100万吨催化裂化装置反应-再生系统工艺设计
石油加工生产技术:催化裂化反应原理及工艺流程

二级旋风分离器 13~20m/s 7~8m/s 汽提
再生催化剂 650~700 ℃
200~℃250高低并列反应再生系统
二、分馏系统
过热油气 460~480 ℃
为了取走分馏塔的过剩热量,设有塔顶循环回流、一 个至两个中段回流以及塔底油浆循环
三、吸收解吸系统有两种流程:
双塔流程
单塔流程
双塔流程由于单塔流程,可同时满足高吸收率和高 解析率的要求。
2、三阀
单动滑阀用于床层反应器催化裂化和高低并列式提升管催化裂化装置。 其作用是:正常操作时用来调节催化剂在两器间的循环量,出现重大事故时用 以切断再生器与反应沉降器之间的联系,以防造成更大事故。
双动滑阀
双动滑阀是一种两块阀板双向动作的超灵敏调节阀,安装在再生器出口管线上 (烟囱),其作用是调节再生器的压力,使之与反应沉降器保持一定的压差。
单动滑阀结构示意图 双动滑阀结构示意图
塞阀
同轴式
塞阀用于同轴式催化 裂化装置
塞阀比滑阀具有以下优点: (1)磨损均匀而且较少; (2)高温下承受强烈磨损的部 件少; (3)安装位置较低,操作维修 方便。
(三)三机
三机包括
ห้องสมุดไป่ตู้主风机
气压机
增压机
五、催化裂化装置主要设备
(一)三器——提升管反应器、沉降器及再生器
提升管反应器
预提升:由提升 管底部吹入水蒸 气(称预提升蒸 汽),使出再生 斜管的再生催化 剂加速,以保证 催化剂与原料油 相遇时均匀接触。
沉降器
沉降器是用碳 钢焊制成的圆筒 形设备,上段为 沉降段,下段是 汽提段。
再生器
再生器的作用 是为催化剂再 生提供场所和 条件。
催化裂化反应原理及工艺流程
石油化工催化裂化装置工艺流程图.docx
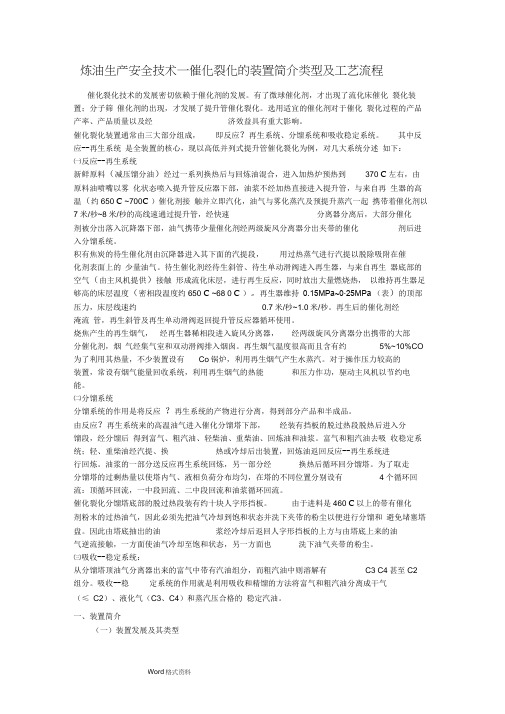
炼油生产安全技术一催化裂化的装置简介类型及工艺流程催化裂化技术的发展密切依赖于催化剂的发展。
有了微球催化剂,才出现了流化床催化裂化装置;分子筛催化剂的出现,才发展了提升管催化裂化。
选用适宜的催化剂对于催化裂化过程的产品产率、产品质量以及经济效益具有重大影响。
催化裂化装置通常由三大部分组成,即反应?再生系统、分馏系统和吸收稳定系统。
其中反应--再生系统是全装置的核心,现以高低并列式提升管催化裂化为例,对几大系统分述如下:㈠反应--再生系统新鲜原料(减压馏分油)经过一系列换热后与回炼油混合,进入加热炉预热到370 C左右,由原料油喷嘴以雾化状态喷入提升管反应器下部,油浆不经加热直接进入提升管,与来自再生器的高温(约650 C ~700C )催化剂接触并立即汽化,油气与雾化蒸汽及预提升蒸汽一起携带着催化剂以7米/秒~8米/秒的高线速通过提升管,经快速分离器分离后,大部分催化剂被分出落入沉降器下部,油气携带少量催化剂经两级旋风分离器分出夹带的催化剂后进入分馏系统。
积有焦炭的待生催化剂由沉降器进入其下面的汽提段,用过热蒸气进行汽提以脱除吸附在催化剂表面上的少量油气。
待生催化剂经待生斜管、待生单动滑阀进入再生器,与来自再生器底部的空气(由主风机提供)接触形成流化床层,进行再生反应,同时放出大量燃烧热,以维持再生器足够高的床层温度(密相段温度约650 C ~68 0 C )。
再生器维持0.15MPa~0∙25MPa (表)的顶部压力,床层线速约0.7米/秒~1.0米/秒。
再生后的催化剂经淹流管,再生斜管及再生单动滑阀返回提升管反应器循环使用。
烧焦产生的再生烟气,经再生器稀相段进入旋风分离器,经两级旋风分离器分出携带的大部分催化剂,烟气经集气室和双动滑阀排入烟囱。
再生烟气温度很高而且含有约5%~10%CO 为了利用其热量,不少装置设有Co锅炉,利用再生烟气产生水蒸汽。
对于操作压力较高的装置,常设有烟气能量回收系统,利用再生烟气的热能和压力作功,驱动主风机以节约电能。
第六节催化裂化反应再生系统资料
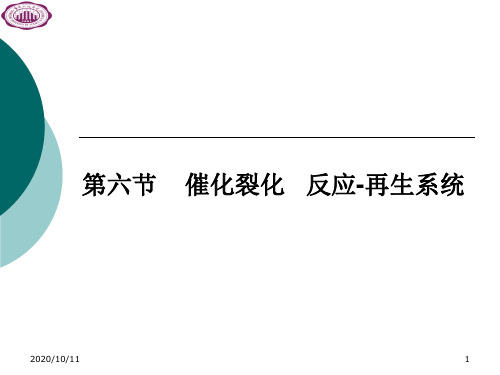
2020/10/11
19
c.快速床(循环流化床)再生 ➢气相转化成连续相,催化剂颗粒变为分散相,从而强化 了烧碳过程 ➢随着气速的提高,返混程度减小,中、上部接近于平推 流,也有利于烧碳强度的提高 ➢在快速流化床区域,必须有较大的固体循环量才能保持 较高的床层密度 ➢催化裂化装置的烧焦罐再生就是属于循环流化床的一种 再生方式
➢再生温度对烧碳反应速率的影响十分显著,提高再生温 度是提高烧碳速率的有效手段,在单段再生时,密相创层 的温度一般不超过730℃
➢工业上一般采用的空气线速为0.6~0.7m/s ➢工业装置采用的再生器压力在0.25~0.4MPa(绝)之间 ➢单段再生的主要问题是再生温度的提高受到限制和密相 床层的有效催化剂含炭量低
9
分段反应
➢不同的馏分需要不同的反应条件,理想选择是不同的 馏分在不同的场所和条件下进行反应 ➢两段提升管(Ⅰ型)催化裂化:
★第一段提升管只进新鲜原料,段间抽出柴油出装置 ★第二段提升管单独进循环油,显著改善产品分布 ★第二段提升管底部回炼汽油,降低汽油烯烃含量 ➢分段进料避免了新鲜原料和油浆的相互干扰
2020/10/11
18
b.两段再生 ➢两段再生是把烧碳过程分为两个阶段进行 ➢与单段相比,两段再生的主要优点是:
①对于全混床反应器,第一段出口的半再生剂的含碳量 高于再生剂的含碳量,从而提高了烧碳速率;
②在第二段再生时可以用新鲜空气和更高的温度,提高 了烧碳速率;
③第二段内的水气分压可以很低,减轻了催化剂的水热 老化;且第二段的催化剂藏量比单段再生器的催化剂藏量低, 停留时间较短。因此,第二段可采用较高的再生温度。
2020/10/11
20
2020/10/11
21
第六节 催化裂化反应-再生系统

2010-112010-11-7
石油加工工程
4
提升管下部进料段的油剂接触状况对重油催化裂化的反应 提升管下部进料段的油剂接触状况对重油催化裂化的反应 油剂接触状况 有重要影响。减小原料油的雾化粒径,可增大传热面积, 有重要影响。减小原料油的雾化粒径,可增大传热面积, 从而提高了原料的气化率, 从而提高了原料的气化率,且可以改善产品产率的分布 汽提汽用量一般为 沉降器下面的汽提段的作用是用水蒸气脱出催化剂上吸附 沉降器下面的汽提段的作用是用水蒸气脱出催化剂上吸附 2~3kg/1000kgCat 的油气及置换催化剂颗粒之间的油气。汽提段的效率与水 的油气及置换催化剂颗粒之间的油气。汽提段的效率与水 蒸气用量、催化剂在汽提段的停留时间、 蒸气用量、催化剂在汽提段的停留时间、汽提段的温度及 压力、 压力、以及催化剂的表面结构有关 重油催化裂化则用4 重油催化裂化则用4~ 5kgH2O/1000kgCat
2010-112010-11-7 石油加工工程 10
短反应时间
两段技术,采用分段反应, 两段技术,采用分段反应,两段反应时间之和比常规 催化反应时间还短( 秒以内) 催化反应时间还短(2秒以内)
催化裂化装置工艺设计
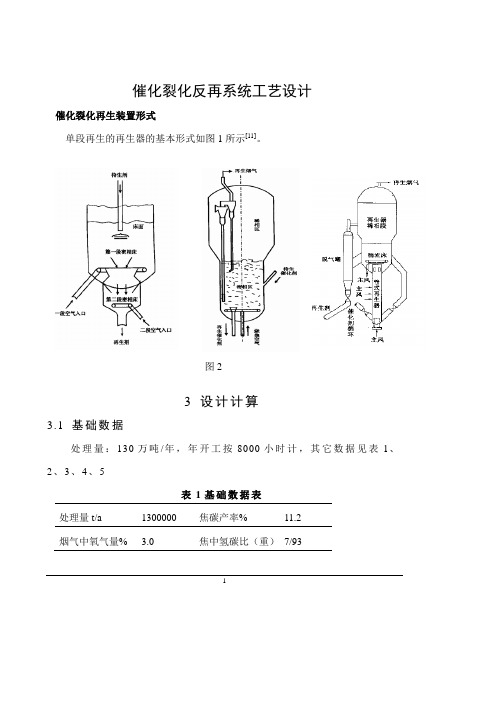
1催化裂化反再系统工艺设计催化裂化再生装置形式单段再生的再生器的基本形式如图1所示[11]。
图23 设计计算3.1 基础数据处理量:130万吨/年,年开工按8000小时计,其它数据见表1、2、3、4、5表1基础数据表处理量t/a 1300000 焦碳产率%11.2烟气中氧气量%3.0焦中氢碳比(重) 7/93空气相对湿度% 56 大气温度℃15大气压力KPa 101 再生剂含碳量% 0.06表2 原料和产品性质项目原料有汽有柴有回炼有比重d2040.8957 0.7477 0.8541 0.9027恩氏蒸馏10﹪93 236 403 30﹪112 255 419 50﹪132 286 433 70﹪152 317 450 90﹪173 349 489残炭w﹪ 4.34回炼比:0.5υ100(厘斯)27.50苯胺点121.00表3 产品收率产品总气体汽有柴有焦炭合计产率w﹪12.0 40.1 36.7 11.2 100表4 气体组成组分H2H2S C01 C02 C=2C03 w﹪ 5.04 0.29 5.13 4.75 4.09 5.23 组分C=3IC04NC04C=4-1IC=4TC=4-2C=4-22w﹪22.14 12.17 3.71 20.25 9.6 7.6表5 催化剂组成孔体积骨架密度充气密度筛分组成wt﹪ml/g g/ml g/ml <20µ 20~40µ 40~80µ 80~110µ >110µ 0.146 2.86 0.85 7.1 20.2 60.5 11.2 1.0 3.2 再生部分计算3.2.1 燃烧计算(1) 焦中碳量、氢量及硫量烧焦量=1300000×11.2%=18200 kg/h先计算干气平均分子量M=34×0.29+2×5.04+16×5.13+30×4.75+28×4.09+44×5.23+42×22.14+58×12.17+56×9.6+56×7.6+56×20.25+58×3.71=45.06 kg/kmol焦中硫含量=原料中硫含量-干气中硫含量即1300000×0.13%―1300000×12.0%×0.29%×32÷45.06=171.566 kg/h=5.36 kmol/h则烧碳量=(18200-171.57) ×93%=16766.44kg/h=1397.2 kmol/h烧氢量=(18200-171.57) ×7%=1262kg/h =631 kmol/h(2) 烧焦需空气量和燃烧产物量3①理论耗O2量碳生成二氧化碳耗氧量=1397.2×1=1397.2 kmol/h氢生成水耗氧量=631×0.5=315.5 kmol/h硫生成二氧化硫耗氧量=5.36×1=5.36 kmol/h理论耗氧量=1397.2+315.5+5.36=1718.06 kmol/h=54977.92 kg/h②燃烧产物量碳生成CO2量=1397.2 kmol/h=61476.8 kg/h氢生成H2O量=631 kmol/h=11358 kg/h硫生成SO2量=5.36mol/h=343.04 kg/h③理论干空气量理论氮气量=1718.06×79/21=6463.18kmol/h=180969kg/h 理论干空气量=1718.06×32+6463.18×28=235947 kg/h空气相对分子量=235947÷8181.24=28.84 kg/kmol④实际干空气量烟气中过剩氧体积3%则:3%= O2过/(理论干烟气量+ O2过+ N2过)= O2过/(CO2+N2理+SO2+ O2过+ N2过)= O2过/(1397.2+6463.18+5.36+ O2过+ O2过×79/21) 故:O2过=275.3 kmol/hN2过=275.3×79/21=1035.7 kmol/h4过剩干空气量=275.3+1035.7=1311 kmol/h实际干空气量=8181.24+1311=9492.25kmol/h=273756.45 kg/h⑤湿空气量(主风量)大气温度15℃,相对湿度56%,查《石有加工工艺学》中册图6—29,得绝对湿度为0.009kg水汽/kg干空气空气带入水量=273756.45×0.009=2463.81kg/h=136.88 kmol/h湿空气量=9492.25+136.88=9629.13kmol/h=215692.5 [m3(N)/h]=3594.87 [m3(N)/min]此即正常主风量依此量×110%,可作为选主风机的依据:3594.87×110%=3954.4[m3(N)/min]故选D800–33型主风机6台并联。
催化裂化的装置简介及工艺流程
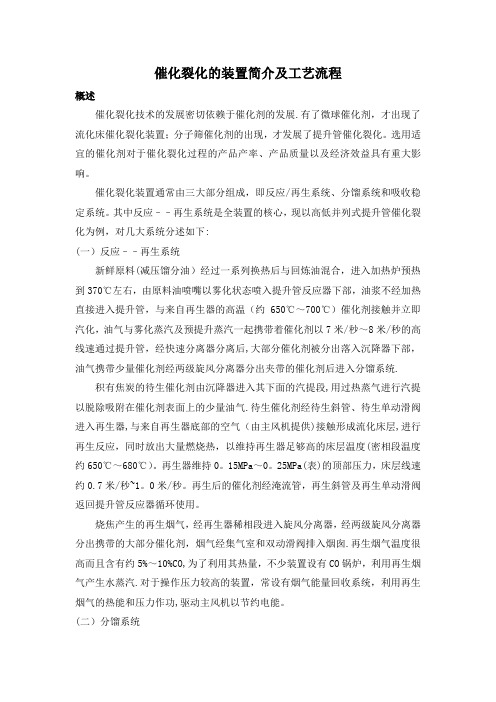
催化裂化的装置简介及工艺流程概述催化裂化技术的发展密切依赖于催化剂的发展.有了微球催化剂,才出现了流化床催化裂化装置;分子筛催化剂的出现,才发展了提升管催化裂化。
选用适宜的催化剂对于催化裂化过程的产品产率、产品质量以及经济效益具有重大影响。
催化裂化装置通常由三大部分组成,即反应/再生系统、分馏系统和吸收稳定系统。
其中反应––再生系统是全装置的核心,现以高低并列式提升管催化裂化为例,对几大系统分述如下:(一)反应––再生系统新鲜原料(减压馏分油)经过一系列换热后与回炼油混合,进入加热炉预热到370℃左右,由原料油喷嘴以雾化状态喷入提升管反应器下部,油浆不经加热直接进入提升管,与来自再生器的高温(约650℃~700℃)催化剂接触并立即汽化,油气与雾化蒸汽及预提升蒸汽一起携带着催化剂以7米/秒~8米/秒的高线速通过提升管,经快速分离器分离后,大部分催化剂被分出落入沉降器下部,油气携带少量催化剂经两级旋风分离器分出夹带的催化剂后进入分馏系统.积有焦炭的待生催化剂由沉降器进入其下面的汽提段,用过热蒸气进行汽提以脱除吸附在催化剂表面上的少量油气.待生催化剂经待生斜管、待生单动滑阀进入再生器,与来自再生器底部的空气(由主风机提供)接触形成流化床层,进行再生反应,同时放出大量燃烧热,以维持再生器足够高的床层温度(密相段温度约650℃~680℃)。
再生器维持0。
15MPa~0。
25MPa(表)的顶部压力,床层线速约0.7米/秒~1。
0米/秒。
再生后的催化剂经淹流管,再生斜管及再生单动滑阀返回提升管反应器循环使用。
烧焦产生的再生烟气,经再生器稀相段进入旋风分离器,经两级旋风分离器分出携带的大部分催化剂,烟气经集气室和双动滑阀排入烟囱.再生烟气温度很高而且含有约5%~10%CO,为了利用其热量,不少装置设有CO锅炉,利用再生烟气产生水蒸汽.对于操作压力较高的装置,常设有烟气能量回收系统,利用再生烟气的热能和压力作功,驱动主风机以节约电能。
催化裂化
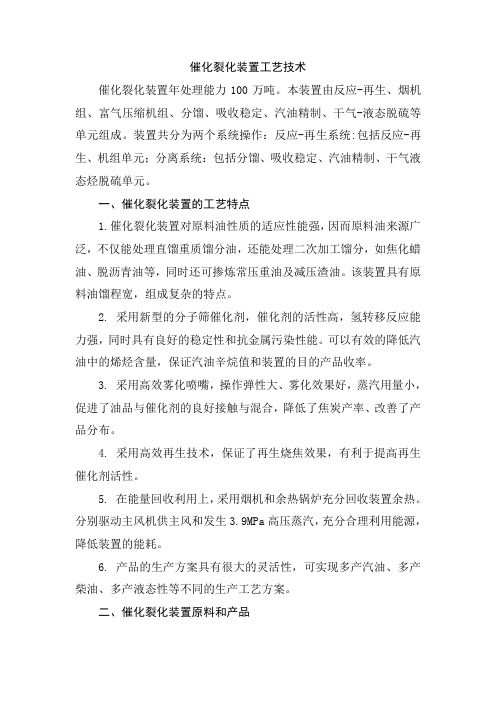
催化裂化装置工艺技术催化裂化装置年处理能力100万吨。
本装置由反应-再生、烟机组、富气压缩机组、分馏、吸收稳定、汽油精制、干气-液态脱硫等单元组成。
装置共分为两个系统操作:反应-再生系统:包括反应-再生、机组单元;分离系统:包括分馏、吸收稳定、汽油精制、干气液态烃脱硫单元。
一、催化裂化装置的工艺特点1.催化裂化装置对原料油性质的适应性能强,因而原料油来源广泛,不仅能处理直馏重质馏分油,还能处理二次加工馏分,如焦化蜡油、脱沥青油等,同时还可掺炼常压重油及减压渣油。
该装置具有原料油馏程宽,组成复杂的特点。
2. 采用新型的分子筛催化剂,催化剂的活性高,氢转移反应能力强,同时具有良好的稳定性和抗金属污染性能。
可以有效的降低汽油中的烯烃含量,保证汽油辛烷值和装置的目的产品收率。
3. 采用高效雾化喷嘴,操作弹性大、雾化效果好,蒸汽用量小,促进了油品与催化剂的良好接触与混合,降低了焦炭产率、改善了产品分布。
4. 采用高效再生技术,保证了再生烧焦效果,有利于提高再生催化剂活性。
5. 在能量回收利用上,采用烟机和余热锅炉充分回收装置余热。
分别驱动主风机供主风和发生3.9MPa高压蒸汽,充分合理利用能源,降低装置的能耗。
6. 产品的生产方案具有很大的灵活性,可实现多产汽油、多产柴油、多产液态性等不同的生产工艺方案。
二、催化裂化装置原料和产品(一)原料催化裂化装置原料主要是减三线、减四线蜡油和加氢蜡油HGO,一般来讲,衡量原料油性质指标有:馏份组成、烃类族组成、残碳、重金属、硫氮含量等五个方面。
(l) 馏份组成:馏份组成可以辨别原料的轻重和沸点范围的宽窄,在组成类型相近时,馏份越轻,越不易裂化,馏份越重,越容易裂化,因为轻组分多,不但裂化条件苛刻,而且减少了装置处理能力,同时降低汽油的辛烷值。
重组分多,使重金属含量增加及焦炭产率增加,轻质油收率下降,还会使催化剂中毒。
(2) 烃类族组成:原料油的烃类族组成说明了原料油被催化剂吸附反应的快慢。
催化裂化工艺流程及主要设备
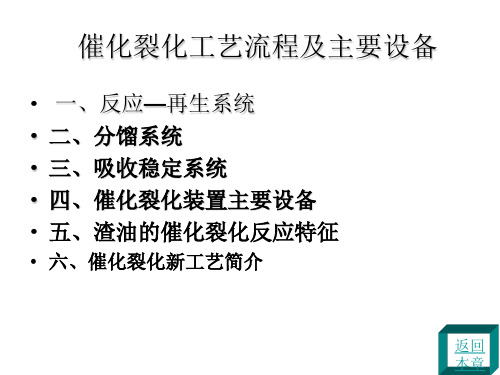
③催化剂减活及磨损较少; ④易于操作,能耗及投资少; ⑤能满足环保要求
• 工业上再生器的 主要形式可分为 三类:单段再生、 两段再生、快速 床再生
单段再生
单段再生的温度多在650~700℃之间。 提高再生温度是提高烧碳速率的有效手段。 在高温下,催化剂的水热失活也比较严重。 因此,在单段再生时,密相床层的温度一 般很少超过730℃。 单段再生的主要问题是再生温度的提高受 到限制和密相床层的有效催化剂含碳量低。
塞阀
塞阀用于同轴式催化 裂化装置
同轴式
塞阀比滑阀具有以下优点: (1)磨损均匀而且较少; (2)高温下承受强烈磨损的部 件少; (3)安装位置较低,操作维修 方便。
三机
• 主风机承担着向再生器提供烧焦用风的重 要任务。 • 气压机的作用是将分馏部分来的富气压力 提升到吸收稳定部分操作所需的压力。 • 增压机为外取热器提供提升风和流化风以 及为待生套筒提供流化风
100~125mm厚的隔热耐磨衬里。 伸到汽提段、沉降器内的部分只设耐磨衬里。 提升管的上端出口处设有气-固快速分离机构,用于使催化剂与油气 快速分离以及抑制反应的继续进行
快速分离机构的形式有多种多样,比较简单的有伞帽形、T字形的构
件,现在用得比较多的是初级旋风分离器
沉降器
• 沉降器的作用是使来自 提升管的油气和催化剂 分离,油气经旋风分离 器分出所夹带的催化剂 后经集气室去分馏系统; 由提升管快速分离器出 来的催化剂靠重力在沉 降器中向下沉降落入汽 提段。
也提供裂化反应所需的热量
分布器可分为板式(蝶形)和管式(平面树枝或环形)两种
重催再生器需设取热设备: a.内取热式 b.外取热式
主要要求有:
①再生剂的含炭量较低,一般要求低于0.2%,甚
- 1、下载文档前请自行甄别文档内容的完整性,平台不提供额外的编辑、内容补充、找答案等附加服务。
- 2、"仅部分预览"的文档,不可在线预览部分如存在完整性等问题,可反馈申请退款(可完整预览的文档不适用该条件!)。
- 3、如文档侵犯您的权益,请联系客服反馈,我们会尽快为您处理(人工客服工作时间:9:00-18:30)。
兰州理工大学毕业设计设计题目:100万吨催化裂化装置反应-再生系统工艺设计院系:石油化工学院专业班级:化学工程与工艺学生姓名:王晶指导教师:赵秋萍2010年1 月14 日毕业设计任务书一、设计题目:100万吨催化裂化装置反应-再生系统工艺设计二、设计内容以某炼油厂的直馏馏分油为原料,建一个年产100万吨的催化裂化装置。
主要生产稳定汽油、轻柴油。
年开工按330天计算。
三、基本数据1、处理量:100万吨/年2、开工时:8000 小时/年3、原始数据及再生-反应及分馏操作条件原料油及产品性质分别见表1、表2产品的收率及性质见表3 再生器操作及反应条件见表4、提升管反应器操作条件表5 催化裂化分馏塔回流取热分配见表6分馏塔板形式及层数见表7 分馏塔操作条件表见8表1 原料油及产品性质物料,性质稳定汽油轻柴油回炼油回炼油浆原料油密度0.7423 0.8707 0.8800 0.9985 0.8995恩氏蒸馏℃初馏点54 199 288 224 10% 78 221 347 380 377 30% 106 257 360 425 438 50% 123 268 399 450 510 70% 137 300 431 470 550 90% 163 324 440 490 700 终馏点183 339 465平均相对分子量表2 原料油的主要性质项目数据项目数据密度0.8995 族组成分析/W%馏程℃饱和烃62.27 初馏点224 芳烃2510% 377 胶质11.88 30% 438 沥青质0.85 350℃馏出率/v% 7.5 重金属含量/μg×g-1500℃馏出率/v% 49 Ni 5.99 元素组成/w% V 4.77H 12.85 Fe 5.91 硫/w% 0.77 残炭,W% 5.38表3 产品产率(质量分数)产品产率% 流量,t/h5.0液化气11.0稳定汽油48.0轻柴油21.2油浆 6.0焦炭8.0损失0.8原料油100.0表4 再生器操作条件项目数据备注再生器顶部压力/ MPa 0.200主风入再生器温度/℃162再生器密相温度/℃700待生剂温度/℃大气温度/℃25大气压力/ MPa 0.1013空气相对湿度/% 70烟气组成(体)/%CO2 14.2CO 0.2O2 4.0焦碳组成/ H/C,质待生剂含碳量/% 1.10再生剂含碳量/% 0.02烧焦碳量/ t/h表5 提升管反应器操作条件项目数据备注提升管出口温度/℃505沉降器顶部压力/ MPa 0.200原料预热温度/℃235回炼油进反应器温度/℃265回炼油浆进反应器温度/℃350催化剂活性/% 60.0剂油比 6.0反应时间/ S 3.0回炼比0.5催化剂循环量/ t×h-1原料进料量/ t×h-1回炼油/回炼油浆1:0.25表6 催化裂化分馏塔回流取热分配(参考)物料顶循环回流一中循环回流二中循环回流油浆循环回流取热比例% 15~20 15~20 15~20 40~50 备注表7 分馏塔塔板形式及层数(参考)序号塔段塔板形式层数1 油浆换热段人字挡板或园型挡板6~82 回炼油抽出以下固舌形 23 回炼油抽出口上至一中回流抽出下口下固舌形,条形浮阀,填料10~124 一中回流固舌形,条形浮阀,填料3~45 轻柴油抽出以上至顶循环回流段抽出下固舌形,筛孔,条形浮阀,填料8~9 6 循环回流段固舌形,条形浮阀,填料3~4分馏塔总塔板数28~32表8 催化裂化分馏塔操作条件(参考)序号物料温度/℃压力/MPa塔板位置塔板类型1 分馏塔塔顶油气125 0.255 30 浮阀2 顶循环回流100 30 浮阀3 顶循环回流出塔160 27 浮阀4 富吸收油(再吸收油,视为轻柴油)返分馏塔120 20 浮阀5 轻柴油抽出220 19 浮阀6 一中回流返回160 18 浮阀7 一中回流抽出275 16 固舌形8 回炼油返回210 5 固舌形9 回炼油抽出265 2 固舌形10 油浆循环回流返回270 1 固舌形11 回炼油浆抽出350 塔底12 循环/外排油浆抽出350 塔底13 轻柴油汽提蒸汽温度250 1.014 反应油气进分馏塔500 塔底四、设计步骤(一)再生系统计算1、燃烧计算;2、热量平衡;3、催化剂循环量计算;4、空床流速计算;(二)提升管反应器计算1、物料衡算;2、热量衡算;3、提升管工艺计算;4、旋风分离器工艺计算;五、要求(一)应完成的图:1、通过实习绘出带控制点的催化裂化装置工艺流程图,要求用CAD出图。
2、反应-再生装置的工艺尺寸图,要求用CAD出图。
(二)论文印装1、毕业设计用A4大小纸张手写。
2、打印要求:正文用宋体小四字号,行间距18磅;版面页边距上3cm,下、左2.5cm,右2cm;页眉加“兰州理工大学石油化工学院毕业设计”字体为隶书3号字居中,页眉距边界2cm;页码用小五号字底端居中,页脚距边界1.75cm。
(三)论文结构及要求1、毕业论文由以下部分组成:A. 封面;B. 毕业设计任务书;C.中文摘要,关键词;D. 英文摘要,关键词;E. 目录;F. 正文;G. 致谢;H. 参考文献;I. 附录;J. 有关图纸(大于3#图幅时单独装订)。
2、中英文摘要要求中文在前,英文在后,应陈述简要,尽量反映论文的主要信息,内容包括研究目的、方法、成果和结论,不含图表,不加注释,具有独立性和完整性。
3、关键词是反映毕业设计主题内容的名词,是供检索使用的。
主题词条应为通用技术词汇,不得自造关键词,尽量从《汉语主题词表》中选用。
按词条外延层次(学科目录分类),由高至低顺序排列。
4、目录按三级标题编写,要求层次清晰,且要与正文标题一致。
主要包括绪论、正文主体、结论、致谢、主要参考文献及附录等。
(四)毕业设计(论文)装订顺序1、毕业设计(论文)封面2、毕业设计(论文)任务书3、中文摘要、关键词4、英文摘要、关键词5、目录(列出三级)6、正文7、附录8、外文翻译(原文、译文)9、封底(五)工作量1.参考资料10篇以上,其中外文资料不少于2篇;2.实习报告不少于3000字3.文献综述不少于8000字;4.毕业设计说明书,一般不得少于1.5万字,5.中英文摘要约400字左右,关键词3~5个,6.学生另需完成2~3万印刷符号的外文文献翻译1篇。
7.设计计算书不少120页八时间安排毕业设计说明书题目(题目、姓名、导师)目录一、绪论(文献综述)(一)课题背景、发展简史1、- - - - - - -(内容省略)- - - - - - - - - - - - - - - -2、- - - - - - -(内容省略)- - - - - - - - - - - - - - - -3、设计依据或项目来源(二)国内外现状1、- - - - - - -(内容省略)- - - - - - - - - - - - - - - -2、- - - - - - -(内容省略)- - - - - - - - - - - - - - - -3、- - - - - - -(内容省略)- - - - - - - - - - - - - - - -(三)选题的依据(或项目来源)、前景、计划和方案1、- - - - - - -(内容省略)- - - - - - - - - - - - - - - -2、- - - - - - -(内容省略)- - - - - - - - - - - - - - - -3、- - - - - - -(内容省略)- - - - - - - - - - - - - - - -二、主要设计参数及技术指标、设计及依据、工艺流程等(一)- - - - - - - - (内容省略) - - - - - - - - - - - --1. - - - - - - - - -(内容省略) - - - - - - - - - - - - - -2. - - - - - - - -(内容省略) - - - - - - - - - - - - - - -(1)- - - - - - - - (内容省略) - - - - - - - - - - - -(2)- - - - - - - - (内容省略) - - - - - - - - - - - -(二)- - - - - - - - (内容省略) - - - - - - - - - - - --1. - - - - - - - - -(内容省略)- - - - - - - - - - - - - -2. - - - - - - - - (内容省略) - - - - - - - - - - - -- - -(1)- - - - - - - - (内容省略) - - - - - - - - - - - -(2)- - - - - - - - (内容省略) - - - - - - - - - - - -(内容主要包括:生产流程或生产方案的确定;生产流程简述及说明;生产所用原料油及性质说明;产品的方案、性质及恩氏蒸馏曲线图;原油实沸点曲线及平衡汽化曲线图;精馏塔工艺参数计算结果图;精馏塔全塔汽、液相分布图及结果分析;精馏塔塔径及塔高;精馏塔的水力学计算结果参数表;常压精馏塔的操作区示意图及分析;精馏塔工艺猜算的计算机程序及框图;常减压工艺流程图;设备装配图)三、计算、工艺要求等(一)- - - - - - - - -(内容省略)- - - - - - - - - - - - -(二)- - - - - - - - (内容省略) - - - - - - - - - - - -四、说明、性能、安全评价等五、结论六、致谢七、参考文献论文中被引用的参考文献序号置于所引用部分的右上角,如******[1]。
参考文献表上的著作按论文中引用顺序排列。
著作按如下格式著录:[序号]著者. 书名(期刊).出版地:出版社,出版年.如:[1] 江北. 场论. 北京: 科学技术出版社, 2000年2月论文按如下格式著录:[序号]著者.论文题目.期刊名,年,卷(期):起始页码-结束页码.如:[1] 肖安陆, 孔渝华. 氧化铁脱硫剂硫容的不同测定方法及其结果比较.湖北化工2001,16(2):22~25八、附录(一)一些图表(二)其他(收集原始的记录、图表、测试报告单,个人实习体会、收获,个人意见、建议等。
)九、外文翻译(原文、翻译)十、封底石油炼制工程,林世雄(第三版),或石油加工工艺;催化裂化工艺设计,后一本尽量借。
毕业设计内容简介格式要求一、版面要求1、A4幅面,4页。
2、行间距:15磅,首行缩进2字符。
3、页边距:上0.75英寸、下1英寸、左0.625英寸、右0.625英寸。