内检测技术在长输管道中的应用
浅析长输压力管道无损检测技术
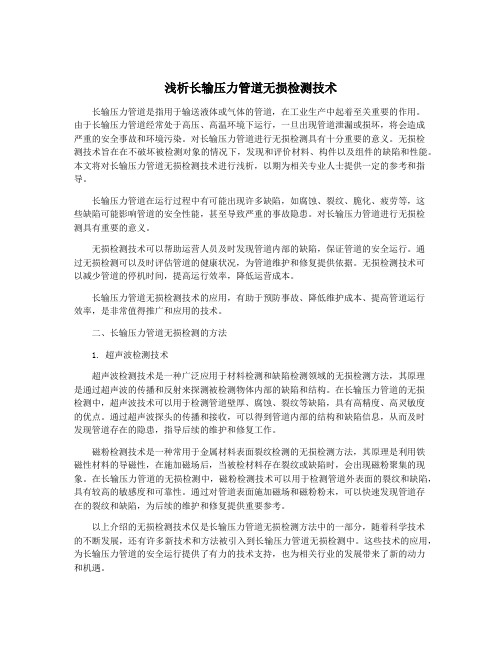
浅析长输压力管道无损检测技术长输压力管道是指用于输送液体或气体的管道,在工业生产中起着至关重要的作用。
由于长输压力管道经常处于高压、高温环境下运行,一旦出现管道泄漏或损坏,将会造成严重的安全事故和环境污染。
对长输压力管道进行无损检测具有十分重要的意义。
无损检测技术旨在在不破坏被检测对象的情况下,发现和评价材料、构件以及组件的缺陷和性能。
本文将对长输压力管道无损检测技术进行浅析,以期为相关专业人士提供一定的参考和指导。
长输压力管道在运行过程中有可能出现许多缺陷,如腐蚀、裂纹、脆化、疲劳等,这些缺陷可能影响管道的安全性能,甚至导致严重的事故隐患。
对长输压力管道进行无损检测具有重要的意义。
无损检测技术可以帮助运营人员及时发现管道内部的缺陷,保证管道的安全运行。
通过无损检测可以及时评估管道的健康状况,为管道维护和修复提供依据。
无损检测技术可以减少管道的停机时间,提高运行效率,降低运营成本。
长输压力管道无损检测技术的应用,有助于预防事故、降低维护成本、提高管道运行效率,是非常值得推广和应用的技术。
二、长输压力管道无损检测的方法1. 超声波检测技术超声波检测技术是一种广泛应用于材料检测和缺陷检测领域的无损检测方法,其原理是通过超声波的传播和反射来探测被检测物体内部的缺陷和结构。
在长输压力管道的无损检测中,超声波技术可以用于检测管道壁厚、腐蚀、裂纹等缺陷,具有高精度、高灵敏度的优点。
通过超声波探头的传播和接收,可以得到管道内部的结构和缺陷信息,从而及时发现管道存在的隐患,指导后续的维护和修复工作。
磁粉检测技术是一种常用于金属材料表面裂纹检测的无损检测方法,其原理是利用铁磁性材料的导磁性,在施加磁场后,当被检材料存在裂纹或缺陷时,会出现磁粉聚集的现象。
在长输压力管道的无损检测中,磁粉检测技术可以用于检测管道外表面的裂纹和缺陷,具有较高的敏感度和可靠性。
通过对管道表面施加磁场和磁粉粉末,可以快速发现管道存在的裂纹和缺陷,为后续的维护和修复提供重要参考。
科技成果——长输油气管道内检测系统

科技成果——长输油气管道内检测系统所属领域油气储运成果简介近20年来,管线工业得到迅速发展,长输管道运行安全性成了一个关系到国计民生的重大问题。
管道内检测系统由管道漏磁内检测系统(俗称智能PIG)和管道变径内检测系统组成,管道漏磁内检测系统应用漏磁检测原理对输送管道进行在线无损检测,为管道运行、维护及安全评价提供科学依据。
管道漏磁内检测系统以管道输送介质为行进动力,在管道中行走,对管道进行在线直接无损检测是当前国内外公认的主要的管道检测手段。
该系统完成长输油/气管道缺陷检测,完成管道缺陷、管壁变化、管壁材质变化、缺陷内外分辨、管道特征(管箍、补疤、弯头、焊缝和三通等)识别检测,可提供缺陷面积、程度、方位和位置等全面信息。
管道变径内检测系统完成管道机械变形的检测功能,变径管道检测器在管道中由输送介质推动,在管道内运行,完成管道机械变形检测,变径管道检测器由机械变形传感器、计算机数据处理系统和定位系统组成。
应用范围φ159-φ1400各规格钢质长输油/气管技术特点管道漏磁内检测系统性能指标获奖情况2001年11月通过了国家自然科学基金委员会组织的鉴定,认为在主要指标上达到国际先进水平。
该项目2004年获国家科技进步二等奖,2003年获辽宁省科技进步一等奖。
该项目取得了一系列漏磁管道探伤理论成果,添补国内空白,打破国际垄断,同时为项目应用企业取得了巨大的经济效益和社会效益。
专利情况授权发明专利1项,申请发明专利9项。
技术水平国际先进生产使用条件适用于国内外已使用的钢质长输油气管道。
市场前景目前我国在役长距离油/气输送管道总长约3万公里,在建和拟建的西部十余条管线长达近万公里。
近年来,国内管道故障时常发生,一般事故将造成上百万乃至几百万的经济损失,且造成环境污染,所以管道运行检测在国内已引起高度关注。
管道内检测是管道检测的直接有效手段,在国际上属于垄断技术,每套设备标价几百万至几千万美元,且不易购买。
国外公司在我国进行管道检测的服务费用亦十分昂贵,每公里检测费用达上万美元。
浅析长输管道清管及内检测
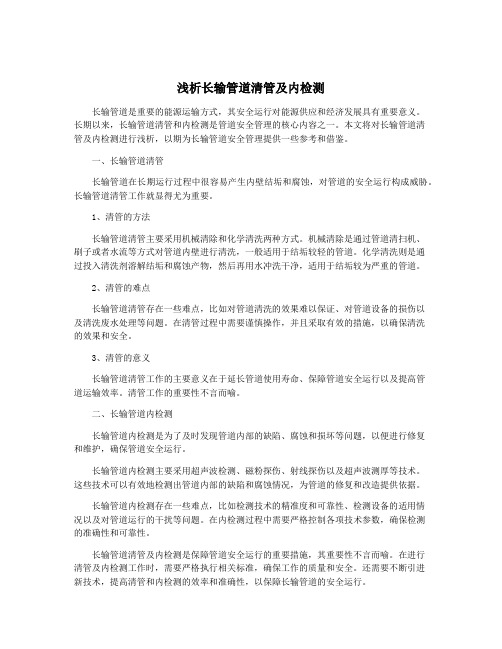
浅析长输管道清管及内检测长输管道是重要的能源运输方式,其安全运行对能源供应和经济发展具有重要意义。
长期以来,长输管道清管和内检测是管道安全管理的核心内容之一。
本文将对长输管道清管及内检测进行浅析,以期为长输管道安全管理提供一些参考和借鉴。
一、长输管道清管长输管道在长期运行过程中很容易产生内壁结垢和腐蚀,对管道的安全运行构成威胁。
长输管道清管工作就显得尤为重要。
1、清管的方法长输管道清管主要采用机械清除和化学清洗两种方式。
机械清除是通过管道清扫机、刷子或者水流等方式对管道内壁进行清洗,一般适用于结垢较轻的管道。
化学清洗则是通过投入清洗剂溶解结垢和腐蚀产物,然后再用水冲洗干净,适用于结垢较为严重的管道。
2、清管的难点长输管道清管存在一些难点,比如对管道清洗的效果难以保证、对管道设备的损伤以及清洗废水处理等问题。
在清管过程中需要谨慎操作,并且采取有效的措施,以确保清洗的效果和安全。
3、清管的意义长输管道清管工作的主要意义在于延长管道使用寿命、保障管道安全运行以及提高管道运输效率。
清管工作的重要性不言而喻。
二、长输管道内检测长输管道内检测是为了及时发现管道内部的缺陷、腐蚀和损坏等问题,以便进行修复和维护,确保管道安全运行。
长输管道内检测主要采用超声波检测、磁粉探伤、射线探伤以及超声波测厚等技术。
这些技术可以有效地检测出管道内部的缺陷和腐蚀情况,为管道的修复和改造提供依据。
长输管道内检测存在一些难点,比如检测技术的精准度和可靠性、检测设备的适用情况以及对管道运行的干扰等问题。
在内检测过程中需要严格控制各项技术参数,确保检测的准确性和可靠性。
长输管道清管及内检测是保障管道安全运行的重要措施,其重要性不言而喻。
在进行清管及内检测工作时,需要严格执行相关标准,确保工作的质量和安全。
还需要不断引进新技术,提高清管和内检测的效率和准确性,以保障长输管道的安全运行。
长输油气管道漏磁内检测技术

着眼于管道内检测技术侧重介绍基于漏磁的管道内检测技术对油气管道漏磁内检测器基本结构检测原理和影响因素进行归纳总结阐述了管道漏磁内检测中轴向励磁和周向励磁等关键技术的研究现状对工程化应用的国内外漏磁内检测器检测能力进行对比介绍了漏磁信号的处理方法及管道的完整性评价技术提出了管道漏磁内检测行业的未来展望
1 9 2 0 ] 对漏磁场进行了准确的建模, 仿真分析; 黄作英等人 [
质, 可用于石油、 天然气管道检测, 但其换能效率低、 受噪 声干扰严重
[ 3 ]
。漏磁检测技术可检测出油气管道金属损
通过测量漏磁信号离散傅里叶变换后的系数, 实现对管 u s a nN a t i o n a l U n i v e r s i t y 的H u i M. 道裂纹的检测; 韩国 P
7 ] K . 等人 [ 利用三维有限元法对轴向定向裂纹的检测进 8 ] 行了研究; 印度的 D a n i e l J 等人 [ 利用神经网络和小波
?CM检测技术在油气长输管道检测中的应用
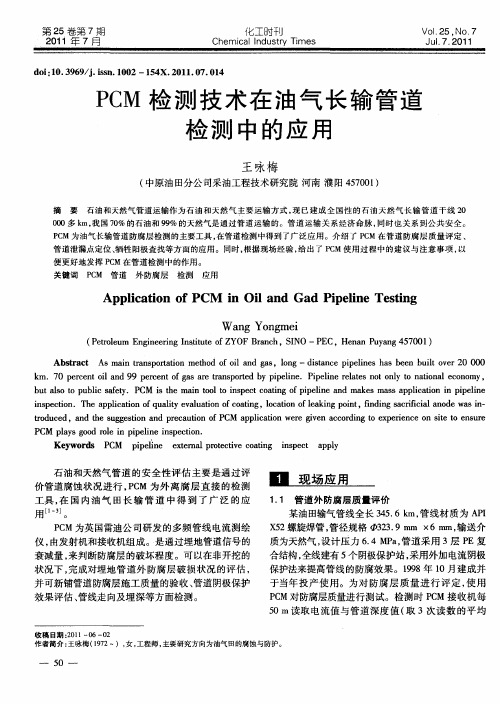
P 检 测 技 术在 油 气 长 输 管 道 C M 检 测 中 的 应 用
王 咏梅
( 中原油 田分 公 司采油 工程技 术研 究 院 河南 濮 阳 4 70 ) 50 1
摘 要 石油 和天然气 管道 运输作为石油 和天然 气主要运输 方式 , 已建成 全 国性 的石油 天然气 长输 管道 干线 2 现 O
Ap l a i n o p i to fPCM n Oi a d Ga p ln si g c i l n d Pi ei e Te tn
W a g Yo g i n n me
( e oem E g e r gIs t eo Y FB ac , I O—P C, e a u ag4 7 0 ) P t l n i ei tu f O rn h SN r u n n n it Z E H n nP yn 5 0 1
第2 5卷 第 7期 21 0 1年 7月
化 工时 刊
Ch m ia I d s r i e e c l n u ty T m s
Vo125, . No. 7 Ju . 2 1 I7. 01
d i1 . 9 9 j i n 1 0 o :0 3 6 / . s .0 2—1 4 2 1 .7 0 4 s 5 X.0 1 0 . 1
ቤተ መጻሕፍቲ ባይዱ
00多 k 我 国 7 %的石油 和 9 %的天然气是通过管 道运输 的。管道运 输关 系经济命脉 , 0 m, 0 9 同时 也关 系到公共 安全。
P M 为油气长输管道防腐层检测 的主要 工具 , C 在管道检测 中得到了广泛应 用。介绍 了 P M在管道 防腐层质量 评定 、 C
管道 泄漏 点定位、 牺牲阳极查找等方 面的应 用。同时 , 根据现场经验 , 出了 P M使 用过程 中的建议与 注意事项 , 给 C 以 便更 好地 发挥 P M在管道检测 中的作用。 C 关键词 P M 管道 C 外防腐层 检测 应用
长输油气管道漏磁内检测技术研究

长输油气管道漏磁内检测技术研究摘要:长输油气管道漏磁内检测技术作为管道完整性管理的核心技术已经在管道检测工作中得到广泛应用,该技术可以对管道本体缺陷进行识别、定位和量化统计,是指导管道合理维修、开展管道完整性管理工作的重要手段,是管道运行安全的重要技术保障。
该文主要阐述漏磁内检技术及原理、漏磁检测应用等,该方法具有高精度、非破坏性、经济高效、安全可靠等特点,在长输油气管道完整性管理工作中得到广泛应用,对保障长输油气管道安全具有很高应用价值。
关键词:油气管道;漏磁内检测;技术引言长输油气管道在运行过程中由于受到多种因素的影响,在服役运行过程中难免会发生腐蚀、变形等问题,为了及时发现管道本体缺陷,以便管道企业科学合理的开展管道维修维护,避免因管道本体缺陷失效造成安全事故,需要通过内检测技术的支持来获取管道缺陷信息并开展修复整治,而长输油气管道内检测技术具有检测准确度高、对管道运行无影响等优点,被广泛应用于长输油气管道的安全管理中,是提升管道本质安全的一项重要技术支撑手段。
1 内检测方法管道内检测技术最早产生于上世纪 60 年代美国,漏磁通无损检测技术的成功运用开启了管道内检测技术的先河,发展至今已形成管道漏磁、管道超声波和管道涡流等内检测方法,是目前主要的内检测方法。
1.1漏磁检测检测器在管道内运行过程中,其携带的永久磁铁将管壁饱和磁化,管壁与钢刷、磁铁及铁心形成磁回路,当管壁没有缺陷时,磁力线在管道内均匀分布,形成匀强磁场,当管壁有缺陷时,磁力线在管壁扭曲,穿出管壁产生漏磁,磁感线被磁传感器采集,传感器模块探头将表征管道特征的磁场信号转化为电信号,经过信号集中分析处理实现检测,这些检测数据通过专业人员分析可得出管道缺陷信息。
1.2涡流检测涡流检测是以电磁场理论为基础的电磁无损探伤方法,其基本原理是利用通有交流电的线圈(励磁线圈%)产生交变的磁场,使被测金属管道表面产生涡流,而该涡流又会产生感应磁场作用于线圈,从而改变线圈的电参数,只要被测管道表面存在缺陷,就会使涡流环发生畸变,通过感受涡流变化的传感器(检测线圈)测定由励磁线圈激励起来的涡流大小、分布及其变化就可以获取被测管道的表面缺陷和腐蚀状况。
长输管道内检测数据比对方法
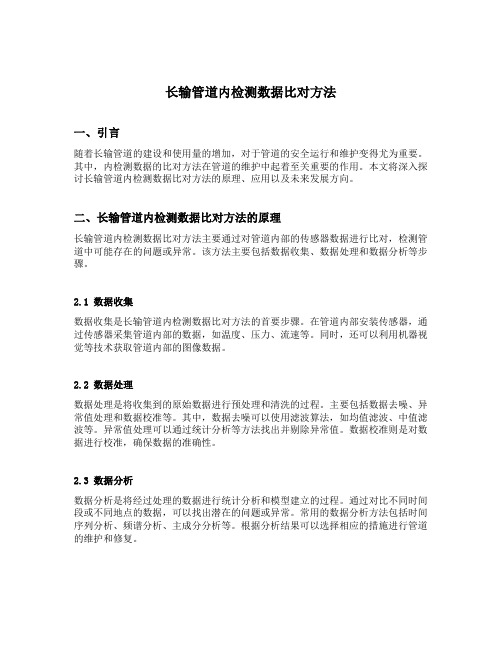
长输管道内检测数据比对方法一、引言随着长输管道的建设和使用量的增加,对于管道的安全运行和维护变得尤为重要。
其中,内检测数据的比对方法在管道的维护中起着至关重要的作用。
本文将深入探讨长输管道内检测数据比对方法的原理、应用以及未来发展方向。
二、长输管道内检测数据比对方法的原理长输管道内检测数据比对方法主要通过对管道内部的传感器数据进行比对,检测管道中可能存在的问题或异常。
该方法主要包括数据收集、数据处理和数据分析等步骤。
2.1 数据收集数据收集是长输管道内检测数据比对方法的首要步骤。
在管道内部安装传感器,通过传感器采集管道内部的数据,如温度、压力、流速等。
同时,还可以利用机器视觉等技术获取管道内部的图像数据。
2.2 数据处理数据处理是将收集到的原始数据进行预处理和清洗的过程。
主要包括数据去噪、异常值处理和数据校准等。
其中,数据去噪可以使用滤波算法,如均值滤波、中值滤波等。
异常值处理可以通过统计分析等方法找出并剔除异常值。
数据校准则是对数据进行校准,确保数据的准确性。
2.3 数据分析数据分析是将经过处理的数据进行统计分析和模型建立的过程。
通过对比不同时间段或不同地点的数据,可以找出潜在的问题或异常。
常用的数据分析方法包括时间序列分析、频谱分析、主成分分析等。
根据分析结果可以选择相应的措施进行管道的维护和修复。
三、长输管道内检测数据比对方法的应用长输管道内检测数据比对方法在管道的维护和检修中有着广泛的应用。
主要体现在以下几个方面:3.1 检测管道的漏损和腐蚀通过对比不同时期的数据,可以检测管道的漏损和腐蚀情况。
例如,对比两个时间段的压力数据,如果发现压力下降,则可能存在泄漏情况。
对比两个时间段的温度数据,如果发现温度上升,则可能存在腐蚀情况。
3.2 监测管道的运行状态通过对比不同地点或不同时间段的数据,可以监测管道的运行状态。
例如,对比不同地点的流速数据,可以查找是否存在流速异常的情况。
对比不同时间段的震动数据,可以判断管道是否存在振动问题。
漏磁内检测技术在集输管道检测中的应用

漏磁内检测技术在集输管道检测中的应用摘要:管道内检测不仅能清洁管道,提高输送效率和减少腐蚀性介质,而且还能有效地检出管道缺陷。
目前常采用的超声内检测检测精度高,但对管壁清洁度要求较高、需要耦合剂等,不适用于集输输气管道;电磁超声内检测检测精度高、检测缺陷类别多,不需要耦合剂,但国内应用较少且费用较高;CCTV摄像技术能通过图像信息识别缺陷,但不能对缺陷量化,只能识别内壁缺陷且易漏检;涡流内检测检测速度快,适应工况强,对表面缺陷检测灵敏度高,但是国内技术尚不成熟,量化精度相对不高,且对管道深层缺陷和外壁缺陷不敏感。
基于此,对漏磁内检测技术在集输管道检测中的应用进行研究,以供参考。
关键词:漏磁内检测;集输管道;分析引言2011年以来新建的高钢级油气管道,尤其是口径较大的输气管道,相继出现环焊缝失效事件,失效类型以开裂为主,因此环焊缝裂纹缺陷检测是天然气管道内检测的重点。
此外,随着管道口径、壁厚、管材等级的不断提高,对管道内检测技术也提出了更高的要求,内检测器的尺寸越大,自重越大,对其在管道中运行稳定性影响越大,可能引起局部速度波动,不同位置探头提离值不一致,进而影响缺陷检出概率和尺寸量化精度。
1管道漏磁内检测技术管道漏磁内检测技术利用漏磁内检测器上安装的强磁铁对管道壁进行饱和磁化,在管壁与漏磁内检测器之间形成磁回路,空气中的磁场信息被霍尔传感器接收,经过一系列转化生成可判读的漏磁内检测数据。
当管壁发生变化,如出现增厚、减薄、缺失等情况时,传感器接收到的磁场信息会发生变化,对应的漏磁内检测数据也会发生变化,据此判断缺陷及异常情况。
管道环焊缝由人工焊接而成,不同位置的增厚减薄情况不一致,因此漏磁信号极不规则。
2检测原理漏磁内检测技术是最早引入油气管道检测研究的一种技术,也是应用最广泛、技术最成熟的管体缺陷检测技术。
漏磁内检测的技术原理是通过测量被磁化的铁磁材料表面漏磁通量的大小来判断被测工件的缺陷程度。
- 1、下载文档前请自行甄别文档内容的完整性,平台不提供额外的编辑、内容补充、找答案等附加服务。
- 2、"仅部分预览"的文档,不可在线预览部分如存在完整性等问题,可反馈申请退款(可完整预览的文档不适用该条件!)。
- 3、如文档侵犯您的权益,请联系客服反馈,我们会尽快为您处理(人工客服工作时间:9:00-18:30)。
内检测技术在长输管道中的应用摘要:天然气和石油主要的运输方式是管道运输,在管道输运过程中管道安全是十分重要的,所以检测和保养护理是一个重要的任务,它直接关系着管道的使用寿命和安全,而管道的使用年限又受到自然地理等复杂环境的影响,如何细致精确的了解管道的腐蚀和使用情况,有针对性的对管道进行维修与护理,确保管道能够安全无危险的运行,延长管道的使用年限和寿命,是进行管道检测的根本目的。
关键词:管道;内检测;安全
在我国油气长输管道运输中,绝大多数的管道由于使用年限的延长,已到了服役的最终年限或已超过服役年限,这标志着我国石油天然气管道的使用情况已到了高危迸发阶段。
在加上近几年盗油分子猖獗的在管道上打孔盗油,造成了管道进一步的损坏和腐蚀,加大了管道事故的隐患,严重影响了管道运输的生产运行,造成国家和有关单位不必要的损失,直接影响了国家经济的发展和人民的日常生活,所以迫切的需要对油气管道全面的检测维护和评估,降低或减少事故的发生而造成的经济损失和一系列的环境问题,确保长输管道能够安全保质的安全运行。
确保管道大修的准确性,能够合理的利用管道修理费用减少资金的损失同时也避免重大事故的发生,为下一步的检修和维护提供科学的依据。
1、内检测技术长输管道中应用原理
在我国长运输管道检测技术中,多采用传统的管道外检测技术,通过对管道阴极电极的保护系统以及使用电子检测仪器进行常规
的检测,从而获得对管道腐蚀情况的了解,这种检测方式属于间接的检测管道腐蚀的方法。
而内检测技术是有目标性的对管道的内侧做检测,管道的变形检测仪器是针对内检测工作,其工作原理就是在正常介质输送的情况之下,利用介质的流动性推动管道变形检测器的运行,可以自动的检测出来管道直径的编号情况,利用介质的流动性推动管道变形检测器的运行,它可以自动的检测出管道直径的变化情况,同时处理系统对数据进行采集、记录和分析,探明管道内阀门、弯头、焊接处以及管道壁的厚度变化等情况,以及反馈问题管道所在的位置。
管道漏磁腐蚀检测器的原理主要是采用了无损检测原理,就是通过设备在管道中利用介质的流动性跟随着介质运行,能够在线检测出管道壁外腐蚀或内腐蚀而引起的管道的损坏情况,同时在检测管道壁时也能检测出管道机械的损伤情况。
这套检测设备的原理是自身携带着磁铁利用磁场回路的原理,在圆形管道的周长上产生磁场回路。
管道漏磁腐蚀检测器在管道中运行时如果管道壁没有缺陷和损坏,则磁力圈附着在管道壁内侧,如果管道壁内侧或外则出现缺陷和损坏,则磁力圈就会穿过管道壁向外发出磁场也就是说漏磁,从管道壁缺损处散发出来,这时紧贴在管道壁上的探头能检测的到,并产生感应信号,这些感应信号通过滤波和放大处理后记录
到检测器上并储存,再经过检测处理后对数据进行分析判断。
2、内检测技术在我国管道的应用
在近几年,我国管道局管道技术公司先后从德国和美国等一些技术比较先进的国家引进了一些不同规格的管道检测器,现在已经投入使用,取得了良好的社会效益和经济效益。
因此为了全面了解运输管道的管线情况,评价管道腐蚀控制措施,及时的排除事故的隐患、合理利用维修费用、实现科学化的管理,除了利用防腐层检测外我们还可以设计对大口径的管线进行内腐蚀检测,而内腐蚀检测就是通过管内介质的流动使检测设备跟随着介质运行,在线进行内检测,及时了解管壁的情况。
例如:96年10月对新疆输油管理局的彩南、火烧山和北三台全长138.85km、管壁8mm的φ273的原油管道进行了内检测。
检测的结果表明:壁厚减少了4.5mm,腐蚀点77处;减少了2.25~4.5mm 之间的腐蚀点234处;减少了2.25mm一下的腐蚀点307处。
经过挖管验证,检测的结果完全正确,就一个火烧山到北三台这段距离的管道节约了135万的维修费用,可见经济效益很明显。
在对新疆的验证后,97年又对乌鲁木齐到太原的油管进行了检测证实,只要对该石油管道适当的维修就可以用作天然气管线,不用重新另建管道,这样就节约了国家2亿多元的开支,节省了一年半的工期。
以及06年5月对大庆与哈尔滨输油管线实施的清管及漏磁腐蚀检测,通过检测分析发现腐蚀管线多为底部焊接附近,共发现损失4762
处,最严重的损失达管壁厚度的76%,腐蚀最严重的区间为4—8公里。
在中一站到中二战这段管道中共发现了6015损失处,最严重的损失度达到81%。
通过这些数据分析得出检测技术的应用能够使管道的运营得到大大的改善,同时减少了事故的发生与经济资源人力资源的浪费。
3、内检测技术应用产生良好效果
通过对管道线内检测技术的实施与应用,解决和排除了存在于管道线上的安全隐患,为管道线的维修与维护提供了准确的科学依据。
内检测腐蚀技术程度可以按一下标准划分:轻微腐蚀占壁厚的10%;轻度腐蚀占壁厚的10%~25%;中度腐蚀占壁厚的25%~50%;以及重度腐蚀 50% 以上。
在加强了内检测技术后最近这几年管道风险运行系数有了明显的下降。
经过试验验证,这些缺陷实际情况与检测数据分析结果相符,并且能够确定检测器检测的精确度,在通过对管道实际的检测可以看出,长输管线漏磁在线检测技术可以在不影响生产的情况下,准确的知道服役管道“完整性、安全性”的状况,可以预知管线不同区域的使用情况和剩余的使用寿命。
对服役的管道有一个充分的了解,对维修和维护做好准备,视情况有针对性的进行维修。
大大降低了经济损失和维修费用的支出,其经济效益和社会效益明显。
总之,现在国家采用了内检测技术,在管道维修设计中,减少了维修成本,降低了管道运行风险系数,同时也降低了人力资源的
使用,节约了不必要的浪费,延长了管道使用的年限,确保了安全生产。
(作者单位:中石油管道公司)
参考文献:
[1] 宋生奎,宫敬,才建等。
油气管道内检测技术研究进展[j],石油工程建设,2005,31(2)
[2] 范像红,王少华,那晶。
我国管道漏磁检测技术及其成就[j]石油科技论坛,2007,(4)
[3] 何宏,李琳,江秀汉,管道内腐蚀检测技术进展[j].西安石油学院学报:自然与科学版,2001,16(3).
[4] 孟庆宏,陈德林,胜利油田首次为海地管道“查体”[j].大众网—经济导报。
2010(06)。