材料性能与测试课件-第六章材料的磨损性能
合集下载
材料性能学.ppt

F=μp
• 摩擦的害处:磨损、消耗能量、降低机器性能。 • 摩擦的益处:行走、车辆制动等。
2020/2/1
4
2、磨损
• 摩擦运动的结果是产生磨屑,即产生磨损。
• 磨屑的形成也是材料发生变形和断裂的过程。
• 材料的磨损过程除造成材料损失外,还将发生 一系列物理、化学状态的变化,如形变硬化( 高锰钢履带)和摩擦热引起的相变(淬火钢中 的残余奥氏体转变为马氏体)等。这些变化将 影响材料的摩擦磨损性能。
• 切向摩擦力与压应力共同作用在接触区域上,使 应力分布相应改变,最大切应力的位置将向表面 移动。当摩擦系数>0.2时,最大切应力的位置将 移到材料接触表面,因此接触疲劳裂纹的产生地 也将移到零件表面。
2020/2/1
27
3、接触疲劳过程
接触疲劳
• 当最大切应力大于材料剪切疲劳强度时,在长期 循环作用,裂纹便在该处形成。根据最大切应力 位置的深浅,接触疲劳分3类:
渗碳淬火试样试验表明:
• 切应力/抗剪切强度的比值大于0.55时,在过 渡区产生疲劳裂纹,出现大块剥落。
• 比值在0.5~0.55时,出现表层剥落和麻点剥落 的混合情况。
• 比值小于0.5时,则出现麻点剥落。
影响材料接触疲劳的因素: •除了加载条件外, •主要是材料因素, 如材料成分和组织状态,表面硬度与心部硬度或摩擦 副硬度匹配、硬化层深度、表面状态
2020/2/1
5
3、磨损的3个阶段:
• 跑合阶段:表面逐步磨平, 实际接触面积不断增大磨损 速率不断减小。
• 稳定磨损阶段:磨损量呈线 性,磨损速率为一定值。工 件服役阶段,跑合越好,磨 损速率越低。
• 剧烈磨损阶段:摩擦接触面 间隙增大,机件的振动加剧 ,润滑膜或保护层被损坏, 机件表面被恶化,磨损速率 迅速加大。
• 摩擦的害处:磨损、消耗能量、降低机器性能。 • 摩擦的益处:行走、车辆制动等。
2020/2/1
4
2、磨损
• 摩擦运动的结果是产生磨屑,即产生磨损。
• 磨屑的形成也是材料发生变形和断裂的过程。
• 材料的磨损过程除造成材料损失外,还将发生 一系列物理、化学状态的变化,如形变硬化( 高锰钢履带)和摩擦热引起的相变(淬火钢中 的残余奥氏体转变为马氏体)等。这些变化将 影响材料的摩擦磨损性能。
• 切向摩擦力与压应力共同作用在接触区域上,使 应力分布相应改变,最大切应力的位置将向表面 移动。当摩擦系数>0.2时,最大切应力的位置将 移到材料接触表面,因此接触疲劳裂纹的产生地 也将移到零件表面。
2020/2/1
27
3、接触疲劳过程
接触疲劳
• 当最大切应力大于材料剪切疲劳强度时,在长期 循环作用,裂纹便在该处形成。根据最大切应力 位置的深浅,接触疲劳分3类:
渗碳淬火试样试验表明:
• 切应力/抗剪切强度的比值大于0.55时,在过 渡区产生疲劳裂纹,出现大块剥落。
• 比值在0.5~0.55时,出现表层剥落和麻点剥落 的混合情况。
• 比值小于0.5时,则出现麻点剥落。
影响材料接触疲劳的因素: •除了加载条件外, •主要是材料因素, 如材料成分和组织状态,表面硬度与心部硬度或摩擦 副硬度匹配、硬化层深度、表面状态
2020/2/1
5
3、磨损的3个阶段:
• 跑合阶段:表面逐步磨平, 实际接触面积不断增大磨损 速率不断减小。
• 稳定磨损阶段:磨损量呈线 性,磨损速率为一定值。工 件服役阶段,跑合越好,磨 损速率越低。
• 剧烈磨损阶段:摩擦接触面 间隙增大,机件的振动加剧 ,润滑膜或保护层被损坏, 机件表面被恶化,磨损速率 迅速加大。
材料摩擦磨损课件

摩擦表面的生成与演化
磨合阶段
在摩擦初期,接触表面的粗糙度会导致微凸体的相互挤压和剪切,从而产生磨屑和热量。 这个阶段结束后,表面会逐渐变得光滑。
稳定磨损阶段
经过磨合阶段后,表面逐渐形成了一层光滑的氧化膜,这层氧化膜具有较好的耐磨损性能 ,能够减小摩擦力和磨损量。这个阶段是磨损的主要阶段,也是材料使用寿命的主要影响 因素。
落。
疲劳磨损的主要机制包括疲劳裂纹的形成和扩展、微粒的断裂和剥落, 这些机制会导致材料表面出现疲劳斑和剥落坑。
腐蚀磨损
腐蚀磨损是指由于化学腐蚀作用,导致 材料表面损伤的现象。
腐蚀磨损通常发生在潮湿的环境中,如 海洋环境、化工环境等。由于化学腐蚀 的作用,材料表面逐渐被腐蚀,最终导
致表面损伤和破坏。
腐蚀磨损的主要机制包括氧化、腐蚀和 电化学腐蚀,这些机制会导致材料表面
出现腐蚀斑和剥落。
冲蚀磨损
冲蚀磨损是指由于高速流动的液体或固体颗粒冲击材料表面,导致材料表面逐渐被磨损的现 象。
冲蚀磨损通常发生在流体动力学环境下,如喷气发动机、水轮机等。由于高速流动的液体或 固体颗粒冲击材料表面,导致材料表面逐渐被冲蚀和破坏。
化学表面合金化
通过化学反应在基材表面 形成一层具有特殊性能的 合金层,如不锈钢的钝化 膜。
热扩散表面合金化
通过加热使基材表面的原 子与加入的元素发生互扩 散,形成具有优异性能的 合金层。
表面织构技术
表面微织构技术
在基材表面加工出微小的凹坑或 凸起,改变表面形态,降低摩擦 系数和提高耐磨性。
表面纳米织构技术
THANKS
感谢观看
摩擦系数及其影响因素
材料性质
材料的硬度、弹性模量、表面粗糙度等都会影响摩擦系数的大小。一 般来说,硬度越高、表面粗糙度越小的材料,其摩擦系数越小。 Nhomakorabea表面条件
【管理资料】材料性能学-第六章概要汇编

第 单位滑动距离内出现的接触点数
六
章
N=n/d=4p/(3πσscd3)。
材
料
实际相对滑动中,软材料上被拉拽出半球的几率
的
为K,总拉拽出的磨损量W可表示为:
磨 损
W
KNV'L
K
4p
3 scd3
2
3
d 3L 2
性
K pL K pL
能
9sc
3Hv
Hv为软材料硬度,Hv≈3 σsc
V’为接触点半球体积
2020年6月30日星期二
第
4、粘着磨损的两种形式
六
章
a、 若粘着点结合强度低于两侧材料,则沿接触
材
面剪断,磨损量较小,摩擦面较平滑,只有轻微
料
擦伤(巴氏合金—钢的滑动摩擦)。
的
磨
b、 若粘着点的结合强度比两侧任一材料的强度
损 都高时,分离面发生在强度较弱的材料上,被剪
性 断的材料将转移到强度较高的材料上,结果,使
能
法向力在表面形成压痕;切向力推动磨料前进,
产生浅长滑痕(切痕)。
2020年6月30日星期二
微观切削
第
六
4.磨料磨损的机制 (2)微观犁沟
章
材
(3)微观断裂(剥落)
料
的
磨
损
性
能
2020年6月30日星期二
第
5、磨粒切削磨损模型
六
章
压力P将硬材料的凸出部分或磨粒(圆锥体)压
材
入较软材料中
料
的
p/πr2=3σsc
能
A、跑合阶段(OA段)
零件表面被逐渐磨平,实际接触面积不断增大。 材料表层产生应变硬化,磨损速率逐渐下降。
材料力学性能第6章-材料的磨损性能
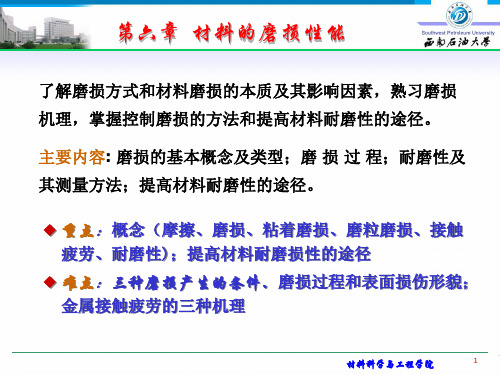
由于磨损,将造成表层材料的损耗,零件尺寸发生 变化,直接影响了零件的使用寿命。
还增加能耗,产生噪音、振动,造成环境污染。
材料科学与工程学院
2
第一节 磨损的基本概念及类型
一、摩擦与磨损的概念
1.摩 擦 两个相互接触的物体或物体与介质之间在外力作用下,发生相对 运动,或者具有相对运动的趋势时,在接触表面上所产生的阻碍 作用称为摩擦。这种阻碍相对运动的阻力称为摩擦力。
深度在0.1~0.2mm的小块剥落称点 蚀,剥块形状为不对称V型针状或 痘状凹坑。
发生在兼有滚动和滑动
浅层剥落深度一般为0.2~0.4mm, 剥块底部大致与表面平行,裂纹沿 与表面成锐角或直角扩展。
纯滚动或摩擦很小
深层剥落深度与表面强化层深相当
(>0.4mm),剥落时裂纹垂直于表面
扩展。
表面强化层深度不够
材料科学与工程学院
7
根据粘着点与两侧材料强度的差异,粘着剪断可出现以 下两种形式: ①粘着点结合强度低于两侧材料
沿接触面剪断,磨损量较小,摩擦面显得较平滑,只有轻 微擦伤。锡基合金与钢的滑动属此类型。
②粘着点结合强剪断的材料将转移 到强度较高的材料上。
W= pLtan K pLtan
3 sc
H
(6-6)
材料科学与工程学院
13
三、接触疲劳
1.现象与特征
接触疲劳概念: 两接触材料作滚动或滚动加滑动摩擦时,
交变接触压应力长期作用使材料表面疲劳损伤,局部区
域出现小片或小块状材料剥落,而使材料磨损的现象,
故又称表面疲劳磨损或麻点磨损,是齿轮、滚动轴承等
3)组织2:在基体为马氏体的组织中,减小碳化物粒度并使之 呈球状均匀分布,使基体中马氏体、残余奥氏体和未溶碳化 物量之间有最佳匹配,可最大限度地提高接触疲劳抗力。
还增加能耗,产生噪音、振动,造成环境污染。
材料科学与工程学院
2
第一节 磨损的基本概念及类型
一、摩擦与磨损的概念
1.摩 擦 两个相互接触的物体或物体与介质之间在外力作用下,发生相对 运动,或者具有相对运动的趋势时,在接触表面上所产生的阻碍 作用称为摩擦。这种阻碍相对运动的阻力称为摩擦力。
深度在0.1~0.2mm的小块剥落称点 蚀,剥块形状为不对称V型针状或 痘状凹坑。
发生在兼有滚动和滑动
浅层剥落深度一般为0.2~0.4mm, 剥块底部大致与表面平行,裂纹沿 与表面成锐角或直角扩展。
纯滚动或摩擦很小
深层剥落深度与表面强化层深相当
(>0.4mm),剥落时裂纹垂直于表面
扩展。
表面强化层深度不够
材料科学与工程学院
7
根据粘着点与两侧材料强度的差异,粘着剪断可出现以 下两种形式: ①粘着点结合强度低于两侧材料
沿接触面剪断,磨损量较小,摩擦面显得较平滑,只有轻 微擦伤。锡基合金与钢的滑动属此类型。
②粘着点结合强剪断的材料将转移 到强度较高的材料上。
W= pLtan K pLtan
3 sc
H
(6-6)
材料科学与工程学院
13
三、接触疲劳
1.现象与特征
接触疲劳概念: 两接触材料作滚动或滚动加滑动摩擦时,
交变接触压应力长期作用使材料表面疲劳损伤,局部区
域出现小片或小块状材料剥落,而使材料磨损的现象,
故又称表面疲劳磨损或麻点磨损,是齿轮、滚动轴承等
3)组织2:在基体为马氏体的组织中,减小碳化物粒度并使之 呈球状均匀分布,使基体中马氏体、残余奥氏体和未溶碳化 物量之间有最佳匹配,可最大限度地提高接触疲劳抗力。
第六章 材料的磨损性能
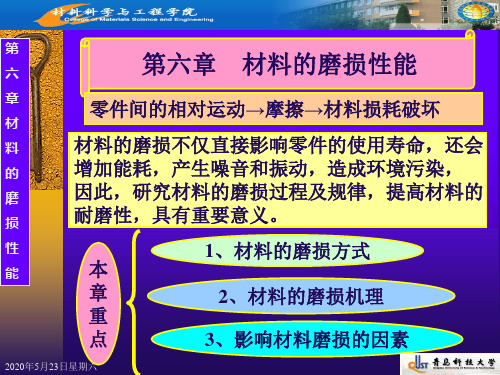
2012年5月3日星期四
第 六 章 材 料 的 磨 损 性 能
5、阿查得(J.F.Archard)估算粘着磨损量的方法: 、阿查得( )估算粘着磨损量的方法: 设在法向力P 作用下,摩擦面上有n 个微凸体接触粘着。 设在法向力 作用下,摩擦面上有 个微凸体接触粘着。 接触面的真实面积为πd , 接触面的真实面积为 2/4,则n个相同的接触点同 个相同的接触点同 时塑性接触时,法向力 法向力p 时塑性接触时 法向力
2012年5月3日星期四
第 六 章 材
B、稳定磨损阶段(AB段) 、稳定磨损阶段( 段 该段为一直线,斜率即磨损速率(常数), ),零件 该段为一直线,斜率即磨损速率(常数),零件 正常工作阶段, 的寿命取决于该阶段。 正常工作阶段,零件 的寿命取决于该阶段。 C、剧烈磨损阶段(BC段) 、剧烈磨损阶段( 段
2012年5月3日星期四
第 六 章 材 料 的 磨 损 性
零件正常运行的磨损过程一般分三个阶段: 零件正常运行的磨损过程一般分三个阶段:
A、跑合阶段(OA段) 、跑合阶段( 段
能
零件表面被逐渐磨平,实际接触面积不断增大。 零件表面被逐渐磨平,实际接触面积不断增大。 材料表层产生应变硬化,磨损速率逐渐下降。 材料表层产生应变硬化,磨损速率逐渐下降。
2012年5月3日星期四
第 六 章 材 料 的 磨 损 性 能
2012年5月3日星期四
第 六 章 材 料 的 磨 损
2、产生条件 、 摩擦副相对滑动速度小,接触面氧化膜脆弱, 摩擦副相对滑动速度小,接触面氧化膜脆弱,润 滑条件差, 滑条件差,以及接触应力大以及机械性能相差不 大的摩擦副的滑动摩擦条件下。 大的摩擦副的滑动摩擦条件下。 3、磨损特征 、 摩擦副表面产生大小不等的结疤。 摩擦副表面产生大小不等的结疤。
材料力学性能教学课件材料的摩擦与磨损性能
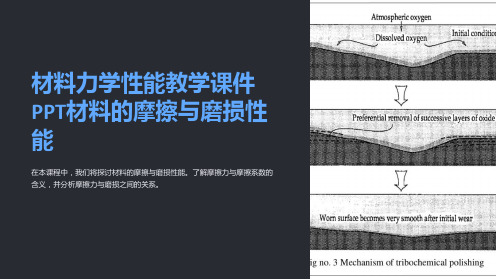
通过选用合适的材料、表面处理、润滑和改善工艺等措施来改善材料的摩擦 与磨损性能,并延长材料的使用寿命。
结论及展望
通过对材料的摩擦与磨损性能的深入研究,可以为材料的选择和应用提供科学依据,进一步提高材料的性能和可靠 性。
金属材料
金属材料通常具有较高的摩擦系数,但也可以通过表面处理和润滑来减少磨损。
聚合物材料
聚合物材料具有较低的摩擦系数,但其耐磨性能相对较差。
陶瓷材料
陶瓷材料通常具有较低的摩擦系数和较高的耐磨性能,但也容易产生表面粉化。
影响摩擦与磨损的因素
1 接触压力
增加接触压力会增加摩擦力和磨损。
3 温度
高温环境下摩擦和磨损会加剧。
2 表面粗糙度
粗糙表面会增加摩擦力和磨损。
摩擦与磨损的测试方法
1
磨损实验
2
使用特定装置和试样进行磨损实验,以获得
材料的磨损特性和性能。
3
滑动摩擦测试
通过模拟实际工况下的滑动摩擦来评估材料 的摩擦和磨损性能。
表面分析
通过观察和分析材料表面的变化,了解摩擦 和磨损的影响。
改善材料的摩擦与磨损性能的 措施
材料力学性能教学课件 PPT材料的摩擦与磨损性 能
在本课程中,我们将探讨材料的摩擦与磨损性能。了解摩擦力与摩擦系数的 含义,并分析擦力与磨损之间的相互作用。探讨不同材料之间的摩擦和 磨损的特点,以及它们对材料性能和寿命的影响。
常见材料的摩擦与磨损性能比较
结论及展望
通过对材料的摩擦与磨损性能的深入研究,可以为材料的选择和应用提供科学依据,进一步提高材料的性能和可靠 性。
金属材料
金属材料通常具有较高的摩擦系数,但也可以通过表面处理和润滑来减少磨损。
聚合物材料
聚合物材料具有较低的摩擦系数,但其耐磨性能相对较差。
陶瓷材料
陶瓷材料通常具有较低的摩擦系数和较高的耐磨性能,但也容易产生表面粉化。
影响摩擦与磨损的因素
1 接触压力
增加接触压力会增加摩擦力和磨损。
3 温度
高温环境下摩擦和磨损会加剧。
2 表面粗糙度
粗糙表面会增加摩擦力和磨损。
摩擦与磨损的测试方法
1
磨损实验
2
使用特定装置和试样进行磨损实验,以获得
材料的磨损特性和性能。
3
滑动摩擦测试
通过模拟实际工况下的滑动摩擦来评估材料 的摩擦和磨损性能。
表面分析
通过观察和分析材料表面的变化,了解摩擦 和磨损的影响。
改善材料的摩擦与磨损性能的 措施
材料力学性能教学课件 PPT材料的摩擦与磨损性 能
在本课程中,我们将探讨材料的摩擦与磨损性能。了解摩擦力与摩擦系数的 含义,并分析擦力与磨损之间的相互作用。探讨不同材料之间的摩擦和 磨损的特点,以及它们对材料性能和寿命的影响。
常见材料的摩擦与磨损性能比较
6-7第六和七讲 材料的其它力学性能-摩擦、磨损与蠕变

5.2 磨粒磨损-磨料磨损
根据磨粒所受应力大小分为: (1)低应力划伤式的磨料磨损-应力不超过磨 料压溃强度,材料表面被轻微划伤。 (2)高应力辗碎式的磨料磨损-磨料压溃。 (3)凿削式磨料磨损-磨料有冲击力,从表面 凿下较大颗料磨屑,如挖掘机斗齿。
金属表面 发生局部 塑性变形
磨粒嵌入金 属表面,切 割金属表面
功耗磨损温度局部烧毁磨损机理粘着磨损磨粒磨损腐蚀磨损微动磨损疲劳局部应力局部塑变碾平51粘着磨损咬合磨损转移脱落典型粘着磨损形貌举例内燃机中活塞环和缸套衬启动或停车换向及载荷运转不稳定或润滑条件不好几何结构参数不恰当而不能建立起可靠的油膜时环和套之间易发生局部直接接触处于边界摩擦或干摩擦的工作状态易粘着磨损
7
3. 4种滑动摩擦状态
干摩擦:表面无任何润滑剂或保护膜的纯接触摩擦。 →功耗↑ 磨损↑ 温度↑→局部烧毁
不允许出现干摩擦!
4. 磨损过程
5. 磨损机理
►粘着磨损 ►磨粒磨损 ►腐蚀磨损 ►微动磨损(疲劳)
5.1 粘着磨损-咬合磨损
局部应力
局部塑变, 碾平
转移,脱落
典型粘着磨损形貌
举例-内燃机中活塞环和缸套衬
1. 材料的摩擦与磨损
世界使用能源约1/31/2消耗于摩擦。减少无 用摩擦消耗,可大量节省能源。 易损零件,由于磨损超过限度而报废和更 换,控制和减少磨损既减少设备维修次数和费 用,又节省制造零件及其所需材料费用。
摩擦是磨损的原因,磨损是摩擦的结果。
2. 摩擦的分类
内摩擦:物质内部发生的阻碍分子间相对运动现象。 外摩擦:相对运动物体表面间发生的相互阻碍作用。 静摩擦:仅有相对运动趋势时的摩擦。 动摩擦:在相对运动进行中的摩擦。 滑动摩擦:物体表面间运动形式是相对滑动,常用。 滚动摩擦:物体表面间的运动形式是相对滚动,高速、 高精度、重载。
材料的力学性能课件06_缺口试样

缺口试样的静拉伸试验 缺口试样偏斜拉伸试验 缺口试样的静弯曲试验 缺口试样冲击试验 缺口试样疲劳试验
缺口敏感性试验
在缺口试样试验 中,缺口的几何形状、 大小是一个很重要的影 响因素。缺口几何参数 通常包括缺口深度t、 缺口根部曲率半径ρ以 及缺口张角ω。
缺口敏感性试验-缺口试样的静拉伸
由于断裂韧度有多种不同的定义方式,包括Kc、Gc、Jc、δc等,加之材
料的特性不同,测试方法也有很多种。其中最重要的就是平面应变断裂
韧度KⅠc的测定,这已在工程实践当中有着重要的应用。
不同于缺口敏感性试验,该类试验重在分析缺口试样局部区域的力学行 为,因此对试样尺寸有着严格要求,一定要符合理论计算模型的要求。
断裂韧度测定试验-KⅠc的测定
测定KIC用的试样尺寸 必须保证裂纹顶端处
于平面应变及小范围 屈服状态
断裂韧度测定试验-KⅠc的测定
断裂韧度测定试验-KⅠc的测定
三点弯曲试样加载时,裂纹尖端的应力强度因子KI为:
紧凑拉伸试样加载时,裂纹尖端的应力强度因子KI为:
将当前B、W条件下裂纹失稳扩展的临界载荷FQ及试样的裂 纹长度a0代人上述KI表达式即可求出KI的条件值,记为KQ。
缺口效应
缺口对材料的力学行为影响可归结为四个方面: ①应力集中; ②双向或三向复杂应力状态; ③应变集中; ④局部应变速率增大。 这些统称为缺口效应,其中应力集中是最为重要的一种影响。
缺口效应
缺口效应
应力集中系数
反映局部应力增高程度的参数称为应力集中系数。 将应力集中区域内的峰值应力与不考虑应力集中时的基准应力的比值称为 理论应力集中系数:
疲劳裂纹扩展试验
当材料中存在裂纹并且外加应力达到某一临界值后,裂纹就会发生失 稳扩展。因此含裂纹材料的断裂可根据断裂韧度加以判别。不过在很 多情况下,这种足够大的宏观临界裂纹是在载荷作用下由萌生的小裂 纹逐渐扩展而成的,这也就是所谓的亚临界裂纹扩展过程。 疲劳载荷下的亚临界裂纹扩展尤为重要,这也是导致材料疲劳破坏的 主要原因。通过疲劳裂纹扩展试验,得到疲劳裂纹从萌生到亚临界扩 展再到最后失稳扩展的全过程,可以测定材料中疲劳裂纹扩展的门槛 值,得到疲劳裂纹扩展速率的变化规律,进而估算材料的疲劳寿命。
- 1、下载文档前请自行甄别文档内容的完整性,平台不提供额外的编辑、内容补充、找答案等附加服务。
- 2、"仅部分预览"的文档,不可在线预览部分如存在完整性等问题,可反馈申请退款(可完整预览的文档不适用该条件!)。
- 3、如文档侵犯您的权益,请联系客服反馈,我们会尽快为您处理(人工客服工作时间:9:00-18:30)。
4
风阻:550公里/小时 轨道磨损
弓网:大电流下的摩擦磨损
5
水中航行体的主要能源和动力 被用来克服行进中的阻力,其中 摩擦阻力占最大成分(水下80%); 对于诸如输油管道这类管道运输, 其能量几乎全部被用来克服流固 表面的摩擦阻力。
6
卫星飞轮 轴承润滑油 耐磨轴承材料 稳定的微量供油技术 航空发动机 叶片和摩擦阻尼器
振动故障占发动机总故障的60%以上,而叶片的故障要 占发动机振动故障的70%以上
压气机盘与涡轮盘
7
§目 录
§6.1 磨损的概念和类型 §6.2 磨损过程
§6.3 耐磨性指标及其测试 §6.4 提高耐磨性的途径 §6.5 补充:炭炭复合材料的磨损 补充:
8
§6.1 磨损的概念和类型
一、摩擦与磨损的概念
10
2、各种磨损类型可以发生转化。 、各种磨损类型可以发生转化。
图6-2 磨损类型转化
11
§6.2 磨损过程
一、粘着磨损特点和过程
1、特点: 、特点: 机件表面有大小不等的结疤, 机件表面有大小不等的结疤, 2、发生条件: 、发生条件: 多发生在摩擦副相对滑动速度小;接触面 多发生在摩擦副相对滑动速度小 接触面 氧化膜脆弱;润滑条件差 润滑条件差; 氧化膜脆弱 润滑条件差 以及接触应力大的滑动摩擦条件下。 以及接触应力大的滑动摩擦条件下。 3、磨损过程: 、磨损过程: 表面接触的少量微凸体→产生很高的应 表面接触的少量微凸体 产生很高的应 图6-3 粘着磨损形貌和示意图 力 →发生塑性变形 形成粘着点 发生塑性变形→形成粘着点 发生塑性变形 →被剪断、拉开 转移到一方材料表面 被剪断、 被剪断 拉开→转移到一方材料表面 →脱落下来 形成磨屑。 脱落下来→形成磨屑。 脱落下来 形成磨屑 就是粘着点不断形成, 就是粘着点不断形成,又不断被破坏并脱 落的过程。 落的过程。
3
Wear This is the progressive loss of substance of one body because of rubbing by another body. There are many different types of wear, including sliding wear, abrasive wear, corrosion, and surface fatigue.
1、摩擦: 、摩擦: 接触物体间的一种阻碍运动的现象。 接触物体间的一种阻碍运动的现象。 2、磨损: 、磨损: 在摩擦作用下物体相对运动时, 在摩擦作用下物体相对运动时,表面 逐渐分离出磨屑(局部变形和断裂 局部变形和断裂), 逐渐分离出磨屑 局部变形和断裂 , 从而不断损伤的现象。 从而不断损伤的现象。 3、磨损过程: 、磨损过程: 1) 跑合 磨合 阶段 磨损速率下降。 跑合(磨合 阶段: 磨损速率下降。 磨合)阶段 2) 稳定磨损阶段 磨损速率稳定。 稳定磨损阶段: 磨损速率稳定。 3) 剧烈磨损阶段 磨损速率增加。 剧烈磨损阶段: 磨损速率增加。 时间变化; 载荷大小方向随 时间变化;
17
3、接触应力概念 、
两物体相互接触时, 两物体相互接触时 在局部表面产生 的压应力。分为线接触(如圆柱与圆柱 的压应力。分为线接触 如圆柱与圆柱 接触)与点接触 如滚珠与轴承圈)两类 与点接触(如滚珠与轴承圈 两类。 接触 与点接触 如滚珠与轴承圈 两类。 (d) (c)
(a)
(b)
两圆柱体线接触表面应力分布(a); 图6-6 两圆柱体线接触表面应力分布 ; (b)沿接触深度的应力分布; 沿接触深度的应力分布; 沿接触深度的应力分布 (c) 点接触表面应力分布; 点接触表面应力分布; (d) 综合切应力沿深度分布 综合切应力沿深度分布.
分为麻点剥落 点蚀 浅层剥落、 深层剥落(表面 分为麻点剥落(点蚀 、浅层剥落、 深层剥落 表面 麻点剥落 点蚀)、 压碎)三类 三类。 压碎 三类。
a 点蚀 深度在 ~0.2mm的小块剥落,形状为不对称 点蚀: 深度在0.1~ 的小块剥落, 的小块剥落 形状为不对称V 型针状或痘状凹坑。 型针状或痘状凹坑。 b 浅层剥落 深度在 ~0.4mm的小块剥落 剥块底部大 浅层剥落: 深度在0.2~ 的小块剥落→剥块底部大 的小块剥落 致与表面平行,裂纹沿与表面成锐角或直角扩展。 致与表面平行,裂纹沿与表面成锐角或直角扩展。 c 深层剥落 深度 0.4mm的小块剥落 深度与表面强化层 深层剥落: 深度> 的小块剥落→深度与表面强化层 的小块剥落 深相当,裂纹垂直于表面扩展。 深相当,裂纹垂直于表面扩展。
15
三、接触疲劳特点和过程
1、现象和特征: 、现象和特征: 出现许多痘状、贝壳状或不规则形状的凹坑 麻坑 麻坑)。 出现许多痘状、贝壳状或不规则形状的凹坑(麻坑 。 有的凹坑较深,底部有疲劳裂纹扩展线的痕迹。 有的凹坑较深,底部有疲劳裂纹扩展线的痕迹。
图6-5 接触疲劳磨损的形貌
16
2、接触疲劳分类 、
9
图6-1 磨损量和时间曲线
二、摩擦的基本类型
1、根据摩擦面损伤和破坏的形式,大致可分四类: 、根据摩擦面损伤和破坏的形式,大致可分四类: a 粘着磨损 粘着磨损(Adhesive Wear):材料表面某些接触点局部压应力超 : 过该处材料屈服强度发生粘合并拉开而产生的磨损; 过该处材料屈服强度发生粘合并拉开而产生的磨损; b 磨粒磨损 磨粒磨损(Abrasive Wear):摩擦副的一方表面存在坚硬的细微 : 凸起或在接触间存在硬质粒子时产生的磨损;如锉削、磨金相、 凸起或在接触间存在硬质粒子时产生的磨损;如锉削、磨金相、 抛光等 c 腐蚀磨损 包括氧化、微动、浸蚀磨损 腐蚀磨损(包括氧化 微动、浸蚀磨损)(Corrsion Wear):在腐 包括氧化、 : 蚀应用环境中摩擦表面与周围介质发生反应, 蚀应用环境中摩擦表面与周围介质发生反应,在表面形成腐蚀 产物粘附不牢,摩擦中被剥落下来, 产物粘附不牢,摩擦中被剥落下来,新的表面又进一步发生反 产生磨损。 应,产生磨损。 d 接触疲劳磨损 接触疲劳磨损(Rolling Contact Wear):两接触材料作滚动或者 : 滚动滑动摩擦时, 滚动滑动摩擦时,交变接触压应力长期作用使得材料表面疲劳 磨损,局部区域出现小片或者小块状材料剥落,而产生的磨损; 磨损,局部区域出现小片或者小块状材料剥落,而产生的磨损; 是齿轮、滚动轴承常见失效方式。 是齿轮、滚动轴承常见失效方式。
图6-8 剥层磨损裂纹形成示意图
20
3)深层剥落 3)深层剥落 裂纹源多位于硬化层与心部 的交界处(过渡区) 的交界处(过渡区) → 优先萌 生→ 造成沿硬化层的大块材料 剥落。 剥落。
综上所述, 综上所述,接触疲劳裂纹 的形成与扩展是接触综合切应 力高于材料接触疲劳强度的结 果。
图6-9 深层剥落裂纹示意图
2
Friction This phenomenon is encountered whenever there is relative motion between contacting surfaces, and it always opposes the motion. As no mechanically prepared surfaces are perfectly smooth, when the surfaces are first brought into contact under light load, they touch only along the asperities (real area of contact). The early theories attributed friction to the interlocking of asperities; however, it is now understood that the phenomenon is far more complicated.
21
四、腐蚀磨损特点和过程
1)氧化磨损: 1)氧化磨损: 氧化磨损 滑动时, 滑动时,空气或润滑剂中的氧扩散到变形层内形成氧化 遇到突起剥落,新漏出的表面又被氧化, 膜,遇到突起剥落,新漏出的表面又被氧化,磨掉 → 氧化 磨损; 磨损; 特征:磨损产物为氧化物,如红褐色的Fe2O3 Fe2O3, 特征:磨损产物为氧化物,如红褐色的Fe2O3,灰褐色的 Fe3O4;磨损速率取决于氧化膜的脆性程度、膜基结合力。 Fe3O4;磨损速率取决于氧化膜的脆性程度、膜基结合力。 氧化磨损时一种广泛的磨损形态, 氧化磨损时一种广泛的磨损形态,材料在干燥大气中的 氧化磨损值在0.1 0.5μm/h;若空气中含有少量的水汽, 0.1氧化磨损值在0.1-0.5μm/h;若空气中含有少量的水汽, 化学反应产物是氢氧化物,加快腐蚀; 化学反应产物是氢氧化物,加快腐蚀;空气中有二氧化硫 或二氧化碳,腐蚀更快。 或二氧化碳,腐蚀更快。
1
§引 言
摩擦: 摩擦:相互接触的两个物体有相对运动或相对运 动的趋势时,在接触界面上出现阻碍相对运动的现象。 动的趋势时,在接触界面上出现阻碍相对运动的现象。 摩擦力的方向与引起相对运动的切方向相反。 摩擦力的方向与引起相对运动的切方向相反。摩擦力 与施加在摩擦面上的垂直载荷之比称为摩擦系数: 与施加在摩擦面上的垂直载荷之比称为摩擦系数:μ =F/N 磨损:物体表面相互摩擦时, 磨损:物体表面相互摩擦时,材料自表面逐渐小 时的过程称为磨损。 时的过程称为磨损。 摩擦是磨损的原因,磨损是摩擦的结果。 摩擦是磨损的原因,磨损是摩擦的结果。机器运 转时相对运动产生的摩擦而磨损, 转时相对运动产生的摩擦而磨损,不仅直接影响零件 的使用寿命,还增加能耗,产生噪声和振动。 的使用寿命,还增加能耗,产生噪声和振动。磨损是 降低机器和工具效率、精确度甚至使其报废重要原因; 降低机器和工具效率、精确度甚至使其报废重要原因; 磨损失效; 机件间摩擦磨损引起失效叫磨损失效 机件间摩擦磨损引起失效叫磨损失效; 磨损方式、磨损机理、磨损本质、影响因素; 磨损方式、磨损机理、磨损本质、影响因素;提 高耐磨性途径; 高耐磨性途径;