转炉炼钢新技术
转炉自动化炼钢技术应用分析
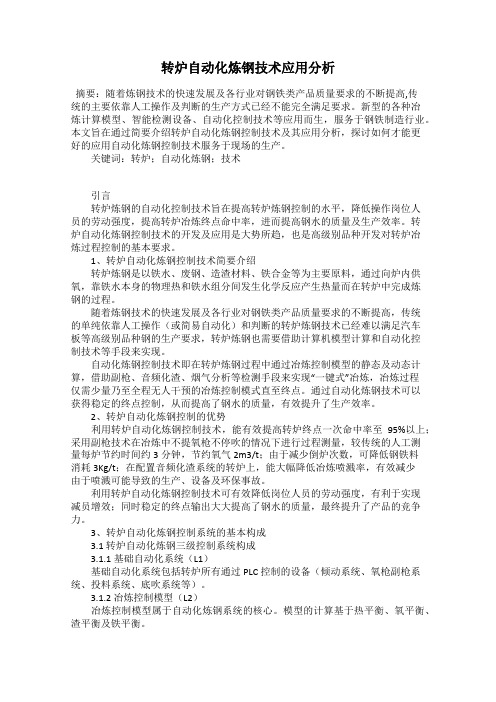
转炉自动化炼钢技术应用分析摘要:随着炼钢技术的快速发展及各行业对钢铁类产品质量要求的不断提高,传统的主要依靠人工操作及判断的生产方式已经不能完全满足要求。
新型的各种冶炼计算模型、智能检测设备、自动化控制技术等应用而生,服务于钢铁制造行业。
本文旨在通过简要介绍转炉自动化炼钢控制技术及其应用分析,探讨如何才能更好的应用自动化炼钢控制技术服务于现场的生产。
关键词:转炉;自动化炼钢;技术引言转炉炼钢的自动化控制技术旨在提高转炉炼钢控制的水平,降低操作岗位人员的劳动强度,提高转炉冶炼终点命中率,进而提高钢水的质量及生产效率。
转炉自动化炼钢控制技术的开发及应用是大势所趋,也是高级别品种开发对转炉冶炼过程控制的基本要求。
1、转炉自动化炼钢控制技术简要介绍转炉炼钢是以铁水、废钢、造渣材料、铁合金等为主要原料,通过向炉内供氧,靠铁水本身的物理热和铁水组分间发生化学反应产生热量而在转炉中完成炼钢的过程。
随着炼钢技术的快速发展及各行业对钢铁类产品质量要求的不断提高,传统的单纯依靠人工操作(或简易自动化)和判断的转炉炼钢技术已经难以满足汽车板等高级别品种钢的生产要求,转炉炼钢也需要借助计算机模型计算和自动化控制技术等手段来实现。
自动化炼钢控制技术即在转炉炼钢过程中通过冶炼控制模型的静态及动态计算,借助副枪、音频化渣、烟气分析等检测手段来实现“一键式”冶炼,冶炼过程仅需少量乃至全程无人干预的冶炼控制模式直至终点。
通过自动化炼钢技术可以获得稳定的终点控制,从而提高了钢水的质量,有效提升了生产效率。
2、转炉自动化炼钢控制的优势利用转炉自动化炼钢控制技术,能有效提高转炉终点一次命中率至95%以上;采用副枪技术在冶炼中不提氧枪不停吹的情况下进行过程测量,较传统的人工测量每炉节约时间约3分钟,节约氧气2m3/t;由于减少倒炉次数,可降低钢铁料消耗3Kg/t;在配置音频化渣系统的转炉上,能大幅降低冶炼喷溅率,有效减少由于喷溅可能导致的生产、设备及环保事故。
唐钢转炉炼钢新技术
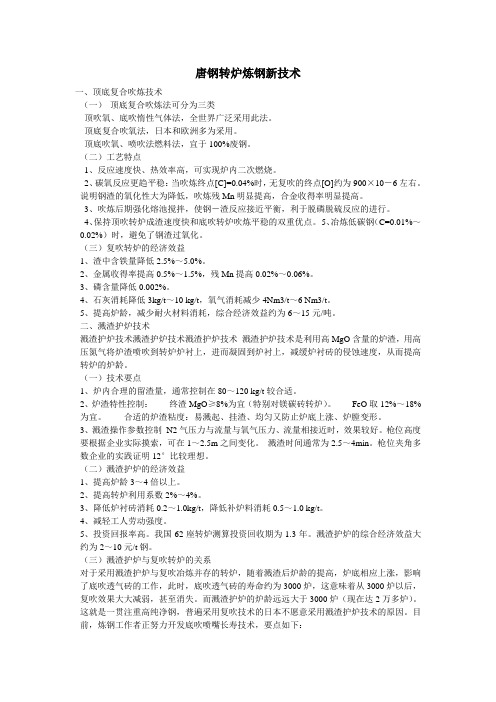
唐钢转炉炼钢新技术一、顶底复合吹炼技术(一)顶底复合吹炼法可分为三类顶吹氧、底吹惰性气体法,全世界广泛采用此法。
顶底复合吹氧法,日本和欧洲多为采用。
顶底吹氧、喷吹法燃料法,宜于100%废钢。
(二)工艺特点1、反应速度快、热效率高,可实现炉内二次燃烧。
2、碳氧反应更趋平稳:当吹炼终点[C]=0.04%时,无复吹的终点[O]约为900×10-6左右。
说明钢渣的氧化性大为降低,吹炼残Mn明显提高,合金收得率明显提高。
3、吹炼后期强化熔池搅拌,使钢-渣反应接近平衡,利于脱磷脱硫反应的进行。
4、保持顶吹转炉成渣速度快和底吹转炉吹炼平稳的双重优点。
5、冶炼低碳钢(C=0.01%~0.02%)时,避免了钢渣过氧化。
(三)复吹转炉的经济效益1、渣中含铁量降低2.5%~5.0%。
2、金属收得率提高0.5%~1.5%,残Mn提高0.02%~0.06%。
3、磷含量降低0.002%。
4、石灰消耗降低3kg/t~10 kg/t,氧气消耗减少4Nm3/t~6 Nm3/t。
5、提高炉龄,减少耐火材料消耗,综合经济效益约为6~15元/吨。
二、溅渣护炉技术溅渣护炉技术溅渣护炉技术溅渣护炉技术溅渣护炉技术是利用高MgO含量的炉渣,用高压氮气将炉渣喷吹到转炉炉衬上,进而凝固到炉衬上,减缓炉衬砖的侵蚀速度,从而提高转炉的炉龄。
(一)技术要点1、炉内合理的留渣量,通常控制在80~120 kg/t较合适。
2、炉渣特性控制:终渣MgO≥8%为宜(特别对镁碳砖转炉)。
FeO取12%~18%为宜。
合适的炉渣粘度:易溅起、挂渣、均匀又防止炉底上涨、炉膛变形。
3、溅渣操作参数控制N2气压力与流量与氧气压力、流量相接近时,效果较好。
枪位高度要根据企业实际摸索,可在1~2.5m之间变化。
溅渣时间通常为2.5~4min。
枪位夹角多数企业的实践证明12°比较理想。
(二)溅渣护炉的经济效益1、提高炉龄3~4倍以上。
2、提高转炉利用系数2%~4%。
转炉负能炼钢与煤气回收技术
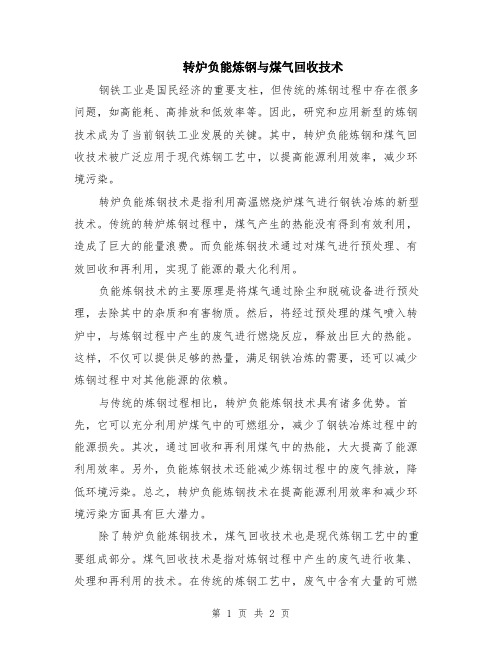
转炉负能炼钢与煤气回收技术钢铁工业是国民经济的重要支柱,但传统的炼钢过程中存在很多问题,如高能耗、高排放和低效率等。
因此,研究和应用新型的炼钢技术成为了当前钢铁工业发展的关键。
其中,转炉负能炼钢和煤气回收技术被广泛应用于现代炼钢工艺中,以提高能源利用效率,减少环境污染。
转炉负能炼钢技术是指利用高温燃烧炉煤气进行钢铁冶炼的新型技术。
传统的转炉炼钢过程中,煤气产生的热能没有得到有效利用,造成了巨大的能量浪费。
而负能炼钢技术通过对煤气进行预处理、有效回收和再利用,实现了能源的最大化利用。
负能炼钢技术的主要原理是将煤气通过除尘和脱硫设备进行预处理,去除其中的杂质和有害物质。
然后,将经过预处理的煤气喷入转炉中,与炼钢过程中产生的废气进行燃烧反应,释放出巨大的热能。
这样,不仅可以提供足够的热量,满足钢铁冶炼的需要,还可以减少炼钢过程中对其他能源的依赖。
与传统的炼钢过程相比,转炉负能炼钢技术具有诸多优势。
首先,它可以充分利用炉煤气中的可燃组分,减少了钢铁冶炼过程中的能源损失。
其次,通过回收和再利用煤气中的热能,大大提高了能源利用效率。
另外,负能炼钢技术还能减少炼钢过程中的废气排放,降低环境污染。
总之,转炉负能炼钢技术在提高能源利用效率和减少环境污染方面具有巨大潜力。
除了转炉负能炼钢技术,煤气回收技术也是现代炼钢工艺中的重要组成部分。
煤气回收技术是指对炼钢过程中产生的废气进行收集、处理和再利用的技术。
在传统的炼钢工艺中,废气中含有大量的可燃物质和热能,没有得到有效利用。
而煤气回收技术通过对废气的处理,可以使其达到清洁排放标准,并回收其中的可燃物质和热能。
煤气回收技术的主要原理是通过收集废气,并进行除尘、脱硫等处理,使之达到环保要求。
然后,将处理后的废气中的可燃物质和热能回收利用,提供给炼钢过程中的各项能源需求。
这样,不仅可以减少对其他能源的依赖,还可以减少废气排放,保护环境。
煤气回收技术的应用对钢铁工业的可持续发展具有重要意义。
转炉底吹氧底喷粉新技术

转炉底吹氧底喷粉新技术
转炉底吹氧底喷粉新技术是一种新型的钢铁冶炼技术,它采用了底吹氧气和底喷粉末的方式,使钢铁冶炼过程更加高效、环保和节能。
传统的钢铁冶炼技术中,常采用顶吹氧气的方式,但这种方式存在着一些问题,如氧气利用率低、炉温不易控制等。
而底吹氧气和底喷粉末的方式则可以有效地解决这些问题。
底吹氧气可以使炉内氧气浓度均匀分布,从而提高氧气利用率,同时还可以使炉内温度更加均匀,有利于钢铁的冶炼。
底喷粉末则可以使炉内的化学反应更加充分,从而提高钢铁的质量和产量。
底吹氧气和底喷粉末的方式还可以减少炉内的氧化物排放,从而达到环保的目的。
同时,由于底吹氧气和底喷粉末的方式可以提高钢铁冶炼的效率,因此也可以节约能源和降低生产成本。
转炉底吹氧底喷粉新技术是一种高效、环保、节能的钢铁冶炼技术,它的应用将会对钢铁行业的发展产生积极的影响。
浅析大型转炉设备新技术
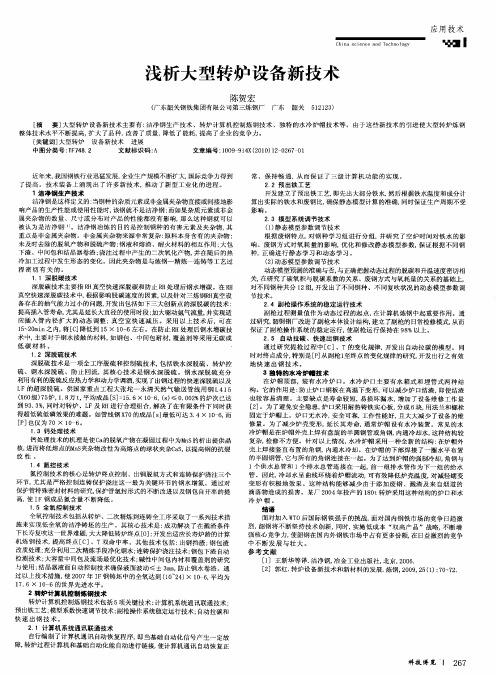
常、 保 持畅 通 , 而 保 证 了三 级 计 算 机 功 能 的实 现 。 从 2 2预 出铁 工艺 开发 建立 了预 出铁 工艺, 即先 出大 部分 铁水, 然后 根据 铁水温 度和 成分 计 算 出实 际 的铁 水和 废钢 比, 确保 静态 模型 计算 的准 确, 同时 保证 生产周 期不 受 影响。 2 3 模 型系 统调 节技 术 . () 态模 型参 数调 节技 术 1静 根 据 废钢 特 点, 对钢 种 学 习组 进行 分 组, 并研 究 了空 炉 时问 对铁 水 的影 响 、废 钢 方 式对 氧 耗量 的影 响 , 化 和修 改静 态 模 型参 数, 证根 据 不 同钢 优 保 种,正确 进 行静 态 学 习和 动 态学 习 。 () 态模 型参数 调节 技术 2动 动态 模型预 测 的准 确与 否, 与正确 把握动 态过程 的脱碳 和升温 速度密切 相 关, 在研 究 了碳氧积 与 脱碳 系数 的关系 、废钢 方式 与氧 耗量 的关 系的基 础上 。 对 不 同钢种 共分 1 组 , 2 开发 出 了不 同钢 种 、不 同复吹 状况 的动 态模 型参数 调 节 技术 。 2 4 副枪操 作 系统 的稳 定运行 技术 . 副枪 过程 测量 值 作为 动态 过程 的起 点 , 在计 算机 炼钢 中起重 要作 用 。通 过研 究I 韶钢钢 厂改进 了副枪 本体设 计结构 , 建立 了副 枪的 日常检修 模式, 从而 保 证 了副枪 操作 系 统 的稳定 运行 , 副 枪运 行保 持在 9 %以上 。 使 8 2 5 自动拉碳 、快速 出钢 技 术 . 通 过 研究 提枪 过 程 中 [ ] C 、T的变 化规 律 , 发 出 自动拉 碳 的模 型 。 同 开 时对 终点 成分, 特别 是 [] 副枪 1 终点 的变 化规律 的研 究, P从 至 开发 出行之 有效 地快速出钢技术 。
炼钢与连铸若干新技术
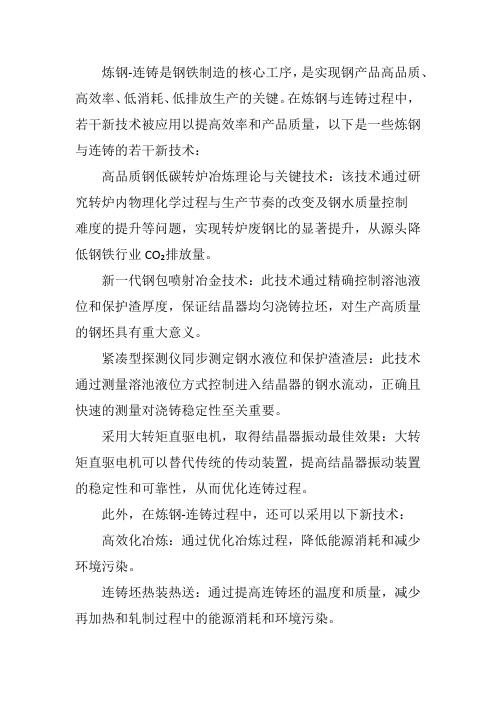
炼钢-连铸是钢铁制造的核心工序,是实现钢产品高品质、高效率、低消耗、低排放生产的关键。
在炼钢与连铸过程中,若干新技术被应用以提高效率和产品质量,以下是一些炼钢与连铸的若干新技术:高品质钢低碳转炉冶炼理论与关键技术:该技术通过研究转炉内物理化学过程与生产节奏的改变及钢水质量控制难度的提升等问题,实现转炉废钢比的显著提升,从源头降低钢铁行业CO₂排放量。
新一代钢包喷射冶金技术:此技术通过精确控制溶池液位和保护渣厚度,保证结晶器均匀浇铸拉坯,对生产高质量的钢坯具有重大意义。
紧凑型探测仪同步测定钢水液位和保护渣渣层:此技术通过测量溶池液位方式控制进入结晶器的钢水流动,正确且快速的测量对浇铸稳定性至关重要。
采用大转矩直驱电机,取得结晶器振动最佳效果:大转矩直驱电机可以替代传统的传动装置,提高结晶器振动装置的稳定性和可靠性,从而优化连铸过程。
此外,在炼钢-连铸过程中,还可以采用以下新技术:高效化冶炼:通过优化冶炼过程,降低能源消耗和减少环境污染。
连铸坯热装热送:通过提高连铸坯的温度和质量,减少再加热和轧制过程中的能源消耗和环境污染。
近终形化生产:通过采用先进的工艺和技术,生产更小断面的连铸坯,提高成材率和生产效率。
精确控制结晶器液面和保护渣厚度:通过精确控制结晶器液面和保护渣厚度,提高连铸坯的质量和稳定性。
电磁搅拌技术:通过采用电磁搅拌技术,改善连铸坯的凝固过程,提高产品质量和生产效率。
自动化的物流系统:通过采用先进的物流系统和技术,实现生产过程中物料的自动化运输和跟踪管理,提高生产效率和产品质量。
高效节能的轧制技术:通过采用高效节能的轧制技术,降低轧钢过程中的能源消耗和提高产品质量。
环保型轧制工艺:通过采用环保型轧制工艺和技术,减少轧钢过程中的环境污染和资源浪费。
集成化工艺控制技术:通过采用集成化工艺控制技术,将炼钢、连铸和轧制等工艺过程进行优化和控制,提高生产效率和产品质量。
这些新技术的应用可以显著提高炼钢-连铸生产的效率和产品质量,同时降低能源消耗和环境污染。
解析转炉炼钢技术的应用及革新途径
工作探索解"转炉炼&技(的应用,革新/0刘冈U(河钢宣钢一钢轧厂,河北张家口075000)摘要:我们国家开展各项工业生产活动的过程中,需要使用到很多钢铁材料,所以铁材料的质量对于整个钢铁企业生产活动有着重要作用。
好的钢铁可以推动炼钢技术的革新和发展,也能在整体上提高炼钢企业的核心竞争实力,所以先对转炉炼钢的技术应用进行分析,之后进一步研究了转炉炼钢技术的革新手段和方法,能炼钢企业的进作用。
关键词:转炉;炼钢;工技术;应用;发展1转炉炼钢技术的相关应用1.1的炼钢技术减少残渣的炼钢技术主要是重复利用脱离了碳元素的残渣,在整个炼钢阶段,因为之前要在炉内进行脱碳这一步骤,于是有较多的炉渣残存下来,但是之前的工艺很难有效的清理掉转炉中的残渣。
而现在,通过新技术来减少残渣,把残渣保留于炉内,直接用于下一次转炉炼钢工作,这是对以往技术的创新和完善。
除此之外,之前的技术手段很难有效地兑铁和高效脱磷,但通过减少残渣的炼钢技术可以有效地对转炉实现脱磷或是脱碳。
1.2尘埃的技术我们国家在转炉炼钢过中要实施中的除:,但是现在是有转炉炼钢以往的除技术,而除技术难以到工作节约能源减少排放的目的。
这年来,我国节约源和的国,以除尘技术有了较的完善,节约能源和减少排放这一前进。
炼钢多的除工艺,这技术是来源于国外,但我们国家实对理用。
1.3阻挡的技术钢铁转炉工作钢到钢这一中,残渣的技术有助于渣减少,通过炼还能进钢中少,磷现,而高钢的除此之外,残渣的技术有于或脱用次的减少,高,了转炉行\的来,转炉炼钢过中残渣的技术需要用,这一要钢口,通过能下渣的外,而实现操控,进一保钢的\1.4脱磷元的炼钢技术下,用多的脱磷是转炉和铁三脱预制结合、双渣%或者转炉双联方法。
而转炉双联主要是指通过两台转炉作行,中一台用于脱磷作,等到脱磷结束之后,将钢铁放在另一台转炉中;而双渣主要是通过一台转炉来完两次造渣工作。
炼钢厂通过对以往炼钢技术进行革新,高了钢数量以及碳量,炼钢厂中整体钢质有高。
转炉炼钢终点控制技术探讨
转炉炼钢终点控制技术探讨转炉炼钢是一种重要的钢铁冶炼技术,终点控制技术是整个炼钢过程中非常重要的环节。
终点控制技术的优劣直接影响钢水的质量和生产成本,因此各个钢铁企业对于炼钢终点控制技术的研究和应用非常重视。
本文将就转炉炼钢终点控制技术进行探讨,分析目前常见的终点控制技术,以及未来的发展趋势。
一、转炉炼钢终点控制技术简介1.1 转炉炼钢的工艺流程转炉炼钢是通过在高炉出产的铁水中直接进行冶炼的工艺,通常采用氧气和其他燃料进行加热,将铁水中的碳和其他杂质物质氧化掉,从而得到纯净的钢水。
转炉炼钢的工艺流程相对比较简单,但是终点控制技术是非常重要的环节,其质量直接关系到最终钢水的品质。
1.2 终点控制技术的重要性终点控制技术是指在转炉炼钢的末端阶段,通过对各种工艺参数的调控,使得钢水的成分、温度和状态满足生产要求的技术。
终点控制技术的好坏直接影响钢水的成分均匀性、温度稳定性和氢氧化物的含量,这些都决定了最终钢水的品质,所以终点控制技术的研究和应用对于提高钢水质量、降低生产成本具有非常重要的意义。
2.1 观察法传统的终点控制技术是通过观察钢水的表面状态、温度和比重等指标,结合生产经验对终点进行判定。
这种方法简单易行,但是受到人员主观因素和钢水状态的影响较大,不能保证终点的准确性。
2.2 化学分析法化学分析法是通过实时监测钢水的成分变化来判断炼钢终点的技术。
目前主要采用的是光谱分析技术,通过对钢水中各种元素的含量进行实时监测和分析,从而判断炼钢终点。
这种方法能够准确地监测钢水的成分变化,但是需要大量的化验设备和人员,成本较高。
2.3 数学模型法数学模型法是通过对炼钢过程中各种参数的变化规律建立数学模型,从而预测炼钢终点。
目前,随着计算机技术的发展,数学模型法在炼钢终点控制技术中得到了广泛的应用。
通过对各种重要参数的变化规律进行建模,可以实时监测炼钢过程中各种指标的变化,从而控制终点。
这种方法能够准确地监测和控制炼钢终点,但是需要大量的数据和计算能力。
转炉炼钢工艺流程NEW
转炉炼钢工艺流程NEW这种炼钢法使用的氧化剂是氧气。
把空气鼓入熔融的生铁里,使杂质硅、锰等氧化。
在氧化的过程中放出大量的热量(含1%的硅可使生铁的温度升高200摄氏度),可使炉内达到足够高的温度。
因此转炉炼钢不需要另外使用燃料。
转炉炼钢是在转炉里进行。
转炉的外形就像个梨,内壁有耐火砖,炉侧有许多小孔(风口),压缩空气从这些小孔里吹炉内,又叫做侧吹转炉。
开始时,转炉处于水平,向内注入1300摄氏度的液态生铁,并加入一定量的生石灰,然后鼓入空气并转动转炉使它直立起来。
这时液态生铁表面剧烈的反应,使铁、硅、锰氧化(FeO,SiO2 , MnO,) 生成炉渣,利用熔化的钢铁与炉渣的对流作用,使反应遍及整个炉内。
几分钟后,当钢液中只剩下少量的硅与锰时,碳开始氧化,生成一氧化碳(放热)使钢液剧烈沸腾。
炉口由于溢出的一氧化炭的燃烧而出现巨大的火焰。
最后,磷也发生氧化并进一步生成磷酸亚铁。
磷酸亚铁再跟生石灰反应生成稳固的磷酸钙与硫化钙,一起成为炉渣。
当磷与硫逐步减少,火焰退落,炉口出现四氧化三铁的褐色蒸汽时,说明钢已炼成。
这时应立即停止鼓风,并把转炉转到水平位置,把钢水倾至钢水包里,再加脱氧剂进行脱氧。
整个过程只需15分钟左右。
假如空气是从炉低吹入,那就是低吹转炉。
随着制氧技术的进展,现在已普遍使用氧气顶吹转炉(也有侧吹转炉)。
这种转炉吹如的是高压工业纯氧,反应更为剧烈,能进一步提高生产效率与钢的质量。
转炉一炉钢的基本冶炼过程。
顶吹转炉冶炼一炉钢的操作过程要紧由下列六步构成:(1)上炉出钢、倒渣,检查炉衬与倾动设备等并进行必要的修补与修理;(2)倾炉,加废钢、兑铁水,摇正炉体(至垂直位置);(3)降枪开吹,同时加入第一批渣料(起初炉内噪声较大,从炉口冒出赤色烟雾,随后喷出暗红的火焰;3~5min后硅锰氧接近结束,碳氧反应逐步猛烈,炉口的火焰变大,亮度随之提高;同时渣料熔化,噪声减弱);(4)3~5min后加入第二批渣料继续吹炼(随吹炼进行钢中碳逐步降低,约12min后火焰微弱,停吹);(5)倒炉,测温、取样,并确定补吹时间或者出钢;(6)出钢,同时(将计算好的合金加入钢包中)进行脱氧合金化。
转炉负能炼钢与煤气回收技术(三篇)
转炉负能炼钢与煤气回收技术1转炉炼钢工序能耗实现负值负能炼钢在转炉内,把铁水炼成钢的过程,主要是降碳、升温、脱磷、脱硫以及脱氧和合金化等高温物理化学反应过程,其工艺操作是控制供氧、造渣、温度及加入合金料等,以获得所要求的钢液并浇铸成钢锭或连铸坯。
氧气顶吹转炉炼钢法的特点之一是不需要外来热源,根据物料和热平衡计算:以铁水的物理热和化学热为主要热收入,抵消金属和炉渣的含热量以及各项热损失外,还有剩余热量。
因此常将废钢、铁矿石和石灰石等作为冷却剂加入炉内以平衡热量防止炉温过高。
1.1炼钢过程的能量消耗炼钢过程需要有足够的能量输入才能完成,通常要消耗电力、氧气、燃气、惰性气体、虚缩空气以及水、蒸汽等。
以宝钢一期工程为例,详见表1。
1.2炼钢过程能量的释放在吹炼过程中,碳氧反应是冶炼过程始终存在的一个重要反应,反应的生成物主要是C0气体(浓度约为85%~90%),但也有少量碳与氧直接作用生成CO2,其化学反应式为2C+O22CO2C+2O22CO22CO+O22CO2在冶炼过程中炉内处于高温,碳氧反应形成的CO气体也称转炉煤气,温度约在1600℃。
此时高温转炉煤气的能量约为1GJ/t,其中煤气显热能约占1/5,其余4/5为潜能(燃烧时转化为热能,不燃烧时为化学能),这就是转炉冶炼过程中释放出的主要能量。
因此,转炉煤气回收利用是炼钢节能降耗的重要途径。
氧气顶吹转炉炼钢过程自台量平衡见图1。
1.3炼钢工序能耗实现负值分析炼钢工序能耗是按生产出每吨合格产品(钢锭或连铸坯)所用的各种能量之和扣除相应回收的能量(标煤)进行计算的。
消耗能量回收能量时,耗能为正值消耗能量-回收能量=0时(称零能炼钢)消耗能量回收能量时,耗能为负值(称负能炼钢)1.4实现负能炼钢是可能的转炉炼钢过程中释放出的能量是以高温煤气为载体,若以热能加以度量分析,具体表现为潜热占83.6%,显热占16.4%,详见图3。
显然,煤气所拥有的能量占总热量中的绝大部分。
- 1、下载文档前请自行甄别文档内容的完整性,平台不提供额外的编辑、内容补充、找答案等附加服务。
- 2、"仅部分预览"的文档,不可在线预览部分如存在完整性等问题,可反馈申请退款(可完整预览的文档不适用该条件!)。
- 3、如文档侵犯您的权益,请联系客服反馈,我们会尽快为您处理(人工客服工作时间:9:00-18:30)。
转炉炼钢的新技术主要是铁水预处理(三脱)、顶底复合吹炼,溅渣护炉与转炉长寿、转炉吹炼自动控制,煤气回收与负能炼钢等。
一、铁水预处理工艺技术
铁水预处理是指将铁水兑人转炉之前进行的各种提纯处理。
可分为普通铁水预处理和特殊铁水预处理。
普通铁水预处理包括:铁水脱硫、脱硅、脱磷的三脱预处理。
特殊铁水预处理是针对铁水中含有特殊元素进行提纯精炼或资源综合利用,如铁水提钒、提铌、脱铬等预处理工艺。
对特殊铁水预处理此不赘述。
1 铁水“三脱“预处理的目的和意义
1。
1 转炉渣量大幅度降低(15~25 kg/t),实现少渣冶炼。
可降低成本、节能、提高钢质量和洁净度。
1.2 脱碳速度加快,终点控制容易,氧效率提高,提高生产率。
1-3 锰的回收率提高,可进行锰矿熔融还原,降低成本。
1.4 转炉煤气成分稳定,煤气回收控制更加容易,以利实现转炉负能炼钢、节能、降成本。
1.5 有利于扩大品种(高碳、高锰钢系列)
2 铁水脱硫工艺技术
铁水脱硫法是指在铁水罐、铁水包、混铁车中进行脱硫。
在高炉、炉外精炼炉和转炉内每脱除1 kg硫的成本分别是铁水脱硫法的2.6倍、6。
1倍、16.9倍,铁水脱硫法的成本低效率高。
2 1 铁水脱硫预处理的工艺方法
投掷法一将脱硫剂投入铁水中。
喷吹法—将脱硫剂喷人铁水中。
搅拌法(KR法)一将通过中空机械搅拌器向铁水内加入脱硫剂,搅拌脱硫。
三种方法的比较见表1。
2。
2 铁水脱硫剂的选择
元素的脱硫能力,由高到低依次为:CaC 、NaO 、Mg、BaO、CaO、MnO MgO
工业中常用的脱硫剂有:CaO系、CaO+CaC 系、CaC 、CaO+Mg 系、Mg系。
几种脱硫剂的特点见表2。
3 铁水脱磷工艺技术
3。
1 铁水脱磷可在四种容器中进行:混铁车同时脱硫脱磷;铁水罐同时脱硫脱磷;铁水包同时脱硫脱磷;转炉铁水脱磷。
3。
2 铁水预处理脱磷反应温度低(1 300℃~1 350℃),热力学条件好,易于脱磷。
铁水中c、si含量高,提高了铁水磷的活度,有利于脱磷。
由于铁水预处理脱磷具备良好的化学热力学条件,渣钢间磷的分配系数是炼钢脱磷的5~10倍,因而渣量小,可以控制较低的渣中Fe0含量,脱磷成本低。
3l3 在氧化条件下,脱磷反应是阳极反应( 一ps++5e),脱硫反应是阴极反应(fS]+2e--~S 之),所以铁水间同时脱磷脱硫是可行的,只是需采用较大脱硫能力
的熔剂。
4 铁水脱硅工艺技术
4。
1 脱硅是脱磷的必要条件,换言之,铁水须先脱硅,然后再同时脱磷脱硫。
脱硅易于减少转炉石灰用量和渣量。
可在低碱度下实现脱硅,成本低。
4。
2 铁水脱硅可在高炉的铁水沟连续进行,分为一段法和两段法,也可在铁水罐脱硅。