转炉炼钢脱磷工艺的探讨
转炉炼钢过程脱磷和吹氧模型的研究
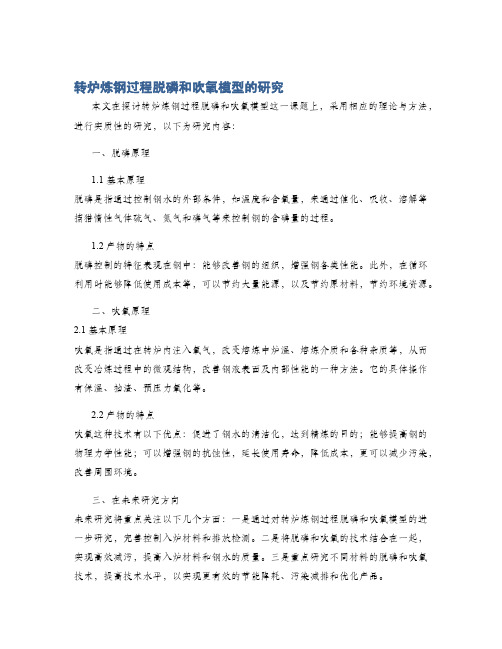
转炉炼钢过程脱磷和吹氧模型的研究
本文在探讨转炉炼钢过程脱磷和吹氧模型这一课题上,采用相应的理论与方法,进行实质性的研究,以下为研究内容:
一、脱磷原理
1.1 基本原理
脱磷是指通过控制钢水的外部条件,如温度和含氧量,来通过催化、吸收、溶解等捕猎惰性气体硫气、氮气和磷气等来控制钢的含磷量的过程。
1.2产物的特点
脱磷控制的特征表现在钢中:能够改善钢的组织,增强钢各类性能。
此外,在循环利用时能够降低使用成本等,可以节约大量能源,以及节约原材料,节约环境资源。
二、吹氧原理
2.1基本原理
吹氧是指通过在转炉内注入氧气,改变熔炼中炉温、熔炼介质和各种杂质等,从而改变冶炼过程中的微观结构,改善钢液表面及内部性能的一种方法。
它的具体操作有保温、抽渣、预压力氧化等。
2.2产物的特点
吹氧这种技术有以下优点:促进了钢水的清洁化,达到精炼的目的;能够提高钢的物理力学性能;可以增强钢的抗蚀性,延长使用寿命,降低成本,更可以减少污染,改善周围环境。
三、在未来研究方向
未来研究将重点关注以下几个方面:一是通过对转炉炼钢过程脱磷和吹氧模型的进一步研究,完善控制入炉材料和排放检测。
二是将脱磷和吹氧的技术结合在一起,实现高效减污,提高入炉材料和钢水的质量。
三是重点研究不同材料的脱磷和吹氧技术,提高技术水平,以实现更有效的节能降耗、污染减排和优化产品。
转炉炼钢流程中的脱磷工艺
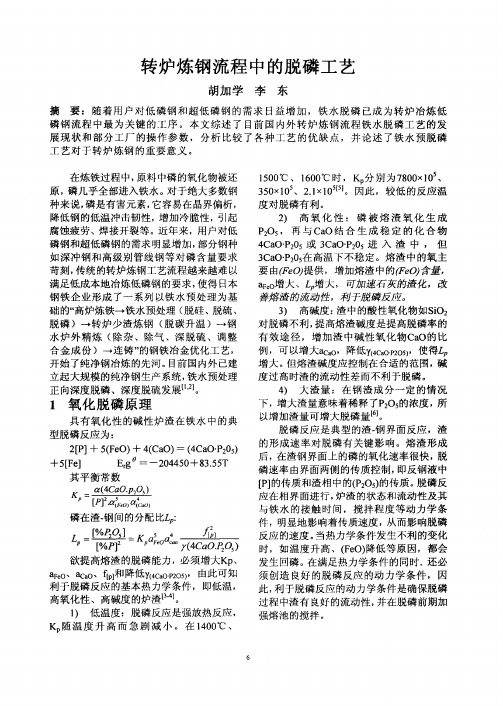
磷 在渣. %P
:
a ̄
7 C . ・ y4 a Q ) ( OP 0 2
欲提 高熔 渣 的脱磷 能力 ,必须增 大K 、 p ae、aa、f]口 F 0 co t 降低1 C .O) 由止 可 失 p , P 5 ( O2 , 4 匕 l J 利 于脱磷 反应 的基 本热 力学 条件 , 即低温 , 高 氧化 性 、高碱度 的炉 渣 【 3 。 1 低温 度 :脱磷 反应 是强 放热 反应 , ) KD 温 度 升 高 而 急 剧 减 小 。 在 10  ̄ 随 4 0C、
3 高碱 度 : 中的酸 性氧化 物如 SO2 ) 渣 i 对脱 磷 不利 , 高熔渣 碱 度是 提 高脱磷 率 的 提 有 效 途 径 ,增 加 渣 中 碱 性氧 化物 C O的 比 a 例 ,可 以增大 a ,降低 丫CO 25 co (a.o) 4 P ,使得三 p 增 大 。 熔渣碱 度 应控 制在 合适 的范 围 , 但 碱 度过 高 时渣 的流 动性差 而 不利 于脱磷 。 4 大 渣 量 :在 钢渣 成 分 一 定 的情 况 ) 下 ,增 大渣 量意 味着稀 释 了P05 2 的浓度 , 所 以增 加渣 量 可增 大脱磷 量 【。 o J 脱 磷 反应 是 典型 的渣 界 面 反应 ,渣 钢 的形 成 速 率对 脱 磷 有 关 键影 响 。熔 渣 形成 后 ,在渣 钢 界面上 的磷 的氧 化速 率很 快 , 脱 磷速 率 由界 面两侧 的传 质控 制 , 即反钢 液 中 【] P 的传 质 和渣相 中 的(2 ) Po5的传质 。 磷反 脱 应 在相 界面 进 行 , 炉渣 的状 态和 流动 性及其 与 铁 水 的接触 时 间 ,搅 拌程 度 等 动 力 学条 件 ,明显地 影响着 传质 速度 , 从而 影 响脱磷 反应 的速度 。 当热 力学条 件 发生 不利 的变化 时 ,如温 度升 高 、(e ) F O 降低 等原 因,都会 发 生 回磷 。在满足 热力 学条 件 的 同时 . 还必 须 创 造 良好 的脱 磷 反 应 的动 力 学 条 件 , 因 此 , 于脱 磷 反应 的动力 学 条件 是确 保脱磷 利 过 程 中渣 有 良好 的流 动性 , 并在 脱磷 前期加 强熔 池 的搅 拌 。
铁水转炉吹氧脱磷工艺-概述说明以及解释

铁水转炉吹氧脱磷工艺-概述说明以及解释1.引言1.1 概述铁水转炉吹氧脱磷工艺是钢铁生产中常用的一种去除磷元素的工艺方法。
在铁水中磷元素的含量对钢铁的性能有着重要影响,因此需要采取相应措施进行去除。
吹氧脱磷工艺通过向铁水中吹入氧气,利用氧气与磷元素的化学反应,在高温条件下将磷元素氧化移除,从而减少磷元素含量,提高钢铁的质量和性能。
本文将详细介绍铁水转炉吹氧脱磷工艺的原理、步骤以及其在钢铁生产中的应用。
通过对该工艺的深入探讨,可以更好地了解吹氧脱磷的作用机制和优势,为钢铁生产提供技术支持和参考。
1.2 文章结构1.3 目的本文旨在深入探讨铁水转炉吹氧脱磷工艺,通过对该工艺的原理、步骤、优势以及应用前景进行分析,旨在说明吹氧脱磷工艺在钢铁生产中的重要性和价值。
同时,通过总结工艺的特点和优势,为相关行业提供参考,促进该工艺的广泛应用,提高生产效率,降低成本,推动钢铁行业的可持续发展。
2.正文2.1 铁水转炉工艺概述:铁水转炉是一种用于炼钢的高炉,它是一种旋转的容器,通常由耐火材料和金属外壳构成。
在钢铁冶炼过程中,铁水转炉扮演着至关重要的角色。
铁水转炉工艺通常用于生产高品质的钢铁,其主要特点是操作简单,生产效率高,并能够满足不同规格和质量要求的钢铁生产。
在铁水转炉中,主要通过向铁水中吹入氧气使其氧化,从而提高炉内温度,促使不同元素的相互作用,达到脱除杂质的目的。
铁水转炉通常配有各种喷嘴和氧气喷嘴,以确保充分的氧化反应和高效的燃烧过程。
铁水转炉工艺的优点包括:1. 生产效率高:铁水转炉可以持续生产,操作简单,生产效率高。
2. 能够生产高品质钢铁:通过吹氧脱磷等工艺,可以去除杂质,生产高品质的钢铁。
3. 适用范围广:铁水转炉可以生产各种规格和质量要求的钢铁,适用性广泛。
总的来说,铁水转炉工艺在钢铁冶炼领域具有重要的地位,其优点包括高效、高质以及适用范围广泛,为钢铁行业的发展做出了重要贡献。
2.2 吹氧脱磷的原理2.3 吹氧脱磷的步骤:吹氧脱磷是铁水转炉炼钢过程中的关键环节之一,其步骤主要包括以下几个方面:1. 吹氧开始: 在铁水转炉底部喷入高纯度氧气,形成氧吹。
转炉脱磷造渣工艺
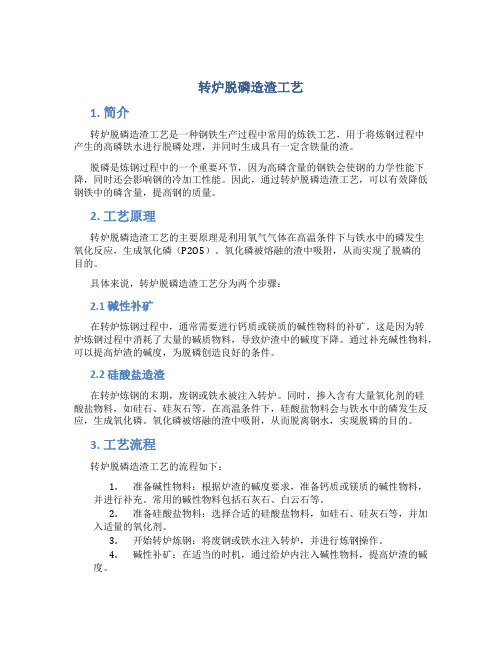
转炉脱磷造渣工艺1. 简介转炉脱磷造渣工艺是一种钢铁生产过程中常用的炼铁工艺,用于将炼钢过程中产生的高磷铁水进行脱磷处理,并同时生成具有一定含铁量的渣。
脱磷是炼钢过程中的一个重要环节,因为高磷含量的钢铁会使钢的力学性能下降,同时还会影响钢的冷加工性能。
因此,通过转炉脱磷造渣工艺,可以有效降低钢铁中的磷含量,提高钢的质量。
2. 工艺原理转炉脱磷造渣工艺的主要原理是利用氧气气体在高温条件下与铁水中的磷发生氧化反应,生成氧化磷(P2O5)。
氧化磷被熔融的渣中吸附,从而实现了脱磷的目的。
具体来说,转炉脱磷造渣工艺分为两个步骤:2.1 碱性补矿在转炉炼钢过程中,通常需要进行钙质或镁质的碱性物料的补矿。
这是因为转炉炼钢过程中消耗了大量的碱质物料,导致炉渣中的碱度下降。
通过补充碱性物料,可以提高炉渣的碱度,为脱磷创造良好的条件。
2.2 硅酸盐造渣在转炉炼钢的末期,废钢或铁水被注入转炉。
同时,掺入含有大量氧化剂的硅酸盐物料,如硅石、硅灰石等。
在高温条件下,硅酸盐物料会与铁水中的磷发生反应,生成氧化磷。
氧化磷被熔融的渣中吸附,从而脱离钢水,实现脱磷的目的。
3. 工艺流程转炉脱磷造渣工艺的流程如下:1.准备碱性物料:根据炉渣的碱度要求,准备钙质或镁质的碱性物料,并进行补充。
常用的碱性物料包括石灰石、白云石等。
2.准备硅酸盐物料:选择合适的硅酸盐物料,如硅石、硅灰石等,并加入适量的氧化剂。
3.开始转炉炼钢:将废钢或铁水注入转炉,并进行炼钢操作。
4.碱性补矿:在适当的时机,通过给炉内注入碱性物料,提高炉渣的碱度。
5.硅酸盐造渣:当转炉炼钢接近末期时,通过给炉内注入硅酸盐物料,利用氧化剂促进磷的氧化反应。
6.淋渣:根据炉内的渣情况,选择合适的时间进行淋渣操作。
淋渣可以通过人工或机械设备进行。
7.渣铁分离:在脱磷过程中,渣中生成的氧化磷会被吸附在渣中,从而脱离钢水。
通过合适的方法,将渣与钢水分离。
8.尾渣处理:处理分离出来的尾渣,并对其进行资源化利用或安全处理。
氧气转炉炼钢的脱磷问题

20
炼铁技术由中东向欧州南部传播
21
埃及古墓墙上的图画
大约公元前1500年
22
16世纪时的木炭炼铁炉 世纪时的木炭炼铁炉
18世纪时的鼓风炼铁炉 世纪时的鼓风炼铁炉
19世纪初时的炼铁炉 世纪初时的炼铁炉
空气底吹炼钢转炉诞生
H.Bessemer(1856), W.Kelly(1857) H.Bessemer(1856), W.Kelly(1857)
铸造生铁可用于生产铸管、机床等设备底座等; 铸造生铁可用于生产铸管、机床等设备底座等; 硬而脆,几乎没有塑性,不能进行轧制、 硬而脆,几乎没有塑性,不能进行轧制、锻压 等塑性变形加工。 等塑性变形加工。
钢材: 钢材:
具有良好塑性,能够进行轧制、锻压、 具有良好塑性,能够进行轧制、锻压、拉拔等 塑性变形加工; 塑性变形加工; 钢制品具有强度高、韧性好、易焊接、耐高温、 钢制品具有强度高、韧性好、易焊接、耐高温、 耐腐蚀等优良特性,因此被广泛利用。 耐腐蚀等优良特性,因此被广泛利用。
成渣较底吹转炉好; 成渣较底吹转炉好; 搅拌较顶吹转炉强; 搅拌较顶吹转炉强; 反应平衡程度高; 反应平衡程度高; 大多数大中型转炉采用了 复吹转炉炼钢。 复吹转炉炼钢。
32Leabharlann 底吹搅拌强度33氧气转炉炼钢主要设备
烟气净化 系统
渣料系统 氧枪系统
主原料装入系统
倾动系统
出钢、 出钢、出渣系统
34
35
3
生铁与钢的成分差别
元素 C P S Si Mn Cr Ni Mo Nb, Nb,V,Ti 生铁 3.5~5.0% 3.5~5.0% 0.06 1.50% 0.06~1.50% 0.015~0.06% 0.015~0.06% 0.25~1.20% 0.25~ 0.25~0.60 0.25~0.60% 钢 0.001~1.2% 0.001~1.2% 0.002~0.04 0.002~0.04% 0.0005~0.04% 0.0005~0.04% 0.01~6.5% 0.01~6.5% 0.12~13.0% 0.12~13.0% ~18% 18% ~10% 10% ~2% ~0.2% 0.2%
精选转炉脱磷少渣炼钢工艺技术发展与现
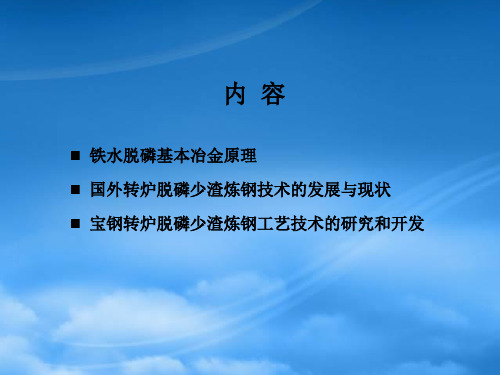
(1) (2)
2[P]+8(FeO)=(3FeO•P2O5)+5Fe
(3)
由于在1400~1600℃时,(3FeO•P2O5)不稳定,为了有效脱磷,则必 须使渣中磷在高碱度下生成更稳定的化合物(4CaO•P2O5),即发生 置换反应:
(3FeO•P2O5)+4(CaO)=(4CaO•P2O5)+3(FeO)
项目
脱磷炉
脱碳炉
炉容量 顶吹氧 底吹搅拌气体及底吹强度
熔剂成分及用量 处理时间 铁水成分
250 t
1.0~1.3 Nm3/t.min CO2: 0.05~0.20
Nm3/t.min 转炉渣-铁矿-石灰-萤石:
30~60 kg/t 8~10 min Si:0.2~0.57 % P:0.090~0.128 %
内容
铁水脱磷基本冶金原理 国外转炉脱磷少渣炼钢技术的发展与现状 宝钢转炉脱磷少渣炼钢工艺技术的研究和开发
铁水脱磷基本冶金原理
第一部分 铁水脱磷基本冶金原理
铁水在氧化性渣下的脱磷反应可表述如下:
2[P]+5(FeO)=(P2O5)+5Fe 3(FeO)+(P2O5)=(3FeO•P2O5) (1)式+(2)式:
铁水包喷吹 脱磷脱硫
铁水包 扒渣
复吹转炉 (LD-OB)
国外转炉脱磷少渣炼钢技术的发展与现状
ORP-M工艺要点
采用混铁车内脱硅,铁水包内脱磷脱硫。 脱硅处理是采用两根喷枪向混铁车铁水喷入CaO、FeO和O2,铁水
[Si]由0.35%降至0.10%; 脱硅铁水倒入铁水包,铁水包吊放置于转盘上(有4个处理工作位
(4)
铁水脱磷基本冶金原理
(3)式+(4)式: 2[P]+5(FeO)+ 4(CaO)=(4CaO•P2O5)+5Fe
顶吹转炉脱磷热力学分析和工艺优化
顶吹转炉脱磷热力学分析和工艺优化磷在大多数钢中都是有害元素,脱磷是转炉炼钢的主要任务,本文从热力学角度入手,分析了顶吹转炉炼钢脱磷的影响因素,提出了优化转炉脱磷的措施,对强化顶吹转炉炼钢脱磷、提高钢材质量有重要意义。
标签:顶吹转炉;脱磷;措施1 前言磷在钢中(除炮弹钢、耐蚀钢以外)是有害元素,易使钢发生“冷脆”现象,尤其在高碳钢中更是明显,其原因是由于磷元素富集在铁素体晶界上形成“固溶强化”的作用,造成晶粒间的强度提高,从而产生脆性。
除此之外,磷含量越高越容易在结晶边界析出磷化物,降低钢的冲击值[2]。
因此,控制顶吹转炉炼钢过程中的脱磷反应是控制回磷和提高钢材质量重要而复杂的工作。
2 脱磷的热力学分析2.1 温度由上可知,温度越高。
K值越小,因此,低温对脱磷有利。
但需要指出的是,提高熔池温度,会使磷的分配比降低,对磷从金属向炉渣的转移不利。
但温度升高降低了炉渣的粘度,加速了石灰的熔解,从而有利于磷从金属向炉渣的转移。
理论研究表明,最有效的脱磷有一个最佳的温度范围(1450~1500℃)。
这就要求冶炼初期,要根据铁水温度采用不同的操作制度。
铁水温度低(1250℃以下),要采用低枪位操作以提高熔池温度,加速石灰的熔解,迅速形成初期渣,充分利用前期炉渣FeO高、炉温低的优势,快速脱磷。
若铁水温度特别高(大于1350℃),冶炼初期要适当采用高枪位操作,并加入部分矿石,抑制炉温的快速升高,同时也有利于石狄的溶解,延长冶炼在低温区(1500℃以下)的运行时间。
实践证明,尽管冶炼终点温度高,会降低磷在钢一渣中的分配比,但脱磷的关键仍然是冶炼过程渣特别是终渣的控制。
也就是说温度的影响不如(FeO)和(Cao)显著。
2.2 炉渣碱度因为CaO是使aP205降低的主要因素,增加(CaO)达到饱和含量可以增大aCa0,亦即增加自由CaO(不与酸性氧化物结合)的浓度,会使(P205)提高或鋼中[P]降低。
但渣中(CaO)过高,将使炉渣变稠,同样不利于脱磷。
转炉炼钢脱磷工艺理论与实践
转炉炼钢脱磷工艺理论与实践摘要:中国的钢铁生产领先于世界,现在正是处在从钢铁大国到强国的高速发展阶段,许多炼钢技术在国际上拥有领头地位。
判断钢铁品质好坏关键指标就是其中的磷含量。
脱磷效果是否良好决定了产钢是否符合标准。
本文主要介绍转炉炼钢厂脱磷工艺的原理,并融合炼钢实际操作对脱磷工艺中的注意事项进行详细介绍。
关键词:转炉炼钢;磷含量;炉外脱磷前言:全球使用范围最广的金属材料就是钢铁,是现代建筑不可或缺的生产材料。
钢材加工有冷热加工两种,按照途可将钢铁分为结构钢,工具钢,特种钢,专业钢等,加工方法。
因为生产方式的多样化就对非金属元素的要求非常严格,其中主要为磷元素,它的含量是钢材质量是否达标的重要指标。
恰当的磷含量能增加钢的强性,但对于大部分的钢来说,磷都是一个有危害的元素,高磷量会使钢的可塑性减弱,可焊性和冲击韧性变低。
有研究表明,在钢水凝固过程中,磷的偏析集中在晶界,从而引起钢在低温环境下的脆性,将这种现象叫做“冷脆” 。
磷含量对钢的影响是如此之大,以至于即使极少的磷(0.01%)也会引发钢的低温脆性。
所以要求普通钢的磷含量小于0.04%。
像寒冷地区的钻井平台,船舶,钢轨,钢制轴承零件,液化气管道等要求钢的磷含量应小于0.03%。
脱磷反应是转炉炼钢过程中重要的物理化学反应,也是转炉炼钢的基本任务之一。
本文依据最常用的转炉炼钢工艺介绍脱磷工艺原理,并与实际情况相融合表明脱磷工艺中的注意事项。
1磷的来源与存在形式铁矿石含大量磷,磷在高炉炼铁中几乎都进到了铁水里,铁水中磷的含量和铁矿石中磷的含量成正比,冶炼的生铁中磷含量可达2.0%以上。
此外,在炼钢过程中加入铁合金也会带来许多磷。
磷在铁水中大多以元素形式存在,一小部分为磷化物。
2 转炉炼钢脱磷原理与条件2.1 转炉炼钢脱磷原理在转炉吹炼过程中,铁水中的磷被氧化成P2O5变成炉渣。
P2O5是一种酸性含氧物质,能和炉渣中的碱性含氧物质FeO、CaO、MnO、MgO等形成磷酸盐化合物。
转炉炼钢脱磷工艺理论与实践
转炉炼钢脱磷工艺理论与实践摘要:适当的磷可以提升钢的强度,但是对于大多数的钢种都是有害元素,磷含量过高会降低钢材的塑性、焊接性以及冲击韧性。
研究表明磷在钢液凝固过程中发生偏析现象比较集中地聚集在晶界处,导致较低温度下钢材性能变脆,通常成为“冷脆”现象。
磷含量对钢铁的影响极大,即使很少量的磷(0.01%)也会导致钢材的低温脆性。
因此对于普通的钢种磷含量要求在0.04%以内,在低温环境下应用的钢种要求含磷低到0.003%以下,如严寒地区的钻井平台、船舶、轨道、钢结构承重件、液化气管道等。
脱磷反应是转炉炼钢过程重要的物理化学反应,也是转炉炼钢的基本任务之一。
结合实践进行说明脱磷过程注意事项。
关键词:转炉炼;钢脱磷;工艺1转炉炼钢脱磷原理与条件1.1转炉炼钢脱磷原理转炉吹炼过程铁水中的磷被氧化生成P2O5进入炉渣中,P2O5是酸性氧化物,能与炉渣中的碱性氧化物FeO、CaO、MnO、MgO等生成磷酸盐化合物,更稳定的存在渣中,随炉渣一起除掉。
炉渣碱度较低时磷多以磷酸铁(3FeO•P2O5)的形式存在,炉渣碱度较高时磷多以磷酸钙(3CaO•P2O5或4CaO•P2O5)的形式存在。
1.1.1磷的氧化反应磷的氧化反应在钢—渣界面上进行,反应方程式一般有2种:4/5[P]+2[O]=2/5(P2O5)标准吉布斯能△Gθ=-384953+170.24T(J/mol)。
或者:4/5[P]+2(FeO)=2/5(P2O5)+2Fe(l)标准吉布斯能△Gθ=-142944+65.48T(J/mol)。
1.1.2P2O5在炉渣中的固定氧化生成的P2O5如要在渣中稳定存于炉渣中,必须与炉渣中的CaO等碱性氧化物反应生成稳定的磷酸盐化合物3CaO•P2O5或4CaO•P2O5,反应方程式为:2[P]+5[O]+3(CaO)=(3CaO•P2O5)标准吉布斯能△Gθ=-1486160+6360T。
由反应方程式可以看出,转炉炼钢脱磷原理在于磷的氧化进入渣中和转化为稳定的磷酸盐,脱磷速度主要取决于钢—渣界面磷的氧化反应。
转炉炼钢脱磷工艺分析
II
第三章 试验方案的设计.............................................................................................................. 27 3.1 沙钢双渣脱磷的现状........................................................................................................ 27 3.1.1 双渣操作的好处......................................................................................................... 27 3.1.2 沙钢双渣脱磷情况.....................................................................................................27 3.1.3 脱磷的效果及回磷问题............................................................................................ 28 3.2 目前存在的问题................................................................................................................. 29 3.2.1 前期脱磷结果............................................................................................................. 29 3.3 影响前期脱磷的主要因素............................................................................................... 30 3.3.1 钢水中硅的氧化......................................................................................................... 30 3.3.2 前期渣碱度的控制.....................................................................................................30 3.3.3 倒前期渣时间的控制................................................................................................ 31 3.4 180t 转炉冶炼终点脱磷情况.......................................................................................... 32 3.4.1 增碳剂加入量的控制................................................................................................ 32 3.4.2 冶炼终点脱磷情况.....................................................................................................32 3.5 180t 转炉冶炼工艺改进方案.......................................................................................... 32 3.5.1 冶炼前期控制............................................................................................................. 33 3.5.2 冶炼终点控制............................................................................................................. 33 结论..............................................................................................................................................35 参考文献..................................................................................................................................... 36 致 谢....................................................................................................................................... 37
- 1、下载文档前请自行甄别文档内容的完整性,平台不提供额外的编辑、内容补充、找答案等附加服务。
- 2、"仅部分预览"的文档,不可在线预览部分如存在完整性等问题,可反馈申请退款(可完整预览的文档不适用该条件!)。
- 3、如文档侵犯您的权益,请联系客服反馈,我们会尽快为您处理(人工客服工作时间:9:00-18:30)。
转炉炼钢脱磷工艺的探讨
【摘要】本文从脱磷的热力学分析入手,对冶炼过程中温度、炉渣碱度、渣中(FeO),等对磷含量的影响进行了探讨。
同时探讨了回磷的原因、影响的因素和防止的措施。
【关键词】转炉炼钢;脱磷工艺;探讨
磷在钢中是以【Fe3P】或【Fe2P】形式存在,一般以【P】表示。
磷含量高时,会使钢的朔性和韧性降低,即使钢的脆性增加,这种现象低温时更严重,通常把它称为“冷脆”。
且这种影响常常随着氧,氮含量的增加而加剧。
磷在连铸坯中的偏析仅次于硫,同时它在铁固溶体中扩散速度又很小。
不容易均匀化,因而磷的偏析和难消除。
由于炼铁过程为还原性气氛,脱磷能力较差。
因此脱磷是炼钢过程的重要任务之一。
在20世纪90年代中后期,为解决超低磷钢的生产难题,世界上各大钢厂都曾经进行过转炉铁水脱磷实验研究。
1、铁水预处理方法
1.1喷吹苏打粉处理
日本住友公司鹿岛厂开发的“住友碱精炼法”是成功用于工业生产的苏打精炼法。
工艺流程:从高炉流出的铁水先经脱硅处理,即将高炉铁水注入混铁车内,用氮气输送和喷吹烧结矿粉,喷入量为每吨铁水40公斤,最大供粉速度为每分钟400公斤,最大吹氧量为每分钟50立方米,脱硅量约为0.4%。
脱硅处理后的铁水硅含量可降到0.1%以下。
然后用真空吸渣器吸出脱硅渣,进行脱磷处理,以氮气为载气向铁水中喷入苏打粉,苏打粉用量为每吨18公斤,最大供粉量为每分钟250公斤,最大吹氧量为每分钟50立方米,处理后铁水中【P】≤0.001%,【S】≤0.003%,再用真空吸渣器吸出脱磷渣,并将其送到苏打回收车间,经水浸后可回收约80%的Na2O,最后将处理过的铁水倒入转炉冶炼。
1.2喷吹石灰系熔剂处理
由于石灰系熔剂具有成本低,对环境污染小的优点,因此受到重视,并不断对其深入研究,以使其满足精炼铁水的需要。
工艺流程:向高炉铁沟中加入铁磷进行脱硅处理,加入量为每吨铁水27公斤,处理后铁水含硅量由0.5%降到0.15%,氧的利用率为80%-90%。
脱硅后的铁水流入混铁车中,并与混铁车内上一炉脱磷脱硫渣混合,待渣与铁分离后扒渣。
然后,向混铁车内铁水中用氮气为载气体,流量为每分钟为3-5立方米,喷入石灰熔剂。
处理后温度为13500C左右,处理时间25分钟。
将处理后的铁水倒入转炉,在转炉内进一步脱磷,可使钢中【P】≤0.001%。
2、转炉冶炼过程中脱磷
2.1氧化脱磷
磷在钢液中能够无限溶解,。
而它的氧化物P2O5在钢液的溶解度却很小,因此,要除去钢中的磷,可设法使磷氧化生成P2O5进入炉渣,并固定在渣中。
炼钢过程中的脱磷反应在渣—钢界面和氧气顶吹转炉的乳浊液中,是被渣中FeO 氧化,其反应为:
2【P】+5(FeO)= (P2O5)+5【Fe】
△G0=-1495194+684.92T(J/mol)
生成的P2O5的密度较小,几乎不溶于钢液,所以一旦生成即上浮转入渣相。
但由于冶炼初期渣中较多的碱性氧化物是FeO,因此进入炉渣的P2O5仅和FeO 结合成磷酸铁盐。
其反应:
(P2O5)+3(FeO)=(3FeO·P2O5)
△H0=-128030J/mol
根据生成焓△H0判断,渣中(P2O5),(3FeO·P2O5)却不稳定,它们在炼钢过程中随着熔池温度的不断升高而逐渐分解,使磷又回到钢液之中。
所以在炼钢温度下,以氧化铁为主的炉渣脱磷能力很低。
为了使脱磷过程进行得比较彻底,防止已被氧化的磷大量返回钢液,目前大多工厂的做法是向熔池加入一定量的石灰,增加渣中强碱性氧化物CaO的含量,使五氧化二磷和氧化钙生成较稳定的磷酸钙,从而提高炉渣的脱磷能力。
在生产中,随着石灰的变化,炉渣的碱度会逐渐升高,渣中的游离的CaO逐渐增加,此时将发生置换反应:
即:(3FeO·P2O5)+4(CaO)=(4CaO·P2O5)+5【Fe】
所以,碱性氧化渣脱磷的总反应为:
2【P】+5(FeO)+4(CaO)=(4CaO·P2O5)+5【Fe】
转炉冶炼过程中低碳低磷铁水转炉去磷率达到90%以上。
2.1.1影响炉渣脱磷的主要因素:(1)炉渣成分的影响:炉渣成分对脱磷反应的影响主要反应在渣中的FeO含量和炉渣碱度上。
渣中的FeO是脱磷的首要条件,如果渣中没有氧化铁或氧化铁含量很低,就不可能使磷氧化。
但是,纯氧化铁炉渣只有很小的去磷效果,因为渣中(3FeO·P2O5)在高温下不稳定,它会分解或被硅、锰还原,而渣中(4CaO·P2O5)在17100c的温度下比较稳定,即炼钢温度下它分解的可能性不大,所以CaO是脱磷的必要条件;(2)温度的影响:脱磷反应是强放热反应,升高温度会使其平衡常数的数值减小,去除效率下降。
从热力学条件来看,降低温度有利于去P反应进行,但是应该辩证地看待温度的影响,尽管升高温度会使反应的平衡常数K值减少,然而与此同时较高的温度能使炉渣的粘度下降,加速石灰的成渣速度和渣中各组元的扩散速度,强化了磷从金属液向炉渣的转移。
其影响可能超过Kp值得降低,温度过高时,Kp值的下降起主导作用,会使炉渣的去P效率下降。
钢中的磷含量回升;(3)炉渣粘度的影响:炼钢熔池中的脱P反应主要是在炉渣与金属液两相的界面上进行的,所以反应速度与炉渣粘度有关。
通常情况下,炉渣粘度越低,渣中反应物FeO向渣—钢界面的扩散转移速度就越快,渣中反应产物P2O5离开界面溶入炉渣的速度也就越快。
因此,在脱P要求的高碱度条件下,应及时加入稀渣剂改善炉渣的流动性,以促进脱P反应的顺利进行;(4)渣量的影响:随着脱磷反应的进行,渣中P2O5的含量不断升高,炉渣脱P能力逐渐下降。
在一定条件下,增大渣量必然会使渣中的P2O5含量降低,破坏磷在钢—渣间分配的平衡性,促进脱磷反应的继续进行,使钢中的磷含量进一步降低。
所以炉内渣量的多少决定着钢液的脱磷程度。
但渣量过大,会使钢液面上渣层过厚而减慢去磷速度,同时还压抑了钢液的沸腾,使气体及夹杂物的排除受到影响。
2.2回磷
2.2.1产生回磷的原因:冶炼终点一般被认为脱P 反应达到平衡,在出钢过程向钢包加入脱氧剂,将使使钢中的氧以及渣中(FeO)下降,脱氧产物(SiO2),(Al2O3)等进入炉渣,使炉渣碱度降低,从而打破了脱磷反应的平衡状态,有利于(P2O5)的分解和还原,磷又重新进入钢液。
2.2.2影响回磷的因素:(1)出钢过程中下渣是磷的主要原因。
下渣量大,回磷严重;(2)出钢合金化或增碳操作不合理。
如出钢后期补加硅铁,碳化硅,碳粉等;(3)吹氩时,使用氩气压力过高,造成钢液-炉渣翻腾,卷渣,也会增加回磷。
2.2.3防止回磷的措施:要防止钢水会磷,首先是挡好渣,减少出钢过程的下渣量。
其次是严格出钢合金化操作,杜绝出钢后补加合金。
再次出钢时向钢包内投入少量小块石灰以提高钢包内渣层的碱度,稠化炉渣,降低炉渣的反应能力,阻止钢渣接触时发生回磷反应。
3、结束语
转炉脱磷工艺在各国冶金工作者的努力下不断地发展,同时适合转炉脱磷工艺的新型脱磷剂也在研究与发展中,随着世界转炉炼钢技术的发展及炼钢设备的多样化,使传统的转炉炼钢过程逐步转向单一化,这样不仅可以提高钢水的质量,缩短转炉冶炼周期,降低原材料消耗和能耗,而且有利于冶炼过程的控制和管理,更好发挥转炉脱磷工艺的优点。
做好这些就有利于我国目前进行技术改进,提高钢水纯净度,更好的优化钢铁冶炼工艺水平。