车削工艺流程
内圆车削工艺与技巧
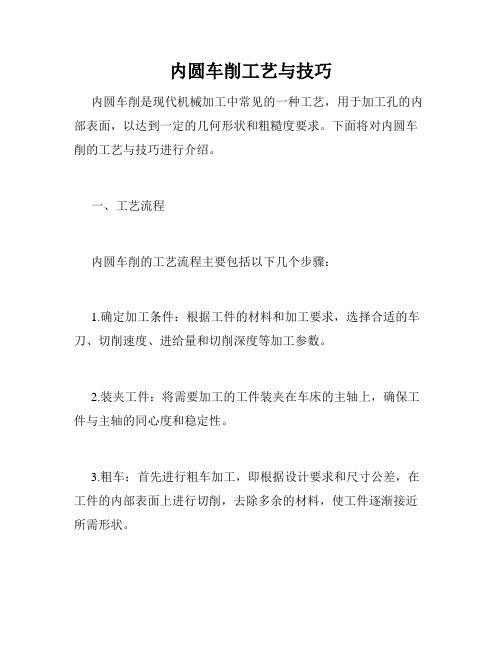
内圆车削工艺与技巧内圆车削是现代机械加工中常见的一种工艺,用于加工孔的内部表面,以达到一定的几何形状和粗糙度要求。
下面将对内圆车削的工艺与技巧进行介绍。
一、工艺流程内圆车削的工艺流程主要包括以下几个步骤:1.确定加工条件:根据工件的材料和加工要求,选择合适的车刀、切削速度、进给量和切削深度等加工参数。
2.装夹工件:将需要加工的工件装夹在车床的主轴上,确保工件与主轴的同心度和稳定性。
3.粗车:首先进行粗车加工,即根据设计要求和尺寸公差,在工件的内部表面上进行切削,去除多余的材料,使工件逐渐接近所需形状。
4.精车:在粗车基础上进行精细加工,使用更小的切削深度和进给量,以达到更高的表面质量和尺寸精度。
5.修整边:对加工后的内圆边缘进行修整,去除毛刺和凹坑,保证边缘的平滑和一致性。
6.清洁工件:清洁工件表面,去除切屑和切削液,保持工件的清洁与干燥。
7.测量检验:使用合适的测量工具,对加工后的内圆进行尺寸和形状的检验,确保符合设计要求。
8.完工与记录:将加工完毕的工件进行标识,填写加工记录,并做好工件的保养和储存。
二、技巧要点1.选择合适的车刀:根据工件的材料和要求选择合适的车刀类型,在加工过程中要注意刀具的刃磨状态和刀尖的尺寸,确保切削效果和加工质量。
2.合理设置加工参数:根据工件的材料、硬度和加工要求,合理设置切削速度、进给量和切削深度等加工参数,以保证加工效率和加工质量。
3.注意切削液的选择和使用:在内圆车削过程中,切削液的选择和使用对于加工效果和工具寿命有重要影响。
合理选择切削液,并控制好切削液的供给方式和用量。
4.保持工具与工件的同心度:在进行内圆车削时,保持工具与工件的同心度是关键。
要选用具有高精度的工具和夹具,确保工具能够精确地旋转在工件的内表面,并控制好车刀的进给深度和速度。
5.合理安排工作顺序:在进行多道工序的内圆车削时,要合理安排各道工序的顺序和加工次序,确保前一道工序的切削量和加工质量对后续工序的影响最小化。
典型零件的加工工艺
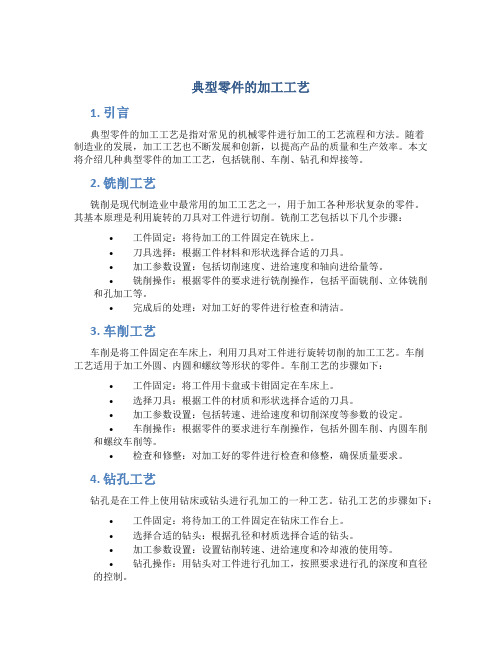
典型零件的加工工艺1. 引言典型零件的加工工艺是指对常见的机械零件进行加工的工艺流程和方法。
随着制造业的发展,加工工艺也不断发展和创新,以提高产品的质量和生产效率。
本文将介绍几种典型零件的加工工艺,包括铣削、车削、钻孔和焊接等。
2. 铣削工艺铣削是现代制造业中最常用的加工工艺之一,用于加工各种形状复杂的零件。
其基本原理是利用旋转的刀具对工件进行切削。
铣削工艺包括以下几个步骤:•工件固定:将待加工的工件固定在铣床上。
•刀具选择:根据工件材料和形状选择合适的刀具。
•加工参数设置:包括切削速度、进给速度和轴向进给量等。
•铣削操作:根据零件的要求进行铣削操作,包括平面铣削、立体铣削和孔加工等。
•完成后的处理:对加工好的零件进行检查和清洁。
3. 车削工艺车削是将工件固定在车床上,利用刀具对工件进行旋转切削的加工工艺。
车削工艺适用于加工外圆、内圆和螺纹等形状的零件。
车削工艺的步骤如下:•工件固定:将工件用卡盘或卡钳固定在车床上。
•选择刀具:根据工件的材质和形状选择合适的刀具。
•加工参数设置:包括转速、进给速度和切削深度等参数的设定。
•车削操作:根据零件的要求进行车削操作,包括外圆车削、内圆车削和螺纹车削等。
•检查和修整:对加工好的零件进行检查和修整,确保质量要求。
4. 钻孔工艺钻孔是在工件上使用钻床或钻头进行孔加工的一种工艺。
钻孔工艺的步骤如下:•工件固定:将待加工的工件固定在钻床工作台上。
•选择合适的钻头:根据孔径和材质选择合适的钻头。
•加工参数设置:设置钻削转速、进给速度和冷却液的使用等。
•钻孔操作:用钻头对工件进行孔加工,按照要求进行孔的深度和直径的控制。
•清洁和检查:对加工好的孔进行清理和检查,确保孔的质量。
5. 焊接工艺焊接是将两个或多个工件通过熔化和凝固的过程连接在一起的工艺。
焊接工艺的步骤如下:•工件准备:准备待焊接的工件,包括清洁和坡口处理等。
•焊接机器设置:根据材料和焊接方式设置焊接机器的参数,包括电流、电压和焊接速度等。
数控车削加工课件

得到解决。
06
数控车削加工的发展趋势和未来 展望
数控车削加工的技术发展趋势和创新方向
升级,向更高精度、更高效率、更低成 本方向发展。
智能化是未来数控车削加工技术的重要发展方向,通过引入人 工智能、机器学习等技术,实现加工过程的自动化和智能化控
实现对螺纹的加工。
05
数控车削加工的实践操作和技术 要点
数控车削加工的操作步骤和注意事项
操作步骤 1. 仔细阅读和理解图纸,了解工件的材料、尺寸和精度要求。
2. 根据图纸要求,选择合适的刀具和切削参数。
数控车削加工的操作步骤和注意事项
3. 安装工件,调整机床,确保安全防护措施到位。 4. 输入程序,进行模拟加工,确认无误后开始实际加工。
数控车削加工在机械制造、汽 车制造、航空航天等领域得到 广泛应用。
数控车削加工的工艺流程
数控车削加工的工艺 流程包括以下几个步 骤
2. 工件装夹:将工件 放置在数控车床上, 通过夹具进行固定和 定位。
1. 确定加工方案:根 据零件图和工艺要求 ,确定加工方案和加 工顺序。
数控车削加工的工艺流程
3. 刀具选择和调整
水平发展。
智能制造
智能制造是未来制造业的重要趋 势,数控车削加工将更加深入地 与人工智能、物联网等技术结合 ,实现加工过程的智能化和自适
应化。
定制化生产
随着消费者需求的多样化,制造 业向定制化生产方向发展,数控 车削加工将更加注重个性化和定 制化的需求,满足不同客户的需
求。
数控车削加工的人才培养和教育现状及未来发展需求
数控车削加工课件
车削的总结
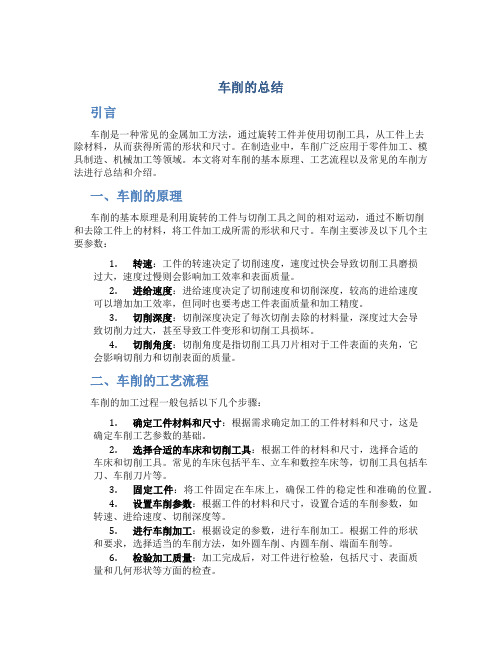
车削的总结引言车削是一种常见的金属加工方法,通过旋转工件并使用切削工具,从工件上去除材料,从而获得所需的形状和尺寸。
在制造业中,车削广泛应用于零件加工、模具制造、机械加工等领域。
本文将对车削的基本原理、工艺流程以及常见的车削方法进行总结和介绍。
一、车削的原理车削的基本原理是利用旋转的工件与切削工具之间的相对运动,通过不断切削和去除工件上的材料,将工件加工成所需的形状和尺寸。
车削主要涉及以下几个主要参数:1.转速:工件的转速决定了切削速度,速度过快会导致切削工具磨损过大,速度过慢则会影响加工效率和表面质量。
2.进给速度:进给速度决定了切削速度和切削深度,较高的进给速度可以增加加工效率,但同时也要考虑工件表面质量和加工精度。
3.切削深度:切削深度决定了每次切削去除的材料量,深度过大会导致切削力过大,甚至导致工件变形和切削工具损坏。
4.切削角度:切削角度是指切削工具刀片相对于工件表面的夹角,它会影响切削力和切削表面的质量。
二、车削的工艺流程车削的加工过程一般包括以下几个步骤:1.确定工件材料和尺寸:根据需求确定加工的工件材料和尺寸,这是确定车削工艺参数的基础。
2.选择合适的车床和切削工具:根据工件的材料和尺寸,选择合适的车床和切削工具。
常见的车床包括平车、立车和数控车床等,切削工具包括车刀、车削刀片等。
3.固定工件:将工件固定在车床上,确保工件的稳定性和准确的位置。
4.设置车削参数:根据工件的材料和尺寸,设置合适的车削参数,如转速、进给速度、切削深度等。
5.进行车削加工:根据设定的参数,进行车削加工。
根据工件的形状和要求,选择适当的车削方法,如外圆车削、内圆车削、端面车削等。
6.检验加工质量:加工完成后,对工件进行检验,包括尺寸、表面质量和几何形状等方面的检查。
7.修整和抛光:根据实际需求,对加工后的工件进行修整和抛光,提高其表面质量。
三、常见的车削方法车削方法根据切削方向和切削工具的运动方式可以分为以下几类:1.外圆车削:将工件固定在车床上,通过旋转工件,切削工具在工件表面上进行横向切削,使工件外圆面达到所需的直径和粗糙度要求。
车削工艺设计流程

车削工艺设计流程
车削工艺设计流程是机械加工中常用的一种工艺,用于通过旋转刀具对工件进行加工和修整。
下面将介绍车削工艺的设计流程。
首先,车削工艺设计的第一步是分析工件的形状和尺寸要求。
根据工件的轮廓和尺寸,确定最佳的车削方式和加工顺序。
例如,内外圆的车削顺序可能不同,需要先粗车后精车。
第二步是选择合适的车削工具和刀具。
根据工件材料、形状和加工要求选择合适的车刀。
如硬质合金车刀、螺旋刀等。
同时,还需确定刀具的切削速度、进给速度和切削深度。
第三步是确定车削过程中的工艺参数。
根据工件材料的硬度和加工难度,确定合适的切削速度、进给速度和切削深度。
同时还需考虑冷却液的选择和切削润滑问题,确保车削过程的稳定性和质量。
第四步是进行车削工艺的实际加工。
根据前面确定的工艺参数和车削顺序,进行机床的调整和装夹工件。
在加工过程中,要注意及时检查刀具的磨损情况,并进行必要的更换和修整,以保证加工质量。
最后,完成车削加工后,还需要进行工件的质量检验。
通过测量工件的尺寸、表面粗糙度和平行度等参数,来判断加工结果是否满足要求。
综上所述,车削工艺设计流程包括工件分析、刀具选择、工艺参数确定、实际加工和质量检验。
设计良好的车削工艺可以提高生产效率和产品质量,并有效控制加工成本。
机加工流程及工艺

机加工流程及工艺一、引言机加工是一种常见的制造工艺,它通过使用机械设备对工件进行切削、钻孔、铣削等加工操作,以达到预定的形状和尺寸要求。
本文将介绍机加工的基本流程及常用的工艺。
二、机加工流程1.工件准备:首先需要准备待加工的工件,通常是由金属或其他材料制成的原始零件。
工件应经过清洗和检查,以确保表面没有污垢或损坏。
2.工艺规划:在进行机加工之前,需要进行工艺规划。
这包括确定所需的切削工具、加工顺序和切削参数等。
根据工件的形状和要求,选择合适的机床和夹具。
3.装夹工件:将工件安装在机床上的夹具中,以便进行加工操作。
夹具应牢固固定工件,以确保加工过程中的稳定性和精度。
4.切削加工:根据工艺规划,使用合适的切削工具进行切削操作。
切削工具通常是钻头、铣刀、刀具等。
通过旋转、移动或振动切削工具,将工件表面的材料逐渐切除,以达到所需的形状和尺寸。
5.加工检验:在切削加工完成后,需要对加工后的工件进行检验。
使用测量工具,如千分尺、卡尺等,对工件的尺寸、平面度、圆度等进行测量,以确保加工质量符合要求。
6.表面处理:根据需要,对工件进行表面处理。
这可能包括研磨、抛光、电镀等工艺,以改善工件的表面光洁度、耐腐蚀性或装饰效果。
7.清洁和包装:最后,对加工完成的工件进行清洁和包装。
清洁工作可以通过清洗、喷气或擦拭来完成。
包装工作可以采用纸箱、泡沫塑料等材料,以保护工件免受损坏。
三、常用机加工工艺1.车削:车削是一种常见的机加工工艺,它使用车床上的刀具对工件进行切削。
通过旋转工件,同时移动切削刀具,将工件上的材料逐渐切除,以得到所需的形状和尺寸。
2.铣削:铣削是另一种常见的机加工工艺,它使用铣床上的刀具对工件进行切削。
通过旋转刀具,同时移动工件,将工件表面的材料逐渐切除,以得到所需的形状和尺寸。
3.钻孔:钻孔是一种用于在工件上钻孔的机加工工艺。
使用钻床或钻头,将刀具旋转并施加压力,以将工件材料逐渐切除,形成孔洞。
4.切割:切割是一种用于将工件切成所需尺寸的机加工工艺。
车削加工方法技术介绍
数控车削技术
总结词
数控车削技术是一种基于数字控制的切削加工方法。
详细描述
数控车削技术是现代制造技术的重要组成部分,它通过使用数控机床和专用的数控编程软件,可以实现自动化、 高效率的切削加工。数控车削技术不仅可以提高加工效率,还可以提高加工精度和表面质量,广泛应用于各种机 械制造领域。
绿色车削加工的发展需要加强 环保法规的制定和执行,推广 绿色制造理念和技术,提高企 业的环保意识。
高效车削加工
02
01
03
高效车削加工是一种以提高加工效率为目标的方法, 通过采用高速切削、多轴联动等技术实现。
高效车削加工能够大幅提高加工效率,缩短加工周期 ,降低生产成本。
高效车削加工的发展需要不断研发新的切削材料和刀 具,优化加工工艺参数,提高设备运行稳定性。
车削加工方法技术介绍
目
CONTENCT
录
• 引言 • 车削加工的基本原理 • 车削加工的主要技术 • 车削加工的应用领域 • 车削加工的未来发展
01
引言
主题简介
车削加工是一种常见的机械加工方法,主要用于加工旋转体零件 ,如轴、齿轮、螺纹等。
车削加工技术广泛应用于机械制造、汽车、航空航天、能源等领 域。
目的和意义
目的
介绍车削加工方法和技术,包括车削原理、车削刀具、车削工艺 参数等,以提高人们对车削加工的认识和应用水平。
意义
车削加工技术是机械制造领域中的重要组成部分,掌握车削加工 技术对于提高产品质量、降低生产成本、推动机械制造业的发展 具有重要意义。
车工工艺步骤
车工工艺步骤
在机械加工领域中,车工是一种常见的加工方式,车工过程中需要按照一定的
工艺步骤来完成加工操作,下面将详细介绍车工的工艺步骤:
第一步:确定加工零件工艺要求
在进行车工操作之前,首先需要确定加工零件的工艺要求,包括加工尺寸、精度、表面粗糙度等参数,以及加工工艺方案和夹具设计等。
第二步:选择合适的车床和刀具
根据零件的加工要求,选择适合的车床设备,确定刀具的种类、规格和切削参数,确保刀具的合理性和寿命。
第三步:进行开料准备
在车床上进行开料准备工作,包括安装工件、夹紧工件、调整工件位置和车床
刀架的安全操作等。
第四步:粗车工序
通过粗车工序对工件进行初步加工,根据工艺要求和刀具选择进行合理切削,
确保零件的形状和尺寸精度。
第五步:精车工序
进行精车工序,对零件进行精加工和精度控制,保证加工表面的光洁度和平整度。
第六步:配合测量检查
在车工过程中,需要进行配合测量检查,确保零件的尺寸和形位精度符合要求,避免在加工后出现问题。
第七步:完成工件加工
最后完成工件的加工操作,根据要求进行表面处理和除毛刺等工艺,保证零件
的最终质量。
通过以上工艺步骤的合理操作,能够有效提高车工加工的效率和质量,保证零
件的精度和表面质量,符合工艺要求。
车工车削的工艺流程
车工车削的工艺流程
车工车削是指在车工加工制造过程中,将车体不需要的部分去除以达到精确尺寸的过程。
其工艺流程主要包括:
1. 定位定标。
将车体定位到车削中心,使用测头测量车体四周形状,并将数据输入车削中心系统,进行定位定标。
2. 选料检验。
检查要车削的车体材质是否符合要求,是否存在差异过大的不佳部位。
3. 程序设计。
根据车体三维数据模型和定标结果,使用车削中心软件设计出初始车削程序。
4. 试车削。
使用低速试削,观察试削形貌是否符合要求,如有差异及时修改程序。
5. 粗车削。
使用较高转速和较大进给,进行主要车削,形成大体形貌。
6. 精车削。
使用更高转速和精确进给,对粗车削形貌进行精细修饰,达到尺寸公差。
7. 检测修整。
使用三坐标测量仪检测车体尺寸是否达标,如有不合格尺寸部分再行修整车削。
8. 除珠清洁。
使用除珠机除去车体表面粗糙度高的区域,清洁整个车体表面。
9. 程控优化。
针对不同型号车体,持续优化车削程序,提高效率和质量。
以上过程从定位定标开始到除珠清洁结束,即为一般车工车削的完整工艺流程。
车削五种加工工艺流程
车削五种加工工艺流程下载温馨提示:该文档是我店铺精心编制而成,希望大家下载以后,能够帮助大家解决实际的问题。
文档下载后可定制随意修改,请根据实际需要进行相应的调整和使用,谢谢!并且,本店铺为大家提供各种各样类型的实用资料,如教育随笔、日记赏析、句子摘抄、古诗大全、经典美文、话题作文、工作总结、词语解析、文案摘录、其他资料等等,如想了解不同资料格式和写法,敬请关注!Download tips: This document is carefully compiled by theeditor. I hope that after you download them,they can help yousolve practical problems. The document can be customized andmodified after downloading,please adjust and use it according toactual needs, thank you!In addition, our shop provides you with various types ofpractical materials,such as educational essays, diaryappreciation,sentence excerpts,ancient poems,classic articles,topic composition,work summary,word parsing,copy excerpts,other materials and so on,want to know different data formats andwriting methods,please pay attention!车削五种加工工艺流程一、普通车削工艺流程。
在进行普通车削加工之前,需要做好充分的准备工作。
- 1、下载文档前请自行甄别文档内容的完整性,平台不提供额外的编辑、内容补充、找答案等附加服务。
- 2、"仅部分预览"的文档,不可在线预览部分如存在完整性等问题,可反馈申请退款(可完整预览的文档不适用该条件!)。
- 3、如文档侵犯您的权益,请联系客服反馈,我们会尽快为您处理(人工客服工作时间:9:00-18:30)。
车削工艺流程
1.模具的准备,把从烘干箱里取出冷却后的成型模具用专用
工具(简称板卡)使模具头与模具盒分离、清理干净放在盛器里(以下
简称半成品)。
2.车床的准备,在空压机正常工作的情况下,运作机床空转
5到10分钟,目的是磨合机器将机器气阀、控制器中可能残留的余
压释放(简称预热)。
预热结束后是车削铜头,取掏过丝的铜棒一枚,旋进车床上拧紧。
用普通刀头换下单晶片刀头,运转机器。
以剖开
的半成品为样本车削铜棒直至得到匹配的铜头(目前的匹配要求是用
手能够轻松套上、用手取时费劲但是可以取下、机器能够轻松取下)。
再用单晶片换下普通刀头。
3.调试运行,将半成品倒入自动上料池里。
取一颗半成品嵌
进铜头,如果知道上一次加工的半成品度数,就以上次度数加工参
数为基准调试机器。
如果不知道上一次的参数,就运转车床加工一
个以这个加工过的半成品的参数为基准调试机器。
调试结束后,转
自动试做几个,选第三个、第五个(跟个人习惯)检查参数是否和预
设参数一致(因为是气动多少会有出入这里都是取接近值。
干片参数
区间: 度数+0.15 -0.1 透光区直径±0.5中心厚度±0.5边
缘厚度极点落差≤2,除度数外单位均是0.01㎜)。
如果一致运转
机器转自动开始正式加工。
如果不一致把第一、二、四个加工后的
半成品也检测一下,如果都与预设参数不一致且前者一致,就以前
者参数为基准调试机器,重复前一步奏;如果都与预设参数不一致
且出入浮动很大(一般没有这种情况),检查气压是否稳定,自动上
料机器运转有没有异常,工作台有没有被异物卡住,观察刀头运行
轨迹是否合理找出问题所在。
解决问题后重新调试机器检验参数直
至参数一致转自动开始加工。
4.抽验,车床转自动开始加工运行中,随机抽验(数量没有一
定一般是每100个抽验1到2个)车削过的半成品的参数和当前度数
的标准参数是否一致。
如果一致继续生产;如果不一致取最新一颗
加工过的半成品检验参数与前者参数对比。
如果一致关闭机器退回
到步奏3以当前镜片参数为基准重新调试机器;如果不一致且与当
前度数镜片标准参数也不一致关闭机器退回步奏3以当前镜片参数
为基准重新调试机器,反之继续运转机器生产。
(完)。