实验5 模压成型工艺实验
塑料模压成型工艺与实例

塑料模压成型工艺与实例
塑料模压成型是一种常用于制造大批量塑料制品的工艺。
它通过将高温熔化的塑料注
入到具有特定形状和尺寸的模具中,然后在一定压力和温度条件下,在模具中冷却和固化,最终得到所需的塑料制品。
塑料模压成型工艺一般包括以下步骤:
1. 模具设计和制造:首先需要设计出具有所需形状和尺寸的模具,并进行加工制造。
模具可采用金属、塑料或其他材料制成,其选择应根据所需制品的特性以及成本等因素进
行综合考虑。
2. 塑料料进料:将塑料料粒或块状物料放入预先设计好的注塑机中,加热至高温熔
化状态。
3. 注塑成型:熔化的塑料料通过注塑机喷射到模具中。
通常,注塑机会在一定的压
力和时间范围内将塑料料注入模具中,以确保塑料料可以填满模具。
4. 冷却和固化:待塑料料注入模具后,模具需要在一定的温度和时间条件下进行冷
却和固化。
这一步骤非常关键,因为模具温度和时间的控制能够影响到成型品的质量和尺
寸精度。
5. 成品处理:成型品在模具中固化后,需要将其从模具中取出并进行清洁和处理。
成品的后续处理可能包括支架、组装、加工或进一步加工等。
下面介绍几个具有代表性的塑料模压成型实例:
1. 塑料瓶的制造:塑料瓶是一种广泛使用的塑料制品,其制造一般采用注塑成型或
吹塑成型等工艺。
其中,注塑成型是一种常用于生产大批量塑料瓶的工艺。
通过注入熔化
的塑料料到模具中,模具经过冷却和固化,即可得到所需的塑料瓶制品。
总之,塑料模压成型是一种常用于制造大批量塑料制品的工艺。
其具有成本低、成型
效率高等优势,并被广泛应用于塑料制品的生产中。
模压成型工艺实验报告模板怎么写

模压成型工艺实验报告模板怎么写
一、实验目的
本实验旨在探究模压成型工艺在制备材料中的应用,通过实验检测和分析,了解模压成型工艺对材料性能的影响,为后续工艺优化提供参考。
二、实验原理
模压成型工艺是一种常见的材料成型工艺,通过在高温高压条件下将原材料塑性变形,使其充分填充模具腔体并定型成型的工艺方法。
通过实验测试和观察,可以评估材料的密实性、硬度、耐磨性等性能指标。
三、实验步骤
1.准备实验所需的原材料和模具,根据实验设计调配好配方比例;
2.将原材料放入模具中,注意填充均匀,并确保模具密封;
3.将装有原材料的模具放入预热好的模压机中,根据设定的压力和温度进行成型;
4.成型完成后,取出样品进行冷却,并进行外观检查和尺寸测量;
5.对样品进行性能测试,包括密实度、硬度、耐磨性等指标的检测;
6.记录实验数据并撰写实验报告。
四、实验结果与分析
通过实验我们得到了模压成型材料的密实度、硬度和耐磨性等数据,发现随着成型压力的增加,材料的密实度和硬度会提高,而耐磨性则有所下降。
这为进一步优化模压成型工艺提供了参考依据。
同时,通过对不同配方的材料进行实验,可以比较不同条件下材料的性能差异,为工艺参数选择提供支持。
五、结论
模压成型工艺是一种有效的制备材料的方法,通过实验我们对其应用和影响有了更深入的了解。
在实际应用中,需要根据具体材料和成型要求来选择合适的工艺参数,以达到最佳成型效果。
六、致谢
在此感谢实验中给予支持和帮助的所有人员,以及为实验提供设备和材料支持的相关单位。
以上为模压成型工艺实验报告模板的写作参考,在进行实际撰写时,可以根据具体实验内容和结果进行适当的调整和完善。
塑料的模压成型

六、实验报告
1.写出酚醛树脂与甲醛在碱性条件下,进一步 缩合和交联的反应式。 2.列出平板硫化机的技术参数。报告实验所用 原料和助剂,操作工艺条件。 3.用游标卡尺测试2个正常试样的尺寸,结合模 具尺寸,计算制品的收缩率。 4.分析模压制件的表面质量受工艺条件的影响 情况;结合后面力学性能的测试结果,分析力学 性能与实验工艺条件之间的关系。
四、实验步骤
3.模具准备 模具所有工作面进行脱模机处理
四、实验步骤
4.压制成型
(1)通过加热和温控装置将上、下模板温度控制在 (160±5)℃。 (2)将压制模具放入压机上、下模板间在压制温度 下预热10min。
(3)按成型模具的容积及模压制品的比重(约 1.4)计算加料量,放置在模具的模腔内,模具闭 合后置于压机模板的中心位置,在已加热的模板 间接触闭合的情况下(未受压力)预热约10min。酚醛树脂 Nhomakorabea、实验原理
酚醛树脂和上述各种配合剂通过一定的共混加 工程序就得到酚醛树脂压塑粉。共混的工序是 首先对块状树脂进行粉碎后和配合剂的捏合混 合,然后再在130℃左右的温度下进行辊压塑 炼,再经过冷却、磨碎而成。压塑粉中的树脂 已经经过高温的塑炼,具有适宜的流动性,也 有适当的细度、均匀度和适当的挥发物的含量, 可以满足制品成型和使用的要求。
混合可以在高速混 合机或捏合机中进 行,是物料的初混 合,最终便形成均 匀的粉状掺混物
• 当试验用料量少时, 可采用手工掺混
加工设备--电热平板压机
压制成型过程包括物 料的熔融、流动、充模成 型和最后冷却定型等程序, 是物理变化过程,不应发 生化学变化。 正确选择和控制压制的 温度、压力、保压的时间 及冷却定型程度等都是很 重要的。
二、实验原理
模压成型工艺实验报告现象分析总结与反思

模压成型工艺实验报告现象分析总结与反思在模压成型工艺实验中,我们以提高产品质量和生产效率为目标,通过一系列实验观察、记录和分析,最终得出了一些有价值的现象分析和总结。
这些实验数据和结果为我们深入了解模压成型工艺提供了重要参考,并引发了我们一些反思和改进方向。
首先,在实验过程中我们发现,模具温度对产品成型质量有着非常重要的影响。
当模具温度过高或过低时,都会导致产品表面出现瑕疵和变形现象。
经过多次调整实验发现,在适宜的模具温度范围内,产品成型效果最佳,表面光滑且尺寸稳定。
因此,控制好模具温度是确保产品质量稳定的关键之一。
其次,模压时间也是影响产品成型效果的重要因素之一。
我们在实验中发现,适当延长模压时间可以提高产品密实度和强度,但时间过长则会使产品过热变形。
因此,在制定生产计划时需要合理安排模压时间,避免因时间不当而影响产品质量。
另外,原料的选择和配比也是影响模压成型工艺的重要因素之一。
在实验中我们尝试了不同配比的原料,发现某些配比下产品成型效果更佳,同时也提高了生产效率。
因此,在实际生产中需要根据具体情况选择合适的原料配比,以获得更好的成型效果。
通过以上实验现象的分析和总结,我们不仅对模压成型工艺有了更深入的了解,也为我们今后的生产提供了一些建设性的改进建议。
在未来的工作中,我们将进一步优化模具设计、调整工艺参数,以提高产品质量和生产效率。
同时,也将继续进行实验研究,不断探索模压成型工艺的改进空间,为企业的发展注入新的动力。
总的来说,通过这次模压成型工艺实验,我们不仅积累了宝贵的经验,也发现了一些问题和改进方向,相信在不断的努力和探索中,我们能够取得更好的成果,不断提升企业的竞争力和发展水平。
1。
模压成型工艺实验报告怎么写的
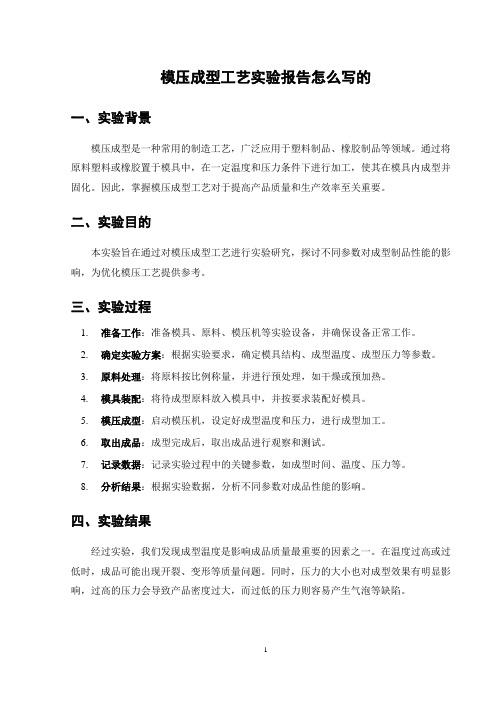
模压成型工艺实验报告怎么写的一、实验背景模压成型是一种常用的制造工艺,广泛应用于塑料制品、橡胶制品等领域。
通过将原料塑料或橡胶置于模具中,在一定温度和压力条件下进行加工,使其在模具内成型并固化。
因此,掌握模压成型工艺对于提高产品质量和生产效率至关重要。
二、实验目的本实验旨在通过对模压成型工艺进行实验研究,探讨不同参数对成型制品性能的影响,为优化模压工艺提供参考。
三、实验过程1.准备工作:准备模具、原料、模压机等实验设备,并确保设备正常工作。
2.确定实验方案:根据实验要求,确定模具结构、成型温度、成型压力等参数。
3.原料处理:将原料按比例称量,并进行预处理,如干燥或预加热。
4.模具装配:将待成型原料放入模具中,并按要求装配好模具。
5.模压成型:启动模压机,设定好成型温度和压力,进行成型加工。
6.取出成品:成型完成后,取出成品进行观察和测试。
7.记录数据:记录实验过程中的关键参数,如成型时间、温度、压力等。
8.分析结果:根据实验数据,分析不同参数对成品性能的影响。
四、实验结果经过实验,我们发现成型温度是影响成品质量最重要的因素之一。
在温度过高或过低时,成品可能出现开裂、变形等质量问题。
同时,压力的大小也对成型效果有明显影响,过高的压力会导致产品密度过大,而过低的压力则容易产生气泡等缺陷。
1五、结论与建议1.合理控制成型温度和压力是保证产品质量的关键,需要根据具体情况进行调整。
2.在模压成型过程中,注意原料配比和预处理工作,确保原料质量符合要求。
3.实验过程中要认真记录数据,及时发现问题并进行调整。
通过本实验,我们深入了解了模压成型工艺的重要性以及影响因素,这将有助于我们在实际生产中更好地应用模压成型技术,提高产品质量和生产效率。
2。
模压成型工艺实验报告现象分析总结怎么写

模压成型工艺实验报告现象分析总结怎么写引言模压成型工艺作为一种常见的加工方法,广泛应用于塑料制品、橡胶制品等领域。
本文通过对模压成型工艺实验的现象分析总结,旨在探讨实验中可能出现的问题和解决方法,以期提高生产效率和产品质量。
实验条件描述实验中我们选用了标准的模压设备和塑料原料,设定了适当的温度、压力和时间参数进行成型。
模具设计合理,包括了产品的形状、尺寸以及凹凸平整度等要求。
实验过程中,我们发现了以下几个现象:1.成型不完整:部分产品出现了成型不完整的情况,主要表现为产品表面凹凸不平或者有空洞存在。
2.产品变形:有些产品成型后发生了形状变形,与设计要求不符,造成产品无法使用。
3.色差问题:成型后的产品出现了一些色差,与预期颜色不一致。
现象分析成型不完整成型不完整的现象可能由以下原因引起:1.模具问题:模具表面存在划痕、损伤等情况,导致产品表面不平整。
2.温度设置不当:温度过高或过低都会影响塑料的流动性,导致成型不完整。
3.压力不均匀:压力分布不均匀会造成部分区域成型不完整,出现空洞。
解决方法: - 定期检查模具的表面情况,及时保养和更换受损模具。
- 调整温度至适宜范围内,确保塑料材料可以均匀流动。
- 调整压力均匀分布,避免空洞产生。
产品变形产品变形可能是由以下原因引起:1.冷却不均匀:产品在冷却阶段受到外部环境温度影响不均匀,导致变形。
2.材料质量:原料质量差、成分不均匀等因素可能导致产品变形。
解决方法: - 调整冷却设备,保证产品整体受热冷却均匀。
- 定期检查原料质量,选用优质原料,并保持原料成分稳定。
色差问题产品出现色差问题可能由以下原因引起:1.原料选择问题:选用了不同批次或不同品牌的原料可能导致颜色不一致。
2.温度控制:温度波动大或不稳定会影响颜色的稳定性。
解决方法: - 统一选用同一批次、同一品牌的原料,确保颜色一致。
- 稳定温度控制在设定值范围内,避免温度波动。
总结通过对模压成型工艺实验中出现的成型不完整、产品变形以及色差问题进行分析,我们可以看出,影响成型质量的因素是多方面的,需要从多个角度进行改进和优化。
模压成型实验
模压成型实验一、实验目的热塑性塑料、热固性塑料以及橡胶的成型,都可以采用模压工艺。
本实验通过橡胶的混炼试验以及模压成型,加深学生理解复合物配制及其工艺控制对产品外观和力学性能的作用,掌握压制成型特点和生产操作。
二、实验原理混合工序是利用对物料加热和搅拌作用,使树脂粒子在吸收液体组分的同时,受到反复撕捏、剪切,形成能自由流动的粉状掺混物。
塑炼工序是使物料在粘流温度以上和较大的剪切作用下来回折迭、辊压,使各组分分散更趋均匀,同时驱出可能含有水份等挥发气体。
经塑炼后,可塑性得到很大改善,配方中各组分的独特性能和它们之间的“协同作用”将会得到更大发挥,这对下一步成型和制品性能有着极其重要的影响。
因此,塑炼过程中与料温和剪切作用有关的工艺参数、设备特性(如辊温、辊距、辊速、时间)以及操作的熟练程度都是影响塑炼效果的重要因素。
压制是板材成型的重要方法,正确选择和调节压制温度、压制压力、时间以及制品的冷却程度是控制板材性能的工艺措施。
通常在不影响制品性能的前提下,适当提高压制温度,降低成型压力,缩短成型周期对提高压机生产效率是行之有效的;但过高的温度、过长的加热时间会加剧树脂降解和熔料外溢,致使制品颜色暗淡、毛边增多及力学性能变劣。
三. 主要技术指标1.开炼机2.平板硫化机3.平板模具4.小铜刀、棕刷、手套、剪刀等实验用具。
5. 250kN 平板硫化机技术规格最大关闭压力 250kN工作液最大压力 15 MPa柱塞最大行程 150 mm平板面积 350 mm×350 mm平板单位面积压力 2 MPa工作层数 2每层间距离 75 mm每块平板加热功率 2.4 kW总加热功率 7.2 kW最高工作温度 180℃6. 250kN 平板硫化机的组成平板硫化机,在硫化机机座里装有工作液压缸,在缸里有柱塞,在柱塞上端固定着升降平板,在平板上固定着下平板,上机座与下机座由柱轴连接固定,硫化机除有上下平板外,中间还有活动平板,该平板可以上下移动,为了使可动平板下降到一定位置时停止,在柱轴安有限制器以便使活动平板与上下平板之间有一定的空间,便于放入模具,合模时,柱塞的上升是油泵供给工作液托起柱塞并对平板施加压力,工作液施加压力由表指示出来,而所需压力值大小由调压阀调节,平板上下过程是由操作手轮控制,平板的加热、油泵电机的开启及指示均由电器控制箱上的开关、按钮和指示灯等所控制和显示。
模压成型工艺实验
模压成型工艺实验模压成型是一种常见的制造工艺,用于生产各种塑料制品和零部件。
在实际生产中,对模压成型工艺的控制和优化至关重要,因此进行模压成型工艺实验具有重要意义。
本实验旨在探讨模压成型工艺中的一些关键参数对制品质量的影响,以期能够优化生产过程,提高产品的质量和生产效率。
实验目的本实验旨在通过调整模压成型工艺中的关键参数,如模具温度、压力和注塑速度等,探讨它们对制品质量的影响,为工艺参数的调优提供依据。
实验材料和设备•模压成型机•塑料颗粒•模具•温度计•压力计实验步骤1.准备模压成型机并调试至合适工作状态。
2.将塑料颗粒加入注塑机的料斗中,设定注塑机的温度和加热时间。
3.调整模具温度和模具压力参数,通常会根据塑料材料的特性和产品的要求进行设定。
4.进行模压成型生产,观察和记录生产过程中的关键参数,如模具温度、压力曲线等。
5.取出模压成型好的产品,进行质量检测和评估。
主要包括外观质量、尺寸精度和力学性能等方面的测试。
6.根据实验结果和数据分析,总结关键参数对产品质量的影响规律,并提出优化建议。
实验结果和分析通过实验发现,模具温度是影响产品外观质量的重要因素之一。
当模具温度过高或过低时,都会导致产品表面出现瑕疵,如熔胶不良或热应力痕迹等。
因此,合理控制模具温度是确保产品质量的关键步骤。
另外,模具压力也对产品的尺寸精度和力学性能有显著影响。
适当增加模具压力可以有效减少产品翘曲和变形的情况,同时提高产品的强度和硬度。
实验结论通过模压成型工艺实验的研究和分析,我们得出了以下结论: 1. 模具温度是影响产品外观质量的重要因素,需要合理控制。
2. 模具压力的调整可以改善产品的尺寸精度和力学性能。
3. 工艺参数的优化可以提高生产效率和产品质量。
总结模压成型工艺是一种常见的塑料制品生产工艺,通过实验研究和数据分析,我们可以更好地了解和掌握工艺参数对产品质量的影响规律,从而优化生产过程,提高产品的质量和生产效率。
热塑性塑料模压成型
热塑性塑料模压成型一、实验原理热塑性塑料硬板多为半成品,作为热成型及二次加工的原材料,用于制作箱体、壳体、家具、防腐槽、复合装饰板等。
本实验通过高速混合、双辊塑炼成片和热压成型制备PVC塑料硬板,加深理解PVC复合物配制及其工艺控制对产品外观和力学性能的作用,掌握压制成型特点和生产操作。
二、实验原理PVC是应用很广泛的树脂之一。
单纯的PVC树脂是较刚硬的原料,其熔体粘度大,流动性差,虽具有一般非晶态线型高聚物的热力学状态,但T g~Td范围窄,对热不稳定,在成型温度下会发生严重的降解,放出氯化氢气体、变色和粘附设备。
因此,在成型加工之前必须加入热稳定剂、加工改性剂、润滑剂、抗冲改性剂等多种助剂。
压制硬PVC板材生产过程包括下列工序:①混合:按一定配方称量PVC及各种组分,按一定的加料顺序,将各组分加入到高速混合机中进行几何分散;②双辊塑炼拉片:用双辊塑炼机将混合物料熔融混合塑化,得到组成均匀的成型用PVC片材;③压制:把PVC片材放入恒温压制模具中,预热、加温加压使PVC熔融塑化,然后冷却定型成硬质PVC板材。
硬质PVC板材,可以制成透明的或不透明的两种类型。
在配方设计中主体成分是树脂和稳定剂,适量加入润滑剂和其他添加剂,不加或少量加入增塑剂,使复合制品能够达到外观光洁,具有较高的热变形温度、冲击强度、刚性和耐化学稳定性。
三、实验用设备及配方1.设备SHR-10A高速混合机1台(张家港市曙光机械厂生产),SK—160B双辊炼塑机1台(上海橡胶机械厂生产),XLB型平板硫化机1台,不锈钢模板(型腔尺寸120mm×120mm)1付,浅搪瓷盘1个,水银温度计(0~250℃)2支,表面温度计(0~250℃)1支,天平(感量0.1g)1台,剪刀、手套等实验用具。
2.配方表1 硬质PVC板材配方示例原料用量(理论)用量(实际)PVC 0.4kg 0.40kgDOP 16~24ml 22.0ml 三盐基性硫酸铅20~24kg 23.0g液体石蜡2~4mL 2.5mLCaCO340g 40.0gBaSt 6g 6.0gCaSt 4g 4.0g四、实验条件及操作(见下图)图1 实验操作流程及条件①按照配方在天平上称量树脂及各种添加剂的用量,经研磨后,依次加入配料盘中。
薄膜压延成型实验报告
一、实验目的1. 了解薄膜压延成型的原理和工艺过程;2. 掌握薄膜压延成型的实验操作技能;3. 分析薄膜压延成型过程中影响产品质量的因素;4. 评价薄膜压延成型工艺的可行性和优化方向。
二、实验原理薄膜压延成型是一种将高分子材料通过加热、塑化、挤压和延展等过程,使其连续成型为规定尺寸的薄膜或片材的加工方法。
实验过程中,通过调整温度、转速、辊筒间隙等工艺参数,实现对薄膜厚度、宽度和表面质量等性能的调控。
三、实验材料与设备1. 实验材料:聚氯乙烯(PVC)树脂、增塑剂、稳定剂、填加料等;2. 实验设备:高速混合机、密炼机、挤出机、压延机、冷却辊筒、引离辊等。
四、实验步骤1. 配方设计:根据薄膜制品的用途和要求,确定PVC树脂及其他辅料的使用比例,并计算所需物料的质量;2. 物料混合:将PVC树脂及其他辅料按配方比例加入高速混合机中,搅拌均匀;3. 塑炼:将混合好的物料加入密炼机中,进行塑炼,使其达到接近粘流温度;4. 挤出:将塑炼好的物料加入挤出机中,通过挤出机将物料挤出成条状;5. 压延:将挤出后的条状物料送入压延机,通过压延机将物料压延成薄膜;6. 冷却:将压延好的薄膜送入冷却辊筒,进行冷却定型;7. 引离:将冷却好的薄膜从压延机上引离,进行后续加工。
五、实验结果与分析1. 薄膜厚度:通过调整压延机辊筒间隙,可以控制薄膜的厚度。
实验结果表明,辊筒间隙越小,薄膜厚度越薄;反之,辊筒间隙越大,薄膜厚度越厚。
2. 薄膜宽度:薄膜宽度受压延机辊筒长度限制。
实验中,通过调整辊筒长度和辊筒间隙,可以控制薄膜的宽度。
3. 薄膜表面质量:薄膜表面质量受多种因素影响,如辊筒温度、转速、物料塑化程度等。
实验结果表明,在适宜的工艺条件下,薄膜表面质量较好,无明显气泡、裂纹等缺陷。
4. 薄膜性能:通过测试薄膜的拉伸强度、撕裂强度、热稳定性等性能指标,可以评价薄膜的质量。
实验结果表明,薄膜性能符合要求。
六、实验结论1. 薄膜压延成型是一种有效的薄膜制备方法,具有生产效率高、产品质量好等优点;2. 通过调整工艺参数,可以实现对薄膜厚度、宽度和表面质量等性能的调控;3. 在实验过程中,应注意辊筒温度、转速、物料塑化程度等因素对薄膜质量的影响。
- 1、下载文档前请自行甄别文档内容的完整性,平台不提供额外的编辑、内容补充、找答案等附加服务。
- 2、"仅部分预览"的文档,不可在线预览部分如存在完整性等问题,可反馈申请退款(可完整预览的文档不适用该条件!)。
- 3、如文档侵犯您的权益,请联系客服反馈,我们会尽快为您处理(人工客服工作时间:9:00-18:30)。
答:因为SMC材料力学性质并不完全是各项同性,正交叠合放置有利于保证良好的力学性能
因为SMC材料在模压温度下会产生流动,从而填满型腔。因此要按照成型模具的容积及模压制品的密度来计算铺放料的大小。若铺放料大小与模具投影面一样大,则在模压时会使铺放料溢出而造成浪费。
工艺记录三:
日期:2013.12.17
压力机液压系统油压:12.28(MPa)
模压:12.28(MPa)
工艺实验名称:
SMC模压工艺
模压材料名称:
SMC
上模温度:
162
模压材料重量(g):
556.3
下模温度:
152
板材理论尺寸(mm):
250 250
板材实际尺寸(mm):
250 250
板材实际重量(g):
复合材料工艺学实验报告(第一组)
实验
同济大学
飞行器制造工程
实验
一,实验原理
模压成型工艺是将一定量的模压料放入金属对模中,在一定的温度和压力作用下固化成型制品的一种方法。在模压成型过程中需加热和加压,使模压料塑化,流动充满模腔,并使树脂发生固化反应。在模压料充满模腔的流动过程中,不仅树脂流动而且增强材料也随之流动。模压成型工艺的成型压力要比其他工艺高,属于高压成型。因此它既需要有压力控制的液压机,又需要有高强度,高精度,耐高温的金属模具。
502.5
板材密度(g/
1.7867
实验中出现的问题与反思:
在实验的合模过程中,出现了如图所示的SMC材料溢出模具的情况,据分析,是称取材料时重量达556.3g,偏高于需要的重量造成的,除此之外,将SMC片材放置在模具中时,位置有些偏外也是一个原因。不过由于我们是第一组,缺乏经验导致的这个问题,在提出以后,老师要求后面的组将自己的材料剪去一部分至重量稍稍大于需要的重量为止,并在放至模具中时将位置摆正,大大的改善了这种情况。
模压工艺是利用树脂固化反应中各阶段的特性来实现制品成型的过程。当模压料在模具内被加热到一定的温度时,其中树脂受热熔化成为粘流状态,在压力作用下粘裹纤维一起流动直至填满模腔,此时称为树脂的“粘流阶段”;继续提高温度,树脂发生化学交联,分子量增大,当分子交联形成网状结构时,流动性很快降低直至表现一定弹性,此时称为“凝胶阶段”;再继续受热,树脂交联反应继续进行,交联密度进一步增加最后失去流动性,树脂变为不溶不熔的体型结构,到达了“硬固阶段”。模压工艺中上述各阶段是连续出现的,其间无明显界限,并且整个反应是不可逆的。
对于不饱和聚酯树脂,足够的固化剂的添加量和适当的增进剂的添加量,才能使得不饱和聚酯树脂固化完全,达到理想的效果。
2,模压料用量与挥发分(包含溶剂和缩合水两部分)有什么关系?挥发分大小对模压制品的质量影响?
答:挥发分主要是模压料中稀释剂、脱模剂和有些树脂反应过程中产生的水分、气体等。挥发物在模压料料中的含量对其流动性影响很显著,挥发分含量增加,模压料流动性增加。但挥发分含量不宜过高,否则会使树脂在成型过程中大量流失,严重影响制品质量。当挥发分含量过低时,模压料的流动性显著下降,成型困难。
二,实验目的
1,掌握模压工艺的基本过程与技术要点;
2,学会使用油压机,并操作实践;
3,通过对SMC模压料的进一步了解,学会拟定模压工艺条件的方法。
三,实验内容
1,掌握油压机的操作规程;
2,模压一块尺寸:250 的SMC试样板。
四,实验材料和仪器设备
1,实验材料:SMC模压料,脱模剂;
2,实验工具与设备:剪刀,台秤,钢模具,50吨压机(D=180mm)
油压机的工作原理是巴斯卡定律,压力泵将压力油输送到油缸的活塞腔内,由活塞传力于上(下)平台,液压电磁阀控制压力油方向使活塞带动上(下)平台作上下运动。压力形式通常以油缸的安装位置区分,油缸位于压机上方称上压式油压机,反之称下压式油压机。
油压机一般由主机架,油泵,油缸和活塞,工作平台,阀门,压力指示表,加热和温控系统组成。油压机的额定压力与压力表表压之间的关系通常是按下式计算:
模压成型的优点是生产效率高,制品尺寸精确表面光洁,一次成型。缺点是模具设计和制造较复杂,初次投资高,制件易受设备的限制,所以一般适用于大批量生产的小型复合材料制品。
根据不同的模压料品种其模压成型工艺参数各不相同。下表是不同模压料成型工艺参数:
模压料品种
成型压力
成型温度与保温时间
酚醛模压料
30~50MPa
150~180 ;2~15分/毫米
环氧酚醛类
5~30(MPa)
160~220 ;5~30分/毫米
聚酯类
2~15(MPa)
引发剂的临界温度+40~70 ;
0.5~1分/毫米
为便于脱模,一般在模压时上模温度比下模温度高5~10 .模压制品在保温结束后,一般在压力下逐渐降温。除特殊要求外,采用冷却水强制冷却。
实验5思考题
1,热固性酚醛树脂为什么可以不加固化剂会固化完全?环氧树脂和不饱和聚酯树脂不加固化剂能固化吗?
答:因为树脂本身会发生自聚(交联)反应,其中里面的苯乙烯就是交联剂量,因此不需要加固化剂就可以固化完全;
对于环氧树脂,常用环氧树脂固化剂有脂肪胺、脂环胺、芳香胺、聚酰胺、酸酐、树脂类、叔胺,不加固化剂的话,在光引发剂的作用下紫外线或光也能使环氧树脂固化。常温或低温固化一般选用胺类固化剂,加温固化则常用酸酐、芳香类固化剂。
裁剪铺放时料不应偏多或偏少,以免造成制品尺寸不能到位或缺陷。
4,在150 下开模,迅速按片料铺放面积的整数倍正交叠合,剩余小料放中心位置;
5,合模,加压至5MPa,保温保压5~8分钟后降温至60 以下即可脱模。
6,脱模,待样品充分冷却固化后,修边,去除毛边,称重,测量厚度估算材料密度后将材料名称,模压参数,复材密度等写贴标签。
_工作油压(MPa)
D——油缸内活塞的直径(mm)
F——压机的工作压力(N)
五,实验步骤
1,模具清理,涂脱模剂,合模于压机平台上;
2,制定模压参数,调试压机使上下平台面刚好与钢模接触,加温预热模具至所需温度(150 );
3,按下式计算模压预浸料的用量:G=(1+
式中:
V——模具型腔容积或制品实占空间体积(