焊接变形原因分析及其防止措施
铁路机车铝合金制件焊接变形原因及控制预防
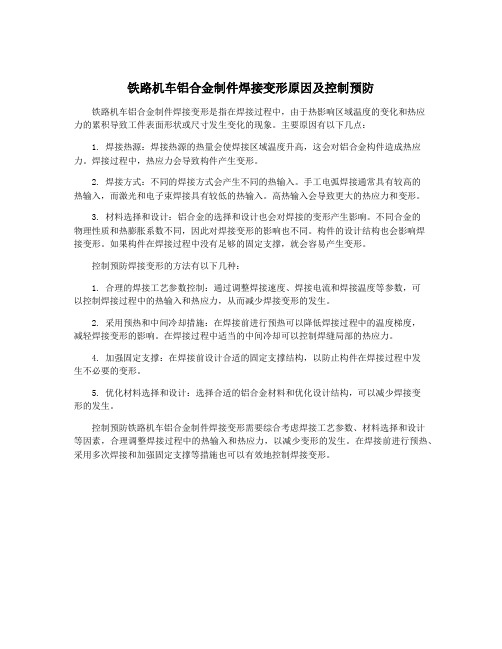
铁路机车铝合金制件焊接变形原因及控制预防铁路机车铝合金制件焊接变形是指在焊接过程中,由于热影响区域温度的变化和热应力的累积导致工件表面形状或尺寸发生变化的现象。
主要原因有以下几点:1. 焊接热源:焊接热源的热量会使焊接区域温度升高,这会对铝合金构件造成热应力。
焊接过程中,热应力会导致构件产生变形。
2. 焊接方式:不同的焊接方式会产生不同的热输入。
手工电弧焊接通常具有较高的热输入,而激光和电子束焊接具有较低的热输入。
高热输入会导致更大的热应力和变形。
3. 材料选择和设计:铝合金的选择和设计也会对焊接的变形产生影响。
不同合金的物理性质和热膨胀系数不同,因此对焊接变形的影响也不同。
构件的设计结构也会影响焊接变形。
如果构件在焊接过程中没有足够的固定支撑,就会容易产生变形。
控制预防焊接变形的方法有以下几种:1. 合理的焊接工艺参数控制:通过调整焊接速度、焊接电流和焊接温度等参数,可以控制焊接过程中的热输入和热应力,从而减少焊接变形的发生。
2. 采用预热和中间冷却措施:在焊接前进行预热可以降低焊接过程中的温度梯度,减轻焊接变形的影响。
在焊接过程中适当的中间冷却可以控制焊缝局部的热应力。
4. 加强固定支撑:在焊接前设计合适的固定支撑结构,以防止构件在焊接过程中发生不必要的变形。
5. 优化材料选择和设计:选择合适的铝合金材料和优化设计结构,可以减少焊接变形的发生。
控制预防铁路机车铝合金制件焊接变形需要综合考虑焊接工艺参数、材料选择和设计等因素,合理调整焊接过程中的热输入和热应力,以减少变形的发生。
在焊接前进行预热、采用多次焊接和加强固定支撑等措施也可以有效地控制焊接变形。
焊接应力及焊接变形预防措施

钢结构工程焊接应力与变形差生的危害及采取的措施随着“绿色建筑”理念的推广,以钢结构件为主体框架结构结合复合砌筑体结构已成为一种必然趋势,因为以钢结构为主的框架结构的回收利用性有效避免钢筋混凝土结构建筑垃圾的产生,具有可持续性。
由于钢结构工程的特有型,焊接作业时钢结构工程最重要的工序之一,而焊接应力及焊接变形产生是影响钢结构安全性及可靠性的重要因素。
本文着重对焊接应力及焊接变形的危害及所采取的对应措施进行分析。
一、焊接应力与变形产生机理焊接热输入引起材料不均匀局部加热,使焊缝区熔化,而熔池毗邻的高温区材料的热膨胀则受到周围材料的限制,产生不均匀的压缩塑性变形。
在冷却过程中,已发生压缩塑性变形的这部分材料又受到周围材料的制约,不能自由收缩,在不同程度上又被拉伸而卸载,与此同时,熔池凝固,金属冷却收缩也产生了相应的收缩拉应力和变形。
这种随焊接热过程而变化的内应力场和构件变形,称为瞬态应力与变形。
而焊后,在室温条件下,残留于构件中的内应力场和宏观变形称为焊接残余应力与焊接残余变形。
焊接残余应力和变形,严重影响焊接构件的承载力和构件的加工精度,应从设计、焊接工艺、焊接方法、装配工艺着手降低焊接残余应力和减小焊接残余变形。
二、焊接残余应力的危害及降低焊接应力的措施1.焊接残余应力的危害影响构件承受静载能力;影响结构脆性断裂;影响结构的疲劳强度;影响结构的刚度和稳定性;易产生应力腐蚀开裂;影响构件精度和尺寸的稳定性。
2.降低焊接应力的措施(1)设计措施尽量减少焊缝的数量和尺寸,在减小变形量的同时降低焊接应力;防止焊缝过于集中,从而避免焊接应力峰值叠加;要求较高的容器接管口,宜将插入式改为翻边式。
(2)工艺措施采用较小的焊接线能量,减小焊缝热塑变的范围,从而降低焊接应力;合理安排装配焊接顺序,使焊缝有自由收缩的余地,降低焊接中的残余应力;层间进行锤击,使焊缝得到延展,从而降低焊接应力;焊接高强钢时,选用塑性较好的焊条;预热拉伸补偿焊缝收缩(机械拉伸或加热拉伸);采用整体预热;降低焊缝中的含氢量及焊后进行消氢处理,减小氢致集中应力。
钢结构焊接变形的原因有哪些,钢结构焊接注意事项

钢结构焊接变形的原因有哪些,钢结构焊接注意事项钢结构连接普遍采用焊接,且对于一些重要焊缝一般都采用全熔透焊接。
金属焊接时在局部加热、熔化过程中,加热区的金属与周边的木材温度相差很大,产生焊接过程中的瞬时应力。
冷却至原始温度后,整个接头区焊缝及近缝区的拉应力区与母材在压应力区数值达到平衡,这就产生了结构本身的焊接残余应力。
此时,在焊接应力的作用下焊接件结构发生多种形式的变形。
残余应力的存在与变形的产生是相互转化的,认清变形规律,就不难从中找到防止减少和纠正变形的方法。
一、焊接变形的形式与原因:钢结构焊接后发生的变形大致可分为两种情况:即整体结构的变形和结构局部的变形。
整体结构的变形包括结构的纵向和横向缩短和弯曲(即翘曲)。
局部变形表现为凸弯、波浪形、角变形等多种。
1.1变形常见基本形式:常见钢结构焊接变形基本形式有如下几种:板材坡口对焊后产生的长度缩短(纵向收缩)和宽度变窄(横向收缩)的变形;板材坡口对接焊接后产生的角变形;焊后构件的角变形沿构件纵轴方向数值不同及构件翼缘与腹板的纵向收缩不一致形成的扭曲变形;薄板焊接后母材受压应力区由于失稳而使板面产生翘曲形成的波浪变形;由于焊缝的纵向和横向收缩相对于构件的中和轴不对称引起构件的整体弯曲,此种变形为弯曲变形。
这些变形都是基本的变形形式,各种复杂的结构变形都是这些基本变形的发展、转化和综合。
1.2焊接变形的原因:在焊接过程中对焊件进行了局部的、不均匀的加热是产生焊接应力及变形的原因。
焊接时焊缝和焊缝附近受热区的金属发生膨胀,由于四周较冷的金属阻止这种膨胀,在焊接区域内就发生压缩应力和塑性收缩变形,产生了不同程度的横向和纵向收缩。
由于这两个方向的收缩,造成了焊接结构的各种变形。
二、影响焊接结构变形的因素:影响焊接变形量的因素较多,有时同一因素对纵向变形、横向变形及角变形会有相反的影响。
全面分析各因素对各种变形的影响,掌握其影响规律是采取合理措施控制变形的基础。
预防焊接变形的措施

焊接变形是焊接过程中常见的问题,它会影响焊接件的尺寸精度和外观质量。
以下是一些预防焊接变形的措施:
1. 预留反变形量:在设计焊接结构时,可以根据焊接变形的趋势和大小,预留一定的反变形量。
这样在焊接过程中,即使产生了变形,也可以通过预留的反变形量来抵消,从而达到防止或减少焊接变形的目的。
2. 选择合适的焊接顺序:焊接顺序对焊接变形的影响很大。
一般来说,应先焊短焊缝,后焊长焊缝;先焊薄板,后焊厚板;先焊中心,后焊边缘。
3. 采用合理的焊接方法:不同的焊接方法对焊接变形的影响也不同。
例如,电弧焊的变形较小,而气焊和氩弧焊的变形较大。
因此,在选择焊接方法时,应尽量选择变形小的方法。
4. 控制焊接参数:焊接参数(如电流、电压、焊接速度等)对焊接变形的影响也很大。
一般来说,应选择较小的焊接电流和较快的焊接速度,以减少焊接热输入,从而减小焊接变形。
5. 采用预热和后热处理:预热可以减小焊接热输入,从而减小焊接变形;后热处理可以通过改变焊缝和母材的金相组织,来减小焊接变形。
6. 采用工装夹具:通过使用工装夹具,可以固定焊接件的位置和形状,防止焊接过程中的位移和变形。
7. 采用多点对称焊接:通过在焊接件的多个位置同时进行焊接,可以分散焊接应力,从而减小焊接变形。
以上就是预防焊接变形的一些措施,希望对你有所帮助。
薄板烧焊变形

薄板烧焊变形是指在薄板烧焊过程中,由于热应力和冷却收缩等因素的影响,导致焊接件发生形状变化的现象。
薄板烧焊变形的原因主要有以下几个方面:
1. 焊接热源引起的温度梯度:焊接热源会使焊接件局部升温,形成温度梯度。
高温区域会发生热膨胀,而低温区域则没有膨胀,导致焊接件发生形状变化。
2. 焊接过程中的热应力:焊接过程中,焊接件会受到热应力的作用,这是由于焊接件不同部位的温度不均匀所引起的。
热应力会使焊接件发生弯曲、扭曲等形变。
3. 焊接过程中的冷却收缩:焊接完毕后,焊接件会经历冷却过程,冷却收缩会使焊接件发生形状变化。
尤其是在焊接薄板时,由于薄板的厚度较小,冷却收缩会更加明显。
为了减少薄板烧焊变形,可以采取以下措施:
1. 控制焊接热源:合理选择焊接参数,控制焊接热源的大小和位置,尽量减小焊接件的温度梯度,降低热应力的产生。
2. 采用适当的焊接顺序:根据焊接件的形状和结构特点,合理安排焊接顺序,避免焊接过程中的热应力集中在某一部位,导致变形。
3. 使用预应力和支撑装置:在焊接过程中,可以利用预应力和支撑装置来平衡焊接件的应力,减小变形的发生。
4. 采用适当的焊接方法:根据实际情况选择合适的焊接方法,如采用
点焊、拍焊等,可以减小热影响区域,降低变形的程度。
综上所述,薄板烧焊变形是在薄板烧焊过程中不可避免的现象,但通过合理控制焊接参数和采取相应的措施,可以有效减小变形的程度。
焊接变形原因及预防措施资料

第二节
焊接变形
一、焊接变形的种类及其影响因素
焊接变形分为5种基本变形形式:收缩变形、 角变形、弯曲变形、波浪变形和扭曲变形。
焊接变形的基本形式
返回本章首页
1. 收缩变形 焊件尺寸比焊前缩短的现象称为收缩变形。
纵向和横向收缩变形 (1)纵向收缩变形 (2)横向收缩变形 2. 角变形 角变形产生的根本原因是由于焊缝的横向收 缩沿板厚分布不均匀所致。
焊接结构的不足之处大多反映在焊接接头 上的问题,主要有以下几方面:
1)焊接过程是一个不均匀的加热和冷却过程, 焊接结构必然存在焊接残余应力和变形,这不仅 影响焊接结构的外形尺寸和外观质量,同时给焊 后的继续加工带来很多麻烦,甚至直接影响焊接 结构的强度。 2)由于焊接接头要经历冶炼、凝固和热处理 三个阶段。 3)焊接会改变材料的部分性能。
只要允许,多采用型材、冲压件;焊缝 多且密集处,可以采用铸—焊联合结构, 就可以减少焊缝数量。此外,适当增加壁 板厚度,以减少肋板数量,或者采用压型 结构代替肋板结构,都对防止薄板结构的 变形有利。
(3)合理安排焊缝位置 梁、柱等焊接构件、常因焊缝偏心配置而产 生弯曲变形。
箱形结构的焊缝安排
合理安排焊缝位置防止变形 2. 工艺措施 (1) 留余量法 (2) 反变形法
1. 对结构强度的影响 2. 对焊件加工尺寸精度的影响
机械加工引起内应力释放和变形 3. 对受压杆件稳定性的影响
四、控制焊接残余应力的措施
1. 设计措施 1)尽量减少结构上焊缝的数量和焊缝尺寸。
2)避免焊缝过分集中,焊缝间应保持足够 的距离。
容器接管焊接 3)采用刚性较小的接头形式。
减小接头的刚性措施
平板对接焊时的反变形法 (3)刚性固定法 1) 将焊件固定在刚性平台上。
薄板焊接单侧加热变形原因
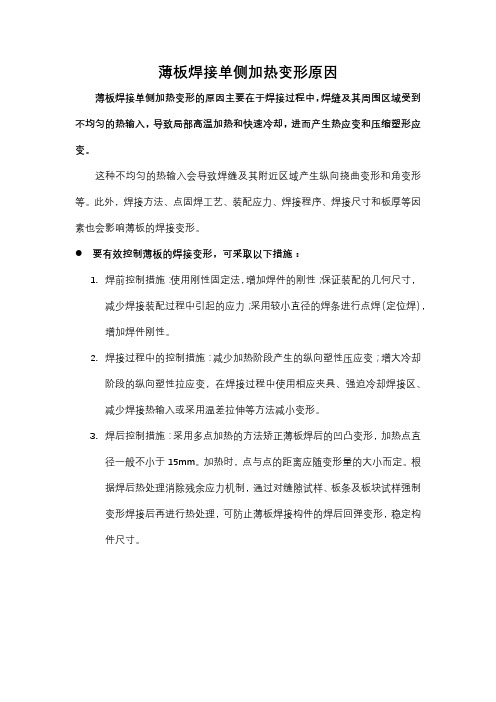
薄板焊接单侧加热变形原因
薄板焊接单侧加热变形的原因主要在于焊接过程中,焊缝及其周围区域受到不均匀的热输入,导致局部高温加热和快速冷却,进而产生热应变和压缩塑形应变。
这种不均匀的热输入会导致焊缝及其附近区域产生纵向挠曲变形和角变形等。
此外,焊接方法、点固焊工艺、装配应力、焊接程序、焊接尺寸和板厚等因素也会影响薄板的焊接变形。
要有效控制薄板的焊接变形,可采取以下措施:
1.焊前控制措施:使用刚性固定法,增加焊件的刚性;保证装配的几何尺寸,
减少焊接装配过程中引起的应力;采用较小直径的焊条进行点焊(定位焊),增加焊件刚性。
2.焊接过程中的控制措施:减少加热阶段产生的纵向塑性压应变;增大冷却
阶段的纵向塑性拉应变,在焊接过程中使用相应夹具、强迫冷却焊接区、减少焊接热输入或采用温差拉伸等方法减小变形。
3.焊后控制措施:采用多点加热的方法矫正薄板焊后的凹凸变形,加热点直
径一般不小于15mm。
加热时,点与点的距离应随变形量的大小而定。
根
据焊后热处理消除残余应力机制,通过对缝隙试样、板条及板块试样强制
变形焊接后再进行热处理,可防止薄板焊接构件的焊后回弹变形,稳定构
件尺寸。
简述焊接时防止金属变形的方法

简述焊接时防止金属变形的方法焊接过程中,由于高温引起的金属热膨胀和冷却后产生的收缩,很容易造成焊接件的变形。
焊接时防止金属变形的方法有以下几种:1.焊接预热:通过在焊接前将焊接部位预先加热到一定温度,可以减缓焊接引起的温度梯度变化,从而减少焊后的变形。
预热可以提高材料变形的动态可塑性,减缓应力集中和收缩速度。
2.焊接时控制冷却速度:焊接完毕后,适当控制焊件的快速冷却速度,可减小焊接残余应力,降低变形的发生。
这一技术被称为焊后热处理,可以通过空冷、水冷或盐浴冷却等方式进行。
3.适当选用正确的焊接序列:在焊接多个零件的情况下,应该选择合适的焊接顺序,以避免焊接引起的变形。
通常情况下,焊接应从内向外、从下向上进行,这样能够保持整体结构的稳定性,减小变形的可能性。
4.使用焊接夹具:焊接夹具能够提供稳定的工作支撑,阻止焊件在焊接过程中的自由变形。
通过使用夹具,可以保持焊件的几何形状,减少热应力的影响。
5.控制焊接速度和电流:焊接速度和电流的选择直接影响着焊接过程中产生的热输入量。
合理控制焊接速度和电流,使其适应材料的热导率和热膨胀系数,可以减小焊接引起的温度梯度变化,降低变形的风险。
6.使用焊接变形补偿技术:有时候,虽然无法完全避免焊接产生的变形,但可以通过采取相应的措施进行补偿。
这些措施包括刻意设置预弯、局部热处理、残余应力复合等,以达到减小、抵消变形的目的。
7.选择合适的焊接工艺:不同的金属材料和焊接工艺对变形的影响程度不同。
因此,在进行焊接之前,应仔细分析和评估待焊接材料的特性和焊接工艺的适用性,选择最合适的焊接工艺,以减小变形的风险。
8.控制焊接参数和热输入量:焊接参数和热输入量的控制可以直接影响焊接过程中的热影响区大小和局部应力状态。
合理选择焊接参数和热输入量,可以减少焊接过程中的温度梯度变化和残余应力,从而减小变形的可能性。
总之,焊接过程中的金属变形是无法完全避免的,但通过合理的预防措施和技术手段,可以最大程度地减小变形的发生。
- 1、下载文档前请自行甄别文档内容的完整性,平台不提供额外的编辑、内容补充、找答案等附加服务。
- 2、"仅部分预览"的文档,不可在线预览部分如存在完整性等问题,可反馈申请退款(可完整预览的文档不适用该条件!)。
- 3、如文档侵犯您的权益,请联系客服反馈,我们会尽快为您处理(人工客服工作时间:9:00-18:30)。
焊接变形原因分析及其防止措施
摘要:本文重点对常见焊接变形的原因进行分析,并根据原因分别从设计和工艺两个方面论述防止变形的措施。
关键词:焊接变形原因分析防止措施
随着新材料、新结构和新焊接工艺的不断发展,有越来越多的焊接应力变形和强度问题需要研究。
焊接变形在焊接结构生产中经常出现,如果构件上出现了变形,不但影响结构尺寸的准确性和外观美观,而且有可能降低结构的承载能力,引起事故。
同时校正焊接变形需要花费许多工时,有的变形很大,甚至无法校正,造成废品,给企业带来损失。
因此掌握焊接变形的规律和控制焊接变形具有十分重要的现实意义。
一、焊接变形种类
生产中常见的焊接变形主要有纵向收缩变形、横向收缩变形、挠曲变形、角变形、波浪变形、错边变形、螺旋变形。
这几种变形在焊接结构中往往并不是单独出现,而是同时出现,相互影响。
在这里重点对生产中经常出现的纵向收缩变形、横向收缩变形、角变形、错边变形进行分析。
二、焊接变形原因分析
1.纵向收缩变形。
焊接时,焊缝及其附近的金属由于在高温下自由变形受到阻碍,产生的压缩性变形,在平行于焊缝的变形称之为纵向收缩性变形。
焊缝纵向收缩变形量可近似的用塑性变形区面积S来衡量,变形区面积S于焊接线能量有直接关系,焊接线能量越小,S越小,反之S越大。
同样截面的焊缝可以一次焊成,也可以分几层焊成,多层焊每次所用的线能量比单层焊时小得多,因此每层焊缝产生的塑性变形区的面积S比单层焊时小,但多层焊所引起的总变形量并不等于各层焊缝的总和。
因为各层所产生的塑性变形区面积和是相互重叠的。
从上述分析可以看出多层焊所引起的纵向收缩比单层焊小,所以分的层数越多,每层所用的线能量就越小,变形也越小。
2.横向收缩变形。
横向收缩变形是指垂直于焊缝方向的变形,焊缝不但发生纵向收缩变形,同时也发生横向收缩变形,其变形产生的过程比较复杂,下面分几种焊缝情况来分析。
2.1堆焊和角焊缝。
首先研究在平板全长上对焊一条焊缝的情况。
当板很窄,可以把焊缝当作沿全长同时加热,采用分析纵向收缩的方法加以处理。
但在实际过程中,在焊缝长度上的加热并不是同时进行的,因此给焊缝长度各点的温度不一致。
在热源附近的金属热膨胀变形不但受到板厚深处、而且受到前后温度较低金属的限制和约束而承受压力,使其在宽度方向产生压缩塑性变形。
而在厚度上
增厚,焊后产生横向收缩变形。
横向变形的大小与焊接线能量Q=q/v和板厚有关。
随着q/v的提高,横向收缩量增加,随着板厚的增加,横向收缩量减少。
横向变形沿焊缝长度上的分布并不均匀,这是因为先焊焊缝的横向收缩对后焊的焊缝产生一个挤压作用,使后者产生更大的横向压缩变形。
这样焊缝的横向收缩沿着焊接方向是由小到大逐渐增长的,到一定长度后趋于稳定。
2.2对接接头焊缝。
以平板对接来分析,两块平板,中间留有一个间隙,在其上进行焊接,随着焊接热源的移动,平板被逐步加热膨胀,使焊接间隙减小。
我们知道单位厚度的焊接线能量q愈大,热膨胀愈大,间隙变化也愈大。
在冷却过程中,焊缝金属由于很快凝固,随后又恢复弹性,因此阻碍平板的焊接边收缩到原来的位置。
这样在冷却过程中就产生了横向收缩变形。
如果两板间没有间隙,则板的膨胀将引起板边的挤压,使之向厚度方向变形,在冷却后,产生的横向收缩比前一种情况有所降低。
3.角变形。
在堆焊、对接焊、搭接和丁字接头的焊接时,很容易产生角变形,这种变形发生的根本原因是横向收缩变形在厚度方向上的不均匀分布。
焊缝正面的变形大,背面的变形小,这样就造成平面的偏转。
3.1堆焊时角变形。
堆焊时,堆焊的高温区金属的热膨胀由于受到附近温度较低金属的阻碍而受到挤压,产生压缩塑性变形。
由于焊接面的温度高于背面,焊接面产生的压缩塑性变形比背面大,有时背面在弯矩的作用下甚至产生拉伸变形,导致焊缝冷却后平板产生角变形。
角变形的大小取决于压缩塑性变形的大小和分布情况,同时也取决于板的刚度。
3.2对接接头时角变形。
对接接头的坡口角度以及焊缝截面形状对于对接接头的角变形影响很大,坡口角度越大,焊接接头上部及下部横向收缩量的差别就越大。
可以用对称坡口X型代替Y型坡口,这样有利于减小角变形。
所以焊接角变形,不但与坡口形势和焊缝截面形状有关,而且还和焊接方式有关。
对于同样的板厚和坡口形式,多层焊比单层焊角变形大,焊接层数越多,角变形越大,多道焊比多层焊角变形大。
3.3角焊缝时角变形。
角焊缝对于丁字接头的焊缝最为明显,这里以丁字接头焊缝来分析。
丁字接头的角变形包括两个内容,筋板与主板的角度变化和主板本身的角变形。
前者相当于对接接头的角变形。
对于不开坡口的角焊缝来说,它的变形相当于坡口为90度时的对接焊缝的角变形,而对主板来说,它就相当于在平板上进行堆焊时引起的角变形。
这两种变形的综合结果,使丁字形接头两板间的角度发生变化,破坏了垂直度,也破坏了平板的平直度。
三、预防焊接变形的措施
从上面对焊接变形的原因进行了分析,知道焊接变形可以从设计和工艺两个方面来解决。
1.设计措施
1.1合理的选择焊缝的尺寸和形状。
焊缝尺寸直接关系到焊接工作量和焊接变形的大小。
焊缝尺寸大,不但焊接量大,而且焊接变形也大,因此在保证结构的承载能力的条件下,设计时应该尽量采用较小的焊缝尺寸。
1.2尽可能减少不必要的焊缝。
在焊接结构中应该力求减少焊缝数量,避免不必要的焊缝。
因为焊缝的增多,必然会增大焊接变形的可能性。
1.3合理地安排焊缝位置。
在设计时,安排焊缝时尽可能的对称于截面中性,或者使焊缝接近中性轴,这对减少梁、柱等一类结构的变形有良好的效果。
焊缝对称于中性轴,有可能使焊缝所引起的变形互相抵消,减少焊接变形。
2.工艺措施
2.1反变形法。
事先估计好结构变形的大小和方向,然后在装配时给于一个相反方向的变形与焊接变形相抵消,使焊后构件保持设计的要求。
例如为了防止对接接头的角变形可以预先将焊接坡口处垫高。
2.2刚性固定法。
这个方法是将构件加以固定起来限制焊接变形。
例如在焊接法兰盘时采用刚性固定法可以有效的减少法兰盘的角变形,使法兰盘面保持平直。
固定的方法可以采用直接点固,或紧压在平台上,或者两个法兰面背对背固定起来。
在焊接薄板时,在焊缝两侧用夹具紧压固定,固定的位置尽量接近焊缝。
2.3选择合理的装配焊接顺序。
例如大型贮油罐的焊接过程中,要合理的选择装配焊接顺序,才能避免焊接变形。
以罐底为例分析,将罐底分为两部分。
第一部分是和罐壁直接连接的边板。
第二部分是不与罐壁连接的中部板。
先把中部板焊成一体,焊接顺序是从中心向两端,先焊接短焊缝,使钢板连成长条,暂不与边板焊接。
然后再焊长条间的焊缝,次序也是由中心向外侧焊接。
焊完这部分后,先把边板与罐壁接触部分的焊缝焊好,再焊罐壁与边板之间的环焊缝,然后焊边板之间余下的焊缝,最后焊接边板与中部板之间的焊缝。
通过这样的焊接顺序,可以有效的防止焊接变形。
四、结束语
通过上述分析,只要我们在设计施工当中正确的应用工艺措施和设计措施来控制焊接变形,就会取得良好的效果。
这样不但保证了构件的结构尺寸,外形美观,而且能提高工作效率,降低生产成本。
参考文献
[1]《实用焊接技术手册》:2002年9月,河北科学技术出版社.
[2]《焊接手册》2001年7月机械工业出版社.
[3]《焊接技师手册、金属管道焊接工艺手册》2005年1月,机械工业出版社.
[4]《焊接原理》机械工业出版社.。