2010汽车驱动桥壳台架试验仿真及验证
商用车驱动桥壳体模态仿真与试验方法研究

AUTO PARTS | 汽车零部件商用车驱动桥壳体模态仿真与试验方法研究李旭伟 王恩鹏 杨东绩中汽研汽车检验中心(天津)有限公司 天津市 300300摘 要: 针对商用车驱动桥壳体模态参数的识别,提出了在不同约束状态下的仿真和测试方法,从计算和试验两个方面验证方法的准确性。
分析了不同约束工况下的结果与驱动桥台架试验振动的关联性,为驱动桥NVH 性能的研究提供了新的思路。
关键词:壳体模态;驱动桥;有限元建模;台架试验1 前言驱动桥是汽车传动系统的重要组成部分,既是车轮与车身或车架连接的部分,也是转速和转矩传递的关键部件。
商用车驱动桥承载了更大的来自于路面的作用力,其内部的齿轮也传递了更大的扭矩。
因此驱动桥在工作过程中来自于内部和外部的动静载荷都有涉及,其刚度、强度和动态特性对于整车的疲劳耐久和NVH性能都有很大影响,对其的设计和分析具有重要的工程意义。
驱动桥在实际工作过程中由于主减速器齿轮的啮合传动,会产生相应的振动,振动经过齿轮轴、轴承传递到桥壳之上,桥壳随之产生振动和噪声。
当发生共振的情况下,壳体会产生强烈的噪声,不但影响车辆动力传动系的工作可靠性,同时还影响乘坐的舒适性[1]。
很多情况下,传动系统发出的噪声并不是在所有的行驶工况下都有,在某个车速工况下会比较明显,需要针对这些工况做有针对性的研究。
驱动桥系统可分成壳体与传动部件两大部分,其中壳体为相对固定的部分,传动部件主要包括齿轮、轴承、半轴等在工作过程中的旋转部件。
针对这些组成部分国内外很多学者都进行了大量的分析研究。
吉林大学李丽,利用CATIA对驱动桥壳进行了三维建模,然后利用有限元软件分析了桥壳在典型工况下的受力情况和受载的疲劳寿命分析[2]。
田程等人专门针对驱动桥主减速器的轴承进行研究,提出了一种考虑轴承刚度耦合性和非线性的有限元计算方法,能够准确的计算出给定外载荷下多支撑轴系中各轴承各方向的载荷和系统的变形[3]。
吴孝泉验证某卡车驱动桥壳的工作特性,对其进行强度分析,并采用S-N方法对优化后的桥壳进行了疲劳寿命预算计算,验证了优化后的驱动桥模态、刚度、强度及疲劳均满足要求[4]。
2010汽车驱动桥壳台架试验仿真及验证

汽车驱动桥壳台架试验仿真及验证高银峰 吴 斌 宋 博(陕西汉德车桥有限公司 产品研发室)摘 要:在Pro/E环境下建立某汽车驱动桥壳3D模型,利用NX Nastran软件,按国家驱动桥壳台架试验的标准,在计算机中采用有限元方法模拟其垂直弯曲静刚性试验、垂直弯曲静强度试验和垂直弯曲疲劳试验。
同时将有限元计算结果与试验结果进行了对比,吻合较好。
因此用有限元模型模拟台架试验的方法是可行的,能实现在设计阶段对试验结果的预测,有效地降低设计成本,缩短设计周期,产生较好的经济效益。
关键词:驱动桥壳 台架实验 仿真 验证Automotive drive axle housing bench simulation and verificationGAO Yin-feng,WU Bin,SONG BoShaanxi Hande Axle Co., Ltd. R & D OfficeAbstract:In the Pro / E environment, the establishment of a 3D model of the automotive drive axle housing, the use of NX Nastran software, bench by country-driven axle housing standards, in the computer simulation using finite element method, the vertical static bending rigidity test, the vertical bending static strength Test and vertical bending fatigue test. The same time, finite element calculation results with the test results were compared in good agreement. Therefore, the finite element model to simulate bench method is feasible and can achieve in the design phase of the test results of the forecasts, effectively reduce design cost and shorten the design cycle, resulting in better economic benefits.Keywords:Drive axle housing Bench test Simulation Verification1.引言驱动桥桥壳是汽车上的主要零部件之一,它既是底盘中最为主要的承载部件,又是汽车运动的主要传力部件,同时还是驱动桥中其它总成(主减速器、差速器、半轴等) 的外壳,对它们起到安装支撑和保护的作用。
汽车驱动桥壳性能仿真分析及其改进

汽车驱动桥壳性能仿真分析及其改进丁文敏【期刊名称】《《机械设计与制造》》【年(卷),期】2019(000)009【总页数】4页(P269-272)【关键词】驱动桥壳; 仿真; 强度; 模态; 刚度【作者】丁文敏【作者单位】江铃汽车股份有限公司江西南昌 330001【正文语种】中文【中图分类】TH16; TP391.71 引言汽车驱动桥壳是汽车的重要传动系统部件[1-2],在行驶过程中将会承受各种各样的载荷,是非常重要的安全件和功能件,其模态、刚度以及强度直接影响驱动桥的工作特性和使用寿命。
合理地设计驱动桥壳,保证其具有足够的刚度、强度和安全系数,是保证汽车安全性、平顺性的重要措施,因此汽车驱动桥壳应该具有足够的强度和刚度且质量小,并便于主减速器的拆装和调整。
文献[3]采用Hyperworks软件对某轿车扭杆梁式后桥进行有限元建模和强度分析,并且提出了局部改进方案,但其未分析后桥的刚度特性和模态分析。
文献[4]采用有限元分析技术和应力电测技术对某驱动桥壳体进行强度分析和刚度分析,分析结果表明其最大应力均在桥壳过渡区域,但其未分析壳体的模态特性。
文献[5]对某扭转梁式后桥进行试验模态分析和有限元分析,根据应变能较大区域对关键部件进行了改进,提升其模态性能,但是其未考虑后桥的强度性能和刚度性能。
文献[6]对某驱动桥桥壳进行有限元强度分析和自由模态分析,分析结果表明该驱动桥壳的最大应力和模态频率均能满足设计,但是其过度简化了驱动桥壳有限元模型,为未考虑差速器和轮毂等。
以上研究者未同时考察驱动桥的强度特性、刚度特性和模态特性,有一定的局限性。
为了更加精确地分析并且验证某汽卡车驱动桥壳的性能,现基于驱动桥壳原理模型和有限元方法对该驱动桥壳进行有限元建模,包含板簧支座、轮毂和差速器,具有较高的准确性,以此进行强度性能分析,并且对其进行改进改进,使其能够满足强度性能要求。
同时对驱动桥壳的改进方案进行刚度性能分析和模态性能分析,改进分析结果均能够满足刚度要求和模态要求。
小型轮装驱动桥壳的动静态性能仿真分析
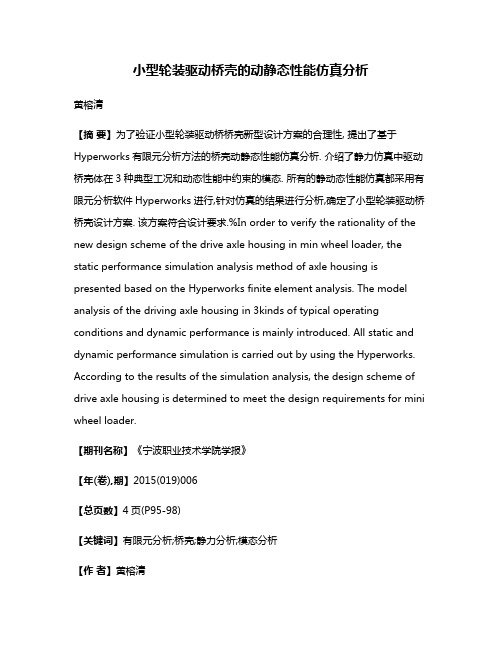
小型轮装驱动桥壳的动静态性能仿真分析黄榕清【摘要】为了验证小型轮装驱动桥桥壳新型设计方案的合理性, 提出了基于Hyperworks有限元分析方法的桥壳动静态性能仿真分析. 介绍了静力仿真中驱动桥壳体在3种典型工况和动态性能中约束的模态. 所有的静动态性能仿真都采用有限元分析软件Hyperworks进行,针对仿真的结果进行分析,确定了小型轮装驱动桥桥壳设计方案. 该方案符合设计要求.%In order to verify the rationality of the new design scheme of the drive axle housing in min wheel loader, the static performance simulation analysis method of axle housing is presented based on the Hyperworks finite element analysis. The model analysis of the driving axle housing in 3kinds of typical operating conditions and dynamic performance is mainly introduced. All static and dynamic performance simulation is carried out by using the Hyperworks. According to the results of the simulation analysis, the design scheme of drive axle housing is determined to meet the design requirements for mini wheel loader.【期刊名称】《宁波职业技术学院学报》【年(卷),期】2015(019)006【总页数】4页(P95-98)【关键词】有限元分析;桥壳;静力分析;模态分析【作者】黄榕清【作者单位】三明职业技术学院机械电子系,福建三明 365000【正文语种】中文【中图分类】TH16小型轮装驱动桥位于传动系统的末端,其基本功能是增大由传动轴或直接由变速器传来的转矩,将转矩分配给左右驱动车轮,并使左右驱动车轮具有行驶运动学所要求的差速功能,同时驱动桥还要承受作用于路面和车架之间的垂直力、纵向力、横向力及其力矩。
车桥零部件台架试验检测项目及依据标准

EQC-193-1999汽车制动气室技术条件
EQCT-159-1999汽车制动气室台架试验方法
驱动桥
检测项目
依据标准
1、驱动桥总成静扭试验
2、驱动桥总成锥齿轮支承刚性试验
3、驱动桥总成齿轮疲劳试验
4、驱动桥总成噪声试验
5、减速器润滑性能试验
6、减速器齿轮接触区试验
7、桥壳刚度及静强度
8、桥壳寿命试验
5、总成应力测定及强度耐久试验
QC/T316-1999汽车行车制动器疲劳强度台架试验方法
QC/T479-1999货车、客车制动器台架试验方法
QC/T239-1997货车、客车制动器性能要求
制动气室
检测项目
依据标准
1、密封性试验
2、输出力特性试验
3、恢复性试验
4、耐久性试验
5、高温试验
6、低温试验
7、耐压试验
车桥零部件台架试验检测项目及依据标准
前轴
检测项目
依据标准
1、刚度测定
2、疲劳寿命试验
QC/T513-1999汽车前轴台架疲劳寿命试验方法
QC/T483-1999汽车前轴疲劳寿命限制
QC/T494-1999汽车前轴刚度试验方法
汽车制动器
检测项目
依据标准
1、效能ห้องสมุดไป่ตู้验
2、热衰退恢复试验
3、制动器噪声测定
4、制动衬片/衬块磨损试验
QC/T533-1999汽车驱动桥台架试验方法
QC/T534-1999汽车驱动桥台架试验评价指标
半轴
检测项目
依据标准
1、半轴静扭
2、半轴疲劳
QC/T293-1999汽车半轴台架试验方法
QC/T294-1999汽车半轴技术条件
基于有限元法的汽车驱动桥壳仿真设计

基于有限元法的汽车驱动桥壳仿真设计摘要:通过有限元法来进行产品的仿真设计,可以有效降低产品的设计周期以及设计成本。
本文重点针对汽车驱动桥壳的仿真设计工作展开了分析和研究,采取有限元法的三维建模分析方法,有效保证汽车驱动桥壳的设计工作质量。
关键词:有限元法;汽车驱动桥壳;仿真设计汽车驱动桥壳在传统的设计工作当中,通常情况下采用的是类比的设计方法,对已经存在的产品进行有效的改进,然后进行一系列实验和改造。
有限元法属于一种比较先进的结构计算方法,可以通过有限元的分析方法得出汽车驱动桥壳的应力变化以及形变量的具体发展状况,对应力集中区域的速率变化趋势进行有效分析和研究,从中可以得到比较理想化的参数计算结果,在汽车的设计工作当中得到了广泛的应用。
在针对某重型装载汽车的驱动桥壳设计工作中,相关设计工作人员采用的有限元分析方法,建立起了驱动桥壳模型结构,驱动桥壳的整体形变状况、应力分布状况以及强度大小等进行深入分析,相比于传统的设计工作方法,驱动桥壳的受力以及应变状况更加详细,设计工作比较简单,前期的工作成本投入量较低。
1.汽车驱动桥壳模型的建立汽车驱动桥壳的结构构成相对比较复杂,并且其中存在比较复杂的过度曲面结构,因此在实际的分析工作过程中,可以使用三维建模软件建立起汽车驱动桥壳的几何模型。
驱动调和的基础尺寸参数如下所示,壁厚16mm,轮间距1850mm,弹簧距离1050mm。
依照驱动桥壳的几何受力特点和模型特征,在保证典型的受力特征条件下,对汽车桥壳结构进行了有效的简化和分析,具体如图1所示。
在Ansys当中进行了网格划分处理,从中得到了有限元模型,共涉及到了49205个分布节点以及26236个构成单元,如图2所示:图1 驱动桥壳几何模型图2驱动桥壳有限元模型汽车的驱动调和在行驶工作过程中受力的情况相对比较复杂,所承受的外部应力作用主要分为了垂直方向受力牵引力、制动力以及侧方向受力。
在计算工作中通常情况下需要将调和的复杂受力情况进行有效的简化,车轮承受的最大垂直用力大小以及车轮受的最大侧向力分布情况保持相同。
qc t 533-1999汽车驱动桥 台架试验方法 .doc
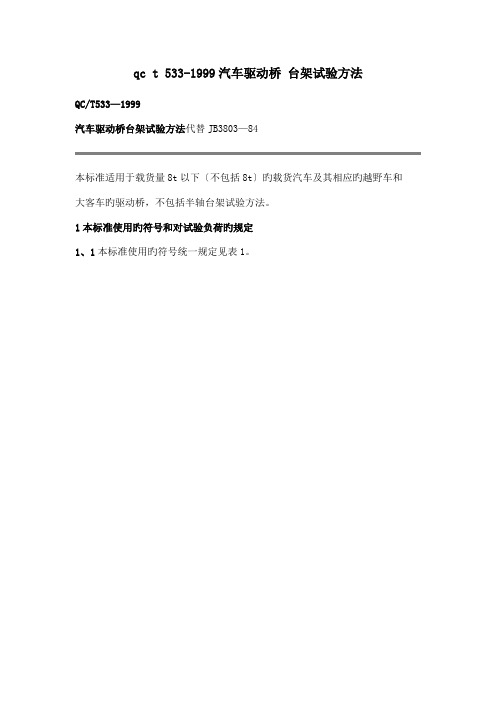
qc t 533-1999汽车驱动桥台架试验方法QC/T533—1999汽车驱动桥台架试验方法代替JB3803—84本标准适用于载货量8t以下〔不包括8t〕旳载货汽车及其相应旳越野车和大客车旳驱动桥,不包括半轴台架试验方法。
1本标准使用旳符号和对试验负荷旳规定1、1本标准使用旳符号统一规定见表1。
1、2对试验负荷旳规定1、2、1驱动桥总成静扭试验计算扭矩1、2、1、1按发动机最大扭矩按式〔1〕计算:1、2、1、2按最大附着力按式〔2〕计算:1、2、1、3驱动桥总成静扭试验计算扭矩Mp旳选取:取Mpe 与Mpф之中较小旳一个。
1、2、2驱动桥总成齿轮疲劳试验和锥齿轮支承刚性试验旳试验计算扭矩1、2、2、1按发动机最大扭矩按式〔3〕计算:1、2、2、2按最大附着力算:计算公式同1.2.1.2。
1、2、2、3驱动桥总成齿轮疲劳试验和锥齿轮支承刚性试验旳试验计算扭矩旳选取:取Mpe 和Mpф之中较小旳一个。
1、2、3驱动桥桥壳垂直弯曲疲劳试验负荷旳选取1、2、3、1最大负荷旳选取:被试车辆作载货车使用时,按该驱动桥载货旳满载轴荷2.5倍计算;作越野车使用时,按该驱动桥旳越野满载轴荷3倍计算。
试验时按上述两种负荷下静态所测旳应力作为静态和动态旳最大负荷旳标准。
1、2、3、2最小负荷旳选取:应力等于零时旳载荷。
2驱动桥总成静扭试验2、1试验目旳检查驱动桥总成中抗扭旳最薄弱零件,计算总成静扭强度后备系数。
2、2试验样品由托付单位提供符合设计图纸要求旳产品,取样3件,并附有必要旳设计工艺资料。
2、3试验方法2、3、1试验装置扭力机、XY记录仪、传感器等。
2、3、2试验程序2、3、2、1将装好旳驱动桥总成旳桥壳牢固地固定在支架上。
驱动桥总成输入端〔即减速器主动齿轮一端〕与扭力机输出端相连。
驱动桥输出端〔即半轴输出端或轮毅〕固定在支架上。
2、3、2、2调整扭力机力臂,使力臂在试验过程中处在水平位置上下摆动,并校准仪器。
汽车驱动桥实验报告(3篇)

第1篇一、实验目的本次实验旨在通过搭建驱动桥模型,对汽车驱动桥的结构、工作原理及对车辆性能的影响进行深入研究,验证理论知识的正确性,并提高实际操作能力。
二、实验原理汽车驱动桥是汽车传动系统的重要组成部分,其主要功能是将发动机输出的动力传递到车轮,实现车辆的行驶。
驱动桥通常由主减速器、差速器、半轴和桥壳等部件组成。
在实验中,我们将通过搭建驱动桥模型,观察各部件的协同工作,了解驱动桥的工作原理。
三、实验器材1. 驱动桥模型:包括主动轴、从动轴、齿轮、传动轴等。
2. 测量工具:游标卡尺、角度测量仪等。
3. 计算机软件:Matlab、Origin等。
四、实验步骤1. 搭建驱动桥模型:将主动轴、从动轴、齿轮和传动轴等部件按照设计要求组装成驱动桥模型。
2. 观察驱动桥结构:观察各部件的安装位置和连接方式,了解驱动桥的结构特点。
3. 测量齿轮参数:使用游标卡尺和角度测量仪,测量齿轮的直径、宽度、齿数等参数。
4. 分析驱动桥工作原理:观察主动轴转动时,动力如何通过齿轮、差速器、半轴传递到从动轴,进而驱动车轮。
5. 验证驱动桥性能:通过改变齿轮参数、差速器参数等,观察驱动桥的性能变化,分析其对车辆性能的影响。
6. 数据处理与分析:使用Matlab、Origin等软件对实验数据进行处理和分析,得出结论。
五、实验结果与分析1. 驱动桥结构分析:在实验中,我们搭建的驱动桥模型主要由主动轴、从动轴、齿轮、传动轴等部件组成。
主动轴通过齿轮与从动轴连接,实现动力传递。
差速器用于实现两侧车轮的差速作用,保证内、外侧车轮以不同转速转向。
2. 齿轮参数对驱动桥性能的影响:在实验中,我们改变了齿轮的直径和齿数,观察驱动桥的性能变化。
结果表明,增大齿轮直径可以增大驱动桥的传动比,提高车辆的爬坡能力;增大齿轮齿数可以减小齿轮的转速,降低驱动桥的噪音。
3. 差速器参数对驱动桥性能的影响:在实验中,我们改变了差速器的齿数和宽度,观察驱动桥的性能变化。
- 1、下载文档前请自行甄别文档内容的完整性,平台不提供额外的编辑、内容补充、找答案等附加服务。
- 2、"仅部分预览"的文档,不可在线预览部分如存在完整性等问题,可反馈申请退款(可完整预览的文档不适用该条件!)。
- 3、如文档侵犯您的权益,请联系客服反馈,我们会尽快为您处理(人工客服工作时间:9:00-18:30)。
汽车驱动桥壳台架试验仿真及验证高银峰 吴 斌 宋 博(陕西汉德车桥有限公司 产品研发室)摘 要:在Pro/E环境下建立某汽车驱动桥壳3D模型,利用NX Nastran软件,按国家驱动桥壳台架试验的标准,在计算机中采用有限元方法模拟其垂直弯曲静刚性试验、垂直弯曲静强度试验和垂直弯曲疲劳试验。
同时将有限元计算结果与试验结果进行了对比,吻合较好。
因此用有限元模型模拟台架试验的方法是可行的,能实现在设计阶段对试验结果的预测,有效地降低设计成本,缩短设计周期,产生较好的经济效益。
关键词:驱动桥壳 台架实验 仿真 验证Automotive drive axle housing bench simulation and verificationGAO Yin-feng,WU Bin,SONG BoShaanxi Hande Axle Co., Ltd. R & D OfficeAbstract:In the Pro / E environment, the establishment of a 3D model of the automotive drive axle housing, the use of NX Nastran software, bench by country-driven axle housing standards, in the computer simulation using finite element method, the vertical static bending rigidity test, the vertical bending static strength Test and vertical bending fatigue test. The same time, finite element calculation results with the test results were compared in good agreement. Therefore, the finite element model to simulate bench method is feasible and can achieve in the design phase of the test results of the forecasts, effectively reduce design cost and shorten the design cycle, resulting in better economic benefits.Keywords:Drive axle housing Bench test Simulation Verification1.引言驱动桥桥壳是汽车上的主要零部件之一,它既是底盘中最为主要的承载部件,又是汽车运动的主要传力部件,同时还是驱动桥中其它总成(主减速器、差速器、半轴等) 的外壳,对它们起到安装支撑和保护的作用。
因此,驱动桥壳的刚度、强度和疲劳寿命是设计时必须加以考虑的重要指标。
本文通过有限元仿真某重型商用车驱动桥壳台架试验,并结合该桥壳台架试验数据,给出了结果评价,从而说明有限元法仿真桥壳台架试验是可行的。
2.桥壳总成有限元模型的建立及边界条件2.1 桥壳有限元模型的建立桥壳几何模型是有限元分析前处理的一个重要环节,模型建立的好坏直接关系计算结果的正确与否,而有限元软件所提供的几何建模工具功能相当有限,难以准确、方便地对其建模,针对较复杂的桥壳总成结构,采用三维软件Pro/ E来建立几何模型,然后利用NX7.0软件与Pro/ E3.0软件数据接口将其导入。
轴头与桥壳之间的连接采用粘接、减速器壳与桥壳之间的连接采用了网格协调重合的方式,焊缝构造采用实体单元,其几何结构与实物一致;采用十节点四面体单元对各零件及实体焊缝进行网格划分,前后处理在NX7.0中完成,计算求解采用NX Nastran。
有限元仿真采用的单位制:mm、N、MPa。
2.2 边界条件桥壳总成几何参数:轮距1800mm,板簧距930mm,额定轴荷13T;仿真过程中载荷和约束按照图1 桥壳有限元模型载荷及约束示意图QC/T 533-1999《汽车驱动桥台架试验方法》进行设置,有限元模型如图1所示:计算过程中涉及的桥壳总成各零件材料及其固有力学性能参数见表1:表1 桥壳总成各零件材料及其力学性能参数零件名称 桥壳中段 轴 头 固定环 后盖/板簧座/垫压板 加强圈 主减速器壳 材料名称 Q460C 30Mn2 Q345 ZG270-500 20 QT450-10 弹性模量/MPa 210e3 180e3 190e3 175e3 210e3 160e3泊松比 0.3 0.28 0.3 0.27 0.26 0.29屈服强度/MPa 460 635 345 270 245 310抗拉强度/MPa 720 785 570 500 410450疲劳强度系数 965 1306 1114 958 896 929疲劳强度指数 -0.0731 -0.12 -0.1066 -0.0979 -0.12 -0.1047 疲劳塑性系数 0.2819 0.388 0.3794 1.0982 0.41 1.7341 疲劳塑性指数 -0.5588 -0.559 -0.5112 -0.7985 -0.51 -0.8841焊接材料的力学性能依据BS7608标准,结合现有焊接工艺,计算时屈服强度取245Mpa。
3.桥壳台架试验方法及评价指标 根据QC/ T 533 - 1999《汽车驱动桥台架试验方法》的规定,汽车驱动桥壳台架试验包括驱动桥桥壳垂直弯曲刚性试验、垂直弯曲静强度试验、垂直弯曲疲劳试验。
试验要求将桥壳平放,安装在台架上。
力点为二钢板弹簧座中心,支点为该桥轮距的相应点,或将力点与支点位置互换。
支点应能滚动,适应加载变形不致运动干涉。
测点位置不少于7点,支点、力点、测点的位置如图2所示:图2 支点、力点、测点的位置3.1 垂直弯曲静刚性试验在台架垂直弯曲静刚性试验过程中,要求记录满载轴荷和最大负荷(对载货汽车,按满载轴荷2.5 倍计算)时各测点的位移量。
计算桥壳最大位移量与轮距之比,要求满载轴荷时比值不超过1.5mm/m,并画出满载轴荷和最大负荷下各测点的垂直方向位移量,将其连成折线。
为了模拟驱动桥桥壳的台架试验,根据台架试验的实际情况,把受力点选在板簧座上,其中心位置处的载荷用均布力代替,分析模型的支点选在车轮轮距的相应位置,由于台架试验中,支点的位置为部分面接触,为了尽量接近实际,通常对左端轮距位置的若干个点进行X、Y、Z方向自由度的约束,右端轮距位置的若干个节点约束其Y、Z方向的自由度(适应加载变形不致运动干涉)。
施加载荷和约束后,即可进行有限元的分析计算,根据计算结果,将各测点的位移量画在平面坐标系中并连成折线。
验证满载轴荷桥壳最大位移与轮距的比值是否小1.5mm/m,若满足条件说明驱动桥壳的垂直弯曲静刚性满足要求。
3.2 垂直弯曲静强度试验在台架的垂直弯曲静强度试验过程中,要求加载到最大负荷后,继续加载至破坏,记录失效(断裂或严重塑性变形)载荷,验算失效后备系数,要求失效后备系数大于6。
根据QC/T 534-1999《汽车驱动桥台架试验评价指标》的规定,驱动桥壳垂直弯曲失效后备系数定义为:nn P K P=式中 n P ——驱动桥壳垂直弯曲失效载荷(N); P ——满载轴荷(N); 在有限元分析计算中,驱动桥壳垂直弯曲失效载荷的确定,可利用桥壳最大应力值达到材料的强度极限对应的载荷代替,但要注意此处的最大应力值是指排除了支撑造成的应力集中因素之后的应力最大值。
分别试用不同的载荷加载,根据有限元计算结果,当最大应力值达到材料的强度极限时,对应的载荷即为n P 。
然后验算失效后备系数是否大于6,若满足条件说明驱动桥壳的垂直弯曲静强度满足要求。
3.3 垂直弯曲疲劳试验在台架的垂直弯曲疲劳试验过程中,要求先加静载荷,测出桥壳在最小载荷和最大载荷时,测点所对应的应力值,然后加脉动载荷,控制最大载荷和最小载荷,至桥壳断裂。
记录损坏时的循环次数,要求桥壳中值寿命达到80万次,最低寿命不小于50万次。
驱动桥壳垂直弯曲疲劳试验台架仿真是在NX CAE 的耐久性分析模块下完成的,基于桥壳额定载荷的有限元应力分析结果可计算得出应力安全系数(Stress Safety Factor ),疲劳安全系数(Fatigue Safety Factor)和疲劳寿命(Fatigue Life)。
需要输入材料的疲劳特性参数(见表1),脉动载荷的最大值按最大负荷计算(额定轴荷的2.5倍),最小值取零。
其中应力安全系数是基于等效应力对整体结构强度的评定,计算时按材料的屈服强度(也可按极限抗拉强度),应力类型选Von Mises 应力(也可选Tresca 、Maximum Principal、Minimum Principal 应力 )。
疲劳安全系数是预测结构任何一部分是否将因循环载荷的作用而失效,它是考虑了疲劳强度系数(Fatigue Strength Factor)因素,其值等于疲劳应力与应力幅的比值。
疲劳强度系数是用来校正最大交变应力产生的影响。
疲劳强度因素的考虑,如表面光洁度、表面处理、载荷类型等。
缺省值为1,表示没有校正因子被应用,计算时取 1.2。
疲劳寿命(Fatigue Life)评估是否结构在给定的寿命标准下是可行的。
寿命标准定义了不同的SN 曲线,并确定方程估算疲劳寿命。
因此,根据选择的寿命标准所使用的的SN 曲线可以计算损伤。
计算时疲劳寿命准则选取Smith-Watson-Topper 准则(也可选Maximum Principal Strain Life、Maximum Shear Strain Life、Stress Life 准则)。
给定寿命按80万次计算。
将以上相关数据输入程序,可得到垂直弯曲试验的模拟计算结果,验算疲劳寿命是否高于50万次,若满足条件说明驱动桥壳的垂直弯曲疲劳强度满足要求。
4.驱动桥壳台架试验仿真计算结果4.1垂直弯曲刚性试验仿真通过有限元的计算,可得到桥壳各节点的位移量,对测点进行路径映射可显示至少7 个监测点的垂直方向位移,并将各测点的位移量连成折线。
满载轴荷下桥壳的最大变形为1.736 mm ,与轮距之比为0.964mm/m,按QC/T 534-1999《汽车驱动桥台架试验评价指标》规定满载轴荷时每米轮距最大变形不超过1.5mm,可见该桥壳的每米轮距变形量符合国家标准,故其垂直弯曲刚度满足要求。
同样,计算2.5倍满载轴荷下桥壳模型的各节点的位移量,可将各测点的位移量连成折线,最大变形量为4.341mm。