转炉脱磷影响因素分析及其工艺应用
铁水转炉吹氧脱磷工艺-概述说明以及解释

铁水转炉吹氧脱磷工艺-概述说明以及解释1.引言1.1 概述铁水转炉吹氧脱磷工艺是钢铁生产中常用的一种去除磷元素的工艺方法。
在铁水中磷元素的含量对钢铁的性能有着重要影响,因此需要采取相应措施进行去除。
吹氧脱磷工艺通过向铁水中吹入氧气,利用氧气与磷元素的化学反应,在高温条件下将磷元素氧化移除,从而减少磷元素含量,提高钢铁的质量和性能。
本文将详细介绍铁水转炉吹氧脱磷工艺的原理、步骤以及其在钢铁生产中的应用。
通过对该工艺的深入探讨,可以更好地了解吹氧脱磷的作用机制和优势,为钢铁生产提供技术支持和参考。
1.2 文章结构1.3 目的本文旨在深入探讨铁水转炉吹氧脱磷工艺,通过对该工艺的原理、步骤、优势以及应用前景进行分析,旨在说明吹氧脱磷工艺在钢铁生产中的重要性和价值。
同时,通过总结工艺的特点和优势,为相关行业提供参考,促进该工艺的广泛应用,提高生产效率,降低成本,推动钢铁行业的可持续发展。
2.正文2.1 铁水转炉工艺概述:铁水转炉是一种用于炼钢的高炉,它是一种旋转的容器,通常由耐火材料和金属外壳构成。
在钢铁冶炼过程中,铁水转炉扮演着至关重要的角色。
铁水转炉工艺通常用于生产高品质的钢铁,其主要特点是操作简单,生产效率高,并能够满足不同规格和质量要求的钢铁生产。
在铁水转炉中,主要通过向铁水中吹入氧气使其氧化,从而提高炉内温度,促使不同元素的相互作用,达到脱除杂质的目的。
铁水转炉通常配有各种喷嘴和氧气喷嘴,以确保充分的氧化反应和高效的燃烧过程。
铁水转炉工艺的优点包括:1. 生产效率高:铁水转炉可以持续生产,操作简单,生产效率高。
2. 能够生产高品质钢铁:通过吹氧脱磷等工艺,可以去除杂质,生产高品质的钢铁。
3. 适用范围广:铁水转炉可以生产各种规格和质量要求的钢铁,适用性广泛。
总的来说,铁水转炉工艺在钢铁冶炼领域具有重要的地位,其优点包括高效、高质以及适用范围广泛,为钢铁行业的发展做出了重要贡献。
2.2 吹氧脱磷的原理2.3 吹氧脱磷的步骤:吹氧脱磷是铁水转炉炼钢过程中的关键环节之一,其步骤主要包括以下几个方面:1. 吹氧开始: 在铁水转炉底部喷入高纯度氧气,形成氧吹。
转炉脱磷造渣工艺
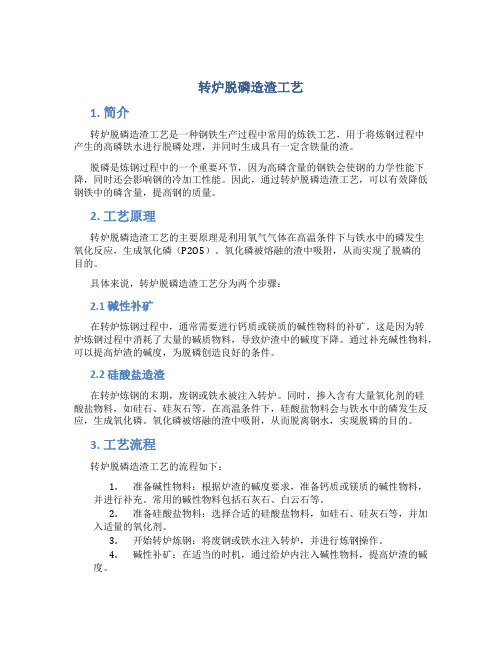
转炉脱磷造渣工艺1. 简介转炉脱磷造渣工艺是一种钢铁生产过程中常用的炼铁工艺,用于将炼钢过程中产生的高磷铁水进行脱磷处理,并同时生成具有一定含铁量的渣。
脱磷是炼钢过程中的一个重要环节,因为高磷含量的钢铁会使钢的力学性能下降,同时还会影响钢的冷加工性能。
因此,通过转炉脱磷造渣工艺,可以有效降低钢铁中的磷含量,提高钢的质量。
2. 工艺原理转炉脱磷造渣工艺的主要原理是利用氧气气体在高温条件下与铁水中的磷发生氧化反应,生成氧化磷(P2O5)。
氧化磷被熔融的渣中吸附,从而实现了脱磷的目的。
具体来说,转炉脱磷造渣工艺分为两个步骤:2.1 碱性补矿在转炉炼钢过程中,通常需要进行钙质或镁质的碱性物料的补矿。
这是因为转炉炼钢过程中消耗了大量的碱质物料,导致炉渣中的碱度下降。
通过补充碱性物料,可以提高炉渣的碱度,为脱磷创造良好的条件。
2.2 硅酸盐造渣在转炉炼钢的末期,废钢或铁水被注入转炉。
同时,掺入含有大量氧化剂的硅酸盐物料,如硅石、硅灰石等。
在高温条件下,硅酸盐物料会与铁水中的磷发生反应,生成氧化磷。
氧化磷被熔融的渣中吸附,从而脱离钢水,实现脱磷的目的。
3. 工艺流程转炉脱磷造渣工艺的流程如下:1.准备碱性物料:根据炉渣的碱度要求,准备钙质或镁质的碱性物料,并进行补充。
常用的碱性物料包括石灰石、白云石等。
2.准备硅酸盐物料:选择合适的硅酸盐物料,如硅石、硅灰石等,并加入适量的氧化剂。
3.开始转炉炼钢:将废钢或铁水注入转炉,并进行炼钢操作。
4.碱性补矿:在适当的时机,通过给炉内注入碱性物料,提高炉渣的碱度。
5.硅酸盐造渣:当转炉炼钢接近末期时,通过给炉内注入硅酸盐物料,利用氧化剂促进磷的氧化反应。
6.淋渣:根据炉内的渣情况,选择合适的时间进行淋渣操作。
淋渣可以通过人工或机械设备进行。
7.渣铁分离:在脱磷过程中,渣中生成的氧化磷会被吸附在渣中,从而脱离钢水。
通过合适的方法,将渣与钢水分离。
8.尾渣处理:处理分离出来的尾渣,并对其进行资源化利用或安全处理。
顶吹转炉脱磷热力学分析和工艺优化
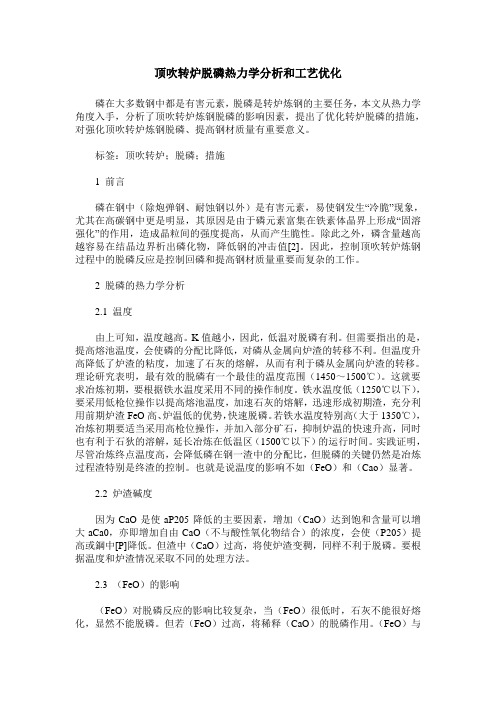
顶吹转炉脱磷热力学分析和工艺优化磷在大多数钢中都是有害元素,脱磷是转炉炼钢的主要任务,本文从热力学角度入手,分析了顶吹转炉炼钢脱磷的影响因素,提出了优化转炉脱磷的措施,对强化顶吹转炉炼钢脱磷、提高钢材质量有重要意义。
标签:顶吹转炉;脱磷;措施1 前言磷在钢中(除炮弹钢、耐蚀钢以外)是有害元素,易使钢发生“冷脆”现象,尤其在高碳钢中更是明显,其原因是由于磷元素富集在铁素体晶界上形成“固溶强化”的作用,造成晶粒间的强度提高,从而产生脆性。
除此之外,磷含量越高越容易在结晶边界析出磷化物,降低钢的冲击值[2]。
因此,控制顶吹转炉炼钢过程中的脱磷反应是控制回磷和提高钢材质量重要而复杂的工作。
2 脱磷的热力学分析2.1 温度由上可知,温度越高。
K值越小,因此,低温对脱磷有利。
但需要指出的是,提高熔池温度,会使磷的分配比降低,对磷从金属向炉渣的转移不利。
但温度升高降低了炉渣的粘度,加速了石灰的熔解,从而有利于磷从金属向炉渣的转移。
理论研究表明,最有效的脱磷有一个最佳的温度范围(1450~1500℃)。
这就要求冶炼初期,要根据铁水温度采用不同的操作制度。
铁水温度低(1250℃以下),要采用低枪位操作以提高熔池温度,加速石灰的熔解,迅速形成初期渣,充分利用前期炉渣FeO高、炉温低的优势,快速脱磷。
若铁水温度特别高(大于1350℃),冶炼初期要适当采用高枪位操作,并加入部分矿石,抑制炉温的快速升高,同时也有利于石狄的溶解,延长冶炼在低温区(1500℃以下)的运行时间。
实践证明,尽管冶炼终点温度高,会降低磷在钢一渣中的分配比,但脱磷的关键仍然是冶炼过程渣特别是终渣的控制。
也就是说温度的影响不如(FeO)和(Cao)显著。
2.2 炉渣碱度因为CaO是使aP205降低的主要因素,增加(CaO)达到饱和含量可以增大aCa0,亦即增加自由CaO(不与酸性氧化物结合)的浓度,会使(P205)提高或鋼中[P]降低。
但渣中(CaO)过高,将使炉渣变稠,同样不利于脱磷。
影响转炉脱磷的因素分析

表 1 表明,随着副枪一的温度升高,过程温度 也随之升高,因为提高熔池温度,会使磷的分配比 降低,对磷从金属向炉渣的转移不利,所以汽车板 副枪一脱磷率比 SPHC、P3A2 系列低。而是温度 升高降低了炉渣的黏度,加速了石灰的熔解,从而 有利于磷从 金 属 向 炉 渣 的 转 移,所 以 转 炉 终 点 时 脱磷率基 本 相 同。 实 践 证 明,尽 管 冶 炼 终 点 温 度 高,会降低磷在钢—渣中的分配比,但脱磷的关键 仍然是冶炼 过 程 渣 特 别 是 终 渣 的 控 制,温 度 的 影 响不如炉渣碱度和 FeO 显著。
在冶炼初期,加入炉内的大量石灰因温度低, 在表面形成冷凝外壳,并未熔化。在此期间,液态 炉渣主要与铁水中的 Si、Mn、Fe 氧化产物反应,随 着氧化和 温 度 的 升 高,使 石 灰 熔 化,碱 度 开 始 提 高,此时碱度约为 1. 3 ~ 1. 5; 在冶炼中期,由于炉 温升高石灰进一步熔化,但因脱碳速度加快,导致 渣中的 FeO 逐渐降低,使石灰熔化速度减缓。在 此期间,碱度的增加较缓慢,此时碱度约为 1. 8 左 右; 在冶炼后期,脱碳速度下降,渣中 FeO 再次升
Vol. 31 No. 1 March 2 0 1 0
影响转炉脱磷的因素分析
王凌川,李伯超,孙 光,侯海龙
( 黑龙江省冶金研究所,哈尔滨 150040)
摘 要: 本文主要从转炉脱磷的理论分析入手,探讨了炉渣碱度、FeO 的质量分数和冶炼过程温度对磷质量分 数的影响及回磷的原因、影响因素及防止措施等。同时本文指出应控制炉渣碱度、FeO、终点温度在合理范围 内,并应重视钢水回磷问题。 关键词: 脱磷; 碱度; 温度
我们 选 取 操 作 平 稳,副 枪 一 碳 在 0. 30% ~ 0. 40% 之间的数据作为研究对象,从其副枪温度 推断其过程 温 度,如 副 枪 一 温 度 高 则 其 过 程 温 度 肯定会高。副枪一温度和副枪二温度与脱磷率的 关系,选取的数据均是平均值,如表 1。
转炉炼钢脱磷工艺理论与实践
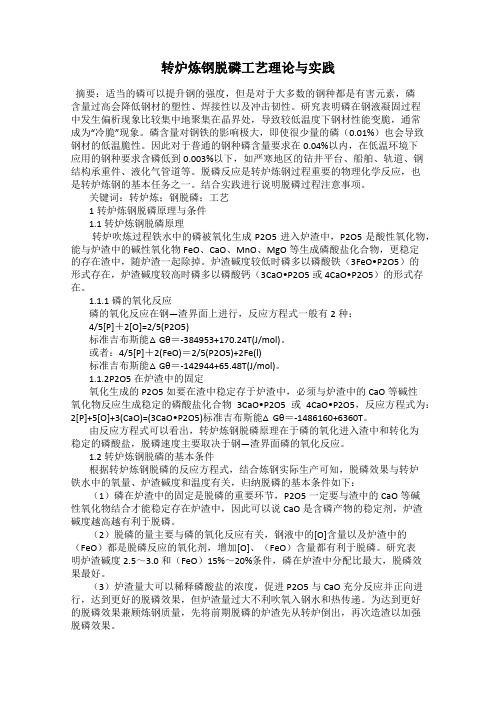
转炉炼钢脱磷工艺理论与实践摘要:适当的磷可以提升钢的强度,但是对于大多数的钢种都是有害元素,磷含量过高会降低钢材的塑性、焊接性以及冲击韧性。
研究表明磷在钢液凝固过程中发生偏析现象比较集中地聚集在晶界处,导致较低温度下钢材性能变脆,通常成为“冷脆”现象。
磷含量对钢铁的影响极大,即使很少量的磷(0.01%)也会导致钢材的低温脆性。
因此对于普通的钢种磷含量要求在0.04%以内,在低温环境下应用的钢种要求含磷低到0.003%以下,如严寒地区的钻井平台、船舶、轨道、钢结构承重件、液化气管道等。
脱磷反应是转炉炼钢过程重要的物理化学反应,也是转炉炼钢的基本任务之一。
结合实践进行说明脱磷过程注意事项。
关键词:转炉炼;钢脱磷;工艺1转炉炼钢脱磷原理与条件1.1转炉炼钢脱磷原理转炉吹炼过程铁水中的磷被氧化生成P2O5进入炉渣中,P2O5是酸性氧化物,能与炉渣中的碱性氧化物FeO、CaO、MnO、MgO等生成磷酸盐化合物,更稳定的存在渣中,随炉渣一起除掉。
炉渣碱度较低时磷多以磷酸铁(3FeO•P2O5)的形式存在,炉渣碱度较高时磷多以磷酸钙(3CaO•P2O5或4CaO•P2O5)的形式存在。
1.1.1磷的氧化反应磷的氧化反应在钢—渣界面上进行,反应方程式一般有2种:4/5[P]+2[O]=2/5(P2O5)标准吉布斯能△Gθ=-384953+170.24T(J/mol)。
或者:4/5[P]+2(FeO)=2/5(P2O5)+2Fe(l)标准吉布斯能△Gθ=-142944+65.48T(J/mol)。
1.1.2P2O5在炉渣中的固定氧化生成的P2O5如要在渣中稳定存于炉渣中,必须与炉渣中的CaO等碱性氧化物反应生成稳定的磷酸盐化合物3CaO•P2O5或4CaO•P2O5,反应方程式为:2[P]+5[O]+3(CaO)=(3CaO•P2O5)标准吉布斯能△Gθ=-1486160+6360T。
由反应方程式可以看出,转炉炼钢脱磷原理在于磷的氧化进入渣中和转化为稳定的磷酸盐,脱磷速度主要取决于钢—渣界面磷的氧化反应。
转炉深脱磷反应机理
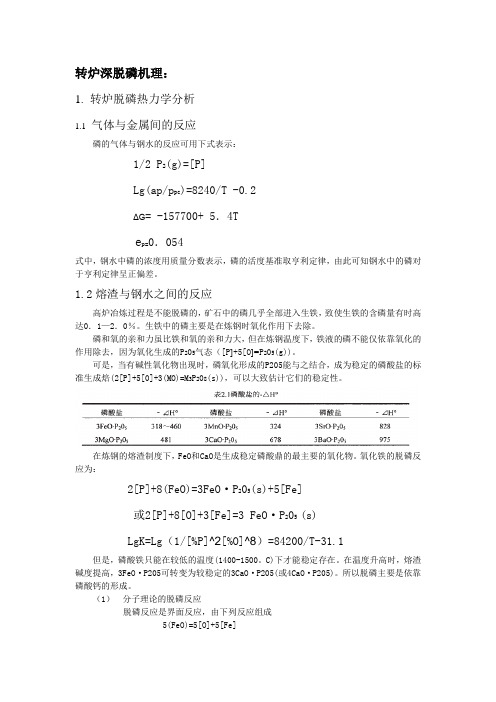
转炉深脱磷机理:1.转炉脱磷热力学分析1.1气体与金属间的反应磷的气体与钢水的反应可用下式表示:1/2 P2(g)=[P]Lg(ap/p pc)=8240/T -0.2ΔG= -157700+ 5.4Te p=0.054式中,钢水中磷的浓度用质量分数表示,磷的活度基准取亨利定律,由此可知钢水中的磷对于亨利定律呈正偏差。
1.2熔渣与钢水之间的反应高炉冶炼过程是不能脱磷的,矿石中的磷几乎全部进入生铁,致使生铁的含磷量有时高达0.1—2.0%。
生铁中的磷主要是在炼钢时氧化作用下去除。
磷和氧的亲和力虽比铁和氧的亲和力大,但在炼钢温度下,铁液的磷不能仅依靠氧化的作用除去,因为氧化生成的P205气态([P]+5[O]=P205(g))。
可是,当有碱性氧化物出现时,磷氧化形成的P205能与之结合,成为稳定的磷酸盐的标准生成焙(2[P]+5[0]+3(MO)=M3P208(s)),可以大致估计它们的稳定性。
在炼钢的熔渣制度下,FeO和CaO是生成稳定磷酸鼎的最主要的氧化物。
氧化铁的脱磷反应为:2[P]+8(FeO)=3FeO·P205(s)+5[Fe]或2[P]+8[O]+3[Fe]=3 FeO·P205 (s)LgK=Lg(1/[%P]^2[%O]^8)=84200/T-31.1但是,磷酸铁只能在较低的温度(1400-1500。
C)下才能稳定存在。
在温度升高时,熔渣碱度提高,3FeO·P205可转变为较稳定的3CaO·P205(或4CaO·P205)。
所以脱磷主要是依靠磷酸钙的形成。
(1)分子理论的脱磷反应脱磷反应是界面反应,由下列反应组成5(FeO)=5[O]+5[Fe]2[P]+5[0]=(P205)(P205)+4(CaO)=(4CaO·P205)综合得:2[P]+5(FeO)+4(CaO)=4CaO·P205+5[Fe]LgK=Lg (a (4Ca0·P205)/[%P]^2 a FeO^5·a CaO^4)=40067/T-15.06式中:K------------------脱磷反应的化学平衡常数:T------------------钢水温度。
转炉炼钢脱磷工艺分析

II
第三章 试验方案的设计.............................................................................................................. 27 3.1 沙钢双渣脱磷的现状........................................................................................................ 27 3.1.1 双渣操作的好处......................................................................................................... 27 3.1.2 沙钢双渣脱磷情况.....................................................................................................27 3.1.3 脱磷的效果及回磷问题............................................................................................ 28 3.2 目前存在的问题................................................................................................................. 29 3.2.1 前期脱磷结果............................................................................................................. 29 3.3 影响前期脱磷的主要因素............................................................................................... 30 3.3.1 钢水中硅的氧化......................................................................................................... 30 3.3.2 前期渣碱度的控制.....................................................................................................30 3.3.3 倒前期渣时间的控制................................................................................................ 31 3.4 180t 转炉冶炼终点脱磷情况.......................................................................................... 32 3.4.1 增碳剂加入量的控制................................................................................................ 32 3.4.2 冶炼终点脱磷情况.....................................................................................................32 3.5 180t 转炉冶炼工艺改进方案.......................................................................................... 32 3.5.1 冶炼前期控制............................................................................................................. 33 3.5.2 冶炼终点控制............................................................................................................. 33 结论..............................................................................................................................................35 参考文献..................................................................................................................................... 36 致 谢....................................................................................................................................... 37
转炉脱磷及深脱磷

转炉脱磷工艺摘要磷是有害元素,对于高级别钢,除需要硫含量很低外,还需要磷含量控制在很低的水平。
由于炼铁过程为还原性气氛,脱磷能力较差,脱磷是炼钢过程中的重要环节之一。
本文主要从转炉冶炼的双渣法双联法进行分析,探讨了冶炼过程中温度、炉渣碱度、铁水中Si含量、(FeO)对P含量的影响,回磷的原因、以及两种冶炼方法脱磷效率的对比,针对鞍钢三炼钢的转炉炼钢冶炼数据分析了两种方法在温度、炉渣碱度、铁水中Si含量、(FeO)对P含量的影响,并对转炉脱磷现状进行了分析。
结果表明,双联法在脱磷方面优越与双渣法,效果显著,工艺简单,渣量减少,为生产超低P钢创造了优越的条件。
关键词:转炉,脱磷,双渣法,双联法AbstractPhosphor is one of the elements destroying the properties of steel product.Besides the low content of sulphur,it needs low phosphor for high quality steel.Since the ironmaking process is reduction atmosphere,the ability for dephosphorization is poor,thus dephosphorization during the steelmaking becomes the main step.This research mainly analyzed the Double Slag Process and the Deplexing process of converter, discussed the impact of smelting temperature, slag basicity, hot metal Si content and (FeO) on phosphorus content and the reason of rephosphorization as well as the comparison of the two methods on the efficiency of dephosphorization. In this research, we have looked into the figure of No. 3 Steelmaking Plant of An Steel Corporation to analyze the effect of smelting temperature, slag basicity, hot metal Si content and (FeO) and current situation of converter dephosphorization. The result indicates the advantage of Deplexing Process over Double Slag Process, which is effective, easy and produces less slag. Thus it provided superb conditions to produce lowest phosphorus steel.Key words :converter dephosphorization the Double Slag Process the Deplexing process of converter目录一国内外转炉深脱磷发展现状 (1)1.1国际上对超低磷钢的研究 (1)1.2我国国内对超低磷钢的研究以及这方面的探索 (7)二转炉深脱磷机理: (9)2.1转炉脱磷热力学分析 (9)2.1.1气体与金属间的反应 (9)2.1.2熔渣与钢水之间的反应 (10)2.2脱磷反应的动力学分析 (14)2.2.1脱磷动力学的研究基础 (14)2.2.2温度对反应速度的影响 (14)2.2.3 化能对反应速度的影响 (15)三实验现状 (15)3.1鞍钢第一炼钢生产工艺 (15)3.2 实验方案 (17)3.2.1双炼法 (17)3.2.2 双渣法脱磷过程分析及工艺要点 (21)3.3 实验结果分析 (26)3.3.1 双渣法数据处理 (32)3.3.2双联法转炉脱磷数据处理 (39)四结论 (45)近年来,随着我我国钢材的发展,对低磷钢的生产要求越来越高,对高级别钢特别是低磷钢的需求大大增加,这些产品对钢中磷的质量分数提出了很高的要求,大多要求磷含量低于0.015%;低温用钢管、特殊深冲钢、镀锡板要求钢中磷低于0.010%;一些航空、原子能、耐腐蚀管线用钢要求磷低于0.005%,所以超低磷钢将成为以后发展的主要方向。
- 1、下载文档前请自行甄别文档内容的完整性,平台不提供额外的编辑、内容补充、找答案等附加服务。
- 2、"仅部分预览"的文档,不可在线预览部分如存在完整性等问题,可反馈申请退款(可完整预览的文档不适用该条件!)。
- 3、如文档侵犯您的权益,请联系客服反馈,我们会尽快为您处理(人工客服工作时间:9:00-18:30)。
转炉脱磷影响因素分析及其工艺应用
作者:李家通
来源:《中国新技术新产品》2017年第01期
摘要:本文简单阐述了目前我国的转炉脱磷工艺,通过具体分析溶池温度、炉渣碱度、渣量以及FeO含量等影响因素对转炉脱磷的影响与工艺发展概况,为转炉脱磷工艺发展提供了技术参考。
关键词:转炉脱磷;碱度;温度;FeO含量;炉渣
中图分类号:TF714 文献标识码:A
磷是钢铁产品中属于有害杂质(特殊情况除外),钢铁产品中的磷元素会使钢的韧性和可塑性大打折扣,使其在低温情况尤其容易冷脆断裂。
在大部分优质的钢铁产品中,其对钢中磷含量的要求非常严格,只有这样才能保证其高韧性,防止冷脆断裂的现象发生。
随着科学技术水平的提高,现代工业中对低磷钢、超低磷钢的使用需求日渐增长,因此本文就溶池温度、炉渣碱度、渣量以及FeO含量等影响因素分析如何提高转炉脱磷技术,以期为我国转炉脱磷工艺发展提供经验参考。
1.转炉脱磷工艺概述
转炉脱磷工艺主要包括:SRP工艺、多功能转炉脱磷工艺、COMI炼钢工艺脱磷工艺以及复吹转炉深脱磷工艺,其中复吹转炉深脱磷工艺又包括两路双联工艺、单渣工艺以及单炉新双渣工艺。
在炼铁过程中,原料中的磷几乎全部浸会入铁水中,转炉和炉渣为脱磷提供了良好的脱磷环境。
在转炉冶炼过程中,可以通过控制主要脱磷影响因素达到良好的脱磷效果。
通常在转炉脱磷初期阶段,溶池温度较低,磷含量较高,热力学条件较好,但是由于此阶段炉渣的流动性较弱、炉渣碱度较低,动力学条件较差,因此需要通过改善动力学条件来配合热力学条件来加速脱磷,即提高炉渣流动性、炉渣碱度等;在转炉脱磷处理后期,钢水磷经过前阶段的脱磷之后,磷含量降低,炉渣流动性较高,具备良好的动力学条件,然而溶池温度较高,热力条件较差,不利于脱磷的进行,此时可以通过提高炉渣的碱度来改善热力学条件。
2.转炉脱磷影响因素分析
2.1 温度的影响
通常转炉脱磷中的“温度”专指“溶池温度”,一般情况下,需要从两方面考虑温度对转炉脱磷效果的影响。
一方面,当熔池温度较低时,从热力学原理上分析,低温将有助于脱磷反应正常进行,但是当温度过低时,石灰在表面容易形成一层冷凝外壳,并未熔化,并降低化渣速度
和炉渣流动速度,碱度降低,最终降低脱磷反应速度;另一方面,熔池温度升高过程中也会对脱磷效果产生影响。
当熔池温度升高时,磷的分配比率会降低,脱碳反应的速度加快,炉渣中氧化铁含量随之减少,并且形成硅酸二钙覆盖在石灰表面,其熔点较高会阻碍石灰的进一步熔化,导致出现炉渣的“返干”现象。
同时,时温度过高会使转炉熔池反应剧烈,易发生喷溅,使倒渣困难,不利于脱磷。
相反的是,当熔池温度升高时,熔渣的碱度和流动性相应提高,动力学条件良好,加速脱磷反映。
根据生产实践可知,要使脱磷效果达到最佳状态,温度一般需要控制在1300℃~1350℃范围内。
因此,高效率的转炉脱磷需要根据溶池不同的温度,来决定使用何种操作机制较为科学。
当溶池温度低于1250℃时,需要通过低枪位吹氧方式来使熔池温度快速达到有效温度,加速石灰熔解以及炉渣的形成,充分利用高炉渣氧化铁含量、低炉温的有利条件,加速转炉脱磷。
当钢水温度超过1350℃时,高枪位操作有助于抑制炉温,延长在极限高温下的冶炼运行时间。
但是实践证明,终渣的控制才是转炉脱磷的关键环节,FeO含量和炉渣碱度对转炉脱磷效果影响更显著,溶池温度控制对脱磷效果的影响较弱。
2.2 碱度的影响
五氧化二磷属于酸性氧化物,钢渣中氧化钙、氧化镁、氧化锰、氧化铁等碱性氧化物,一定程度上降低五氧化二磷的活度,其中氧化钙的脱磷能力最强。
在炼钢温度下,氧化钙反应生成的磷酸钙稳定性较高,氧化镁次之,而氧化锰和氧化铁则最弱。
因此,氧化钙是控制五氧化二磷活性的主要因素,氧化钙浓度的增加,且不与酸性氧化物发生反应,有助于降低磷含量。
脱磷效率会随着炉渣碱度的增减而升降,当炉渣碱度升高到3.5数值左右时,脱磷效果处于饱和状态,炉渣碱度的提高对脱磷效率作用不再显著。
如果氧化钙含量过多,导致氧化钙颗粒不能完全熔化,炉渣随之增加,炉渣的黏度也大大提升,此时炉渣的流动性减弱,脱磷反应动力学条件变差,最终使脱磷效率降低。
因此,在实际操作中,炉渣碱度一般被控制在3.0~3.5数值左右。
2.3 FeO含量的影响
炉渣中FeO含量是转炉脱磷技术的主要影响因素之一。
FeO既可以作为氧化剂加速磷的氧化,又可以将五氧化二磷结合成较稳定的磷酸盐化合物从而起到脱磷的作用。
在冶炼过程中,随着炉渣FeO含量的升高,炉渣氧化性也会增强,炉渣与钢水中磷含量的分配比也会随之增大,此时,CaO在渣中的溶解速度会随着FeO的升高而加快,有助于加快脱磷速度。
当FeO 含量较低时,石灰不容易被熔化,无法生成稳定的磷酸盐化合物,不利于脱磷的进行。
脱碳反应在转炉脱磷的中期会更剧烈,控制不当就会经常出现炉渣“返干”现象,回磷也随之加快,破坏转炉脱磷效果。
当FeO含量过高时,炉渣碱度会相对降低,与此同时会大量消耗铁。
所以,脱磷初期FeO含量一般控制在7%~9%左右,终渣FeO含量应不超过20%。
除此之外,实际操作中,氧化铁和碱度是共同对转炉脱磷效果产生的,炉渣碱度在2.8~3.5、FeO含量在18%~20%时,脱磷效率可以达到85%~90%左右。
当然,不同钢种对钢产品的终点碳含量也不尽相同。
在终点碳含量较高的情况下,氧化性也会随之降低,这一定程度上影响了脱磷效果。
随着钢液碳含量的提高,磷的分配系数随其提高而呈减小的趋势。
在一定温度条件下,熔池的碳浓度与氧浓度的乘积为一定值,因此,碳氧含量成反比,即碳含量越高,氧含量就越低,条件下熔渣中的FeO含量也越低。
而根据上述炉渣中FeO含量的影响效果分析,熔渣氧化性的高低会直接影响着脱磷的效果。
2.4 渣量的影响
除了以上溶池温度、炉渣碱度以及FeO含量对转炉脱磷效果有影响之外,渣量控制对转炉脱磷效果影响更大,因此,终渣的控制才是转炉脱磷的关键环节。
虽然,渣量并不影响脱磷的分配比,但在一定的分配比下,渣量的增加导致五氧化二磷的浓度降低,磷酸盐化合物含量也随之降低,有助于提高转炉脱磷效率。
但是,渣量过多钢水温度有影响,进而影响化渣效果,动力学条件不足,最终导致冶炼成本增加。
反之,渣量太少导致磷容量不足,从而进一步影响脱磷率。
除此之外,在实际操作中,分批造渣是控制较大渣量的重要手段之一,其可改善一次性大渣量在脱磷效果中的不足。
综上所述,溶池温度、炉渣碱度、渣量以及FeO含量等是转炉脱磷的重要影响因素。
首先,碱度影响磷的分配系数,碱度的提高导致磷的分配系数增大,脱磷效果增加。
但是,当碱度超过一定值后,碱度的增加对脱磷效率的影响会下降,最终达不到脱磷的高效率要求。
因此脱磷最佳效果是碱度控制在2.5~3.5范围内。
其次,炉渣中FeO含量是转炉脱磷技术的主要影响因素之一,FeO含量的提高会引起磷的分配系数增大,同样达到提高脱磷效率的效果。
再者,在冶炼过程中溶池温度与磷的分配系数成反相关,温度越高,磷的分配系数越低,因此低温有助于提高转炉脱磷效率。
最后,渣量是最重要的影响因素之一,终渣的控制才是转炉脱磷的关键环节。
渣量越大,脱磷效果越好。
总而言之,高碱度、高FeO含量、低温、大渣量是转炉脱磷效率提高的有利影响因素。
3.转炉脱磷工艺在我国的应用
随着经济的高速发展,为了加大低磷钢、超低磷钢市场供应,我国在转炉脱磷工艺上也在不断地研究探索,并取得了重大技术进步。
当前转炉脱磷工艺具有如下特点:转炉容积大、反应速度快、效率高、可节省造渣剂的用量等,有利于生产低磷钢以及超低磷钢。
目前国内常见的转炉脱磷工艺有:双渣法、单渣法以及转炉双联法等,其工艺特点主要是在冶炼前期尽早成渣,提高炉渣碱度为转炉脱磷创造有利条件,但这不适用于较大渣量的转炉脱磷操作;对于脱磷而言,双渣法效果比较单渣法更有优势,在实际生产中,转炉双渣法脱磷效率高达九成,但同时存在着转炉热量损失和冶炼周期延长等缺陷,因此亟待进一步改进。
结语
由于我国转炉脱磷研究起步较晚,因此与众多发达国家相比技术还不够成熟,然而历时数十年探索实践,国内转炉脱磷工艺已经取得较大的进展。
笔者期望通过本文对转炉脱磷技术影响因素的探究,为我国转炉脱磷工艺改进提供绵薄之力。
参考文献
[1]邱鑫.转炉双联脱磷工艺过程成渣路线的理论及实验研究[D].重庆大学,2013.。