转炉炼钢脱磷工艺的探讨
转炉炼钢流程中的脱磷工艺
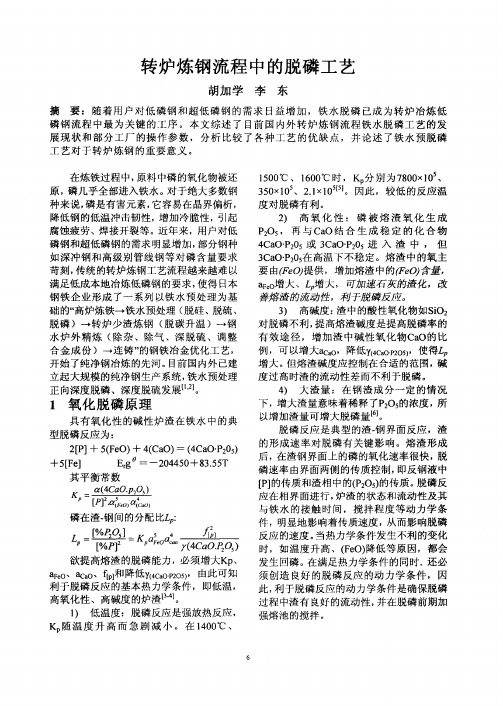
磷 在渣. %P
:
a ̄
7 C . ・ y4 a Q ) ( OP 0 2
欲提 高熔 渣 的脱磷 能力 ,必须增 大K 、 p ae、aa、f]口 F 0 co t 降低1 C .O) 由止 可 失 p , P 5 ( O2 , 4 匕 l J 利 于脱磷 反应 的基 本热 力学 条件 , 即低温 , 高 氧化 性 、高碱度 的炉 渣 【 3 。 1 低温 度 :脱磷 反应 是强 放热 反应 , ) KD 温 度 升 高 而 急 剧 减 小 。 在 10  ̄ 随 4 0C、
3 高碱 度 : 中的酸 性氧化 物如 SO2 ) 渣 i 对脱 磷 不利 , 高熔渣 碱 度是 提 高脱磷 率 的 提 有 效 途 径 ,增 加 渣 中 碱 性氧 化物 C O的 比 a 例 ,可 以增大 a ,降低 丫CO 25 co (a.o) 4 P ,使得三 p 增 大 。 熔渣碱 度 应控 制在 合适 的范 围 , 但 碱 度过 高 时渣 的流 动性差 而 不利 于脱磷 。 4 大 渣 量 :在 钢渣 成 分 一 定 的情 况 ) 下 ,增 大渣 量意 味着稀 释 了P05 2 的浓度 , 所 以增 加渣 量 可增 大脱磷 量 【。 o J 脱 磷 反应 是 典型 的渣 界 面 反应 ,渣 钢 的形 成 速 率对 脱 磷 有 关 键影 响 。熔 渣 形成 后 ,在渣 钢 界面上 的磷 的氧 化速 率很 快 , 脱 磷速 率 由界 面两侧 的传 质控 制 , 即反钢 液 中 【] P 的传 质 和渣相 中 的(2 ) Po5的传质 。 磷反 脱 应 在相 界面 进 行 , 炉渣 的状 态和 流动 性及其 与 铁 水 的接触 时 间 ,搅 拌程 度 等 动 力 学条 件 ,明显地 影响着 传质 速度 , 从而 影 响脱磷 反应 的速度 。 当热 力学条 件 发生 不利 的变化 时 ,如温 度升 高 、(e ) F O 降低 等原 因,都会 发 生 回磷 。在满足 热力 学条 件 的 同时 . 还必 须 创 造 良好 的脱 磷 反 应 的动 力 学 条 件 , 因 此 , 于脱 磷 反应 的动力 学 条件 是确 保脱磷 利 过 程 中渣 有 良好 的流 动性 , 并在 脱磷 前期加 强熔 池 的搅 拌 。
(完整word版)转炉脱磷分析及采取的措施2
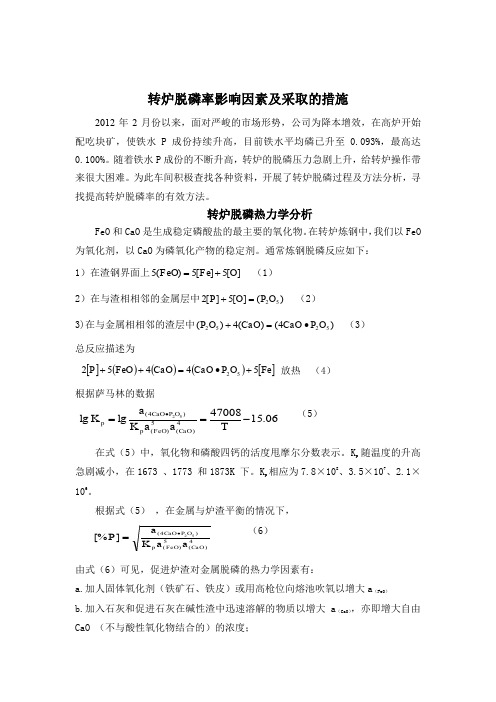
转炉脱磷率影响因素及采取的措施2012年2月份以来,面对严峻的市场形势,公司为降本增效,在高炉开始配吃块矿,使铁水P 成份持续升高,目前铁水平均磷已升至0.093%,最高达0.100%。
随着铁水P 成份的不断升高,转炉的脱磷压力急剧上升,给转炉操作带来很大困难。
为此车间积极查找各种资料,开展了转炉脱磷过程及方法分析,寻找提高转炉脱磷率的有效方法。
转炉脱磷热力学分析FeO 和CaO 是生成稳定磷酸盐的最主要的氧化物。
在转炉炼钢中,我们以FeO 为氧化剂,以CaO 为磷氧化产物的稳定剂。
通常炼钢脱磷反应如下:1)在渣钢界面上][5][5)(5O Fe FeO += (1)2)在与渣相相邻的金属层中)(][5][252O P O P =+ (2)3)在与金属相相邻的渣层中)4()(4)(5252O P CaO CaO O P ∙=+ (3)总反应描述为[]()()()[]Fe O P CaO CaO FeO P 5445252+∙=++ 放热 (4)根据萨马林的数据(5)在式(5)中,氧化物和磷酸四钙的活度甩摩尔分数表示。
K p 随温度的升高急剧减小,在1673 、1773 和1873K 下。
K p 相应为7.8×108、3.5×107、2.1×106。
根据式(5) ,在金属与炉渣平衡的情况下,(6)由式(6)可见,促进炉渣对金属脱磷的热力学因素有:a.加人固体氧化剂(铁矿石、铁皮)或用高枪位向熔池吹氧以增大a (FeO )b.加入石灰和促进石灰在碱性渣中迅速溶解的物质以增大a (CaO ),亦即增大自由CaO (不与酸性氧化物结合的)的浓度;06.1547008lg lg 4)(5)()4(52-==∙T a a K a K CaO FeO p O P CaO p 4)(5)()4(52][%CaO FeO p O P CaO a a K a P ∙=c.用更新与金属接触的渣相的方法,亦即放渣和加入CaO 与FeO 造新渣的方法来减小)4(52O P CaO a ∙d.保持适当的低温,因为温度从1673 增到1873K ,使反应(4)的平衡常数K p 减小到1/370 。
转炉脱磷、造渣工艺

是中期是碳剧烈氧化期,不能变化太快,抑制脱碳反应
突然温度降低,防止喷溅。据上所述,碳的大量氧化,
低磷,在因钢为坯中复的杂偏零析件度要很求大,钢而板在很α和高γ的固塑溶体性内。的IF扩钢散速度 却[很P小]<,0使.0它15不%容易均匀化。因此,按照用途不同对钢中磷含
量有严格要求:
东大冶金
1. 脱P反应
1. 脱P反应
.cn , 110004
2[P]+5[O]= P2O5 2[P]+5(FeO)=(P2O5)+5Fe 3(FeO)+(P2O5)=(3FeO·P2O5) (聚磷酸铁)
EMTI
Shenyang NEU Metallurgical Technology Corporation Limited
技术精益求精 · 创新永无止境
转炉脱磷、造渣工艺
沈阳东大冶金科技股份有限公司
东大冶金110004
磷在钢中以[Fe2P]形式存在,也可以用[P]表示。磷虽然能
前期渣中的(FeO)含量对脱磷反应的进行有重要 作用,这是因为:
12
东大冶金
3. 氧气转炉各期脱磷
.cn , 110004
影响前期脱磷的主要因素是碱度。而高的(FeO)含量 只是一个不可缺少的条件——也是在操作上前期快速成渣 的手段。换言之,就是控制喷枪,使(FeO)在10~15%左 右。炉渣前期 碱度为1.5左右,碱度提高更有利于脱磷,但 因前期温度低,客观上不可能造成高碱度炉渣。并且在此 (FeO)含量范围,碱度在0.82~1.5范围内,炉渣具有较低 的粘度,而碱度高于1.5时,粘度值随碱度增加而快速提 高,炉渣流动性显著变差,不利于脱磷。总之,通常必须 根据铁水条件把前期渣碱度控制在1.5左右;而(FeO) 在10~15%左右或更高些。
顶吹转炉脱磷热力学分析和工艺优化
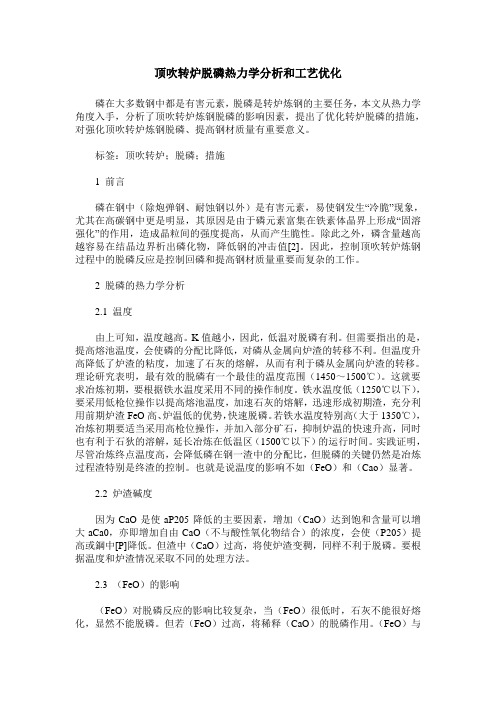
顶吹转炉脱磷热力学分析和工艺优化磷在大多数钢中都是有害元素,脱磷是转炉炼钢的主要任务,本文从热力学角度入手,分析了顶吹转炉炼钢脱磷的影响因素,提出了优化转炉脱磷的措施,对强化顶吹转炉炼钢脱磷、提高钢材质量有重要意义。
标签:顶吹转炉;脱磷;措施1 前言磷在钢中(除炮弹钢、耐蚀钢以外)是有害元素,易使钢发生“冷脆”现象,尤其在高碳钢中更是明显,其原因是由于磷元素富集在铁素体晶界上形成“固溶强化”的作用,造成晶粒间的强度提高,从而产生脆性。
除此之外,磷含量越高越容易在结晶边界析出磷化物,降低钢的冲击值[2]。
因此,控制顶吹转炉炼钢过程中的脱磷反应是控制回磷和提高钢材质量重要而复杂的工作。
2 脱磷的热力学分析2.1 温度由上可知,温度越高。
K值越小,因此,低温对脱磷有利。
但需要指出的是,提高熔池温度,会使磷的分配比降低,对磷从金属向炉渣的转移不利。
但温度升高降低了炉渣的粘度,加速了石灰的熔解,从而有利于磷从金属向炉渣的转移。
理论研究表明,最有效的脱磷有一个最佳的温度范围(1450~1500℃)。
这就要求冶炼初期,要根据铁水温度采用不同的操作制度。
铁水温度低(1250℃以下),要采用低枪位操作以提高熔池温度,加速石灰的熔解,迅速形成初期渣,充分利用前期炉渣FeO高、炉温低的优势,快速脱磷。
若铁水温度特别高(大于1350℃),冶炼初期要适当采用高枪位操作,并加入部分矿石,抑制炉温的快速升高,同时也有利于石狄的溶解,延长冶炼在低温区(1500℃以下)的运行时间。
实践证明,尽管冶炼终点温度高,会降低磷在钢一渣中的分配比,但脱磷的关键仍然是冶炼过程渣特别是终渣的控制。
也就是说温度的影响不如(FeO)和(Cao)显著。
2.2 炉渣碱度因为CaO是使aP205降低的主要因素,增加(CaO)达到饱和含量可以增大aCa0,亦即增加自由CaO(不与酸性氧化物结合)的浓度,会使(P205)提高或鋼中[P]降低。
但渣中(CaO)过高,将使炉渣变稠,同样不利于脱磷。
转炉脱磷及深脱磷
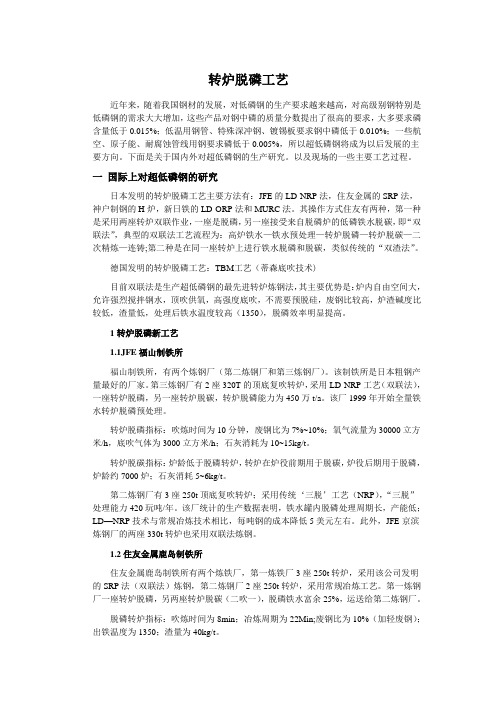
转炉脱磷工艺近年来,随着我国钢材的发展,对低磷钢的生产要求越来越高,对高级别钢特别是低磷钢的需求大大增加,这些产品对钢中磷的质量分数提出了很高的要求,大多要求磷含量低于0.015%;低温用钢管、特殊深冲钢、镀锡板要求钢中磷低于0.010%;一些航空、原子能、耐腐蚀管线用钢要求磷低于0.005%,所以超低磷钢将成为以后发展的主要方向。
下面是关于国内外对超低磷钢的生产研究。
以及现场的一些主要工艺过程。
一国际上对超低磷钢的研究日本发明的转炉脱磷工艺主要方法有:JFE的LD-NRP法,住友金属的SRP法,神户制钢的H炉,新日铁的LD-ORP法和MURC法。
其操作方式住友有两种,第一种是采用两座转炉双联作业,一座是脱磷,另一座接受来自脱磷炉的低磷铁水脱碳,即“双联法”,典型的双联法工艺流程为:高炉铁水—铁水预处理—转炉脱磷—转炉脱碳—二次精炼—连铸;第二种是在同一座转炉上进行铁水脱磷和脱碳,类似传统的“双渣法”。
德国发明的转炉脱磷工艺:TBM工艺(蒂森底吹技术)目前双联法是生产超低磷钢的最先进转炉炼钢法,其主要优势是:炉内自由空间大,允许强烈搅拌钢水,顶吹供氧,高强度底吹,不需要预脱硅,废钢比较高,炉渣碱度比较低,渣量低,处理后铁水温度较高(1350),脱磷效率明显提高。
1转炉脱磷新工艺1.1JFE福山制铁所福山制铁所,有两个炼钢厂(第二炼钢厂和第三炼钢厂)。
该制铁所是日本粗钢产量最好的厂家。
第三炼钢厂有2座320T的顶底复吹转炉,采用LD-NRP工艺(双联法),一座转炉脱磷,另一座转炉脱碳,转炉脱磷能力为450万t/a。
该厂1999年开始全量铁水转炉脱磷预处理。
转炉脱磷指标:吹炼时间为10分钟,废钢比为7%~10%;氧气流量为30000立方米/h,底吹气体为3000立方米/h;石灰消耗为10~15kg/t。
转炉脱碳指标:炉龄低于脱磷转炉,转炉在炉役前期用于脱碳,炉役后期用于脱磷,炉龄约7000炉;石灰消耗5~6kg/t。
钢液脱磷、脱硫 炼钢过程

二、钢液的脱硫
炼钢原料S含量较高,如铁水、生铁块和石灰(石灰窑内 从燃料中吸收S),常超过钢种要求。
S在钢液中无限溶解,不可能自行溢出。在生产中必须采 用相应的手段进行脱S,以满足钢种要求。
钢液的脱硫主要是通过两种途径来实现,即炉渣脱硫和气 化脱硫。在一般炼钢操作条件下,炉渣脱硫占主导。氧化渣 脱硫占总脱硫量的90%,气化脱硫占10%左右。因此,主要 分析炼钢渣与金属间的脱硫反应。
钢液脱磷、脱硫
《转炉炼钢生产》
一、钢液的脱磷
脱磷反应是炼钢过程的基本反应之一,也是一个必要的冶金反应。 磷是一个有害元素,其含量越低越好。在脱氧合金化和炉外精炼过 程中,会发生一定量的回磷现象。而减少其含量是降低危害的唯一 措施。
从理论上来说,钢水的脱磷包括两种方法:氧化脱磷和还原脱磷。 还原脱磷成本高(用Ca脱磷)、工艺复杂,目前处于理论研究 阶段,在生产中基本不使用还原脱磷。在转炉、电炉和铁水预处理 工艺中,主要采用氧化法脱磷工艺。
二、钢液的脱硫
•渣量。增加渣量,降低了渣中(S2-)浓度,促使脱硫反应进行。 •金属液成分的影响。金属液中[C] 能增加硫的活度系数f[S],降低氧 活度,有利于脱硫,铁水含硅高时对脱硫不利,虽然[Si]能使金属中 f[FeS]增大,但它低偿不了生成的SiO2对降低碱度和影响石灰熔化的 负作用。 •脱硫的有利条件:高温,高碱度,低(FeO),大渣量。
一、钢液的脱磷
从 CaO-P2O5 相 图 中 可 以 看 出 3CaO·P2O5 为 最 稳 定 , 4CaO·P2O5次之。可以认为存在于碱性渣中的应是3CaO·P2O5 。
由于3CaO·P2O5和4CaO·P2O5的反应生成自由能值很相近,在 热力学分析时,有两种磷酸盐得出的结论基本上是一致的。在实 验室条件下,达到平衡时的反应产物通常是4CaO·P2O5 。
低铁耗条件下转炉高碳低磷工艺实践与应用

低铁耗条件下转炉高碳低磷工艺实践与应用随着钢铁工业的不断发展,转炉炼钢工艺已经成为当前最主要的炼钢方法之一。
然而,传统的转炉炼钢工艺存在着铁耗高、炉衬寿命短、炉渣质量不稳定等问题,给钢铁企业带来了很大的经济和环境压力。
为了解决这些问题,近年来研究人员通过实践探索和理论研究,提出了低铁耗条件下转炉高碳低磷工艺,该工艺不仅可以降低铁耗,延长炉衬寿命,还可以提高炉渣质量,降低环境污染。
一、低铁耗条件下转炉高碳低磷工艺的原理传统转炉炼钢工艺中,铁矿石是主要的还原剂,由于还原反应需要消耗大量的CO和H2,所以铁矿石的使用量较大,铁耗也相应较高。
而低铁耗条件下转炉高碳低磷工艺则采用了冶金渣还原法,将炉渣作为还原剂,利用炉渣中的FeO、Fe2O3等氧化铁直接与炉内的碳反应生成CO和Fe,从而实现炉内铁的补给,降低铁耗。
同时,该工艺还采用了高碳低磷的炉料组成,使得炉渣质量更加稳定,可以达到较好的脱磷效果。
二、低铁耗条件下转炉高碳低磷工艺的实践1. 炉料组成的优化低铁耗条件下转炉高碳低磷工艺的炉料组成需要根据炉型、炉容、炉温、炉渣成分等因素进行优化。
在实践中,可以采用高含碳量的石墨块、高品质的生铁、高品质的废钢等作为原料,以达到高碳低磷的炉料组成。
2. 炉渣还原反应的控制炉渣还原反应是低铁耗条件下转炉高碳低磷工艺的关键。
在实践中,需要控制好炉渣中的FeO、Fe2O3含量,以及炉温、炉气成分等因素,以实现炉渣还原反应的有效控制。
同时,还需要注意炉渣中的SiO2、Al2O3等氧化物含量,以保证炉渣的流动性和稳定性。
3. 炉衬材料的选择和维护低铁耗条件下转炉高碳低磷工艺需要选择适合的炉衬材料,以延长炉衬寿命。
在实践中,可以采用高铝质炉衬、镁砖、碳砖等材料,以抵抗高温、高碳、高磷的腐蚀作用。
同时,还需要注意炉衬的维护和保养,及时更换炉衬,保证炉衬的完整性和稳定性。
三、低铁耗条件下转炉高碳低磷工艺的应用低铁耗条件下转炉高碳低磷工艺已经在国内外多个钢铁企业得到了广泛应用。
莱钢转炉脱磷优化生产工艺措施

莱钢转炉脱磷优化生产工艺措施摘要:通过对现有装备和工艺技术能力进行系统分析,莱钢炼钢厂通过完善与优化转炉护炉技术、推广应用连铸新技术和新工艺、在铁水预处理、转炉、二次精炼、等方面的先进工艺技术,保证了炼钢生产的稳定运行。
关键词:转炉品种结构工艺优化1、前言高效转炉工艺技术主要以保证质量为前提,以高作业率为基本手段来实现高质量、低成本。
实现转炉的高效生产不仅需要科学管理,更重要的是持续不断的技术改造创新,采用优质耐材和先进工艺、生产设备技术,以不断提高转炉脱磷工艺技术装备水平。
莱钢炼钢转炉系统经过近年来改革和发展,坚持走引进、消化、吸收、再创新的道路,在品种、质量等方面有了质的飞跃,而且自主开发集成了多项关键技术。
目前,莱钢炼钢系统主要包括转炉炼钢和电炉炼钢,转炉炼钢现有3座50t转炉、1座60t转炉,5座120t转炉,相应配套小方坯连铸机、带钢坯连铸机、矩形坯连铸机、异型坯连铸机、板坯连铸机,生产能力为1 000万t/a。
莱钢炼钢厂针对实际生产中存在的薄弱工艺环节,对现有设备工艺进一步优化改造,提高了生产装备水平,完善炼钢新工艺、新技术,进一步发挥了转炉的潜能,提高了质量,降低了成本。
2、依靠技术创新,提升工艺水平自金融危机以来。
全球钢铁消费需求不断下滑,国内钢企面临日益严峻的增支减利和结构优化调整压力。
为了更好地生存与发展,坚持以效益为中心,以技术创新为手段,立足于自主开发,加快新技术和新工艺的集成应用,大力发展循环经济,挖掘节能降耗潜力;同时加大高端新产品开发力度,提高产品质量,改善品种结构,积极应对市场变化。
莱钢炼钢系统充分发挥广大工程技术人员的聪明才智,大力开展技术攻关,提升工艺技术水平,促进了生产顺行,改善了产品质量,降低了生产成本。
特别是在炼钢系统,不断开发和应用新技术、新工艺,依靠技术进步和创新,工艺降本增效和新产品开发工作取得了显著成效。
3、转炉炼钢工艺过程在转炉炼钢过程中,通过氧枪向熔池内吹入氧气,与铁水中的碳、硅、磷、硫等元素反应生成炉渣、废气等,同时释放热量使熔液的温度升高,进而得到所需的钢种。
- 1、下载文档前请自行甄别文档内容的完整性,平台不提供额外的编辑、内容补充、找答案等附加服务。
- 2、"仅部分预览"的文档,不可在线预览部分如存在完整性等问题,可反馈申请退款(可完整预览的文档不适用该条件!)。
- 3、如文档侵犯您的权益,请联系客服反馈,我们会尽快为您处理(人工客服工作时间:9:00-18:30)。
转炉炼钢脱磷工艺的探讨
[摘要]本文从脱磷的热力学分析入手,对冶炼过程中温度、炉渣碱度、渣中
(FeO),等对磷含量的影响进行了探讨。同时探讨了回磷的原因、影响的因素
和防止的措施。
【关键词】转炉炼钢;脱磷工艺;探讨
磷在钢中是以【Fe3P】或【Fe2P】形式存在,一般以【P】表示。磷含量高
时,会使钢的朔性和韧性降低,即使钢的脆性增加,这种现象低温时更严重,通
常把它称为“冷脆”。且这种影响常常随着氧,氮含量的增加而加剧。磷在连铸坯
中的偏析仅次于硫,同时它在铁固溶体中扩散速度又很小。不容易均匀化,因而
磷的偏析和难消除。由于炼铁过程为还原性气氛,脱磷能力较差。因此脱磷是炼
钢过程的重要任务之一。在20世纪90年代中后期,为解决超低磷钢的生产难题,
世界上各大钢厂都曾经进行过转炉铁水脱磷实验研究。
1、铁水预处理方法
1.1喷吹苏打粉处理
日本住友公司鹿岛厂开发的“住友碱精炼法”是成功用于工业生产的苏打精
炼法。
工艺流程:从高炉流出的铁水先经脱硅处理,即将高炉铁水注入混铁车内,
用氮气输送和喷吹烧结矿粉,喷入量为每吨铁水40公斤,最大供粉速度为每分
钟400公斤,最大吹氧量为每分钟50立方米,脱硅量约为0.4%。脱硅处理后的
铁水硅含量可降到0.1%以下。然后用真空吸渣器吸出脱硅渣,进行脱磷处理,
以氮气为载气向铁水中喷入苏打粉,苏打粉用量为每吨18公斤,最大供粉量为
每分钟250公斤,最大吹氧量为每分钟50立方米,处理后铁水中【P】≤0.001%,
【S】≤0.003%,再用真空吸渣器吸出脱磷渣,并将其送到苏打回收车间,经水
浸后可回收约80%的Na2O,最后将处理过的铁水倒入转炉冶炼。
1.2喷吹石灰系熔剂处理
由于石灰系熔剂具有成本低,对环境污染小的优点,因此受到重视,并不断
对其深入研究,以使其满足精炼铁水的需要。
工艺流程:向高炉铁沟中加入铁磷进行脱硅处理,加入量为每吨铁水27公
斤,处理后铁水含硅量由0.5%降到0.15%,氧的利用率为80%-90%。脱硅后的
铁水流入混铁车中,并与混铁车内上一炉脱磷脱硫渣混合,待渣与铁分离后扒渣。
然后,向混铁车内铁水中用氮气为载气体,流量为每分钟为3-5立方米,喷入石
灰熔剂。处理后温度为13500C左右,处理时间25分钟。将处理后的铁水倒入
转炉,在转炉内进一步脱磷,可使钢中【P】≤0.001%。
2、转炉冶炼过程中脱磷
2.1氧化脱磷
磷在钢液中能够无限溶解,。而它的氧化物P2O5在钢液的溶解度却很小,
因此,要除去钢中的磷,可设法使磷氧化生成P2O5进入炉渣,并固定在渣中。
炼钢过程中的脱磷反应在渣—钢界面和氧气顶吹转炉的乳浊液中,是被渣中FeO
氧化,其反应为:
2【P】+5(FeO)= (P2O5)+5【Fe】
△G0=-1495194+684.92T(J/mol)
生成的P2O5的密度较小,几乎不溶于钢液,所以一旦生成即上浮转入渣相。
但由于冶炼初期渣中较多的碱性氧化物是FeO,因此进入炉渣的P2O5仅和FeO
结合成磷酸铁盐。
其反应:
(P2O5)+3(FeO)=(3FeO·P2O5)
△H0=-128030J/mol
根据生成焓△H0判断,渣中(P2O5),(3FeO·P2O5)却不稳定,它们在炼
钢过程中随着熔池温度的不断升高而逐渐分解,使磷又回到钢液之中。所以在炼
钢温度下,以氧化铁为主的炉渣脱磷能力很低。为了使脱磷过程进行得比较彻底,
防止已被氧化的磷大量返回钢液,目前大多工厂的做法是向熔池加入一定量的石
灰,增加渣中强碱性氧化物CaO的含量,使五氧化二磷和氧化钙生成较稳定的
磷酸钙,从而提高炉渣的脱磷能力。在生产中,随着石灰的变化,炉渣的碱度会
逐渐升高,渣中的游离的CaO逐渐增加,此时将发生置换反应:
即:(3FeO·P2O5)+4(CaO)=(4CaO·P2O5)+5【Fe】
所以,碱性氧化渣脱磷的总反应为:
2【P】+5(FeO)+4(CaO)=(4CaO·P2O5)+5【Fe】
转炉冶炼过程中低碳低磷铁水转炉去磷率达到90%以上。
2.1.1影响炉渣脱磷的主要因素:(1)炉渣成分的影响:炉渣成分对脱磷反
应的影响主要反应在渣中的FeO含量和炉渣碱度上。渣中的FeO是脱磷的首要
条件,如果渣中没有氧化铁或氧化铁含量很低,就不可能使磷氧化。但是,纯氧
化铁炉渣只有很小的去磷效果,因为渣中(3FeO·P2O5)在高温下 不稳定,它
会分解或被硅、锰还原,而渣中(4CaO·P2O5)在17100c的温度下比较稳定,
即炼钢温度下它分解的可能性不大,所以CaO是脱磷的必要条件;(2)温度的
影响:脱磷反应是强放热反应,升高温度会使其平衡常数的数值减小,去除效率
下降。从热力学条件来看,降低温度有利于去P反应进行,但是应该辩证地看待
温度的影响,尽管升高温度会使反应的平衡常数K值减少,然而与此同时较高
的温度能使炉渣的粘度下降,加速石灰的成渣速度和渣中各组元的扩散速度,强
化了磷从金属液向炉渣的转移。其影响可能超过Kp值得降低,温度过高时,Kp
值的下降起主导作用,会使炉渣的去P效率下降。钢中的磷含量回升;(3)炉渣
粘度的影响:炼钢熔池中的脱P反应主要是在炉渣与金属液两相的界面上进行
的,所以反应速度与炉渣粘度有关。通常情况下,炉渣粘度越低,渣中反应物
FeO向渣—钢界面的扩散转移速度就越快,渣中反应产物P2O5离开界面溶入炉
渣的速度也就越快。因此,在脱P要求的高碱度条件下,应及时加入稀渣剂改善
炉渣的流动性,以促进脱P反应的顺利进行;(4)渣量的影响:随着脱磷反应的
进行,渣中P2O5的含量不断升高,炉渣脱P能力逐渐下降。在一定条件下,增
大渣量必然会使渣中的P2O5含量降低,破坏磷在钢—渣间分配的平衡性,促进
脱磷反应的继续进行,使钢中的磷含量进一步降低。所以炉内渣量的多少决定着
钢液的脱磷程度。但渣量过大,会使钢液面上渣层过厚而减慢去磷速度,同时还
压抑了钢液的沸腾,使气体及夹杂物的排除受到影响。
2.2回磷
2.2.1产生回磷的原因:冶炼终点一般被认为脱P 反应达到平衡,在出钢过
程向钢包加入脱氧剂,将使使钢中的氧以及渣中(FeO)下降,脱氧产物(SiO2),
(Al2O3)等进入炉渣,使炉渣碱度降低,从而打破了脱磷反应的平衡状态,有
利于(P2O5)的分解和还原,磷又重新进入钢液。
2.2.2影响回磷的因素:(1)出钢过程中下渣是磷的主要原因。下渣量大,
回磷严重;(2)出钢合金化或增碳操作不合理。如出钢后期补加硅铁,碳化硅,
碳粉等;(3)吹氩时,使用氩气压力过高,造成钢液-炉渣翻腾,卷渣,也会增
加回磷。
2.2.3防止回磷的措施:要防止钢水会磷,首先是挡好渣,减少出钢过程的
下渣量。其次是严格出钢合金化操作,杜绝出钢后补加合金。再次出钢时向钢包
内投入少量小块石灰以提高钢包内渣层的碱度,稠化炉渣,降低炉渣的反应能力,
阻止钢渣接触时发生回磷反应。
3、结束语
转炉脱磷工艺在各国冶金工作者的努力下不断地发展,同时适合转炉脱磷工
艺的新型脱磷剂也在研究与发展中,随着世界转炉炼钢技术的发展及炼钢设备的
多样化,使传统的转炉炼钢过程逐步转向单一化,这样不仅可以提高钢水的质量,
缩短转炉冶炼周期,降低原材料消耗和能耗,而且有利于冶炼过程的控制和管理,
更好发挥转炉脱磷工艺的优点。做好这些就有利于我国目前进行技术改进,提高
钢水纯净度,更好的优化钢铁冶炼工艺水平。