试模流程图
试模流程图
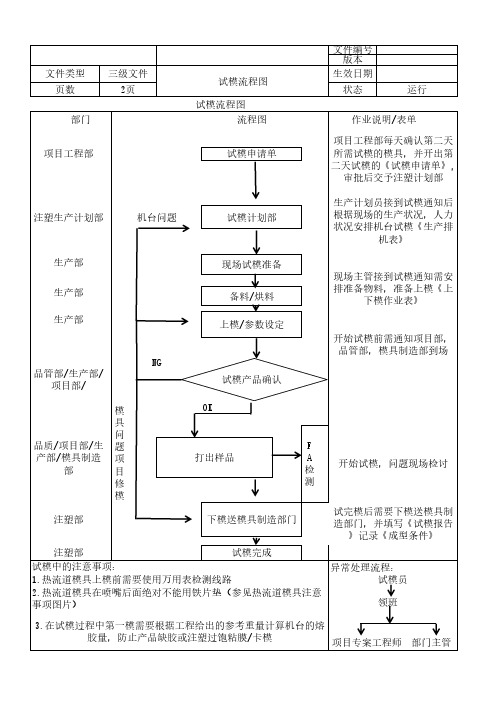
三级文件 2页
部门
项目工程部
试模流程图 试模流程图
流程图
试模申请单
文件编号 版本
生效日期
状态
运行
作业说明/表单
项目工程部每天确认第二天 所需试模的模具,并开出第 二天试模的《试模申请单》,
审批后交予注塑计划部
注塑生产计划部
机台问题
试模计划部
生产计划员接到试模通知后 根据现场的生产状况,人力 状况安排机台试模《生产排
注塑部
下模送模具制造部门
试完模后需要下模送模具制 造部门,并填写《试模报告
》记录《成型条件》
注塑部
试模完成
试模中的注意事项: 1.热流道模具上模前需要使用万用表检测线路
异常处理流程: 试模员
2.热流道模具在喷嘴后面绝对不能用铁片垫(参见热流道模具注意 事项图片)
领班
ቤተ መጻሕፍቲ ባይዱ
3.在试模过程中第一模需要根据工程给出的参考重量计算机台的熔
胶量,防止产品缺胶或注塑过饱粘膜/卡模
项目专案工程师 部门主管
机表》
生产部
生产部 生产部
NG 品管部/生产部/
项目部/
现场试模准备 备料/烘料
上模/参数设定
试模产品确认
现场主管接到试模通知需安 排准备物料,准备上模《上
下模作业表》
开始试模前需通知项目部, 品管部,模具制造部到场
模
具
问
品质/项目部/生 题
产部/模具制造 项
部
目
修
模
OK 打出样品
F A 检 开始试模,问题现场检讨 测
模具生产工艺流程图(精AA

模具制造工艺流程图 模具名称 模具编号 要求交模日期 计划第一次试模日期 模具设计人 工艺编制 生产计划制订 进度跟踪 生产准备检查 材料 图纸 镶件加工 计划 实际 铜公加工 计划 实际 生产准备检查 材料 图纸 CNC加工 计划 实际 铣方及孔加工 计划 实际 生产准备检查 材料 图纸 综合铣加工 计划 实际 EDM清角 计划 实际 配镶件 计划 实际 EDM加工 计划 实际 抛 光 计划 实际 生产准备检查 材料 图纸 铜公加工 计划 实际 镶件加工 计划 实际 生产准备检查 材料 图纸 生产准备检查 材料 图纸 深孔钻加工水孔 计划 实际 CNC加工 计划 实际 摇臂钻钻孔 计划 实际 EDM加工 计划 实际 配镶件 计划 实际 打磨、抛光 计划 实际 配滑块、配模 计划 实际 钻斜导柱孔,钻攻抽芯螺孔 计划 实际 总装、试模 计划 实际 备检查 材料 图纸 划线,加工吊环孔 计划 实际 凸台、镶件槽CNC加工 计划 实际 EDM清角 计划 实际 钻水孔、螺孔 计划 实际 配镶件 计划 实际 钻镶件槽螺孔 计划 实际 装镶件,配模芯、模板 计划 实际 钻司筒、顶针孔 计划 实际 扩司筒、顶针孔 计划 实际 铰司筒、顶针孔 计划 实际 CNC加工成型面 计划 实际 EDM加工 计划 实际 配模 计划 实际 抛光 计划 实际 铜公加工 计划 实际 生产准备检查 材料 图纸 推方、角铁加工 计划 实际 生产准备检查 材料 图纸 年 月 日 滑块 定模 动模芯 推方角铁 镶 件 铜公 铜公 镶件 铜公 镶件
模具试模流程
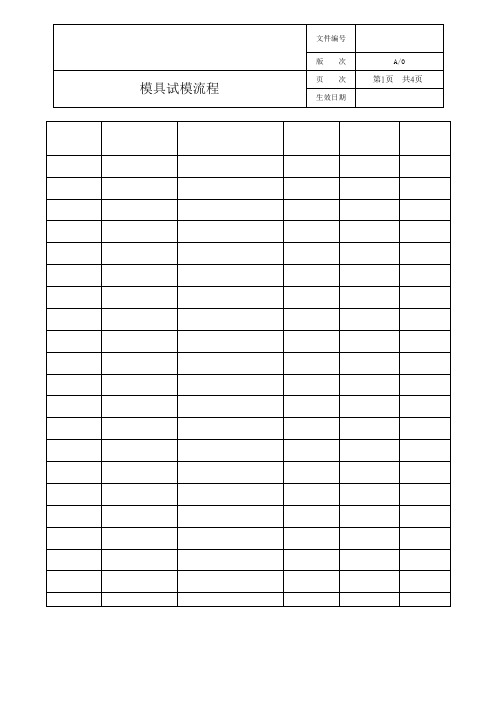
1.目的:利用所分配的公司资源,优质、高效地完成试模所有工作,确保新模具转产后成型工艺能够得到有效控制。
试模的目的是要找出优化的工艺参数和模具设计2.范围:适用于本公司所有模具试模的全过程3.试模流程:3.1.新模试模3.1.1模具工确定模具状况后填写试模申请单,并交给模具部计划员,计划员根据模具完成的时间及客户要样板的节点按顺序编号安排试模(原则上需提前一天安排)。
3.1.2试模组(机修组)根据试模计划单进行安排到待试模区领模。
根据计划单内容要求开单领料备料烘烤,做好试前准备。
3.1.3试模技术员到待试模区检查确认模具的状况后将模具拉到相应的机台上机装模,连接冷却水管,调试模具顶出装置,检查活动部位,准备好试模,确认完好后通知项目/工程、模具设计、品质、模具工、机修到现场参与试模。
3.1.4机修先调试出产品打不足的测试产品,确认进浇是否均衡,再调试出整件产品检测产品的外观,如无异常注塑5模产品交品质初步检测产品尺寸与装配效果。
3.1.5品质确认好样品后通知试模组,试模技术员按试模计划单要求数量注塑样品。
3.1.6品质确认样品NG,机修会同模具设计、项目、模具工商讨问题的根源与发生原因并做出相应的措施,在模具上或注塑工艺等方面做改善。
如客户要样急,项目与品质可以同意限量注塑样品。
3.1.7完成试模后机修卸下模具,并将模具清洗干净,并喷上防锈剂,异型分型面模具卸模前通知模具工涂上红丹并将模具放回原位。
3.1.8注塑出来的样品安排人员加工并放置在指定区域由项目或模具部取走3.1.9机修根据试模过程中出现的问题如实填写《模具试模状况表》《成型条件表》,在样品上不良位置做出标记并提出相应的改善建议,机修组长审核后提交模具部作修改模和2次试模参考.3.1.10机修组长总结T0 、T1等试模状况,审核总结完毕后提交项目部存档;3.1.11品质现场确认样品OK,把样品交与测量做详细尺寸报告,由品质主管审核,确认OK,递交项目送样给客户确认,确认NG把把样品报告连同一模测量样品交模具部做改模参考。
模具验证流程图
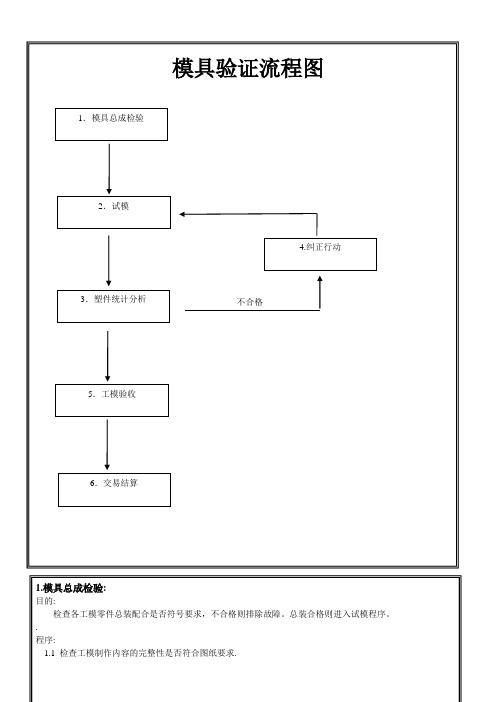
模具验证流程图不合格1.模具总成检验:目的:检查各工模零件总装配合是否符号要求,不合格则排除故障。
总装合格则进入试模程序。
.程序:1.1 检查工模制作内容的完整性是否符合图纸要求.1.模具总成检验 2.试模 3.塑件统计分析 4.纠正行动5.工模验收6.交易结算1.2 检查工模零件主要的形状尺寸和位置尺寸.1.3 检查工模行位运行情况,斜顶运行情况.1.4 检查工模FIT模分型面各处碰穿和插穿.1.5 检查工模开合模,顶出和复位运行.1.6 检查工模油缸,油缸附件,行程开关运行.1.7 检查工模浇口入水和排气槽.1.8 检查工模冷却系统是否漏水以及运水压力和流量数据.1.9 检查工模铭牌编号和试模及运输所需的安全装置,以及与注塑机配合码模螺孔尺寸.1.10 各工模零件总装完整性和正确性,避免零件错装漏装以及装配不当等缺陷.1.11 检查成形零件表面的省模光洁度.1.12 填写工模总装检查报告(TABLE 1).2. 试模:2.1 目的:通过试模找出所有试模过程中所遇到的问题,来评估模具是否满足注塑生产要求,以进一步决定对模具作出相应修改.2.2 内容:2.2.1 根据模具设计任务书,选择相应注塑机.2.2.2 试调校空运行,检查模具运行状态,如有必要及时送制作组维修.2.2.3 根据模腔大小,调节合适的射胶压力、速度,以第一模走满约70%左右(不允许第一模爆棚),逐步加压加速.2.2.4 对于多型腔的模,通过SHORT SHOT试验,对比各腔进胶速度的快慢,加大填充进胶较慢的型腔流道,使各型腔保持平衡入水.2.2.5 试调校不同之注塑参数(设置不同的温度、速度、压力、模温之组合)各成型200~300啤,并对成型工艺条件作详细的记录,分类填写试模报告.(TABLE 2)2.2.6 进行尺寸检测收集数据资料,进行塑件统计分析.3. 塑件统计分析:3.1 目的:通过数据收集,进行统计分析,从而掌握零件尺寸的波动情况,判断产品优劣.3.2 方法:3.2.1 每25啤抽出5PCS连续啤塑的产品,使用相应仪器(CMM,投影仪,千分尺,百分表等)读出要求测量的尺寸,并记录。
试模产品试样作业规范

版本:A/1文件編号:DG-QA-075 版本/版次修改事项/摘要生效日期A/1 初版发行。
2022年7月24日编制:职位:生产主管签署:______________ 日期:审核:职位:经理签署:______________ 日期:批准:职位:经理签署:______________ 日期:此文件若盖有红色“受控发行”的印章,则是正式文件.任何员工不得私自影印,请妥善保管好正式文件!正本印章受控发行印章版本:A/1文件編号:DG-QA-0751.目的为了确保本公司模具及新产品在量产前进行过实际验证,以保证量产的顺畅。
2.定义2.1.1试模之目的是为了确认新开模具的外观尺寸及工艺要求是否符合设计之要求。
2.1.2试样之目的是为了做样品给客户确认产品之功能和品质是否符合客户之要求。
2.1.3试产之目的是为量产做准备,排除设计和制程问题,做好量产前数据分析。
3.范围适用于本公司各种模具及新产品的导入。
4.权责4.1工程部负责新产品的模具开发及资料和模具的提供,项目部负责新产品试产导入,物料齐料跟进,工程部负责试模和试样,试产过程中问题的解决,各阶段审查总裁决。
4.2试产小组:由下列各部门主管(工程部、项目部、品质部、生产部、计划部、)派任人员,负责各阶段跟进。
4.3项目部:4.3.1要把模具及文件提供给生产和品质部使用部门(含:图纸BOM、Gerber、SMT打件资、电路图、样品、其他生产相关注意事项等)。
4.3.2负责提出要求试模,试样的需求,并开出手动工单给到相关试产部门及PMC按排设备进行生产。
4.3.3负责跟进试模试样产品之物料齐料情况。
4.3.4负责试产产品所使用物料的系统扣数。
4.3.5负责试模试产样后成品的接收和管理。
4.3.6参与评估零组件外发加工的交期、价格、及零件生命周期。
4.4工程部:4.4.1模具和工治具开发及验收。
4.4.2跟进试模、试样、及生产过程中问题的解决4.4.3试模试样产品结果的确认。
模具试模流程

4品质部检测完将检测结果及数据记录于《样品检测报告》。
5《样品检测报告》由研发部、品质部、项目部共同确认,对检测结果真实性负责。
6产品注塑成型工艺参数在确定试模OK后,由注塑技术员进行记录。
试模报告
样品检测报告
成型工艺参数表
塑胶产品检验规范
产品图纸
005
试模检讨
试模产品
3注塑生产部在试模当日前,完成原料的烘烤和配料。
4为避免其它人员等待浪费时间,注塑部技术员应提前1-2小时进行模具安装与机台调试。
注塑排产
注塑原料
安装好的模具
调试好的机台
上下模作业指导书
003
现场试模
注塑原料
安装好的模具
调试好的机台
工模部
注塑部
品质部
研发部
项目部
2H
1试模加料前应确认料斗内原料已清洗干净。
工程部:
制造部:
项目管理部:
人资行政部:
IT部:
11.编修/审批记录:
版本
编制人
审核人
编制/修订日期
修订内容及理由(摘要)
签批人
A/0
新版发行
04
PMC
PC
计划安排试模所需的机台及物料。
熟练操作办公软件,能独立安排生产计划。
05
品质部
PQE
1负责试模样品的随机抽样检测。
2对抽样样品进行尺寸、结构、外观进行检测,出具检测报告。
3试模问题点对产品质量影响的风险评估,提出改善建议。
4试模问题点改善后的跟进验证。
1熟悉模具结构。
2熟悉注塑原理及成型工艺。
项目部
营销部
客户
富士康内部资料-试模流程PPT课件.ppt

7.打出標准值產品后,模具廠及成型廠試模師依模具狀況及 成品狀況再作出下限值產品并記下成型條件.依此再試作 上限值之產品并記記下成型條件.再將保壓取消打出未保 壓成品.
8.完成三種基本條件之成型品,依其條件各備5件并作記號送 于工程師驗証其所需規格.若須作調整時,亦不會偏離此三 種成型條件規范太多,故可以很快調出工程師所需之式樣. (每次微調完成式樣時,在塑件上須編號且須作成型條件記 錄,方可送樣給工程師確認).
立、废料销毁……)
三、试 模 后
1.保压取消打出的未饱模成品2PCS 2.水口 3.尺寸上限样品2PCS及成型条件 4.尺寸下限样品2PCS及成型条件 5.较佳成型条件样品2PCS及成型条件 6.试模后模具保养 7.试模问题检讨
試模作業
15.若成品表面是否有异常现象是否有确认模具上有 相同现象
16.有咬花现象时是否有与咬花样板核对
17.有刻字、印刷时是否有与黑白稿核对并确认是否正确
18.确认结合线的位置及不当的位置
19.是否有进胶喷痕、流痕现象
20.是否有银丝现象,并确认原料干燥烘烤情形 21.是否有将试模完的样品交代后续处理事项(喷漆、组
D(油),溫度是否先行確認.(查模溫機) 2.射出料管加熱溫度是否有按照原料廠所提供的資料
及要求設定. 3.如果是熱膠道的模具,每個加熱點溫度、作動是否
正常(即溫控器與加熱器是否正常).
4.射出成型機台大小及料管直徑是否與上次試模相同.
5.射嘴與模具的澆口襯套之間是否有漏膠的現象,塑料 在射管中是否停留過久,如果有過久時是否有先行將 料管內的料射出不用.
试
模作业流程
目录
一、試 模 流 程 二、试 模 前 三、试 模 中 四、试 模 后
模具验收流程
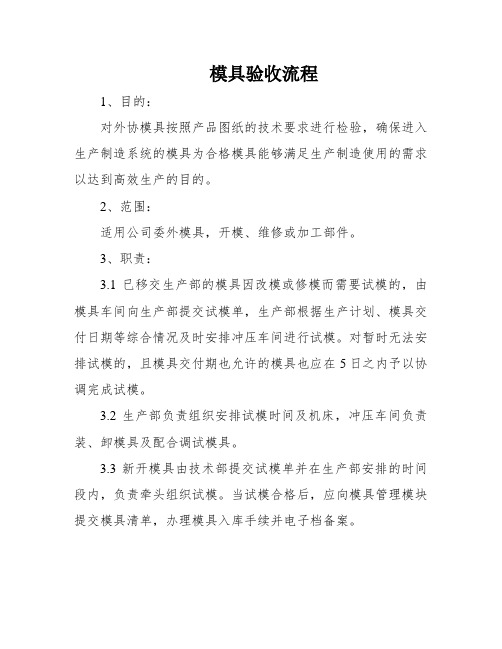
模具验收流程
1、目的:
对外协模具按照产品图纸的技术要求进行检验,确保进入生产制造系统的模具为合格模具能够满足生产制造使用的需求以达到高效生产的目的。
2、范围:
适用公司委外模具,开模、维修或加工部件。
3、职责:
3.1已移交生产部的模具因改模或修模而需要试模的,由模具车间向生产部提交试模单,生产部根据生产计划、模具交付日期等综合情况及时安排冲压车间进行试模。
对暂时无法安排试模的,且模具交付期也允许的模具也应在5日之内予以协调完成试模。
3.2生产部负责组织安排试模时间及机床,冲压车间负责装、卸模具及配合调试模具。
3.3新开模具由技术部提交试模单并在生产部安排的时间段内,负责牵头组织试模。
当试模合格后,应向模具管理模块提交模具清单,办理模具入库手续并电子档备案。
3.4试模时品质部应按照图纸技术要求仔细检验试模样件是否符合,并做好相关记录,无论试模样件状态如何都应详实、准确予以记录备案以便后期查验。
3.5改模、修模需试模的在试模合格后,应在模具维修记录表上做好相干记录,并由模具办理存案电子档。
3.6对试模不合格的模具,由牵头部门负责反馈、联系重新修改或返工并重新走流程予以试模。
附:1、试模流程图
2、试模申请表(申请、评审二合一表)
模具进厂填写申请表安排试模试模记录
办理入库标识、油漆相关方检讨
OK
返修、重做退回厂家
办理入库让步存案
拒收、隔离
NG。
- 1、下载文档前请自行甄别文档内容的完整性,平台不提供额外的编辑、内容补充、找答案等附加服务。
- 2、"仅部分预览"的文档,不可在线预览部分如存在完整性等问题,可反馈申请退款(可完整预览的文档不适用该条件!)。
- 3、如文档侵犯您的权益,请联系客服反馈,我们会尽快为您处理(人工客服工作时间:9:00-18:30)。
台州大发模具制造有限公司
试模流程图
<A>通知试模:其它部门【总经理、工程部(设计师)、制造部(制作组长)、品保部】
得知需试模,用《内部联系条》把客户编号、模具编号、产品名称、试模胶料、数
量等知会制造部文员;
<B>试模通知单:制造部文员填写《试模通知单》(并登记于《试模状况记录一览表》
上,每月统计公布一次),经审批,分发各单位,统一安排试模(填单前需由品保部工艺员确认试模用物料是否齐全);
<C>试模前准备:①品保部工艺员专人负责试模用物料(含胶料、包装等)的出入库, 领
用物料需填写《试模用料状况一览表》; ②制作组长派组员与工艺员一起领齐(运送)试模用物料,并由工艺员专人负责烘料;③注塑车间安排机台,并通知品保部工艺员; ④试模前品保部提前安排T01前点检,并填写《模具表现评估表之一(T01前)》;
<D>参与试模:①由品保部工艺员通知参与试模人员,参与试模人员需在《试模情况记
录表》上签到(《试模情况记录表》由制造部文员专人保管);②新模T01、T1时,制作组长、设计师、品保部人员必须到场;③新模T2以后及修(改)模试模,制作组长及品保部人员必须到场,其它人员视情况而定;
<E>试模件处理:①试模件由品保部负责分类管理(试模件放于专用仓库,出入库及用
途需记录);②品保部人员负责试模件包装(可请注塑车间人员帮忙);③每次试模品保部必须保留两啤以上完整试模板(含浇口);④品保部负责对试模件进行外观检测及尺寸检测,并填写《模具表现评估表之三(试模件评估)》及《首件检测报告》;
⑤林助理负责对试模件送样(含包装要求);
<F>试模后现场清理:①注塑车间把模具卸下,放于指定位置,并通知制造部文员;
②制造部文员(含叫叉车)通知制作组长把模具拉回制作车间;③水压机、新模用温
控箱等工具由品保部专人保管,制作组长领用需写借条;
<G>试模记录:①试模相关人员(试模员、品保部、制造部)填写《试模情况记录表》,
并交制造部文员专人保管;②品保部跟模人员填写《模具表现评估表之二(试模现场)》;
③试模相关人员(试模员、品保部、制造部)如实填写《试模用料状况一览表》,并
交制造部文员专人保管;
<H>修(改)模事宜:①由品保部、制造部(制作组长)把相关资料(问题点),汇总
到林助理处;②由林助理出具《修(改)模通知单》,制造部修(改)模,设计师负责修改模技术支持,制造部负责进度.。