成形工艺基础砂型铸造
砂型铸造的特点及应用范围

砂型铸造的特点及应用范围砂型铸造是一种常见的金属铸造工艺,其特点和应用范围非常广泛。
下面我将详细介绍砂型铸造的特点及应用范围。
一、砂型铸造的特点:1. 灵活性强:砂型铸造适用于各种不同材料的铸造,包括铁、钢、铜、铝等多种金属材料。
同时,砂型铸造还能够制造复杂形状的铸件,满足不同行业的需要。
2. 成本低:相比其他金属铸造工艺,砂型铸造的成本相对较低。
砂型铸造所需的原料——砂、石膏等非常常见且廉价,而且制作砂型的工艺也相对简单,降低了制造成本。
3. 生产周期短:砂型铸造的生产周期相对较短。
制作砂型的过程相对简单,可以快速完成,并且对于大批量生产具有较高的效率。
这使得砂型铸造成为一种非常快速的金属成型工艺。
4. 精度较差:相比其他铸造工艺,砂型铸造的精度相对较差。
砂型铸造的铸件表面容易产生砂眼、夹渣等缺陷。
因此,在一些对精度要求较高的行业,如航空、汽车等,砂型铸造应用相对有限。
5. 铸造尺寸范围广:砂型铸造适用于不同尺寸的铸件。
小型铸件可以使用手工制作砂型,而大型铸件可以采用自动化设备制作砂型。
二、砂型铸造的应用范围:1. 机械制造:砂型铸造在机械制造行业中应用广泛。
可以用于生产各种机械零部件,如机床床身、机械箱体、机械零件等。
砂型铸造可以用来制造各种不同材料的金属件,满足机械制造行业的需求。
2. 汽车工业:砂型铸造在汽车工业中也有重要的应用。
可以用来制造发动机缸体、曲轴、活塞、减震器等关键零部件。
砂型铸造具有生产周期短、成本低的优势,适合汽车工业中对大批量生产的需求。
3. 船舶工业:砂型铸造在船舶工业中也有广泛的应用。
可以用来制造船体、推进器、螺旋桨等部件。
船舶工业对于零件的尺寸要求较大,砂型铸造可以满足这一要求。
4. 石油化工:砂型铸造在石油化工行业中也有应用。
可以制造石油钻探设备的关键零部件,如钻井头、套管等。
砂型铸造可以满足对于大尺寸、大负荷的工作环境的要求。
5. 冶金行业:砂型铸造在冶金行业中也有重要的应用。
砂型铸造工艺流程及所需材料
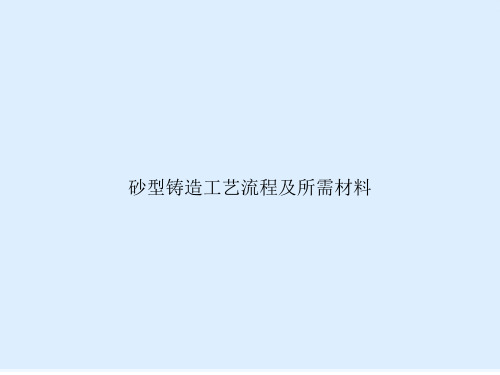
2. 铸造工艺准备工作
2.4 铸造涂料
涂料是指覆盖在型腔和型芯表面,以改善型腔和型芯表面耐火性、 化学稳定性、抗金属液冲刷性、抗黏砂性等性能的铸造辅助材料系统。
涂料的主要作用有:
a、提高铸件表面质量;
b、防止或减少铸件夹砂或砂眼等缺陷;
c、改善铸件表面性能。
涂料需要具有一定性能,才能起到应有的作用:
钢、铁和大型多数芯有用色合来金形铸成件都铸可件用内砂型部铸空造腔方法或获局得部。外形。造型芯的芯砂要比型砂具有更高的强度、透气
清除砂芯的方法主要有水力清砂除芯法、水爆清砂除芯法等。
铸造用性型、砂的耐种高类温可分性为、石退英砂让、性镁和砂、溃橄散榄性石砂。、锆英石砂、石灰石砂、黏土砂、水玻璃砂、树脂砂、油砂等。
模样材料: a、木材:轻便,易加工,价格低;但强度低,易吸潮变形,寿命短。 b、金属:铝合金轻便,加工性好,表面光洁,不易锈,但耐磨性差;铜 合金易加工,表面光滑,耐蚀、耐磨,但成本高,重量大;铸铁强度硬 度高,耐磨,低价,但重量大、易锈且不易加工。 c、塑料:制造简便、修理方便、较耐磨、变形小、生产周期短,但导热 性差、不可加热。 d、泡沫塑料:密度小,重量轻,制造简便,但模样表面不够光滑,易撞 破,只能使用一次。
浇铸
落砂 清理 表面处理
3.砂型铸造工艺
但生产3率.1低造,型劳动强度大,铸件质量不易保证。
b、触变性;
此外,还需手要进工行造铸件型质:量操进行作射方线便检验灵。活、适应性强,模样生产准备时间短;但生产率低,劳动强度大 清f、除较砂高,芯的铸的耐方件火法度质主;量要有不水易力保清砂证除。芯只法、适水用爆于清砂单除件芯小法等批。量生产。
1.砂型铸造简介
砂型铸造较之其它铸造方法成本低、生产工艺简单、生产周期短。 所以像汽车的发动机气缸体、气缸盖、曲轴等铸件都是用粘土湿型砂工 艺生产的。
砂型铸造的工艺过程

砂型铸造的工艺过程
砂型铸造的工艺过程
砂型铸造是一种制造金属零件的重要工艺,它主要是通过在成型模具中注入熔融金属,浇铸成型件,再经过热处理加工成型。
砂型铸造包括三个基本步骤:模具制作、铸件制作、热处理加工。
下面就来详细介绍下砂型铸造的工艺步骤:
一、模具制作
模具制作是砂型铸造工艺中的第一步,它根据铸件图纸要求而制作出的由砂型铸造砂组成的砂型,用于成型铸件。
由于型腔之间的温度差,因而在型腔内注入的熔融金属就会凝固成所需的形状。
1、首先,根据铸件图纸,设计砂型,这里需要考虑型腔的形状、位置、尺寸、回转角度等。
2、其次,根据砂型的设计图,按照由大而小的尺寸,用砂型铸造砂组合成型腔。
3、最后,将模具的砂型组成的型腔固定位置,制作好模具。
二、铸件制作
铸件制作是砂型铸造工艺中的第二步,其主要是将熔融金属倒入模具内,然后进行铸造,以便形成所需的金属铸件。
1、首先,根据铸件图纸规定的材料,将相应的金属材料加入电熔炉中,加热熔融,获得所需的熔融金属。
2、其次,将熔融金属倒入模具内,使其填满模具内的型腔。
3、最后,将模具放入电熔炉中,进行熔炼,当金属凝固时,就
可以取出模具,打开模具,拆出金属铸件。
三、热处理加工
热处理加工是砂型铸造工艺中的第三步,它主要是利用加热和冷却等技术,对砂型铸件进行处理,改变其物理性能,以满足使用要求。
1、首先,将打磨干净的金属铸件放入热处理炉内。
2、其次,根据铸件所需的性能要求,设定加热温度、保温时间、冷却速度等参数。
3、最后,将热处理完成的金属铸件拆出热处理炉,进行粗抛光处理,完成砂型铸造工艺。
用型砂紧实成型进行铸造的方法

用型砂紧实成型进行铸造的方法,称为砂型铸造。
砂型铸造生产的铸件占铸件总产量的80%以上,而在砂型铸造中,重要而大量的工作是制造铸型。
与其它金属加工方法相比,铸造具有如下优点:(1)原材料来源广。
(2)生产成本低。
(3)铸件形状与零件接近,尺寸不受限制。
但铸造生产目前还存在着若干问题,如铸件内部组织粗大,常有缩松、气孔等铸造缺陷,导致铸件力学性能不如锻件高。
铸造工序多,而且一些工艺过程还难以精确控制,使得铸件质量不够稳定,废品率高。
砂型铸造所用的型(芯)砂由原砂和粘结剂组成,必要时,还加入各种附加物。
原砂是耐高温材料。
常用的是含SiO2较多的硅砂。
常用的粘结剂有粘土、水玻璃等。
型砂和芯砂应具有以下性能:(1)透气性(2)强度(3)耐火度(4)可塑性(5)退让性上述性能要求是最基本的,有时又是互相矛盾的,因此,要求型砂具有良好的综合性能。
生产中常采用砂子、粘土(常用膨润土)和水等经混制而成的粘土砂。
为满足透气性、型砂中还可加入锯末、煤粉等。
铸型一般由上型、下型、型芯、浇注系统等几部分组成。
图3-2为常用两箱造型的铸型示意图。
图中铸型各组成部分的作用列入表3-1。
表3-1铸型各部分的作用型芯的作用及形成3、型芯是砂型中的重要组成部分,在制造中空铸件或有妨碍起模的凸台铸件时,往往要使用型芯。
常用的型芯有:(1)水平型芯,(2)垂直型芯,(3)悬臂型芯,(4)悬吊型芯,(5)引伸型芯(有利于取模),(6)外型芯(可使三箱造型变为两箱造型)等。
图3-3是上述几种型芯的示意图。
造型方法按砂型紧实方式分为手工造型和机器造型两大类。
手工造型手工造型是全部用手工或手动工具紧实型砂、制成砂型的造型方法。
其优点是操作方便,灵活性强,特别适合于单件小批生产。
用机器全部完成或至少完成紧砂操作的造型方法称为机器造型。
按紧砂和起模方式不同,有多种不同类型的机器造型方法及相应的造型机。
手工造型工序流程。
根据铸件结构、生产批量和生产条件,可选用不同的手工造型方法。
简述铸造成型的工艺特点

简述铸造成型的工艺特点铸造成型是一种重要的制造工艺,采用这种工艺可以制造出大量高质量的零部件和组件。
不同的铸造成型工艺有着各自独特的特点,本文将按照工艺类别对其各自的特点进行简述。
一、砂型铸造砂型铸造是应用最广泛的一种铸造成型工艺。
其工艺特点主要有以下几个方面:1. 砂型制作灵活,能够适应各种形状、大小、结构的铸件制作。
2. 砂型材料便宜,易得,能够降低成本,提高生产效率。
3. 砂型铸造适用于各种铸造材料,包括铸铁、铸钢、铝合金等材料。
4. 砂型铸造的表面质量较差,需要进行后续处理和加工,才能达到要求。
二、压铸工艺压铸是另一种常见的铸造成型工艺,其工艺特点主要有以下几个方面:1. 压铸制品表面质量高,尺寸精度高,能够生产出复杂、高精度的零部件和组件。
2. 压铸工艺节约原材料,减少成本,提高生产效率。
3. 压铸同时还能够进行镁合金、铝合金、铜合金等各种工程材料铸造,可满足不同领域的需要。
三、熔模铸造熔模铸造是一种相对高级的工艺,其工艺特点主要有以下几个方面:1. 熔模铸造制品的表面质量和尺寸精度都非常高,能够铸造出复杂形状和高精度的铸件,适用于生产高质量的小批量铸件。
2. 熔模铸造适用于铸造高熔点,难加工的合金,如钨合金等。
3. 熔模铸造的模具寿命长,可反复使用,具有较高的经济效益,但是模具的制造成本也较高。
四、连铸工艺连铸是大型铸造工艺中的一种,其工艺特点主要有以下几个方面:1. 连铸生产效率高,适用于大规模、长期稳定的铸造生产。
2. 连铸制品表面质量好,尺寸精度高,适用于生产大量定尺的铸件。
3. 连铸适用于各种合金的铸造生产,包括铝合金、铜合金、钢等。
总体而言,铸造成型是一种非常常用的制造工艺。
不同的工艺具有各自的优缺点,工程师和制造商需要根据铸件特点和生产需要综合选择具体的铸造成型工艺,以平衡成本、质量和生产效率等因素。
粉末冶金成型砂型铸造的工艺流程

粉末冶金成型砂型铸造的工艺流程工艺流程如下:1.设计模具:首先,根据待生产的零部件的形状和尺寸,设计出相应的模具。
模具的设计需要考虑到零部件的几何形状、材料特性以及加工要求等因素。
2.制备粉末:选取适合的金属材料,通过粉末冶金的方法制备所需的金属粉末。
制备过程中需要考虑金属粉末的粒度、成分和形状等因素,以保证最终产品的质量。
3.砂型制备:在模具中放置一层砂子,并将其压实以形成一个砂型。
砂型需要具备一定的强度和稳定性,以承受后续的金属充填和加工过程。
4.充填金属粉末:将事先制备好的金属粉末均匀地充填到砂型中。
充填过程中需要特别注意金属粉末的分布和密度,以确保最终产品的均匀性和密实度。
5.加压成型:在金属粉末充填完成后,对砂型进行加压成型。
加压的力度需要根据具体的工艺要求进行调整,以确保金属粉末的密实度和形状的准确性。
6.烧结工艺:将加压成型完成的砂型置于烧结炉中进行烧结工艺。
烧结的温度和时间需要根据金属粉末的种类和要求进行设定,以使金属粉末颗粒之间发生了扩散和凝聚,形成了致密的金属件。
7.去砂和清理:经过烧结后,待铸造的金属件被固化在砂型中。
这时,需要将砂型进行去砂和清理的工艺处理,以将金属件从砂型中完整地取出,并清除可能残留的砂粒和其他杂质。
8.补修和整形:去砂和清理完成后,对金属件进行补修和整形。
这包括对可能出现的瑕疵、凹凸不平或其他缺陷进行修复和矫正,以达到设计和质量要求。
9.精加工和表面处理:最后,经过补修和整形的金属件需要进行必要的精加工和表面处理。
这包括对尺寸、光洁度、硬度等进行检查和调整,以满足最终产品的要求。
综上所述,粉末冶金成型砂型铸造是一个相对复杂的工艺流程,但它能够制造出具有高质量和复杂结构的金属件。
这一技术在汽车、航空航天、电子等行业中得到了广泛的应用,并为传统铸造工艺的改进和发展提供了强大的技术支持。
粉末冶金成型砂型铸造的工艺流程

粉末冶金成型砂型铸造的工艺流程粉末冶金成型砂型铸造是一种先进的金属制造工艺,它融合了粉末冶金和铸造技术的优势,能够制造出复杂形状、高精度的零部件。
下面将介绍这一工艺的具体流程。
粉末冶金成型砂型铸造的工艺流程包括原料准备、模具制造、粉末充填、压实成型、烧结、浸渍、热处理和后续加工等步骤。
在进行这一工艺之前,首先需要准备好金属粉末、粘结剂、砂型等原料。
模具制造是整个工艺流程的第一步。
模具的设计和制造直接影响到最终产品的质量和形状。
通常情况下,模具可以采用3D打印或传统加工工艺制造而成。
在模具制造完成后,就可以进行粉末充填的工序了。
粉末冶金是将金属粉末和粘结剂混合,然后填充到模具中,经过压实成型后得到所需形状的零件。
压实成型是通过高压使粉末颗粒之间产生变形和结合,从而形成密实的零件。
这一步是整个工艺中最关键的环节之一。
接下来是烧结工艺。
在高温下,粉末中的粘结剂会烧结成为一种固体结构,从而使得粉末颗粒之间结合更加牢固。
烧结后的零件具有一定的强度和硬度,但还需要进行后续处理才能得到最终的产品。
浸渍工艺是将烧结后的零件浸入液态金属中,使其表面形成一层金属皮。
这样可以提高零件的密封性和耐腐蚀性。
浸渍后的零件还需要进行热处理,以消除内部应力和提高材料的性能。
经过热处理和后续加工,粉末冶金成型砂型铸造的零件就可以得到最终的形态。
这些零件通常具有高精度、复杂形状和良好的性能,可以广泛应用于航空航天、汽车制造、电子设备等领域。
总的来说,粉末冶金成型砂型铸造是一种高效、精密的制造工艺,能够满足复杂零件的生产需求。
通过粉末冶金成型砂型铸造,可以实现金属材料的高效利用,提高生产效率,降低成本,推动制造业的发展。
希望通过不断的技术创新和工艺改进,粉末冶金成型砂型铸造能够为各行各业带来更多的惊喜和发展机遇。
砂型铸造

安徽工业大学
三箱分模造型
安徽工业大学
AHUT
工 程 材 料 与 成 形 技 术 基 础
安徽工业大学
三箱造型视频
安徽工业大学
AHUT
工 程 材 料 与 成 形 技 术 基 础
安徽工业大学
三箱分模造型改两箱分模造型
安徽工业大学
AHUT
工 程 材 料 与 成 形 技 术 基 础
安徽工业大学
AHUT
1、整模造型与分模造型
安徽工业大学
AHUT
工 程 材 料 与 成 形 技 术 基 础
模型是一个整体,其特点是造型时模样 全部放在一个砂箱内,分型面为平面。
工艺操作过程: (1)安放模样 (2)填砂舂砂 (3)扎通气孔 (4)撒分型砂 (5)放直浇口棒
(6)划分型线
(7)起模 (8)修型
(9)合型
安徽工业大学
量少,劳动强度小,大批量生产。在大批量生产中铸 件的成本能显著降低。
缺点:厂房,设备等要求高,投资大,批量生产才经
济,只适于两箱(中箱无法紧实),不宜用活块。
方法:常用的方法有:震压造型、射压造型等。 安徽工业大学
震 压 造 型 机 的 工 作 原 理 图
震压造型视频
安徽工业大学
AHUT
工 程 材 料 与 成 形 技 术 基 础
安徽工业大学
AHUT
工 程 材 料 与 成 形 技 术 基 础
安徽工业大学
手工制芯视频(采用刮板)
安徽工业大学
AHUT
工 程 材 料 与 成 形 技 术 基 础
安徽工业大学
型芯的作用视频
安徽工业大学
AHUT
工 程 材 料 与 成 形 技 术 基 础
- 1、下载文档前请自行甄别文档内容的完整性,平台不提供额外的编辑、内容补充、找答案等附加服务。
- 2、"仅部分预览"的文档,不可在线预览部分如存在完整性等问题,可反馈申请退款(可完整预览的文档不适用该条件!)。
- 3、如文档侵犯您的权益,请联系客服反馈,我们会尽快为您处理(人工客服工作时间:9:00-18:30)。
成形工艺基础-铸3
4
合脂砂以合成脂肪酸残渣经煤油稀释而成的 合脂作粘结剂。
油砂或合脂砂制造结构复杂、要求高的型芯 4.树脂砂 树脂砂是以树脂为粘结剂配制成的型砂。 又分为热硬树脂砂、壳型树脂砂、覆模砂等。 用树脂砂造型或制芯,铸件质量好、生产率 高、节省能源和工时费用、工人劳动强度低、
成形工艺基础-铸3
5
易于实现机械和自动化、适宜成批大量生产。 型砂还包括石墨型砂、水泥砂和流态砂等. 二、 型(芯)砂性能 为防止铸件产生粘砂、夹砂、砂眼、气孔和
裂纹等缺陷 ,型砂应具备下列性能。 1.型砂强度 指型砂试样抵抗外力破坏的能力。 2.透气性 表示紧实砂样孔隙度的指标。
成形工艺基础-铸3
6
若透气性不好,易在铸件内部形成气孔等缺陷。
整模造型因操作简便,无砂箱错位现象,适 用于外形轮廓上有一个平面可作分型面的简单铸 件,如齿轮坯、轴承、皮带、轮罩等。
成形工艺基础-铸3
8
2)分模造型 特点是:铸件的最大截面不在端部而在中部, 因而木模沿最大截面分成两半。
操作简便,适用于形状较复杂的铸件,特别 广泛用于有孔或带有型芯的铸件,如套筒、水管、 阀体、箱体、曲轴、立柱等。
后图为水管铸件的分模造型过程。
3)挖砂造型
成形工艺基础-铸3
9
当铸件最大截面在中部,模样又不便分成 两半(如分模后模样太薄或分面是曲面)时,只能 将模样做成整模,造型时挖掉防碍起模的砂子。
挖砂造型操作麻烦,生产率低,要求操作 技术水平高,仅适用于单件小批量生产。
对于分型面为阶梯面或曲面的铸件,当生产 数量较多时,可用成形底板代替平面底板,并将 模样放置在成形底板上造型,可省去挖砂操作。
成形工艺基础-铸3
16
气动微振压实造型机,它采用振击(频率 150~500次/分,振幅25~80mm)-压实-微振(频 率700~1000次/分,振幅5~10mm)来紧实造型。 这种造型机噪音较小,型砂紧实度均匀,生产率高.
2.射压式造型机 射压式造型机有两种机型,一种是垂直分型 无箱造型机,另一种是水平分型脱箱造型机。
成形工艺基础-铸3
17
其共同的特点是:不用砂箱,节省工装费用, 占地面积较小。
垂直分型无箱造型是指在造型、下芯、合型 及浇注过程中,铸型的分型面呈垂直状态(垂直 于地面)的无箱射压造型法。
3.其他机器造型
压实造型机中有高压造型机和水平分型脱 箱压实造型机两种。
1)高压造型机 近年来正向负压加砂高压
掌握砂型铸造是合理选用铸造方法,正确设 计铸件的基础和关键,金工课的核心内容。
铸造工艺图—在零件图上用各种工艺符号及 参数表示出铸造工艺方案的图形。
其中有:浇注位置、铸型分型面、芯(非
“蕊”也)子的数量、形状、尺寸及固定方法、
加工余量、浇注系统、起模斜度、冒口和冷铁的
尺寸和布置等。
成形工艺基础-铸3
12
1.单件、小批生产
图示件属大尺寸、回转体,可采用刮板-地 坑造型。
2.成批生产
当批量 大,但又无机械化生产条件时,可 采用模样两箱造型。
四、机器造型(造芯)
手工造型中的摏箱、起模两工序不仅效率低, 劳动条件差,而且铸件尺寸不准确等不足。
成形工艺基础-铸3
13
机器造型能较好的改变上述缺点。
用机器代替手工进行造型(芯),称机器造型(芯).
3.型砂耐火性
型砂耐火性指型砂承受高温作用的能力。耐 火性差,铸件易产生粘砂。
4.退让性
退让性指型砂不阻碍铸件收缩的高温性能。
退让性不好,铸件易产生内应力或开裂。
还有:紧实度、成形性、起模性及溃散性等.
成形工艺基础-铸3
7
三、手工造型 1.砂箱及造型工具 如图所示。
2.常见手工造型方法 1)整模造型 特点是:模样是整体的,铸型的型腔一般 只在下箱。
成形工艺基础-铸3
3
2.水玻璃砂
水玻璃砂是以水玻璃(硅酸钠Na2O·mSiO2的 水溶液)为粘结剂配制成的化学硬化砂。
它是除粘土砂外用得最广泛的一种型砂。
水玻璃砂铸型或芯无需烘干、硬化速度快、 生产周期短、易于机械化、劳动条件改善。
3.油砂和合脂砂
油砂是以桐油、亚麻仁油等植物油为粘结剂
配制成的型砂。
成形工艺基础-铸3
1
成形工艺基础-铸3
2
型(芯)砂按粘结剂的种类可分为:
1.粘土砂
粘土砂是以粘土为粘结剂配制成的型砂。
由原砂(应用最广的是硅砂,主 成分SiO2 ) 、 粘土、水及附加物按一定比例配制而成。
粘土砂是迄今为止铸造生产中应用最广泛的 型砂。可用于制造铸铁件、铸钢件及非铁合金的 铸型和不重要的型芯。
粘土砂结构见示意图。
11
5)刮板造型
用与铸件截面相适应的刮板代替实体模样 造型的方法。
刮板造型,可以降低模样成本,缩短生产 准备时间,但要求操作技能高,铸件尺寸精度低, 生产率低,故只适用于中小批生产尺寸较大的回 转体铸件,如皮带轮、齿轮等。
下面请同学们,根据前面的讨论,试分析下 面的图例,应该用何种方法造型。
成形工艺基础-铸3
造型过程包括:填砂、紧实、起模、下芯、 合箱以及铸型、砂箱的运输等工艺环节。
大部分造型机主要是实现型砂的紧实和起模 工序的机械化,至于合箱、铸型和砂箱的运输则 由辅助机械来完成。
不同的紧砂方法和起模方式的组合,组成了 不同的造型机。
成形工艺基础-铸3
14
造型机的种类很多,按紧砂方法不同可分: 震压式造型机; 震实式造型机; 压实式造型机; 射压式造型机起 模机构和控制系统组成。
成形工艺基础-铸3
10
成形底板可根据生产数量的不同,分别用 金属、木材制作;如果件数不多,可用粘土较多 的型砂春紧制成砂质成形底板,称为假箱。
4)活块造型
将模样上妨碍起模的部分,如凸台、肋、耳 等,做成活动的,称为活块。
活块用销式燕尾与模样的主体连接,在起模 时须先取出模样主体,然后取出活块。
成形工艺基础-铸3
成形工艺基础-铸3
15
多通过震击和压实紧实型砂,绝大部分都 是边震边压。
震击压实都采用气动,为高频率低振幅的微 振形式,铸型硬度均匀.
为减轻振动,设有缓冲机构,缓冲机构有气 垫式和弹簧式两种。
所有机器都带有起模结构,起模比较平稳。 这种造型机的特点是:机构简单、操作方便、投 资较小,适用于各种材质小件的造型。