表面处理工艺方法及其检测
铜材表面处理工艺的几大方法

铜材表面处理工艺的几大方法铜材作为一种常用的金属材料,在工业生产和日常生活中都有广泛的应用。
为了提高铜材的耐腐蚀性、美观性和机械性能,常常需要对其表面进行处理。
下面将介绍几种常见的铜材表面处理工艺方法。
1. 酸洗酸洗是一种常用的铜材表面处理方法,通过将铜材浸泡在酸性溶液中,可以去除表面的氧化物、油污和其他杂质。
常用的酸洗溶液包括硫酸、盐酸和硝酸等。
酸洗可以有效地清洁铜材表面,提高其表面质量。
2. 电镀电镀是一种将金属离子沉积在铜材表面的方法,可以改善铜材的外观和性能。
常见的电镀方法包括镀铬、镀镍和镀锡等。
电镀可以增加铜材的耐腐蚀性、硬度和光泽度,同时还可以改变其颜色和外观。
3. 化学氧化化学氧化是一种通过在铜材表面形成氧化层来改变其性质的方法。
常见的化学氧化方法包括氧化铜和氧化铝等。
化学氧化可以增加铜材的耐腐蚀性和耐磨性,同时还可以改变其颜色和外观。
4. 喷砂喷砂是一种通过高速喷射砂粒来冲击铜材表面的方法,可以去除表面的氧化物、污渍和毛刺。
喷砂可以使铜材表面变得光滑均匀,提高其美观性和质量。
5. 涂层涂层是一种在铜材表面形成保护层的方法,可以提高其耐腐蚀性和耐磨性。
常见的涂层材料包括漆料、涂料和涂膜等。
涂层可以改变铜材的颜色和外观,同时还可以增加其表面硬度和耐候性。
铜材表面处理工艺有酸洗、电镀、化学氧化、喷砂和涂层等几种常见方法。
这些方法可以改善铜材的表面质量、耐腐蚀性和美观性,使其在各个领域得到更广泛的应用。
在实际应用中,可以根据具体需求选择适合的表面处理工艺,以达到最佳效果。
表面处理通用检验标准
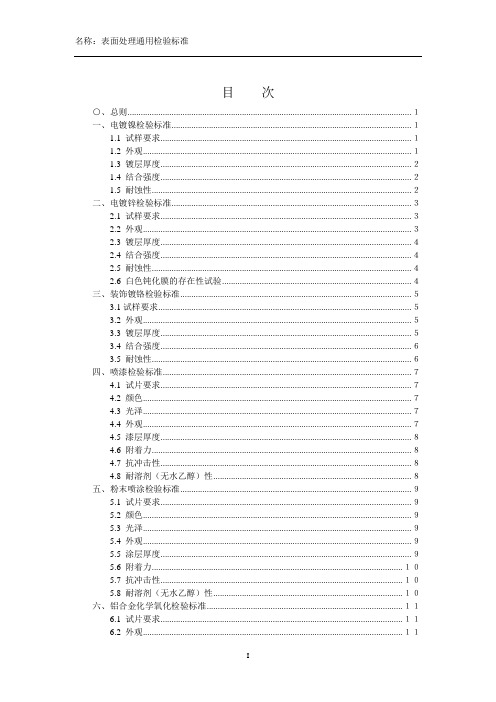
目次○、总则................................................................................................................................. 1一、电镀镍检验标准............................................................................................................. 11.1 试样要求.................................................................................................................. 11.2 外观.......................................................................................................................... 11.3 镀层厚度.................................................................................................................. 21.4 结合强度.................................................................................................................. 21.5 耐蚀性...................................................................................................................... 2二、电镀锌检验标准............................................................................................................. 32.1 试样要求.................................................................................................................. 32.2 外观.......................................................................................................................... 32.3 镀层厚度.................................................................................................................. 42.4 结合强度.................................................................................................................. 42.5 耐蚀性...................................................................................................................... 42.6 白色钝化膜的存在性试验...................................................................................... 4三、装饰镀铬检验标准......................................................................................................... 53.1试样要求................................................................................................................... 53.2 外观.......................................................................................................................... 53.3 镀层厚度.................................................................................................................. 53.4 结合强度.................................................................................................................. 63.5 耐蚀性...................................................................................................................... 6四、喷漆检验标准................................................................................................................. 74.1 试片要求.................................................................................................................. 74.2 颜色.......................................................................................................................... 74.3 光泽.......................................................................................................................... 74.4 外观.......................................................................................................................... 74.5 漆层厚度.................................................................................................................. 84.6 附着力...................................................................................................................... 84.7 抗冲击性.................................................................................................................. 84.8 耐溶剂(无水乙醇)性.......................................................................................... 8五、粉末喷涂检验标准......................................................................................................... 95.1 试片要求.................................................................................................................. 95.2 颜色.......................................................................................................................... 95.3 光泽.......................................................................................................................... 95.4 外观.......................................................................................................................... 95.5 涂层厚度.................................................................................................................. 95.6 附着力.................................................................................................................. 105.7 抗冲击性.............................................................................................................. 105.8 耐溶剂(无水乙醇)性...................................................................................... 10六、铝合金化学氧化检验标准......................................................................................... 116.1 试片要求.............................................................................................................. 116.2 外观...................................................................................................................... 116.3 耐蚀性.................................................................................................................. 11七、铝合金喷砂光亮阳极化检验标准............................................................................. 127.1 试片要求.............................................................................................................. 127.2 外观...................................................................................................................... 127.3 氧化膜厚度.......................................................................................................... 127.4 耐蚀性.................................................................................................................. 127.5 封闭质量.............................................................................................................. 12八、喷砂及拉丝检验标准................................................................................................. 138.1 拉丝件.................................................................................................................. 138.2 喷砂件.................................................................................................................. 13表面处理通用检验标准○、总则0.1 零部件表面处理前应去除毛刺、飞边、划痕、氧化层等缺陷,锐边棱角倒钝。
热处理中的表面处理工艺及其应用

热处理中的表面处理工艺及其应用热处理是指通过加热和冷却的过程改变材料的性质和结构,以提高材料的硬度、强度和耐磨性等特性。
在热处理中,表面处理是一个关键的环节,它可以对材料的表面进行改良,增强其耐磨、耐腐蚀等性能。
本文将重点介绍热处理中的表面处理工艺及其应用。
一、淬火和回火淬火和回火是热处理中最常用的表面处理工艺之一。
淬火是指将材料加热到临界温度以上,然后迅速冷却,使材料表面形成马氏体结构,提高材料的硬度和强度。
而回火则是在淬火后将材料加热到较低的温度并保持一段时间,以减轻淬火带来的内应力和脆性,提高材料的韧性和可加工性。
淬火和回火广泛应用于钢材、合金材料等的表面处理和强化。
二、氮化处理氮化处理是一种将材料表面与氮元素发生化学反应,形成氮化物薄膜的表面处理工艺。
氮化处理可以显著提高材料的硬度、耐磨性和耐腐蚀性能。
常见的氮化处理包括气体氮化、离子氮化和盐浴氮化等。
氮化处理在汽车零部件、模具制造以及航空航天等领域有广泛的应用。
三、电镀电镀是一种透过将金属离子置于电解质溶液中,然后利用电解作用,在导电的基材上沉积所需的金属薄膜的表面处理工艺。
电镀可以改善材料表面的电导性、耐磨性和抗腐蚀能力。
常见的电镀方法包括镀铬、镀镍、镀锌等。
电镀广泛应用于汽车制造、电子设备以及装饰品制作等行业。
四、渗碳处理渗碳处理是一种通过将材料浸入具有高碳含量的介质中,使其表面碳原子浸渗进入材料内部形成高碳浓度层的表面处理工艺。
渗碳处理可以显著提高材料的硬度、耐磨性和疲劳寿命。
常见的渗碳处理方法包括气体渗碳、盐浴渗碳和液体渗碳等。
渗碳处理广泛应用于汽车零部件、机械设备以及工具制造等领域。
五、喷涂喷涂是一种利用喷枪将涂料、涂敷剂等喷射到材料表面形成涂层的表面处理工艺。
喷涂可以改善材料的耐磨性、耐高温性和防腐性能。
常见的喷涂方法包括喷漆、喷粉末和喷涂保温涂料等。
喷涂广泛应用于汽车制造、建筑装饰以及航空航天等领域。
六、机械加工机械加工是一种通过对材料表面进行切削、锉磨、打磨等加工方法,以改善材料表面的粗糙度和平整度的表面处理工艺。
钣金件表面处理主要工艺方法介绍

表面处理工艺表面处理技术介绍一、什么叫做表面处理表面处理:以最经济和最有效的方法改变产品表面及近表面区的形态、化学成分和组织结构,有效地改善和提高产品的装饰性能、耐腐蚀性能和耐磨性能,延长产品的使用寿命。
常见的表面处理:电镀,化学镀,转化膜技术,物理气相沉积,化学气相沉积,热喷涂,热浸镀,喷砂,化学转化,阳极氧化,涂装等;表面处理技术还能赋予材料表面各种光、电、磁、热、声、化学以及功能转换等特性。
1.各种光的表面技术:镜子;防反光;2.各种电的表面技术:绝缘的镀银,金,铜;导电的用塑料保护3.各种磁的表面技术:隐身技术(重点)4.热的表面技术:红外,吸收红外,防热;5.声的表面技术:防声纳6.化学:钢材镀锌表面处理的种类表面处理根据产品的使用要求可以分为:防护型表面处理,如电镀、氧化(化学氧化、电化学氧化)、装饰型表面处理(如涂装、、功能型表面处理,总的来说,没有明显的划分界限,其主要目的是延长产品的使用寿命,最大程度的节省和利用资源。
二、钣金加工中为什么要进行表面处理?1.钣金加工所用的材料多为冷轧板、热轧板、电解板、白口铁、不锈钢、铝合金板及型材、铜材等,这些材料暴露在大气中,与空气中的水分和氧充分接触后,会发生电化学反应,从而造成材料表面腐蚀,同时物理及化学性质不同的材料间相互接触也会由于彼此间的电位差而形成原电池,从而造成接触腐蚀。
为避免钣金加工中材料在各加工工序间及成品在存放及使用中发生腐蚀,生产中通过对材料进行表面处理方式来控制腐蚀的产生或延缓腐蚀的产生,从而减少由于腐蚀的产生而造成产品返修或报废,尽可能地节约资源及生产成本。
2.各种材料经过钣金加工转化为商品时,为了满足顾客的需求及商品给予人视觉上的美感,就对产品外观作各种表面处理,如电镀、氧化着三、在钣金加工业中铝合金材料通常需进行哪些表面处理?在钣金加工业中,铝合金材料通常需进行以下表面处理:无色化学氧化、黑色化学氧化、金黄色化学氧化、拉丝无色化学氧化、喷砂无色化学氧化、光亮无色化学氧化、喷砂光亮阳极氧化、化学氧化着色、化学氧化后涂装(喷漆、喷粉),其中氧化层有导电与绝缘两种;硬质、耐磨等;前处理四、磷化工艺A、磷化工艺流程:预脱脂----脱脂----流动水洗----流动水洗----表调----磷化----流动水洗----流动水洗----纯水洗----烘干B、前处理生产线喷淋线、浸泡线装生产前为何要进行磷化处理?1、磷化是通过化学的方法使铁基材或锌基材与磷酸盐发生反应而生成一层致密的化学转化膜的过程。
塑胶表面处理工艺测试方法

塑胶表面处理工艺测试方法
塑胶表面处理工艺的测试方法主要包括外观检验、涂层附着力测试和耐磨性测试。
外观检验主要通过目测和手感进行,以评估表面是否光滑、色泽均匀等。
涂层附着力测试通过百格试验进行,用刀片在涂层表面划出方格,然后贴上胶纸并迅速拉起,检查方格涂层的粘脱和损伤情况。
不同涂层厚度有不同的合格判定标准。
耐磨性测试主要通过纸带耐磨测试、振动耐磨测试和橡皮耐磨测试进行。
纸带耐磨测试使用专用的NORMAN RCA耐磨测试仪和纸带,施加一定载荷后,在样本表面摩擦一定循环次数,以油漆不透底为合格。
振动耐磨测试使用rosler振动耐磨测试仪和专用磨料,设定测试时间后进行摩擦,测试后加工涂膜的脱落最多允许4处。
橡皮耐磨测试使用专用橡皮擦在涂层表面摩擦一定圈数,印刷层不能出现图案不清晰或字体缺损为合格。
以上方法仅供参考,如需了解更多信息,建议咨询专业人士。
铜材表面处理工艺的几大方法

铜材表面处理工艺的几大方法
由于铜材材质的特点,其表面在空气中耐腐蚀性差,常常在潮湿的环境中更容易生锈,所以我们要对铜材进行表面处理,在这说说最新的几大铜材表面处理工艺。
一、按铜材表面的锈迹严重程度处理
1、锈迹严重的处理工艺:铜材脱脂剂→水洗→铜材酸洗抛光液→水洗→铜材铬钝化液→(水洗)→铜材护膜液。
2、锈迹轻微的处理工艺:铜材脱脂剂→水洗→超声波清洗剂→水洗→铜材铬钝化液→(水洗)→铜材护膜液。
3、只是稍微的一点点锈迹和油污的处理工艺:铜材除锈脱脂剂→水洗→铜材铬钝化液→(水洗)→铜材护膜液。
二、按铜材的材质分类
1、紫铜(即纯铜)的处理工艺有两种:铜材脱脂剂→水洗→铜材酸洗抛光液→水洗→铜材钝化液A→(水洗)→铜材护膜液铜材脱脂剂→水洗→铜材酸洗抛光液→水洗→铜材无铬钝化液→(水洗)→铜材护膜液。
2、黄铜、青铜、白铜的处理工艺:铜材脱脂剂→水洗→环保洗铜水→水洗→铜材铬钝化液→(水洗)→铜材护膜液。
三、按工件的特殊用途分类
1、工件后期需要导电、导热、焊接的处理工艺:铜材脱脂剂→水洗→铜材酸洗抛光液→水洗→铜材钝化液→(水洗)。
2、工件后期不需要导电、导热、焊接等的处理工艺:铜材脱脂剂→水洗→铜材酸洗抛光液→水洗→铜材钝化液→(水洗)→铜材护膜液。
四、按工件大小分类
1、小尺寸的工件处理工艺:铜材脱脂剂→水洗→铜材酸洗抛光液→水洗→铜材钝化液→(水洗)→铜材护膜液。
2、大尺寸的工件处理工艺:水洗→擦铜水→水洗。
常用表面处理方式及检验标准

电铸
电铸就是把预先按所需形状制成的原模作为阴极, 用电铸材料作为阳极,一同放入与阳极材料相同的金 属盐溶液中,通以直流电。在电解作用下,原模表面 逐渐沉积出金属电铸层,达到所需的厚度后从溶液中 取出,将电铸层与原模分离,便获得与原模形状相对 应的金属复制件。 电铸的主要用途是精确复制微细、复杂和某些难 于用其他方法加工的特殊形状模具及工件等,例如制 作纸币和邮票的印刷版、唱片压模、铅字字模、玩具 滚塑模、模型模具、金属艺术品复制件等。
挂镀即利用挂具吊挂制件进行的电镀,工件装 夹在挂具上,适宜大零件,每一批能镀的产品数量 少,镀层厚度10μ m以上的工艺。 优点 :挂镀适用于一般尺寸的制品, 挂镀时, 产品独立固定,过程中没有产品间的碰撞,产品表 面不会划伤。 缺点 :小的零件或不规则零件无法进行吊挂。
自动挂镀线
挂具
滚镀过程是这样的:将小零件装进滚筒内,零 件靠自身的重力作用将滚筒内的阴极导电装置紧紧 压住,然后,滚筒以一定的速度按一定的方向旋转, 零件在滚筒内受到旋转作用后不停地翻滚、跌落。 同时,金属离子受到电场作用后在零件表面还原为 金属镀层,滚筒外新鲜溶液连续不断地通过滚筒壁 板上无数的小孔补充到滚筒内,而滚筒内的旧液及 电镀过程中产生的氢气也通过这些小孔排出筒外。
2.电镀
2.1 电镀原理 2.2 电镀方式 2.3 电镀的检验标准
2.1 电镀原理
电镀是利用电解作用使金属或其它材料制件的 表面附着一层金属膜的工艺从而起到防止腐蚀,提 高耐磨性、导电性、反光性及增进美观等作用。 具体操作:电镀时,镀层金属或其他不溶性材 料做阳极,待镀的工件做阴极,镀层金属的阳离子 在待镀工件表面被还原形成镀层,含镀层金属阳离 子的溶液做电镀液,以保持镀层金属阳离子的浓度 不变。
NPMC表面处理工艺
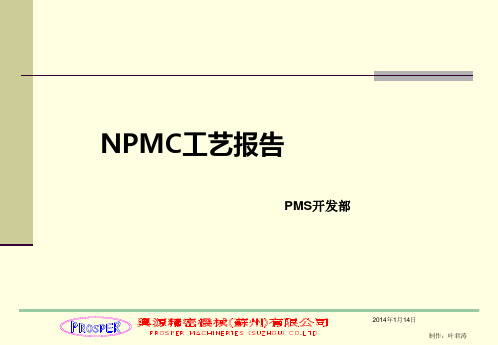
3. NPMC工艺能达到的工艺需求
4. NPMC与其他表面处理工艺对比
硬度
不能有划痕(铅笔下笔处除外)
百格
表面剥落≤5%
酒精 橡皮擦 耐污
表面不可見底材 不可露底材 测试区不能有污渍或褪色,不能有顏色印到 棉布上
3. NPMC工艺能达到的工艺需求
NPMC表面效果(外观)可覆盖业界PVD、阳极、ED、喷涂效果.
NPMC表面效果(颜色)多种色彩供客户选择,可做单色\双色\套色... 等,也可依客户喜好开发. NPMC应用 (素材)所有金属表面皆可处理,不会有金属析出问题 ,部分无感刮伤也可覆盖(依实际产品定义) NPMC非腐蚀性制程,是在产品表面覆盖纳米涂层,理论上0.1~0.6Ra 容易做到 NPMC制程色差可控范围△E≤0.7 NPMC制程光泽可控范围G值10~95度 NPMC制程光泽可控范围G值10~95度
备注:纳米原料是指乙酸、乙酯为溶剂及纳米镐为主体的原料
生产工艺及说明:
IQC→清洗→上色→IPQC→PVD →FQC→包装入库 →OQC。
清洗:无磷无碳无酸专用前处理剂(常温清洗) 上色:分喷涂\拉伸两种方式,无色差。 PVD:独特真空制程,披覆均匀(150~200℃)。
2.性能检测方式
项目 条件 温度20 ± 2℃,湿度55 ± 5% 带子速度:50mm/s,3000mm/min 固定载入:RCA系统175gf,3秒开/ 1秒关, 要求纸袋:60#密织平纹 6H三菱铅笔,持45°角度并加荷重750g直线向前移动约6.5mm. 以1.0mm切割导向辅助工具,用百格刀橫豎垂直各劃11條線. 每一條劃線必須露底材,後用3M-610粘貼.保證和薄膜有良好 的接觸,放置30min後,拿住膠帶末端,以盡可能接近180° 的角度,迅速的拉,以上動作最少重複20次 用粗綿布折貼後,蘸濕95%異丙醇加500g砝碼磨擦100回(一前一 後為一回). 使用EF74號橡皮,耐磨機荷重500g,300cycle 使用耐磨耗測驗機. 将橙汁×10 c.c /可樂×10 c.c /咖啡×10 c.c涂抹在产品表面上, 室温放置1H后用自来水冲洗,如污渍看得见使用肥皂液清洗 。 合格条件 RCA 50次不能见到底材
- 1、下载文档前请自行甄别文档内容的完整性,平台不提供额外的编辑、内容补充、找答案等附加服务。
- 2、"仅部分预览"的文档,不可在线预览部分如存在完整性等问题,可反馈申请退款(可完整预览的文档不适用该条件!)。
- 3、如文档侵犯您的权益,请联系客服反馈,我们会尽快为您处理(人工客服工作时间:9:00-18:30)。
经酸洗的工件,放入发黑槽中,20-25分钟,取出放入回收槽清洗后再放入发黑槽10-15分钟。
发黑到清洗再发黑这样重复也可多作几次,3-5次都行,视经验定。
一般情况下,不要在处理过程中加水,必要时再加,随着材料的的消耗应不断添加补充新配制溶液,按以下成份事先配制好:
表面处理工艺/方法及其检测:
术语
涂/镀层
通过电镀、化学镀、渗金属和非金属、铝合金阳极氧化、金属热喷涂、钢铁件化学氧化、喷涂有机或无机涂层等表面防腐处理工艺,在金属表面形成的保护层。
外观质量
外观质量检测应在天然散射光线或无反射光的白色透射线下目视检查。光照度应不低于300lx(即相当于零件放在40W日光灯下距离500mm处的光照度),必要时可以用3-5倍放大镜观察。
NaNO3含量过高,调整其含量。
酸洗后在空气中停留时间过长,可重新酸洗一次再发黑。
F、工件表面有白色斑或条纹:
去油去锈不良,可加强去油去锈工作。
工件互相挤靠,接触处氧化不足,注意翻动工件。
G、血红色的锈蚀斑点
酸洗或发黑时工件互相挤靠,可注意翻动工件。
五、发黑的质量检验
1、外观检查
浸油前后均应进行外观检查,用肉眼查氧化膜的外表,钢材成分不同氧化膜的色泽会有所不同,但都应均匀一致,不允许有花斑,未氧化的斑点及锈迹存在。
氯化钠
60
阴极性镀层
铝及其合金
铝试剂
3.5
10
氯化钠
150
注:1.除铝试剂为分析纯级外,其余均为化学纯级;2.除铝试剂、氯化钠溶液,其余检测溶液均应用棕色玻璃瓶盛装存放在阴暗处,当发现变黑或有悬浮物时,便不能再用。
1.3操作步骤
1.3.1.
检验前,镀层表面受检部位可用有机溶剂除油,若在镀覆后立即进行检验,可不必进行除油;
E、酸洗后应立即发黑,尽量避免在空气中的停留时间,以防止重新生锈
二、氧化处理
发黑液温度138-140℃(沸腾温度)
1升水中含NaOH 600克含NaNO3150克按此比例配制
配制发黑溶时应先将NaOH(火碱)分批加入一次不宜过多,等大部分溶解后再加入NaNO3。新配制的发黑液呈乳白色,但处理几筐后,则可能变成粉红色稍带蓝紫色,有的使用一段时间后变成豆黄色这都是正常的。
需要发黑的工件,表面必须光洁,不得有锈迹、油污块、氧化物及其他脏物。
(1)机械清理
A:表面有严重氧化物及锈斑者,需经手工打磨,滚磨或喷砂、喷丸处理。
B:一般工件上的脏物,洗涮掉即可;
(2)去油
A:有严重油污者,先用汽油或煤油浸洗15分钟以上,然后用清水洗净;
B:油迹较少者,在去油槽去油即可;
a、去油槽的成分:
发黑工艺流程如表:
工序
名称
溶液
工艺条件
备注
组成
含量k/L
温度℃
时间(分)
1
水冲洗
2
化学除油
Na3PO4
30-40
大于90
10-15分钟
NaOH
30-50
3
热水洗
大于80
4
冷水冲洗
清洗
用水管从上往下冲洗
5
酸洗
盐酸
15%
5-10分钟
表面氧化皮、锈迹不好时间加长
6
流动水洗
清洗
7
发黑
NaOH
600-700
135-145
1.3.3.2.为显示达到镍层的孔隙,将带有孔隙斑痕的检验滤纸放在洁净的玻璃板上,然后均匀的滴加二甲基乙二醛肟的氨水溶液(2克二甲基乙二醛肟溶于500毫升的氨水中),这时滤纸上镍的黄色斑点即变成玫瑰色斑点,用水洗净后干燥,到达钢或铜层的斑点会失去色彩,但不妨碍计算到镍层的孔隙数目。
1.3.3.3.检验最外层的镀铬层的镀层孔隙时,要在镀完铬30分钟后进行。对镀铜的钢件,铜及铜合金件上的松孔镀铬层在检验孔隙时,因直到铜及铜合金的孔隙痕迹不完全印在滤纸上,因此,应该计算在零件上呈现的红褐色斑点。
具有内覆盖层或外覆盖层的试样都可能发生变化。虽然在某些情况下,检查弯曲的内边可能看到更多的数据,但是,一般都是在试样的外边观察到覆盖层的性能。
4.11.拉力试验
这只适用于某些类型的镀覆零件。对零件施加拉伸应力直至断裂。断口附近的镀覆层一般都会显现出一些开裂。不应有镀覆层从基体金属上明显脱落的现象。
4.12.热震
1、涂层应均匀光滑、不粘手,不得有流挂、气泡等缺陷;
2、钢铁氧化件表面不允许有挂灰;不得有膜层损伤、氧化斑等缺陷;
3、镀层结晶细致、均匀,不得有表面粗糙、硬刺、烧焦等缺陷;不得产生树枝状、海绵状和条纹状结晶;
4、涂镀层不允许出现裂纹、起皮、起泡、脱落等缺陷;
5、允许由于热处理、焊接、表面加工状态不同,电镀层呈现不同颜色和光泽;允许有轻微水渍;
皂化时,皂沫应盖住液面。
四、常见的缺陷及补充防止办法:
A、工件表面挂有红色附着物:
温度过高或NaOH含量过高,可用加水降低温度或降低NaOH含量,已处理的工件应统一酸洗再发黑处理。
B、氧化铁(FeOH)过多,降低溶液温度可使FeOH溶解,已处理的工件不必酸洗,可继续发黑即可。
C、件表面挂有墨绿色附着物,清洗浸油后变为红色。
溶液温度过高,加水附着物洗去,则继续发黑,否则酸洗重新发黑。
NaNO3过高,这时可以看到氧化膜很薄,只要调整NaNO3的含量即可。
D、工件色浅或发灰
温度较低,时间不足,只要继续发黑即可。
NaNO3含量高,调整后继续发黑即可。
E、工件不上色
温度浓度过低,可按比例加入材料或加热让水分蒸发。
温度和浓度过高,加水即可。
1.4孔隙率的计算
将划有方格的玻璃板(方格面积为2厘米2),放在印有孔隙斑点的滤纸上,分别数出方格内包含各种颜色的斑点数,然后分别计算镀层到基体金属或下层镀层金属的孔隙率(斑点数/厘米2)。
2.溶液浇浸法
2.1方法原理
2.2检验溶液
2.3操作步骤
2.4孔隙率的计算
浇浸法使用的检验溶液的配制方法
3.涂膏法
同一零件,同一材料,因工艺方法不同而引起的氧化膜色泽不同。
喷钢丸
√
√
阴极处理
√
√
√
注:√表示覆盖层所适用的试验方法
4.1.摩擦抛光
4.2.钢球摩擦抛光
4.3.喷丸
4.4.剥离
4.5.锉刀
4.6.磨、锯
4.7.凿子
4.8.划线、划格
采用磨为30°锐刃的硬质钢划刀,相距约2mm划两根平行线。在划两根平行线时,应当以足够的压力一次刻线即穿过覆盖层切割到基体金属。如果在各线之间的任一部分的覆盖层从基体金属上剥落,则认为覆盖层未通过此试验。
铜
镍
镍+铬
银
锡
锡-镍合金
锌
金
摩擦抛光
√
√
√
√
√
√
√
√
√
钢球磨光
√
√
√
√
√
√
√
√
√
√
剥离(钎焊法)
√
√
√
√
剥离(粘结法)
√
√
√
√
√
√
√
√
锉刀
√
√
√
√
凿子
√
√
√
√
√
划痕
√
√
√
√
√
√
√
√
弯曲和缠绕
√
√
√
√
√
磨与锯
√
√
√
√
拉力
√
√
√
√
√
√
√
热震
√
√
√
√
√
√
深引(埃里克森)
√
√
√
√
√
深引(凸缘帽)
√
√
√
√
√
√
NaOH 240克;NaNO380克;水1升;
按经验发黑2-3次,加补溶液2升。
发黑液要保持清洁,浮渣用漏勺撇去,每星期停炉前将槽壁和槽底的渣除去。
三、氧化处理后的补充处理:
(1)发黑工件先放入回收槽回收从发黑槽带出的发黑液,回收槽中的水应保持干净,回收槽中的水亦可作为发黑槽的添加水,也可加入去油槽中。
厚度测量:
1、秤量法
2、磁性法
3、横截面显微镜法
4、阴极溶解库伦法
性质检测
1、耐蚀性能
1.1.醋酸盐雾
参照GB6459的规定进行。
试验方法:
要求:
1.2.二氧化硫腐蚀试验。
参照GB9789的规定进行。
试验方法:
要求:
2、耐磨性能
试验方法:
要求:
3、延伸率
4、结合力
适用于各种金属镀层的附着强度试验
镉
铬
方法是:将工件置于水中数秒,然后取出观察,若表面全部被浸湿,则去油质量良好,如工件表面水聚为不完整的水膜+水球状,则说明去油质量不良,应继续去油。合格才可转下道工序
(3)去锈:
A、酸洗溶液的成分及使用温度;
酸洗槽的溶液为:15%的盐酸溶液常温下使用,配制溶液时,应该将盐酸慢慢的倒入水中,切不可以将水猛的加入酸中,以免酸液喷溅伤人。
要求:
涂镀层厚度符合要求,不允许出现膨胀、松软等变化。
9、
10、
常见涂镀层:
镀铜
0.025-0.04
镀锌
0.010-0.015
镀锌镍合金
0.02-0.025或0.025-0.030
镀铬
0.05-0.07
化学沉积
电泳漆