普通车床螺纹车削常见故障及解决方法
车削螺纹时常见故障及解决方法

车削螺纹时常见故障及解决方法螺纹车削是机械加工中的一项重要工艺,常用于制作螺栓、螺母等产品。
在车削螺纹过程中,有时会遇到一些常见的故障,如螺纹断裂、螺纹毛刺等问题。
本文将针对这些常见故障,给出相应的解决方法。
一、螺纹断裂螺纹断裂是车削螺纹中最常见的故障之一,主要原因有以下几点:1. 切削量过大。
车削螺纹时,如果一次性切削量过大,容易导致螺纹切削力过大,从而造成螺纹断裂。
2. 车削速度过高。
车削速度过高,会使螺纹材料在车削过程中产生过热现象,从而影响螺纹强度,导致断裂。
3. 切削刃磨损严重。
切削刃磨损严重会导致螺纹车削时切削力不均匀,从而容易引起断裂。
解决方法:1. 合理控制切削量。
在车削螺纹时,应根据工件的材料和尺寸,选择合适的切削量,避免一次性过大的切削力。
2. 控制切削速度。
根据螺纹材料的硬度和热处理情况,选择合适的切削速度,避免过高的车削速度造成螺纹断裂。
3. 及时更换刀具。
定期检查和更换切削刃,保证切削刃的锐利度,避免因刀具磨损产生过大的切削力。
二、螺纹毛刺螺纹毛刺是车削螺纹常见的表面缺陷之一,主要原因有以下几点:1. 加工精度不高。
车削螺纹时,如果刀具偏斜、工件夹紧不稳定等,容易导致精度不高,从而产生毛刺。
2. 切削液不合适。
切削液在车削螺纹时起到冷却、润滑的作用,选用不合适的切削液容易造成毛刺。
3. 刀具磨损严重。
刀具磨损严重会导致切削力不均匀,从而产生毛刺。
解决方法:1. 提高加工精度。
在车削螺纹前,检查刀具和夹持装置,确保工艺参数设置正确,以提高加工精度。
2. 合理选择切削液。
根据螺纹材料的特性和切削条件,选择合适的切削液,保证切削液的冷却和润滑效果,减少毛刺。
3. 及时更换刀具。
定期检查和更换刀具,保证刀具的切削锋利度,减少切削力不均匀引起的毛刺问题。
三、螺纹尺寸不准确螺纹尺寸不准确是车削螺纹常见的质量问题之一,主要原因有以下几点:1. 刀具磨损不均匀。
刀具磨损不均匀会导致切削力不均匀,从而影响螺纹尺寸的精度。
浅谈车床加工螺纹常见故障及解决方法
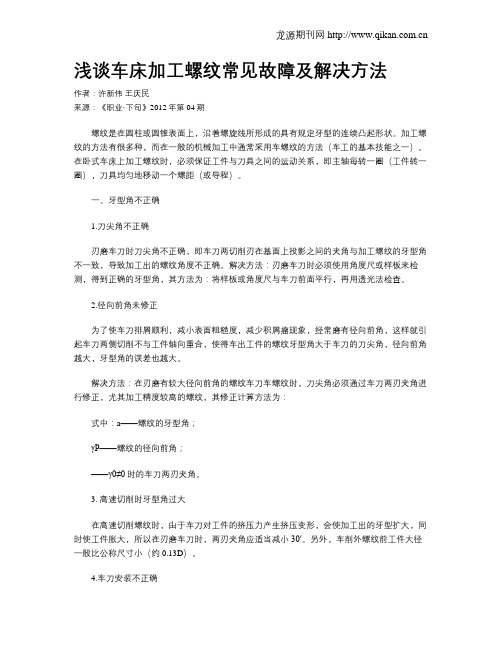
浅谈车床加工螺纹常见故障及解决方法作者:许新伟王庆民来源:《职业·下旬》2012年第04期螺纹是在圆柱或圆锥表面上,沿着螺旋线所形成的具有规定牙型的连续凸起形状。
加工螺纹的方法有很多种,而在一般的机械加工中通常采用车螺纹的方法(车工的基本技能之一)。
在卧式车床上加工螺纹时,必须保证工件与刀具之间的运动关系,即主轴每转一圈(工件转一圈),刀具均匀地移动一个螺距(或导程)。
一、牙型角不正确1.刀尖角不正确刃磨车刀时刀尖角不正确,即车刀两切削刃在基面上投影之间的夹角与加工螺纹的牙型角不一致,导致加工出的螺纹角度不正确。
解决方法:刃磨车刀时必须使用角度尺或样板来检测,得到正确的牙型角,其方法为:将样板或角度尺与车刀前面平行,再用透光法检查。
2.径向前角未修正为了使车刀排屑顺利,减小表面粗糙度,减少积屑瘤现象,经常磨有径向前角,这样就引起车刀两侧切削不与工件轴向重合,使得车出工件的螺纹牙型角大于车刀的刀尖角,径向前角越大,牙型角的误差也越大。
解决方法:在刃磨有较大径向前角的螺纹车刀车螺纹时,刀尖角必须通过车刀两刃夹角进行修正,尤其加工精度较高的螺纹,其修正计算方法为:式中:a——螺纹的牙型角;γP——螺纹的径向前角;——γ0≠0时的车刀两刃夹角。
3. 高速切削时牙型角过大在高速切削螺纹时,由于车刀对工件的挤压力产生挤压变形,会使加工出的牙型扩大,同时使工件胀大,所以在刃磨车刀时,两刃夹角应适当减小30′。
另外,车削外螺纹前工件大径一般比公称尺寸小(约0.13D)。
4.车刀安装不正确车刀安装不正确即车刀两切削刃的对称中心线与工件轴线不垂直,造成加工出的牙型角倾斜(俗称倒牙)。
解决方法:用角度尺或样板来安装车刀,使对称中线与工件轴线垂直,并且刀尖与工件中心等高。
5.刀具磨损刀具磨损后没有及时刃磨,造成加工出的牙型角两侧不是直线而是曲线或“乱牙”。
解决方法:合理选用切削用量,车刀磨损后及时刃磨。
二、螺距(或导程)不正确1.螺纹全长不正确螺纹全长不正确的原因是交换齿轮计算或组装错误,进给箱、溜板箱有关手柄位置扳错,可重新检查进给箱手柄位置或验算挂轮。
普通车床上车削螺纹常见故障举析
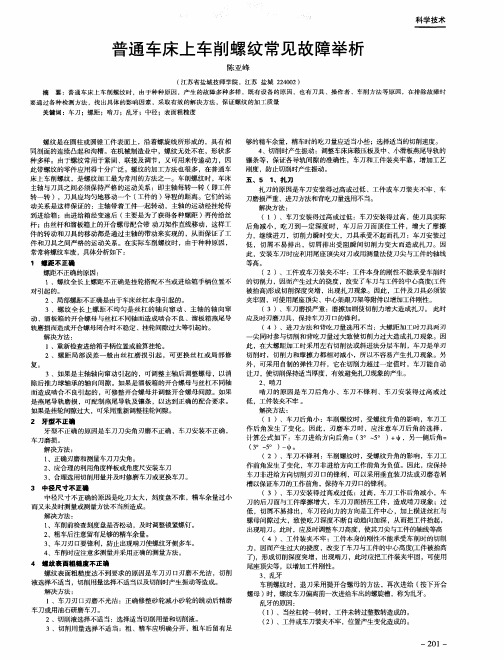
够的精车余量,精车时的吃刀量应适当小些 ; 选择适当的切削速度。 4 、切削时产生振动:调整车床床鞍压板及 中、 小滑板燕 尾导轨的 镶条等 ,保证各 导轨 间隙的准确性 ,车刀和工件装夹牢靠,增加工艺
刚度 ,防止切削时产生振动 。
五 、5 1 、扎 刀
杆 ;由丝杆和溜板箱上 的开合螺母配合带 动刀架作直线移动 ,这样 l T 件的转动和刀具的移动都是通过主轴的带动来实现的 ,从而保证 了工 件和刀具之间严格 的运动关系 。在实际车削螺纹 时,由于种种原因 ,
科学技术
普通 车床上车削螺纹常见 故障举析
陈亚峰
( 江苏省 盐 城技 师学 院 ,江 苏பைடு நூலகம்盐城 2 2 4 0 0 2 )
摘 要 :普 通 车床 上 车削螺 纹 时 ,由 于种种 原 因 ,产生 的 故障 多种 多样 ,既有 设备 的原 因 ,也有 刀 具 、操作 者 、车 削方 法等 原 因 ,在 排 除故 障时 要 通过 各 种检 测方 法 ,找 出具 体 的影响 因 素 ,采 取 有效 的解 决 方法 ,保 证螺 纹 的加工 质量 关键 词 :车刀 ;螺 距 ;啃刀 ;乱牙 ;中径 ;表面 粗糙 度
常常将螺纹车废,具体分析如下 :
1 螺距不正确 螺距不正确的原因: 1、 螺纹全长上螺距不正确是挂轮搭配不 当或进给箱手柄位置不
对引起的。
2 、局部螺距不正确是 由于车床丝杠本身引起 的。 3、螺纹全 长上螺距 不均匀是 丝杠的轴 向窜动 、主轴的轴 向窜 动 、溜板箱的开合螺母与丝杠不同轴而造成啮合不 良、溜板箱燕尾导 轨磨损而造成开合螺母闭合时不稳定 、挂轮间隙过大等引起的。
螺纹是在圆柱 或圆锥工件表面上 ,沿着螺旋 线所形成 的,具有相 同剖 面的连续 凸起和沟槽 。在机械制造业 中,螺纹无处不在 ,形状多 种多样。由于螺纹常用于紧 固、 联 接及调节 ,又可用来传递动力 ,因 此带螺纹的零件应用得十分广泛。螺纹 的加工方法也很多 ,在普通车 床上车削螺纹 ,是螺纹加工最为常用 的方法之一 。车削螺纹时 ,车床 主轴与刀具之 间必须保持严格的运 动关 系:即主轴每转一转 ( 即工件 转一转 ),刀具应均匀地移动一个 ( 工件 的 ) 导程的距离 。它 们的运 动关系是这样保证 的:主轴带着工件一起转动 ,主轴的运动经挂轮传 到进给箱 ;由进给箱经变速后 ( 主要是 为了获得各种螺距 ) 再传 给丝
车削螺纹时常见故障及解决方法
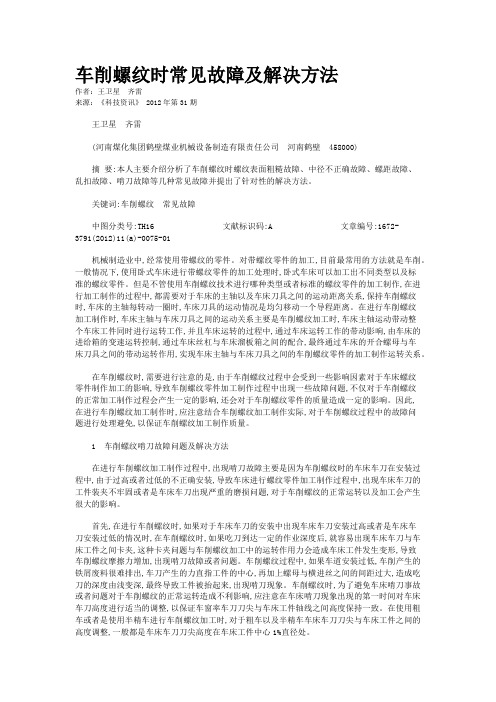
车削螺纹时常见故障及解决方法作者:王卫星齐雷来源:《科技资讯》 2012年第31期王卫星齐雷(河南煤化集团鹤壁煤业机械设备制造有限责任公司河南鹤壁 458000)摘要:本人主要介绍分析了车削螺纹时螺纹表面粗糙故障、中径不正确故障、螺距故障、乱扣故障、啃刀故障等几种常见故障并提出了针对性的解决方法。
关键词:车削螺纹常见故障中图分类号:TH16 文献标识码:A 文章编号:1672-3791(2012)11(a)-0075-01机械制造业中,经常使用带螺纹的零件。
对带螺纹零件的加工,目前最常用的方法就是车削。
一般情况下,使用卧式车床进行带螺纹零件的加工处理时,卧式车床可以加工出不同类型以及标准的螺纹零件。
但是不管使用车削螺纹技术进行哪种类型或者标准的螺纹零件的加工制作,在进行加工制作的过程中,都需要对于车床的主轴以及车床刀具之间的运动距离关系,保持车削螺纹时,车床的主轴每转动一圈时,车床刀具的运动情况是均匀移动一个导程距离。
在进行车削螺纹加工制作时,车床主轴与车床刀具之间的运动关系主要是车削螺纹加工时,车床主轴运动带动整个车床工件同时进行运转工作,并且车床运转的过程中,通过车床运转工作的带动影响,由车床的进给箱的变速运转控制,通过车床丝杠与车床溜板箱之间的配合,最终通过车床的开合螺母与车床刀具之间的带动运转作用,实现车床主轴与车床刀具之间的车削螺纹零件的加工制作运转关系。
在车削螺纹时,需要进行注意的是,由于车削螺纹过程中会受到一些影响因素对于车床螺纹零件制作加工的影响,导致车削螺纹零件加工制作过程中出现一些故障问题,不仅对于车削螺纹的正常加工制作过程会产生一定的影响,还会对于车削螺纹零件的质量造成一定的影响。
因此,在进行车削螺纹加工制作时,应注意结合车削螺纹加工制作实际,对于车削螺纹过程中的故障问题进行处理避免,以保证车削螺纹加工制作质量。
1 车削螺纹啃刀故障问题及解决方法在进行车削螺纹加工制作过程中,出现啃刀故障主要是因为车削螺纹时的车床车刀在安装过程中,由于过高或者过低的不正确安装,导致车床进行螺纹零件加工制作过程中,出现车床车刀的工件装夹不牢固或者是车床车刀出现严重的磨损问题,对于车削螺纹的正常运转以及加工会产生很大的影响。
车削螺纹时常见故障及解决方法

车工技师论文摘要:螺纹是在圆柱工作表面上,沿着螺旋线所形成的具有相同剖面的连续凸起和沟槽,在机械制造中,螺纹零件应用十分广泛,用车削的方法加工螺纹,是目前常用的加工方法,在卧式车床(C6140)上车削米制、英制、模数和径制四种标准螺纹,无论哪螺纹种,车床主轴与刀具之间必须保持严格的动运关系:即:主轴每转一转(工件转一转),刀具的运动经挂轮到进给箱。
由进给箱变速(获得各种螺距)传给丝杠,由丝杠和溜板箱上的开合螺母配合带动刀架作直线移动,这样工件和转动和刀具的移动都是通过主轴带动来实现的,从而保证了工件和刀具之间严格的运动关系。
在实际车削螺纹时,由于多种原因,造成由主轴到刀具之间的运动关系在某一环节出现问题,引起车削螺纹时产生废次品,影响正常加工生产及经济效益。
关键词:螺纹、故障、解决方案1、扎刀故障分析:⑴、原因是车刀安装得过高或过低:车刀安装得过高,使刀具实际后角减小,则吃刀到一定深度时,车刀的后刀面顶住工件,增大摩擦力,甚至把工件顶弯,造成扎刀现象;车刀安装得过低,使刀具实际前角增大,则切屑不易排出,造成扎刀。
⑵、工件或车刀装夹不牢:工件本身的刚性不能承受车削时的切削力,因而产生过大的挠度,改变了车刀与工件的中心高度(工件被抬高)形成切削深度突增,出现扎刀现象。
⑶、车刀磨损严重:磨擦加剧使切削力增大造成扎刀。
⑷、进刀方法和进给量选用不当:大螺距加工时刀具两刃一尖同时参与切削和进给量过大致使切削力过大造成扎刀现象。
解决方法:⑴、安装车刀时利用尾座顶尖对刀或用测量法使刀尖与工件的轴线等高。
[在粗车和半精车时,刀尖位置比工件的中心高出1%D约为0.2~0.5mm,D=工件直径。
]⑵、工件及刀具必须装夹牢固,可使用尾座顶尖中心架跟刀架等附件以增加工件刚性。
⑶、正确及时刃磨刀具几何角度参数。
如下图:⑷、在大螺距加工时采用左右切削法或斜进法进行,车刀是单刃切削的,切削力和摩擦力都相对减小,所以不容易产生扎刀现象。
普通车床常见故障分析与排除

普通车床常见故障分析与1、刀具工件之间引起的振动;1、检查刀杆伸出量,太长容易颤振,应缩短,一般L≤1.5b;调整刀尖安装位置,使刀尖略高于工件中心线,但高出量不超过0.5mm;采用正前角切削,过渡刃不易太大,始终保持其切削性能。
2、光杆弯曲变形引起溜板的浮动;拆下光杆进行校直。
3、电动机旋转不平稳及皮带轮摆振等原因引起机床振动。
3、检修电机,最好将电机转子进行动平衡。
消除皮带轮振摆,对其进行光整车削修正。
1、片式摩离合器调整过松或磨损,或摩擦片翘曲变形;1、调整好离合器片接触松紧度,更换或修理磨损、翘曲的摩擦片。
2、主轴箱体主轴孔与滚动轴承外环配合松动;2、用压套或镀镍的方法修复;3、带式制动器(刹车)没有调整好;3、调整带式制动器的刹车阻力;4、电动机传动皮带过松打滑;4、调整皮带的松紧程度;5、电动机功率达不到额定值;5、检查电机的联接和电流、电压值,要求功率达到额定标准;6、主轴箱内滑动齿轮定位失灵,使齿轮脱开;6、加大定位件的弹簧力;7、操纵离合器的拨叉或杠杆(元宝销)磨损。
7、修复磨损部位,严重的予以更新。
1、床身导轨磨损使溜板倾斜下沉,造成开合螺母与丝杠(呈单片啮合);1、用补偿法修复导轨,恢复尺寸链精度。
2、托架支撑孔磨损,造成丝杠回转中心线不稳定;2、托架支撑孔采取镗孔镶套。
3、方刀架与小刀架底板接触不良;3、修刮刀架底座前,恢复接触精度。
4、丝杠轴向窜动过大。
4、调整丝杠的轴向间隙,一般间隙应≤0.01mm。
1、床身齿条表面在某处凸起或齿条接缝处齿距误差过大;1、检查校正导轨齿条接缝,修整齿条凸出的表面,或更换新齿条,使其达到要求。
2、床身导轨在固定的长度位置上有碰伤凸痕等2、修刮或用油石磨去凸痕或毛刺等。
1、主轴滚动轴承的某一粒或几颗滚柱磨损严重;1、更换轴承、2、主轴上的传动齿轮节径振摆过大。
2、消除主轴齿轮的节径振摆,或更换齿轮副。
14工件端面出现螺纹状波纹1、主轴后端推力球轴承中,某一粒滚珠尺寸特大。
车削螺纹时常见故障及解决方法
车削螺纹时常见故障及解决方法在机械加工中,车削螺纹是一项基本技能。
然而,在操作过程中经常会发生一些故障,例如螺纹深度不够、刀具磨损过快等,这些问题会影响到加工效率和产品质量。
本文将介绍几种常见的车削螺纹故障及其解决方法。
1. 螺纹深度不够螺纹深度不够是一个常见而难以发现的问题,经常在现场加工中出现。
它通常是由于刀具高度不够或车削深度过浅引起的。
以下是解决该问题的方法:•提高刀具高度:可以通过增加支撑刀杆高度或调整刀具上的螺纹垫片来解决。
•增加车削深度:可以通过增加刀具与工件的接触时间或增加刀具超前量来解决。
2. 刀具磨损过快刀具磨损过快通常是由于切削速度太高或切削深度过大引起的。
如果您遇到这种问题,请参考以下建议:•降低切削速度:将切削线速降低到合适的范围内,通常介于5~20 m/min。
•降低切削深度:通过减少车削深度来降低切削负荷。
•更换高质量的刀具:选择具有高刚性和切削耐受性的刀具,可以显著提高刀具的使用寿命。
3. 螺纹折断或错位螺纹折断或错位通常是由于不当的刀具选择、不均匀的切削、机床闲置时间过长和工件内部缺陷引起的。
为了防止发生这种情况,请使用以下技巧:•选择合适的工具:使用专业用于螺纹车削的刀具,确保刀具的角度和尺寸正确。
•均匀切削:确保刀具与工件之间的接触均匀,并避免在工件周边产生太多的压力。
•机床保养:确保机床在加工前和加工后进行适当的保养,防止闲置过长,影响机床的性能。
4. 边角毛刺边角毛刺通常是由于刀尖磨损、粗糙的工件表面和不规则的车刀线轮廓等原因引起的。
如果您的工件出现边角毛刺,可以尝试以下措施:•更换刀具:将刀具钝化或磨损过度的刀具更换为新的刀具。
•改进车床设置:通过改变车床的速度、进给和角度等参数来改善车削表面的粗糙度。
•维护工件表面:对工件表面进行抛光、喷砂或磨削等操作,以改善表面质量。
5. 超出公差范围对于车削螺纹来说,公差范围非常重要。
如果您的工件超出了规定的公差范围,则可能会导致部件的不适合和效率低下。
车削螺纹时常见故障及解决方法范本
车削螺纹时常见故障及解决方法范本在车削螺纹的过程中,常会遇到一些常见的故障,比如螺纹断裂、螺纹质量不合格、刀具磨损严重等。
下面是一些常见的故障及解决方法范本:一、螺纹断裂:故障原因:螺纹材料硬度过高,切割力过大,导致螺纹断裂。
解决方法:使用更适合的刀具材料,减小切削力,合理调整车削参数。
如果螺纹断裂发生在材料较薄的部位,可以采用退刀或退刀速度减小的方法解决。
二、螺纹质量不合格:故障原因:刀具磨损严重,切削液不足,车削参数不合理等。
解决方法:及时更换磨损严重的刀具,调整切削液供给量,合理选择车削参数。
注意刀具的冷却和润滑,以保证螺纹的质量。
三、刀具磨损严重:故障原因:切削条件不合理,切削液不足,刀具质量不佳等。
解决方法:调整切削条件,增加切削液的供给量,更换质量较好的刀具。
合理选择刀具材料和刀具形状,可以延长刀具的使用寿命。
四、刀具断裂:故障原因:刀具材料问题,切削参数不合理,刀具过热等。
解决方法:选择更合适的刀具材料,调整切削参数。
注意刀具的冷却和润滑,以避免刀具过热断裂的问题。
五、螺纹内外径不一致:故障原因:车床的进给不稳定,刀具磨损不均匀,切削液不足等。
解决方法:调整车床的进给机构,保持稳定的进给量。
及时更换磨损严重的刀具,增加切削液的供给量。
六、螺纹表面粗糙:故障原因:刀具磨损严重,车削参数不合理,切削液不足等。
解决方法:更换磨损严重的刀具,调整合理的车削参数。
增加切削液的供给量,以保证螺纹表面的质量。
总之,对于车削螺纹过程中的常见故障,应根据具体情况进行分析,并采取相应的解决方法。
只有不断总结经验,提高技术水平,才能有效地解决故障,提高车削螺纹的质量和效率。
普通车床螺纹车削常见故障及解决方法(三篇)
普通车床螺纹车削常见故障及解决方法1. 放松刀夹:在车削过程中,如果刀夹没有固定好,会导致刀具松动或者偏位,从而造成螺纹不良。
解决方法是检查刀夹固定螺母是否紧固,如果松动则重新固定。
2. 刀具磨损:长时间使用刀具会磨损,导致刀尖变钝,从而无法进行正常的车削。
解决方法是更换刀具,保持刀具的锐利度。
3. 机床不稳定:如果机床本身存在不稳定的问题,例如床身变形、主轴不平衡等,会导致螺纹加工时产生偏差。
解决方法是定期检测和调整机床,确保其稳定性。
4. 刀具与工件匹配不良:在螺纹车削过程中,刀具与工件的匹配也非常重要。
如果选用的刀具尺寸不合适,就会导致螺纹加工结果不理想。
解决方法是选择合适尺寸的刀具,确保刀具与工件的配合良好。
5. 刀具进给速度不恰当:刀具进给速度过快或者过慢都会影响螺纹加工的质量。
解决方法是根据不同的工件材料和螺纹规格,调整刀具的进给速度,确保加工的质量。
6. 冷却液不适用:在螺纹车削过程中,适当使用冷却液可以降低温度,减少摩擦,提高切削润滑效果,从而改善加工质量。
如果使用的冷却液性质不合适,也会影响螺纹加工结果。
解决方法是选择合适的冷却液,根据加工工件的要求进行选择。
7. 机床刚度不足:机床刚度不足会导致在螺纹车削过程中产生振动和共振,造成螺纹不良。
解决方法是增加机床的刚度,例如加强机床床身的结构,增加加工时的稳定性。
8. 机床零件磨损:长时间使用机床,有些零部件会磨损,例如导轨、导向轨等,会导致加工误差。
解决方法是定期检查和更换机床零部件,保证机床的准确性和稳定性。
总之,普通车床螺纹车削常见故障的解决方法就是:确保刀具的固定和锐利度,稳定机床的结构和性能,选择合适尺寸和质量的刀具,调整进给速度和冷却液的使用,定期检查和维护机床零部件,确保加工质量和效果。
普通车床螺纹车削常见故障及解决方法(二)车床螺纹车削是机械加工中常见的一种加工方式,常用于制作螺纹零件。
然而,在车削过程中,可能会遇到一些常见的故障。
车削螺纹时常见的故障相应的解决方法
车削螺纹时常见的故障相应的解决方法作者:孟令新李智慧来源:《卷宗》2012年第04期螺纹是在圆柱工件表面上,沿着螺旋线所形成的,具有相同剖面的连续凸起和沟槽,在机械制造业中,带螺纹的零件应用得十分广泛。
用车削的方法加工螺纹,是目前常用的加工方法。
在车削螺纹时,由于各种原因会引起多种多样的故障,影响正常生产;在排除故障时要具体情况具体分析,才能采取有效方法进行解决,车削螺纹时常见故障及解决方法如下:一、牙型角不正确1.刀尖角不正确刃磨车刀时刀尖角不正确,即车刀两切削刃在基面上投影之间的夹角与加工螺纹的牙型角不一致,导致加工出的螺纹角度不正确。
解决方法:刃磨车刀时必须使用角度尺或样板来检测,得到正确的牙型角,其方法为:将样板或角度尺与车刀前面平行,再用透光法检查。
常用的公制螺纹牙型角:三角形螺纹60°,梯形螺纹30°,蜗杆40°(单边20°)。
2.径向前角未修正为了使车刀排屑顺利,减小表面粗糙度,减少积屑瘤现象,经常磨有径向前角,这样就引起车刀两侧切削不与工件轴向重合,使得车出工件的螺纹牙型角大于车刀的刀尖角,径向前角越大,牙型角的误差也越大。
同时使车削出的螺纹牙型在轴向剖面内不是直线,而是曲线,影响螺纹副的配合质量。
解决方法:在刃磨有较大径向前角的螺纹车刀车螺纹时,刀尖角必须通过车刀两刃夹角进行修正。
3.高速切削时牙型角过大在高速切削螺纹时,由于车刀对工件的挤压力产生挤压变形,会使加工出的牙型扩大,同时使工件胀大,所以在刃磨车刀时,两刃夹角应适当减小30′。
另外,车削外螺纹前工件大径一般比公称尺寸小(约0.13P)。
4.车刀安装不正确车刀安装不正确即车刀两切削刃的对称中心线与工件轴线不垂直,造成加工出的牙型角倾斜(俗称倒牙)。
解决方法:用角度尺或样板来安装车刀,使对称中线与工件轴线垂直,并且刀尖与工件中心等高。
5.刀具磨损刀具磨损后没有及时刃磨,造成加工出的牙型角两侧不是直线而是曲线或“烂牙”。
- 1、下载文档前请自行甄别文档内容的完整性,平台不提供额外的编辑、内容补充、找答案等附加服务。
- 2、"仅部分预览"的文档,不可在线预览部分如存在完整性等问题,可反馈申请退款(可完整预览的文档不适用该条件!)。
- 3、如文档侵犯您的权益,请联系客服反馈,我们会尽快为您处理(人工客服工作时间:9:00-18:30)。
普通车床螺纹车削常见故障及解决方法车削螺纹时常见故障及解决方法如下:
1.啃刀
原因是车刀安装的过高或过低,工件装夹不牢或车刀磨损过大。
车刀安装得过高,则吃刀到一定深度时,车刀的后刀面支撑住工件,增大摩擦力,甚至把工件支撑弯,造成啃刀现象;过低,则切屑不
易排出,车刀背向力的方向是工件中心,加上横进丝杠与螺母间隙
过大,至使背吃刀量不断自动趋向加大,从而把工件抬起,出现啃刀。
此时,应及时调整车刀高度,使其刀尖与工件的轴线等高(可利用尾座支撑刀尖对刀,也可用加工工件试切法对刀)。
在粗车和半精车时,刀尖位置比工件的中心高出工件直径的1%。
工件装夹不牢,
工件本身的刚性不能承受车削时的切削力,因而产生过大的挠度,
改变了车刀与工件的中心高度(工件被抬高了),形成背吃刀量突增,出现啃刀,此时应把工件装夹牢固,使用尾架支撑顶尖、中心架等,以增加工件刚性。
车刀磨损过大引起切削力增大,支撑弯工件,出
现啃刀。
此时,应对工件加以修磨。
2.乱扣
原因是当丝杠转一转时,工件未转过整数转而造成的。
当车床丝杠螺距与工件螺距不成整倍数时,如果退刀,采用打开开合螺母的方法将床鞍摇至起始位置,那么,再次闭合开合螺母时,就会发生车刀刀尖不在前一刀所车出的螺旋槽内,以致出现乱扣。
解决方法是采用正反车法来退刀,即在第一次行程结束时,不提起开合螺母,把刀沿径向退出后,将主轴反转,使车刀沿纵向退回,再进行第二次行程,这样往复过程中,因主轴、丝杠和刀架之间的传动没有分离过,车刀始终在原来的螺旋槽中,就不会出现乱扣。
对于车削车床丝杠螺距与工件螺距成整数倍的螺纹,可采用打开开合螺母法进行加工,工件和丝杠都在旋转,提起开合螺母后,至少要等丝杠转过一转,才能重新合上开合螺母,这样当丝杠转过一转时,工件转了整数倍转,车刀就能进入前一刀车出的螺旋槽内,就不会出现乱扣。
这样退刀快,有利于提高生产率和保持丝杠精度,同时丝杠也较安全。
3.螺距不正确
螺纹全长上不正确,原因是交换齿轮搭配不当或进给箱手柄位
置不对,可重新检查进给箱手柄位置或验算交换齿轮。
局部不正确,原因是由于车床丝杠本身的螺距局部误差(一般由磨损引起),可更换丝杠或局部修复。
螺纹全长上螺距不均匀,原因是:丝杠的轴向窜动、主轴的轴向窜动、溜板箱的开合螺母与丝杠不同轴而造成啮合
不良、溜板箱燕尾导轨磨损而造成开合螺母闭合时不稳定、交换齿
轮的间隙过大等。
通过检测:如果是丝杠轴向窜动造成的,可对车
床丝杠与进给箱连接处的调整螺母进行调整,以消除连接处推力球
轴承轴向间隙;如果是主轴轴向窜动引起的,可调整主轴后调整螺母,以消除后推力球轴承的轴向间隙;如果是溜板箱的开合螺母与
丝杠不同轴而造成啮合不良引起的,可修整开合螺母并调整开合螺
母间隙;如果是燕尾导轨磨损,可配制燕尾导轨及镶条,以达到正
确的配合要求;如果是交换齿轮间隙过大,可重新调整交换齿轮间隙;如果出现竹节纹,原因是从主轴到丝杠之间的齿轮传动有周期
性误差引起的,如交换齿轮箱内的齿轮、进给箱内的齿轮,由于本
身制造误差、局部磨损或齿轮在轴上安装偏心等造成旋转中心低,
从而引起丝杠旋转周期性不均匀,导致竹节纹的出现,可以修换有
误差或磨损的齿轮。
4.中径不正确
原因是吃刀量太大,刻度盘不准,刀具刃磨不准,而又未及时
测量所造成。
解决方法是精车时要详细检查刻度盘是否松动,精车
余量要适当,车刀刃磨角度要正确、刃口要锋利,并要及时测量。
5.螺纹表面粗糙
原因是车刀刃口磨得不光洁,切削液不适当,切削速度和工件
材料不适合以及切削过程产生振动造成。
解决方法是:正确修整砂
轮或用油石精研刀具;选择适当切削速度和切削液;调整车床床鞍
压板及中、小滑板燕尾导轨的镶条等,保证各导轨间隙的准确性,
防止切削时产生振动。
总之,车削螺纹时产生的故障形式多种多样,既有设备的原因,也有刀具、操作者等的原因,在排除故障时要具体情况具体分析,
通过各种检测和诊断手段,找出具体的影响因素,采取有效的解决
方法。