双氧水装置事故分析案例
电化学车间双氧水未遂事故(NEM)报告

10
事故原因与分析
设备部件故障及其引发结果分析: • 3、从双氧水加液管和槽体变形部位分析,分解反应起于管道中部和槽底部。 现象分析:从事故引发的物理性变化来看,双氧水加液管中部和槽底部 变形最大。分析情况为:双氧水和氯化铜的溶和,在管道的中部达到临界值 ,从而引发分解反应,而此时泵阀因故障没有起到单向止回作用,分解后的 溶液流到槽的底部,从而引发更为剧烈的反应。
2
事故经过
• 在无人触动的情况下,储液槽内双氧水发生分解反应。 – 2012年12月27日,材料员领取280升双氧水,于当日用泵加入储液槽, 目前已使用了1月零3天,使用量为约为80升左右。 • 当日工作与现场情况。 – 上午蚀刻机正常工作。 – 下午1:30分左右发生分解反应。 – 下午2:30分左右已经将双氧水槽处理完毕。废弃的双氧水排入污水处理 站。 – 没有造成人员危害。
电化学车间储液槽内双氧水 发生分解反应未遂事故(NEM)报告
电化学车间 2013/02/01
事故经过
• 储液槽内双氧水,自然发生反应。 – 时间:2013年1月31日下午13:20 – 地点:电化学车间腐蚀间 – 事情经过:在腐蚀机正常工作期间,刘杏梅发现双氧水储液槽大量蒸 汽挥发,立刻向工段长报告,发现槽内双氧水已发生分解反应,槽体 温度较高,立即用自来水冲洗槽体降温。并指示张立华打开双氧水排 液阀门,用水冲洗。
3
事故报告与分析
• • 1月31日下午15时左右,接报告后,戴助理与乔森来到现场与技术人员 一起分析事故原因、指导工作。 2月1日下午,设备厂家保定蓝盾公司来到现场查看情况,与车间相关人 员和操作者一起讨论和分析事故原因。
4
事故原因与分析
原因分析: • 根据与设备厂家、化学品厂家和以往的综合实验情况分析,槽中的双氧水只 有在和重金属、有机物、氧化物、盐类、水等物质混合,达到其临界值时, 才会发生分解反应,且反应速度非常迅猛和剧烈。 从设备结构来看,异物进入双氧水槽的入口只有2个, 1、从槽原加液口进入。目前双氧水的灌装已改为机械泵和管道阀门连接 加液,无需打开原槽体加液口,所以,由此混入的可能性基本排除。 2、从蚀刻机溶液反向流入双氧水槽。从目前看到和分析的情况来看,此 种可能性最大。
双氧水储运事故案例

双氧水储运事故案例•2013年12月29日,山东省临沂市兰山区九州化工厂在一辆双氧水槽罐车卸料至多个双氧水包装桶过程中,一装满双氧水的包装桶发生爆炸,造成3人死亡,直接经济损失200余万元。
事故的直接原因是违规使用盛装过盐酸的塑料桶盛装双氧水,桶内残存的Fe3+及其他金属杂质引起双氧水急剧分解导致超压爆炸。
••2013年4月9日清晨6点45分左右,江苏金坛市区一家名为江苏蓝色星球环保科技股份有限公司的化工厂发生爆炸经调查,发生爆炸的是该厂R125车间一只1立方米的双氧水储罐。
爆炸未造成企业人员伤亡。
但爆炸引起的冲击波将周围部分建筑物门窗玻璃震碎,造成2人被玻璃划伤。
••2012年2月5日晚上6点45左右,天津市滨海新区塘沽一家化工厂内一双氧水储罐爆炸起火,大约22:00左右,火灾才被初步控制住。
••2011年7月23日凌晨2时15分许,山西省太原东兴装饰城的一间仓库内,一商户存贮的工业用双氧水,因为高温发生爆炸,事故现场瞬间被浓烟、大火吞噬,周边大量商铺的玻璃门窗被爆炸产生的巨大冲击波震碎。
所幸的是,没有人员在此次事故中受伤。
•双氧水储运要求1)包装和贮运双氧水应用塑料或不锈钢容器,且其上盖应设有防尘的排气口,以安全释放可能产生的气体,避免爆炸的产生。
2)双氧水是强氧化剂且有腐蚀性,所以应注意在贮运容器上涂刷GB190 中规定的“腐蚀性物品标志”,以及GB191 中规定的“ 向上标志”。
3)按氧化剂的运输规则,组织运输,防止剧烈振摇。
4)双氧水应存贮于阴凉、通风的库房中。
在贮运过程中,避免阳光直射或受热。
5)严禁与碱、金属及金属化合物、易燃品、还原剂等物品混存混运。
6)请勿直接用手接触双氧水,操作时应配戴塑胶手套,当双氧水沾染人体或溅入眼睛时,应立即用大量水冲洗或用3%的KMnO4 溶液冲洗。
7)若包装破裂渗漏或当外溢的双氧水与可燃物质接触时,应立即用大量水将其冲洗掉。
8)接触或贮存双氧水的设备和容器,应有足够大的排气口,以防设备憋压造成超压爆破而引起着火爆炸事故。
b4双氧水事故汇编最终版

配制釜R1501超压事故一、事故经过1998年8月操作人员在切换稀品贮槽V1305A/B时,误将进口阀全部关闭,致使双氧水由稀品分离器V1304溢流至废芳烃贮槽V1504,造成废芳烃贮槽V1504内的芳烃从顶部喷出,操作人员又将废芳烃贮槽V1504内的双氧水放入配制釜。
当时配制釜内存有碱性工作液,双氧水接触到碱性物质时,大量分解为水和氧气,放出大量的热,引起配制釜超温超压。
配制釜内的双氧水分解超压后,操作人员果断地打开了配制釜放空阀和底部排放阀,使配制釜快速卸压排料,避免了一起恶性爆炸事故发生。
二、原因分析操作人员误将双氧水放入盛有碱性工作液配制釜,使大量双氧水遇碱性工作液后急剧分解。
三、事故教训及防范措施1、针对误操作问题,加强技术培训,提高大家的责任心和技术水平。
2、岗位之间加强协调合作,职责分明。
3、配制釜加装安全阀,放空阀常开,釜内工作液随抽随洗,并严格交接。
氧化塔排污视镜炸裂事故一、事故经过1999年10月18日操作人员在氧化塔上塔排污时,关闭视镜下部阀门的瞬间视镜炸裂,操作人员及时关闭了上部切断阀,避免了重大事故的发生。
二、原因分析1、视镜为玻璃制品,又是冬季,冷热相激,玻璃炸裂。
2、排污管线较长,支撑少。
在关闭下部阀门时,扭力突然增大,玻璃炸裂。
3、排污视镜内是废双氧水,浓度较高,双氧水发生分解,关闭下阀时,压力突然升高,玻璃炸裂。
三、事故教训及防范措施针对炸裂的原因,为防止类似事故的发生,采取了以下措施:1、氧化塔排污阀上阀保持关闭状态,下阀保持全开或稍开状态。
2、排污时先开下阀再缓慢开上阀,缓慢排污,排完后关上阀。
3、排污视镜定期更换,并外加金属丝网,防止炸裂伤人。
萃取塔内双氧水分解事故一、事故经过2000年12月8日,双氧水装置检修后开车过程中,萃取塔内双氧水分解。
装置紧急停车,打开萃取塔紧急排放阀排放,打烂玻璃视镜排料卸压,避免了一起萃取塔爆炸事故发生。
二、原因分析1 、因工作液温度低,造成干燥塔液泛,工作液大量带碱,带碱后没有及时处理。
修改后的-双氧水车间事故案例统计分析

双氧水车间事故案例统计分析1、1997年7月萃取塔底部视镜坏,影响生产造成停车。
岗位:一楼岗位原因:萃取塔底部视镜安装变形紧固不均匀,温差变化大,在开车过程中造成视镜破裂。
现象:双氧水从底部视镜断裂处流出造成大量浪费。
安全处理措施:将萃取塔内双氧水全部放至视镜以下用不锈钢盲板代替视镜将视镜处盲死。
教训:两系统开车升温时一定要缓慢,尽量避免温度大起大落。
2、1997年10月萃取塔严重积料最低流量降至30立方/每小时难以维持生产。
岗位:原因:由于空气压力波动导致2#氧化液气液分离器出料不稳,氧化液中溶解少量的空气带入萃取塔,使萃取塔内产生大量气泡造成液泛致使积料的产生。
现象:萃取塔内有机层增厚,淹没降液管致使工作液在塔内积聚,纯水加不进造成大量带水。
安全处理措施:在氧化液2#气液分离器后加设氧化液槽和氧化液泵,使溶解的气体在槽内得到释放,增设氧化液泵后增加了工作液的上浮动力,使积料问题得到有效解决。
教训:3、1997年11月后处理出料不畅,影响系统流量。
岗位:一楼岗位原因:后处理白土床更换氧化铝时,没有彻底清理底部瓷球及杂物,使瓷球及杂物堵塞管道造成工作液流动不畅。
现象:工作液计量槽液位不好降,流量加不上,白土床出料不畅。
安全处理措施:及时清除堵塞物恢复正常生产。
教训:加强更换氧化铝时清理工作的检查,在扒氧化铝重新装填新氧化铝时一定要将瓷球及杂物清理干净并用纯水冲洗干净后再装填。
4、1998年4月触媒再生后效果不好,主要表现在氢化效率不好提。
岗位:主控岗位原因:触媒再生后没有将水分吹干,使触媒中水分超标,致使活性提不起来。
现象:氢化效率低安全处理措施:改用热氮气吹干触媒。
教训:再生后一定要用热氮气吹干,只有这样才能将触媒中的水分吹出,才能恢复触媒的活性。
5、1998年7月氢化液过滤器垫片损坏,造成跑料停车。
岗位:二楼岗位原因:氢化液过滤器垫片是石棉板,再加上过滤器进口压力超标,使垫片浸渍后变形承受不了压力造成垫片损坏造成跑料。
b4双氧水事故汇编最终版

配制釜R1501超压事故一、事故经过1998年8月操作人员在切换稀品贮槽V1305A/B时,误将进口阀全部关闭,致使双氧水由稀品分离器V1304溢流至废芳烃贮槽V1504,造成废芳烃贮槽V1504内的芳烃从顶部喷出,操作人员又将废芳烃贮槽V1504内的双氧水放入配制釜。
当时配制釜内存有碱性工作液,双氧水接触到碱性物质时,大量分解为水和氧气,放出大量的热,引起配制釜超温超压。
配制釜内的双氧水分解超压后,操作人员果断地打开了配制釜放空阀和底部排放阀,使配制釜快速卸压排料,避免了一起恶性爆炸事故发生。
二、原因分析操作人员误将双氧水放入盛有碱性工作液配制釜,使大量双氧水遇碱性工作液后急剧分解。
三、事故教训及防范措施1、针对误操作问题,加强技术培训,提高大家的责任心和技术水平。
2、岗位之间加强协调合作,职责分明。
3、配制釜加装安全阀,放空阀常开,釜内工作液随抽随洗,并严格交接。
氧化塔排污视镜炸裂事故一、事故经过1999年10月18日操作人员在氧化塔上塔排污时,关闭视镜下部阀门的瞬间视镜炸裂,操作人员及时关闭了上部切断阀,避免了重大事故的发生。
二、原因分析1、视镜为玻璃制品,又是冬季,冷热相激,玻璃炸裂。
2、排污管线较长,支撑少。
在关闭下部阀门时,扭力突然增大,玻璃炸裂。
3、排污视镜内是废双氧水,浓度较高,双氧水发生分解,关闭下阀时,压力突然升高,玻璃炸裂。
三、事故教训及防范措施针对炸裂的原因,为防止类似事故的发生,采取了以下措施:1、氧化塔排污阀上阀保持关闭状态,下阀保持全开或稍开状态。
2、排污时先开下阀再缓慢开上阀,缓慢排污,排完后关上阀。
3、排污视镜定期更换,并外加金属丝网,防止炸裂伤人。
萃取塔内双氧水分解事故一、事故经过2000年12月8日,双氧水装置检修后开车过程中,萃取塔内双氧水分解。
装置紧急停车,打开萃取塔紧急排放阀排放,打烂玻璃视镜排料卸压,避免了一起萃取塔爆炸事故发生。
二、原因分析1 、因工作液温度低,造成干燥塔液泛,工作液大量带碱,带碱后没有及时处理。
山东国金化工厂“8·25”双氧水车间较大爆炸事故调查报告
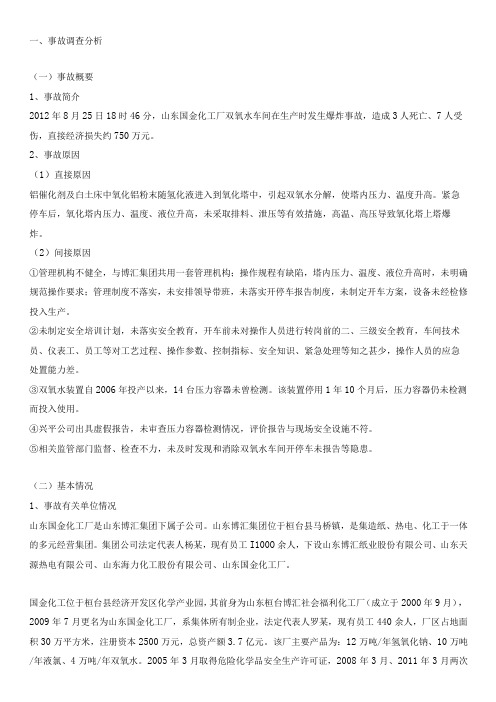
一、事故调查分析(一)事故概要1、事故简介2012年8月25日18时46分,山东国金化工厂双氧水车间在生产时发生爆炸事故,造成3人死亡、7人受伤,直接经济损失约750万元。
2、事故原因(1)直接原因铝催化剂及白土床中氧化铝粉末随氢化液进入到氧化塔中,引起双氧水分解,使塔内压力、温度升高。
紧急停车后,氧化塔内压力、温度、液位升高,未采取排料、泄压等有效措施,高温、高压导致氧化塔上塔爆炸。
(2)间接原因①管理机构不健全,与博汇集团共用一套管理机构;操作规程有缺陷,塔内压力、温度、液位升高时,未明确规范操作要求;管理制度不落实,未安排领导带班,未落实开停车报告制度,未制定开车方案,设备未经检修投入生产。
②未制定安全培训计划,未落实安全教育,开车前未对操作人员进行转岗前的二、三级安全教育,车间技术员、仪表工、员工等对工艺过程、操作参数、控制指标、安全知识、紧急处理等知之甚少,操作人员的应急处置能力差。
③双氧水装置自2006年投产以来,14台压力容器未曾检测。
该装置停用1年10个月后,压力容器仍未检测而投入使用。
④兴平公司出具虚假报告,未审查压力容器检测情况,评价报告与现场安全设施不符。
⑤相关监管部门监督、检查不力,未及时发现和消除双氧水车间开停车未报告等隐患。
(二)基本情况1、事故有关单位情况山东国金化工厂是山东博汇集团下属子公司。
山东博汇集团位于桓台县马桥镇,是集造纸、热电、化工于一体的多元经营集团。
集团公司法定代表人杨某,现有员工I100O余人,下设山东博汇纸业股份有限公司、山东天源热电有限公司、山东海力化工股份有限公司、山东国金化工厂。
国金化工位于桓台县经济开发区化学产业园,其前身为山东桓台博汇社会福利化工厂(成立于2000年9月),2009年7月更名为山东国金化工厂,系集体所有制企业,法定代表人罗某,现有员工440余人,厂区占地面积30万平方米,注册资本2500万元,总资产额3.7亿元。
该厂主要产品为:12万吨/年氢氧化钠、10万吨/年液氯、4万吨/年双氧水。
博汇及鲁西双氧水装置事故原因评析

2. 鲁 西 双 氧 水 火 灾 事 故 简 介 ↓ 现场 照片
13
2. 鲁 西 双 氧 水 火 灾 事 故 简 介 ↓ 现场 照片
14
2. 鲁 西 双 氧 水 火 灾 事 故 简 介 ↓ 现场 照片
15
2. 鲁 西 双 氧 火 灾 产 事 故 简 介 ↓ 现场 照片
16
2. 鲁 西 双 氧 水 火 灾 事 故 简 介 ↓ 现场 照片
9
1. 博 汇 双 氧 水 爆 炸 事 故 简 介 ↓ 现场 照片
10
2.鲁西双氧水“7.27”火灾事故简介
2013年7月27日16时45分左右,鲁西化工集团股份有限公司18 万吨/年双氧水生产装置的萃取塔发生火灾事故,直接经济损失约 200万元。这起事故虽未造成人员伤亡,但产生了较大社会影响( 网上传播、东方时空)。 鲁西化工集团股份有限公司是由原鲁西化肥厂(1976年建厂) 逐步发展起来的国有大型化工企业,总部位于聊城高新技术开发区 鲁西化工园区,总资产159亿元,职工11000余人。 发生事故的18万吨/年双氧水生产装置由聊城市鲁西化工工程 设计有限公司设计,鲁西工业装备有限公司安装,2013年6月5日取 得试生产方案备案告知书,7月25日开始投料试生产。
19
1.技术层面的事故原因分析
(1)系统内杂质的存在是造成双氧水分解加速的原因。
2
前言:博汇及鲁西双氧水事故简介
1.博汇“8.25”双氧水爆炸事故简介
2012年8月25日18时46分许,博汇集团山东国金化工厂4万吨/ 年双氧水生产装置在停车过程中发生爆炸事故,造成3人死亡,7 人受伤,伤亡损失惨重,社会影响较大。 ☆ 距爆炸事故80m范围内的所有玻璃全部震碎; ☆ 爆炸物将500m以外的液氨球罐顶部阀门砸坏,罐内液氨全 部泄漏,持续泄漏长达36小时左右。
双氧水装置事故分析案例

企业和当地政府迅速启动应急预案扑救火灾;27日20时左右火势
得到有效控制;28日3时36分火灾被全部扑灭; 清净下水全部封堵在厂
区内并导入环境安全应急池;经环保部门对大气和周边水体检测;未发
现有毒有害物质和水体污染;
10
鲁西双氧水7 27火灾事故
2
鲁
西
双
氧
水
火
灾
事
故
简
介
↓
现场
照片
11
鲁西双氧水7 27火灾事故
氧化反应;为过氧化工艺;也属于重点监管的危险化工工艺; 工艺危险特点:过氧化工艺过程;因为过氧基OO的存在;具
有很强的分解爆炸危险; 安全控制基本要求:反应釜温度和压力的报警和联锁;反应
物料的比例控制和联锁及紧急切断动力系统;紧急断料系统;紧 急冷却系统;紧急送入惰性气体的系统;气相氧含量监测 报警 和联锁;紧急停车系统;安全泄放系统;可燃和有毒气体检测报 警装置等;
双氧水易分解的特点也给安全管理带来难度;
25
博汇及鲁西双氧水装置事故原因评析
3 生产原辅材料的危险性分析
1过氧化氢
纯净的过氧化氢在任何浓度下都很稳定;但与重金属及其盐类 灰
9
鲁西双氧水7 27火灾事故
2 鲁西双氧水7 27火灾事故简介续
事故发生经过:
该双氧水装置于7月23日工作液进系统循环;7月25日引氢气进系 统;正式投料试生产;27日12时05分;萃取塔开始分出双氧水;浓度为
27%;
27日16时45分左右;中控室操作人员通过远程视频监控发现萃取 塔 萃余分离器位置有浓烟冒出; 随后操作人员离开中控室前往现场; 发现萃余分离器部位起火;火势随萃余液油质可燃物的泄露增大;并伴 有爆鸣声;立即通知中控室其他操作人员进行一键安全停车;同时启 动装置切断氢气并充氮保护;
- 1、下载文档前请自行甄别文档内容的完整性,平台不提供额外的编辑、内容补充、找答案等附加服务。
- 2、"仅部分预览"的文档,不可在线预览部分如存在完整性等问题,可反馈申请退款(可完整预览的文档不适用该条件!)。
- 3、如文档侵犯您的权益,请联系客服反馈,我们会尽快为您处理(人工客服工作时间:9:00-18:30)。
而,应着眼于整套装置落实“加氢工艺”的安全控制措施。
(下页 “过氧化工艺”的安全控制措施落实,同此项)
23
博汇及鲁西双氧水装置事故原因评析
1.双氧水生产的反应机理分析(续)
2)过氧化工艺。双氧水生产工艺的第二步反应,即通常所 讲的“氧化反应”,为“过氧化工艺”,也属于重点监管的危险 化工工艺。 工艺危险特点:“过氧化工艺”过程,因为过氧基(-O-O-) 的存在,具有很强的分解爆炸危险。
车(注:距18时46分 发生爆炸接近3.5小时,应该有足够的时间处 理异常),车间通知电工检修线路、未发现异常。
15时50分乙班人员接班后,因氮气中氧含量一直不合格无法
再次开车。
3
博汇 “8.25”双氧水爆炸事故
1.博汇 “8.25”双氧水爆炸事故简介----事故发生经过 (续) :
在装置停车时段内,DCS主操发现氧化塔压力由17时25 分的 0.08MPa升至 18时24分的 0.2MPa,通过远程控制打开氧化塔尾气 调节阀泄压,由于阀的开度过小,塔内压力升高速度短暂减缓后 仍继续升高; 18时39分塔内压力急剧升高,通过远控阀泄压已不起作用, 18时46分压力升至测量传感器满量程(0.6MPa)并继续升压; 18时46分22秒发生了氧化塔爆炸,并相继引燃了氧化塔周边
博汇 “8.25”双氧水爆炸事故
1. 博 汇 双 氧 水 爆 炸 事 故 简 介 ↓ 现场 照片
7
博汇 “8.25”双氧水爆炸事故
1. 博 汇 双 氧 水 爆 炸 事 故 简 介 ↓ 现场 照片
8
鲁西双氧水“7.27”火灾事故
2.鲁西双氧水“7.27”火灾事故简介
2013年7月27日16时45分左右,鲁西化工集团股份有限公司18 万吨/年双氧水生产装置的萃取塔发生火灾事故,直接经济损失约 200万元。这起事故虽未造成人员伤亡,但产生了较大社会影响( 网上传播、东方时空)。 鲁西化工集团股份有限公司是由原鲁西化肥厂(1976年建厂) 逐步发展起来的国有大型化工企业,总部位于聊城高新技术开发区 鲁西化工园区,总资产159亿元,职工11000余人。 发生事故的18万吨/年双氧水生产装置由聊城市鲁西化工工程 设计有限公司设计,鲁西工业装备有限公司安装,2013年6月5日取 得试生产方案备案告知书,7月25日开始投料试生产。
博汇及鲁西双氧水装置事故原因评析
2.操作层面的事故原因分析(续)
(3)对双氧水装置静电危害的重视程度不够。
1)防静电设施和措施不够全面。萃取塔至萃余液分离器、高 位集液槽、工作液计量槽的气液相管路法兰既未做静电跨接,也没 有测量接触电阻,存在静电积聚的安全隐患。 2)系统设计缺陷导致多个易产生静电的环节。 萃取塔与萃余液分离罐高达6.8米的位差,造成工作液的流速 在岀液管道内大大加快,易产生静电; 萃取塔溢流管设计不合理造成萃取塔塔顶液位不稳定,特别是 在双氧水分解较活跃的状况下,萃取塔萃余液出口管内介质为气液 非均相混合物,管内介质流速快而紊乱,易产生静电。
鲁西双氧水“7.27”火灾事故
2. 鲁 西 双 氧 水 火 灾 事 故 简 介 ↓ 现场 照片
11
鲁西双氧水“7.27”火灾事故
2. 鲁 西 双 氧 水 火 灾 事 故 简 介 ↓ 现场 照片
12
鲁西双氧水“7.27”火灾事故
2. 鲁 西 双 氧 水 火 灾 事 故 简 介 ↓ 现场 照片
13
1) 爆炸物。工作液的闪点为42℃左右,其蒸汽属于火灾爆炸 性物质,且爆炸下限较低(0.8%-7%)容易形成爆炸性混合物。
2)助燃物。(见下页)
3)点火源。(见下页)
16
博汇及鲁西双氧水装置事故原因评析
(2)三个基本条件的具备导致火灾爆炸事故的发生(续) 。
2)助燃物。双氧水的大量分解可提供足够的氧气。另外,放空 管设置不合理产生的“烟囱效应”,萃取塔溢流管设计不合理造成 的“虹吸现象”,都存在负压抽吸进入空气的可能。 3)点火源。
博汇及鲁西双氧水装置事故原因评析
1.双氧水生产的反应机理分析(续)
1)加氢工艺。双氧水生产工艺的第一步反应,即通常所讲的 “氢化反应”,为“加氢工艺”,属于重点监管的危险化工工艺。
工艺危险特点:
(a)反应物料具有燃爆危险性,氢气的爆炸极限为4%—75%, 具有高燃爆危险特性;
(b)加氢为强烈的放热反应,氢气在高温高压下与钢材接触,钢 材内的碳分子易与氢气发生反应生成碳氢化合物,使钢制设备强度 降低,发生氢脆; (c)催化剂再生和活化过程中易引发爆炸;
鲁西双氧水“7.27”火灾事故
2. 鲁 西 双 氧 火 灾 产 事 故 简 介 ↓ 现场 照片
14
博汇及鲁西双氧水装置事故原因评析
一、两起双氧水事故的原因分析 相同点: (1)都是双氧水分解造成的。博汇事故是双氧水急剧分解造 成的氧化塔物理爆炸事故,鲁西事故是由于双氧水分解较快造成管 道内介质流速过快产生静电引起的设备内化学爆炸和燃烧事故。 (2)都发生在装置的试运行阶段。一个是长期停车恢复运行, 一个是新建装置开始试运行。 不同点: (1)一个造成了人员伤亡,一个没造成人员伤亡。 (2)一个是物理爆炸事故,一个是化学爆炸和燃烧事故。 (3)一个是在事故(或异常)发生时没有采取有效的防范 (或控制)措施,一个是在事故(或异常)发生时采取了有效的防 范(或控制)措施。 15
博汇及鲁西双氧水装置事故原因评析
1.技术层面的事故原因分析
(1)系统内杂质的存在是造成双氧水分解加速的原因。
1)博汇未对生产系统中可能产生钯催化剂和氧化铝粉末杂质 的因素进行彻底排除,造成开车以后系统内杂质较多。
2)鲁西通过查找原始记录、询问操作人员,发现开车过程中 氢化液过滤器、工作液过滤器因阻力大频繁清洗,说明系统清洁度 较差,酸洗钝化不彻底或系统内有积留杂质的死角。 (2)三个基本条件的具备导致火灾爆炸事故的发生。
1
双氧水装置事故分析案例
10、上海远大过氧化物有限公司“7.28”爆炸事故及分析
11、柳化“12.16”循环工作液贮槽爆炸事故报告 12、浙江:龙鑫化工双氧水生产车间发生爆炸事故 13、太阳纸业济宁福利达化工有限公司事故分析
2
博汇 “8.25”双氧水爆炸事故
1.博汇 “8.25”双氧水爆炸事故简介(续)----事故发生经过: 山东国金化工厂4万吨/年双氧水装置2012年8月13日至14日重 新调剂人员组织开车,8月16日零时复产投料。 装置运行至8月25日15时10分左右循环工作液泵跳停,在开启 备用泵运行5分钟后氧化液泵又发生跳停,装置于15时18分紧急停
萃取塔与萃余液分离罐高达6.8米的位差,造成工作液的流速在 岀液管道内大大加快,易产生静电;
萃取塔溢流管设计不合理造成萃取塔塔顶液位不稳定,特别是 在双氧水分解较活跃的状况下,萃取塔萃余液出口管内介质为气液 非均相混合物,管内介质流速快而紊乱,易产生静电; 萃取塔、萃余分离器、高位集液槽、工作液计量槽的气液相管 路法兰(4个螺栓以上 )未进行静电跨接等原因,造成静电积聚。 17
安全控制基本要求:反应釜温度和压力的报警和联锁;反应 物料的比例控制和联锁及紧急切断动力系统;紧急断料系统;紧 急冷却系统;紧急送入惰性气体的系统;气相氧含量监测、报警 和联锁;紧急停车系统;安全泄放系统;可燃和有毒气体检测报 警装置等。 24
博汇及鲁西双氧水装置事故原因评析
2.双氧水生产的工艺过程分析 蒽醌法双氧水生产工艺一般分为氢化、氧化、萃取及净化、后 处理、配制五个工段。 双氧水生产工艺涉及的危险物品主要有:工作液(蒽醌、重芳 烃和磷酸三辛酯)、氢气、催化剂、氧气、双氧水等。 有人这样描述蒽醌法双氧水的生产:用危险的原料,通过危险 的过程,生产危险的产品。这确实是蒽醌法双氧水生产的写照。 整个工艺过程中,蒽醌、重芳烃和磷酸三辛酯组成的工作液循 环使用,仅有少量工艺损耗,主要物耗为氢气,电耗全部为动力电 耗,因而具有原料简便、能耗较低的优点。同时,由于具有易燃易 爆性的工作液大量地在系统内循环留存,也形成安全隐患。 双氧水生产工艺属有机工艺生产无机产品,生产过程中伴随 着工作液的酸、碱转换,氢化工艺属典型的气液固三相反应,生产 25 过程中双氧水易分解的特点也给安全管理汇 “8.25”双氧水爆炸事故
2、鲁西双氧水“7.27”火灾事故 3、山东双氧水生产装置发生爆炸 4、浙江善高化学有限公司双氧水车间爆炸火灾事故 5、磷酸泄漏事故
6、山东国金化工厂“8.25”爆炸事故
7、临沂兰山九州化工厂双氧水桶爆炸事故 8、山东双氧水厂火灾事故 9、山东恒通化工双氧水车间工作液贮槽爆炸着火事故及分析
(d)加氢反应尾气中有未完全反应的氢气和其他杂质在排放时易 22 引发着火或爆炸。
博汇及鲁西双氧水装置事故原因评析
1.双氧水生产的反应机理分析(续) 总局规定的“加氢工艺”的安全控制基本要求: 温度和压 力的报警和联锁;反应物料的比例控制和联锁系统;紧急冷却 系统;搅拌的稳定控制系统;氢气紧急切断系统;加装安全阀、 爆破片等安全设施;循环氢压缩机停机报警和联锁;氢气检测 报警装置等。 鉴于蒽醌法双氧水生产工艺属于连续生产,其氢化工段 (核心设备氢化塔)仅属于整套生产工艺的一个组成部分,因
博汇及鲁西双氧水装置事故原因评析
二、双氧水生产的技术复杂性 从双氧水的反应机理、生产工艺过程、所涉及物质的危险特性 三个方面剖析一下双氧水生产的技术复杂性。 1.双氧水生产的反应机理分析 目前我国双氧水生产装置已全部为蒽醌法生产装置。该法以重 芳烃和磷酸三辛酯为溶剂,以2-乙基蒽醌(简称蒽醌)为溶质,配 成工作液;工作液中的蒽醌与氢气在钯催化剂的作用下发生氢化反 应,得到氢蒽醌溶液(氢化液);氢化液经空气氧化,得到双氧水 和蒽醌的混合液(氧化液);氧化液经萃取分离出双氧水,再经净 化、浓缩处理为合格的双氧水(浓度一般为27.5%)。 化学反应方程式:蒽醌 + H2 = 氢蒽醌(钯催化剂) 氢蒽醌 + O2 = 蒽醌 + H2O2 21 总反应式:H2 + O2 = H2O2(蒽醌、钯催化)