催化裂化催化剂
催化裂化催化剂主要成分
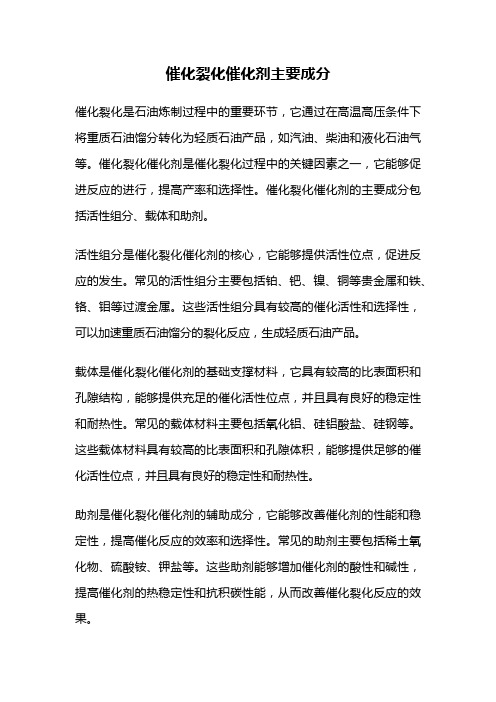
催化裂化催化剂主要成分催化裂化是石油炼制过程中的重要环节,它通过在高温高压条件下将重质石油馏分转化为轻质石油产品,如汽油、柴油和液化石油气等。
催化裂化催化剂是催化裂化过程中的关键因素之一,它能够促进反应的进行,提高产率和选择性。
催化裂化催化剂的主要成分包括活性组分、载体和助剂。
活性组分是催化裂化催化剂的核心,它能够提供活性位点,促进反应的发生。
常见的活性组分主要包括铂、钯、镍、铜等贵金属和铁、铬、钼等过渡金属。
这些活性组分具有较高的催化活性和选择性,可以加速重质石油馏分的裂化反应,生成轻质石油产品。
载体是催化裂化催化剂的基础支撑材料,它具有较高的比表面积和孔隙结构,能够提供充足的催化活性位点,并且具有良好的稳定性和耐热性。
常见的载体材料主要包括氧化铝、硅铝酸盐、硅钢等。
这些载体材料具有较高的比表面积和孔隙体积,能够提供足够的催化活性位点,并且具有良好的稳定性和耐热性。
助剂是催化裂化催化剂的辅助成分,它能够改善催化剂的性能和稳定性,提高催化反应的效率和选择性。
常见的助剂主要包括稀土氧化物、硫酸铵、钾盐等。
这些助剂能够增加催化剂的酸性和碱性,提高催化剂的热稳定性和抗积碳性能,从而改善催化裂化反应的效果。
催化裂化催化剂的制备过程通常包括活性组分的负载、载体的制备和助剂的添加。
活性组分的负载是将活性组分与载体进行物理或化学吸附,使其均匀分散在载体的表面,增加催化剂的活性位点。
载体的制备是通过合成和煅烧等工艺,将原料转化为具有良好孔隙结构和稳定性的载体材料。
助剂的添加是在载体上加入一定量的助剂,通过改变催化剂的酸碱性质和热稳定性,提高催化剂的性能和稳定性。
催化裂化催化剂的性能主要取决于活性组分的选择和负载量、载体的比表面积和孔隙结构、助剂的种类和添加量等因素。
合理选择催化剂的成分和制备工艺,可以提高催化裂化反应的效率和选择性,降低能耗和环境污染。
因此,催化裂化催化剂的研究和开发对于石油工业的发展具有重要意义。
催化裂化催化剂的发展历程及研究进展

催化裂化催化剂的发展历程及研究进展催化裂化是一种重要的石油加工技术,通过将石油分子在催化剂的作用下进行裂解,得到高附加值的产品,如汽油和石脂油。
催化裂化催化剂的发展历程可以追溯到20世纪初,经过了多个阶段的演进和改进。
本文将详细介绍催化裂化催化剂的发展历程及研究进展。
20世纪初,催化裂化催化剂主要采用天然矿物催化剂,如石英、蛭石等。
这些催化剂具有一定的催化活性,但缺乏稳定性和选择性,难以应对复杂的原料和严苛的工业操作条件。
20世纪30年代,随着石油需求的增加和技术的进步,人们开始研发新型催化剂。
那时,主要采用的是氧化物催化剂,如铝、硅等。
这些催化剂的活性和稳定性有了一定的提升,但仍然存在一些问题,如选择性不高、催化剂寿命短等。
20世纪50年代,人们开始尝试使用酸性功能组分的催化剂,如酸化铁、硫酸等。
这些催化剂具有较高的催化活性和选择性,但具有腐蚀性,容易造成催化剂失效和设备损坏。
20世纪60年代,人们将焦油催化裂化硅铝酸催化剂推向了催化裂化工业化生产的舞台。
这种催化剂具有良好的热稳定性和选择性,能够实现高效的催化裂化反应。
焦油催化裂化硅铝酸催化剂的应用推动了石油工业的发展,成为当时催化裂化的主流技术。
近年来,催化裂化催化剂的研究进展主要集中在以下几个方面:1.催化剂结构设计:通过调控催化剂的孔径分布、酸中心密度和酸强度等结构参数,以提高其活性、选择性和稳定性。
常见的结构设计方法包括合金化、钾的添加、微介孔化等。
2.催化剂负载材料研究:将催化剂负载在合适的载体上,可以提高催化剂的分散性和稳定性。
常用的载体材料包括Al2O3、SiO2、TiO2等。
3.催化剂表面改性:通过表面改性的方法,如纳米粒子修饰、溶胶-凝胶法制备等,可以改变催化剂的活性中心和表面酸性,以提高其催化效果。
4.新型催化剂开发:人们正在探索使用新型催化剂,如纳米材料、金属有机骨架材料(MOFs)等,以提高催化裂化过程的效率和选择性。
催化裂化催化剂

催化裂化催化剂催化裂化催化剂是一种具有特殊作用的化学物质,在物理学和化学的研究中起着重要作用。
它们常用于生物化学,有机化学,无机化学,营养学,药物化学,电化学和环境化学中,可以大大缩短反应时间,提高反应效率,节省能源,节约空间,从而更有效地为人们服务。
1. 催化裂化催化剂的作用- 降低反应活化能:催化剂分解反应物,使反应的活化能达到足够的低水平,从而使反应过程可以顺利进行。
- 抑制非催化反应:催化剂结合不参与反应的分子,阻止它们参与和持续的反应,因此,大大抑制了惰性分子,使反应更加有效率。
- 促进反应:催化剂可以在分子上形成特殊的反应态,并大大提高反应速度,促进反应顺利进行,使反应可以更有效地完成。
2. 催化裂化催化剂的选择- 选择催化剂时,要考虑被催化反应物的性质,例如:大部分催化剂只能催化液态的材料,但也有一些可以作用于固体物质的催化剂;- 还要考虑反应的条件,例如高温,低温,缺氧,高压等,反应的催化剂以及反应条件都是影响催化活性的关键因素;- 另外,要考虑催化剂的毒性,催化活性和相容性,选择的催化剂应该有较高的催化活性和较低的环境毒性。
3. 催化裂化催化剂的应用- 催化裂化催化剂用于液态燃料的低温催化燃烧,可以有效提高汽油和柴油等液态燃料的热效率;- 用于催化分解氧化物,可把硫氧化物和其他气态污染物分解为清洁的原料;- 也用于原料的催化裂解,可用于制备碳氢化合物,碳烃,溶剂和其他有机产品; - 催化裂化催化剂也用于homeostasis反应中,帮助维持身体正常情况;- 再大型工业反应中,也会使用到催化裂化催化剂,比如碳烃裂解,烯烃裂解,烯烃制备和提取等等,以有效地完成大面积反应。
总之,催化裂化催化剂是一种能够显著提高反应效率的特殊化学物质,用于广泛的研究领域,几乎无处不在。
如果遵循正确的选择原则,就可以获得良好的成果。
当然,还是要注意催化裂化催化剂的安全性,以免出现危险情况。
催化裂化催化剂的研究与应用

催化裂化催化剂的研究与应用催化裂化是一种重要的炼油工艺,其主要目的是将原油中的长链烃分子通过催化剂的作用裂解成更加有价值的短链烃分子。
催化裂化技术在炼油工业中具有广泛的应用,可以提高炼油产物的质量,并且有效地提高了炼油产品的产率。
而催化裂化催化剂的研究与应用则是催化裂化技术能够持续发展的重要保障。
一、催化裂化催化剂的研究现状催化裂化催化剂是催化裂化技术中最为关键的部分,其性能直接影响着催化裂化的效率和产品质量。
目前,催化裂化催化剂主要包括酸性固体催化剂和贵金属催化剂两大类。
酸性固体催化剂是催化裂化技术中使用最为广泛的催化剂,其主要成分包括硅铝酸盐和沸石等。
这类催化剂具有良好的酸性和孔道结构,可以有效地裂解重质原油中的长链烃分子。
近年来,随着炼油工业对产品质量要求的提高,科研人员对酸性固体催化剂的研究也在不断深入。
通过提高催化剂的酸性和表面积,优化催化剂的孔道结构等手段,使得酸性固体催化剂在催化裂化中的性能得到了显著提升。
贵金属催化剂是近年来催化裂化领域的一个研究热点。
与传统的酸性固体催化剂相比,贵金属催化剂具有更高的催化活性和选择性,可以实现更加精确的烃分子裂解,得到更加高品质的裂化产品。
目前,科研人员主要将贵金属催化剂应用于催化裂化技术中的深度加工环节,通过与酸性固体催化剂的结合使用,可以实现更加高效的原油加工和产品提纯。
二、催化裂化催化剂的应用现状催化裂化催化剂的应用主要体现在炼油工业中的实际生产中。
目前,国内外的炼油企业对催化裂化催化剂的应用已经非常成熟,可以实现从原油到成品油的高效加工转化。
在实际生产中,催化裂化催化剂的应用主要体现在以下几个方面:1.原油加工:催化裂化催化剂可以将重质原油中的长链烃分子裂解成较为轻质的烃类化合物,提高了成品油的产率,并且显著提高了成品油的质量。
在炼油厂的原油加工装置中,催化裂化催化剂是实现高效加工的关键。
2.产品提纯:通过催化裂化技术,可以将原油中的硫、氮、金属等杂质去除,得到更加纯净的成品油产品。
催化裂化催化剂密度

催化裂化催化剂密度催化裂化是一种重要的石油加工方法,可以将较重的石油馏分转化为更轻的产品,如汽油、液化石油气和石脑油等。
催化裂化反应需要催化剂的参与,其中催化剂的密度对反应的效果起到重要的影响。
催化裂化催化剂密度是指催化剂的单位体积质量,通常以g/cm³或kg/m³表示。
催化剂密度的选择与催化裂化反应的条件和要求密切相关。
催化剂密度的选择需要考虑反应器的体积和形状。
反应器通常是一个填充有催化剂的柱状容器,催化剂密度的大小将直接影响到催化剂的装填量。
如果催化剂密度过大,将会导致反应器容积的浪费,增加生产成本;而如果催化剂密度过小,反应器容积的利用率将降低,影响反应的效果。
因此,在选择催化剂密度时需要综合考虑反应器的大小和形状,以及生产成本和产量要求。
催化剂密度的选择还需要考虑反应器内气体和液体的传质和传热效果。
催化裂化反应是一个复杂的多相反应过程,需要气体和液体之间的传质和传热来实现。
催化剂密度的大小会影响气体和液体在催化剂颗粒之间的扩散速率,从而影响反应的速度和效果。
如果催化剂密度过大,将会限制气体和液体的扩散速率,降低反应速度;而如果催化剂密度过小,将会增加气体和液体的扩散路径,同样会降低反应速度。
因此,在选择催化剂密度时需要考虑气体和液体之间的传质和传热效果,以及反应速度和效果的要求。
催化剂密度的选择还需要考虑催化剂颗粒之间的机械强度。
催化裂化反应需要经历高温、高压和剧烈的气体和液体流动,催化剂颗粒之间会受到机械冲击和磨损。
催化剂密度的大小会直接影响催化剂颗粒之间的接触面积和接触力,从而影响催化剂颗粒的机械强度。
如果催化剂密度过大,催化剂颗粒之间的接触面积和接触力将增加,催化剂颗粒容易产生压碎和磨损;而如果催化剂密度过小,催化剂颗粒之间的接触面积和接触力将减小,催化剂颗粒的机械强度将降低。
因此,在选择催化剂密度时需要考虑催化剂颗粒的机械强度和催化剂寿命的要求。
催化裂化催化剂密度是影响催化裂化反应效果的重要因素。
催化裂化催化剂

催化裂化催化剂是一种用于催化裂化反应的化学物质,它可以促进反应的速度,节省
能源,减少废物,提高反应的效率和质量。
催化裂化反应是一种有机反应,它可以通过将
大分子的碳链分割成更小的碳链或气体而产生。
催化裂化催化剂是一种有机物,如硫酸盐、硅酸盐、过氧化物和酸类催化剂,它们具有活性位点,可以激活反应物,使反应变得更快、更有效。
催化裂化催化剂的主要应用是在石油和其他烃类化合物的加工中,以便用于生产汽油、柴油和其他燃料。
它们还可用于制造化学品,如聚合物、纤维素和合成橡胶,以及用于生
物燃料生产的烃类化合物,如乙醇和乙酸乙酯。
此外,催化裂化催化剂还可用于石油加工
中的其他反应,如裂化、氢化、烯烃交换、氧化和还原反应等。
催化裂化催化剂的使用具有一定的风险,由于其高活性,它们可能会对人体和环境造
成污染,因此应及时处理和储存。
此外,还应注意控制蒸汽压力,检查催化剂的活性,以
及控制反应温度,以确保反应的有效性和安全性。
总之,催化裂化催化剂是一种重要的化学物质,它可以提高反应的效率和质量,减少
能源消耗,提高生产率,在石油加工中具有重要作用,但它也存在一定的风险,应该加以
重视。
催化裂化催化剂主要成分

催化裂化催化剂主要成分催化裂化是石油炼制工艺中的一项重要技术,用于将重质石油馏分转化为轻质石油产品。
而催化裂化催化剂则是催化裂化过程中不可或缺的关键元素。
催化裂化催化剂主要由活性组分、载体和助剂组成。
活性组分是催化裂化催化剂的核心成分,它决定了催化剂的催化活性和选择性。
常见的活性组分包括铂、钯、铑等贵金属,以及铝、硅、硼等非贵金属。
这些活性组分能够与石油分子发生反应,并在反应过程中发挥催化作用,促进分子的裂化和转化。
其中,贵金属常用于加氢反应,非贵金属则主要用于非加氢反应。
载体是催化裂化催化剂的支撑物质,主要用于提高催化剂的稳定性和机械强度。
常见的载体材料有沸石、硅铝酸盐、氧化铝等。
载体具有较大的比表面积和适当的孔隙结构,能够提供活性组分的分散度和催化反应所需的表面活性位点。
此外,载体还能够吸附和保持反应物分子,促进反应的进行。
助剂是催化裂化催化剂中的辅助成分,主要用于改善催化剂的物化性质和催化性能。
常见的助剂包括钠、钾、锰、钴等金属离子,以及磷酸根、硼酸根等阴离子。
助剂的添加可以调节催化剂的酸碱性、氧化还原性和表面性质,从而提高催化剂的催化活性和选择性。
催化裂化催化剂的合成过程通常采用浸渍法、共沉淀法、离子交换法等方法。
在合成过程中,需要控制活性组分、载体和助剂的配比和添加顺序,以确保催化剂的成分均匀分布和良好的物相结构。
此外,还需要进行干燥、活化和硫化等后处理步骤,以提高催化剂的催化活性和稳定性。
催化裂化催化剂的性能与其成分密切相关。
活性组分的种类和含量直接影响催化剂的活性和选择性。
载体的比表面积和孔隙结构对催化剂的反应活性和承载能力有重要影响。
助剂的添加可以调节催化剂的物化性质和催化性能。
因此,在催化裂化工艺中,选择合适的催化裂化催化剂成分是实现高效转化和优质产品的关键。
催化裂化催化剂主要由活性组分、载体和助剂组成。
活性组分是催化剂的核心成分,决定了催化剂的催化活性和选择性。
载体是催化剂的支撑物质,提供活性组分的分散度和反应所需的表面活性位点。
催化裂化催化剂生产技术
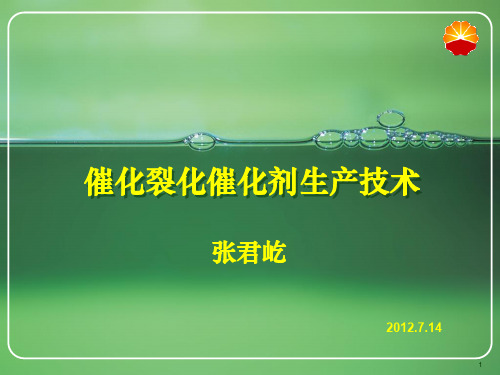
分子筛制备理论和生产技术
分子筛
影响催化剂的活性、选择性和产品质量
催化剂主要组分,催化剂选择性和大部分活性由它提供。催化剂的性能主要 取决于分子筛的种类和性质。了解分子筛的结构、类型、裂化机理和性质对 于选择合适的催化剂以达到预期收率是必要的。
钠的存在能降低分子筛的水热稳定性,也可与分子筛酸中心反应降低催化剂 活性,钠离子倾向于中和最强的酸中心。
兰州石化公司催化剂厂
8
催化裂化催化剂简介
按基质类型划分: 1、全合成催化剂(九十年代初国内已淘汰) 2、全白土催化剂:特色催化剂 3、半合成催化剂(目前主要是粘结剂型催化剂):主流催
化剂
兰州石化公司催化剂厂
9
催化裂化催化剂简介
全合成分子筛催化剂简介 1、八十年代我国催化裂化加工的主导催化剂; 2、基质为合成SiO2-Al2O3,分子筛为稀土Y型; 3、以水玻璃(硅酸钠)、硫酸铝、偏铝酸钠
兰州石化公司催化剂厂
31
分子筛制备理论和生产技术
一级结构单元 硅氧四面体(SiO4)及铝氧四面体(AlO4)均采取SP3杂
化轨道与氧原子成键,其中Si—O键长1.61Å,Al—O键长 1.75Å。由于硅原子半径(0.41Å)、铝原子半径 (0.50Å)均比氧原子半径(1.40Å)小得多,可以认为 Si、Al原子实际上被埋在氧原子堆成的四面体中心。 由此形成的TO4四面体即是沸石的一级结构单元。
1948年,硅铝微球催化剂出现; 4、1964年,分子筛裂化催化剂:
稀土型-稀土氢型-超稳型-复合分子筛型。
兰州石化公司催化剂厂
3
催化裂化催化剂简介
1、1958年由前苏联设计的第一套移动床催化裂化装置在兰州 投产。1964年建成了二套TCC装置,使用硅铝小球催化剂; 2、1965年第一套高低并列式流化催化裂化装置(Ⅳ型)在抚 顺投产; 3、1974年第一套提升管催化裂化装置在玉门投产;上世纪八 十年代以后,我国提升管催化裂化工艺迅猛发展。
- 1、下载文档前请自行甄别文档内容的完整性,平台不提供额外的编辑、内容补充、找答案等附加服务。
- 2、"仅部分预览"的文档,不可在线预览部分如存在完整性等问题,可反馈申请退款(可完整预览的文档不适用该条件!)。
- 3、如文档侵犯您的权益,请联系客服反馈,我们会尽快为您处理(人工客服工作时间:9:00-18:30)。
催化裂化催化剂一、关于催化剂所谓催化剂就是能够将有可能发生的化学在其存在的条件下加速反应的物质。
而自身的组成和质量在反应后保持不变。
因此,它不能使不可能发生的化学反应在其存在的条件下变为可能。
另外,不同的催化剂会产生不同的反应加速,同各催化剂也是如此。
这些都取决于催化剂的化学组成和物理结构。
也就是说催化剂具有选择性。
催化剂的种类繁多,但就催化裂化而言,应大致分为三种:即天然白土催化剂、合成硅铝催化剂和分子筛催化剂。
催化剂的发展历史也是按这个顺序走到今天的,性能也变的越来越好。
天然白土催化剂的主要成份也是硅酸铝,因为化学组成中的与物理结构上的不规则无定型,使应用效果较后两种较差。
现已不再作为催化裂化剂使用。
合成硅酸铝催化剂的主要成份也是硅酸铝,应用较为广泛,现仍是多数固定床反应器应用的首选。
由于是合成催化剂,化学组成中的杂质得到清除,物理结构也被优化筛分,使质量得到很大改善。
分子筛催化裂化催化剂是今后催化剂发展的必然方向,因为它是在合成催化裂化催化剂的基础上改进提高的,所以是在起点更高的基础上研究发展起来的。
主要改进方面是将具有规整结晶的硅铝“分子筛”均匀分布在催化剂担体上,从而实现了对催化裂化催化剂的要求(约占10~15%)。
二、催化剂的化学组成与物理结构催化剂的化学组成,它是由SiO2、Al2O3、H2O为主要成份组成的。
上述厂部份占其总量的97.5~99.5%。
二氧化(SiO2)、三氧化二铝(Al2O3)以及结构水(H2O)的结合,形成了结构复杂的硅、铝氧化物。
其中含量很少的水是必要的活性组份。
而其它1%不是化合物而是催化裂化催化剂的,制造中应尽力除去。
纯粹的SiO2和Al2O3是没有明显活性的,只有按一定比例结合方能显示其活性,并且有少量结构水存在情况下会使活性大大提高。
工业上合成分为低铝(SiO2 /Al2O3分子比为12)和高铝(SiO2 /Al2O3分子比为5)两种,区别主要是高铝较低铝在热稳定性及耐磨性上占优,但价格要高出低铝成本的10%。
分子筛催化剂是上世纪六十年代发展起来的高活性催化剂,它使催化裂化装置无论是产品收率、产品质量、加工能力都有很大提高。
因此成为当今催化裂化催化剂的最佳选择。
具有结晶形的天然或人造硅酸名句本来名称叫“泡沸石”,由于其具有规则的晶型结构,使孔排列得非常整齐,孔径大小也很均匀。
当吸附分子时,只有孔径小的分子方可进入孔内,而直径大于孔陉的分子则不能进入。
这种选择性,恰似筛子把大小不同分子分开。
因此被形象的称作“分子筛”,而它的真名则渐渐被陌生起来。
分子筛与前面讲到的无定型硅酸铝同样属硅氧和铝氧四面体。
并其规则的排列方式和经共用顶点的氧联接在一起的特殊结构,使其经稀土离子交换后,化学性质发生了极大变化,在晶格结构中产生了很强的静电并具有酸性。
这种酸的酸度比普通硅酸铝的酸度高百倍甚至千倍,也使活性大大增强。
三、分子筛催化裂化催化剂活性的来源分子筛催化剂在经过稀土离子交换后,使化合状态的铝原子外围有缺一对电子的空位,形成了酸性中心的边缘组成无水酸,又因铝氧四面体的化合结构使四个Al—O交点中有一配价电存在,就使铝原子带上负电,和配价电上的氧结合成一个质子,而这个带正电质子(H+)是由催化剂中的结构水(H2O)提供的(整修催化剂整体仍保持了中性),它是催化剂酸性中心的主要组成来源称质子酸,高温时质子酸会因失水(化合水)而形成无水酸,低温时又会吸水形成质子酸,不管在操作条件下互相转化的酸性中心如何变化都能使油品分子变为阳碳离子而进行催化裂化反应。
由上述介绍,使我们可以了解到催化剂的活性本质,其中少量化合水的存在是十分重要的。
另外,若想让催化剂中有足够多的酸性中心,就势必将其制造成内表面积很大的多孔结构。
实际上催化剂的表面积还不到内表面积的0.1%,也就是说催化剂的内表面积越大,分布其中的酸性中心就会越多,而酸性中心越多酸度就越大,酸度越大吸附能力就越强,活性也就越大。
但也须说明,只有让油分子能够通过适宜的孔径方能显示出实际活性的大,否则虽有众多活性中心和高的酸度,因不能加速反应,实际活性并不会大。
因此,在催化剂的制作时,要对其微孔孔径进行适当的控制,以满足反应时的需要。
四、工业分子筛催化剂的使用性能工业生产希望得到怎样的催化剂呢?有以下八项内容:1、高活性和选择性2、良好的稳定性3、产品收率高、质量好4、抗污染,不易中毒5、强度高,耐磨损6、易再生,不易烧结熔融7、粒径适中,流化性能好8、热容量大,操作易控制为达到上述使用性能要求,楠做下述指标控制:1、物理性质:⑴颜色与形状:新鲜催化裂化催化剂均为白色,固定床采用球状与柱状、也有棱状、三叶棱状,流化床大都采用微球形状。
采用与制作有关,也与生产要求易流化有关。
⑵粒度组成:催化裂化催化剂因在流化床层使用时要保证具有很好的流态化性能。
那么粒陉越小的球状则能满足条件,但对制造而言,不可能生产出同样粒径的微球,那么粒陉此时变一个范围约在20μm~100μm间,要求平衡剂粒径<40μm的细粒在15~20%,大于80μm的粗粒与小于40μm的细粒的比值叫粗度系数。
一般不大于3,细粉含量大时,易流化,损失大,粗粒多,则流化性能差,磨损大。
适宜的平衡剂粒度范围应该是40~80μm的占70%以上,最佳,通常把粒度组成称为“筛分组成”⑶密度:催化剂的密度有骨架密度、颗粒密度、堆积密度三种,是衡量催化剂流化性能、流化质量、藏量、设计流化设备的重要参数。
骨架密度:指扣除颗粒内微孔体积时的实体密度2300kg/m3(低铝)颗粒密度:指包括颗粒密度内微孔体积在内的密度,新剂0.6ml/g,1000 kg/m3 平衡剂体积缩小后0.4 ml/g为1200 kg/m3关系式为:r颗粒=10001000/ r骨架(式中r骨架:1kg/m3V孔:ml/g)堆积密度:指包括颗粒堆积空隙在内的密度。
平衡密度为:800~900kg/m3新剂密度为:800 kg/m3⑷结构特性:孔体积、比表面积、孔径孔体积是表示催化剂颗粒内微孔的总体积,以毫升/克为单位。
比表面积是催化剂内外表面的总面积,以米2/克为单位,通常表面积越大催化剂活性就越高,活性中的所占面积只占催化剂总表面积的百分之几。
新鲜剂比面积可500~700m2/g,平衡剂则会降至100 m2/g左右。
孔径指催化剂微孔的直径,因大小不一,常指平均直径,由计算得出:孔体积(毫升/克)孔径(O A)=4××104比表面积(米2/克)āī孔径(O A)=,为长度单位,1毫米=107O A(读作1000万埃),1微米μ=104O A(1万埃)⑸、比热:也称热容,是物质特性,单位为千卡/公斤℃,即一公斤物质温度升高1℃需要的热量。
2、催化性质,有三项:活性、选择性、稳定性⑴活性:反映催化剂加快反应速度的能力,通俗的讲,就是在操作反应条件下使原料变为产品的能力,通常以(D+L)%表示,式中D为反应物汽油的液体部分,C为反应物汽油的损失部分,指汽油占反应后液体产物体积的分数,因流化床分子筛的广泛应用,使(D+L)%不易准确计量,新分析方法模拟流化床生产条件,对转化率测定,把生产物中汽油、气体焦炭三者产率指标定为活性指标,称作“微反活性”。
⑵选择性:选择性主要对获取目标产率高低而言,有选择汽油多的、柴油多的还有选液态烃多的、气体多的、C二多的。
相比较而言,分子筛催化剂选择性最好,但在遭受重金属污染后会使其选择性大大降低,另外选择性高低也与制造质量、品种有关,与生产操作条件及设备工艺性能有关。
⑶稳定性:批催化剂在使用条件下保持活性的能力,采用750℃通蒸汽6小时测定活性判定稳定性。
催化剂平衡活性越高说明稳定性越好,也就量说在反复使用条件下的抗老化能力、在高温水蒸汽作用下的抗崩溃能力。
3、 机械性质:指机械强度和耐磨性,测定方法为将>15μ颗粒所占重量百分数称磨损指数,该指数的高低可看出催化剂易不易损失,是催化剂重要的指标项目。
五、 催化裂化的反应:催化裂化的反应是在催化剂上进行的,前提条件是原料的气化。
1、 反应过程:⑴原料气体分子扩散到达催化剂微孔内表面。
⑵微孔表面的原料气体分子被活性中心吸附。
⑶进行了A 裂化反应、B 异构化反应、C 氢转移反应、D 芳构化反应、E 叠合反应、F 烷基化反应、G 甲基转移反应A :正庚烷→丙烯+正丁烷、异丁基苯→苯+异丁烷B :正丁烷→异丁烷、丁烯-1→丁烯-2C :甲基环乙烷+丁烯-2→甲基环乙烯+正丁烷D :庚烯-2→→ +6HCE:丙烯+丙烯→C —CC= C —C2甲基戌烯-3F :烷基化反应+C= C —C —C →丁烯-1 β— 甲基萘 C2甲基,3仲丁基萘G :甲基转移反应:+ → 甲苯 甲苯 苯 —C —C对间邻二甲苯其中:以A、B、C、D为理想反应,E、F、G则为产生焦炭和干气的不理想反应⑷反应产品从催化剂上脱附。
⑸脱附后的反应产品向离开反应器的气流扩散。
由此可知:首选被活性中心吸附,方能发生反应,吸附难易发生顺序为(同类烃则分子量越大越容易被吸附)稠环芳烃>稠环环烷烃>烯烃>烷基苯>环烷烃>烷烃。
化学反应速度大小顺序为:烯烃>异构烷与烷基环烷烃>正构烷烃>烷基萘>稠环芳烃上述可见:烃类吸附难易与反应快慢顺序并不一致。
另外,催化表面各类烃被吸附的数量除与它们被吸附的难易有关外,还与它们在原料中含量有关。
也是说与原料组成有关。
如易吸附的不易反应的太多时,则会使焦炭气体产率上升,催化剂含炭量上升快导致迅速失活,不再反应。
另外,当催化剂被重金属污染后也会发生催化剂不再反应的情况,而这种情况是最为严重的,因为被重金属污染的催化剂将不能再生恢复活性只能用更换新鲜剂的方法维持反应系统的活性。
并应迅速查找原因,查出污染源,杜绝污染源侵入。
不同催化剂对重金属污染的第三程度不同:工业上为防止重金属污染,采用定期加入钝化剂和维持催化剂系统钝化剂贮量的办法进行预防;也采用卸出部分平衡催化剂补充新剂以维持床层催化剂活性的办法;催化剂的研究部门则用氢离子交换办法脱除重金属以恢复催化剂的活性。
一般此法均不为工业生产所用,性价比不合理。
常用也是最有效的办法是从源头用采取措施。
即防止原料中重金属含量超标。
原料中富含重金属的馏份人数在重质组份中,因此,适当控制重质原料组份的掺炼是防止催化剂最有效的办法。
随着工业生产装置的技术进步,催化裂化催化剂也有了新的开发领域。
如重油催化裂化装置的投产运行,使重油掺炼比例高达40%,重金属污染在所难免,就要求催化剂在制作生产中就具备优良的抗重金属能力。
如新开发的全白土、稀土氢Y、富镧等,均有较高的抗重和。
另外在钝化剂的研究方面也有了很大的进展,这里不再陈述。
六、催化裂化的反应机理,催化裂化的反应究竟是如何进行的?正如地球是如何形成一样,众说风云,假说众多。