转炉脱磷及深脱磷
转炉炼钢流程中的脱磷工艺
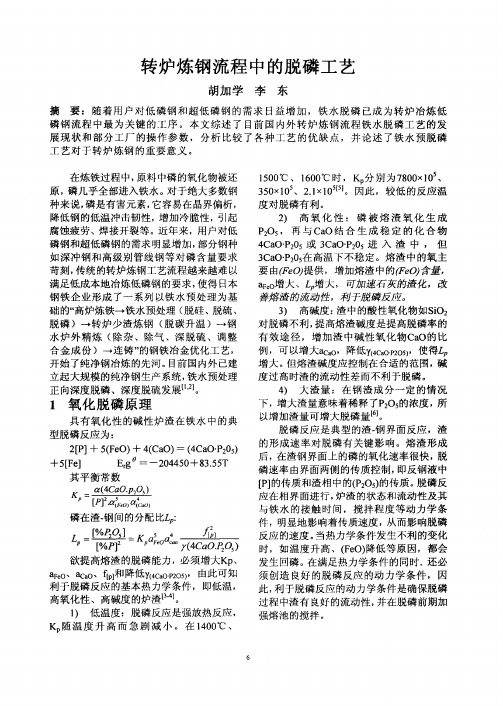
磷 在渣. %P
:
a ̄
7 C . ・ y4 a Q ) ( OP 0 2
欲提 高熔 渣 的脱磷 能力 ,必须增 大K 、 p ae、aa、f]口 F 0 co t 降低1 C .O) 由止 可 失 p , P 5 ( O2 , 4 匕 l J 利 于脱磷 反应 的基 本热 力学 条件 , 即低温 , 高 氧化 性 、高碱度 的炉 渣 【 3 。 1 低温 度 :脱磷 反应 是强 放热 反应 , ) KD 温 度 升 高 而 急 剧 减 小 。 在 10  ̄ 随 4 0C、
3 高碱 度 : 中的酸 性氧化 物如 SO2 ) 渣 i 对脱 磷 不利 , 高熔渣 碱 度是 提 高脱磷 率 的 提 有 效 途 径 ,增 加 渣 中 碱 性氧 化物 C O的 比 a 例 ,可 以增大 a ,降低 丫CO 25 co (a.o) 4 P ,使得三 p 增 大 。 熔渣碱 度 应控 制在 合适 的范 围 , 但 碱 度过 高 时渣 的流 动性差 而 不利 于脱磷 。 4 大 渣 量 :在 钢渣 成 分 一 定 的情 况 ) 下 ,增 大渣 量意 味着稀 释 了P05 2 的浓度 , 所 以增 加渣 量 可增 大脱磷 量 【。 o J 脱 磷 反应 是 典型 的渣 界 面 反应 ,渣 钢 的形 成 速 率对 脱 磷 有 关 键影 响 。熔 渣 形成 后 ,在渣 钢 界面上 的磷 的氧 化速 率很 快 , 脱 磷速 率 由界 面两侧 的传 质控 制 , 即反钢 液 中 【] P 的传 质 和渣相 中 的(2 ) Po5的传质 。 磷反 脱 应 在相 界面 进 行 , 炉渣 的状 态和 流动 性及其 与 铁 水 的接触 时 间 ,搅 拌程 度 等 动 力 学条 件 ,明显地 影响着 传质 速度 , 从而 影 响脱磷 反应 的速度 。 当热 力学条 件 发生 不利 的变化 时 ,如温 度升 高 、(e ) F O 降低 等原 因,都会 发 生 回磷 。在满足 热力 学条 件 的 同时 . 还必 须 创 造 良好 的脱 磷 反 应 的动 力 学 条 件 , 因 此 , 于脱 磷 反应 的动力 学 条件 是确 保脱磷 利 过 程 中渣 有 良好 的流 动性 , 并在 脱磷 前期加 强熔 池 的搅 拌 。
(完整word版)转炉脱磷分析及采取的措施2
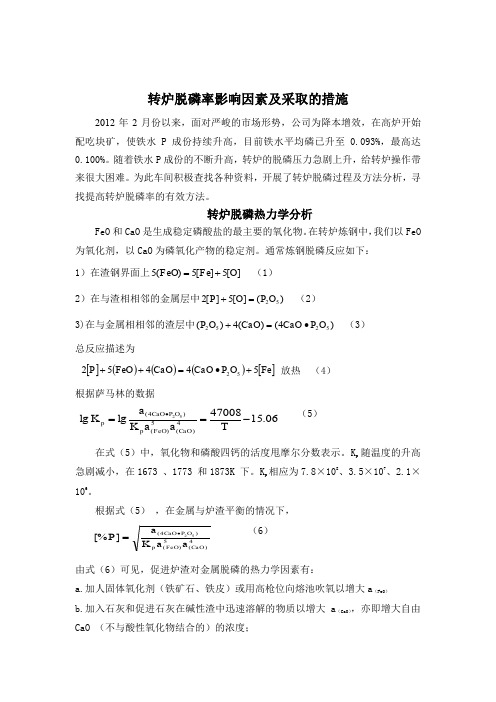
转炉脱磷率影响因素及采取的措施2012年2月份以来,面对严峻的市场形势,公司为降本增效,在高炉开始配吃块矿,使铁水P 成份持续升高,目前铁水平均磷已升至0.093%,最高达0.100%。
随着铁水P 成份的不断升高,转炉的脱磷压力急剧上升,给转炉操作带来很大困难。
为此车间积极查找各种资料,开展了转炉脱磷过程及方法分析,寻找提高转炉脱磷率的有效方法。
转炉脱磷热力学分析FeO 和CaO 是生成稳定磷酸盐的最主要的氧化物。
在转炉炼钢中,我们以FeO 为氧化剂,以CaO 为磷氧化产物的稳定剂。
通常炼钢脱磷反应如下:1)在渣钢界面上][5][5)(5O Fe FeO += (1)2)在与渣相相邻的金属层中)(][5][252O P O P =+ (2)3)在与金属相相邻的渣层中)4()(4)(5252O P CaO CaO O P ∙=+ (3)总反应描述为[]()()()[]Fe O P CaO CaO FeO P 5445252+∙=++ 放热 (4)根据萨马林的数据(5)在式(5)中,氧化物和磷酸四钙的活度甩摩尔分数表示。
K p 随温度的升高急剧减小,在1673 、1773 和1873K 下。
K p 相应为7.8×108、3.5×107、2.1×106。
根据式(5) ,在金属与炉渣平衡的情况下,(6)由式(6)可见,促进炉渣对金属脱磷的热力学因素有:a.加人固体氧化剂(铁矿石、铁皮)或用高枪位向熔池吹氧以增大a (FeO )b.加入石灰和促进石灰在碱性渣中迅速溶解的物质以增大a (CaO ),亦即增大自由CaO (不与酸性氧化物结合的)的浓度;06.1547008lg lg 4)(5)()4(52-==∙T a a K a K CaO FeO p O P CaO p 4)(5)()4(52][%CaO FeO p O P CaO a a K a P ∙=c.用更新与金属接触的渣相的方法,亦即放渣和加入CaO 与FeO 造新渣的方法来减小)4(52O P CaO a ∙d.保持适当的低温,因为温度从1673 增到1873K ,使反应(4)的平衡常数K p 减小到1/370 。
转炉脱磷造渣工艺
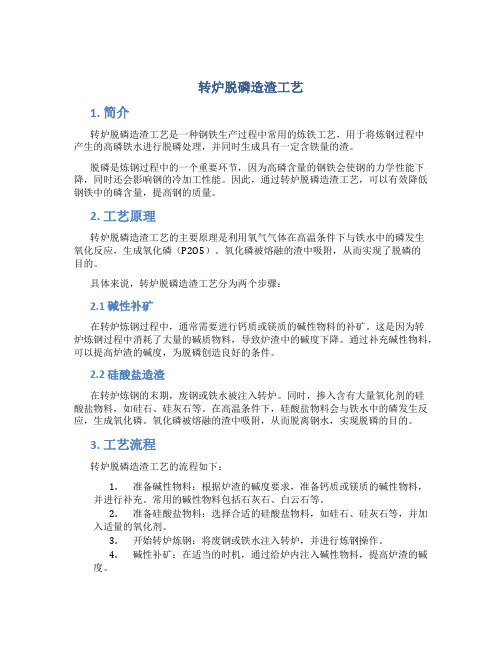
转炉脱磷造渣工艺1. 简介转炉脱磷造渣工艺是一种钢铁生产过程中常用的炼铁工艺,用于将炼钢过程中产生的高磷铁水进行脱磷处理,并同时生成具有一定含铁量的渣。
脱磷是炼钢过程中的一个重要环节,因为高磷含量的钢铁会使钢的力学性能下降,同时还会影响钢的冷加工性能。
因此,通过转炉脱磷造渣工艺,可以有效降低钢铁中的磷含量,提高钢的质量。
2. 工艺原理转炉脱磷造渣工艺的主要原理是利用氧气气体在高温条件下与铁水中的磷发生氧化反应,生成氧化磷(P2O5)。
氧化磷被熔融的渣中吸附,从而实现了脱磷的目的。
具体来说,转炉脱磷造渣工艺分为两个步骤:2.1 碱性补矿在转炉炼钢过程中,通常需要进行钙质或镁质的碱性物料的补矿。
这是因为转炉炼钢过程中消耗了大量的碱质物料,导致炉渣中的碱度下降。
通过补充碱性物料,可以提高炉渣的碱度,为脱磷创造良好的条件。
2.2 硅酸盐造渣在转炉炼钢的末期,废钢或铁水被注入转炉。
同时,掺入含有大量氧化剂的硅酸盐物料,如硅石、硅灰石等。
在高温条件下,硅酸盐物料会与铁水中的磷发生反应,生成氧化磷。
氧化磷被熔融的渣中吸附,从而脱离钢水,实现脱磷的目的。
3. 工艺流程转炉脱磷造渣工艺的流程如下:1.准备碱性物料:根据炉渣的碱度要求,准备钙质或镁质的碱性物料,并进行补充。
常用的碱性物料包括石灰石、白云石等。
2.准备硅酸盐物料:选择合适的硅酸盐物料,如硅石、硅灰石等,并加入适量的氧化剂。
3.开始转炉炼钢:将废钢或铁水注入转炉,并进行炼钢操作。
4.碱性补矿:在适当的时机,通过给炉内注入碱性物料,提高炉渣的碱度。
5.硅酸盐造渣:当转炉炼钢接近末期时,通过给炉内注入硅酸盐物料,利用氧化剂促进磷的氧化反应。
6.淋渣:根据炉内的渣情况,选择合适的时间进行淋渣操作。
淋渣可以通过人工或机械设备进行。
7.渣铁分离:在脱磷过程中,渣中生成的氧化磷会被吸附在渣中,从而脱离钢水。
通过合适的方法,将渣与钢水分离。
8.尾渣处理:处理分离出来的尾渣,并对其进行资源化利用或安全处理。
转炉脱磷、造渣工艺

是中期是碳剧烈氧化期,不能变化太快,抑制脱碳反应
突然温度降低,防止喷溅。据上所述,碳的大量氧化,
低磷,在因钢为坯中复的杂偏零析件度要很求大,钢而板在很α和高γ的固塑溶体性内。的IF扩钢散速度 却[很P小]<,0使.0它15不%容易均匀化。因此,按照用途不同对钢中磷含
量有严格要求:
东大冶金
1. 脱P反应
1. 脱P反应
.cn , 110004
2[P]+5[O]= P2O5 2[P]+5(FeO)=(P2O5)+5Fe 3(FeO)+(P2O5)=(3FeO·P2O5) (聚磷酸铁)
EMTI
Shenyang NEU Metallurgical Technology Corporation Limited
技术精益求精 · 创新永无止境
转炉脱磷、造渣工艺
沈阳东大冶金科技股份有限公司
东大冶金110004
磷在钢中以[Fe2P]形式存在,也可以用[P]表示。磷虽然能
前期渣中的(FeO)含量对脱磷反应的进行有重要 作用,这是因为:
12
东大冶金
3. 氧气转炉各期脱磷
.cn , 110004
影响前期脱磷的主要因素是碱度。而高的(FeO)含量 只是一个不可缺少的条件——也是在操作上前期快速成渣 的手段。换言之,就是控制喷枪,使(FeO)在10~15%左 右。炉渣前期 碱度为1.5左右,碱度提高更有利于脱磷,但 因前期温度低,客观上不可能造成高碱度炉渣。并且在此 (FeO)含量范围,碱度在0.82~1.5范围内,炉渣具有较低 的粘度,而碱度高于1.5时,粘度值随碱度增加而快速提 高,炉渣流动性显著变差,不利于脱磷。总之,通常必须 根据铁水条件把前期渣碱度控制在1.5左右;而(FeO) 在10~15%左右或更高些。
转炉深脱磷反应机理
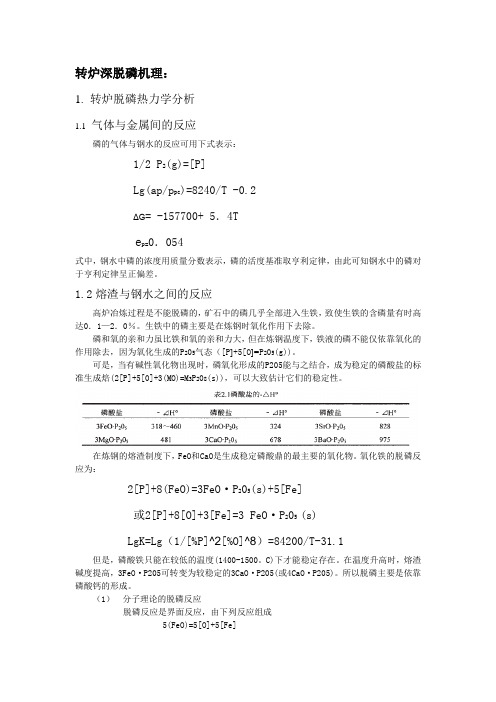
转炉深脱磷机理:1.转炉脱磷热力学分析1.1气体与金属间的反应磷的气体与钢水的反应可用下式表示:1/2 P2(g)=[P]Lg(ap/p pc)=8240/T -0.2ΔG= -157700+ 5.4Te p=0.054式中,钢水中磷的浓度用质量分数表示,磷的活度基准取亨利定律,由此可知钢水中的磷对于亨利定律呈正偏差。
1.2熔渣与钢水之间的反应高炉冶炼过程是不能脱磷的,矿石中的磷几乎全部进入生铁,致使生铁的含磷量有时高达0.1—2.0%。
生铁中的磷主要是在炼钢时氧化作用下去除。
磷和氧的亲和力虽比铁和氧的亲和力大,但在炼钢温度下,铁液的磷不能仅依靠氧化的作用除去,因为氧化生成的P205气态([P]+5[O]=P205(g))。
可是,当有碱性氧化物出现时,磷氧化形成的P205能与之结合,成为稳定的磷酸盐的标准生成焙(2[P]+5[0]+3(MO)=M3P208(s)),可以大致估计它们的稳定性。
在炼钢的熔渣制度下,FeO和CaO是生成稳定磷酸鼎的最主要的氧化物。
氧化铁的脱磷反应为:2[P]+8(FeO)=3FeO·P205(s)+5[Fe]或2[P]+8[O]+3[Fe]=3 FeO·P205 (s)LgK=Lg(1/[%P]^2[%O]^8)=84200/T-31.1但是,磷酸铁只能在较低的温度(1400-1500。
C)下才能稳定存在。
在温度升高时,熔渣碱度提高,3FeO·P205可转变为较稳定的3CaO·P205(或4CaO·P205)。
所以脱磷主要是依靠磷酸钙的形成。
(1)分子理论的脱磷反应脱磷反应是界面反应,由下列反应组成5(FeO)=5[O]+5[Fe]2[P]+5[0]=(P205)(P205)+4(CaO)=(4CaO·P205)综合得:2[P]+5(FeO)+4(CaO)=4CaO·P205+5[Fe]LgK=Lg (a (4Ca0·P205)/[%P]^2 a FeO^5·a CaO^4)=40067/T-15.06式中:K------------------脱磷反应的化学平衡常数:T------------------钢水温度。
1161 转炉冶炼过程脱磷分析
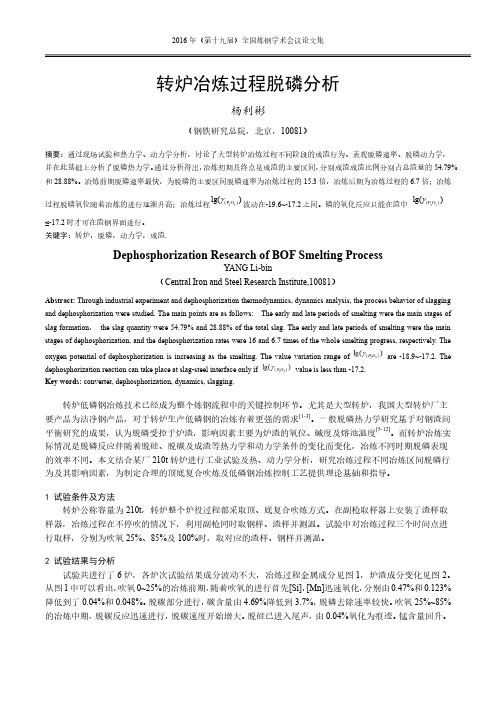
(2)
(3)
(4)
图 5 冶炼过程磷含量及表观脱磷速率 Fig.5 [P] content and apparent rate of dephosphorization
冶炼过程磷含量及表观脱磷速率如图 5 所示。可以看出,冶炼前期磷含量由 0.098%脱除到 0.038%, 脱除速率最快,平均表观脱磷速率为 0.0153%/min。冶炼过程平均表观脱磷速率为 0.001%/min。冶炼后期, 表观脱磷速率为 0.0067%/min,脱磷速率回升。冶炼过程表观脱磷速率波动范围为 0.00088%/min~ 0.02448%/min,冶炼前期熔池温度低,炉渣氧化性强,成渣效率高,表观脱磷速率最高为 0.016%/min,为 冶炼过程脱磷速率的 15.3 倍。冶炼中期炉渣氧化性为冶炼过程最低,化渣效率差,且熔池温度不断升高, 表观脱磷速率最小为 0.001%/min,冶炼后期随着渣中氧化性的提高,炉渣进一步熔化,表观脱磷速率回升 达到 0.006%/min,为冶炼过程脱磷速率的 6.7 倍。可以发现冶炼前期及冶炼后期是脱磷的主要区间。 冶炼终点表观脱磷速率常数最大,冶炼前期次之。反应平衡磷含量随着冶炼的进行逐渐增加,熔池驱 动力(磷含量浓度差)逐渐降低。说明,冶炼前期脱磷的主要动力为平衡的磷含量较低导致脱磷驱动力大, 冶炼终点脱磷主要是由于表观脱磷速率常数较大。
lg( ( P2O5 ) )
波动在-19.6~-17.2 之间。磷的氧化反应只能在渣中
lg( ( P2O5 ) )
Dephosphorization Research of BOF Smelting Process
YANG Li-bin (Central Iron and Steel Research Institute,10081)
转炉炼钢脱磷工艺理论与实践
转炉炼钢脱磷工艺理论与实践摘要:适当的磷可以提升钢的强度,但是对于大多数的钢种都是有害元素,磷含量过高会降低钢材的塑性、焊接性以及冲击韧性。
研究表明磷在钢液凝固过程中发生偏析现象比较集中地聚集在晶界处,导致较低温度下钢材性能变脆,通常成为“冷脆”现象。
磷含量对钢铁的影响极大,即使很少量的磷(0.01%)也会导致钢材的低温脆性。
因此对于普通的钢种磷含量要求在0.04%以内,在低温环境下应用的钢种要求含磷低到0.003%以下,如严寒地区的钻井平台、船舶、轨道、钢结构承重件、液化气管道等。
脱磷反应是转炉炼钢过程重要的物理化学反应,也是转炉炼钢的基本任务之一。
结合实践进行说明脱磷过程注意事项。
关键词:转炉炼;钢脱磷;工艺1转炉炼钢脱磷原理与条件1.1转炉炼钢脱磷原理转炉吹炼过程铁水中的磷被氧化生成P2O5进入炉渣中,P2O5是酸性氧化物,能与炉渣中的碱性氧化物FeO、CaO、MnO、MgO等生成磷酸盐化合物,更稳定的存在渣中,随炉渣一起除掉。
炉渣碱度较低时磷多以磷酸铁(3FeO•P2O5)的形式存在,炉渣碱度较高时磷多以磷酸钙(3CaO•P2O5或4CaO•P2O5)的形式存在。
1.1.1磷的氧化反应磷的氧化反应在钢—渣界面上进行,反应方程式一般有2种:4/5[P]+2[O]=2/5(P2O5)标准吉布斯能△Gθ=-384953+170.24T(J/mol)。
或者:4/5[P]+2(FeO)=2/5(P2O5)+2Fe(l)标准吉布斯能△Gθ=-142944+65.48T(J/mol)。
1.1.2P2O5在炉渣中的固定氧化生成的P2O5如要在渣中稳定存于炉渣中,必须与炉渣中的CaO等碱性氧化物反应生成稳定的磷酸盐化合物3CaO•P2O5或4CaO•P2O5,反应方程式为:2[P]+5[O]+3(CaO)=(3CaO•P2O5)标准吉布斯能△Gθ=-1486160+6360T。
由反应方程式可以看出,转炉炼钢脱磷原理在于磷的氧化进入渣中和转化为稳定的磷酸盐,脱磷速度主要取决于钢—渣界面磷的氧化反应。
转炉深脱磷反应机理
转炉深脱磷机理:1.转炉脱磷热力学分析1.1气体与金属间的反应磷的气体与钢水的反应可用下式表示:1/2 P2(g)=[P]Lg(ap/p pc)=8240/T -0.2ΔG= -157700+ 5.4Te p=0.054式中,钢水中磷的浓度用质量分数表示,磷的活度基准取亨利定律,由此可知钢水中的磷对于亨利定律呈正偏差。
1.2熔渣与钢水之间的反应高炉冶炼过程是不能脱磷的,矿石中的磷几乎全部进入生铁,致使生铁的含磷量有时高达0.1—2.0%。
生铁中的磷主要是在炼钢时氧化作用下去除。
磷和氧的亲和力虽比铁和氧的亲和力大,但在炼钢温度下,铁液的磷不能仅依靠氧化的作用除去,因为氧化生成的P205气态([P]+5[O]=P205(g))。
可是,当有碱性氧化物出现时,磷氧化形成的P205能与之结合,成为稳定的磷酸盐的标准生成焙(2[P]+5[0]+3(MO)=M3P208(s)),可以大致估计它们的稳定性。
在炼钢的熔渣制度下,FeO和CaO是生成稳定磷酸鼎的最主要的氧化物。
氧化铁的脱磷反应为:2[P]+8(FeO)=3FeO·P205(s)+5[Fe]或2[P]+8[O]+3[Fe]=3 FeO·P205 (s)LgK=Lg(1/[%P]^2[%O]^8)=84200/T-31.1但是,磷酸铁只能在较低的温度(1400-1500。
C)下才能稳定存在。
在温度升高时,熔渣碱度提高,3FeO·P205可转变为较稳定的3CaO·P205(或4CaO·P205)。
所以脱磷主要是依靠磷酸钙的形成。
(1)分子理论的脱磷反应脱磷反应是界面反应,由下列反应组成5(FeO)=5[O]+5[Fe]2[P]+5[0]=(P205)(P205)+4(CaO)=(4CaO·P205)综合得:2[P]+5(FeO)+4(CaO)=4CaO·P205+5[Fe]LgK=Lg (a (4Ca0·P205)/[%P]^2 a FeO^5·a CaO^4)=40067/T-15.06式中:K------------------脱磷反应的化学平衡常数:T------------------钢水温度。
转炉炼钢脱磷工艺分析
II
第三章 试验方案的设计.............................................................................................................. 27 3.1 沙钢双渣脱磷的现状........................................................................................................ 27 3.1.1 双渣操作的好处......................................................................................................... 27 3.1.2 沙钢双渣脱磷情况.....................................................................................................27 3.1.3 脱磷的效果及回磷问题............................................................................................ 28 3.2 目前存在的问题................................................................................................................. 29 3.2.1 前期脱磷结果............................................................................................................. 29 3.3 影响前期脱磷的主要因素............................................................................................... 30 3.3.1 钢水中硅的氧化......................................................................................................... 30 3.3.2 前期渣碱度的控制.....................................................................................................30 3.3.3 倒前期渣时间的控制................................................................................................ 31 3.4 180t 转炉冶炼终点脱磷情况.......................................................................................... 32 3.4.1 增碳剂加入量的控制................................................................................................ 32 3.4.2 冶炼终点脱磷情况.....................................................................................................32 3.5 180t 转炉冶炼工艺改进方案.......................................................................................... 32 3.5.1 冶炼前期控制............................................................................................................. 33 3.5.2 冶炼终点控制............................................................................................................. 33 结论..............................................................................................................................................35 参考文献..................................................................................................................................... 36 致 谢....................................................................................................................................... 37
专用转炉脱磷定义
专用转炉脱磷定义
专用转炉脱磷是一种钢铁冶炼工艺,用于降低钢铁中的磷含量。
在转炉冶炼过程中,将含有高磷含量的生铁或废钢加入转炉中,并通过氧气吹炼来氧化磷元素。
氧化的磷会形成磷酸盐,并通过被吹入的氧气或其他气体带离炉体,从而实现钢铁中磷含量的脱除。
这种脱磷方法可以有效地降低钢铁中的磷含量,提高钢材的质量和性能。
专用转炉脱磷通常采用两种方法进行操作:直喷法和底吹法。
直喷法是将含有高磷含量的生铁或废钢加入转炉中,同时通过氧气喷嘴将高压氧气喷射到炉料表面。
氧气在炉内与炉料中的磷反应,将其氧化成磷飞渣,然后通过氧气吹出口排出炉外。
这种方法在转炉冶炼过程中进行,可以实现较好的脱磷效果。
底吹法则是将转炉底部设置氧气吹口,以气体形式喷入炉底。
气体能够有效地搅动炉料,促进炉料和氧气的接触,并加速磷元素的氧化反应。
炉底吹气法可以提高脱磷速度和脱磷效果,但同时也增加了炉底的磨损和耐火材料的消耗。
专用转炉脱磷方法具有高效、灵活、可控性好等优点,可以根据钢铁的不同需求和磷元素的含量来选择适当的操作方法。
通过脱磷工艺,可以有效地降低钢铁中的磷含量,提高钢材的质量和性能,同时满足不同领域的使用要求。
- 1、下载文档前请自行甄别文档内容的完整性,平台不提供额外的编辑、内容补充、找答案等附加服务。
- 2、"仅部分预览"的文档,不可在线预览部分如存在完整性等问题,可反馈申请退款(可完整预览的文档不适用该条件!)。
- 3、如文档侵犯您的权益,请联系客服反馈,我们会尽快为您处理(人工客服工作时间:9:00-18:30)。
精心整理转炉脱磷工艺近年来,随着我国钢材的发展,对低磷钢的生产要求越来越高,对高级别钢特别是低磷钢的需求大大增加,这些产品对钢中磷的质量分数提出了很高的要求,大多要求磷含量低于0.015%;低温用钢管、特殊深冲钢、镀锡板要求钢中磷低于0.010%;一些航空、原子能、耐腐蚀管线用钢要求磷低于0.005%,所以超法,空间大,允许强烈搅拌钢水,顶吹供氧,高强度底吹,不需要预脱硅,废钢比较高,炉渣碱度比较低,渣量低,处理后铁水温度较高(1350),脱磷效率明显提高。
1转炉脱磷新工艺1.1JFE福山制铁所福山制铁所,有两个炼钢厂(第二炼钢厂和第三炼钢厂)。
该制铁所是日本粗钢产量最好的厂家。
第三炼钢厂有2座320T的顶底复吹转炉,采用LD-NRP工艺(双联法),一座转炉脱磷,另一座转炉脱碳,转炉脱磷能力为450万t/a。
该厂1999年开始全量铁水转炉脱磷预处理。
转炉脱磷指标:吹炼时间为10分钟,废钢比为7%~10%;氧气流量为30000),“三25%,运送给第二炼钢厂。
脱磷转炉指标:吹炼时间为8min;冶炼周期为22Min;废钢比为10%(加轻废钢);出铁温度为1350;渣量为40kg/t。
脱碳转炉指标:吹炼时间为14min;冶炼周期为30Min;锰矿用量为15kg/t (Mn回收率:30%~40%);渣量为20kg/t(以干渣方式回收)。
1.3住友金属和歌山制铁所住友金属和歌山制铁所粗钢产能390万吨。
炼钢生产采用SRP法,100%铁水经转炉脱磷。
该厂脱磷转炉与脱碳转炉设在不同跨,脱磷转炉和脱碳转炉的吹炼时间9~12min,转炉炼钢的冶炼周期在20min以内。
一个转炉炼钢车间供钢水给三台连铸机,是目前世界上炼钢生产节奏最快的钢厂。
SRP法优点是:IF钢由于神户制钢生产的高碳钢比例较大,转炉的脱磷负荷大,铁水脱磷,脱硫预处理用H炉(专用转炉),处理过程分两步:首先在高炉出铁沟用喷吹法对铁水进行脱硅处理,用撇渣器去除脱硅渣后,将铁水在兑入H炉进行脱磷,脱硫。
脱磷时,喷吹石灰系渣料,同时顶吹氧气;脱磷后,在喷入苏打粉系渣料脱硫。
经预处理的铁水再装入另一座转炉进行脱碳。
用H炉进行铁水脱磷,脱硫处理具有如下特征:(1)H炉内空间大,进行铁水预处理时,炉内反应效率高,反应速度快,可在较短的时间内连续完成脱磷,脱硫处理;(2)可用块状生石灰和转炉渣代替部分脱磷渣;(3)脱磷过程中添加部分锰矿,可提高脱磷效率,且增加了铁水中的猛含量。
1.5新日铁八幡制铁所新日铁八幡制铁所有两个炼钢厂,第一炼钢厂2座170t转炉,采用传统的三脱工艺;第二炼钢厂2座350t转炉生产采用新日铁名古屋制铁所发明的LD—ORP工艺(双联法)见下图:1.6新日铁君津制铁所新日铁君津制铁所有2个炼钢厂,第一炼钢厂和第二炼钢厂均采用KR法脱硫(S<=0.002%)。
第一炼钢厂有3座230t复吹转炉;第二炼钢厂有2座300t复吹转炉,采用LD—ORP法和MURC(双渣法)法两种工艺炼钢。
LD—ORP法渣量少,可生产高纯净钢。
脱磷转炉弱供氧,大渣量,碱度2.5~3.0,温度为1320~1350,纯脱磷时间约为9~10min,冶炼周期约20min,废钢比通常为9%,为了提高产量,目前废钢比已达到11%~14%,经脱磷后钢水(P<=0.002%)兑入脱碳转炉,总收得率92%以上。
转炉的复吹寿命约4000炉。
脱碳转炉强供氧,少渣量,冶炼周期为28~30min,脱碳转炉不吃废钢。
从脱磷至脱碳结束的总冶炼周期约为50Min.恰好与连铸机的浇灌周期50~60min相匹配。
日本大型钢铁厂转炉双联法生产指标参见下表复吹“双MURC(约MURC法中间扒渣是其最突出的特点。
如果扒渣不稳定,含磷渣排出少,将影响脱磷效果和脱碳的正常运行。
因此,MURC法的关键是中间扒脱磷渣的操作稳定。
在脱磷吹炼末期,会出现一定量的泡沫渣,可有效的利用渣的泡沫化进行扒渣。
渣的泡沫化是中间扒渣的关键,应注意控制脱磷吹炼渣的成分和碱度。
1.8德国的TBM脱磷工艺TBM是由蒂森一克虏博炼钢厂转炉炼钢的一种冶炼工艺,该技术除了具有传统底吹的冶金效果之外,还具有显着的底吹深脱磷功能。
它主要是通过独特的环形布置的底枪提高供气强度,为脱磷提供良好的动力学条件,从而提高转炉脱磷率。
同时也使转炉终点碳.氧反应更接近平衡,从而降低了钢中氧含量。
TBM技术是一个喷气模型系统,其有如下优点:非常高的气体喷吹速度,完BRP工艺万元。
2002~2005年项目总经济效益约为6亿元。
BRP工艺生产的主要是低磷和超低磷钢,包括管线钢,IF钢,帘线钢,石油钻杆钢等,脱磷炉停吹时,磷含量平均在0.015%以下,最低达到0.003%,钢坯磷含量低于0.006%,进行少渣吹炼时,脱磷和脱碳后的总渣量低于60kg/t。
BRP 工艺对于拓展品种,提高钢水品质以及实现效益最大化有重要作用。
2.2首钢脱磷工艺近年来,首钢为了提高自身产品在市场中的竞争力,投资近两亿元,在第三炼钢厂兴建了LF精炼炉和VD真空脱气设备,并改造了一台130mm×130mm八流小方坯连铸机,使该厂具备了优质长材坯料生产条件。
在开发和生产82B、77B、72A等高碳品种的过程中,针对钢中磷含量要求严格的问题,进行了转炉脱磷冶%;首钢迁钢原转炉脱磷率仅为75%左右,自采用副枪系统后,脱磷效果明显改善,脱磷率提高至85%以上。
根据副枪模型数据、加料情况、钢样和渣样化验数据,结合声纳化渣图,分析了首钢迁钢转炉脱磷率提高的原因,为今后进一步优化脱磷工艺提供依据。
2.4本钢转炉脱磷工艺的研究随着本钢生产工艺及设备的不断改进与完善,一些特殊钢种(薄板钢种、深冲钢等)相继投入生产。
这些钢种对钢的纯净度要求越来越高,尤其对钢中的[P]含量的要求也越来越低,最低值在0.0085以下。
针对我厂的生产工艺条件,如何稳定有效的控制[P]含量,满足钢种的要求,有必要对转炉脱磷工艺进行研究。
先进工艺的采用是建立在先进设备的基础上,而鞍钢作为一个老企业,尚有部分转炉仅有顶吹功能,且还不具备全部铁水预脱磷的能力,因而探索顶吹转炉的脱磷规律,优化脱磷工艺,对于降低成本、提高企业自主创新能力和产品的市场竞争力有着重要的意义。
鞍钢一炼钢100t氧气顶吹转炉进行了单渣法和双渣法脱磷的过程分析和工艺实践,在反应热力学和动力学分析的基础上,设计了有针对性的试验。
根据现场数据,利用统计和回归分析工具,逐一分析了转炉装料、造渣、供氧、温度制度等工艺参数对脱磷反应的影响,提炼出影响脱磷效率的主要因素,总结出不同工艺下转炉出钢磷、脱磷率等与各参数的定量关系,为优化顶吹转炉脱磷工艺提11.11.1.形成了大量的[0],渣钢界面处的氧化性能强,钢渣都具有较高的氧化性,强烈的氧化性氛围促进了脱磷的顺利快速进行。
1.1.2转炉功能单一化可缩短冶炼周期由于转炉功能趋于专一化,使得每炉钢水冶炼时间有效缩短,莱钢炼钢厂脱磷转炉吹氧时间7~9min,冶炼周期26"--30min,脱碳转炉吹氧时间9~12min,冶炼周期28~32min,与传统冶炼方式相比,转炉冶炼时间缩短8~10min。
1.1.3渣量少于普通转炉因将传统转炉工艺分为脱磷和脱碳。
脱磷渣不进入脱碳炉,因而不用担心钢水回磷,脱碳炉可以采用较少的渣量进行冶炼。
莱钢炼钢厂脱磷转炉渣量约为30~50kg /t,脱碳转炉渣量约为15~30kg/t。
1.1.205含量14301.1.调整,从而实现铁水与废钢同步调整。
根据脱磷热力学条件,铁水脱磷的温度为1350---1430℃范围较好。
从冶炼操作实绩来看,当铁水温度控制在1250~1330℃时,采用92%的铁水比较为合理,吹炼终点平均温度为1388℃,平均硼(C)=2.68%,为脱碳转炉提供了较好的原料条件,见表2。
1.1.6脱磷转炉造渣制度根据磷分配比情况,将脱磷转炉终渣碱度控制在2.4~2.8,可保证良好的脱磷效果。
为防止铁水脱磷过程产生喷溅,升温过快等异常情况,要求头批料加入石灰2/3,烧结矿全部的1/2,后期根据情况逐步加入石灰及烧结矿进行调整。
烧结矿的大量加入可以有效提高(FeO),在短时间内促进了化渣,同时确保了熔池温度的1.1.(FeO).80~0.1.1.℃,3),2TBM脱磷工艺2.1.T酬强搅拌工艺原理及内容2.1.1TBM强搅拌工艺原理控制转炉吹炼的困难主要是反应速度太快,脱碳高峰期产生大量CO气泡,剧烈搅动熔池,渣钢充分乳化,使渣中(FeO)迅速降低,基本不具备成渣和脱除钢中硫、磷的条件。
因此,吹炼前期迅速形成流动性良好的高碱度炉渣和吹炼后期保证渣钢反应接近平衡,是提高转炉冶炼强度的重要环节。
采用TBM工艺,可以实现在吹炼前期,加强熔池搅拌,促进石灰熔解,提高成渣速度;在吹炼末期,提高熔池搅拌强度,促进渣钢反应平衡。
2.1.2TBM强搅拌工艺主要内容(1)t.min77降至1.39(CMS)(2)达到1终渣,炉渣(3)实现平衡吹炼:TBM采用提高供气强度和改变复吹供气模式,有利于转炉吹炼过程中实现平衡吹炼。
转炉炼钢过程中存在着熔池反应(如c—o、C-—Mn反应等)和钢渣反应(如脱硫、脱磷反应)两种反应过程。
实现熔池反应平衡,一般要求底吹搅拌强度应达到0.08~O.12m3/t.min;实现渣钢反应趋于平衡,底搅强度应达到0.15"-"0.30m3/t.min的水平。
2.2.TBM的底吹供气制度TBM的底吹供气制度是根据氧步即供氧时间阶段来设定的,气体种类是根据钢种对氮含量的要求设定的,以20#钢为例,具体供气制度(见表1)从炉底供给溶池的气体,通过元件喷出后以气泡的形式上浮,抽引钢水随之向卜流动,从而使溶池得到搅拌。
其目的就是改善溶池混合状态,增强物质传递速度,l。
2.3TBM2.3.1【C】-图2是2.3.2T含量渣中%,平均降低2.3.3对转炉吹炼操作的影响由于底枪数量增加,采用环形布置,进一步增加了渣.钢之间的接触面积,使碳—氧反应更接近平衡,钢中残留氧有所下降,使渣中(FeO)降低,进而减少了因渣中(FeO)聚集而产生的爆发性喷溅的可能性,使吹炼更加平稳。
另外,由于降碳速度的加快,使供氧时间缩短。
表2为转炉供氧时间,2.3.4T BM对脱磷率的影响从热力学的观点看,TBM使渣中(FeO)降低,不利于脱磷反应的进行,但TBM之后,供气强度的增大使熔池搅拌加强,大大改善了脱磷反应的动力学条件,提高了熔池的传质速度,使脱磷反应更接近于平衡,提高了转炉脱磷率。
取同一时期相同铁水条件下,80吨和120吨转炉一倒脱磷率比较,见表3,从表3,即磷在钢中以Fe3P或Fe2P形式存在,但通常以[P]来表达。
炼钢过程的脱磷反应是在金属液与熔渣界面进行的,首先是[P]被氧化成(P2O5),而后与(CaO)结合成稳定的磷酸钙,其反应式可表示为:2[P]+5(FeO)+4(CaO)=(4CaO·P2O5)+5[Fe]2[P]+5(FeO)+3(CaO)=(3CaO·P2O5)+5[Fe]从CaO-P2O5相图中可以看出3CaOP·2O5为最稳定,4CaO·P2O5次之。