典型零件选材及工艺分析.
零件选材及工艺路线

(5)选材时应考虑我国的资源和供应情况,尽量选 用我国资源丰富的合金钢系列,如锰钢、硅锰钢 等;少选或不选含镍、铬、钴等我国资源缺乏的 钢种。 (6)应根据厂家的具体情况选择工艺成熟的材料, 以降低加工费,提高成品率。同时,还应考虑所 选材料的品种尽量少而集中,以减少管理费用; 尽量选用本地区或就近可以供应的材料,以降低 运输费用。此外,所选材料还应考虑环保问题等。
§ 1 选材的原则
1.2工艺性能选材原则(陶瓷材料)
硬而脆且导热性较差。根据陶瓷制品的材料、性能 要求、形状尺寸精度及生产率不同,可选用粉浆成形、
压制成形、挤压成形、可塑成形等方法。陶瓷材料的
切削加工性能极差,除极少数陶瓷外 ( 如氮化硼陶瓷 ) , 其它陶瓷均不可切削加工;陶瓷虽可磨削加工,但其
§ 3 典型零件选材与工艺分析
工程材料的应用概况
复合材料克服了高分子材料和陶瓷材料的不足,综
合了各种不同材料的优良性能,具有高的比强度、比刚 度、抗疲劳、减振、耐磨性能优良等特点。尤其是金属 基复合材料,从力学性能角度看,可能是最理想的机械 工程材料。但复合材料价格昂贵,除在航天航空、船舶、 武器装备等国防工业中的重要结构件上应用外,在一般 的民用工业上应用有限。但应注意的是,随着复合材料 的生产成本降低,其应用潜力巨大、前景极其广阔。
预防和控制热处理变形的方法与措施
预防和控制热处理变形的方法与措施
1.2工艺性能选材原则(高分子材料)
齿轮常用材料的选择及其热处理工艺分析
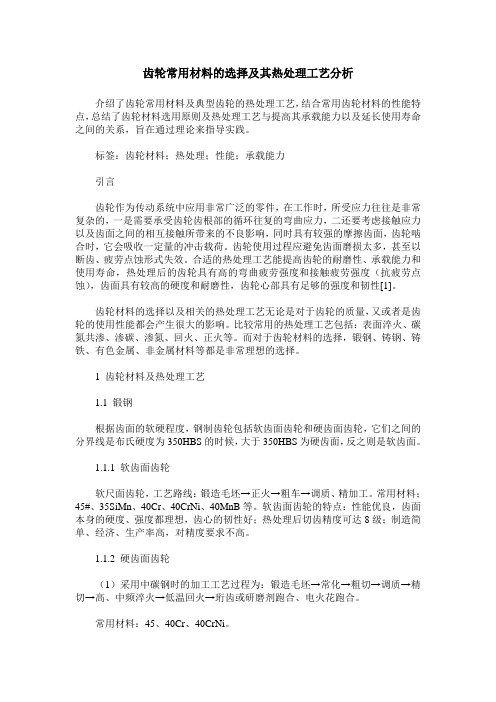
齿轮常用材料的选择及其热处理工艺分析介绍了齿轮常用材料及典型齿轮的热处理工艺,结合常用齿轮材料的性能特点,总结了齿轮材料选用原则及热处理工艺与提高其承载能力以及延长使用寿命之间的关系,旨在通过理论来指导实践。
标签:齿轮材料;热处理;性能;承载能力引言齿轮作为传动系统中应用非常广泛的零件,在工作时,所受应力往往是非常复杂的,一是需要承受齿轮齿根部的循环往复的弯曲应力,二还要考虑接触应力以及齿面之间的相互接触所带来的不良影响,同时具有较强的摩擦齿面,齿轮啮合时,它会吸收一定量的冲击载荷。
齿轮使用过程应避免齿面磨损太多,甚至以断齿、疲劳点蚀形式失效。
合适的热处理工艺能提高齿轮的耐磨性、承载能力和使用寿命,热处理后的齿轮具有高的弯曲疲劳强度和接触疲劳强度(抗疲劳点蚀),齿面具有较高的硬度和耐磨性,齿轮心部具有足够的强度和韧性[1]。
齿轮材料的选择以及相关的热处理工艺无论是对于齿轮的质量,又或者是齿轮的使用性能都会产生很大的影响。
比较常用的热处理工艺包括:表面淬火、碳氮共渗、渗碳、渗氮、回火、正火等。
而对于齿轮材料的选择,锻钢、铸钢、铸铁、有色金属、非金属材料等都是非常理想的选择。
1 齿轮材料及热处理工艺1.1 锻钢根据齿面的软硬程度,钢制齿轮包括软齿面齿轮和硬齿面齿轮,它们之间的分界线是布氏硬度为350HBS的时候,大于350HBS为硬齿面,反之则是软齿面。
1.1.1 软齿面齿轮软尺面齿轮,工艺路线:锻造毛坯→正火→粗车→调质、精加工。
常用材料;45#、35SiMn、40Cr、40CrNi、40MnB等。
软齿面齿轮的特点:性能优良,齿面本身的硬度、强度都理想,齿心的韧性好;热处理后切齿精度可达8级;制造简单、经济、生产率高,对精度要求不高。
1.1.2 硬齿面齿轮(1)采用中碳钢时的加工工艺过程为:锻造毛坯→常化→粗切→调质→精切→高、中频淬火→低温回火→珩齿或研磨剂跑合、电火花跑合。
常用材料:45、40Cr、40CrNi。
齿轮硬度要求

齿轮硬度要求 IMB standardization office【IMB 5AB- IMBK 08- IMB 2C】二、典型零部件选材及工艺分析金属材料、高分子材料、陶瓷材料及复合材料是目前的主要工程材料。
高分子材料的强度、刚度较低、易老化,一般不能用于制作承受载荷较大的机械零件。
但其减振性好,耐磨性较好,适于制作受力小、减振、耐磨、密封零件,如轻载齿轮、轮胎等。
陶瓷材料硬而脆,一般也不能用于制作重要的受力零部件。
但其具有高熔点、高硬度、耐蚀性好、红硬性高等特点,可用于制作高温下工作的零部件、耐磨耐蚀零部件及切削刀具等。
复合材料克服了高分子材料和陶瓷材料的不足,具有高比强度、高减振性、高抗疲劳能力、高耐磨性等优异性能,是一种很有发展前途的工程材料。
与以上三类工程材料相比,金属材料具有优良的使用性能和工艺性能,储藏量大,生产成本比较低、广泛用于制作各种重要的机械零件和工程构件,是机械工业中最主要、应用最广泛的一类工程结构材料。
下面介绍几种钢制零部件的选材及热处理工艺分析。
㈠齿轮类零件的选材齿轮是机械工业中应用广泛的重要零件之一,主要用于传递动力、调节速度或方向。
1、齿轮的工作条件、主要失效形式及对性能的要求。
⑴齿轮的工作条件:①啮合齿表面承受较大的既有滚动又有滑动的强烈磨擦和接触疲劳压应力。
②传递动力时,轮齿类似于悬臂梁,轮齿根部承受较大的弯曲疲劳应力。
③换挡、启动、制动或啮合不均匀时,承受冲击载荷。
⑵齿轮的主要失效形式:①断齿:除因过载(主要是冲击载荷过大)产生断齿外,大多数情况下的断齿,是由于传递动力时,在齿根部产生的弯曲疲劳应力造成的。
②齿面磨损:由于齿面接触区的磨擦,使齿厚变小、齿隙加大。
③接触疲劳;在交变接触应力作用下,齿面产生微裂纹,遂渐剥落,形成麻点。
⑶对齿轮材料的性能要求:①高的弯曲疲劳强度;②高的耐磨性和接触疲劳强度;③轮齿心部要有足够的强度和韧性。
2、典型齿轮的选材⑴机床齿轮机床齿轮的选材是依其工作条件(园周速度、载荷性质与大小、精度要求等)而定的。
机械工程材料第6章典型零件选材
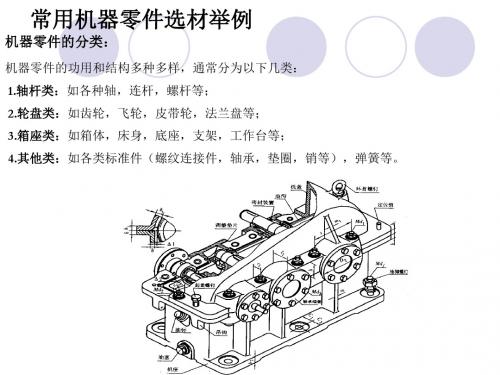
表6.1
工作条件 ①与滚动轴承配合 ②轻、中载荷,转速低 ③精度要求不高 ④稍有冲击
表6.1 机床主轴工作条件、用材及热处理
材料 45 主要热处理 正火或调质 硬度 220~250 HBS 使用实例 一般简式机床
①与滚动轴承配合 ②轻、中载荷,转速略高 ③精度要求不太高 ①与滑动轴承配合 ②有冲击载荷 ①与滚动轴承配合 ②中等载荷,转速较高 ③精度要求较高 ④冲击与疲劳较小 ①与滑动轴承配合 ②中等载荷,转速较高 ③精度要求很高 ①与滑动轴承配合 ②中等载荷,心部强度不高,转 速高 ③精度要求不高 ④有一定冲击和疲劳 ①与滑动轴承配合 ②重载荷,转速高 ③有较大冲击和疲劳载荷
2、轴类零件选材及加工工艺路线确定步骤
1)看懂零件图 了解和分析零件的形状、大小与特征; 2)分析其工作条件、性能要求和热处理要求; 3)确定材料及热处理工艺 根据用途,选择合适的材料和强 化工艺; 4)确定零件的加工工艺路线 制造轴类零件常采用锻造、切 削加工、热处理(预先热处理及最终热处理)等工艺,其中 切削加工和热处理工艺是制造轴类零件必不可少的。台阶尺 寸变化不大的非重要轴,可选用与轴的尺寸相当的圆棒料直 接切削加工而成,然后进行热处理,不必经过锻造加工。
右图为“解放”牌载重汽车变速箱变速 齿轮。该齿轮将发动机动力传递到后轮, 并起倒车的作用,工作时承载、磨损及 冲击负荷均较大。要求齿轮表面有较高 的耐磨性和疲劳强度,心部有较高的强 度(σb > 1 000 MPa)及韧性(αk>60 J/ cm2)。 选材及加工工艺路线有以下两种方式。
“解放”牌载重汽车变速箱变速齿轮选材及加工工艺路线
2)汽车半轴: 汽车半轴是一个传递扭矩的重要 部,工作时承受冲击、弯曲疲 劳和扭转应力的作用,要求材 料有足够的抗弯强度、疲劳强 度和较好的韧性。
典型零件的选材与工艺路线分析.

2. 汽车齿轮
汽车齿轮功能—在变速箱中,通过它改变发动机、曲轴和主轴齿轮的速比; 在差速器中,齿轮增加扭矩,并调节左右轮的转速。全部 发动机动力均通过齿轮传给车轴,推动汽车运行。 工作条件—汽车齿轮受力较大,受冲击频繁,其耐磨性、疲劳强度、 心部强度以及冲击韧性等,均要求比机床齿轮高。 选材—用低碳钢进行渗碳处理来作重要齿轮。我国应用最多的 是合金渗碳钢20CrMnTi,
三、齿轮材料的性能要求
1.高的弯曲疲劳强度; 2. 高的接触疲劳强度和耐磨性;
3. 较高强度和冲击韧性。
还要求有较好的热处理工艺性能,例如热处理变形小,或变形有一定规律等。
四、典型齿轮选材举例
1.机床齿轮
机床变速箱齿轮担负传递动力,改变运动速度和方向的任务。 工作条件较好,转速中等,载荷不大,工作平稳无强烈冲击。 一般可选中碳钢制造,为了提高淬透性,也可选用中碳合金钢。
喷丸—增大表层压应力,提高疲劳强度,并清除氧化皮。
第八章 典型零件的选材与工艺路线分析
8.1齿轮选材
单元34- 1
第八章 典型零件的选材与工艺路线分析 8.1 齿轮选材 齿轮主要用于传递扭矩和调节速度, 一. 齿轮的工作条件
1.由于传递扭矩,齿根承受很大的变弯曲应力;
2.换挡、启动或啮合不均时,齿部承受一定冲击载荷;
3.齿面相互滚动或滑动接触,承受很大的接触压应力及摩擦力的作用。
第八章 典型零件的选材与工艺路线分析
8.1齿轮选材
单元34- 4
工艺路线:下料→锻造→正火→切削加工→渗碳→、淬火 及低温回火→喷丸→磨削加工 正火—可消除锻造应力,均匀组织,改善切削加工性, 改善齿轮表面加工质量。
渗碳、淬火及低温回火—得到表面高硬度、高耐磨性和接触疲劳抗力。 由于合金元素提高淬透性,淬火、回火后可 使心部获得较高的强度和足够的冲击韧性。
(完整word版)轴类零件选材及工艺分析
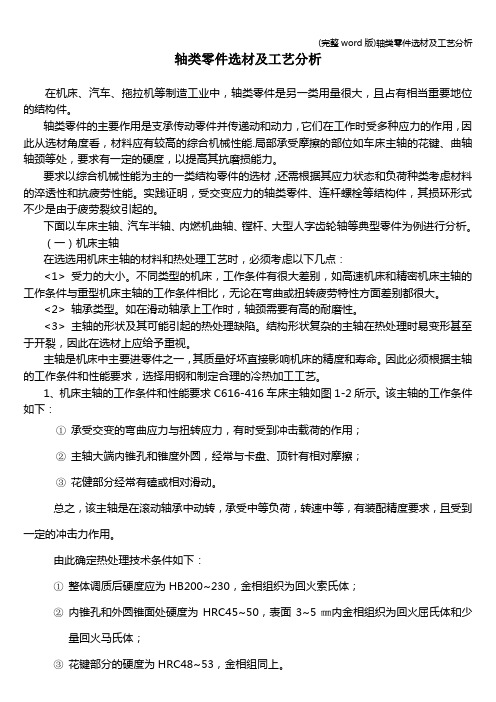
轴类零件选材及工艺分析在机床、汽车、拖拉机等制造工业中,轴类零件是另一类用量很大,且占有相当重要地位的结构件。
轴类零件的主要作用是支承传动零件并传递动和动力,它们在工作时受多种应力的作用,因此从选材角度看,材料应有较高的综合机械性能.局部承受摩擦的部位如车床主轴的花键、曲轴轴颈等处,要求有一定的硬度,以提高其抗磨损能力。
要求以综合机械性能为主的一类结构零件的选材,还需根据其应力状态和负荷种类考虑材料的淬透性和抗疲劳性能。
实践证明,受交变应力的轴类零件、连杆螺栓等结构件,其损环形式不少是由于疲劳裂纹引起的。
下面以车床主轴、汽车半轴、内燃机曲轴、镗杆、大型人字齿轮轴等典型零件为例进行分析。
(一)机床主轴在选选用机床主轴的材料和热处理工艺时,必须考虑以下几点:<1> 受力的大小。
不同类型的机床,工作条件有很大差别,如高速机床和精密机床主轴的工作条件与重型机床主轴的工作条件相比,无论在弯曲或扭转疲劳特性方面差别都很大。
<2> 轴承类型。
如在滑动轴承上工作时,轴颈需要有高的耐磨性。
<3> 主轴的形状及其可能引起的热处理缺陷。
结构形状复杂的主轴在热处理时易变形甚至于开裂,因此在选材上应给予重视。
主轴是机床中主要进零件之一,其质量好坏直接影响机床的精度和寿命。
因此必须根据主轴的工作条件和性能要求,选择用钢和制定合理的冷热加工工艺。
1、机床主轴的工作条件和性能要求C616-416车床主轴如图1-2所示。
该主轴的工作条件如下:①承受交变的弯曲应力与扭转应力,有时受到冲击载荷的作用;②主轴大端内锥孔和锥度外圆,经常与卡盘、顶针有相对摩擦;③花健部分经常有磕或相对滑动。
总之,该主轴是在滚动轴承中动转,承受中等负荷,转速中等,有装配精度要求,且受到一定的冲击力作用。
由此确定热处理技术条件如下:①整体调质后硬度应为HB200~230,金相组织为回火索氏体;②内锥孔和外圆锥面处硬度为HRC45~50,表面3~5㎜内金相组织为回火屈氏体和少量回火马氏体;③花键部分的硬度为HRC48~53,金相组同上。
单元34-1第八章典型零件的选材与工艺路线分析

不锈钢具有优良的耐腐蚀性和机械性能,适用于制造高强度、耐腐蚀的零件,如压力容器、管道等。焊接工艺能够实现异种材料的连接,因此不锈钢材料与焊接工艺相匹配适用于这些零件的制造。
不锈钢材料与焊接工艺
典型零件的选材与工艺路线实例分析
#O4
#2022
轴类零件的选材与工艺路线分析
总结词
轴类零件是机械中常见的支撑和传动零件,其选材和工艺路线分析需考虑强度、耐磨性、耐腐蚀性和热处理工艺。
现有研究的不足与展望
列举了几个典型零件的选材和工艺路线分析案例,如轴类、齿轮类、箱体类等,通过实例说明了选材和工艺路线分析的实际应用和效果。
典型零件选材与工艺路线实例
总结了选材时应考虑的主要因素,包括材料的机械性能、工艺性能、经济性以及环境影响等。强调了选材时需权衡各种因素,以达到最佳的综合效果。
选材原则
铜及铜合金
常用材料介绍
材料性能与零件性能的关系
材料性能直接影响零件的性能,如强度、刚度、耐磨性等。 材料的物理和化学性质对零件的工作环境和使用寿命有重要影响,如耐腐蚀性、导电性、热膨胀系数等。 材料的机械性能对零件的加工制造和装配也有重要影响,如可加工性、焊接性、切削性等。
工艺路线分析
#O2
#2022
04
根据确定的工序顺序和设备、工艺方法,制定详细的工艺流程和工艺标准,明确各工序的加工要求、检验标准等。
制定工艺流程和工艺标准
在实际生产过程中,根据实际情况对工艺路线进行优化和完善,提高生产效率和产品质量。
优化和完善工艺路线
工艺路线制定流程
工艺路线优化方法
通过分析和改进生产过程,减少非增值环节,如等待、搬运、检验等,提高生产效率和产品质量。
典型零件的选材及加工工艺路线分析讲解材料

轻量化
减轻材料重量,提高产品机动性,降低能源 消耗和排放。
环保化
发展可再生、可回收、可降解的材料,减少 对环境的污染。
智能化
研究具有自适应、自修复、自感应等功能的 智能材料。
新材料的研究与开发
碳纤维复合材料
具有高强度、轻质、耐高温等优点,广 泛应用于航空航天、汽车等领域。
高分子合成材料
具有优良的化学稳定性、绝缘性、耐 磨性等,在建筑、电子、化工等领域
03
材料的应用与发展趋势
材料的应用领域
01
航空航天
用于制造飞机、火箭等高强度、轻 质材料。
建筑领域
用于制造桥梁、高层建筑等高强度、 高耐久性材料。
03
02
汽车工业
用于制造发动机、变速器等耐磨、 耐高温材料。
电子产品
用于制造集成电路、晶体管等精密、 小型化材料。
04
材料的发展趋势
高性能化
提高材料的强度、硬度、耐高温等性能,以 满足更高要求的工业应用。
可加工性原则
材料应具有良好的可加工性, 以便于零件的制造和加工。
可维修性原则
材料应易于维修和更换,以提 高零件的使用寿命和降低维修 成本。
常用材料介绍
钢铁
钢铁是机械制造业中应用最广泛的材料之一,具 有高强度、良好的韧性和耐磨性。
铜及铜合金
铜及铜合金具有良好的导电性、导热性、耐腐蚀 性和加工性能,广泛应用于电气、电子、化工等 领域。
实例二:齿轮类零件的选材与加工工艺
灰铸铁
用于制造一般用途的齿轮,如减速器齿轮等。
球墨铸铁
用于制造高强度、高耐磨性的齿轮,如汽车变速毛坯准备
根据零件材料和尺寸要求,准备毛坯。
粗加工
- 1、下载文档前请自行甄别文档内容的完整性,平台不提供额外的编辑、内容补充、找答案等附加服务。
- 2、"仅部分预览"的文档,不可在线预览部分如存在完整性等问题,可反馈申请退款(可完整预览的文档不适用该条件!)。
- 3、如文档侵犯您的权益,请联系客服反馈,我们会尽快为您处理(人工客服工作时间:9:00-18:30)。
典型零件选材及工艺分析一,齿轮类机床、汽车、拖拉机中,速度的调节和功率的传递主要靠齿轮机床、汽车和拖拉机中是一种十分重要、使用量很大的零件。
齿轮工作时的一般受力情况如下:(1)齿部承受很大的交变弯曲应力;(2)换当、启动或啮合不均匀时承受击力;(3)齿面相互滚动、滑动、并承受接触压应力。
所以,齿轮的损坏形式主要是齿的折断和齿面的剥落及过度磨损。
据此,要求齿材料具有以下主要性能:(1)高的弯曲疲劳强度和接触疲劳强度;(2)齿面有高的硬度和耐磨性;(3)齿轮心部有足够高的强度和韧性。
此外,还要求有较好的热处理工艺性,如变形小,并要求变形有一定的规律等。
下面以机床和汽车、拖拉机两类齿轮为例进行分析。
(一)机床齿轮机床中的齿轮担负着传递动力、改变运动速度和运动方向的任务。
一般机床中的齿轮精度大部分是7级精度(GB179-83规定,精度分12级,用1、2、3、……12表示,数字愈大者,精度愈低)。
只是在他度传动机构中要求较高的精度。
机床齿轮的工作条件比起矿山机械、动力机械中的齿轮来说还属于运转平稳、负荷不大、条件较好的一类。
实践证明,一般机床齿轮选用中碳钢制造,并经高频感应热处理,所得到的硬度、耐磨性、强度及韧性能满足要求,而县市频淬火具有变形小、生产率高等优点。
下面以C616机床中齿轮为例加以分析。
1、高频淬火齿轮的工工艺线2、热处理工序的作用正火处理对锻造齿轮毛坯是必需的热处理工序,它可以使同批坯料具有相同的硬度,便于切削加工,并使组织均匀,消除锻造应力。
对于一般齿轮,正火处理也可作为高频淬火前的最后热处理工序。
调质处理可以使齿轮具有较高的综合机械性能,提高齿轮心部的强度和韧性,使齿轮能承受较大的弯曲应力和冲击力。
调质后的齿轮由于组织为回火索氏体,在淬火时变形更小。
高频淬火及低温回火是赋予齿轮表面性能的关键工序,通过高频淬火提高了齿轮表面硬度和耐磨性,并使齿轮表面有压应力存在而增强了抗疲劳破坏的能力。
为了消除淬火应力,高频淬火后应进行低温回火(或自行回火),这对防止研磨裂纹的产生和提高抗冲击能力极为有利。
3、齿轮高频淬火后的变形情况齿轮高频淬火后,其变形一般表现为内孔缩小,外径不变或减小。
齿轮外径与内径之比小于1.5时,内径略胀大;当齿轮有键槽时,内径向键槽方向胀大,形成椭圆形,齿间椭圆形,齿间亦稍有变形,齿形变化较小,一般表现为中间凹0.002~0.0005㎜。
这些微小的变形对生产影响不大,因为一般机床用的7级精度齿轮,淬火回火后,均要经过滚光和推孔才成为成品。
高频淬火齿轮通常用含碳量为0.40~0.50%的碳钢或低合金钢(40、45、40Cr、45Mn2、405MnB 等)制造。
批量生产时,一般要求精选含碳量以保证质量。
45钢限制在0.42~0.47%C,40Cr钢限制在0.37~0.42%C。
经高频淬火交低温回火后,淬硬层应为中碳回火马氏体,而心部则为毛坯热处理(正火或调质)后的组织。
(二)汽车、拖拉机齿轮汽车、拖拉机齿轮主要分装在变速箱和差速器中,在变速箱中,通过它来改变发动机、典轴和主轴齿轮的速比;在差速器中,通过齿轮来增加扭转力钜并调节左右两车轮的转速,通过齿轮将发动机的动力传到主动轮,驱汽车、拖拉机运行。
汽车、拖拉机齿轮的工作条件比机床齿轮要繁重得多,困此在耐磨性、疲劳强度、心部强度和冲击韧性等方面的要求均比机床齿轮为高。
实践证明,汽车、拖拉机齿轮选用渗碳钢制造并经渗碳热处理后使用是较为合合适。
下面以JN-150型载重汽车(载重量为8000㎏)变速箱中第二轴的二、三档齿轮(如图9-26所示)为例进行分析。
1、选用钢;汽车、拖拉机齿轮的生产特点是批量大、产量高,因此在选择用钢时,在满足机械性能的前提下,对工艺性必须给以足够的重视。
20CrMnTi 钢具有较高的机械性能,见第六章表6-4所示。
该钢在渗碳淬火低温回火后,表面硬度为HRC58~62,心部硬度为HRC30~45。
20CrMnTi 的工艺性能尚好。
锻造后一般以正火改善其切削加工性。
20CrMnTi 钢的热处理工艺性较好,有较好的淬透性。
由于合金元素钛的影响,对过热不敏感,故在渗碳后可直接降温淬火。
此外尚有渗碳速度较快,过渡层较均匀,渗碳淬火后变形小等优点,这对制造形状复杂、要求变形小的齿轮零件来说是十分有利的。
20CrMnTi 钢可制造截面在30㎜以下,承受高速中等载荷以及冲击、摩擦的重要零件,如齿轮、齿轮轴等各种渗碳零件。
当含碳量在上限时,也可用于制造截面在40㎜以下,模数大于10的20CrMnTi 齿轮等。
根据JN-150G 型载重汽车变速箱中第二轴的二、三档齿轮的规格和工作条件,选用20CrMnTi 钢制造是比较合适的。
2、二轴齿轮的工艺路线。
下料→锻造→正火→机械加工→渗碳、淬火及低温回火→喷丸→磨内孔及换档槽→装配3、热处理工序的作用;在第六章的“渗碳钢的热处理特点”实例中对此已有叙述,这里不再重复。
4、热处理技术条件和热处理工艺热处理技术条件:渗碳层表面含碳量:0.8~1.05%C;渗碳层厚度:0.8~1.3㎜;淬火后硬度:HRC≮59;回火后表面硬度:HRC58~64;回火后心部硬度:HRC33~48。
齿轮主要尺寸:齿数(Z)=32;模数(m)=5.5;-0.16-0.09 公法线长度(L)=74.88 +0.24 ;键宽 =10 +0.03 。
变形要求:齿部公法线摆动量小于0.055㎜;键宽的变形不超过0.005㎜;齿向的变形不超过0.017㎜。
热处理工艺:渗碳是在JT-75井式炉内进行。
渗碳温度为920~940℃,渗碳时间可查第五章表5-10,确定为5小,渗碳后预冷至840~860℃直接淬火(油冷),淬火后再经≤200℃低温回火。
二轴齿轮经渗碳、淬火及低温回火后得到的统计结果台下:表层含碳量不超过1.05% HRC62~63HRC40~430.02~0.04㎜0.05~0.1㎜0.05㎜表面硬度(回火后)心部硬度(回火后)公法线长度胀大内孔缩小键宽缩小根据上述变形规律,生产上进一步采用冷热加工配合的方法,使变形控制在要求的技条件范围之内。
除高频淬火齿轮与渗碳齿轮外,尚有碳氮共渗齿轮;根据受力情况和性能要求不同,齿轮还可采用中碳合金进行调质并经氮化处理后使用;以及采用铸铁、铸钢制造齿轮。
二、轴类在机床、汽车、拖拉机等制造工业中,轴类零件是另一类用量很大,且占有相当重要地位的结构件。
轴类零件的主要作用是支承传动零件并传递动和动力,它们在工作时受多种应力的作用,因此从选材角度看,材料应有较高的综合机械性能.局部承受摩擦的部位如车床主轴的花键、曲轴轴颈等处,要求有一定的硬度,以提高其抗磨损能力。
要求以综合机械性能为主的一类结构零件的选材,还需根据其应力状态和负荷种类考虑材料的淬透性和抗疲劳性能。
实践证明,受交变应力的轴类零件、连杆螺栓等结构件,其损环形式不少是由于疲劳裂纹引起的。
下面以车床主轴、汽车半轴、内燃机曲轴、镗杆、大型人字齿轮轴等典型零件为例进行分析。
(一)机床主轴在选选用机床主轴的材料和热处理工艺时,必须考虑以下几点:<1> 受力的大小。
不同类型的机床,工作条件有很大差别,如高速机床和精密机床主轴的工作条件与重型机床主轴的工作条件相比,无论在弯曲或扭转疲劳特性方面差别都很大。
<2> 轴承类型。
如在滑动轴承上工作时,轴颈需要有高的耐磨性。
<3> 主轴的形状及其可能引起的热处理缺陷。
结构形状复杂的主轴在热处理时易变形甚至于开裂,因此在选材上应给予重视。
主轴是机床中主要进零件之一,其质量好坏直接影响机床的精度和寿命。
因此必须根据主轴的工作条件和性能要求,选择用钢和制定合理的冷热加工工艺。
1、机床主轴的工作条件和性能要求C616-416车床主轴如图1-2所示。
该主轴的工作条件如下:①承受交变的弯曲应力与扭转应力,有时受到冲击载荷的作用;②主轴大端内锥孔和锥度外圆,经常与卡盘、顶针有相对摩擦;③花健部分经常有磕或相对滑动。
总之,该主轴是在滚动轴承中动转,承受中等负荷,转速中等,有装配精度要求,且受到一定的冲击力作用。
由此确定热处理技术条件如下:①整体调质后硬度应为HB200~230,金相组织为回火索氏体;②内锥孔和外圆锥面处硬度为HRC45~50,表面3~5㎜内金相组织为回火屈氏体和少量回火马氏体;③花键部分的硬度为HRC48~53,金相组同上。
2、选择用钢 C616车床属于中速、中负荷、在滚动轴承中工作的机床,因此选用45钢是可以的。
过去此主轴曾采用45钢经正火处理后使用;后来为了提高其强度和韧性,在粗车后又增加了调质工序。
而且调质状态的疲劳强度比正火为高,这对提高主轴抗疲劳性能也是很重要的。
表1-1为45钢正火和调质后的机械性能比较。
表1-1 45钢正火和调质后的机械性能热处理σb (MN/㎡σs (MN/㎡σ-1(MN/㎡调质 682 490 338正火 600 340 2603、主轴的工艺路线下料→锻造→正火→粗加工(外圆留余4~5㎜)→调质→半精车外圆(留余2.5~3.5㎜),钻中心孔,精车外圆(留余0.6~0.7㎜,锥孔留余0.6~0.7㎜,铣键槽→局部淬火(锥孔及外锥体)→车定刀槽,粗磨外圆(留余0.4~0.5㎜,滚→精磨。
4、热处理工序的作用正火处理是为了得到合适和硬度(HB170~230),以便于机械加工,同时改善锻造组织,为调质处理作准备。
调质处理是为了使主轴得到高的综合机械性能和疲劳强度。
调质后硬度后硬度为HB200~230,组织为回火索氏体。
为了更好的发挥调质效果,将调质安排在粗加工后进行。
内锥孔和外圆锥面部分经盐浴局部淬火和回火后得到所要求的硬度,以保证装配精度和不易磨损。
5、热处理工艺调质淬火时由于主轴各部分的直径不同,应注意谈天问题。
调质后的变形虽然可以通过校直来修正,但校直时的附加应力对主轴精加工后的尺寸稳定性是不利的。
为减小变形,应注意淬火操作方法。
可采取预冷淬火和控制水中冷水机却时间来减小变形。
花键部分可用高频淬火以减小变形和达到硬度要求。
经淬火后的内锥孔和外圆锥面部分需经260~300℃回火,花键部分需经240~260℃回火,以消除淬火应力并达到规定的硬度值。
也有用球墨铸铁制造机床主轴的,如某厂用球墨铸铁的主轴淬火后硬度为HRC52~58,且变形量比45钢为小.(二汽车半轴汽车半轴是驱动车轮转动的直接驱动件。
半轴材料与其工作条件有关,中型载重汽车目前选用40Cr 钢,而重型载汽车则选用性能更高的40CrMnMo 钢。
1、汽车半轴的工作条件和性能在求的半轴为例。
半轴的简图如图9-28所示。
汽车半轴是传递扭矩的一个重要部件。
汽车运行时,发动机输出的扭矩,经过多级以跃进型载重汽车(载重量为2500kg)铣花键→花键淬火变速和主动器传递给半轴,再由半轴传动车轮。