、质量问题等。
本文将针对车间问题进行详细描述,并提出解决建议。
1. 生产效率低:车间生产效率低下是影响企业盈利能力的重要因素。
造成生产效率低的原因可能包括工人技术水平不高、设备老化、生产线布局不合理等。
2. 设备故障频繁:设备故障频繁会导致生产线停机,进而影响生产进度和产品质量。
设备故障的原因可能是设备老化、维护保养不到位、零部件质量差等。
3. 质量问题:车间生产的产品质量直接关系到企业的声誉和市场竞争力。
质量问题可能包括产品不合格、次品率高、质量监控不到位等。
二、问题解决建议1. 提升生产效率:a. 培训提升工人技术水平:加强对工人的培训,提高其技术水平和操作能力,增强生产线的稳定性和效率。
b. 更新设备:及时更新老化设备,引进先进的生产设备,提高生产效率和产品质量。
c. 优化生产线布局:通过合理的生产线布局,减少物料运输路径,提高生产效率。
2. 减少设备故障:a. 定期维护保养:建立完善的设备维护保养制度,定期进行设备维护和保养,减少设备故障的发生。
b. 提高零部件质量:与供应商建立良好的合作关系,确保零部件的质量和可靠性。
c. 引进智能设备:引入智能设备和物联网技术,实现设备远程监控和故障预警,提前解决潜在故障。
3. 提升产品质量:a. 加强质量管理:建立完善的质量管理体系,包括质量监控、质量检验和质量反馈等环节,确保产品质量稳定。
b. 优化工艺流程:对生产工艺进行优化,减少生产过程中的变异性,提高产品一致性和稳定性。
c. 加强员工培训:提高员工对产品质量的重视程度,加强质量意识和质量控制能力的培养。
三、总结车间的问题与解决建议主要包括提升生产效率、减少设备故障和提升产品质量三个方面。
通过培训提升工人技术水平、更新设备、优化生产线布局等措施,可以提高生产效率。
定期维护保养设备、提高零部件质量、引进智能设备等措施可以减少设备故障。
车间的问题与解决建议

车间的问题与解决建议一、问题描述车间是生产过程中的核心环节,但在实际操作中往往会遇到一些问题,影响生产效率和质量。
以下是车间常见的问题描述:1. 设备故障频繁:车间中的设备时常浮现故障,导致生产中断,增加了维修成本和生产时间。
2. 员工技能不足:部份员工缺乏必要的技能和培训,导致生产效率低下和质量问题。
3. 物料供应不稳定:车间所需的原材料供应不稳定,导致生产计划无法按时完成。
4. 工艺流程不合理:车间的工艺流程存在一些不合理的环节,导致生产效率低下和浪费。
5. 交流不畅:车间内部的沟通不够顺畅,导致信息传递不及时和误解。
二、解决建议针对上述问题,我提出以下解决建议,以提高车间的生产效率和质量:1. 设备维护和保养:建立定期的设备维护计划,加强设备的保养和检修工作,提高设备的使用寿命和稳定性。
同时,培训维修人员,提高其技术水平,能够快速解决设备故障。
2. 培训和技能提升:建立员工培训计划,包括技术培训、操作规程培训等,提高员工的技能水平和操作规范性。
同时,建立员工技能评估和奖惩机制,激励员工主动学习和提升。
3. 物料供应链管理:与供应商建立稳定的合作关系,确保原材料的供应稳定。
建立物料采购计划和库存管理系统,及时补充和管理物料库存,避免因物料短缺导致的生产中断。
4. 工艺优化和改进:对车间的工艺流程进行全面的优化和改进,消除不必要的环节和浪费,提高生产效率和质量。
引入先进的生产工艺和设备,提高生产线的自动化程度。
5. 沟通和协作:建立车间内部的沟通机制,包括定期召开工作会议、建立信息传递平台等,确保信息的及时传递和共享。
同时,加强团队建设,培养良好的团队合作精神,提高协作效率和工作质量。
以上是我针对车间问题的解决建议,通过解决这些问题,可以提高车间的生产效率和质量,为企业的发展提供有力支持。
希翼以上建议对您有所匡助。
如果还有其他问题,请随时向我提问。
车间的问题与解决建议

车间的问题与解决建议一、问题描述车间是一个重要的生产环节,但在实际运营中常常会遇到一些问题。
以下是车间常见的问题:1. 生产效率低下:车间生产效率低下,无法满足生产计划要求,导致交货延误。
2. 质量问题:车间生产出的产品存在质量问题,包括外观不良、尺寸偏差等,影响产品的市场竞争力。
3. 设备故障:车间设备经常出现故障,导致生产线停机时间增加,影响生产进度。
4. 人员流动性大:车间人员经常离职,新员工上岗需要时间适应,影响生产效率和质量。
二、解决建议为了解决车间存在的问题,提高生产效率和产品质量,以下是一些建议:1. 优化生产流程:对车间的生产流程进行全面分析,找出瓶颈环节和不必要的等待时间,采取措施优化流程,提高生产效率。
可以引入精益生产的方法,通过价值流图等工具找出浪费,进行改进。
2. 加强员工培训:加大对车间员工的培训力度,提高员工的技术水平和操作能力。
培训内容可以包括生产操作规范、设备维护知识等。
通过培训,提高员工的工作质量和效率。
3. 定期设备维护:建立完善的设备维护计划,定期对车间设备进行检修和保养,减少设备故障发生的可能性。
同时,加强设备操作员的培训,提高设备的使用效率和寿命。
4. 激励机制:建立激励机制,对车间员工的工作表现进行评价和奖励。
可以设立绩效考核制度,根据员工的工作表现给予相应的奖励,激发员工的工作积极性和创造力。
5. 加强沟通与协作:加强车间内部各岗位之间的沟通与协作,建立良好的团队合作氛围。
定期组织会议或工作坊,让各岗位之间交流经验和问题,共同解决存在的困难。
6. 引进先进技术和设备:及时引进先进的生产技术和设备,提高生产线的自动化程度和生产效率。
同时,加强与供应商的合作,确保设备的及时维修和更换。
7. 建立质量控制体系:建立完善的质量控制体系,从原材料采购到成品出厂的每个环节都进行严格的质量控制。
可以引入ISO9001等质量管理体系,确保产品质量符合标准要求。
8. 定期进行绩效评估:定期对车间的生产效率和产品质量进行绩效评估,找出问题所在,并采取相应的改进措施。
- 1、下载文档前请自行甄别文档内容的完整性,平台不提供额外的编辑、内容补充、找答案等附加服务。
- 2、"仅部分预览"的文档,不可在线预览部分如存在完整性等问题,可反馈申请退款(可完整预览的文档不适用该条件!)。
- 3、如文档侵犯您的权益,请联系客服反馈,我们会尽快为您处理(人工客服工作时间:9:00-18:30)。
冶炼车间常见质量问题
一、上引法工序
1、铜杆氧化
产生原因:A)结晶器冷却水进水温度超出规定温度(45℃);B)铜杆上引速度过快;C)结晶器冷却水流量过小;D)石墨模与结晶器不匹配,上引铜杆与结晶器铜管间隙过大。
E).炉内铜液吸氧。
以上五点都会引起铜杆冷却跟不上而导致铜杆表面氧化。
解决方法:A).结晶器冷却水进水温度控制在规定范围内,发现水温过高立即调整。
B)适当降低铜杆上引速度。
C)增大结晶器冷却水流量。
D)上引铜杆与结晶器铜管间隙保持在0.3㎜~0.5㎜之间。
E)注意炉内木炭覆盖厚度和燃烧情况,发现厚度低于90㎜或燃烧成粉末时,需及时添加木炭。
炉内加入废料或双层电解铜时,要防止铜液暴露,造成吸氧。
2、铜杆表面起皮、毛刺
产生原因:A)铜液温度与显示温度不符(过低);B)结晶器石墨模摩损严重;C)铜杆牵引轮、夹轮不光滑;D).铜杆夹轮过紧导致铜杆变形。
解决方法:A)校正铜液温度和显示器温度。
B)更换结晶器石墨模。
C)修理或更换牵引导轮和铜杆夹轮。
D)调整铜杆夹轮松紧度
3、铜杆节距不规则、模糊
产生原因:A)结晶器石墨模使用时间过长,磨损严重;B)石墨模装配与结晶器铜管不垂直;C)牵引导轮与结晶器上引铜杆不垂直。
解决方法:A)更换石墨模。
B)校直或更换结晶器铜管。
C)调整牵引架与结晶器垂直度。
4、铜杆铜粉多
产生原因:加入潮湿电解铜。
解决方法:对潮湿的电解铜烘干后再加入炉内。
5、铜杆芯内有气孔
产生原因:A)加入潮湿的木炭或潮湿的电解铜;B)结晶器漏水;C)铜液温度过高。
解决方法:A)对潮湿的电解铜烘干后再加入炉内B)更换结晶器。
C)调整铜液温度。
6、铜杆柔软性差
产生原因:A)加入潮湿的木炭或潮湿的电解铜,水遇到高温产生氢和氧,造成铜杆结晶不好;B)铜液温度偏低,影响铜杆结晶。
解决方法:A)对潮湿的电解铜烘干后再加入炉内。
B)调整铜液温度。
7、铜杆电阻高于标准
产生原因:铜液中混入铁器类杂质。
解决方法:A)对加入炉内木炭用磁铁吸附铁类物质。
B)严禁废丝中有铁器类等杂物。
二、铜杆轧机
1、铜杆有飞边
产生原因:A)二个轧辊中心高度不一至;B)铜杆导料板磨损严
重,导致轧制过程中铜杆翻转。
解决方法:A)调整轧辊中心高度。
B)更换导料板。
2、铜杆表面有麻点
产生原因:A)轧辊开裂;B)轧辊摩损严重。
解决方法:更换轧辊。
3、铜杆不圆度超标
产生原因:A)轧辊磨损严重;B)轧辊调整不好。
解决方法:A)更换轧辊。
B)调整轧辊。
三、挤压软铜扁线
1、导体表面、R角沟槽。
产生原因:模具开裂或光洁度不好。
解决方法:更换模具或对模具定径区进行抛光。
2、导体尺寸不符标准要求
产生原因:A)模具尺寸不符要求;B)收线张力过紧。
解决方法:A)尺寸超负偏差对模具修理,尺寸超正偏差更换模具。
B)调整收线张力。
3、导体出现气泡
产生原因:A)铜杆空心;B)铜杆表面不清洁;C)挤压轮使用时间长,轮槽磨损变宽。
解决方法:A)更换铜杆。
B)对铜杆表面进行清洁处理或更换铜杆。
C)更换挤压轮。
4、导体表面擦伤
产生原因:A)模具装配不准;B)设备上有伤害导体的部位。
解决方法:A)重新装配模具。
B)检查设备上伤害导体的部位并进行修理。
5、导体表面氧化
产生原因:A)产品冷却水温度过高;B)控氧化剂浓度不够
解决方法:A)增加产品冷却水外循环流量,降低冷却水温度。
B)添加控氧化剂。
6、产品重量与要求不符
产生原因:计米器计米不准确。
解决方法:校正计米器,保证计量正确。
四、扁线拉丝
1、导体起皮、毛刺
产生原因:A)铜杆原因造成;B)拉丝模具开裂、磨损严重;C)设备上有伤害导体的部位。
解决方法:A)调换铜杆。
B)对拉丝模具抛光或调换拉丝模具。
C)检查设备上伤害导体的部位并进行修理。
2、导体表面、R角沟槽
产生原因:A)模具开裂或光洁度不好;B)润滑液润滑效果差解决方法:A)更换模具或对模具进行抛光。
B)按规定配比润滑液浓度、PH值。
3、导体尺寸不符标准要求
产生原因:A)模具尺寸不符要求;B)收线张力过紧;C)配模不
准确
解决方法:A)尺寸超负偏差的对模具修理,尺寸超正偏差的更换模具。
B)调整收线张力。
C)按工艺规定配模。
4、导体底面擦伤
产生原因:设备鼓轮不光滑。
解决方法:更换鼓轮或对不光滑的鼓轮进行抛光。
5、导体有波浪形
产生原因:A)模具配模不准确或模具定径区长度过短;B)出线鼓轮包的帆布不平整。
解决方法:A)按工艺规定配模或调换模具。
B)保证出线鼓轮包的帆布平整、无凸起。
6、导体氧化
产生原因:A)润滑液温度过高;B)用脏的手套或不戴手套接触导体
解决方法:A)控制润滑液温度(60℃)以下。
B)严禁戴脏手套或不戴手套接触导体。
7、导体B边局部伸细
产生原因:压扁过程中放线盘突然受力或铜杆掉到放线架(盘)外边,导致铜杆压扁后宽展不够。
解决方法:生产中应缓慢启动压扁机。
放线架(盘)过满或过重时,应有专人看管。
冶炼车间主要工装
一、上引法工装
铜杆结晶器:是上引铜杆的主要工装。
铜液通过结晶器结晶上引来达到所需的铜杆规格。
装配质量直接影响到上引铜杆质量。
组成部分:上部端座、外壳、、进水接口、出水接口、回水内管、底座内芯(石墨模接口、铜管)、保护套、石墨模
装配注意要点:1、铜管的垂直度;2、铜管与底座石墨模接口的垂直度;3、清除铜管上的水垢;4、检查接口部分密封圈是否完好;5、检查进、出水快速接头是否完好;6、检查底座螺牙是否完好;7、检查结晶器是否漏水(水压试验)、冷却水流量是否正常;8、石墨模与内芯底座是否拧紧;9、保护套与结晶器底座要充分拧紧;10、石墨模与保护套之间间隙要用耐火泥嵌满并烘干。
二、铜杆轧机工装
轧辊、导料板:是轧机的主要工装。
铜杆通过导位板校正进线、轧辊轧制达到所需规格。
轧辊的硬度、表面质量、孔型尺寸、导料板的尺寸将直接影响到铜杆的表面质量。
生产中检查要点:1、扎制铜杆成品及各道铜线坯工艺尺寸应符合下表要
生产中如哪道轧制的铜杆尺寸超出表中规定的尺寸,说明该道轧辊磨损严重,需及时更换。
2、轧辊使用时间长了,表面会出现麻点和裂纹,所以,每次开机前应检查轧辊使用情况,发现麻点或裂纹及时修理或更换。
3、导料板使用时间长了会出现磨损。
当铜杆轧制时出现摇摆,需及时更换,防止铜杆轧制时发生飞边。
三、挤压工装
挤压轮、腔体、挤压模:是挤压机的主要工装。
铜杆通过挤压轮摩擦升温进入腔体、挤压模达到所需的扁线规格
A、挤压轮长时间工作后,轮槽会磨损变宽,导致溢料进入腔体、模具,使产品产生气泡。
挤压轮加工硬度过大会开裂,产生工装冷却水从开裂处漏出,影响产品质量。
关闭挤压轮冷却水应在停机后10分钟,防止挤压轮、主轴高温断水。
B.腔体长时间使用后,腔体上的鼻子会后仰,使摩擦增加,温度升高,最终影响挤压轮使用寿命并形响产品质量。
腔体与挤压轮应保持一定的装配间隙(0.35㎜~0.45㎜),防止挤压轮与腔体摩擦产生的铁屑挤入产品中。
C、挤压模的主要作用是铜料通过模具,使之达到与模具一样的形状,并得到导体所要求的尺寸和表面质量。
导体的形状、尺寸直接取决于模具,所以,模具的质量直接影响到挤压导体的质量。
生产中应随时注意模具是否开裂、导体尺寸、表面质量是否满足标准要求。
四、扁线拉丝工装
拉丝模具是扁线拉丝的主要工装
拉丝模的主要作用是铜杆通过模具,使之达到与模具一样的形状,并得到导体所要求的尺寸和表面质量。
导体的形状、尺寸直接取决于成品模具和整套模具的配比,所以,成品模具的质量和整套模具的配比直接影响到拉丝导体的质量。
生产中应随时注意模具是否开裂、导体尺寸、表面质量是否满足标准要求,模具配比是否符合要求。