铁基粉末冶金零件热处理
粉末冶金铁基零件的烧结_硬化处理_韩凤麟

粉末冶金热处理

粉末冶金热处理一、前言粉末冶金热处理是一种重要的金属材料加工方法,它能够通过高温处理改善材料的性能,提高其机械性能、耐腐蚀性和耐磨损性等。
本文将从粉末冶金的基础知识开始,详细介绍粉末冶金热处理的原理、方法和应用。
二、粉末冶金基础知识1. 粉末冶金定义粉末冶金是一种制造零件的技术,它通过将金属或非金属材料制成微小颗粒,再利用压缩、烧结等工艺将这些颗粒化为块体或形成复合材料。
2. 粉末制备方法常用的粉末制备方法有机械法、化学法和物理法等。
其中机械法是最常用的方法之一,包括球磨法、振荡球磨法和高能球磨法等。
3. 粉末冶金加工工艺主要包括压制、烧结和后处理等过程。
其中压制是将粉末填充到模具中进行压缩成形;烧结则是将压制好的坯体进行高温处理,使其颗粒结合成为固体材料;后处理则是对烧结好的材料进行加工和表面处理。
三、粉末冶金热处理原理1. 热处理定义热处理是指通过加热和冷却等方式改变材料的组织结构和性能,以达到提高其机械性能、耐腐蚀性和耐磨损性等目的的过程。
2. 粉末冶金热处理原理粉末冶金材料在制备过程中由于颗粒之间存在空隙,因此其密度较低。
而经过高温热处理后,这些空隙会被填充,颗粒之间的结合力也会增强,从而提高了材料的密度和强度。
此外,热处理还可以改善材料的晶体结构和组织状态,增强其机械性能、耐腐蚀性和耐磨损性等。
四、粉末冶金热处理方法1. 真空烧结法真空烧结法是一种在真空环境下进行高温加工的方法。
由于真空环境下不存在氧化反应,因此可以避免材料表面被氧化和污染。
此外,真空烧结法还可以控制材料的晶体结构和组织状态,从而提高其机械性能和耐腐蚀性能。
2. 气氛烧结法气氛烧结法是一种在特定气氛下进行高温加工的方法。
常用的气氛有惰性气体、还原性气体和氧化性气体等。
这种方法可以控制材料的晶体结构和组织状态,从而改善其性能。
3. 热等静压法热等静压法是一种将粉末填充到模具中后,在高温高压下进行加工的方法。
这种方法可以使材料颗粒之间更加紧密地结合,从而提高其密度和强度。
粉末冶金铁基零件的烧结-硬化处理

粉末冶金铁基零件的烧结-硬化处理作者:刘宁凯来源:《城市建设理论研究》2014年第22期摘要:铁基粉末冶金零件用烧结-硬化处理,能得到和常规的热处理相同的显微组织与力学性能,从而可取消传统的将零件用间歇式加热炉重新加热奥氏体化-油淬火等作业,不但节能,而且可减低生产费用。
关键词:粉末冶金铁基零件;烧结硬化;淬透性中图分类号:TF文献标识码: A一、粉末冶金铁基零件的烧结以及热处理工艺(一)烧结工艺烧结实际是将压述在低于主要组分恪点的温度下进行的热处理。
目的是使粉末颗粒问从机械喃合转变为原子之间的晶界结合。
压还内部是粉末颗粒表面问机械压力下接触,而原子与原子之间结合的材料,需要通过烧结,使压还达到冶金结合的材料,使粉末冶金材料达到所需要的力学性能和物化性能。
图1烧结过程示意图如图1所示,图1(a)是烧结前压述中粉末的接触状态,这种结合只是机械结合,粉末颗粒的界面仍然可区分可分离开。
图1 (b)中粉末颗粒接触点的结合状态发生了改变,颗粒界面为晶界面所取代。
随着烧结的进行,结合面增加,直至颗粒界面完全转变为晶界面,最后成为图1(C)所示的状态,颗粒之间的孔隙由不规则的形状转变为球形的孔隙。
粉末烧结是系统自由能降低的过程,换句话说,压还的内能高于烧结体的内能,其主要体现在:(1)粉末颗粒的表面能。
粉末压还具有很大的表面自由能,这种表面能随粉末颗粒的细化而增加。
压还烧结后,颗粒表面消失,将会释放出较大的表面能,这也成为烧结的驱动能。
(2)粉末颗粒内部的畸变能。
在混合和压制过程中粉末颗粒会发生变形而产生畸变,蕴藏着丰富的能量,这些能量液是烧结的驱动能。
由此可见,压还从热力学上来说是处于非常不稳定的状态。
当内能高到一定的程度会发生自动烧结,但在一般情况下,体系的内能不足以驱动烧结进行,所以需要加热到某一温度才能进行烧结。
(二)热处理与其他金属材料一样,我们同样可以通过热处理的方法改善粉末冶金材料力学性能。
应用在粉末冶金材料中的热处理方法有:退火、正火、萍火、回火以及渗碳、渗氮等。
铁基粉末冶金蒸汽处理硬度要求
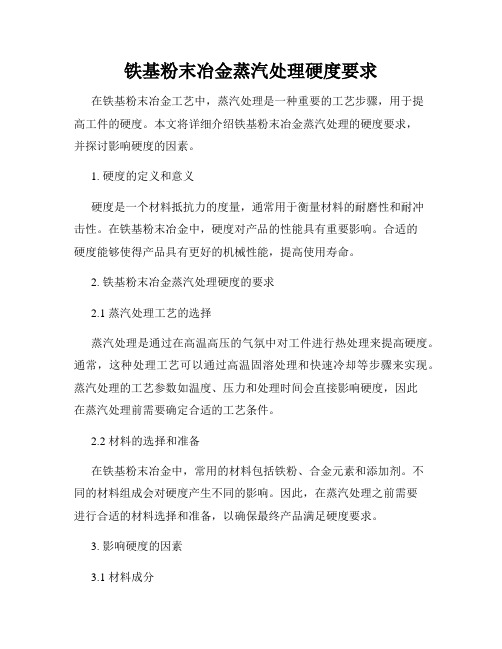
铁基粉末冶金蒸汽处理硬度要求在铁基粉末冶金工艺中,蒸汽处理是一种重要的工艺步骤,用于提高工件的硬度。
本文将详细介绍铁基粉末冶金蒸汽处理的硬度要求,并探讨影响硬度的因素。
1. 硬度的定义和意义硬度是一个材料抵抗力的度量,通常用于衡量材料的耐磨性和耐冲击性。
在铁基粉末冶金中,硬度对产品的性能具有重要影响。
合适的硬度能够使得产品具有更好的机械性能,提高使用寿命。
2. 铁基粉末冶金蒸汽处理硬度的要求2.1 蒸汽处理工艺的选择蒸汽处理是通过在高温高压的气氛中对工件进行热处理来提高硬度。
通常,这种处理工艺可以通过高温固溶处理和快速冷却等步骤来实现。
蒸汽处理的工艺参数如温度、压力和处理时间会直接影响硬度,因此在蒸汽处理前需要确定合适的工艺条件。
2.2 材料的选择和准备在铁基粉末冶金中,常用的材料包括铁粉、合金元素和添加剂。
不同的材料组成会对硬度产生不同的影响。
因此,在蒸汽处理之前需要进行合适的材料选择和准备,以确保最终产品满足硬度要求。
3. 影响硬度的因素3.1 材料成分材料的成分对蒸汽处理后的硬度有明显影响。
合理的合金元素添加可以增强材料的强度和硬度。
此外,添加剂的选择和组成也会对硬度产生影响。
3.2 蒸汽处理工艺参数蒸汽处理工艺参数的选择对硬度起着决定性的作用。
蒸汽处理的温度、压力和持续时间需要进行准确的控制,以确保产品达到预期的硬度要求。
此外,快速冷却过程的选择也会影响硬度的最终结果。
3.3 微观组织蒸汽处理后,铁基粉末冶金产品的微观组织也会对硬度产生影响。
合理的加热和冷却工艺可以使得材料的晶粒细化,从而提高硬度。
4. 硬度测试方法硬度的测试是评估铁基粉末冶金产品硬度性能的重要方法。
常用的硬度测试方法包括洛氏硬度测试、维氏硬度测试和布氏硬度测试等。
测试结果可以直观地反映产品的硬度水平,为进一步的优化提供依据。
5. 硬度要求的调整和优化根据产品的实际使用条件和要求,硬度的要求可能存在差异。
在铁基粉末冶金中,硬度要求可以根据实际情况进行调整和优化,以实现最佳的性能。
粉末冶金材料的热处理工艺

粉末冶金材料的热处理工艺热处理是粉末冶金材料制备过程中的关键步骤之一,通过控制材料的温度和时间,在一定的环境条件下改变材料的组织结构和性能,从而达到提高材料性能的目的。
本文将介绍粉末冶金材料的热处理工艺及其影响因素。
一、热处理的基本原理热处理是通过加热和冷却来改变材料的组织结构和性能。
具体来说,热处理可以改变材料的晶粒尺寸、晶界分布、相组成和相形态等。
通过调控这些因素,可以改善材料的硬度、强度、耐磨性、耐腐蚀性等性能。
二、热处理的基本步骤粉末冶金材料的热处理通常包括加热、保温和冷却三个步骤。
1. 加热:将粉末冶金材料置于炉中,通过加热设备提供的热能使材料升温。
加热温度应根据材料的成分和热处理要求进行选择,一般可以分为预热、保温和回火等几个阶段。
2. 保温:在达到所需的加热温度后,将材料保持在一定温度下一段时间,以使材料内部发生相应的组织变化。
保温时间的长短应根据材料的性质和要求来确定。
3. 冷却:在保温结束后,需要将材料迅速冷却至室温。
冷却速度的选择对于材料性能的改善至关重要,过快或过慢的冷却速度都可能导致材料性能不理想。
三、影响热处理效果的因素1. 温度:热处理温度是影响材料组织和性能的重要因素。
过高的温度可能导致材料过度烧结或晶粒长大,而过低的温度则可能使材料的相变不完全。
2. 时间:保温时间的长短对于材料的组织结构和性能有着重要影响。
过短的保温时间可能无法完全实现相变,而过长的保温时间则可能导致材料的晶粒长大。
3. 冷却速度:冷却速度的选择对于材料性能的改善至关重要。
过快的冷却速度可能导致材料的内部应力过大,而过慢的冷却速度则可能使材料的相变不完全。
4. 环境气氛:热处理过程中的气氛对于材料的表面质量和性能有着重要影响。
不同的气氛条件下,材料的表面可能会发生氧化、碳化等现象,从而影响材料的性能。
四、热处理工艺的应用粉末冶金材料的热处理工艺广泛应用于汽车、航空航天、电子、机械等行业。
例如,在汽车制造中,通过热处理可以提高发动机零部件的耐磨性和耐高温性能;在航空航天领域,热处理可以提高飞机结构材料的强度和耐腐蚀性能。
铁基粉末冶金零件热处理
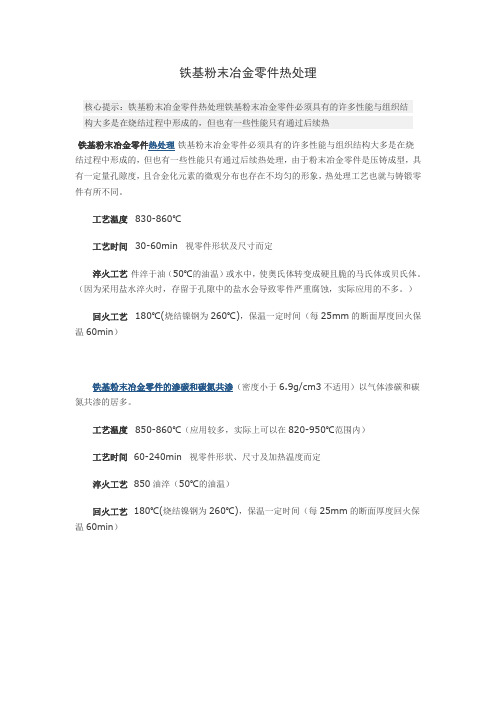
铁基粉末冶金零件热处理
核心提示:铁基粉末冶金零件热处理铁基粉末冶金零件必须具有的许多性能与组织结构大多是在烧结过程中形成的,但也有一些性能只有通过后续热
铁基粉末冶金零件热处理铁基粉末冶金零件必须具有的许多性能与组织结构大多是在烧结过程中形成的,但也有一些性能只有通过后续热处理,由于粉末冶金零件是压铸成型,具有一定量孔隙度,且合金化元素的微观分布也存在不均匀的形象,热处理工艺也就与铸锻零件有所不同。
工艺温度830-860℃
工艺时间30-60min 视零件形状及尺寸而定
淬火工艺件淬于油(50℃的油温)或水中,使奥氏体转变成硬且脆的马氏体或贝氏体。
(因为采用盐水淬火时,存留于孔隙中的盐水会导致零件严重腐蚀,实际应用的不多。
)
回火工艺180℃(烧结镍钢为260℃),保温一定时间(每25mm的断面厚度回火保温60min)
铁基粉末冶金零件的渗碳和碳氮共渗(密度小于6.9g/cm3不适用)以气体渗碳和碳氮共渗的居多。
工艺温度850-860℃(应用较多,实际上可以在820-950℃范围内)
工艺时间 60-240min 视零件形状、尺寸及加热温度而定
淬火工艺 850油淬(50℃的油温)
回火工艺 180℃(烧结镍钢为260℃),保温一定时间(每25mm的断面厚度回火保温60min)。
铁基粉末冶金零件温压工艺及进展

铁基粉末冶金零件温压工艺及进展1 温压工艺的国内外进展粉末冶金法是指以金属粉末或金属、非金属粉末的混合物为原料,借助其他助剂,通过成形和烧结,制造出各种类型配件的工艺技术。
从制备工艺来看,粉末冶金法与陶瓷工艺高度近似,是将陶瓷工艺移植到金属材料加工当中的一种加工技术。
从目前来看,世界上的温压专利粉末技术主要为美国的Hoeganaes公司、瑞典的Hogannas AB公司和加拿大的QMP公司所掌握,德国和日本在这个领域也具有较高的水平;具有绝对领先优势的温压专利加热设备主要是美国的EL-TEMP、Micro-VIet、TPP300、TOPS四大系統和瑞典的Linde Metal/teknik系统,两国加热装备的区别在于加热方法的不同,美国的装备通过电阻加热,而瑞典的装备通过热油加热。
当然,温压技术不可能实现室温一次压制成型,不断地涌现出各种标志性的产品。
由于粉末冶金技术一直被国外的粉末冶金公司视为绝密技术,控制非常严格,通常情况下其他研究机构是没有机会对其密化机理进行系统研究的。
我国的温压技术起步较晚,研究领域主要集中在粉末材料、润滑剂、温度和压力对粉末冶金零件密度的影响上,国内的生产线和预制粉末一般都源自于国外,仍未摆脱对国外的设备和原料的依赖。
2 温压工艺及其关键技术所谓的温压工艺就是利用特殊的加热系统对模具和加有特殊润滑剂的金属粉末进行加热,使其温度控制在预设温度土2.5℃的范围内,以更好地保证粉末的流动性和充填行为,而后利用传统的粉末压制工艺完成零件加工生产。
国外对温压工艺的专利保护主要集中在温压粉末技术(包括加入和未加入特殊高温润滑剂的金属粉末)和温压工艺的主要技术与设备两个方面,而这两个方面都是最为关键的温压技术。
2.1 温压粉末技术及发展状况温压粉末的制作是温压工艺的基础环节。
用于温压工艺的混合粉末必须要满足非常苛刻的要求,既要具有良好的流动性、压缩性和持久不变的松装密度,也要保证零件成本性能的一致性。
铁基粉末冶金零件的蒸汽处理
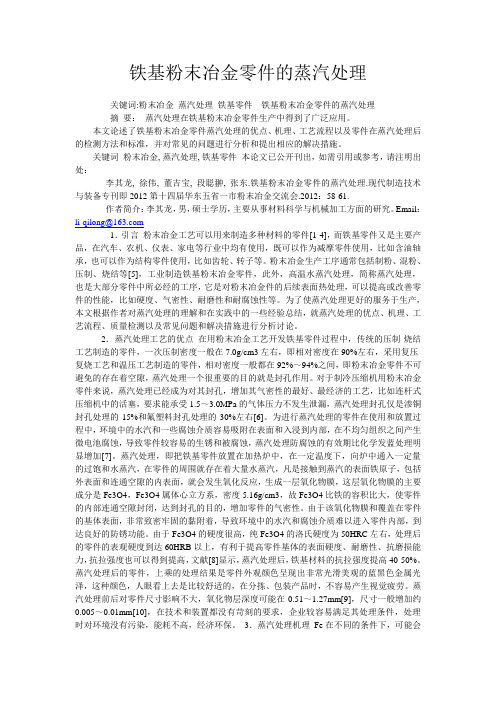
铁基粉末冶金零件的蒸汽处理关键词:粉末冶金蒸汽处理铁基零件铁基粉末冶金零件的蒸汽处理摘要:蒸汽处理在铁基粉末冶金零件生产中得到了广泛应用。
本文论述了铁基粉末冶金零件蒸汽处理的优点、机理、工艺流程以及零件在蒸汽处理后的检测方法和标准,并对常见的问题进行分析和提出相应的解决措施。
关键词粉末冶金, 蒸汽处理, 铁基零件本论文已公开刊出,如需引用或参考,请注明出处:李其龙, 徐伟, 董吉宝, 段聪翀, 张东.铁基粉末冶金零件的蒸汽处理.现代制造技术与装备专刊即2012第十四届华东五省一市粉末冶金交流会.2012:58-61.作者简介:李其龙,男,硕士学历,主要从事材料科学与机械加工方面的研究。
Email:*****************1.引言粉末冶金工艺可以用来制造多种材料的零件[1-4],而铁基零件又是主要产品,在汽车、农机、仪表、家电等行业中均有使用,既可以作为减摩零件使用,比如含油轴承,也可以作为结构零件使用,比如齿轮、转子等。
粉末冶金生产工序通常包括制粉、混粉、压制、烧结等[5],工业制造铁基粉末冶金零件,此外,高温水蒸汽处理,简称蒸汽处理,也是大部分零件中所必经的工序,它是对粉末冶金件的后续表面热处理,可以提高或改善零件的性能,比如硬度、气密性、耐磨性和耐腐蚀性等。
为了使蒸汽处理更好的服务于生产,本文根据作者对蒸汽处理的理解和在实践中的一些经验总结,就蒸汽处理的优点、机理、工艺流程、质量检测以及常见问题和解决措施进行分析讨论。
2.蒸汽处理工艺的优点在用粉末冶金工艺开发铁基零件过程中,传统的压制-烧结工艺制造的零件,一次压制密度一般在7.0g/cm3左右,即相对密度在90%左右,采用复压-复烧工艺和温压工艺制造的零件,相对密度一般都在92%~94%之间,即粉末冶金零件不可避免的存在着空隙,蒸汽处理一个很重要的目的就是封孔作用。
对于制冷压缩机用粉末冶金零件来说,蒸汽处理已经成为对其封孔,增加其气密性的最好、最经济的工艺,比如连杆式压缩机中的活塞,要求能承受1.5~3.0MPa的气体压力不发生泄漏,蒸汽处理封孔仅是渗铜封孔处理的15%和氟塑料封孔处理的30%左右[6]。
- 1、下载文档前请自行甄别文档内容的完整性,平台不提供额外的编辑、内容补充、找答案等附加服务。
- 2、"仅部分预览"的文档,不可在线预览部分如存在完整性等问题,可反馈申请退款(可完整预览的文档不适用该条件!)。
- 3、如文档侵犯您的权益,请联系客服反馈,我们会尽快为您处理(人工客服工作时间:9:00-18:30)。
铁基粉末冶金零件热处理
摘要:热处理是一种成熟的,经常使用的工艺性技术。
这篇文章评述了人们不大注意的铁基粉末冶金零件整体淬火时,孔隙度与合金含量对其淬透性的影响。
关键词:铁基粉末冶金零件;热处理;淬透性
在铁基粉末冶金零件生产中,零件材料必须具有的许多性能与组织结构都是在烧结过程中形成的,但其中一些性能只有通过后续热处理,才能得到改进与完善。
因此,热处理对于铁基粉末冶金零件产业是极其重要的一项技术。
铁基粉末冶金零件的热处理原理,虽然和成分相同的铸锻零件相同,但由于粉末冶金零件具有一定量孔隙度与合金化元素的微观分布可能不均一,因此,粉末冶金零件的热处理工艺可能有所不同。
关于孔隙度对铁基粉末冶金零件材料热处理性能的影响,经几十年的探索与实践,已有较清楚地认识,摘要介绍如下。
1 孔隙度对铁基粉末冶金零件整体淬火的影响
大部分铁基粉末冶金零件,为了增高强度、硬度及耐磨性,都需要进行整体淬火,即淬火与回火。
需要进行整体淬火的铁基粉末冶金零件,其化合碳含量应≥0.3%(质量分数),并且在图1中的A3温度以上呈奥氏体状态。
图1 碳钢的热处理相图
铁基粉末冶金零件的整体淬火由以下3道工序组成:
奥氏体化。
在具有和化合碳含量相当碳势的保护性气氛下,将零件加热到高于A3温度,通常为850℃,并保温一定时间,其长短视零件形状及尺寸而定。
诸如30min,使之奥氏体化。
淬火。
从奥氏体化温度或稍低,但仍高于A3的温度,将零件淬于油或水中,使奥氏体转变成硬且脆的马氏体或贝氏体。
对于铁基粉末冶金零件,最好是淬于温油(50℃)中,这是因为粉末冶金零件具有孔隙度,淬火冷却速度太快时,零件可能开裂。
另外,采用盐水淬火时,淬火后,存留于孔隙中的盐水会导致零件严重腐蚀。
回火。
依据GB/T19076-2003“烧结金属材料-规范”铁基粉末冶金零件通常是在180℃(烧结镍钢为260℃)下回火,回火时间通常是依据零件断面厚度,按每25.4mm回火1h。
其目的是消除奥氏体转变为马氏体与贝氏体时产生的内应力。
回火可减小马氏体与贝氏体的脆性,提升零件材料的韧性。
1.1 孔隙度对粉末冶金Fe-C材料淬透性的影响
淬透性的定义是,快速冷却时,在一给定深度,材料试样从奥氏体转变为马氏体的能力。
淬透性通常是用顶端淬火法测定的。
为测定烧结碳钢的淬透性,由水雾化铁粉与0.9%(质量分数)石墨粉的混合粉,用压制-烧结制成Φ80mm×高30mm,密度为6.0~7.1g/cm3的坯料[化合碳0.8%(质量分数)]。
再由坯料切削加工成顶端淬火试样,于870℃,在中性气氛中,奥氏体化30min后水淬。
从淬火端每隔2.5mm测定一次表观硬度HRA。
同时,还和由C-1080锻钢切削加工的顶端淬火试样进行了对比。
试验结果示于图2。
从图2可看出,材料试样的密度(即孔隙度)对淬透性有若干影响。
首先,孔隙度减低材料的热导率,这是因为孔隙中充满空气,而空气的热导率比钢小。
另外,由于硬度压痕和材料基体中的孔隙度相关,从而也影响测定的硬度值。
图2还表明,淬透性差不多随着烧结钢材料密度增大呈直线性增高。
因此,在设计-具有给定材料密度的粉末冶金碳钢零件时,对于选择使零件横截面能全部转变成马氏体的合适材料组成,图2是有用的。
1.2 铁基粉末冶金材料的淬透性标准
在设计-铁基粉末冶金零件时,要想使粉末金零件的横截面经过淬火-回火转变成马氏体,就必须依据材料的淬透性来选择适当的材料。
图2 烧结碳钢与常规C-1080碳钢的顶端淬火淬透性比较[2、3]
烧结钢试棒是用雾化铁粉混入0.90%石墨,经压制、烧结而成,密度为6.0~7.1g/cm3。
于870℃在中性气氛中奥氏体化30min后水淬。
从淬火端每隔2.5mm测量一点就铁基粉末冶金材料而言,除上述的孔隙度影响材料的淬透性外,添加于材料中的合金化元素,诸如铜、镍、钼等,也影响材料的淬透性。
美国金属粉末工业联合会(MPIF)在1997年第一次发布了铁基粉末冶金材料的淬透性标准,见表1。
这个标准是依据ASTMA255顶端淬火试验方法标准制定的。
硬度与深度的关系曲线是用HRA硬度标尺作出的。
端淬深度是指在试样上从淬火端到硬度值低于65HRA 处的深度(每间隔1.6mm(1/16英寸)取一硬度读数)。
倘若试样表面的硬度未达到65HRA,则将其端淬深度(深度J)列为<1。
J65若为2,就表明端淬深度为2×1.6mm=3.2mm。
鉴于表2中列出的淬透数据都是用表观硬度测定的,因此,测定的结果中也包括密度的影响。
综上所述,要想得到粉末冶金材料的精确淬透性,必须对材料在同一密度条件下进行比较。
2 合金含量对铁基粉末冶金材料淬透性的影响
美国评定MPIF标准35“粉末冶金结构零件材料标准”中的材料热处理性能的粉末冶金技术中心(CPMT)最近的协调工作证实,烧结零件名义组成的含碳量(指化合碳)为0.5%(质量分数)时,热处理的材料性能最好,随着烧结体密度与合金含量增高,其可进一步减小。
含碳量较高的零件淬火时,变形、脆化及淬裂的几率增大。
图3示二种预合金化粉末冶金钢的这种效应与化合碳含碳增高的关系。
图4示,由于添加铜与镍,粉末冶金材料淬透性的改进。
图4中所示4种组成的试样都是在生产条件下烧结到密度为6.7g/cm3,淬火与回火的。
图4中的数据表明,铜可有效增高表面淬硬性,但只能适度增大淬透性。
同时添加镍时,可进一步增大淬透性,但表面淬硬性增高不大。
图3 合金化烧结钢FL42××与FL46××的含碳量对抗拉强度的影响。
烧结钢密度7.16g/cm3。
(1Ksi=6.985MPa)
图4 铜含量和镍含量对烧结钢淬透性的影响(试棒材料密度6.7g/cm3)对3种烧结体密度为7.0g/cm3的铁基粉末冶金材料和选择的3种常规锻钢进行的顶端淬火对比试验研究结果示于图5。
通常,多用粉末冶金镍钢FN-0205零件替代SAE8620钢零件。
虽然粉末冶金FN-0205钢可达到和SAE8620钢同样的表面显微硬度,但其淬透性差,这会减低零件实际承受载荷的能力。
对于这类情况,零件生产企业必须依据对零件用途的全面分析,来确定这样替代是否合适。
图5 粉末冶金钢与常规锻钢顶端淬火淬透性曲线比较[5]
3 孔隙度对热处理的铁基粉末冶金材料疲劳强度的影响
H1Ferguson[5]认为,近来,对一些铁基粉末冶金材料的疲劳试验的研究表明,孔隙度影响材料的疲劳强度。
孔隙除减低粉末冶金材料的热导率外,孔隙也起到提高应力的作用。
对于承受循环载荷的零件,使零件表层内形成合乎需要的压缩应力是很重要的。
这也是热处理的作用与目的。
零件表面层的残余压缩应力反作用于施加的拉伸应力,可导致零件的疲劳强度增高。
从表1所列8类铁基粉末冶金材料来看,其含碳量[化合碳(质量分数)]可分为两种,一为0.5%,一为0.8%。
对于需要强度、硬度、耐磨性及疲劳强度较高,必须进行热处理的铁基粉末冶金零件,一般推荐化合碳含量为0.5%。
这时,热处理工艺应规定炉子气氛的碳势为0.70%~0.75%(质量分数),以使零件表面具有略高的含碳量,从而保证淬火时表面层能全部转变成马氏体。
这是因为含碳量增高时,马氏体转变的温度(M s)减低。
当心部材料达到温度(M s)时,产生马氏体相变,与之同时体积胀大,结果对淬硬的表面层作用以压力,形成残余压缩应力分布,心部相变越充分残余表面压缩应力就越大。
H1Ferguson认为,倘若粉末冶金零件材料孔隙度过高,则淬透性相应地减低,这时零件心部就只能有部
分转变为马氏体。
这就使表层应力呈平衡状态;或者有可能呈残余拉伸应力状态,这种拉伸应力来源于外加载荷。
结果,减低疲劳强度。
因此,选择高强度铁基粉末冶金零件材料时,必须依据表1所示淬透性的数据来寻找合适的材料组成与密度,使选定的零件材料具有足够高的淬透性,以期使零件能全部产生马氏体相变。
另外,还应使表面层充分渗碳硬化,以期在心部发生马氏体相变之前,其奥氏体就已全部转变成了马氏体。
另外,应该注意的是,当今,许多化合碳含量为0.8%(质量分数)的铁基粉末冶金材料也正在进行热处理。
在这种场合,倘若在零件的烧结过程中未注意到防止表面脱碳,而这是经常发生的,则在零件表面层产生的应力就可能是拉伸应力,从而使零件易于疲劳失效。
对于当前正在推广应用的烧结硬化钢,这一点是特别应该注意的。