铸铁件边冒口设计
冒口设计参考
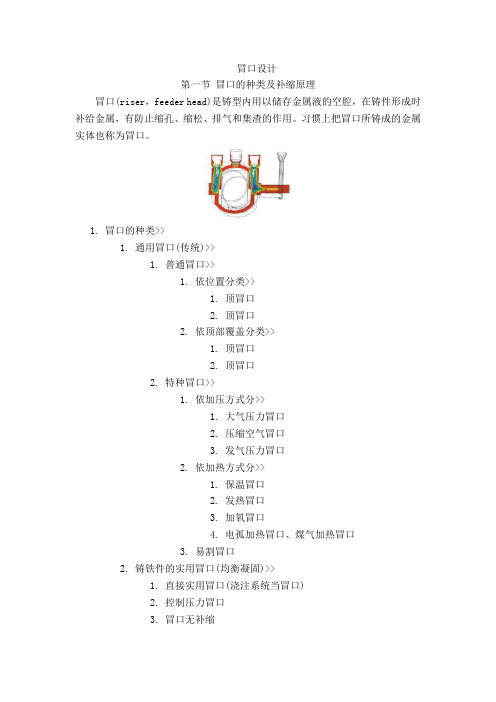
冒口设计第一节冒口的种类及补缩原理冒口(riser,feeder head)是铸型内用以储存金属液的空腔,在铸件形成时补给金属,有防止缩孔、缩松、排气和集渣的作用。
习惯上把冒口所铸成的金属实体也称为冒口。
1.冒口的种类>>1.通用冒口(传统)>>1.普通冒口>>1.依位置分类>>1.顶冒口2.顶冒口2.依顶部覆盖分类>>1.顶冒口2.顶冒口2.特种冒口>>1.依加压方式分>>1.大气压力冒口2.压缩空气冒口3.发气压力冒口2.依加热方式分>>1.保温冒口2.发热冒口3.加氧冒口4.电孤加热冒口、煤气加热冒口3.易割冒口2.铸铁件的实用冒口(均衡凝固)>>1.直接实用冒口(浇注系统当冒口)2.控制压力冒口3.冒口无补缩2.冒口形状冒口的形状有圆柱形、球顶圆柱形、长(腰)圆柱形、球形及扁球形等多种3.通用冒口补缩原理>>1.基本条件>>1.冒口凝固时间大于或等于铸件(被补缩部分)的凝固时间2.有足够的金属液补充铸件的液态收缩和凝固收缩,补偿浇注后型腔扩大的体积3.在凝固期间,冒口和被补缩部位之间存在补缩通道,扩张角向着冒口2.选择冒口位置的原则>>1.冒口应就近设在铸件热节(hotspot)的上方或侧旁2.冒口应尽量设在铸件最高、最厚的部位。
对低处的热节增设补贴或使用冷铁,造成补缩的有利条件3.冒口不应设在铸件重要的、受力大的部位,以防组织粗大降低强度4.冒口位置不要选在铸造应力集中处,应注意减轻对铸件的收缩阻碍,以免引起裂纹5.尽量用一个冒口同时补缩几个热节或铸件6.冒口布置在加工面上,可节约铸件精整工时,零件外观好7.不同高度上的冒口,应用冷铁使各个冒口的补缩范围隔开3.冒口有效补缩距离的确定>>冒口的有效补缩距离为冒口作用区与末端区长度之和,它是确定冒口数目的依据,与铸件结构、合金成分及凝固特性、冷却条件、对铸件质量要求的高低等多种因素有关,简称为冒口补缩距离1.铸钢件冒口的补缩距离有色合金的冒口补缩距离外冷铁的影响补贴(padding)的应用第二节铸钢件冒口的设计与计算铸钢件冒口属于通用冒口,其计算原理适用于实行顺序凝固的一切合金铸件。
可锻铸铁件冒口设计

可锻铸铁件冒口设计铸铁是一种常用的材料,广泛应用于制造行业。
在铸铁制品的生产中,冒口设计是至关重要的,它直接影响到产品质量和加工成本。
正确的冒口设计可以有效地避免缺陷的产生,提高产品的成形质量,同时也可以降低后续加工的难度和成本。
本文将介绍可锻铸铁件冒口设计的相关知识,并提出一种合理的冒口设计方案。
一、可锻铸铁件的特点可锻铸铁是一种含碳量较高的铸铁材料,其强度和硬度较高,具有较好的可锻性,适用于锻造和精密加工。
可锻铸铁件通常用于制造汽车零部件、机械零件等需要高强度和耐磨性的工件。
由于可锻铸铁的成分和性能特点,其在铸造过程中对冒口设计有着特殊的要求。
二、冒口设计原则1.冒口位置:冒口应设置在可锻铸铁件的最高点,以便将浮渣和气泡排除。
通常情况下,冒口位置应位于铸件的上部,离毛口处一定距离。
2.冒口形状:冒口应设计成易于开启和清理的形状,避免产生断口和裂纹。
常见的冒口形状有圆形、方形和椭圆形等,根据铸件的形状和结构来选择合适的冒口形状。
3.冒口尺寸:冒口的尺寸应根据铸件的大小和结构来确定,通常情况下,冒口的面积越大,排气和排渣效果越好。
但是也要避免过大的冒口导致浪费材料和增加加工成本。
4.冒口数量:根据可锻铸铁件的结构和复杂程度,确定冒口的数量和位置。
通常情况下,大型和复杂结构的铸件需要设置多个冒口,以确保浇注材料充分进入铸型腔。
5.冒口连接:冒口应与铸件的毛口连接,以确保铸注产物的完整性和一致性。
冒口的连接处应设计成光滑和密封的结构,避免产生漏料和漏底等问题。
三、可锻铸铁件冒口设计方案针对可锻铸铁件的特点和冒口设计原则,提出一种合理的冒口设计方案:1. 冒口位置:冒口设置在铸件的最高点,离毛口处约5-10mm,以便排气和排渣。
冒口位置应经过精确计算和模拟,确保冒口的位置准确无误。
2.冒口形状:冒口设计为圆形或椭圆形,便于开启和清理。
冒口的形状应光滑和密封,减少产生断口和裂纹的可能性。
3.冒口尺寸:根据铸件的大小和结构确定冒口的尺寸,通常情况下,冒口的直径或长宽比应为1:3-1:5、冒口尺寸的选择应考虑到浇注材料的流动性和铸件的充实度。
铸铁件冒口设计手册

铸铁件冒口设计手册诸葛胜福士科铸造材料(中国)有限公司铸铁冒口设计手册一、概述冒口是一个个储存金属液的空腔。
其主要作用是在铸件成形过程中提供由于体积变化所需要补偿的金属液,以防止在铸件中出现的收缩类型缺陷(如图1和图2所示),而这些需要补偿的体积变化可能有:图1 各种缩孔图2 缩孔生产图a)和冒口的补缩图b)1—一次缩孔 2—二次缩孔 3—缩松 1—缩孔 2—型腔胀大 3—铸件(虚线以内) 4—显微缩松 5—缩陷(缩凹,外缩孔)(1)铸型的胀大(2)金属的液态收缩(3)金属的凝固收缩补偿这些体积变化所需要的金属液量随着铸型和金属种类的不同而异。
此外,冒口还有排气及浮渣和非金属夹杂物的作用。
铸件制成后,冒口部分(残留在铸件上的凸块)将从铸件上除去。
由此,在保证铸件质量要求的前提下,冒口应尽可能的小些,以节省金属液,提高铸件成品率。
由此冒口的补缩效率越高,冒口将越小,铸件成品率越高、越经济。
FOSECO公司的发热保温冒口具有高达35%的补缩效率;因而,具有极高的成品率和极其优越的经济性。
在金属炉料价格飞涨的情况下,其优越性显得尤其突出。
另外,高品质发热保温冒口,及其稳定可靠的产品质量是获得高品质铸件的重要手段和可靠的质量保证。
二、铸铁的特点铸钢和铸铁都是铁碳合金,它们在凝固收缩过程中有共同之处)如凝固前期均析出初生奥氏体树枝晶,都存在着液态、凝固态和固态下的收缩),但也有不同的特点。
其根本不同之处是铸铁在凝固后期有“奥氏体+石墨”的共晶转变,析出石墨而发生体积膨胀,从而可部分地或全部抵消凝固前期所发生的体积收缩,即,具备有“自补缩的能力”。
因此在铸型刚性足够大时,铸铁件可以不设冒口或采用较小的冒口进行补缩。
灰铸铁在共晶转变过程中析出石墨,并在与枝晶间的液体直接接触的尖端优先长大,其石墨长大时所产生的体积膨胀直接作用在晶间液体上,进行“自补缩”。
对于一般低牌号的灰铁铸件,因碳硅含量高,石墨化比较完全,其体积膨胀量足以补偿凝固时的体收缩,故不需要设置冒口,只放排气口。
厚大灰铸铁件上小冒口的研究及应用

4 - , 7艺出品率大幅提高 ,旧 7艺 2 -
◇
工艺 简单, 操作上也几乎没有什么难度。 凝固。
3 小冒口工艺设计要点 . 2
1 ̄6 而 有利于铁液平稳充型,而且 由于内浇道 中冒 口重量 占铸件重量的 2% 2%,
件产生缩松、 缩孔的缺陷。 毋s 。掘下表所示 4 . 冒口的使用不仅节约大量的 3小
扰所抵消, 而造成 冒口根部的缩于 、 从 u缩 注系 统各 蛆元 尺 寸 比例 如 下 f 位 单 松缺陷。
mm)
当量, 加强其石 墨化 膨胀 的作用。 4 铸件质量检测
Байду номын сангаас
直浇道截面 :7 00
数量 1 个
41采 用小 冒 口工 艺生产铸件 , 经 质量检验 , 其结果是 冒口根部的缩孔、 缩
重量及补缩距离在铸件上设置相应的几 个大明冒口。 图二所示。 如 用这种方法生 产铸件工艺布置复杂 , 难度大 . 操作 冒口 去除困难 , 出品率低 , 时冒口的重 工艺 有
量超过铸件重量 的 4%,并且在 冒口根 0
铸铁 件的收缩值 除和浇 注湿度、 化 断面灰铸铁件采 用了有限补缩的方法 ,
维普资讯
D婪 袭 点
厚大灰铸 铁件 上小 冒 口的研 究及应用
岳世琦 兰扑石油化工机器总厂铸铁 分厂 705) 、 3 0 0
3厚断面灰铸铁件有 限补缩的实践 . 所谓有限补缩 ,是 指在铸件上设 置
一
个小 冒I J以补充铸件 在 均衡凝固 阶
1 . 铸铁件的收缩特点
’的拉环 、 屯 冲模系列工装件。 此类铸件特 点是壁厚均匀 , 形状简单 , 属典型的灰铸
铁厚太件。 31 铸造工艺 .
球墨铸铁浇冒口系统设计的关键 (一)

球磨铸铁浇冒口设计的关键第一部分浇流道系统设计1.0浇流道系统设计1.1要求快速浇铸:使充型过程中温度损失最小使冶金学性能衰减最小使氧化物最少清洁浇铸:避免浇铸过程中产生炉渣(浮渣)设计的经济性:使铸件产量最大化1.2关键组成:所示的所有组成部分要求炉渣缺陷最小化1.3规划考虑设计基本设计:优化对铸件的空间利用;冒口设计方法的选择;设置分型面以最小化对模芯的需求;铸件设置在上模中;平稳填充;简单对称的设计系统;同一铸件使用相同的浇冒口;可能的话,在多个铸件上使用一个冒口;在分型面上给浇冒口系统留下足够的空间;具体设计如下:1.4阻流阀的作用定义:阻流阀是浇道系统中一块横截面积,它决定充型时间有两个正确的位置设置阻流阀,因此有两个基本的浇道系统:在简单的浇注系统中,1)阻流阀位于流道和浇口的连接处。
2)阻流阀位于直浇道与横浇道的连接处。
1.5 选择浇流系统类型在浇口-横浇道系统中,铸件分别被一个或多个阻流阀或浇口阻挡。
在直浇道-横浇道系统中,很可能几个铸件共用一个阻流阀。
使用直浇道-横浇道系统在一个模具里生产大量小型件,这是不切实际的对每个铸件分别设置阻流阀(阻流阀尺寸非常小),极大的依赖于模具技术及浇注温度大部分情况下是使用浇口-横浇道系统浇口-横浇道系统与直浇道-横浇道系统特点的结合形成混合系统。
这通常用在要求运输铁水到复杂的铸件型腔的流道系统中。
1.6摩擦并非直浇道顶部所有铁水的潜能都可以转换为铸造型腔中的机械能随着铁水与型腔内壁的撞击和铁水之间的撞击,一些潜能损失在摩擦上由于摩擦造成的损失,延长了模型填充时间,必须考虑何时计算阻流阀截面积和浇铸时间。
选择fr,摩擦损失因子,作为能量损失的估计值对于薄壁平板:fr—0.2对于厚重立方体:fr---0.81.7浇铸时间尽可能快的符合人们的能力及生产例程推荐的浇注时间:非常近似的指导,铸件质量+冒口质量1.8阻流阀的横截面积对总的浇铸质量选择最快的实际浇铸时间(t,sec.)选择合适的fr值确定总的浇铸体积/阻气阀(V)V是所有铸件及冒口,特定阻流阀的下游之和体积=质量/密度液态铸铁,密度=0.25磅/立方英尺或0.007KG/cm3Determine effective ferrostatic head in sprue (H.)确定铸件在上模中的高度(b.)根据Torricelli,铁水在阻流阀的流速当铸件完全处在下模,当铸件完全位于上模,当铸件位于上模和下模中,可以从下面的图谱中,选择合适的Ac图谱数据基于平均上模高度(依铸造不同而变化)。
铸铁件冒口定量设计课件

(4)横浇道模数 Mh
Mh=f横.f2.Mc
f横=0.75~0.85 f2 ——收缩模数系数 Mc ——铸件模数 根据横浇道模数Mh,求出横浇道尺寸
10 浇注系统充填与补缩一体化设计
(1)充填设计(保证浇注时间,大流量,平稳 洁净,有合理的流态,可控的流动路径)
(2)补缩设计(足够的补缩时间和补缩量) (3)取二者较大者,再核算 (4)给出二者都满足的尺寸
(5)内浇道模数Mn
Mn=f内f2.f4Mc f内=0.35~0.40 f2 ——收缩模数系数 f4 ——冒口颈长度系数 f4=0.8~1.0 Mc ——铸件模数 根据内浇道模数Mn,求出内浇道尺寸
11 铸铁件冒口系列
12 结论
(1)冒口位置不要放在铸件的几何热节上; (2)冒口颈 短、 厚、 宽。 (3)铸铁件收缩时间分数,流通效应系数对
提高中国铸件在国际市场上 的竞争力
谢谢
Qm= G Mc3
3 铸铁件均衡凝固冒口设计方法
(1)收缩模数计算法(3f法) (2)查表法 (3)分段比例查表法
4 收缩模数计算法(3 f法)
(1)冒口体模数MR MR=f1f2f3Mc
f1 ——冒口平衡系数 f2 ——收缩模数系数 f3 ——冒口压力系数 Mc ——铸件模数
取f1=1.2 f2=√P f3=1.1~1.3
冒口,冒口颈大小的影响显著。 (4)无冒口铸造的本质是浇注系统当冒口。
均衡凝固技术1988年获 国家科技进步二等奖
1989年国家科委成都均衡凝固推广班
谢谢
联系方式 地址:710048 西安理工大学608信箱
《铸造技术》杂志 电话/传真: 即时联系: Email:
附件
提高铸造企业工艺水平和 铸件品质
铸造工艺学冒口设计
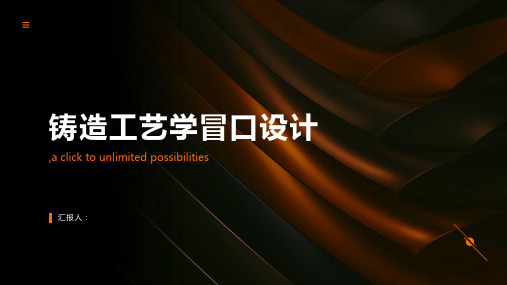
铸造工艺学是一门 研究金属材料成型 规律和工艺方法的 科学
铸造工艺学涉及到 金属材料的性能、 组织结构、成分和 加工方法等方面
铸造工艺学是机械 制造领域中重要的 分支之一
铸造工艺学在汽车 、航空航天、能源 等领域有着广泛的 应用
铸造工艺学的研究对象和内容
添加标题
研究对象:铸造工艺学是研究铸造生产过程及其相关技术的一门学科,包括铸造材料、铸造设备、铸造工 艺等方面的内容。
置,以获得最佳补缩效果
注意浇注温度对冒口的影响
浇注温度过低可能导致冒口 补缩不足,产生缩孔、缩松 等缺陷
合适的浇注温度需要根据合 金种类、铸件结构、浇注系
统等因素固,影响补缩效果
在实际生产中,可以通过调 整浇注温度来优化冒口设计,
提高铸件质量
注意浇注时间对冒口的影响
优化冒口位置: 将冒口设置在 铸件的非重要 部位或应力集 中区域,以减 少后续加工或 修复工作量。
考虑环保因素: 选择环保型冒 口材料,减少 废弃物对环境 的影响,降低
处理成本。
05 冒口设计的具体方法
确定冒口的位置
确定冒口的位置:根据铸件的结构和尺寸,选择合适的冒口位置,以保证铸件的质量和生产效 率。
球墨铸铁材质的冒口设计实例
材质特性:球墨铸 铁具有高强度、高 韧性、耐磨性等特 点
冒口设计原则:根 据铸造工艺要求, 确定冒口的位置、 大小和形状
实例分析:以某实 际生产中的球墨铸 铁零件为例,详细 介绍冒口的设计过 程和优化方案
效果评估:通过对 比分析,阐述优化 后的冒口设计对提 高铸件质量、降低 废品率等方面的作 用
添加 标题
壁厚对冒口尺寸的影响:壁厚越大,需要的 冒口体积也越大,以补偿铸件凝固过程中的 收缩。
熔模铸件冒口当量热节设计法

熔模铸件冒口当量热节设计法熔模铸件的冒口是指连接熔化金属与铸件之间的通道,其作用是让金属在冷却过程中有足够的时间与铸型材料交换热量,以防止铸件出现缩孔、气孔等缺陷。
当然,冒口还可以作为铸件的入口,使金属液顺利流入铸型中。
因此,冒口设计的好坏对铸件的成形质量起着至关重要的作用。
熔模铸件冒口当量热节设计法是一种常用的冒口设计方法,其核心思想是建立一个等效的热节模型,通过计算这个模型的最小截面积来确定冒口的设计尺寸。
具体步骤如下:
1. 确定铸件的凝固收缩量和引起收缩的金属液量。
2. 根据铸件的几何形状和大小,确定冒口底部的面积。
3. 假设冒口底部的面积上方的金属液在冷却过程中达到了和凝固铸件相同的温度,建立等效热节模型。
4. 根据等效热节模型计算出最小截面积,即为合理的冒口设计尺寸。
5. 检查冒口的位置和形状是否合适,需满足金属液能够顺利流入铸型而不引起攻角、涡流等不良现象。
总之,熔模铸件冒口当量热节设计法是一种基于热力学原理的设计方法,可以有效避免因冒口设计不当而导致的铸件缺陷问题。