脱磷转炉吹炼各阶段碳
转炉炼钢过程脱磷和吹氧模型的研究
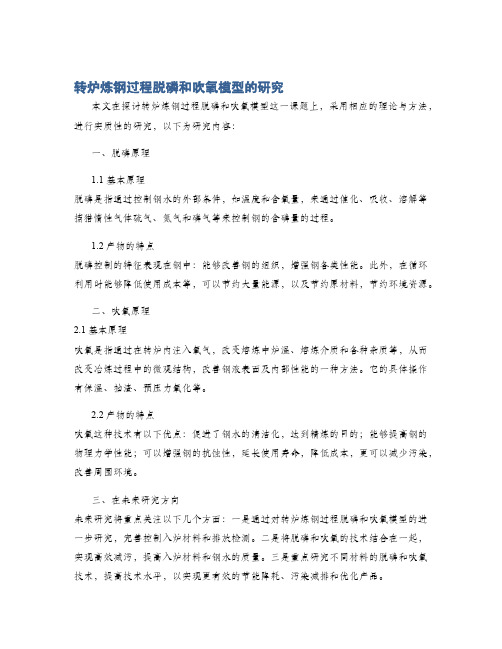
转炉炼钢过程脱磷和吹氧模型的研究
本文在探讨转炉炼钢过程脱磷和吹氧模型这一课题上,采用相应的理论与方法,进行实质性的研究,以下为研究内容:
一、脱磷原理
1.1 基本原理
脱磷是指通过控制钢水的外部条件,如温度和含氧量,来通过催化、吸收、溶解等捕猎惰性气体硫气、氮气和磷气等来控制钢的含磷量的过程。
1.2产物的特点
脱磷控制的特征表现在钢中:能够改善钢的组织,增强钢各类性能。
此外,在循环利用时能够降低使用成本等,可以节约大量能源,以及节约原材料,节约环境资源。
二、吹氧原理
2.1基本原理
吹氧是指通过在转炉内注入氧气,改变熔炼中炉温、熔炼介质和各种杂质等,从而改变冶炼过程中的微观结构,改善钢液表面及内部性能的一种方法。
它的具体操作有保温、抽渣、预压力氧化等。
2.2产物的特点
吹氧这种技术有以下优点:促进了钢水的清洁化,达到精炼的目的;能够提高钢的物理力学性能;可以增强钢的抗蚀性,延长使用寿命,降低成本,更可以减少污染,改善周围环境。
三、在未来研究方向
未来研究将重点关注以下几个方面:一是通过对转炉炼钢过程脱磷和吹氧模型的进一步研究,完善控制入炉材料和排放检测。
二是将脱磷和吹氧的技术结合在一起,实现高效减污,提高入炉材料和钢水的质量。
三是重点研究不同材料的脱磷和吹氧技术,提高技术水平,以实现更有效的节能降耗、污染减排和优化产品。
转炉炼钢流程中的脱磷工艺
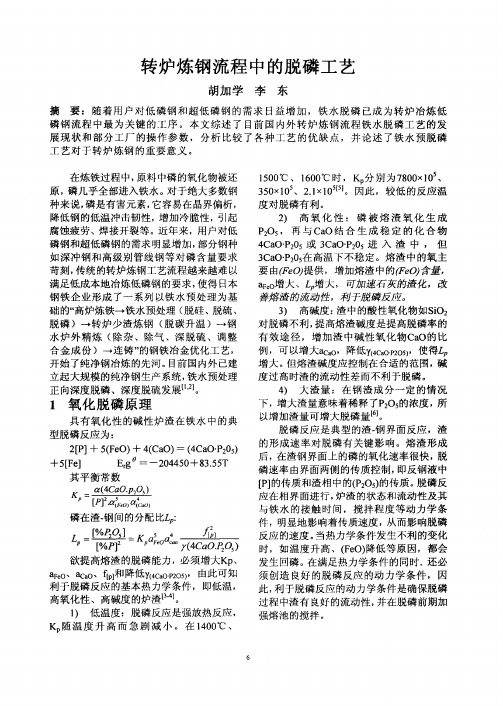
磷 在渣. %P
:
a ̄
7 C . ・ y4 a Q ) ( OP 0 2
欲提 高熔 渣 的脱磷 能力 ,必须增 大K 、 p ae、aa、f]口 F 0 co t 降低1 C .O) 由止 可 失 p , P 5 ( O2 , 4 匕 l J 利 于脱磷 反应 的基 本热 力学 条件 , 即低温 , 高 氧化 性 、高碱度 的炉 渣 【 3 。 1 低温 度 :脱磷 反应 是强 放热 反应 , ) KD 温 度 升 高 而 急 剧 减 小 。 在 10  ̄ 随 4 0C、
3 高碱 度 : 中的酸 性氧化 物如 SO2 ) 渣 i 对脱 磷 不利 , 高熔渣 碱 度是 提 高脱磷 率 的 提 有 效 途 径 ,增 加 渣 中 碱 性氧 化物 C O的 比 a 例 ,可 以增大 a ,降低 丫CO 25 co (a.o) 4 P ,使得三 p 增 大 。 熔渣碱 度 应控 制在 合适 的范 围 , 但 碱 度过 高 时渣 的流 动性差 而 不利 于脱磷 。 4 大 渣 量 :在 钢渣 成 分 一 定 的情 况 ) 下 ,增 大渣 量意 味着稀 释 了P05 2 的浓度 , 所 以增 加渣 量 可增 大脱磷 量 【。 o J 脱 磷 反应 是 典型 的渣 界 面 反应 ,渣 钢 的形 成 速 率对 脱 磷 有 关 键影 响 。熔 渣 形成 后 ,在渣 钢 界面上 的磷 的氧 化速 率很 快 , 脱 磷速 率 由界 面两侧 的传 质控 制 , 即反钢 液 中 【] P 的传 质 和渣相 中 的(2 ) Po5的传质 。 磷反 脱 应 在相 界面 进 行 , 炉渣 的状 态和 流动 性及其 与 铁 水 的接触 时 间 ,搅 拌程 度 等 动 力 学条 件 ,明显地 影响着 传质 速度 , 从而 影 响脱磷 反应 的速度 。 当热 力学条 件 发生 不利 的变化 时 ,如温 度升 高 、(e ) F O 降低 等原 因,都会 发 生 回磷 。在满足 热力 学条 件 的 同时 . 还必 须 创 造 良好 的脱 磷 反 应 的动 力 学 条 件 , 因 此 , 于脱 磷 反应 的动力 学 条件 是确 保脱磷 利 过 程 中渣 有 良好 的流 动性 , 并在 脱磷 前期加 强熔 池 的搅 拌 。
转炉连续脱磷脱碳工艺的开发2001-7-31

分类号:B J84世界金属导报/2001年/07月/31日/第006版/转炉连续脱磷脱碳工艺的开发廖建国1.前言随着对洁净钢需求量的扩大,以铁水预处理为基础的多段组合精炼得到迅速发展。
但是,在使用铁水罐车或铁水包作预处理容器的情况下,由于必须在低温下进行脱磷脱碳精炼,因此存在着转炉热浴度不足、废钢添加量受限制等实质性问题。
另外,在使用转炉进行预处理时,虽然可以提高转炉的热浴度,但必须同时使用两座转炉作为脱磷炉和脱碳炉。
新日铁公司开发了一种能用一座转炉进快速脱磷脱碳的新的精炼工艺(M U R C:M u l t i-R e f i n i n g C o n v e r t e r)。
本文就M U R C法的概况和8t试验转炉的实验结果进行介绍。
2.M U R C法的概况M U R C法就是在同一座炉子中对铁水同时进行连续脱S i、脱P处理和脱碳处理的工艺,其中包括了在处理过程中倾动炉子进行中间扒渣的工序。
由于预先装入废钢,因此M U R C法能在高氧化性气氛下进行操作,而且由于是在同一座转炉中进行处理,因此能保持转炉的热浴度。
另外,利用转炉的强搅拌和高速吹氧的特性,在高氧位势下对低碱度渣进行快速脱磷精炼的同时,由于将脱碳渣全部留在炉内就装入下一炉的铁水,因而可有效地用于脱磷精炼,由此能实现石灰单耗最低的精炼,大幅度减少炉渣的产生量。
3.实验方法使用8t试验转炉进行实验。
先在每t铁水中装入0~180k g的废钢,然后装入用别的感应熔化炉熔化的铁水5~7t。
先用氧枪进行顶吹氧,并加入规定的废钢进行脱硅、脱磷处理,然后倾动炉子,从炉口扒出炉渣,将炉子竖直后再进行顶底吹氧,经脱碳精炼后出钢。
在对脱碳炉渣进行热循环操作的情况下,可将炉渣全部剩留在炉内就装入下一炉铁水。
脱硅脱磷处理时的顶吹氧流量以1000N m~3/h为标准,还有部分以400N m ~3/h和1500N m~3/h为标准进行实验。
底吹气体只使用N_2,其流量标准分别为200N m~3/h和350N m~3/h。
炼钢工艺流程图
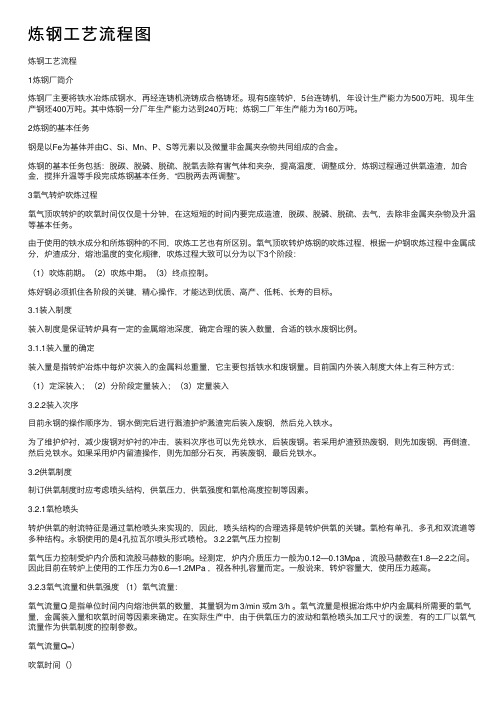
炼钢⼯艺流程图炼钢⼯艺流程1炼钢⼚简介炼钢⼚主要将铁⽔冶炼成钢⽔,再经连铸机浇铸成合格铸坯。
现有5座转炉,5台连铸机,年设计⽣产能⼒为500万吨,现年⽣产钢坯400万吨。
其中炼钢⼀分⼚年⽣产能⼒达到240万吨;炼钢⼆⼚年⽣产能⼒为160万吨。
2炼钢的基本任务钢是以Fe为基体并由C、Si、Mn、P、S等元素以及微量⾮⾦属夹杂物共同组成的合⾦。
炼钢的基本任务包括:脱碳、脱磷、脱硫、脱氧去除有害⽓体和夹杂,提⾼温度,调整成分,炼钢过程通过供氧造渣,加合⾦,搅拌升温等⼿段完成炼钢基本任务,“四脱两去两调整”。
3氧⽓转炉吹炼过程氧⽓顶吹转炉的吹氧时间仅仅是⼗分钟,在这短短的时间内要完成造渣,脱碳、脱磷、脱硫、去⽓,去除⾮⾦属夹杂物及升温等基本任务。
由于使⽤的铁⽔成分和所炼钢种的不同,吹炼⼯艺也有所区别。
氧⽓顶吹转炉炼钢的吹炼过程,根据⼀炉钢吹炼过程中⾦属成分,炉渣成分,熔池温度的变化规律,吹炼过程⼤致可以分为以下3个阶段:(1)吹炼前期。
(2)吹炼中期。
(3)终点控制。
炼好钢必须抓住各阶段的关键,精⼼操作,才能达到优质、⾼产、低耗、长寿的⽬标。
3.1装⼊制度装⼊制度是保证转炉具有⼀定的⾦属熔池深度,确定合理的装⼊数量,合适的铁⽔废钢⽐例。
3.1.1装⼊量的确定装⼊量是指转炉冶炼中每炉次装⼊的⾦属料总重量,它主要包括铁⽔和废钢量。
⽬前国内外装⼊制度⼤体上有三种⽅式:(1)定深装⼊;(2)分阶段定量装⼊;(3)定量装⼊3.2.2装⼊次序⽬前永钢的操作顺序为,钢⽔倒完后进⾏溅渣护炉溅渣完后装⼊废钢,然后兑⼊铁⽔。
为了维护炉衬,减少废钢对炉衬的冲击,装料次序也可以先兑铁⽔,后装废钢。
若采⽤炉渣预热废钢,则先加废钢,再倒渣,然后兑铁⽔。
如果采⽤炉内留渣操作,则先加部分⽯灰,再装废钢,最后兑铁⽔。
3.2供氧制度制订供氧制度时应考虑喷头结构,供氧压⼒,供氧强度和氧枪⾼度控制等因素。
3.2.1氧枪喷头转炉供氧的射流特征是通过氧枪喷头来实现的,因此,喷头结构的合理选择是转炉供氧的关键。
转炉脱磷、造渣工艺

是中期是碳剧烈氧化期,不能变化太快,抑制脱碳反应
突然温度降低,防止喷溅。据上所述,碳的大量氧化,
低磷,在因钢为坯中复的杂偏零析件度要很求大,钢而板在很α和高γ的固塑溶体性内。的IF扩钢散速度 却[很P小]<,0使.0它15不%容易均匀化。因此,按照用途不同对钢中磷含
量有严格要求:
东大冶金
1. 脱P反应
1. 脱P反应
.cn , 110004
2[P]+5[O]= P2O5 2[P]+5(FeO)=(P2O5)+5Fe 3(FeO)+(P2O5)=(3FeO·P2O5) (聚磷酸铁)
EMTI
Shenyang NEU Metallurgical Technology Corporation Limited
技术精益求精 · 创新永无止境
转炉脱磷、造渣工艺
沈阳东大冶金科技股份有限公司
东大冶金110004
磷在钢中以[Fe2P]形式存在,也可以用[P]表示。磷虽然能
前期渣中的(FeO)含量对脱磷反应的进行有重要 作用,这是因为:
12
东大冶金
3. 氧气转炉各期脱磷
.cn , 110004
影响前期脱磷的主要因素是碱度。而高的(FeO)含量 只是一个不可缺少的条件——也是在操作上前期快速成渣 的手段。换言之,就是控制喷枪,使(FeO)在10~15%左 右。炉渣前期 碱度为1.5左右,碱度提高更有利于脱磷,但 因前期温度低,客观上不可能造成高碱度炉渣。并且在此 (FeO)含量范围,碱度在0.82~1.5范围内,炉渣具有较低 的粘度,而碱度高于1.5时,粘度值随碱度增加而快速提 高,炉渣流动性显著变差,不利于脱磷。总之,通常必须 根据铁水条件把前期渣碱度控制在1.5左右;而(FeO) 在10~15%左右或更高些。
转炉炼钢工艺简介
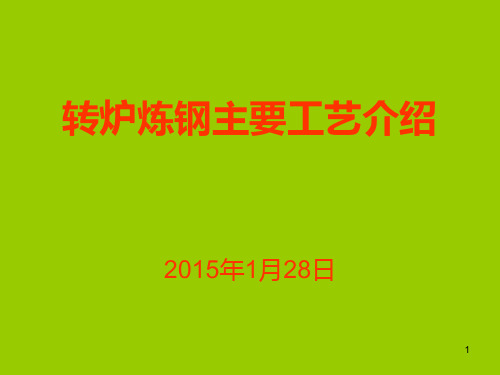
18
萤石作用及要求
• 作用
造渣加入萤石可以加速石 灰的溶解,萤石的助熔作 用是在很短的时间内能够 改善炉渣的流动性,但过 多的萤石用量,会加剧炉 衬的损坏,并污染环境。
• 质量要求 • CaF2≥75%, SiO2≤23%,S≤0.20%, P≤0.08%,H2O≤3.0% • 粒度:5-60mm
渣量=(石灰+镁球或熟白)×(2-3)
8
铁水成分及温度影响
• Mn的影响 • 锰是弱发热元素,铁水中Mn氧化后形成的(MnO)可促 进石灰溶解,加快成渣;减少氧枪粘钢,终点钢中余 锰高,能够减少合金用量,利于提高金属收得率;锰 在降低钢水硫含量和硫的危害方面起到有利作用。 Mn/Si的比值为0.8~1.00时对转炉的冶炼操作控制最 为有利。当前使用较多的为低锰铁水,一般铁水中 [Mn]=0.20%~0.40%。
6.设备少,投资节省。
4
炉顶料仓 振动给料器 电子称 带式运输机 密封料仓 传动机构 实 心 轴
汽包 氧 枪 风 机 不 回 收 时 放 空 回收煤气 进入煤气柜
烟 道
文氏管 脱水器
溜 槽
洗 涤 塔
沉淀池
电动机 渣 罐 转 炉 吸 滤 池
水封逆止阀 送往高炉利用
支架Hale Waihona Puke 氧气顶吹转炉工艺流程示意图
5
二 、转炉炼钢用主要原材料
28
2.1装料制度:废钢量的确定
• 热量来源于:
• 转炉炼钢不需要外来热源;
铁水物理热及元素氧化化学热。 铁水及废钢的合理配比须根据炉子的热平衡计算确定。 • 硅的作用 优点:因发热量大,增大废钢加入量,一般铁水中Si增 加0.1%,废钢比增大1%。 缺点:增大渣量,侵蚀炉衬一般控制在0.3-0.5%。
吹炼过程中的脱磷和脱硫
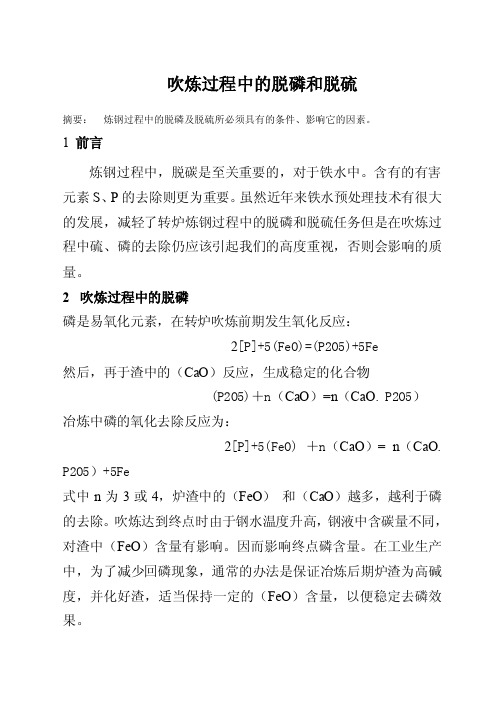
吹炼过程中的脱磷和脱硫摘要:炼钢过程中的脱磷及脱硫所必须具有的条件、影响它的因素。
1前言炼钢过程中,脱碳是至关重要的,对于铁水中。
含有的有害元素S、P的去除则更为重要。
虽然近年来铁水预处理技术有很大的发展,减轻了转炉炼钢过程中的脱磷和脱硫任务但是在吹炼过程中硫、磷的去除仍应该引起我们的高度重视,否则会影响的质量。
2吹炼过程中的脱磷磷是易氧化元素,在转炉吹炼前期发生氧化反应:2[P]+5(FeO)=(P2O5)+5Fe然后,再于渣中的(CaO)反应,生成稳定的化合物(P2O5)+n(CaO)=n(CaO. P2O5)冶炼中磷的氧化去除反应为:2[P]+5(FeO) +n(CaO)= n(CaO. P2O5)+5Fe式中n为3或4,炉渣中的(FeO)和(CaO)越多,越利于磷的去除。
吹炼达到终点时由于钢水温度升高,钢液中含碳量不同,对渣中(FeO)含量有影响。
因而影响终点磷含量。
在工业生产中,为了减少回磷现象,通常的办法是保证冶炼后期炉渣为高碱度,并化好渣,适当保持一定的(FeO)含量,以便稳定去磷效果。
为了去磷,吹炼过程中,应根据去磷的热力学条件,首先要搞好前期渣,尽快形成高氧化性的炉渣,以利于前期低温去磷。
而在吹炼后期要控制好炉渣碱度和渣中的(FeO),以利于后期高温、高碱度、高(FeO)脱磷。
当脱磷反应达到平衡时,用浓度来表示的平衡常数为:Kp= (P2O5)/[p]2(FeO)5(CaO)4常用磷在炉渣和金属中的分配比来表示脱磷能力,其表示方法很多。
常用L p=(P2O5)或Lp= (P2O5)/ [p].Lp越大,炼钢过程中脱磷能力也越大。
平衡常数和温度的关系:Lg=51875/T-33.16从脱磷反应的反应式、平衡常数及温度关系,可知影响脱磷的因素有:2.1炉渣碱度的影响。
由分配比公式可知:渣中的CaO越高,分配比越高,脱磷能力就越强。
CaO的脱磷作用在于:它能使P2O5生成稳定的磷酸钙。
100t顶底复吹转炉冶炼过程矿相及硫磷变化规律解析

100t顶底复吹转炉冶炼过程矿相及硫磷变化规律解析赵斌;吴伟;吴巍;崔怀周;汪成义;王天明【摘要】研究了某钢厂100 t顶底复吹转炉炼钢过程中熔池金属成分、炉渣成分、温度的变化以及熔池脱碳、脱磷、脱硫的情况,检测了炉渣的成分变化和岩相结构.试验结果表明,吹炼终点时脱磷、脱硫反应偏离平衡值较远,转炉炼钢平均脱磷率为87%,平均脱硫率为30%.[C][O]积为0.0045,降碳速度为0.429 %/min,熔池平均升温速度为33.46 ℃/min,每增加1%质量分数的碳,钢水温度提高76.87 ℃.该厂炉龄大于5000炉,导致碳氧积升高,从而影响了碳氧反应的动力学条件.炉渣碱度的变化对转炉脱磷率没有明显影响.增加初期烧结矿平均用量,提高前期化渣速度,可避免后期炉渣返干.%The variation of the composition of melt,slag and the temperature,the reaction of decarburization, dephosphorization and desulfurization of molten pool in a 100 t top and bottom combined with blown converter in a steel plant were studied. The composition changeand petrographic structure of the slag were examined. The experimental results showed that the dephosphorization and desulfurization reactions were far from the equilibrium value at the end of the blowing finish. The average dephosphorization rate was 87%,and the average desulfurization rate was 30%. The product of [C] and [O] was 0.004 5,the rate of carbon reduction was 0.429 %/min, the average heating rate of molten pool was 33.46 ℃/min, the additon of each 1% C (by mass) increased the temperature of molten steel by 76.87℃. The campaign life of the plant exceeded 5 000 heats, so the product of carbon and oxygen increased, thereby affecting the dynamic conditions of carbon oxygen reaction. Thechange of slag basicity has no obvious influence on dephosphorization rate. The increase in the average amount of presintering can improve the early slagging speed, avoiding slag redried during post blowing period.【期刊名称】《上海金属》【年(卷),期】2018(040)003【总页数】6页(P73-78)【关键词】顶底复吹转炉;钢水;炉渣;岩相分析【作者】赵斌;吴伟;吴巍;崔怀周;汪成义;王天明【作者单位】钢铁研究总院冶金工艺研究所,北京 100081;钢铁研究总院冶金工艺研究所,北京 100081;钢铁研究总院冶金工艺研究所,北京 100081;钢铁研究总院冶金工艺研究所,北京 100081;钢铁研究总院冶金工艺研究所,北京 100081;钢铁研究总院冶金工艺研究所,北京 100081【正文语种】中文在钢铁行业产能过剩的大环境下,为降低生产成本,提高产品竞争力,很多钢铁企业在综合考虑自身工艺水平及设备环境条件下,开发高效、低成本、精准控制的转炉洁净钢生产工艺技术,在铁水预处理、转炉“双渣法”和“双联法”脱磷的基础上,希望在转炉内将磷含量控制在合理的水平,因此研究高效、低成本精准控制的转炉洁净钢生产工艺技术十分必要。
- 1、下载文档前请自行甄别文档内容的完整性,平台不提供额外的编辑、内容补充、找答案等附加服务。
- 2、"仅部分预览"的文档,不可在线预览部分如存在完整性等问题,可反馈申请退款(可完整预览的文档不适用该条件!)。
- 3、如文档侵犯您的权益,请联系客服反馈,我们会尽快为您处理(人工客服工作时间:9:00-18:30)。
《脱磷转炉吹炼各阶段碳、磷和温度的关系》试验方案数据采集
Ⅰ、计划试验5炉,对数据进行采集、总结。
Ⅱ、准备
一、原料准备:
1、铝粒:准备铝粒20粒以上,以备取样时使用;
(1)、责任人:赵刚
(2)、完成时间:2008年4月20日前完成;
二、工具准备
1、样勺:共准备4个,赵刚负责,2008年4月20日前完成;
2、样模:共准备3个,赵刚负责,2008年4月20日前完成;
Ⅲ、热平衡参数表
终点目标:
1、终点碳:0.06 %
2、终点温度:1660℃.
Ⅳ、试验过程数据
1、试验炉次使用全铁块
三、辅料条件
根据炼钢厂现有条件,记录试验炉次使用石灰的主要指标,试验时石灰、白云石现场取样10Kg(备检),赵刚负责。
4、污泥球
1、枪位:前期枪位值:900±50mm;
2、压力:0.9±0.05Mpa;
3、流量:10000-12000m3/min;
4、底吹流量:
采用F模式,总流量设定值1080Nm3/h,倒炉,测温,兑铁时,总流量控制在540 Nm3/h,四炉支管流量平均。
预案:若实验时,碰到转炉内兑入回炉钢,底吹采用C模式,总流量设定值220Nm3/h,倒炉,实际总流量可控制在320 Nm3/h左右,四炉支管流量平均在80 Nm3/h。
5、加料方案:
5、取样(要求:取样保证准确,不和别的钢样、渣样掺混,做好标识)
取样由乔春刚负责,化验及结果由亓传军负责
五、出钢操作
1、出钢时间:
(1)、要求≥2分30秒
(2)、试验炉次实际出钢时间:
2、挡渣:前期挡渣塞,出钢挡渣球;
3、下渣量:
(1)、要求钢包内渣层厚度≤50mm,(2)、试验炉次实际渣层厚度:。