甲醇裂解制氢导热油工段
甲醇裂解制氢导热油工段

2.合成型导热油
合成型:是通过人工合成方法获得的。以化工或石油化工产品为原料,经过 有机化学反应合成工艺制得的单一物质或组分简单的较纯净的物质。这类物质的 化学结构有合成芳烃、醇、醚、酯、硅油、氯代烃等 。
这类产品使用温度范围在-40~400℃,热稳定性好,使用寿命长,可再生,即 可以在液态下使用,也可以在气态下使用,但价格昂贵。目前占据世界市场的主 要为合成芳烃系列产品,其代表是联苯——联苯醚混合物(俗称“道生油”)氢 化三联苯氯代烃导热油。
6. 初馏 点和 馏程
第 五 部 分 导热油系统的结垢和清洗
1.结垢形成
导热油在传热过程中主要发生三种化学反应:热氧化反应、热裂解和热聚合反应。结焦产 生于热氧化反应和热聚合反应。热聚合反应因导热油在加热系统运行过程受热而发生,该反应 会生成稠环芳烃、胶质和沥青质等大分子高沸物,其逐渐沉积于加热器和管路表面,形成结焦。 热氧化反应主要因开式加热系统膨胀槽内的导热油接触空气或参与循环而发生,该反应会生成 低分子或高分子的醇、醛、酮、酸等酸性组分,并进一步生成胶质、沥青质等粘稠物质,最后 形成结焦;热氧化是非正常情况引起的,一旦发生,会加速热裂解和热聚合反应,使粘度迅速 增大,传热效率降低,造成过热和炉管结焦。产生的酸性物质还会造成设备腐蚀和泄漏。
甲醇裂解制氢站导热油工段
部 门:公用工程部 讲解人:王 小 波 时 间:2013-9-11
制 氢装置组成
生产装置由导热油加热工段
、甲醇裂解工段和变压吸附提氢(PSA)
工段三大工段组成。整套装置生产能力600Nm³ /h
工 艺 流 程 图
导热油换热器
高压蒸汽 精甲醇 脱盐水
汽化过热 转化反应 变压吸附 (PSA-H2)循环液 冷却、吸收
甲醇制氢装置操作规程
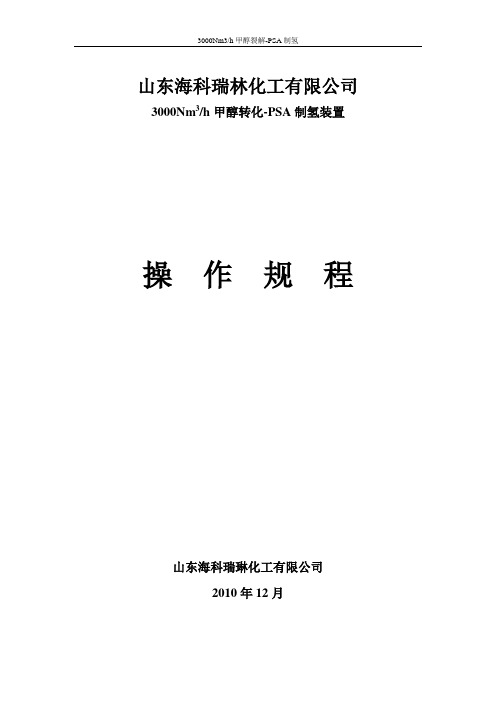
山东海科瑞林化工有限公司3000Nm3/h甲醇转化-PSA制氢装置操作规程山东海科瑞琳化工有限公司2010年12月甲醇裂解转化部分目录1.0前言-----------------------------------------------------22.0料及产品的性格和规格-------------------------------------33.0工艺过程说明---------------------------------------------53.1 工艺过程--------------------------------------------- 53.2 化学反应原理----------------------------------------- 54.0工艺流程叙述--------------------------------------------- 65.0工艺过程主要控制指标------------------------------------- 76.0开车前期工作--------------------------------------------- 97.0操作程序------------------------------------------------- 127.1开车前的准备工作-------------------------------------- 127.2开车操作程序------------------------------------------ 127.3正常操作---------------------------------------------- 147.4催化剂的使用和保护------------------------------------ 168.0环保和安全要点-------------------------------------------- 219.0分析规程-------------------------------------------------- 2210.0安全规程-------------------------------------------------- 301.0 前言氢气广泛用于国民经济各工业部门,特别是近几年来,氢气用户急速增多,传统制氢工艺已不能满足要求。
甲醇裂解法制氢气规程、教材(3)

甲醇裂解制氢装置操作规程................................................................................................... ③甲醇裂解—变压吸附制氢培训教材 (22) (23)甲醇裂解制氢含甲醇蒸汽转化和变压吸附制氢两部分 (33)甲醇裂解装置操作规程 (39)甲醇裂解制取氢气 (56)甲醇裂解制氢装置操作规程目录2.3.原料及转化的规格................................................................................................................... - 3 -3. 工艺.................................................................................................................................................... - 3 -3.1.反应原理................................................................................................................................... - 3 -3.2.工艺过程及化学反应原理....................................................................................................... - 4 -3.3化学反应原理........................................................................................................................... - 5 -3.4.工艺流程叙述........................................................................................................................ - 5 - 4.主要控制指标...................................................................................................................................... - 6 -4.1.原料汽化过热........................................................................................................................... - 6 -4.2.转化反应................................................................................................................................... - 6 -4.3.转化气指标............................................................................................................................... - 7 - 6.操作程序........................................................................................................................................... - 7 -6.1 开车前的准备工作.................................................................................................................. - 7 -6.2 系统置换.................................................................................................................................. - 8 -6.3 汽化过热器开车...................................................................................................................... - 9 -6.4 .转化器开车的条件:.............................................................................................................. - 9 -6.5 正常操作................................................................................................................................ - 10 -6.6 紧急停车操作........................................................................................................................ - 11 -6.7 催化剂的使用和保护............................................................................................................ - 11 - 7.环保和安全要点............................................................................................................................. - 14 - 8.PSA工艺 ........................................................................................................................................ - 14 - 8.1 PSA工作原理和基本工作步骤..................................................................................... - 15 - 8.2.PSA工作过程 .................................................................................................................. - 16 - 9.自动调节系统及工艺过程参数检测.. (20)9.1程序控制自动切换系统(KC-201) (20)9.2.自动调节系统功能说明 (20)9.3 产品气流量计量(FQI-201) (21)9.4.流量控制功能说明 (21)9.5.PLC仪表 (22)9.6.现场工艺参数检测点 (22)10.开车 (23)10.1初次开车前的准备工作 (23)10.2.投料启动 (25)11.停车和停车后再启动 (28)11.1正常停车 (28)11.2紧急停车 (29)11.3临时停车 (29)11.4长期停车 (29)11.5停车后再启动 (30)12.故障与处理方法 (31)13.安全技术 (32)13.1.氢气的性质 (33)13.2.装置的安全设施 (33)13.3.氢气系统运行安全要点 (33)13.4.消防 (34)13.5生产基本注意事项 (35)正文2.3.原料及转化的规格2.3.1原料规格甲醇:符合GB338—2004标准一等品要求。
甲醇裂解变压吸附制氢装置操作手册
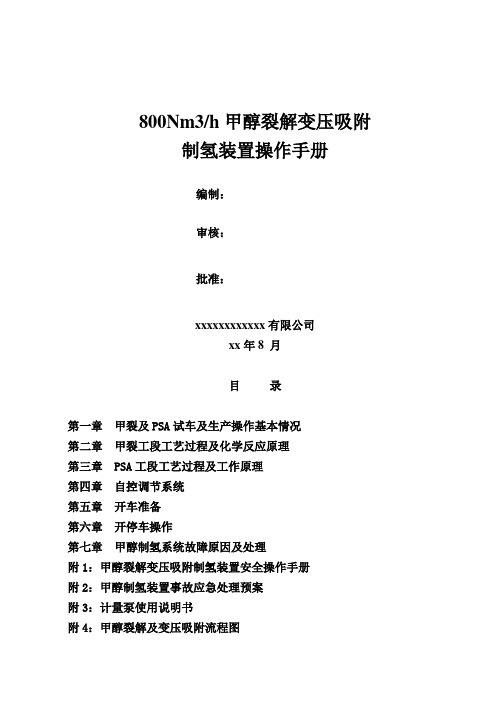
800Nm3/h甲醇裂解变压吸附制氢装置操作手册编制:审核:批准:xxxxxxxxxxxx有限公司xx年8 月目录第一章甲裂及PSA试车及生产操作基本情况第二章甲裂工段工艺过程及化学反应原理第三章 PSA工段工艺过程及工作原理第四章自控调节系统第五章开车准备第六章开停车操作第七章甲醇制氢系统故障原因及处理附1:甲醇裂解变压吸附制氢装置安全操作手册附2:甲醇制氢装置事故应急处理预案附3:计量泵使用说明书附4:甲醇裂解及变压吸附流程图第一章甲裂及PSA试车及生间操作基本情况一、试车及生产操作人员小组人员配置试车组长或生产主管:(业主配置)技术指导:(业主配置)工艺操作工:2人/班分析操作工:1人/班仪表值班:1人/班电气值班:1人/班机械值班:1人/班公用工程协调(调度):1人/班应急对外协作:1人/班安全员:1人/班二、试车时间及地点时间:2019年10月。
地点:甲醇裂解制氢生产区三、工艺指标1.甲醇:符合GB338—2004标准优等品要求。
2.脱盐水:Cl -≤ 1ppmSO42-≤ 1ppm90℃以下稳定,对碳钢、不锈钢无腐蚀电导率≤10μs/cm。
3.温度汽化塔进料温度 140~160℃汽化塔底部温度 160~180℃汽化塔顶部温度~180℃进转化器温度 220~250℃出转化器温度 230~250℃导热油温度 250~280℃出换热器转化气温度 120~140℃出冷凝器转化气温度≤40℃4.压力导热油进口压力0.4~0.6MPa进工段冷却水压力≥0.3 MPa进工段仪表空气压力≥0.4~0.6 MPa 5.浓度甲醇~50%(Wt)水~50%(Wt)转化气组成如下:H273~74.5%23~24.5%CO2CO 0~1%≤ 200ppmCH46.产品气H2≥99.99%(v/v)7.分析内容第二章甲裂工段工艺过程及化学反应原理第一节工艺过程甲醇催化裂解、转化工艺过程包括:原料汽化过程、催化裂解转化反应、转化气冷却冷凝、气液分离等。
氢化车间操作规程

制氢岗位工艺操作规程1目的:制定制氢岗位工艺操作规程;2范围:适应于甲醇裂解和PSA分离的操作要求;3责任:确保操作人员的安全操作和管理人员的责任落实;4内容:4.1任务:按照1:1比例配制的甲醇与纯化水混合加热气化,在一定温度、压力条件下通过催化剂发生催化裂解反应和一氧化碳变换反应后生成氢气和二氧化碳,再经过四塔二均PSA变压吸附分离提纯,制得含氢量99.9%的氢气供生产使用。
CH3OH CO + 2H2 - 90.7 KJ/molCO + H2O CO2 + H2 + 41.2 KJ/mol4.2工艺流程冷却水板式换热器冷凝器吸附塔ABCD氢气去中压储罐冷却水4.3主要工艺指标:醇水混合液比重920+10≤25%混合气H2≥75% CO2催化剂温度 250+5℃系统压力 0.8-1.0 Mpa氢气含量 99.99%吸附时间 420—480秒YL—1 球状480 Kg,YL—2条状960 Kg,YL—3 球状950 Kg) 4.5 制氢的操作要点:1)开车前必须清扫、试压、试漏、置换,电器、仪表必须齐全正常,然后进行催化剂还原升温,升温速率每小时15℃。
2)导热油升温必须缓慢,按照有体热油炉厂家的要求进行,温度不能猛升猛降,以保证制氢催化剂的还原需要。
3)计量泵开启后,流量的调节逐步增大,按照甲醇:纯化水 1:1的方式,先把水调大一些,逐步使混合液的比重符合生产要求。
4)催化剂还原结束后,温度达到反应要求时,按照催化剂的要求初期、中期、后期三个阶段的方式,控制好合适的温度指标,计量泵的流量逐步提高至最大设计值。
5)当分析原料气合格后,打开入提氢系统的进口阀,关闭放空阀,进行提氢系统的置换、冲洗、提压。
6)提氢系统开车可用手动操作,各塔输流置换、全部置换合格,分析含量>99.9% CO﹤100ppm时,即可关闭放空阀,向中压罐冲压。
H27)提氢系统投入四塔二均自动控制阶段后,注意各塔压力变化和各气动阀的运行状况。
氢气装置安全操作规程

编号:Linkye页码 :1/32 1500Nm3/h甲醇裂解制氢装置操作规程编号:Linkye页码 :2/32第一章工艺简介本装置以甲醇、脱盐水为原料,经预热、汽化、催化转化和冷冻干燥净化,所得转化气,再送入变压吸附装置精制,最后得到纯度≥99.999%的氢气送至用户。
系统操作压力为1.0~1.5MPa,属中低压操作装置,转化裂解反应温度在240~290℃范围,由导热油循环供热。
装置组成本装置包括甲醇罐区、脱盐水工段、导热油工段、甲醇转化工段、变压吸附工段五个主体及装置配电室、控制室、分析检测。
装置的工艺流程如下:编号:Linkye页码 :3/32由于本装置原料及产品均属易燃、易爆危险品,操作过程中必须予以高度重视。
同时本装置操作的稳定性、原料消耗指标、催化剂使用寿命、产品纯度的高低、设备、人员安全等在很大程度上取决于操作水平的高低,因此有关操作、管理和维修人员在装置启动运行之前,必须熟知本操作规程,并经考核合格后才能上岗。
在后面的章节,将分工段介绍。
编号:Linkye页码 :4/32第二章导热油炉房的操作规程一、该部份设备的操作需在物料、气源满足的前提下方可调节,因此该部份在燃烧系统作了联锁之后进行调节;自力式调节阀的调节参数如下:PV501 甲醇阀后压力: 0.4MPaPV502 天然气阀后压力: 0.12MPaPV503 液化气阀后压力: 0.05MPaV559 雾化空气阀后压力: 0.1MPa远传压力开关的调节参数如下:PLS501 新风空气压力低报设定值:3.0KPa,正常值6.0KPaPLS502 PSA解析气压力低报设定值:10.0KPa,正常值30.0KPaPHS502 PSA解析气压力高报设定值:40.0KPa,正常值40.0KPaPLS503 天然气压力低报设定值:50.0KPa,正常值100.0KPaPHS503 天然气压力低报设定值:150.0KPa,正常值100.0KPaPLS504 液化气压力低报设定值:5.0KPa,正常值20.0KPaPLS505 雾化空气压力低报设定值:70.0KPa,正常值370.0KPaPHS505 雾化空气压力高报设定值:520.0KPa,正常值370.0KPa二、操作前先熟悉上位机信号联锁在微机上进行系统内各单体设备的运行控制信号联锁;该燃烧系统共有三组运行控制信号联锁,联锁单体设备如下:压力信号联锁一:PIAS504新风空气压力正常值2~5 KPa,报警值L:2.0KPa、LL:1.5.0KPa,联锁关闭SNV501a/b、SNV502a/b、SNV503a/b。
甲醇裂解工艺风险分析以及防范措施

甲醇裂解危险与可操作风险安全分析
1、甲醇制氢裂解装置
确定单元:
混合气
进导热出导热油
以甲醇制氢转化炉的进甲醇气管道为分析单元
综合性分析,在甲醇裂解制氢过程中,应采取以下措施进行防范:
1、定期对制氢装置进行检维修,彻查每一个关键点;
2、定期对原料甲醇的品质进行跟踪化验分析,保证原材料的质量;
3、精心操作,严格生产工艺的执行和检查;
4、增加甲醇、氢气职业危害告知牌;
5、在岗位增加紧急救护设施器材;
6、每天对岗位人员进行劳动防护用品佩戴检查记录;
7、每班人员至少2小时对甲醇、氢气设备周围气体浓度进行检测。
甲醇裂解制氢含甲醇蒸汽转化和变压吸附制氢两部分
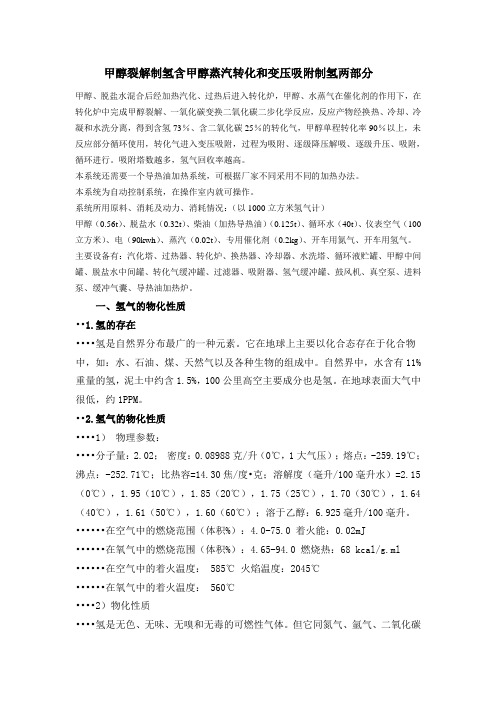
甲醇裂解制氢含甲醇蒸汽转化和变压吸附制氢两部分甲醇、脱盐水混合后经加热汽化、过热后进入转化炉,甲醇、水蒸气在催化剂的作用下,在转化炉中完成甲醇裂解、一氧化碳变换二氧化碳二步化学反应,反应产物经换热、冷却、冷凝和水洗分离,得到含氢73%、含二氧化碳25%的转化气,甲醇单程转化率90%以上,未反应部分循环使用,转化气进入变压吸附,过程为吸附、逐级降压解吸、逐级升压、吸附,循环进行。
吸附塔数越多,氢气回收率越高。
本系统还需要一个导热油加热系统,可根据厂家不同采用不同的加热办法。
本系统为自动控制系统,在操作室内就可操作。
系统所用原料、消耗及动力、消耗情况:(以1000立方米氢气计)甲醇(0.56t)、脱盐水(0.32t)、柴油(加热导热油)(0.125t)、循环水(40t)、仪表空气(100立方米)、电(90kwh)、蒸汽(0.02t)、专用催化剂(0.2kg)、开车用氮气、开车用氢气。
主要设备有:汽化塔、过热器、转化炉、换热器、冷却器、水洗塔、循环液贮罐、甲醇中间罐、脱盐水中间罐、转化气缓冲罐、过滤器、吸附器、氢气缓冲罐、鼓风机、真空泵、进料泵、缓冲气囊、导热油加热炉。
一、氢气的物化性质••1.氢的存在••••氢是自然界分布最广的一种元素。
它在地球上主要以化合态存在于化合物中,如:水、石油、煤、天然气以及各种生物的组成中。
自然界中,水含有11%重量的氢,泥土中约含1.5%,100公里高空主要成分也是氢。
在地球表面大气中很低,约1PPM。
••2.氢气的物化性质••••1)物理参数:••••分子量:2.02;密度:0.08988克/升(0℃,1大气压);熔点:-259.19℃;沸点:-252.71℃;比热容=14.30焦/度•克;溶解度(毫升/100毫升水)=2.15(0℃),1.95(10℃),1.85(20℃),1.75(25℃),1.70(30℃),1.64(40℃),1.61(50℃),1.60(60℃);溶于乙醇:6.925毫升/100毫升。
- 1、下载文档前请自行甄别文档内容的完整性,平台不提供额外的编辑、内容补充、找答案等附加服务。
- 2、"仅部分预览"的文档,不可在线预览部分如存在完整性等问题,可反馈申请退款(可完整预览的文档不适用该条件!)。
- 3、如文档侵犯您的权益,请联系客服反馈,我们会尽快为您处理(人工客服工作时间:9:00-18:30)。
产品氢气
解吸气
导热油工段
第 一部 分
导 热 油
导热油又称传热油,又称热煤油,是有机类传热介质的统 称;是一种热量的传递介质,由于其具有加热均匀,调温控制 温准确,能在低蒸汽压下产生高温,传热效果好,节能,输送 和操作方便等特点。 大部分导热油都具有中等或低等的毒性,只要采取正常的 防护措施,不会对操作人员产生什么危险。导热油通常是在密 闭的系统中使用,一般很少泄露,污染空气、水或土壤。
1.残炭
残炭是多环芳香烃、胶质、沥青质的混合物,在空气不足的条件下 受强热作用易于分解、脱氢缩合而成残炭。残炭的大小可大致判定 导热油在高温使用中的结焦倾向。结焦的传热系数与金属相差很大, 能耗增加,所以残炭是影响导热油的主要因素。导热油裂解产物聚 合(或缩合)后形成的胶质或沥青质,继续受热后形成的炭状物质。残 炭高要引起结焦,影响传热效果,严重时要堵塞设备及管。
3.低挥发性热传导液采用初馏点表示其挥发性。在开式加热系统使用的 热传导液,如初馏点低于使用温度,易使泵产生气蚀,操作系统产生 气阻,同时造成蒸发损耗过大。 4.较好的安全性热传导液采用闪点和自燃点表示其安全性。闪点用以表 示密闭循环系统中热载体的安全性能,而自燃点则可预示热传导液在 高温条件下泄漏时,在空气中的自燃倾向。 5.导液不但具有较高的热稳定性,而且具有优良的传热性能。适宜的粘 度可提供较高的循环效率;较高的比热和导热系数可有效地传递或吸收 热量,提高燃料的经济性和运行效率.
4.水分
水分关系到装置平稳运行的重要指标,载热体中如果水份超标容易在升温过程 中出现沸油现象,也容易加快油品的水解与氧化反应。导致导热油油分解失效。 一般工业装置使用产品不得大于0.05%,民用电热取暖器因无法排除水分,为 保证安全,指标定为不大于0.02%
5.闪点
闪点是导热油加热时,挥发出来的油汽与周围的空气混合,接触明火而发生闪 火的最低温度反映了导热油的蒸发倾向。在导热油中,低沸点的作用于分易蒸 发,闪点高,较安全。但不能理解为闪点越高越适用于高温。不同品牌的导热 油其闪点是不同的,最低只有140℃,最高达200℃。导热油在密闭体系的加热 油炉中使用,使燃烧的三要素不具备(燃烧= 燃料+温度+氧气),所以导热油 不会燃烧。假如系统中有泄漏现象,也是先冒烟,遇到明火情况下,才会发生 闪火现象,及时处理也不会燃烧。由此可见导热油的闪点对导热油报废指标来 说是非重要因素,只要掌握好,导热油是不会燃烧的,也不影响其热油炉的安 全性。 初馏点是指矿油型导热油中,最低沸点的馏分馏出的最低温度。初馏点高,低 沸点的组分含量低,使用时蒸汽压也必然较低,蒸发损失也少,又能保证在最 高使用温度下为液相状态。馏程导热油的馏程关系到导热油的使用温度。它是 指油组成最低沸点与最高沸点之间的范围。其范围越大,沸程就越宽,应考虑 油中最低沸点物。应有的合适的量,以确保用油过程中不致损耗过多,同时不 致因油的粘度过高而影响效果并形成积炭。导热油在规定的使用温度范围内, 馏程较窄为好
2.结垢危害
导热油发生结垢后,大大增加了导热油管壁和导热油之间的传热热阻,降低了传热效率和 传热出力;同时导热油管有效流通截面变小,加大了泵送设备的负荷,浪费了能源,运行成 本增加。 1)管壁上的结焦是一种隔热物质,结焦之后造成导热油升温慢,影响工作效率。实验表明管内 壁每增加一毫米厚碳污则多消耗燃料20~30%。 (2)因管壁内碳污厚薄不等,造成工作面温度不均匀,影响产品质量。 (3)碳污和积碳形成之后酸值上升,形成微电池腐蚀,加速设备的老化和破损。 (4)由于长期不清洗使积碳和碳污大量沉积在管道折弯处,形成局部过热蓄气,造成管裂或喷 油,酿成火灾,锅炉报废。因此,防止导热油加热系统结焦结垢,以及结焦后的及时清洗, 是导热油系统安全可靠运行和节约能源的极其重要的措施。
酸值是导热油中有机酸和无机酸的总量,即每克导热油消耗氢氧化钾的总量。 有机酸又分低分子有机酸和高分子有机酸,低分子有机酸和无机酸对金属有腐 蚀性。特别在水分子存在下,腐蚀会增大。导热油中大部分是高分子有机酸, 高分子有机酸对设备腐蚀很小。导热油在高温运行中有诱导、吸附、硬化和脱 落等步骤的结焦过程。这些过程使热油炉管道中形成一层导热油焦,并影响其 热油炉的传热效果,也同时隔离了导热油与金属管壁的接触,使这些酸不能腐 蚀设备,由此可见酸值对金属的腐蚀性是不显重要。由酸值可判断油品的变质 程度。高温热载体在大于60℃以上时遇空气或水易氧化生成有机酸,其值大小 可以判断出热载体被高温氧化的难易及严重程度。
第二部分 导 热 油 分 类
导热油按化学成 分及其来源分为: 1.矿物油型
2.合 成 型
1.液相
导热油按物理性 质和使用条件:
2.气/液两相
1.矿物油型导热油
矿物油型:将石油蒸馏,截取某段馏分经一系列的精制后调配功能添加剂制 得。矿物油型导热油按其基础油的主要组分的分子结构分为:烷烃基、环烷烃基、 芳烃基。 国内绝大部分导热油都属于矿物油型这类产品组成极其复杂,是由无穷个单 质化合物组成,其结构不均一,每种单质化合物有一个沸点,混合物就呈现出沸 点的分散范围,形成连续曲线,这个曲线就称“馏分”,也叫“馏程”。这类导 热油仅能在液态下传热,其热稳定性由热稳定性最低的组分决定。不可以使用在 300℃以上的加热系统和0℃以下的冷却系统。由技术和经济两个方面原因决定, 使用后的矿物油不能通过回收处理的方法重复使用。 由于芳烃基导热油易挥发物多,需要用氮气封闭,使用条件比较苛刻;同时 因其具有毒性,损害人的血液系统,对环境的危害较大,因此逐渐被淘汰。
2.合成型导热油
合成型:是通过人工合成方法获得的。以化工或石油化工产品为原料,经过 有机化学反应合成工艺制得的单一物质或组分简单的较纯净的物质。这类物质的 化学结构有合成芳烃、醇、醚、酯、硅油、氯代烃等 。
这类产品使用温度范围在-40~400℃,热稳定性好,使用寿命长,可再生,即 可以在液态下使用,也可以在气态下使用,但价格昂贵。目前占据世界市场的主 要为合成芳烃系列产品,其代表是联苯——联苯醚混合物(俗称“道生油”)氢 化三联苯氯代烃导热油。
4.导热油系统清洗时机
导热油加热系统的清洗一般选在以下时机进行:
3.导热油加热系统的清洗
物理清洗
导热油加热系 统的清洗方法:
化学清洗
物理清洗
物理清洗即采用机械人工的方法对加热系统结垢进行清洗。当前应用较多的是机械清焦 法、空气蒸汽清焦法和高压水射流清洗技术。 1)机械清焦法:该方法采用适当直径的塑料球 (或清沽头)依次在压缩空气的推动下,在炉管 内高速旋转推进,将附在管壁上的结焦污垢刮下来。这种技术在炉管的盘管部分及直角弯头 部分效果会受影响。另外,高速旋转的清沾头容易损伤炉管或在炉管中卡塞。另外我们经常 也用刷子清理污垢。 2)空气蒸汽清洗法:该方法是依据结焦及污垢和钢的热胀冷缩系数不同,将炉管升温,然后 吹入空气或者蒸汽使炉管上的结垢剥离下来。该技术需要熟练的工程技术人员来操作,控制 好每段炉管的温升。 3)高压水射流清洗法:该技术主要是用高压水泵产生10MPa压力的水,通过小孔喷射枪产生 高速水射流,形成强大动能,冲击在污垢上使其剥离脱落。高压水射流的速度可以达到常温 下空气中的音速以上,致密的石墨化积碳也可被击破。该技术应用时在炉管弯头处水压有较 明显下降。
第三部分 主 要 性 能
1. 热稳定性是热传导液最重要的使用性能。热稳定性不同,使用中热裂解 和聚合的程度也不同。热裂解产生小分子低沸物,易使系统产生气阻, 使泵产生气蚀,同时还造成油品较高的蒸发损耗和环境污染;热聚合则 产生大分子高沸物,其逐渐沉积于加热器和管路表面,形成的积炭将影 响系统的传热效能及控温精度。 2. 氧化安定性是热传导液另一项重要的使用性能。敞开系统或膨胀槽不 采用氮气封闭的系统,油品与空气接触的界面会发生氧化反应。一般来 说,在高于60℃的条件下,油品与空气接触即发生氧化,氧化产物逐渐形 成胶质和沉渣,附着于加热器和管路表面而产生积炭。同时,氧化反应 产生的酸性物质还会腐蚀设备,造成泄漏。
6. 初馏 点和 馏程
第 五 部 分 导热油系统的结垢和清洗
1.结垢形成
导热油在传热过程中主要发生三种化学反应:热氧化反应、热裂解和热聚合反应。结焦产 生于热氧化反应和热聚合反应。热聚合反应因导热油在加热系统运行过程受热而发生,该反应 会生成稠环芳烃、胶质和沥青质等大分子高沸物,其逐渐沉积于加热器和管路表面,形成结焦。 热氧化反应主要因开式加热系统膨胀槽内的导热油接触空气或参与循环而发生,该反应会生成 低分子或高分子的醇、醛、酮、酸等酸性组分,并进一步生成胶质、沥青质等粘稠物质,最后 形成结焦;热氧化是非正常情况引起的,一旦发生,会加速热裂解和热聚合反应,使粘度迅速 增大,传热效率降低,造成过热和炉管结焦。产生的酸性物质还会造成设备腐蚀和泄漏。
第四部分 导热油品质要求
定期化验导热油指标定期测定和分析热载体的残碳、酸值、 粘度、闪点、馏程等理化指标,及时掌握其品质变化情况,分 析变化原因。当酸值超过0.5mgKOH/g,粘度变化达到15%,闪 点变化达到20%,残碳(质量分数)达到1.5%时,证明导热油 性能已发生了变化。定期适当补充新的热载体,使系统中的残 碳量基本保持稳定。
甲醇裂解制氢站导热油工段
部 门:公用工程部 讲解人:王 小 波 时 间:2013-9-11
制 氢装置组成
生产装置由导热油加热工段
、甲醇裂解工段和变压吸附提氢(PSA)
工段三大工段组成。整套装置生产能力600Nm³ /h
工 艺 流 程 图
导热油换热器
高压蒸汽 精甲醇 脱盐水
汽化过热 转化反应 变压吸附 (PSA-H2)循环液 冷却、吸收
2.酸值
3.粘度
粘度是导热油在规定条件下的稀稠程度及流动性。导热油的粘度指标直接关系 到传热效果,导热油的黏度越小,流动的越快。其传热效率越高。粘度大,内 摩擦力就大,热油泵的输送能力也就差。当机械负荷,转速相同时。所用导热 油的粘度较大,则功率损耗越大。由于国内大部分油用在高温传热阶段,几乎 所有品牌的导热油在高温时粘度相近。一般厂家对导热油粘度变化±15%,认 为该项指标报废。如载热体发生氧化缩聚反应时粘度会显著增大。粘度小泵送 性能好。因过热发生裂解后产生可溶性聚合物,粘度会急剧增大;粘度增大时, 导热油流动点也随着增大,导热油冷却时,热油炉管内会出现沥青粘糊状或固 态现象而使炉管堵塞,热油泵无法转动,热油炉无法升温。此时清洗热油炉需 化大量人力、物力去疏通热油炉管,有时还会使热油炉报废。如发生轻质挥发 物多时,粘度会降低,但蒸汽压变大,挥发性大,使高温状态运行的导热油泵 产生气阻,造成输送困难。