DN1600多层直接冷激式氨合成塔结构设计
氨合成塔结构设计优化

氨合成塔结构设计优化氨合成塔是工业化生产氨气的重要装置之一,其结构设计优化对提高氨合成工艺效率、降低能耗具有重要意义。
本文将从塔体结构、填料设计和塔底设计三个方面进行优化设计。
首先是塔体结构的设计优化。
氨合成塔一般采用立式圆柱形结构,其直径和高度对塔内流体的压降、液相分布等性能有着重要影响。
在设计时应考虑经济性和操作性,合理确定塔体尺寸。
通过优化塔高和直径比,可以减少塔床高度,降低液位高度,提高液相分布效果,减少气液流分离带来的液滴带走和压降增大现象。
此外,塔体内部结构如分层板的设置也需要进行合理优化,以提高液相分布的均匀性。
其次是填料设计的优化。
填料在氨合成塔中起到支撑液体的作用,促进气液两相的充分接触和反应。
合理设计填料种类和布置方式,有助于提高氨合成塔的效率。
常用的填料有环形填料、波纹填料等,每种填料都有其特点和应用范围。
优化填料的选择和布置,可以增加填料表面积,增强气液传质和传质效果,提高氨合成反应的效率。
最后是塔底设计的优化。
氨合成塔底主要包括液相分配装置和气相分配装置。
液相分配装置的设计应合理并保证液体在塔底均匀分布,避免液体集中流向其中一位置,导致气液分离不均匀。
气相分配装置的设计应保证气体均匀分布,避免气体过量或不足引起的反应失效。
同时,可以考虑使用气体分配器件,如多孔板和喷嘴等,以提高气体分布的均匀性。
在氨合成塔的结构设计中,除了上述三个方面,还应考虑到塔体和填料的材料选择、首层填料的设置、塔床厚度等因素。
优化设计需要综合考虑工艺技术要求、经济性和可操作性等多个方面的因素,并进行模拟计算和实验验证。
通过合理的优化设计,可以提高氨合成塔的工艺效率,降低能耗,达到更好的生产效果。
氨合成塔的课程设计

氨合成塔的课程设计一、课程目标知识目标:1. 学生能理解氨合成的基本原理,掌握哈柏-博世工艺流程及氨合成塔的工作原理。
2. 学生能够描述影响氨合成效率的因素,如温度、压力、催化剂等。
3. 学生能够运用化学平衡的知识分析氨合成过程中的物料与能量平衡。
技能目标:1. 学生通过小组合作,设计并构建一个简易的氨合成塔模型,提升实验操作与工程实践能力。
2. 学生能够运用数学计算和图表分析氨合成过程中的数据,培养数据分析与处理技能。
情感态度价值观目标:1. 学生通过本课程的学习,培养对化学工业的兴趣和认识,增强对化学在国民经济中作用的了解。
2. 学生在学习过程中体验团队合作的重要性,提升责任感和合作精神。
3. 学生能够理解化学工业对环境的影响,培养绿色化学和可持续发展的意识。
课程性质分析:本课程为高中化学选修课程,旨在通过氨合成塔的设计,使学生将理论知识与实际工业应用相结合,增强学生的实践操作能力和工程观念。
学生特点分析:高中阶段的学生已具备一定的化学基础知识,具有较强的逻辑思维能力和动手操作兴趣,适合开展此类理论与实践相结合的课程。
教学要求分析:课程要求教师以学生为中心,采用项目式学习法,引导学生主动探索,注重培养学生的创新能力和实践能力。
通过课程的学习,使学生能够综合运用所学知识解决实际问题。
二、教学内容1. 氨合成原理及其在工业中的应用- 哈柏-博世工艺流程介绍- 氨合成反应的化学方程式及平衡- 影响氨合成效率的因素分析2. 氨合成塔的结构与工作原理- 氨合成塔的构造及功能- 催化剂的选择与作用- 氨合成塔内温度、压力分布3. 实践操作:氨合成塔模型设计与制作- 设计简易氨合成塔模型- 实验材料与仪器的选择- 模型制作过程中的安全与环保要求4. 数据分析与处理- 实验数据收集与记录- 数据分析方法与技巧- 图表绘制与应用5. 教学内容的安排与进度- 第一周:氨合成原理及其在工业中的应用- 第二周:氨合成塔的结构与工作原理- 第三周:实践操作:氨合成塔模型设计与制作- 第四周:数据分析与处理教学内容关联教材:本教学内容与教材《化学》选修3《化学工业》章节相关,涉及氨的合成、工业生产过程、化学平衡等知识点。
贵州安顺DN1600合成系统吹扫方案

一、说明由于DN1600合成系统设备容器较多、管道粗、工艺流程长、拆装阀门多而整体空间较小,故在吹扫时气流量要大,吹扫介质要安全可靠,经研究讨论用空气作为吹扫介质,工作压力为1.96MPa,吹扫线速度要求大于20m/s。
(气流来源:新压缩机组)吹扫步骤主要按全系统流程图进行,各个吹出口均一次拆开法兰,拿下透镜垫,对应堵上盲板,最后用白布检测吹扫质量。
在吹扫过程中,以阀前、孔板前、设备前法兰作为吹出点,凡是高压阀门、流量孔板前段大于两米,都应将法兰拆开吹扫,待吹净后再连接拆口。
二、吹扫步骤2.1、主流程的吹扫2.1.1、补气氨冷器入口阀前后新鲜气管的吹扫○1依次拆新鲜气流量控制、新鲜气进口阀前作为吹出点,从新压缩机组来空气吹净阀前管内杂物、油水,直至管内壁及吹出口干净为止。
○2装上新鲜气进口阀,拆补气氨冷“b”口(新鲜气进口)作为吹出点,堵上盲板。
待吹净后再行连接。
2.1.2、补气氨冷出口管─冷交出口管的吹扫○1拆补气油分“b”口作为吹出点,待吹净后再行连接。
○2将氨分“b”口堵上盲板,拆卧式氨冷“b”口作为吹出点。
吹净后再行连接。
○3将卧式氨冷“b”口堵上盲板,拆氨分“b”口作为吹出点。
吹净后再连接氨分“b”口,保持卧式氨冷“b”口的盲板。
○5拆冷交底部“a”口作为吹出点,待吹净后再行连接。
○6将管道PG1712上四个循环机进口阀前部均堵上盲板,拆PG1712西端的盲板作为吹出点,待吹净后再堵上;然后拆PG1712东端的盲板作为吹出点,待吹净后再堵上。
2.1.3、循环机进口管─循环机油分进口管的吹扫A、循环机进口管的吹扫(以其中一台为例,其余三台照此进行)○1拆除循环机进口阀前盲板后再行连接,打开阀门(同时保持PG1712上另外三个进口阀门关闭)○2将循环机近路阀靠管道PG1712一端堵上盲板,拆循环机进口缓冲器进口作为吹出点。
B、循环机出口管的吹扫(以其中一台为例,其余三台照此进行)○1拆循环机出口止回阀前作为吹出点,吹净后再连接。
合成塔冷激式合成塔

合成塔冷激式合成塔概述合成塔冷激式合成塔是一种用于化学反应的设备,主要用于合成有机化学品和石油化工产品。
它采用冷激式技术,通过控制温度和压力来实现反应物的合成。
本文将详细介绍合成塔冷激式合成塔的原理、结构、工作过程以及应用领域。
原理合成塔冷激式合成塔基于化学反应需要在一定的温度和压力条件下进行。
通过控制反应器内的温度和压力,可以调节反应速率、选择性以及产物收率。
在合成塔中,通常使用催化剂来促进反应的进行。
结构1. 反应器反应器是整个合成塔中最核心的部件,它提供了一个封闭的空间来容纳化学反应。
反应器通常由耐高温高压材料制成,如不锈钢或镍基合金。
其内部通常涂有催化剂,以增加反应效率。
2. 加热系统加热系统负责提供所需的热量以使反应器内的反应物达到所需的温度。
常用的加热方式包括电加热、蒸汽加热和火焰加热等。
加热系统需要具备精确的温度控制能力,以确保反应物在合适的温度下进行反应。
3. 冷却系统冷却系统用于控制反应器内部的温度,防止反应过程中产生过多的热量。
冷却系统通常采用循环水或冷却剂来吸收和带走反应器中产生的热量。
4. 压力控制系统压力控制系统用于维持反应器内部的压力稳定。
通过调节进料流量、排出流量以及回收流量等参数,可以实现对反应器内部压力的精确控制。
5. 流体分离装置流体分离装置用于将反应产物从废气或废液中分离出来。
常见的分离技术包括蒸馏、萃取、吸附等。
合成塔中通常会配备多级分离装置,以提高产品纯度和回收率。
工作过程合成塔冷激式合成塔的工作过程可以分为以下几个步骤:1.加料:将反应物通过进料管道加入到反应器中。
加料过程中需要控制流量和浓度,以确保反应物的均匀分布和合适的浓度。
2.加热:启动加热系统,提供所需的热量使反应器内的反应物达到所需温度。
加热过程中需要精确控制温度,以避免过高或过低温度对反应产生不良影响。
3.反应:在适当的温度和压力条件下,催化剂促使反应物发生化学变化。
反应过程中产生的热量会被冷却系统吸收并带走。
NC型φ1600mm氨合成系统改造小结

该系统 的合成塔采用了南化研究院提供的 “ 二轴
二径”内件 ,具有 自 卸催化剂功能 ,催化剂总装 量为 6 0t 。系统工艺流程如图 1 。
我公司是全 国中氮行业 中首家使用 0 0 16 0 r n 成塔 的企 业 。(1 0 UI f 合 l r 2 01T氨合成 系统是 我 )6 T
氨合成系统在较低负荷下稳定生产 ,要达到设计 生产能力 ,还必须做进一步 的技术改造。
20 06年初 ,公 司决 定 利 用 更 换 催 化 剂 的 机 会对 (1 0 m合成氨系统进行彻底的技术改 2 0m )6
2 1 。有效 容积不够 ,导致工 艺气体 流速过 .倍 快 ,气液分离效果差。因此 ,我公 司单台供 D1
维普资讯
第 4期 20 o 7年 7月
中 氮
肥
No. 4
M . i d Ni o e o sFet i rP o rs Sz t g n u riz r g es e r le
J1 0 7 u .2 0
NC型 016 0mm 氨合成 系统改造小结 0
通风冷 却 。 以上改造虽效果 明显 ,但 只能保证 60mm 0
机运行 ,维持人塔循环气量≤10 0 3h的低 7 0m / 0
负荷工 况 。
笔者认为氨分效果差的原因主要是设计的氨 分有 效容 积太 小。该 系统 氨 分规 格为 (10 0 2 0 ) m m ̄4 8 m,有效容积仅为 36 3 9m 6 . m ;而现 8 在即使是 01 0 m 氨合成系统在设计上也倾 0m 5 向于选择规格为 ( 0 m× 2 2 20 ) 1 m 6 5 8 mm的氨分 , 其有效 容积达 7 7 3 .5m ,是该 系统氨分 容积 的
氨合成塔
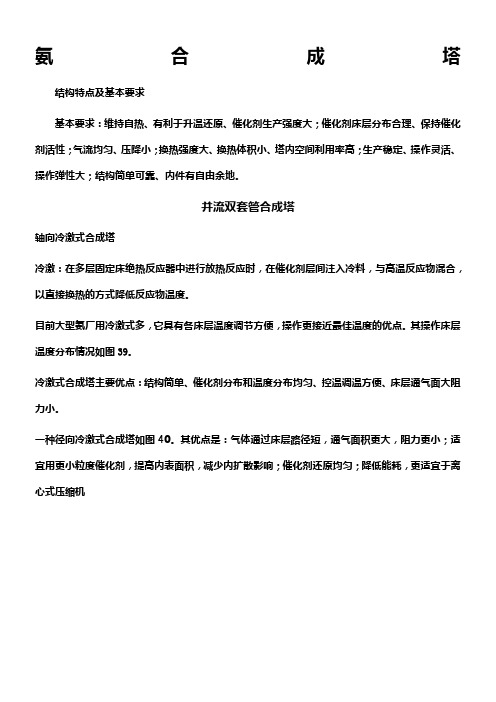
氨合成塔结构特点及基本要求
基本要求:维持自热、有利于升温还原、催化剂生产强度大;催化剂床层分布合理、保持催化剂活性;气流均匀、压降小;换热强度大、换热体积小、塔内空间利用率高;生产稳定、操作灵活、操作弹性大;结构简单可靠、内件有自由余地。
并流双套管合成塔
轴向冷激式合成塔
冷激:在多层固定床绝热反应器中进行放热反应时,在催化剂层间注入冷料,与高温反应物混合,以直接换热的方式降低反应物温度。
目前大型氨厂用冷激式多,它具有各床层温度调节方便,操作更接近最佳温度的优点。
其操作床层温度分布情况如图39。
冷激式合成塔主要优点:结构简单、催化剂分布和温度分布均匀、控温调温方便、床层通气面大阻力小。
一种径向冷激式合成塔如图40。
其优点是:气体通过床层路径短,通气面积更大,阻力更小;适宜用更小粒度催化剂,提高内表面积,减少内扩散影响;催化剂还原均匀;降低能耗,更适宜于离心式压缩机。
氨合成塔封头结构设计与应力分析
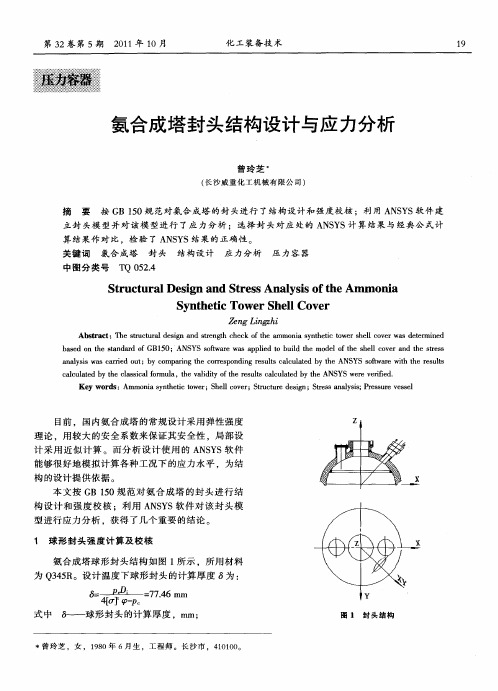
b s d o h t n a d o a e n t e sa d r f GB1 0;ANS ot a e w s a p i d t u l h d lo h h l c v ra d t e sr s 5 YS s f r a p l o b i t e mo e ft e s e l o e n h te s w e d
目前 ,国 内氨合 成塔 的常规 设计 采用 弹性 强度 理论 ,用较 大 的安全 系数 来保 证 其安 全性 ,局 部设
计 采 用 近似 计 算 。 而分 析 设 计 使 用 的 A S S软件 NY
能够 很好 地模 拟 计算 各 种工 况下 的应 力水 平 ,为结 构 的设计 提 供依 据 。
替 循环 排 列 ,最外 层套 筒为 光 气使 用。从 各 个套 筒
内流 出的 流体 ,靠 出 口流速 差异 形 成 的 径 向脉 动 ,
进 行 适 度 的 混 合 . 随 后 使 流 体 的 流 动 尽 可 能 接 近 活
求 ,该 发 明提 出了在 整 个流 通截 面上 .实现 分层 环 状 流体 输入 的套 筒分 布 式反应 器 。采 用套 筒分布 式
S r t a sg n S r s t ucur lDe i n a d t e sAnay i ft eAm m o a lsso h ni
S n h tcTo rS el v r y t ei we h l Co e
Zn e gLig h nzi
Ab ta t h t c u a e i n a d s e gh c e k o e a sr c :T e sr t r l sg n t n t h c ft mmo i y t ei o rs elc v rw s d t r n d u d r h n a s n h t twe h l o e a ee mi e c
氨合成塔【范本模板】

氨合成塔
结构特点及基本要求
基本要求:维持自热、有利于升温还原、催化剂生产强度大;催化剂床层分布合理、保持催化剂活性;气流均匀、压降小;换热强度大、换热体积小、塔内空间利用率高;生产稳定、操作灵活、操作弹性大;结构简单可靠、内件有自由余地。
图34
并流双套管合成塔
图38图37
轴向冷激式合成塔
冷激:在多层固定床绝热反应器中进行放热反应时,在催化剂层间注入冷料,与高温反应物混合,以直接换热的方式降低反应物温度。
目前大型氨厂用冷激式多,它具有各床层温度调节方便,操作更接近最佳温度的优点。
其操作床层温度分布情况如图39。
冷激式合成塔主要优点:结构简单、催化剂分布和温度分布均匀、控温调温方便、床层通气面大阻力小.
图38
一种径向冷激式合成塔如图40。
其优点是:气体通过床层路径短,通气面积更大,阻力更小;适宜用更小粒度催化剂,提高内表面积,减少内扩散影响;催化剂还原均匀;降低能耗,更适宜于离心式压缩机。
- 1、下载文档前请自行甄别文档内容的完整性,平台不提供额外的编辑、内容补充、找答案等附加服务。
- 2、"仅部分预览"的文档,不可在线预览部分如存在完整性等问题,可反馈申请退款(可完整预览的文档不适用该条件!)。
- 3、如文档侵犯您的权益,请联系客服反馈,我们会尽快为您处理(人工客服工作时间:9:00-18:30)。
1绪论现今氨合成工艺在我国氮肥厂得到广泛的应用。
展望国内氨合成塔内件可以说种类繁多,绝大多数的氨厂合成操作压力为31.36MP&合成塔内件为传统的冷管型内件。
其中三套管、单根并流、双套管式内件占大多数。
此外,另有一批冷管改进型内件:比如川J型、YD型、NC型、轴径向、副产蒸汽式等。
塔内换热器大部分为列管式,还有少数为螺旋式、波纹板式。
小型氨厂大部分采用© 600、© 800直径塔。
日产合成氨达80t、100t、150t不等。
中型氨厂大多采用© 1000、© 1200直径塔。
高压筒体高度为13.5〜16m日产氨200t、250t、290t不等。
传统型内件氨净值大部分为9%〜12%之间,改进型内件在12%〜16%之间。
合成塔阻力降0.6〜1.2MP&配置的余热回收装作吨氨副产蒸汽为600〜800kg/t NH 3, 压力为1.3〜2.5MP&下面简单介绍两种内件:全冷激式内件全冷激式内件是一种在中小型氨厂推广使用的新型内件,它与传统内件(内冷式内件)有本质区别,将圆催化剂中的冷管取消,将一个大的催化剂反应床分割为若干个小的催化剂反应床,床层之间采取冷激换热的方式将反应热一直,以便将反应能继续进行下去。
冷激式内件是多层绝热、层间换热式内件中最简单的一种。
它与层间水冷式内件几乎同时应用与多种合成氨厂。
它具有结构简单,运行可靠的特点。
此种内件根据合成系统工作压力、催化剂活性温度、催化剂温区范围、反应热回收方式等因素以及要达到的氨净值来确定催化剂床的数量。
多层换热式内件具有三大特点:(1)多层绝热,层间换热。
用未反应的气体作为冷源,一方面将反应后的热气体热量移走;另一方面自身温度提高达到第一绝热床时的零米温度。
(2)催化剂筐采用径向型(3)宽温区催化剂对于整台合成塔,需设计和制造外壳,所设计的外壳具有一下特点:(1)球形封头结构成熟,使用材料较省,若采用锻件,则将增加一倍以上的重量。
(2)多层包扎筒体国内制造经验丰富。
成熟可靠,材料也易于解决,设备安全性高。
(3)顶部大开口大平盖便于内件安装和维修,便于催化剂装填和卸除,大盖的安装起吊比较方便,顶部的管口易于布置。
(4)顶部筒体密封采用双锥垫结构密封使用成熟,密封可靠。
塔设备的作用是实现气(汽)-液相或液-液相之间的充分接触,从而达到相际间进行传质的目的。
塔设备广泛应用于合成、蒸馏、吸收、介吸、萃取、气体的洗涤、增湿及冷却等单元操作。
它的操作性能好坏,对整个装置的生产,产品产量、质量、成本以及环境保护、“三废”处理都有较大的影响。
因此对塔设备的研究一直是工程界所关注的热点,随着石油、化工的迅速发展,塔设备的合理造型及设计将越来越受到关注和重视。
氨是最为重要的基础化工产品之一,其产量居各种化工产品的首位;同时也是能源消耗的大户,世界上大约有10%勺能源用于生产合成氨。
氨主要用于农业,合成氨是氮肥工业的基础,氨本身是重要的氮素肥料,其他氮素肥料也大多是先合成氨、再加工成尿素或各种铵盐肥料,这部分约占70%勺比例,称之为“化肥氨” 同时氨也是重要的无机化学和有机化学工业基础原料,用于生产铵、胺、染料、炸药、制药、合成纤维、合成树脂的原料,这部分约占30%勺比例,称之为“工业氨”。
未来合成氨技术进展的主要趋势是“大型化、低能耗、结构调整、清洁生产、长周期运行”。
在合成氨流程中,氨合成塔是其最主要的部分。
氨合成装置的结构也是种类繁多,具体情况如下。
(1)按触煤层反应热的取走方式分类触煤层反应热的取走方式有两种:内冷式和冷激式。
(2)按触煤层气流反向分类触煤层的气流方向也有两种:轴向——气体沿塔的轴向通过触煤层;径向一—气体在触煤层内作径向流动。
轴向合成塔径向合成塔轴径向合成塔(3)按外形分类立式合成塔卧式合成塔球形合成塔(4)按合成塔氨日产量分类大型合成塔(日产1000t以上,包括1000t)中型合成塔(日产150t左右)大型合成塔(日产50t左右)三种冷激式合成塔:(1)多层轴向冷激式合成塔(2)三层冷激式径向合成塔(3)两层径向冷激式合成塔(托普索型)国内外氨合成工业的发展状况合成氨是重要的化工产品,可以制成尿素、硝酸按和碳酸氢氨等氨素肥料。
合成氨工业是氮肥工业的基础,对农业生产起着重要作用。
人们常称合成氨为高能耗产品。
这有两层含义,一为氨本身热值较高,气氨的热值为22.488X 106kJ/t, 二为生产过程中损耗了大量能量。
目前常规的合成氨技术能量消耗占总成本的 70%,加上合成塔的庞大及工艺流程的复杂,使合成氨工业具有投资大、能量消耗巨大、停产维修困难、运行费用高等缺点。
目前,我国中小型化肥厂的能耗为 44X 106~71 X 106kJ/t;而国外先进的制氨工艺己降至 30X 106kJ/t左右。
因此降低合成氨的能耗,简化工艺过程,成为合成氨研究的一个重要方向。
(1)国内合成氨工业发展的现状在国内,七十年代之后,氨合成工艺的合成压力是逐年递增。
与国外合成氨工艺的合成压力逐年降低的趋势恰恰相反。
目前普遍采用31.4MPa高压操作,致使能耗高居不下。
大化肥和小化肥的科技进步与技术改造过程充分表明,合成氨工业的技术进步趋势是企业上规模,研发和使用节能型低温低压高活性氨合成催化剂,降低合成压力再辅以先进的工艺和设备,才能达到节能降耗的目的。
中国合成氨生产是在20世纪30年代开始的[6],经过几十年的努力,我国现有大型(30万吨/年)合成氨厂31家、中型56家、小型828家。
近几年我国合第3页共66页成氨产量约3000多万吨,2005年需求约为3500万吨,都居世界首位,是美国的2倍。
合成氨工业每年消耗煤炭 4000多万吨(标煤)、电力400多亿kwh就业人数近百万人。
在大中小三类企业中,引进的大型装置的能耗接近国外水平,而中小企业(占全国总产量的52.14%)的成本远高于大型装置,其能耗则高出先进水平近一倍。
巨大的经济利益始终推动着合成氨工业及其催化剂的技术进步与发展,降低能耗是合成氨工业技术进步的核心。
(2)国外合成氨工业发展的现状自本世纪20年代第一座合成氨装置投产以来,到60年代中期,合成氨工业在欧洲、美国、日本等地区已发展到相当高的技术水平。
美国Kelofgg公司首先开发出以天然气为原料、日产干吨的大型合成氨装置,在美国投产后,使吨氨能耗达到42.OGJ的先进水平。
与此同时,美国Braun公司、丹麦Topsoe公司、英国ICI公司、日本Toyo公司等世界各大制氨公司,也都积极从事制氨技术的开发工作,形成了各具特色的工艺路线,如丹麦Topsoe公司和英国Icl公司在以轻油为原料的制氨技术方面,处于世界领先地位,这是合成氨工业发展史上第一次技术变革和飞跃。
70年代中期,由于世界石油危机,能源价格不断上涨,严重冲击着世界石油危机,能源价格不断上涨,严重冲击着合成氨工业,造成成本上升、经济效益下降,在这种严峻的形势下,世界上各合成氨大公司都以节能为目标,竞相开发出各具特色的节能型新工艺流程,合成氨工业在80年代又经历了第二次突破性的技术变革。
如美国Kellgog公司、Braun公司、KTI公司、丹麦Topsoe公司、英国ICI公司、德国Uhde公司、意大利Mnoetdsno公司等都积极开发新流程及与新流程相适应的高效催化剂和新设备,借以提高制氨技术在世界上的竞争能力。
近年来,为了节能降耗、增加产量,在传统工艺的基础上,国内外均推出了一系列节能型氨合成工艺技术及流程,其主要改进的目的是增加氨合成转化率(提高氨净值)、降低合成压力、减小合成回路压降、合理利用能量。
(3)合成氨工业的发展近年来,氨合成工艺技术已取得长足进步。
特别是市场经济体制的建立,各氮肥企业为了在市场竞争中走在前列,纷纷围绕节能降耗,加大技改力度,为氨第4页共66页合成技术的新发展提供了一个平台。
在此形势下,各企业对氨合成装置的要求,逐渐由以前的强化高负荷生产转变到现在的轻负荷低消耗运行模式上来。
因此氨合成的关键设备合成塔,在同等规模条件下,也逐渐的被大塔取代,出现了“大马拉小车”的局面。
一些© 1200、© 1500、© 1600、© 1800、© 2000的大直径塔逐渐被研制来,并投入到工业生产中去。
伴随着大直径塔的使用,氨合成系统工艺运行条件发生了变化。
低温低压氨合成催化剂的应用,也是企业节能降耗可行途径之一。
大直径塔及低温低压催化剂的使用,加大了企业的设备投入。
企业势必采取各种措施保持装置长周期运行,以求得更多的有效生产时间。
因此,原料气的净化度高,避免催化剂中毒,至关重要。
积极使用原料气净化新技术,实现原料气微量(CO+ CO2)趋近于“零”,避免铜液、油水入塔,最大限度的减少毒物对催化剂的影响将会被人们逐渐重视。
降低能耗始终是合成氨工业技术进步追求的目标。
合成氨工业技术进步的发展趋势是开发与采用新型低温低压高活性催化剂,降低合成氨压力达到降低能耗的目的。
随着氨合成工业技术的进步,世界各国的氨合成塔均向低能耗,高效率的方向发展。
合成塔设计是多学科发展的高科技产物,它依赖于合成氨工艺的发展,合成触媒的开发,高强度抗腐蚀材料的研究,乃至计算机辅助手段的综合发展而逐步完善的。
我国合成塔设计落后于其他发达国家,在一定意义上,主要是受压力容器制造技术的限制和高强度抗腐蚀材料研究的缓慢。
随着我国改革开放和科学技术的迅速发展,我国合成塔的设计,必将有一个新的飞跃。
氨合成塔的工作原理简述在高压、高温下用来使氨气和氢气发生催化反应以进行氨合成的设备。
氨合成塔使合成氨厂的心脏,使一种结构复杂的反应器。
现在工业上氨合成是在压力 15.2~30.4Mpa、温度400~520 C下进行的,为防止高压、高温下氢气对钢材的腐蚀,氨合成塔由耐高压的封头、外筒和装在筒体内耐高温的内件组成。
内件外由保温层,操作时进塔的冷气体流过内、外筒间的环隙,从而避免外筒温度过高。
这样,外筒只承受高压,可用低合金高强度钢制作。
内件虽然是在高温下操作,但是只承受氨合成塔进出口压力差,可用耐热镍铬合金钢制作。
内件包括催化剂筐和换热器两个主要部分,筐内装铁催化剂,氨合成反应在此进行。
从催化剂筐出来的热气体温度通常在460C以上,进入氨合成塔的冷气流体温度根据流程不同,有的为20~30C,有的可达140C以上。
为了使进入氨合成塔的气体能加热到反应温度,同时又能冷却反应后的气体,在塔内还设有换热器。
换热器有列管式,螺旋板式和波纹板式,其中列管式采用最多。
氨合成催化剂在开车之前必须还原,还原需要提供一定的热量,为此中小型氨合成塔内部装有电加热器,大型氨合成塔则采用塔外设置开工加热炉的办法来解决。