ANSYS优化设计_练习
ANSYS优化设计入门

ANSYS TRAININGANSYSANSYS TRAININGA. 设计优化?是一个创建优化设计的过程;?一个优化设计就是求解目标函数并且:a)满足所有特定的要求--应力水平 自震频率 最高温度等b)使总重量(或总体积, 成本, 或其他特定判据)最小。
例如 一个承受弯曲载荷的工字梁, 进行形状优化ANSYS TRAINING...设计优化粉末冶金齿轮*?齿轮在一定载荷下以最大应力不超过极限为约束条件 进行重量最小的优化。
?将实心齿轮变成多孔齿轮 使重量减低了27%。
*粉末冶金齿轮的设计优化, Orbison等著, ANSYS Conference Proceedings 1991, VolIIIANSYS TRAININGB.名词术语一个典型的设计优化问题由以下三部分组成1.一个要求极小或极大的项 即目标函数。
例如 ?总重量或体积(通常为极小)?热流率(通常为极大)ANSYS TRAINING...名词术语2. 为满足目标函数而要改变的设计特征即设计变量。
例如:?厚度?高度?圆角半径?屈服极限?孔数ANSYS TRAINING...名词术语3.设计必须满足的条件 即状态变量。
例如:–最大应力的限制–最大变形的限制–最低的一阶自震频率的限制–最高温度的限制–最大温度梯度的限制。
ANSYS TRAINING200 ft50 ft20 lb/in...名词术语例如, 考虑如下的优化问题:一个承受最大构件应力为10,000磅及最大变形为1英寸的连续跨构架桥的重量最轻。
可以改变构件的横截面积和桥的中跨跨高。
ANSYS TRAINING...名词术语?设计变量(DVs)为 –A1, A2, A3…为水平、垂直和对角构件的横截面积–H1, H2…为1/4和半跨的跨高H1H2A1A2A3?状态变量(SVs) 为–SMAX ≤10,000 psi…所有构件的最大应力–DMAX ≤1.0 in….所有接点处的最大变形?目标函数为总体积V最小H1ANSYS TRAINING...名词术语?一个设计现在可定义为给定一组DV值而创建的一个模型例如, 该构架桥的初始设计为一组定义:–A1 = 2.0 in2–A2 = 2.0–A3 = 2.0–H1 = 0.0 in–H2 = 0.0ANSYS TRAINING...名词术语?一个可行设计是落在所有DV 和SV 的限制范围内的设计。
如何用ansys进行优化设计
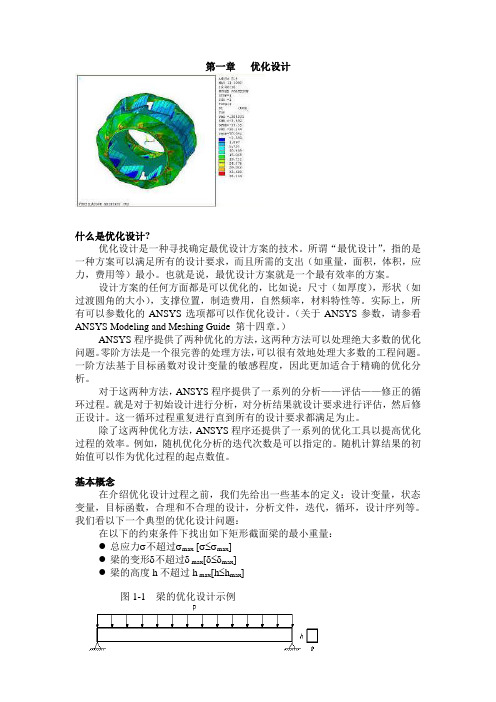
第一章优化设计什么是优化设计?优化设计是一种寻找确定最优设计方案的技术。
所谓“最优设计”,指的是一种方案可以满足所有的设计要求,而且所需的支出(如重量,面积,体积,应力,费用等)最小。
也就是说,最优设计方案就是一个最有效率的方案。
设计方案的任何方面都是可以优化的,比如说:尺寸(如厚度),形状(如过渡圆角的大小),支撑位置,制造费用,自然频率,材料特性等。
实际上,所有可以参数化的ANSYS选项都可以作优化设计。
(关于ANSYS参数,请参看ANSYS Modeling and Meshing Guide 第十四章。
)ANSYS程序提供了两种优化的方法,这两种方法可以处理绝大多数的优化问题。
零阶方法是一个很完善的处理方法,可以很有效地处理大多数的工程问题。
一阶方法基于目标函数对设计变量的敏感程度,因此更加适合于精确的优化分析。
对于这两种方法,ANSYS程序提供了一系列的分析——评估——修正的循环过程。
就是对于初始设计进行分析,对分析结果就设计要求进行评估,然后修正设计。
这一循环过程重复进行直到所有的设计要求都满足为止。
除了这两种优化方法,ANSYS程序还提供了一系列的优化工具以提高优化过程的效率。
例如,随机优化分析的迭代次数是可以指定的。
随机计算结果的初始值可以作为优化过程的起点数值。
基本概念在介绍优化设计过程之前,我们先给出一些基本的定义:设计变量,状态变量,目标函数,合理和不合理的设计,分析文件,迭代,循环,设计序列等。
我们看以下一个典型的优化设计问题:在以下的约束条件下找出如下矩形截面梁的最小重量:●总应力σ不超过σmax [σ≤σmax]●梁的变形δ不超过δ max[δ≤δmax]●梁的高度h不超过h max[h≤h max]图1-1 梁的优化设计示例设计变量(DVs)为自变量,优化结果的取得就是通过改变设计变量的数值来实现的。
每个设计变量都有上下限,它定义了设计变量的变化范围。
在以上的问题里,设计变量很显然为梁的宽度b和高度h。
ansysworkbench优化实例

作业1实验设计Design ExplorationTraining Manual 1•Goal目标–演示Design ExplorationDesign Exploration中进行DOE分析的流程,并且建立响应图;–边界条件如图所示Design Modeler ds_cutout–在Design Modeler中建立模型输入参数:ds_cutout –从中得到的几何参数Bearing load(轴承载荷)输出参数:Mass(质量)Equivalent stress(等效应力)Total deformation(整体变形)Training Manual12Parameter Set 检查所有1. File>Open>Link1.dsdb1. 双击Parameter Set ,检查所有输入和输出参数。
2输入参数输出参数3. 返回到项目中31Training Manual4. 双击“Response Surface”启动DOE分析45. 双击DOEDOE 大纲给出了输入和输出DOE参数51Training Manual6. 在Outline of Design of Experiments中点击选择参数67. 在特性中定义设计变量的类型和上下限。
Ds-cutout,4.5-5-5.5上的连续变量。
78. Bearing load(负载),9-10-1111 上的连续变量8Training Manual19. 选择DOE –默认的DOE 类型是中心组合设计(Central Composite Design )910. 查看和更新设计点1011. 点击Show Progress 展开状态栏11Training Manual1DOE 的表中的给出了9个设计点131312. 选择显示整体变形对应设计点的关系曲线12. 点击Design Points vs Parameter1Training Manual1414. 返回到项目页(ProjectPage)15. 双击ResponseSurface1516. 更新ResponseSurface17. 双击Response17 16Training Manual118. 选择二维模式,如图设置X ,Y 轴1819.选择三维模式,如图设置X ,Y 和Z 轴191Training Manual 20. 点击spider 和local sensitivities 显示图表20Training Manual121. 在响应面上点击鼠标右键选择Insert as Response Point ,将其插入到响应点22. 在需要的响应点上点击鼠标右键选择Insert as Design Point ,将其插入到设计点21其插到设计点22响应点不能和此处给出的一样!Training Manual123. 返回到Project Page2324. 双击Parameter set25. 更新所有设计点242526. 在DP1上点击鼠标右键选择Copy inputs to current 和Updated selected Design Point回到2627. 返回到Project Page271Training Manual28. 双击Solution28检查力学结果作业2What if分析多目标优化设计Training Manual•Goal (目标)–使用参数管理器探索如图所示结构的应力、质量和变形行为因为在垂直载荷的作用下几何参数是在发形行为,因为在垂直载荷的作用下,几何参数是在发生变化的。
基于ANSYS的结构优化设计方法

ωL 1
≤ω1
≤ωU1
( 12 )
因此 ,不但要对结构进行静力分析 ,还要进行模态分析
并判断其一阶固有频率是否满足式 ( 12) 。利用 ANSYS经过
44次迭代 ,得到较理想的结果 。优化过程如表 4所示 。
(下转第 150页 )
四川建筑 第 29 卷 3 期 200 9. 0 6
147
·工 程 结 构 ·
【关键词 】 结构优化 ; 桁架系统 ; 动力优化
【中图分类号 】 TU311. 41 【文献标识码 】 B
在钢结构工程中 ,钢材的用量是非常巨大的 ,这其中不 免会存在材料安全储备太高 ,过于浪费的情况 。如何在保证 结构安全的情况下 ,减少钢材用量 ,降低成本 ,这正是本文研 究的意义所在 。结构优化设计是在满足各种规范或某些特 定要求的条件下 ,使结构的某种指标 (如重量 、造价 、刚度或 频率等 )达到最佳的设计方法 。该方法最早应用在航空工程 中 ,随着计算机的快速发展 ,很快推广到机械 、土木 、水利等 工程领域 。它的出现使设计者从被动的分析 、校核进入主动 的设计 ,这是结构设计上的一次飞跃 [1 ] 。ANSYS作为大型 工程计算软件 ,其模拟分析功能非常强大 ,掌握并使用 AN2 SYS对结构进行模拟 、计算 、优化 ,对提高材料利用率 、减少 成本 ,是很有效的 。
265
341
466
306
59. 2 41. 9 26. 1 0. 01 0. 20 0. 29 0. 17 31. 6 262
264
341
464
296
59. 2 41. 9 26. 1 0. 01 0. 08 0. 28 0. 17 31. 6 262
264
ANSYS优化设计

(2)性能约束 又称性态约束,是由某种设计性能或指标推导出来的一种约束条件。属于这类设计
约束的如零件的工作应力、应变的限制;对震动频率、震幅的限制;对传动效率、温升、 噪声、输出扭矩波动最大值等的限制;对运动学参数如位移、速度、转速、加速度的限 制等。这类约束条件,一般可以根据设计规范中的设计公式或通过物理学和力学的基本 分析导出的约束函数来表示。如例7-2中,悬臂梁设计弯曲强度条件(0.1d3 )<=[б],扭转 强度条件(0.2d³)<=[τ] ,刚度条件3 /(3)<=[ƒ]。已知 [б] = 1002 ,[τ] =752 ,[ƒ]=0.17.03*104 ²,可导出性能约束条件为:
根据前述分析,例7-2的优化设计问题可建立如下数学模型: (X) X = [d, l]T F(X) =πd2 4 20>=0 100>=0 50>=0 150>=0 d31000>=0 d3-6666.6>=0 d43-9.65>=0
可见,这是一个二维的约束非线性规划问题。可求得优化结果: 50 36.84 目标函数即用料53296.5073。
(X) (x12,…)
(7-3)
目标函数与设计变量之间的关系可以用几何图形形象地表示出来。例如,单变量时, 目标函数是二维平面上的一条曲线(图7.2a);双变量时,目标函数是三维空间的一个 曲面(图7.2b)。曲面上具有相同目标函数值的点构成了曲线,该曲线称为等值线(或 等高线)。如 图7.2b所示,在等值线a上的所有点,其目标函数值均为15,在等值线c 上的各点(设计点),目标函数值均为25等等。将其投影到设计空间是一族近似的共 心椭圆,他们共同的中心点就是最优点(图7.2b 中的P点)。因此形象地说,优化设计 就是近似地求出这些共心椭圆的中心。若有n个设计变量时,目标函数是1维空间中的超 曲面,难于用平面图形表示。
利用ANSYS软件进行动臂(四连杆)优化设计

三.利用ANSYS软件进行动臂(四连杆)优化设计3.1有限元模型建立装载机整机的有限元模型是主要是针对力作用的直接部件进行的,主要包括装载机机身上的转台、主要工作部件铲斗、带动铲斗动作的动臂、动力件油缸、以及运动件连杆和摇臂组成。
在实际建模过程中,通常要求设定材料的性能参数与母材相同,这样做的原因是要对各构件的焊接接头进行连续处理,更为重要的一点是为了在后续精力分析中可以有一个光顺的网格划分,在进行有限元模型的建立中,为了更快捷的进行后续计算,以不至于施加于计算机太多计算负荷,将其中不影响结果数据的螺纹孔、倒角等结构进行了移除。
组件几何模型如图3.1所示。
图3.1 工作装置几何模型根据实际情况定义相应材料的性能,包括:弹性模量e = 2.06×106pa,泊松比μ= 0.3,密度ρ= 7850kg / m3。
每个部件均由solid186单元模拟,接头处的销轴由beam188单元模拟,联接单元由销轴与轴套之间的运动关系模拟,而液压缸则由连杆单元模拟。
通过设置诸如截面积,弹性模量和密度之类的参数来实现对实际液压缸的仿真。
要求将元素尺寸控制在15mm〜20mm之内,并在销轴上局部细化网格,这可以提高计算精度。
最后,为了以危险的姿势获得工作装置的整个有限元模型,需要组装每个部件的有限元模型。
有限元模型包括266783个单元,其中包括266638个实体单元,142个梁单元,3个杆单元和444467个节点。
最后,如果装载机转盘需要完全约束,则应采用边界条件。
通过上述过程计算得出的切向和法向挖掘阻力将作为有限元模型中的外部载荷应用于铲斗尖端,如3.2所示。
图3.2 工作装置有限元模型及边界载荷3.2工作装置静强度分析结果据了解,装载机的材料为 q460c 钢,屈服极限为[ ]=235×106 Pa。
结果表明,工作装置的最大应力为802mpa,该应力发生在提升臂的上吊耳的铰孔和铲斗杆的油缸,远远超过了材料的屈服极限。
ANSYS Fluent流体仿真设计快速优化方法

综合识别最有影响力的设计参数。 指定的外形变化将会如何改变性能?
Sensitivity to Body Forces
优化 稳健仿真
使用梯度数据对性能进行系统地改进。
数值方法及格式对网格节点位置的敏 感性。
Sensitivity to Mass Sources
Adjoint Solver的基本理念
• 传统的流体求解器
Adjoint Solver案例:二维导向叶片设计
• 降低整个系统的压降 P
原始设计 132
P = -232.8Pa 预期变化 10.0Pa 实际变化 9.0Pa P = -223.8Pa 预期变化 8.9Pa
实际变化 6.9Pa P = -216.9Pa 预期变化 7.0Pa 实际变化 3.1 P = -213.8
• 优化后的管路,易发生汽蚀处的最低静压值增大了18%,整个管路 系统的压降减少了24%
Adjoint Solver案例:增大散热片的换热能力
• 通过改变散热片的形状,增大其换热能力。
Adiabatic wall
Inflow
Specified fin temperature
Sensitivity to thermal sources
Adjoint Solver的工作流程
优化过的设计
优化
局部最优 ••••1••••100--什设结设手是是单36 么计计果动否否目x因参如是0还有有标x素数何什1是设指还x2影在改么自计定是x?x3响哪变约的动多x4儿?5束运性目优?能动?标化???
CFD分析
qi
Adjoint
c j
Solver
分析伴随求解器的结果
总计降低8%的压降
Adjoint Solver案例:U型管减阻设计
运用ANSYSWorkbench快速优化设计

运用ANSYS Workbench快速优化设计SolidWorks是一个优秀的、应用广泛的3D设计软件,尤其在大装配体方面使用了独特的技术来优化系统性能。
本文给出几种改善SolidWorks装配体性能的方法,在相同的系统条件下,能够进步软件的可操纵性,进而进步设计效率。
众所周知,大多数3D设计软件在使用过程中都会出现这样的情况,随着装配零件数目和复杂度增加,软件对系统资源的需求就相对增加,系统的可操纵性就会下降。
造成这种状况的原因有两种:一是计算机系统硬件配置不足,二是没有公道使用装配技术。
本文对这两种情况进行分析并提出相应的解决方案。
一、计算机系统配置不足的解决方案SolidWorks使用过程中,计算机硬件配置不足是导致系统性能下降的直接原因,其中CPU、内存、显卡的影响最大。
假如计算机系统内存不足,Windows就自动启用虚拟内存,由于虚拟内?*挥谟才蹋?斐上低衬诖嬗胗才唐捣苯换皇?荩?贾孪低承阅芗本缦陆担籆 PU性能过低时,延长运算时间,导致系统响应时间过长;显卡性能不佳时引起视图更新慢,移动模型时出现停顿现象,并导致CPU占用率增加。
运行SolidWorks的计算机推荐以下配置方案:CPU:奔腾Ⅱ以上内存:小零件或装配体(少于300个特征或少于1000个零件),内存最少为512M;大零件或装配体(大于1000个特征或2500个零件),内存需要1G或更多;虚拟内存一般设为物理内存的2倍。
显卡:支持OpenGL的独立显卡(避免采用集成显卡),显存最好大于64M。
对于现有的计算机,使用以下方法分析系统瓶颈,有针对性地升级计算机。
(1)在SolidWorks使用过程中启动Windows任务治理器,在性能页,假如CPU的占用率经常在100%,那么系统瓶颈就在CPU或显卡,建议升级CPU或显卡;假如系统内存大部分被占用,虚拟内存使用量又很大,操纵过程中硬盘灯频繁闪烁,这说明系统瓶颈在内存,建议扩大内存。
- 1、下载文档前请自行甄别文档内容的完整性,平台不提供额外的编辑、内容补充、找答案等附加服务。
- 2、"仅部分预览"的文档,不可在线预览部分如存在完整性等问题,可反馈申请退款(可完整预览的文档不适用该条件!)。
- 3、如文档侵犯您的权益,请联系客服反馈,我们会尽快为您处理(人工客服工作时间:9:00-18:30)。
• NPT = 10 • X,Y,Z = hub_ro+xmid, ymid, 0
• [OK] 5. 将活动坐标系转到全局柱坐标系。这将允许我们创建一个样条曲线并指定 qhub and qrim.为其端部斜率: – Utility Menu > WorkPlane > Change Active CS to > Global Cylindrical
练习 附录
目
1. 介绍性练习 旅行费用最小化 2. 参数化模型 A. 轴对称转盘 B. 六角钢盘
录
3.
设计优化 A. 轴对称转盘 B. 六角钢盘
搜寻设计域 六角钢盘 优化设计 II A. 带肋托盘 B. 风铃 健壮设计 一个励磁器的因素分析 拓朴优化 A. 六角钢盘 B. 拱桥 附录 用健壮设计达到世界级质量 用ANSYS程序将工程质量设计到产品中去
– (Design Opt >) -Design Sets- List… • 选择 Best Set,然后 [OK] – (Design Opt >) -Design Sets- List…
• 选择 ALL Sets,然后 [OK]
W-6
1. 介绍性练习 旅行费用最小化
12. 画出速度对旅行费用曲线: – (Design Opt >) -Design Sets- Graphs/Tables…
E = 30e6 psi r = 7.2e-4 lb-s2/in4 n = 0.3
1.6 qhub xmid ymid qrim
0.5
4.0R
0.6 10.0R
0.4
W-9
2A. 参数化建模 轴对称转盘 指导
1. 进入 ANSYS (或清数据库)并改变 jobname为 rotdisk: – Utility Menu > File > Change Jobname… • 现在 jobname = rotdisk • [OK] 2. 在输入窗内或在标量参数对话框中键入如下的参数定义 (Utility Menu > Parameters > Scalar Parameters…): • pi=3.142 • hub_ri=4 • hub_w=0.6
• rpm=7500 • w=2*pi*rpm/60
• [Close] – (Solution >) Apply > Other > Angular Velocity…
• OMEGY = w • [OK]
13. 现在我们已准备好可以求解。 – Toolbar > [SAVE_DB] – Solution > -Solve- Current LS • 检查状态信息,关闭 “/STAT Command” 窗 • [OK]
W-1
4. 5.
6. 7.
8.
1. 介绍性练习
旅行费用最小化
描述 • 求最优旅行速度,使50-英里的旅程费用最小。 假定旅行者的时间值 10.00美元/小时, 每英里汽油费与速度的平方成反比 (50,000/速度2), 而 汽油费为1.079美元/加仑。该旅行用不超过一小时的时间。 让我们重申本命题:最小化函数 cost = (旅行时间*10)+(50/每英里汽油)*1.079 约束条件 旅行时间 1.0 给定: 旅行时间 = 50/speed 每英里汽油 = 50000/speed**2
•
W-2
1. 介绍性练习 旅行费用最小化
指导
1. 用系统编辑器 (Notepad 或 vi),在你的导师指定的目录下再现(或创建)文件 trip.dat 。文件中应包括如下的参数定义: – speed=100 – triptime=50/speed – mpg=50000/speed**2
– tripcost=(triptime*10)+(50/mpg)*1.079
• • • •
输入 WP X = hub_ri 输入 WP Y = 0 Width = hub_w Height = hub_ht
• [Apply] • WP X = rim_ri • 输入 WP Y = 0 • Width = rim_w
• Height = rim_ht
• [OK]
W-12
2A. 参数化建模 轴对称转盘
2. 3. 进入你的导师指定的 ANSYS 工作目录。 改变作业名( jobname)为 trip: – Utility Menu > File > Change Jobname… • 现在 jobname = trip • 最小化
4. 由文件 trip.dat 中读入: – Utility Menu > File > Read Input from… • 选择 trip.dat,然后 [OK] 进入设计优化程序 (OPT) 并指定分析文件: – Main Menu > Design Opt > -Analysis File- Assign... • 选择 trip.dat,然后 [OK] 定义速度作为设计变量: – (Design Opt >) Design Variables… • [Add…] – 选择 SPEED,然后 – Min = 1 – Max = 100 – TOLER = .001 – [OK] • [Close]
• 点选模型底部三线,然后 [OK]
W-19
2A. 参数化建模 轴对称转盘
12. 加 7500 rpm的角速度载荷。ANSYS 期望弧度/秒,所以先要计算所用参数值。 – Utility Menu > Parameters > Scalar Parameters... type the following:
W-17
2A. 参数化建模 轴对称转盘
10. 指定带预应力作用的静态分析。预应力使后续的预应力模态分析成为可能。 – Main Menu > Solution > New Analysis...
• 选 Static,然后 [OK].
– (Solution >) Analysis Options... • Equation solver = Precondition CG • Tolerance/level = 1e-5
– (Preprocessor >) Create > -Areas- Arbitrary > Through KPs
• 以反时针方向点选中间面四角上的关键点,然后按 OK。 – Toolbar > [SAVE_DB]
W-15
2A. 参数化建模 轴对称转盘
8. 下一步是模型分网,从定义单元类型和材料属性开始。 – Preprocessor > Element Type > Add/Edit/Delete…
W-13
2A. 参数化建模 轴对称转盘
6. 过 KP 10 并以指定的端部斜率创建一样条曲线: – (Preprocessor >) Create > Splines > With Options > Spline thru KPs
• 按自左至右的顺序点选三关键点: – 轮毂右上部KP , KP10,轮缘左上部的KP
• rim_ht=0.5 • thetahub=90
• thetarim=90 • xmid=(rim_ri-hub_ro)/2 • ymid=(hub_ht+rim_ht)/2
W-11
2A. 参数化建模 轴对称转盘
3. 为轮毂和轮缘创建矩形: – Main Menu > Preprocessor > Create > Rectangle > By 2 Corners
hub_ht qhub xmid ymid rim_ht
qrim
• hub_ro=hub_ri+hub_w
• hub_ht=1.6 • rim_ro=10 • rim_w=0.4
hub_ri hub_ro
hub_w
rim_ri rim_ro
rim_w
W-10
2A. 参数化建模 轴对称转盘
2. (续) • rim_ri=rim_ro-rim_w
2A. 参数化建模 轴对称转盘
15. 下一步是将结果送入参数。我们需要最大冯密塞斯应力(将称之为 SMAX),而冯 密塞斯应力的标准差 (称为SDEV)。 首先求 SMAX:
• XVAROPT = SPEED • NVAR = TRIPCOST
• [OK]
W-7
1. 介绍性练习 旅行费用最小化
13. 退出ANSYS: – Toolbar > QUIT
• 选择 Quit - No Save!,然后 [OK]
W-8
2A. 参数化建模
轴对称转盘
描述 • • • 建立一个参数化,如图所示的高速转盘轴对称模型 ,用 thetahub, thetarim, xmid, 和 ymid 作为参数,所有其他尺寸是固定的。 加载: 角速度相当于 15,000 rpm. 材料特性:
W-16
2A. 参数化建模 轴对称转盘
9. 模型分网: – Preprocessor > MeshTool
• 激活 Smart Size • 设定 smart size 为 3
• [Mesh],,然后在Mesh Areas对话框中点 [Pick All] • [Close] – Utility Menu > Plot > Elements – Toolbar > [SAVE_DB]
5.
6.