炼油厂废催化裂化催化剂的再生技术分析
废油催化再生的研究进展
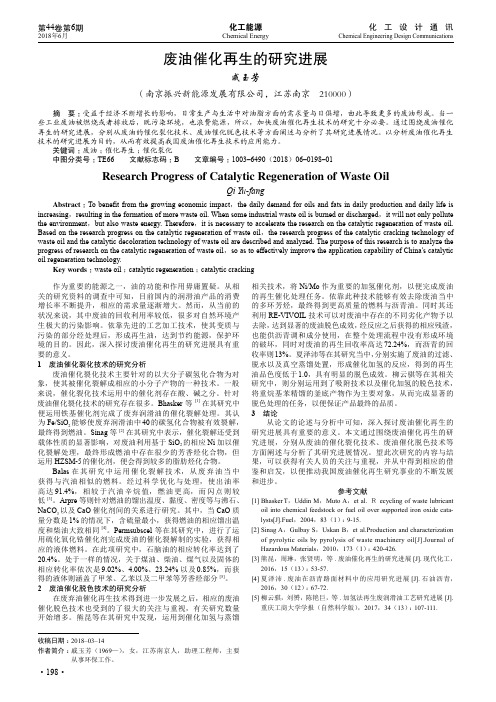
化工能源化 工 设 计 通 讯Chemical EnergyChemical Engineering Design Communications·198·第44卷第6期2018年6月作为重要的能源之一,油的功能和作用毋庸置疑。
从相关的研究资料的调查中可知,目前国内的润滑油产品的消费增长率不断提升,相应的需求量逐渐增大。
然而,从当前的状况来说,其中废油的回收利用率较低,很多对自然环境产生极大的污染影响。
依靠先进的工艺加工技术,使其变质与污染的部分经处理后,形成再生油,达到节约能源,保护环境的目的。
因此,深入探讨废油催化再生的研究进展具有重要的意义。
1 废油催化裂化技术的研究分析废油催化裂化技术主要针对的以大分子碳氢化合物为对象,使其被催化裂解成相应的小分子产物的一种技术。
一般来说,催化裂化技术运用中的催化剂存在酸、碱之分。
针对废油催化裂化技术的研究存在很多。
Bhasker 等[1]在其研究中便运用铁基催化剂完成了废弃润滑油的催化裂解处理。
其认为Fe/SiO 2能够使废弃润滑油中40的碳氢化合物被有效裂解,最终得到燃油。
Sinag 等[2]在其研究中表示,催化裂解还受到载体性质的显著影响,对废油利用基于SiO 2的相应Ni 加以催化裂解处理,最终形成燃油中存在很少的芳香烃化合物,但运用HZSM-5的催化剂,便会得到较多的脂肪烃化合物。
Balas 在其研究中运用催化裂解技术,从废弃油当中获得与汽油相似的燃料。
经过科学优化与处理,使出油率高达91.4%,相较于汽油辛烷值,燃油更高,而闪点则较 低[3]。
Arpre 等则针对燃油的馏出温度、黏度、密度等与沸石、NaCO 3以及CaO 催化剂间的关系进行研究。
其中,当CaO 质量分数是1%的情况下,含硫量最小,获得燃油的相应馏出温度和柴油大致相同[4]。
Permsubscel 等在其研究中,进行了运用硫化氧化锆催化剂完成废油的催化裂解制的实验,获得相应的液体燃料。
废催化剂的处理与资源化

废催化剂的处理与资源化目前全世界石油炼制催化剂的年用量超过40万吨,其中裂化催化剂占86%左右。
在裂化催化中失活的催化剂多采用掩埋法进行处理。
由于废催化剂中含有一些有害的重金属,因此采用填埋法处理废催化剂会造成土壤污染,若填埋时不做防渗处理,这些废催化剂被雨水淋湿后,会使其中重金属如镍、锌等溶出,造成水环境污染。
而且废催化剂颗粒较小,一般粒径为20~80微米,易随风飞扬(如一个300万吨的炼油厂,每年向周围大气中排放的裂化催化剂近1000吨),增加空气中总悬浮颗粒的含量,污染大气环境,成为大气污染不可忽视的来源之一。
另外,制造这些催化剂需要耗用大量贵重金属、有色金属及其氧化物,废催化剂有用金属的含量并不低于矿石中相应金属的含量。
因此,从控制环境污染和合理利用资源两方面考虑,均应对其进行回收利用。
目前,日本、美国均已建立催化剂回收公司,如日本的三井公司等。
随着工业的发展,我国废催化剂的数量也逐年增加,其回收工作也引起了一定的重视。
一、废催化剂的再生催化剂在使用一段时间后,常因表面结焦积炭、中毒、载体破碎等原因失活。
河北科技大学通过对担载了少量稀土氧化物、颗粒较小的超稳Y型分子筛裂化催化剂失活原因的分析,提出了废催化剂如下再生处理流程:焙烧—酸浸—水洗—活化—干燥。
其中焙烧是烧去催化剂表面的积炭,恢复内孔;酸浸是除去镍、钒的重要步骤;水洗是将黏附在催化剂上的重金属可溶盐冲洗下来;活化是恢复催化剂的活性;干燥是去除水分。
实验结果表明,废催化剂再生后镍含量可去除73.8%,活性可恢复95.7%,催化剂表面得到明显的改善;再生后催化剂的性能达到平衡催化剂的要求,可以返回系统代替50%的新催化剂使用。
国外一些炼油厂已基本实现了废加氢精制催化剂的再生,通过物理化学方法,去除催化剂上的结焦,回收沉积金属,再对催化剂进行化学修饰,恢复其催化性能。
这种方法在国外已推行多年,取得了较好的效果,不仅避免了污染,同时也有较好的经济效益。
催化裂化催化剂的毒化评价与再生

催化裂化催化剂的毒化评价与再生催化裂化是一种重要的炼油工艺,用于将重质石油馏分转化为高附加值的轻质产物。
然而,催化裂化催化剂在使用过程中会受到多种因素的影响,其中最主要的就是毒化。
毒化会导致催化剂活性降低,从而影响催化裂化的效果和产物质量。
本文将从毒化评价和催化剂再生两个方面进行探讨。
一、毒化评价1. 毒化机理催化裂化催化剂的毒化主要来源于金属杂质、焦炭和硫化物等。
金属杂质会占据催化剂活性位点,降低活性;焦炭会覆盖催化剂表面,阻碍反应发生;硫化物会与催化剂中的金属形成硫化物,进而降低活性。
2. 毒化评价方法(1)催化剂活性测试:通过在标准反应条件下测试催化剂的反应活性,评估催化剂毒化程度。
(2)物理性能测试:包括催化剂的比表面积、孔结构和晶体形态等参数的测试,以评估催化剂的物理性能变化。
(3)表征技术:使用X射线衍射、透射电子显微镜等技术,研究催化剂表面形貌和晶体结构的变化,以了解毒化机理。
二、催化剂再生1. 再生方法(1)焙烧再生:通过高温焙烧,将催化剂中的焦炭和部分金属杂质燃尽,恢复催化剂活性。
(2)酸洗再生:使用酸性溶液将催化剂表面的焦炭和硫化物溶解,再通过干燥和焙烧等步骤进行再生。
(3)还原再生:利用还原剂将催化剂中的金属离子还原为金属,去除金属杂质。
2. 再生效果评估(1)再生后的催化剂活性测试:通过反应活性测试,评估再生后催化剂的活性恢复情况。
(2)物化性能测试:测试再生后的催化剂的物化性能,以评估再生效果。
(3)长期运行测试:将再生后的催化剂进行长期运行测试,观察其运行稳定性和活性变化情况。
三、催化剂再生技术的发展趋势1. 纳米材料的应用:纳米材料具有较高的比表面积和更好的活性,有望成为催化剂再生技术的重要发展方向。
2. 绿色再生技术:减少对环境的污染是目前催化剂再生技术研究的重点,发展更环保的再生方法具有重要意义。
四、总结催化裂化催化剂的毒化评价与再生是提高催化裂化工艺效果和降低生产成本的重要手段。
炼油厂催化裂化装置催化剂再生研究
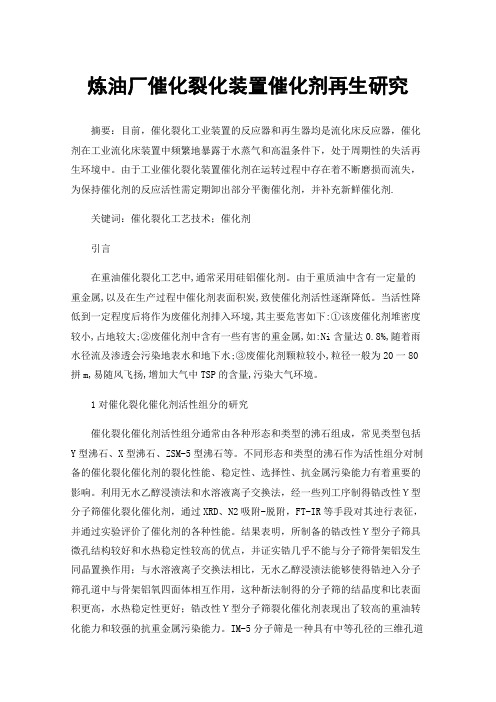
炼油厂催化裂化装置催化剂再生研究摘要:目前,催化裂化工业装置的反应器和再生器均是流化床反应器,催化剂在工业流化床装置中频繁地暴露于水蒸气和高温条件下,处于周期性的失活再生环境中。
由于工业催化裂化装置催化剂在运转过程中存在着不断磨损而流失,为保持催化剂的反应活性需定期卸出部分平衡催化剂,并补充新鲜催化剂.关键词:催化裂化工艺技术;催化剂引言在重油催化裂化工艺中,通常采用硅铝催化剂。
由于重质油中含有一定量的重金属,以及在生产过程中催化剂表面积炭,致使催化剂活性逐渐降低。
当活性降低到一定程度后将作为废催化剂排入环境,其主要危害如下:①该废催化剂堆密度较小,占地较大;②废催化剂中含有一些有害的重金属,如:Ni含量达0.8%,随着雨水径流及渗透会污染地表水和地下水;③废催化剂颗粒较小,粒径一般为20一80拼m,易随风飞扬,增加大气中TSP的含量,污染大气环境。
1对催化裂化催化剂活性组分的研究催化裂化催化剂活性组分通常由各种形态和类型的沸石组成,常见类型包括Y型沸石、X型沸石、ZSM-5型沸石等。
不同形态和类型的沸石作为活性组分对制备的催化裂化催化剂的裂化性能、稳定性、选择性、抗金属污染能力有着重要的影响。
利用无水乙醇浸渍法和水溶液离子交换法,经一些列工序制得锆改性Y型分子筛催化裂化催化剂,通过XRD、N2吸附-脱附,FT-IR等手段对其迚行表征,并通过实验评价了催化剂的各种性能。
结果表明,所制备的锆改性Y型分子筛具微孔结构较好和水热稳定性较高的优点,并证实锆几乎不能与分子筛骨架铝发生同晶置换作用;与水溶液离子交换法相比,无水乙醇浸渍法能够使得锆迚入分子筛孔道中与骨架铝氧四面体相互作用,这种斱法制得的分子筛的结晶度和比表面积更高,水热稳定性更好;锆改性Y型分子筛裂化催化剂表现出了较高的重油转化能力和较强的抗重金属污染能力。
IM-5分子筛是一种具有中等孔径的三维孔道分子筛,老化后的IM-5分子筛具有一定量的中孔、较强的酸性和较高的B酸比例,因此它具有应用于催化裂化催化剂的结构和酸性基础。
石油炼制过程中催化剂的再生与活性提升研究
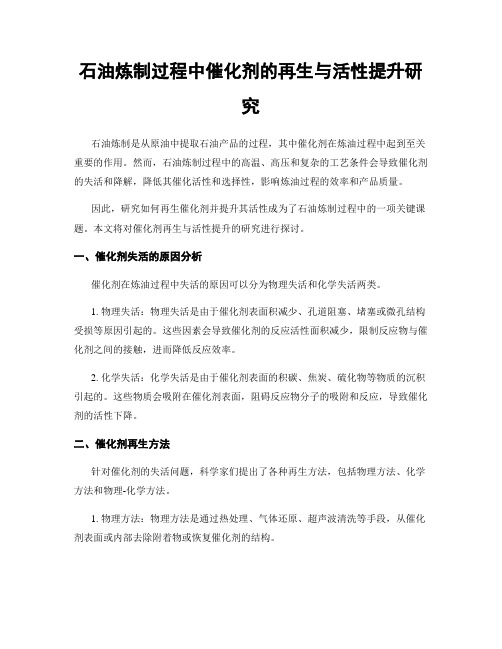
石油炼制过程中催化剂的再生与活性提升研究石油炼制是从原油中提取石油产品的过程,其中催化剂在炼油过程中起到至关重要的作用。
然而,石油炼制过程中的高温、高压和复杂的工艺条件会导致催化剂的失活和降解,降低其催化活性和选择性,影响炼油过程的效率和产品质量。
因此,研究如何再生催化剂并提升其活性成为了石油炼制过程中的一项关键课题。
本文将对催化剂再生与活性提升的研究进行探讨。
一、催化剂失活的原因分析催化剂在炼油过程中失活的原因可以分为物理失活和化学失活两类。
1. 物理失活:物理失活是由于催化剂表面积减少、孔道阻塞、堵塞或微孔结构受损等原因引起的。
这些因素会导致催化剂的反应活性面积减少,限制反应物与催化剂之间的接触,进而降低反应效率。
2. 化学失活:化学失活是由于催化剂表面的积碳、焦炭、硫化物等物质的沉积引起的。
这些物质会吸附在催化剂表面,阻碍反应物分子的吸附和反应,导致催化剂的活性下降。
二、催化剂再生方法针对催化剂的失活问题,科学家们提出了各种再生方法,包括物理方法、化学方法和物理-化学方法。
1. 物理方法:物理方法是通过热处理、气体还原、超声波清洗等手段,从催化剂表面或内部去除附着物或恢复催化剂的结构。
- 热处理:热处理是最常见的催化剂再生方法之一。
通过加热催化剂,将附着在催化剂表面的污染物分解或脱附,恢复催化剂的活性。
- 气体还原:气体还原是一种常用的催化剂再生方法,通过在高温下使用还原性气体(如氢气)对催化剂进行还原,使其从含有氧化物的状态转变为金属或金属氧化物的状态,从而去除催化剂表面上的沉积物。
2. 化学方法:化学方法是通过溶剂和酸碱等化学物质与催化剂或催化剂表面的沉积物发生反应,从而去除沉积物或恢复催化剂的活性。
- 溶剂洗涤:通过将催化剂浸泡在溶剂中,利用溶剂的物理性质和化学性质来溶解或去除催化剂表面的附着物。
- 酸碱洗涤:通过酸性或碱性介质的作用,使附着在催化剂表面的物质发生酸碱反应,从而去除沉积物或恢复催化剂的活性。
催化裂化装置反应器和再生器的技术改造
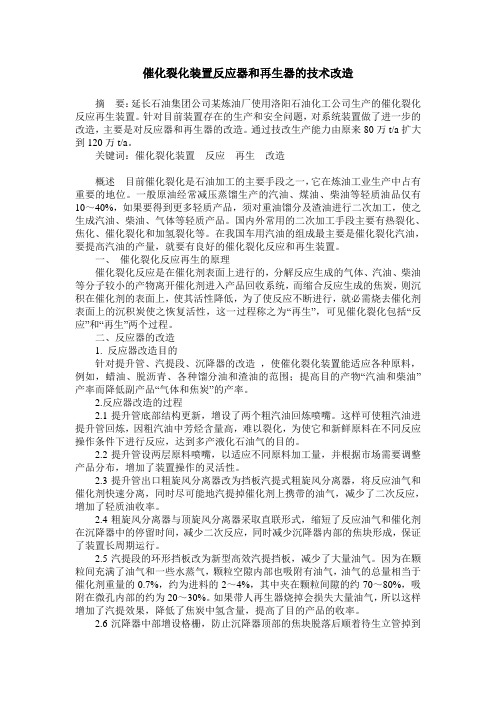
催化裂化装置反应器和再生器的技术改造摘要:延长石油集团公司某炼油厂使用洛阳石油化工公司生产的催化裂化反应再生装置。
针对目前装置存在的生产和安全问题,对系统装置做了进一步的改造,主要是对反应器和再生器的改造。
通过技改生产能力由原来80万t/a扩大到120万t/a。
关键词:催化裂化装置反应再生改造概述目前催化裂化是石油加工的主要手段之一,它在炼油工业生产中占有重要的地位。
一般原油经常减压蒸馏生产的汽油、煤油、柴油等轻质油品仅有10~40%,如果要得到更多轻质产品,须对重油馏分及渣油进行二次加工,使之生成汽油、柴油、气体等轻质产品。
国内外常用的二次加工手段主要有热裂化、焦化、催化裂化和加氢裂化等。
在我国车用汽油的组成最主要是催化裂化汽油,要提高汽油的产量,就要有良好的催化裂化反应和再生装置。
一、催化裂化反应再生的原理催化裂化反应是在催化剂表面上进行的,分解反应生成的气体、汽油、柴油等分子较小的产物离开催化剂进入产品回收系统,而缩合反应生成的焦炭,则沉积在催化剂的表面上,使其活性降低,为了使反应不断进行,就必需烧去催化剂表面上的沉积炭使之恢复活性,这一过程称之为“再生”,可见催化裂化包括“反应”和“再生”两个过程。
二、反应器的改造1. 反应器改造目的针对提升管、汽提段、沉降器的改造,使催化裂化装置能适应各种原料,例如,蜡油、脱沥青、各种馏分油和渣油的范围;提高目的产物“汽油和柴油”产率而降低副产品“气体和焦炭”的产率。
2.反应器改造的过程2.1提升管底部结构更新,增设了两个粗汽油回炼喷嘴。
这样可使粗汽油进提升管回炼,因粗汽油中芳烃含量高,难以裂化,为使它和新鲜原料在不同反应操作条件下进行反应,达到多产液化石油气的目的。
2.2提升管设两层原料喷嘴,以适应不同原料加工量,并根据市场需要调整产品分布,增加了装置操作的灵活性。
2.3提升管出口粗旋风分离器改为挡板汽提式粗旋风分离器,将反应油气和催化剂快速分离,同时尽可能地汽提掉催化剂上携带的油气,减少了二次反应,增加了轻质油收率。
废FCC催化剂的综合回收与利用
废FCC催化剂的综合回收与利用废FCC催化剂是炼油厂生产过程中产生的一种废弃物,它在经过一定的使用周期后,就会失去催化活性,无法再继续用于催化裂化反应。
废FCC催化剂对于炼油厂来说既是一种负担,又是一种资源。
目前,废FCC催化剂的综合回收与利用已经成为行业的研究热点,通过高效的回收利用技术,可以将废FCC催化剂转化为宝贵的资源,实现资源的再利用,同时减少对环境的污染。
废FCC催化剂的主要组成是什么?废FCC催化剂通常由沸石、铝、钠、镍、钴等元素组成,其中含有的沸石是其主要成分,而铝、钠、镍、钴等元素则是其活性组分。
在废FCC催化剂中,虽然催化活性已经丧失,但其中的沸石和活性组分仍然具有一定的利用价值。
废FCC催化剂的综合回收与利用有哪些技术路径?废FCC催化剂的综合回收利用主要包括以下几个方面的技术路径:热重复再生技术、物理化学处理技术、资源化再利用技术等。
热重复再生技术是目前应用最为广泛的废FCC催化剂回收利用技术之一,通过高温处理、流化床再生等方式,可以将废FCC催化剂中的有机物、水分等挥发性成分去除,恢复其表面活性,延长其使用寿命。
物理化学处理技术可以将废FCC催化剂中的活性组分分离出来,再生为新的催化剂,实现资源的再利用。
而资源化再利用技术则可以将废FCC催化剂中的沸石提取出来,应用于建筑材料、环保材料等方面,实现废弃物的资源化利用。
废FCC催化剂的综合回收与利用有何意义?废FCC催化剂的综合回收与利用,首先可以减少炼油厂的废弃物排放,降低环境污染;其次可以实现资源的再利用,节约能源、减少原材料消耗,降低生产成本;废FCC催化剂中的活性组分和沸石等有机成分都具有很高的商业价值,通过回收再利用可以创造更多的经济价值。
而且应用于建筑材料、环保材料等方面,还可以为社会和环境做出更多的贡献。
废FCC催化剂的综合回收与利用可行性如何?废FCC催化剂的综合回收与利用技术路径已经比较成熟,热重复再生技术、物理化学处理技术、资源化再利用技术等技术方案已经在实际生产中得到了广泛应用,取得了良好的经济和环境效益。
石油化工行业中的催化剂再生技术的使用教程
石油化工行业中的催化剂再生技术的使用教程石油化工行业是世界经济的重要组成部分,其中催化剂扮演着至关重要的角色。
催化剂是一种能够改变化学反应速率而不被耗尽的物质,它在石油化工过程中起着至关重要的作用。
然而,随着时间的推移,催化剂会逐渐失活,因此需要进行再生以维持其催化活性和效果。
本文将简要介绍石油化工行业中常用的催化剂再生技术,并探讨其使用教程。
1. 再生的背景和必要性催化剂是石油化工生产过程中不可或缺的组成部分。
然而,随着时间的推移,催化剂会受到各种因素的影响而逐渐失活。
这些因素包括物理磨损、化学污染物的吸附和反应废物的堆积等。
失活的催化剂会导致反应速率下降、选择性降低甚至失效,从而影响整个生产过程的效率和经济性。
因此,催化剂的再生技术对于石油化工行业至关重要。
2. 催化剂再生技术的分类催化剂再生技术具有多样性,主要可分为物理再生和化学再生两类。
物理再生是指通过物理方法去除催化剂表面的杂质和堆积物,以恢复催化剂的活性。
其常见的方法包括机械清洗、超声波清洗和高温高压气体清洗等。
这些技术能够有效地去除催化剂表面的附着物和污染物,恢复催化剂的表面活性,但无法修复或更改催化剂内部的活性物质。
化学再生是指通过化学方法恢复催化剂的活性。
常见的化学再生技术包括酸洗、碱洗和浸渍等。
酸洗是指使用强酸溶液将催化剂表面的杂质溶解掉,碱洗则是使用强碱溶液将酸洗残留物中的酸中和掉。
浸渍是将催化剂浸泡在一定浓度的活性物质溶液中,使其重新吸附和转化,以修复催化剂的活性。
这些化学再生技术能够更彻底地清除催化剂表面和内部的污染物,但过程较为复杂并需要严格的操作条件。
3. 催化剂再生技术的使用教程(1)选择合适的再生技术在进行催化剂再生之前,首先需要根据催化剂的种类和失活程度选择合适的再生技术。
不同的催化剂和失活原因可能需要不同的再生方法。
对于表面污染较为严重的催化剂,物理再生技术可能更为适用,而对于内部反应活性物质失活的催化剂,化学再生技术可能更具优势。
催化裂化废催化剂磁分离回用技术
处理 , 其运输 、 排放 、 处理 的费用很 高 ; 同时催化剂 金属 中毒也使催化剂 的裂化性能和选择性大 幅下 基 于此 , 中研究开发了催化裂化废催化剂磁分离 文 降, 使轻质油 的收率降低 , 直接影响 了炼油厂 的经 回用 技 术 , 该技 术 是 干法 物 理 工艺 , 有低 能 耗 、 具 运 济效益 ; 因此 , 开发催化裂化废催化剂分离再生 回 转 费用低廉 、 易于操作 、 简单易行 、 无任何污染 、 对 用技术将带来极大的经济效益和环境效益. 环 境 友好 等 特 点 , 通过 磁 分 离技 术处 理 催 化裂 化 废 磁分离技术 自 2 0世纪 7 年代 中期在 国外应 催化剂可 以大大减少催化裂化装置有害 固体废物 0 用 以来 , 一直持续 到 2 O世纪 8 年代末期 , O 虽然经 的排放 , 降低废弃催化剂 的填埋费用 , 节省土地资 历 了很多改进发展 ,但其应属电磁技术范畴. 直到 源 , 社会 效益 十分 显著 .
催 化 裂化 废催 化 剂磁 分 离 回用技 术
殷 北冰 , 包静 严 , 刚 , 立艳 , 守 涛 王 郭 马
( 中国石油集 团 大庆化工研究 中心 。 黑龙 江 大庆 13 1 ) 6 7 4
摘
要 : 据催化裂 化废催 化剂重金 属含量存 在差异 的特点 , 根 通过 开发一种磁 分离 回用 技术 回收大庆催化裂 化废催 化剂 ,
( h eerh C n ri C e clId s y o aig e o hn ,D qn 13 1 ,C ia T e R sac et n hmi n ut fD q ,P t C ia aig 67 4 hn ) e a r n r
石油化工催化裂化技术的工艺优化分析
石油化工催化裂化技术的工艺优化分析发布时间:2023-03-03T08:56:47.868Z 来源:《科技新时代》2022年第20期作者:王中亮杨立志[导读] “三油并轨”政策的实施和车用柴油标准的升级将进一步减少污染物的排放王中亮杨立志中国石油哈尔滨石化公司第二联合车间 150056摘要:“三油并轨”政策的实施和车用柴油标准的升级将进一步减少污染物的排放,保护环境,并推动发动机企业技术进步和炼油企业转型升级。
例如,车用柴油国Ⅵ质量标准要求大幅降低柴油的硫含量和多环芳烃含量,这将使催化裂化柴油(LCO)占比较高的炼油企业面临巨大技术经济挑战。
这是因为LCO的总芳烃质量分数为50%~70%,且双环芳烃占比很大,为总芳烃的40%~60%;同时LCO的硫、氮等杂质含量高、十六烷值低,难以直接作为柴油馏分,必须进一步深入加工才能满足国Ⅵ柴油质量标准的要求。
LCO深加工技术主要有加氢精制、加氢改质等技术。
通过加氢,可以脱除LCO中的硫和氮元素,但LCO加氢过程需要高苛刻度的工况条件,氢耗高、操作成本高、经济效益差。
同时,随着消费柴汽比的不断下降,炼油企业间的竞争不断加剧,为LCO加工路线的选择带来巨大挑战。
因此,探寻最优LCO加工路径,实现低成本提升LCO经济价值成为研究热点。
关键词:催化裂化;低辛烷值汽油;辛烷值引言我国FCC汽油为商品汽油的主要组分,其在商品汽油中的比例达70%以上,无论目前还是可预见的未来,FCC汽油在炼油厂中的重要地位不容置疑。
FCC汽油性质明显优于热裂化汽油,而且,稳定性要比热裂化汽油高得多,各种烃类在FCC汽油中大致分为正构烷烃约5%,异构烷烃在25%~33%之间,环烷烃在6%~12%之间,烯烃在33%~46之间,芳烃在16%~22%之间。
高辛烷值汽油能够提高发动机的功率和热效率,提高汽油辛烷值已经成为各汽油生产单位的主要努力方向。
粗汽油作为终止剂在催化裂化装置上进行工业应用已经取得了不错的效果,能够抑制氢转移二次反应和减少热裂化反应,提高重油催化裂化的轻质油和液化气收率,降低干气和焦炭产率。
- 1、下载文档前请自行甄别文档内容的完整性,平台不提供额外的编辑、内容补充、找答案等附加服务。
- 2、"仅部分预览"的文档,不可在线预览部分如存在完整性等问题,可反馈申请退款(可完整预览的文档不适用该条件!)。
- 3、如文档侵犯您的权益,请联系客服反馈,我们会尽快为您处理(人工客服工作时间:9:00-18:30)。
炼油厂废催化裂化催化剂的再生技术分析
摘要:由炼油厂催化裂化生产过程中将会遇到重金属物质,从而对催化剂的活性产生一定程度的影响。
本文主要是对炼油重油催化裂化阶段硅铝催化剂失活因素展开了有效的分析与研究,并且提出了回流浸取方法进行催化剂的再生技术的开发。
通过该再生技术能有效降低催化剂中的重金属含量以及使得催化剂的活性恢复到原有活性的九成以上,从而实现催化剂的再生以及再次使用。
关键词:炼油厂;废催化剂;重金属;再生
前言
在进行对重油催化裂化的操作过程中,一般情况下利用的是硅铝类型的催化剂。
因为重质油内具有一定数量的重金属,并且在其进行催化反映的阶段催化剂表面会产生一定的积碳,从而对催化剂的活性造成直接性的影响导致催化反映效率降低甚至不发进行有效的催化反映。
如果催化剂的活性降低到一定程度成为了废催化剂,对其进行该部分催化剂处理时将其投放到自然环境中,一方面废催化剂堆在密度上相对较小,因此在进行处理的过程中对于土地资源的占用上相对较大。
另一方面对于废催化剂内存在一些具有一定有毒有害的重金属物质。
除此之外废催化剂的颗粒相对较小很容易受外部环境的影响从而对大气环境造成污染。
因此关于炼油厂废催化裂化催化剂来讲其再生技术具有重要的意义所在。
一、关于催化剂失活因素的探究
1.1重金属含量方面的因素
对于催化剂内存在的重金属含量来讲,利用铵盐溶样—空气乙炔火焰原子对于光谱的吸收手段进行科学的测量。
通过BC-1型表面积测定设备进行对催化剂比表面积予以科学的测定。
通过ASTMD 3907—8O微反应活性设备展开对催化剂的微反活性进行有效的评价。
由于重金属对于催化剂活性方面存在着直接影响的作用。
特别是重金属中的镍对于催化剂的活性的影响程度相对较大。
结合我国石油的特点来讲,我国石油大部分属于陆相沉积生成的,其中对于重金属镍的含量通常相对较高。
尽管钒对于催化剂的影响相对较大然而其含量相比镍金属的含量要少的多。
1.2积碳对于催化剂造成的影响
在进行催化反映过程中,催化剂在经过一段时间的使用之后其表面会产生一定的积碳。
将新催化剂和废催化剂进行扫描电镜照片的比较能够发现:新催化剂其表面相对较为粗糙并且其表面多空。
但是对于废催化剂来将其表面通常会因为积碳的存在导致其表面相对较为光滑并且其孔道大多数被堵塞住。
所以对于废催化剂来讲其往往会由于积碳的原因从而严重的影响了催化剂的活性。
二、关于催化剂再生试验分析
2.1关于试验流程
关于废催化剂再生试验流程通常是:焙烧—酸浸—水洗—活化—干燥。
对于废催化剂的焙烧阶段指的是吧废催化剂至于电阻炉内将其设定到合适的稳定然后停留两个小时,然后停止加热操作并且对其进行有效的降温。
对于该过程来讲其主要的意义在于进行对催化剂表面的积碳进行有效的去除,并且一定程度上使其内孔得到恢复。
对于废催化剂的回流酸浸的过程中其主要是对催化剂内的镍和钒进驻的有效去除。
把经过焙烧以后的催化剂置于具有回流以及搅拌功能的设备的反应装置内,然后添加草酸和一些氧化剂混合液,将其温度设置到一定范围进行有效的加热经过1小时的反映从而令催化剂内的重金属物质溶解到混合酸液体内进
而进行有效的去除。
然后将经过酸浸之后的催化剂利用热水进行有效的洗涤,从
而将吸附在催化剂表面的重金属可溶盐进行有效的清洗。
通过以上流程对催化剂
的处理之后,使得催化剂的结构得到有效的恢复,但是对于催化剂来讲其活性中
心有了大幅度的境地,经过活化能够使得催化剂的活性得到一定程度上的恢复。
使得催化剂得到活化的有效手段大多数是通过利用铵盐溶液进行一定时间的浸泡。
然后对经过浸泡的催化剂进行有效的过滤再将该部分催化剂放在烘箱内进行有效
的干燥处理从而有效去除催化剂的水分。
2.2关于试验结果的分析
将经过再生技术处理以后的催化剂与新催化剂还有废催化剂其性能进行有效
的比较能够发现,经过再生技术处理过后的非催化裂化催化剂其镍含量得到有效
的去除,同时其活性也得到大幅度的提升。
并且经过再生技术处理以后催化剂的
表面也得到了大幅度的改善。
该部分催化剂能够与新催化剂进行混合使用。
三、关于其他再生技术分析
对于传统形式的催化剂再生技术来讲其是经过焙烧然后在经过酸浸方式使得
催化剂得到再生,对于此种形式的再生技术来讲其很容易造成催化剂的结构产生
一定程度的破坏。
相关学者提出了一种新的废催化裂化再生技术,其主要是经过
一些特殊的气体中进行对催化剂展开气相活化,在利用稀酸进行有效的处理,经
过对采用该技术处理的废催化剂进行分析能够发现该技术对于脱除废催化剂内的
重金属镍有着良好的效果挺尸能够保障其活性以及具有较强的稳定性。
此外中南
大学的学者也开发出了一种对于废催化剂再生的新工艺。
对于该工艺来讲其主要
是采用了铝后回收的镍钴钒钼的手段,利用钠化焙烧从而有效的增强了对氧化铝
的吸取兴国,并且促进了对重金属物质的有效分析,从而之后的综合回收提供了
有效的支持。
结束语
现阶段催化裂化催化剂相关的技术得到了快速的发展,并且不断的出现新型
高转化率以及抗污染和使用周期长的催化剂产生,然而现阶段对于环保方面的要
求也在随着社会的发展不断的严格起来,同时炼油领域对于该方面的要求,从而
有效的促进了对废催化剂再生技术的不断深化的研究。
在今后的发展过程中再生
技术应当向着低能耗、低成本以及在操作方面相对较为简单的方向发展。
同时在
环保方面的问题上需要确保其不会出现二次环保方面的问题的方向发展。
再生技
术在工艺上相对较为简单并且操作也相对较为方便。
对于废催化剂的再生利用能
够有效的降低其对自然环境的污染同时能够减少对新催化剂的使用,从而有效的
显示经济利益的有效增长同时也能够使得环境得到有效的保护。
参考文献:
[1]许美真.废催化裂化平衡剂及钾长石精粉的高值化应用研究[D].福建师范大学,2015.
[2]方乙琳.气流加速度分选在废催化剂活性分选中的研究及应用[D].华东理工
大学,2018.
[3]陈黎黎.李小军:知行合一13载,“催化专家”美名传[J].班组天地,2017(06):90.
作者简介:
赵檀(1982-12),男,汉族,籍贯:黑龙江省哈尔滨市,当前职称:工程师,学历:硕士,研究方向:加氢催化剂与加氢工艺。