内部裂纹
连铸坯内部裂纹产生的主要原因及解决措施
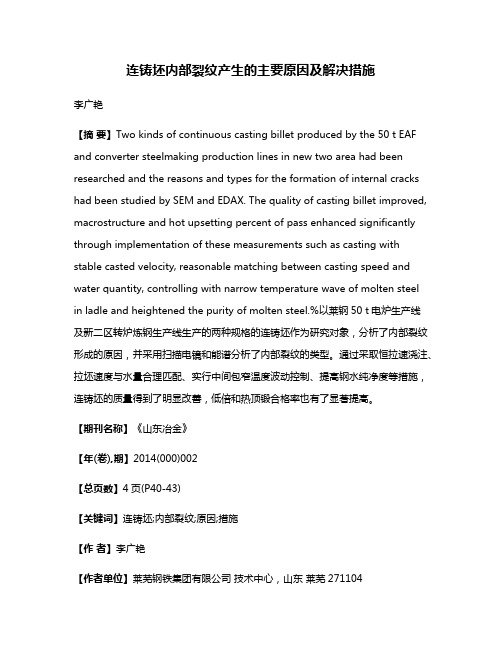
连铸坯内部裂纹产生的主要原因及解决措施李广艳【摘要】Two kinds of continuous casting billet produced by the 50 t EAF and converter steelmaking production lines in new two area had been researched and the reasons and types for the formation of internal cracks had been studied by SEM and EDAX. The quality of casting billet improved, macrostructure and hot upsetting percent of pass enhanced significantly through implementation of these measurements such as casting with stable casted velocity, reasonable matching between casting speed and water quantity, controlling with narrow temperature wave of molten steelin ladle and heightened the purity of molten steel.%以莱钢50 t电炉生产线及新二区转炉炼钢生产线生产的两种规格的连铸坯作为研究对象,分析了内部裂纹形成的原因,并采用扫描电镜和能谱分析了内部裂纹的类型。
通过采取恒拉速浇注、拉坯速度与水量合理匹配、实行中间包窄温度波动控制、提高钢水纯净度等措施,连铸坯的质量得到了明显改善,低倍和热顶锻合格率也有了显著提高。
【期刊名称】《山东冶金》【年(卷),期】2014(000)002【总页数】4页(P40-43)【关键词】连铸坯;内部裂纹;原因;措施【作者】李广艳【作者单位】莱芜钢铁集团有限公司技术中心,山东莱芜271104【正文语种】中文【中图分类】TG115.21 前言铸坯裂纹的形成是一个非常复杂的过程,是传热、传质和应力相互作用的结果。
板坯内部裂纹的原因与措施

板坯内部裂纹的原因与措施文/胡秋芳 罗莉萍裂纹是连铸板坯常见的质量缺陷,它的存在是发生钢板开裂、断板等质量问题的重要原因。
随着市场经济的深入发展和竞争机制的不断深化,产品质量就显得特别重要。
要想使企业在激烈的市场竞争中常胜不衰,就必须保证产品的质量。
目前二钢厂连铸板坯的质量问题比较突出,其表现为裂纹比较多,即有表面裂纹、表面横裂和表面纵裂,也有内部裂纹。
本文结合二钢厂连铸板坯机的生产实践,从铸机设备与工艺两方面对板坯内部裂纹的形成原因、影响因素等进行的探讨并提出改造措施。
一、板坯连铸机连铸机的机型可分为:立式连铸机、立弯式连铸机、多点弯曲连铸机、全弧形连铸机、多半径弧型(椭圆型)连铸机、水平式连铸机等。
二钢厂板坯连铸机是选用立弯式的连铸机、一机两流单点矫直、火焰切割式、浇注断面为250mm×1800mm,拉坯速度为0.9~1.1m/min,振幅5~8mm,塞棒拉流、浸入式保护浇注,其浇注的钢种为Q215、Q235、Q345。
该铸机设计能力为200万吨/年。
二、连铸坯内部裂纹的类型及形成原因连铸坯内部裂纹的主要类型为:三角区裂纹、中间裂纹、中心裂纹。
连铸坯内部裂纹的形成是铸坯凝固过程中各种外部压力和钢水凝固产生的内部压力作用在液相穴的结果。
液相穴深度是指结晶器内钢水液面连铸坯完全凝固处的长度。
连铸坯的液相穴深度随拉坯的速度而改变,若拉坯的速度快,连铸坯的液相穴深度会延长;反之,连铸坯的液相穴深度会短些。
前沿的凝固交界面及附近区域上当综合压力超过该钢种的固相线温度附近的临界强度时,固液界面处的坯壳已不能抵抗压力作用而产生开裂。
由于钢液已形成半凝固态和固态,使钢水无法外流,因此裂纹得以在坯壳内形成。
从本质上说,内部裂纹的产生是各种压力综合作用的结果,也是该种钢高温力学性能不能抵抗综合力的结果,作用于铸坯壳使之发生变形。
导致产生裂纹的作用力有以下几种:鼓肚力;弯曲或矫直压力;热压力;坯壳与结晶器的摩擦力;意外机械作用力裂纹的出现要经历形成和扩展两个过程。
减少内部裂纹的措施

减少内部裂纹的措施引言在许多材料的制造过程中,内部裂纹是一个常见的问题。
这些裂纹可能会导致材料强度的降低,甚至在使用过程中造成严重的失效。
为了保证产品的质量和性能,有必要采取适当的措施减少或防止内部裂纹的形成和扩展。
本文将介绍一些常见的减少内部裂纹的措施。
1. 材料选择选择合适的材料是减少内部裂纹的首要措施。
一些材料在制造过程中更容易形成内部裂纹,而另一些材料则较少受内部裂纹的影响。
例如,某些金属合金具有更好的抗裂纹性能,可以用于替代容易产生内部裂纹的材料。
2. 控制制造过程正确控制制造过程对于减少内部裂纹非常关键。
以下是一些控制制造过程的措施:2.1 温度和湿度控制在制造过程中,适当的温度和湿度控制可以减少内部裂纹的形成。
某些材料在特定温度和湿度条件下更容易产生裂纹。
因此,必须确保制造环境中的温度和湿度处于适宜的范围内。
2.2 控制冷却速率快速冷却过程可能会导致内部裂纹的形成。
对于某些材料,适当的冷却速率可以减少裂纹的发生。
这可以通过调整冷却介质的温度或改变冷却介质的性质来实现。
2.3 减少应力集中应力集中是内部裂纹形成和扩展的主要原因之一。
通过合理设计产品形状和结构,可以减少应力集中,从而降低内部裂纹的风险。
例如,在零件设计中,可以使用过渡半径或舒适圆角来减少应力集中。
2.4 合理控制加工参数在制造过程中,合理控制加工参数也是减少内部裂纹的重要措施。
例如,对于金属加工过程,适当的切削速度和进给速度可以减少应力积聚和裂纹的形成。
3. 优化热处理热处理是一种常用的方法来改善材料的性能和减少内部裂纹。
在热处理过程中,合理选择适当的处理温度和时间,可以使材料达到理想的组织结构,从而减少内部裂纹的发生。
4. 足够的工艺检验对制造过程进行足够的工艺检验是减少内部裂纹的有效手段。
通过使用一些非破坏性检测方法,如超声波检测、磁粉检测等,可以及早发现内部裂纹,并采取相应的措施予以修复或调整制造参数。
5. 定期维护和保养为了减少内部裂纹的形成和发展,定期维护和保养是非常重要的。
裂纹原因分析报告

裂纹原因分析报告1. 引言本报告旨在对裂纹产生的原因进行分析和解释。
通过对裂纹的形成机制、材料特性、工艺参数等方面的研究,对裂纹的产生原因进行归纳总结,并提供相应的解决方案。
2. 裂纹的定义裂纹是指材料中的断裂缝隙,通常由于外部力、热膨胀或其他因素引起。
裂纹的存在对材料的性能和使用寿命都会产生重大影响,因此对裂纹的原因进行深入研究具有重要意义。
3. 裂纹的分类根据裂纹的形态和产生原因,裂纹可以分为以下几种类型:3.1 表面裂纹表面裂纹是指在材料表面形成的裂纹,通常由于外部力或疲劳等因素引起。
表面裂纹的主要特点是易被观察到,并且对材料的疲劳寿命影响较大。
3.2 内部裂纹内部裂纹是指在材料内部形成的裂纹,通常由于材料内部的缺陷或应力集中等因素引起。
内部裂纹的存在对材料的强度和韧性产生较大影响。
3.3 焊接裂纹焊接裂纹是指在焊接过程中产生的裂纹,通常由于焊接材料和基材的热膨胀系数不匹配或焊接过程中的应力集中等因素引起。
焊接裂纹的存在对焊接接头的强度和密封性产生重要影响。
4. 裂纹产生的原因裂纹产生的原因复杂多样,以下列举了几个常见的原因:4.1 材料特性材料的特性是裂纹产生的重要原因之一。
例如,材料的强度、韧性、热膨胀系数等特性会直接影响裂纹的形成和扩展。
如果材料强度较低或韧性较差,则裂纹很容易形成并扩展。
4.2 外部力外部力是裂纹产生的常见原因之一。
当材料受到外部力的作用时,会产生应力集中,从而导致裂纹的形成。
例如,弯曲、拉伸、压缩等外部力都可能引起裂纹的产生。
4.3 工艺参数工艺参数是影响裂纹产生的重要因素之一。
例如,焊接过程中的温度、焊接速度、焊接压力等参数都会对焊接接头的质量产生重要影响。
如果工艺参数设置不当,就会导致焊接裂纹的产生。
4.4 环境条件环境条件是裂纹产生的重要因素之一。
例如,温度变化、湿度变化等环境条件的改变都可能引起材料的热膨胀或收缩,从而导致裂纹的形成。
此外,化学腐蚀等环境因素也会加速裂纹的扩展。
断裂力学三种裂纹类型
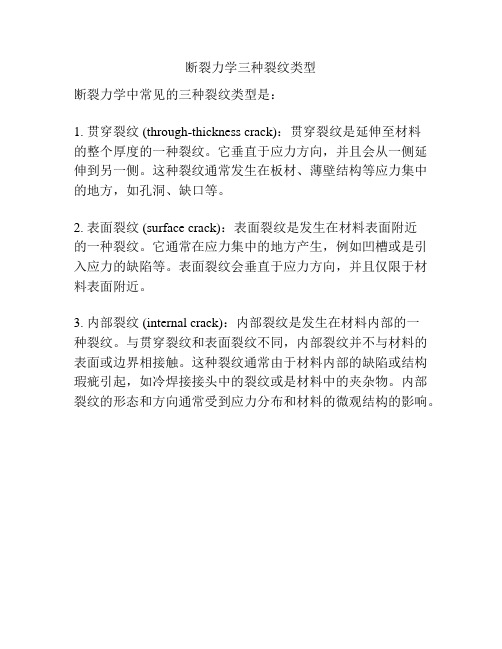
断裂力学三种裂纹类型
断裂力学中常见的三种裂纹类型是:
1. 贯穿裂纹 (through-thickness crack):贯穿裂纹是延伸至材料
的整个厚度的一种裂纹。
它垂直于应力方向,并且会从一侧延伸到另一侧。
这种裂纹通常发生在板材、薄壁结构等应力集中的地方,如孔洞、缺口等。
2. 表面裂纹 (surface crack):表面裂纹是发生在材料表面附近
的一种裂纹。
它通常在应力集中的地方产生,例如凹槽或是引入应力的缺陷等。
表面裂纹会垂直于应力方向,并且仅限于材料表面附近。
3. 内部裂纹 (internal crack):内部裂纹是发生在材料内部的一
种裂纹。
与贯穿裂纹和表面裂纹不同,内部裂纹并不与材料的表面或边界相接触。
这种裂纹通常由于材料内部的缺陷或结构瑕疵引起,如冷焊接接头中的裂纹或是材料中的夹杂物。
内部裂纹的形态和方向通常受到应力分布和材料的微观结构的影响。
钢材 内部裂纹

钢材内部裂纹
钢材的内部裂纹可能是由于多种原因引起的,这些原因可以包括制造过程中的缺陷、应力超载、热处理问题等。
以下是一些可能导致钢材内部裂纹的常见原因:
1.不均匀冷却:在热处理过程中,如果钢材不均匀冷却,可能导致内部应力集中,从而引起裂纹。
2.过快的冷却速度:快速冷却可能导致组织结构的不均匀性,增加内部应力,从而引发裂纹。
3.合金元素含量过高或过低:合金元素的含量不适当可能导致组织结构的异常,从而增加裂纹的风险。
4.不当的退火处理:不适当的退火条件可能导致晶粒的异常长大,使材料更加脆弱,容易发生裂纹。
5.金属中的夹杂物:金属中的夹杂物可能成为裂纹的起始点,特别是当夹杂物与金属基体的性质有较大差异时。
6.应力腐蚀裂纹:长时间暴露在有害环境中,结合应力的作用,可能引发应力腐蚀裂纹。
7.过度的机械加载:长时间或过度的机械加载可能导致应力积累,引起裂纹。
要解决钢材内部裂纹的问题,通常需要在制造和处理过程中采取适当的
措施,例如精确控制冷却速度、合理设计合金配比、优化退火工艺等。
同时,对于使用过程中的应力情况也需要注意,以防止过度的机械加载或应力腐蚀裂纹的发生。
木材开裂原因及基本解决方法
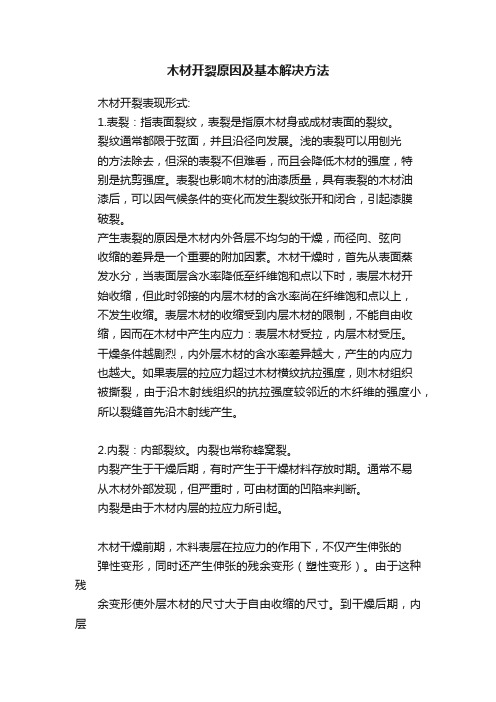
木材开裂原因及基本解决方法木材开裂表现形式:1.表裂:指表面裂纹,表裂是指原木材身或成材表面的裂纹。
裂纹通常都限于弦面,并且沿径向发展。
浅的表裂可以用刨光的方法除去,但深的表裂不但难看,而且会降低木材的强度,特别是抗剪强度。
表裂也影响木材的油漆质量,具有表裂的木材油漆后,可以因气候条件的变化而发生裂纹张开和闭合,引起漆膜破裂。
产生表裂的原因是木材内外各层不均匀的干燥,而径向、弦向收缩的差异是一个重要的附加因素。
木材干燥时,首先从表面蒸发水分,当表面层含水率降低至纤维饱和点以下时,表层木材开始收缩,但此时邻接的内层木材的含水率尚在纤维饱和点以上,不发生收缩。
表层木材的收缩受到内层木材的限制,不能自由收缩,因而在木材中产生内应力:表层木材受拉,内层木材受压。
干燥条件越剧烈,内外层木材的含水率差异越大,产生的内应力也越大。
如果表层的拉应力超过木材横纹抗拉强度,则木材组织被撕裂,由于沿木射线组织的抗拉强度较邻近的木纤维的强度小,所以裂缝首先沿木射线产生。
2.内裂:内部裂纹。
内裂也常称蜂窝裂。
内裂产生于干燥后期,有时产生于干燥材料存放时期。
通常不易从木材外部发现,但严重时,可由材面的凹陷来判断。
内裂是由于木材内层的拉应力所引起。
木材干燥前期,木料表层在拉应力的作用下,不仅产生伸张的弹性变形,同时还产生伸张的残余变形(塑性变形)。
由于这种残余变形使外层木材的尺寸大于自由收缩的尺寸。
到干燥后期,内层木材的含水率降至纤维饱和点以下时,内层木材开始收缩,但由于已经伸张了的外层木材的限制不能自由收缩,于是在材料中发生与干燥前期相反的内应力:内层木材受拉,外层木材受压。
如果内层的拉应力超过木材横纹抗拉强度,则木材组织被撕裂,木材的内裂因此产生。
3.端裂:端面裂纹。
端裂或仅限于木材的端面,或延伸至端部的一侧或两侧,后者通常称为劈裂。
主要原因是由于木材顺纹方向的导水性远远大于横纹方向,当木材干燥时,水分从端面的蒸发要比从侧面蒸发快得多。
模具钢淬火中的裂纹分析及解决方案
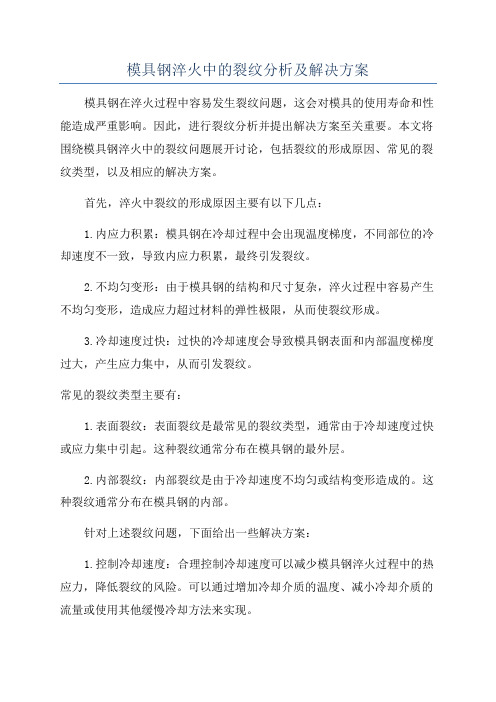
模具钢淬火中的裂纹分析及解决方案模具钢在淬火过程中容易发生裂纹问题,这会对模具的使用寿命和性能造成严重影响。
因此,进行裂纹分析并提出解决方案至关重要。
本文将围绕模具钢淬火中的裂纹问题展开讨论,包括裂纹的形成原因、常见的裂纹类型,以及相应的解决方案。
首先,淬火中裂纹的形成原因主要有以下几点:1.内应力积累:模具钢在冷却过程中会出现温度梯度,不同部位的冷却速度不一致,导致内应力积累,最终引发裂纹。
2.不均匀变形:由于模具钢的结构和尺寸复杂,淬火过程中容易产生不均匀变形,造成应力超过材料的弹性极限,从而使裂纹形成。
3.冷却速度过快:过快的冷却速度会导致模具钢表面和内部温度梯度过大,产生应力集中,从而引发裂纹。
常见的裂纹类型主要有:1.表面裂纹:表面裂纹是最常见的裂纹类型,通常由于冷却速度过快或应力集中引起。
这种裂纹通常分布在模具钢的最外层。
2.内部裂纹:内部裂纹是由于冷却速度不均匀或结构变形造成的。
这种裂纹通常分布在模具钢的内部。
针对上述裂纹问题,下面给出一些解决方案:1.控制冷却速度:合理控制冷却速度可以减少模具钢淬火过程中的热应力,降低裂纹的风险。
可以通过增加冷却介质的温度、减小冷却介质的流量或使用其他缓慢冷却方法来实现。
2.合理设计模具结构:模具的设计结构应该避免尖角和过于薄壁的部位,以减少应力集中导致的裂纹。
在可能的情况下,可以添加过渡圆角和半径,有助于减少裂纹的风险。
3.适当的预处理:通过适当的热处理工艺可以改善模具钢的力学性能和织构,减少应力集中和变形,降低裂纹的发生。
这包括应用回火、退火和正火等热处理方法。
4.使用有效的质量控制措施:在制造模具钢过程中,需要严格控制原材料的质量,以确保材料的均匀性和稳定性。
此外,必须严格控制加工中的工艺参数,以确保产品的质量。
总结起来,模具钢淬火中的裂纹问题对模具的使用寿命和性能都有很大的影响。
针对裂纹的形成原因和类型,我们可以通过控制冷却速度、合理设计模具结构、适当的预处理和使用有效的质量控制措施等方面来解决这一问题。
- 1、下载文档前请自行甄别文档内容的完整性,平台不提供额外的编辑、内容补充、找答案等附加服务。
- 2、"仅部分预览"的文档,不可在线预览部分如存在完整性等问题,可反馈申请退款(可完整预览的文档不适用该条件!)。
- 3、如文档侵犯您的权益,请联系客服反馈,我们会尽快为您处理(人工客服工作时间:9:00-18:30)。
Yamanaka研究所用拉伸装置示意图 Yamanaka研究所用拉伸装置示意图
得出的临界应变分歧较大,在0.5~3.8%之间。 得出的临界应变分歧较大, 0.5~3.8%之间。
10
杉古泰夫研究用小钢锭弯曲装置示意图
11
当应变速率在1×10-4~ 当应变速率在1 /s之间时 之间时, 3×10-4/s之间时,形成 内部裂纹的临界应变随 应变速率的增加而降低, 应变速率的增加而降低, 即高的应变速率有利于 内部裂纹的生成。 内部裂纹的生成。 对于低碳钢, 对于低碳钢,形成内部 裂纹的最低临界应变在 1.7%左右。 1.7%左右。
13
[C]含量增加,临界应变降低; [C]含量增加,临界应变降低; 含量增加 硫含量增加,临界应变降低。 磷、硫含量增加,临界应变降低。
横向弯曲拉伸试验得出的临界应变量
临界应变量,% (变形速率,1.3/s)
钢种
0.08%C-(0.14%Si-0.28%Mn) 0.16%C-( “ ) 0.30%C-( “ ) 0.50%C-( “ )
D + δ k ) ⋅θ k 圆弧 AB=( Rk − 2 D BC=( Rk +1 − + δ k +1 ) ⋅θ k +1 2
(1) (2) (3)
θ k ⋅ Rk = θ k +1 ⋅ Rk +1 = LL
将(2)、(3)、(4)代入(1)式, (2)、(3)、(4)代入(1)式 代入(1)
20
临界应变量,% (变形速率,0.0005/s) 约为 4.0 2.0 3.0 2.0 1.5 1.0
小钢锭弯曲试验得出的临界因变量
钢种 (0.13 ~ 0.19)C-(0.24 ~ 0.27)Si-(0.70 ~ 0.84)Mn-(0.008 ~ 0.02)P-(0.009~0.018)S (0.15 ~ 0.17)C-(0.41 ~ 0.48)Si-(1.31 ~ 1.39)Mn-(0.001 ~ 0.012)P-(0.012~0.019)S (0.42 ~ 0.47)C-(0.31 ~ 0.34)Si-(0.84 ~ 0.89)Mn-(0.01 ~ 0.02)P-(0.012~0.018)S 临界因变量,% > 2.0
Yamanaka研究结果([C]:0.15%,Mn: Yamanaka研究结果([C]:0.15%,Mn:0.65%) 研究结果([C] %,Mn
12
当应变速率在1×10-3/s时,形成内部裂纹的临界变形在 当应变速率在1 /s时 1.5%左右。 1.5%左右。
神户制钢安中弘行等小钢锭弯曲试验的研究结果
பைடு நூலகம்23
鼓肚变形的应变量计算
解析计算和有限元计算; 解析计算和有限元计算; 弹性、弹塑性、蠕变理论等。 弹性、弹塑性、蠕变理论等。 简化计算方法: 简化计算方法:
p ⋅ l 4+ β δ=C1 E S 3v β t g
B φ D
Sδ ε = C2 2 l
> 2.0
1.0~1.5
15
不同碳含量钢生成内部裂纹的临界因变量
碳含量,% < 0.1% 0.1~0.2% > 0.2~0.5% > 0.5%
临界应变,% 约 5.0~2.0 4.5~1.5 3.5~1.0 1.0~0.5
16
凝固界面所受应力分析
热应力: 热应力:沿宽度和长度方向坯壳截面上的温度分布是不均 匀的,由此会造成热应力。 匀的,由此会造成热应力。 矫直应力:矫直过程凝固界面由此会经受矫直应力。 矫直应力:矫直过程凝固界面由此会经受矫直应力。 附加机械应力:连铸机使用过程夹辊表面会磨损。铸坯在 附加机械应力:连铸机使用过程夹辊表面会磨损。 夹辊中运行时, 夹辊中运行时,某些辊子由于刚度不够会 产生弯曲变形。 产生弯曲变形。此外夹辊安装中还会存在 对中、对弧精度的偏差, 对中、对弧精度的偏差,由此均会造成铸 坯凝固截面经受上述原因造成的应力。 坯凝固截面经受上述原因造成的应力。
7
裂纹开裂面光滑,呈自由收缩表面形状,表明裂纹开裂时界 裂纹开裂面光滑,呈自由收缩表面形状, 面处于液态。 面处于液态。
8
内部裂纹的成因
凝固前沿受到的拉应力引发的应变超过了其抵抗裂纹产生 的最大变形(裂纹产生的临界应变量) 的最大变形(裂纹产生的临界应变量),凝固前沿就会沿枝 晶界面开裂,形成内部裂纹。 晶界面开裂,形成内部裂纹。
凝固前沿变形: 凝固前沿变形:
鼓肚; 鼓肚; 弯曲、矫直; 弯曲、矫直; 设备误差引发的变形。 设备误差引发的变形。
9
内部裂纹产生的临界应变
对于形成内部裂纹的临界 应变已有许多的研究, 应变已有许多的研究,所 采用的方法主要有两种, 采用的方法主要有两种, 一种是采用数学模拟的方 法,更多的是采用带液芯 小钢锭弯曲、 小钢锭弯曲、拉伸热模拟 试验的方法。 试验的方法。
(4)
(1 − Rk / Rk +1 )(D / 2 − δ k +1 ) ε k +1 =
Rk − D / 2 + δ k
由于: 由于:
Rk >> D / 2 − δ k
所以有: 所以有:
1 D 1 ε k +1 = − δ k +1 − R R 2 k k +1
2001 Steelmaking Conference Proceedings, Vol.84, p177 28
ε 总=ε 鼓肚+ε 错位+ε 矫直
住友金属鹿岛厂3 住友金属鹿岛厂3#板坯连铸机设计变形率
29
裂纹形成的温度区间
◆内部裂纹形成于 1410~1480℃之 1410~1480℃之 间; ◆内部裂纹发生时 的固相率fs fs在 的固相率fs在0.8 0.99之间 之间; ~0.99之间; ◆与该固相率区间 相对应的温度范 围在零强度温度 ZST和零延性温 ZST和零延性温 ZDT之间 之间。 度ZDT之间。在 该温度区间, 该温度区间,凝 固前沿为糊状区。 固前沿为糊状区。
2
3
内部裂纹一般发生在树枝晶一次晶轴间的晶界处
4
内裂纹的产生往往伴随严重偏析
沿照片中α→β路径的成分变化 沿照片中α→β路径的成分变化 α→β
5
成分
C
分析位置 A 点(铁素体) B 点(珠光体) C 点(珠光体) 铁素体 珠光体 0.04 0.52 0.54 0.05 0.51 0.18
Si
低硫(0.004%) 低磷(0.01%) 5.0 4.5 3.5 2.0
高硫(0.02%) 低磷(0.01%) 4.2 4.0 1.5 1.3
低硫(0.004%) 高磷(0.02%) 4.9 4.5 2.0 1.6
连续铸造における力学的举动,铁钢基础共同研究会,1985年5月,p3
14
局部熔化弯曲试验得出的临界因变量
6
凝固前沿尚未凝固的含较高杂质含量的钢水向裂纹处充 由此造成了内部裂纹伴随严重偏析的现象。 填,由此造成了内部裂纹伴随严重偏析的现象。
新日铁Fujii等加入Au 新日铁Fujii等加入Au198 Fujii等加入 的试验结果
TETSU-TOTETSU-TO-HAGANE, 62(1976), 1813
17
鼓肚应力: 鼓肚应力:
当铸坯在夹辊之间运行时,在相邻夹辊中心位置处, 当铸坯在夹辊之间运行时,在相邻夹辊中心位置处,坯壳的 内表面(凝固前沿)产生的应力为压应力, 内表面(凝固前沿)产生的应力为压应力,坯壳外表面产生的 应力为拉应力。 应力为拉应力。 当鼓肚后的坯壳进入下一对夹辊时,在夹辊与铸坯接触表面, 当鼓肚后的坯壳进入下一对夹辊时,在夹辊与铸坯接触表面, 坯壳内表面所受应力为拉应力,外表面所受应力为压应力。 坯壳内表面所受应力为拉应力,外表面所受应力为压应力。 铸坯在夹辊之间是连续 运动的, 运动的,因此坯壳将发 生鼓肚-压回- 生鼓肚-压回-鼓肚的 循环, 循环,凝固前沿所受应 力也将相应地发生压缩 拉伸- -拉伸-压缩的循环变 化。
21
一点矫直凝固前沿应变: 一点矫直凝固前沿应变:
D 1 ε = -δ ⋅ ×100% 2 R
D:铸坯厚度; 铸坯厚度; 坯壳厚度; δ:坯壳厚度; 铸机弧半径。 R:铸机弧半径。
多点矫直凝固前沿的应变: 多点矫直凝固前沿的应变:
ε k ,k +1
1 D 1 = -δ k +1i − R R ×100% 2 k k +1
δ:最大鼓肚量 ε:最大鼓肚应变 p:单位面积载荷 : l:辊间距 : Et:有效弹性模量 S:坯壳厚度 : vg:拉速 B:铸坯宽度 : D:铸坯厚度 : C1、C2、Φ、β:与钢种和温度有关常数 24
Fujii等基于蠕变模型计算得出的鼓肚应变 Fujii等基于蠕变模型计算得出的鼓肚应变
TETSU-TO-HAGANE, 62(1976), 1813
辊子不对中(错位)造成 辊子不对中(错位) 的坯壳变形: 的坯壳变形:
300Sδ t εm = 2 l
辊子不对中应变,% εm:辊子不对中应变,% S:坯壳厚度 : δt:错位量 l:辊间距 辊间距
27
实际生产中的铸机设备状况非常重要
Mostert等利用3D模型计算得出的5点矫直辊的受力情况 Mostert等利用3D模型计算得出的5 等利用3D模型计算得出的
25
Mostert等实测结果 Mostert等实测结果
1/4宽度处附近鼓肚量 1/4宽度处附近鼓肚量 最大; 最大; 测出的最大鼓肚量在 0.3mm左右。 0.3mm左右。 左右
2001 Steelmaking Conference Proceedings, Vol.84, p177
26
辊列精度、磨损等造成的应变 辊列精度、