机械加工里去毛刺有几种方法
11种去毛刺除毛刺方法选择
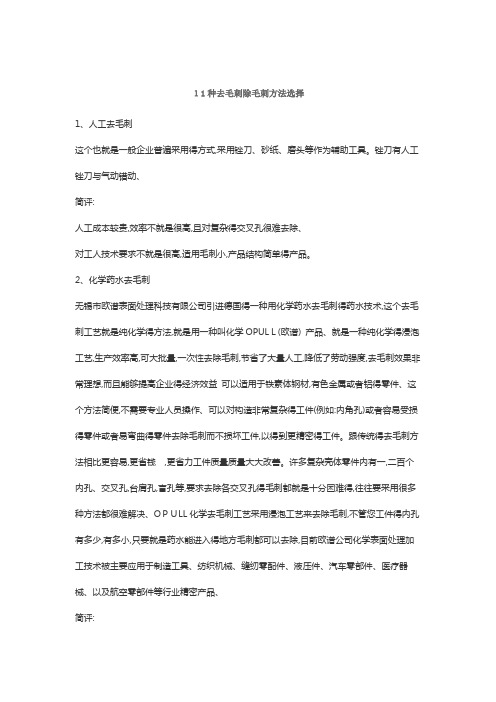
11种去毛刺除毛刺方法选择1、人工去毛刺这个也就是一般企业普遍采用得方式,采用锉刀、砂纸、磨头等作为辅助工具。
锉刀有人工锉刀与气动错动、简评:人工成本较贵,效率不就是很高,且对复杂得交叉孔很难去除、对工人技术要求不就是很高,适用毛刺小,产品结构简单得产品。
2、化学药水去毛刺无锡市欧谱表面处理科技有限公司引进德国得一种用化学药水去毛刺得药水技术,这个去毛刺工艺就是纯化学得方法,就是用一种叫化学OPULL(欧谱) 产品、就是一种纯化学得浸泡工艺,生产效率高,可大批量,一次性去除毛刺,节省了大量人工,降低了劳动强度,去毛刺效果非常理想,而且能够提高企业得经济效益可以适用于铁素体钢材,有色金属或者铝得零件、这个方法简便,不需要专业人员操作、可以对构造非常复杂得工件(例如:内角孔)或者容易受损得零件或者易弯曲得零件去除毛刺而不损坏工件,以得到更精密得工件。
跟传统得去毛刺方法相比更容易,更省钱,更省力工件质量质量大大改善。
许多复杂壳体零件内有一,二百个内孔、交叉孔,台肩孔,盲孔等,要求去除各交叉孔得毛刺都就是十分困难得,往往要采用很多种方法都很难解决、OPULL化学去毛刺工艺采用浸泡工艺来去除毛刺,不管您工件得内孔有多少,有多小,只要就是药水能进入得地方毛刺都可以去除,目前欧谱公司化学表面处理加工技术被主要应用于制造工具、纺织机械、缝纫零配件、液压件、汽车零部件、医疗器械、以及航空零部件等行业精密产品、简评:生产效率高,可大批量,一次性去除毛刺,节省了大量人工,降低了劳动强度,去毛刺效果非常理想,而且能够提高企业得经济效益?、3、冲模去毛刺采用制作冲模配合冲床进行去毛刺。
简评:需要一定得冲模(粗模+精冲模)制作费,可能还需要制作整形模、适合分型面较简单得产品,效率及去毛刺效果比人工佳。
4、研磨去毛刺此类去毛刺包含振动、喷砂、滚筒等方式,目前企业采用较多、简评:存在去除不就是很干净得问题,可能需要后续人工处理残余毛刺或者配合其她方式去毛刺。
壳体类零件机械加工去毛刺改进方案

壳体类零件机械加工去毛刺改进方案摘要:壳体零件具有结构复杂、加工精度高的特点,随着先进制造技术的应用与推广,制造业的竞争日益激烈,客户对于产品的质量要求和加工效率也日益提高,但我们的去毛刺方法仍停留在使用锉刀、固结砂轮、铲刀、钢丝刷、针刷、砂带及油石等带磨料的工具,使用手工方法去除产品加工部位的毛刺。
目前,该方法已经远远不能满足客户的需求,各加工企业也逐渐认识到去毛刺是提高壳体清洁度的一个重要环节,如何提升去毛刺效果和质量成为一个重要课题,去毛刺的效果对于产品的最终加工质量和外观质量至关重要。
据调查,目前清洁度控制的重要环节,可以通过主动去毛刺技术,去除加工过程中产生的毛刺,提升零件的加工质量,避免毛刺引起的清洁度问题。
关键词:壳体类;去毛刺;清洁度1 传统的去毛刺方法壳体零件在制造过程中,加工面的交接处总会产生毛刺或飞边。
去毛刺的内容主要就是清除壳体零件在加工部位周围所形成的刺状物或飞边。
对于壳体零件而言,主要的加工特征为孔、面和槽,毛刺主要存在于这些特征的边缘。
传统的去毛刺方法比较落后,加工效率低,直接影响产品的交付周期及加工质量。
2 壳体毛刺的分类按照对切削过程中毛刺的外观形态及尺寸的要求,将加工过程中的毛刺按照大小划分为微小毛刺、小毛刺和大毛刺。
3 机械加工去毛刺方法机械加工是毛刺产生的源头,同时也是毛刺控制的关键点。
为了进一步提高毛刺去除的加工质量,确保零件的加工效率,采用数控加工的方式,更利于保证壳体零件的加工质量。
按照毛刺大小的划分方法,遵循毛刺从大到小、从小到无的原则进行逐级控制和去除。
对壳体毛刺控制的基本原则:首先,必须消除加工过程中产生的大毛刺,减少小、微毛刺的产生,这样才能减少后期毛刺去除工作量;其次,在加工过程中刀具必须锋利,使得切削过程中不会产生大毛刺,当出现大毛刺时,应及时更换刀具,确保毛刺的大小在可控制范围内;最后,在加工过程中,应遵循一定的加工原则,确保毛刺的产生方向在有利于去除的部位。
打磨去毛刺方案
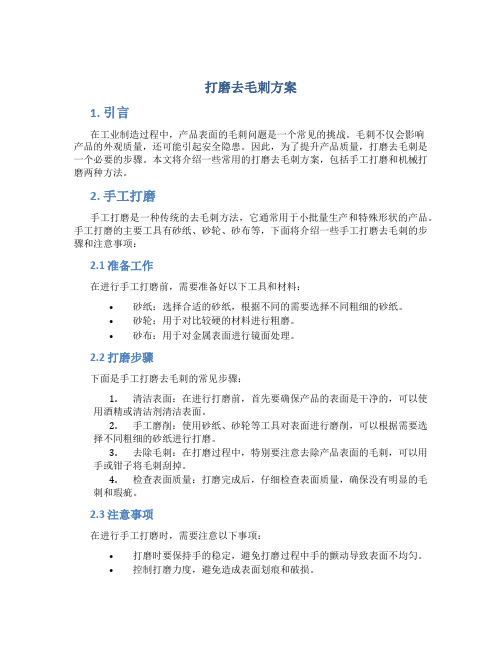
打磨去毛刺方案1. 引言在工业制造过程中,产品表面的毛刺问题是一个常见的挑战。
毛刺不仅会影响产品的外观质量,还可能引起安全隐患。
因此,为了提升产品质量,打磨去毛刺是一个必要的步骤。
本文将介绍一些常用的打磨去毛刺方案,包括手工打磨和机械打磨两种方法。
2. 手工打磨手工打磨是一种传统的去毛刺方法,它通常用于小批量生产和特殊形状的产品。
手工打磨的主要工具有砂纸、砂轮、砂布等,下面将介绍一些手工打磨去毛刺的步骤和注意事项:2.1 准备工作在进行手工打磨前,需要准备好以下工具和材料:•砂纸:选择合适的砂纸,根据不同的需要选择不同粗细的砂纸。
•砂轮:用于对比较硬的材料进行粗磨。
•砂布:用于对金属表面进行镜面处理。
2.2 打磨步骤下面是手工打磨去毛刺的常见步骤:1.清洁表面:在进行打磨前,首先要确保产品的表面是干净的,可以使用酒精或清洁剂清洁表面。
2.手工磨削:使用砂纸、砂轮等工具对表面进行磨削,可以根据需要选择不同粗细的砂纸进行打磨。
3.去除毛刺:在打磨过程中,特别要注意去除产品表面的毛刺,可以用手或钳子将毛刺刮掉。
4.检查表面质量:打磨完成后,仔细检查表面质量,确保没有明显的毛刺和瑕疵。
2.3 注意事项在进行手工打磨时,需要注意以下事项:•打磨时要保持手的稳定,避免打磨过程中手的颤动导致表面不均匀。
•控制打磨力度,避免造成表面划痕和破损。
•定期更换砂纸、砂轮等工具,保持其良好的工作状态。
3. 机械打磨机械打磨是一种自动化的去毛刺方法,它适用于大批量生产和产品形状相对规则的情况。
常见的机械打磨设备有研磨机、抛光机等,下面将介绍一些机械打磨去毛刺的步骤和注意事项:3.1 设备选择根据产品的形状和材料特性,选择合适的机械打磨设备,例如研磨机适用于对较硬材料进行粗磨,抛光机适用于对金属表面进行光洁处理。
3.2 打磨步骤下面是机械打磨去毛刺的常见步骤:1.准备工作:清洁产品表面,确保没有灰尘和污染物。
2.调整机械设备:根据产品的尺寸和要求,调整机器的转速、进给速度等参数。
数控机床加工中的材料去毛刺技巧
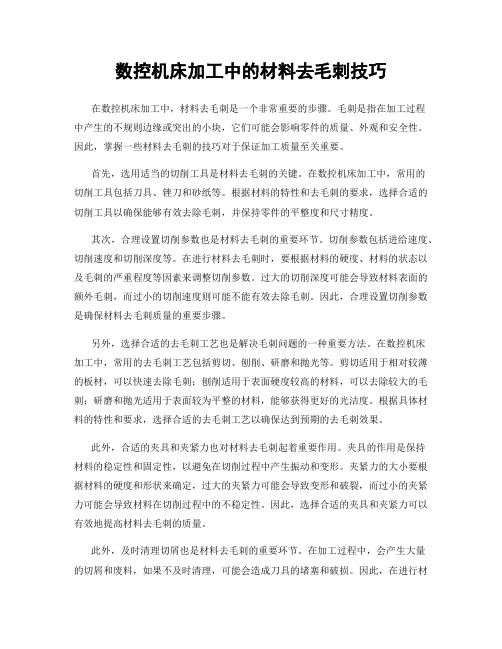
数控机床加工中的材料去毛刺技巧在数控机床加工中,材料去毛刺是一个非常重要的步骤。
毛刺是指在加工过程中产生的不规则边缘或突出的小块,它们可能会影响零件的质量、外观和安全性。
因此,掌握一些材料去毛刺的技巧对于保证加工质量至关重要。
首先,选用适当的切削工具是材料去毛刺的关键。
在数控机床加工中,常用的切削工具包括刀具、锉刀和砂纸等。
根据材料的特性和去毛刺的要求,选择合适的切削工具以确保能够有效去除毛刺,并保持零件的平整度和尺寸精度。
其次,合理设置切削参数也是材料去毛刺的重要环节。
切削参数包括进给速度、切削速度和切削深度等。
在进行材料去毛刺时,要根据材料的硬度、材料的状态以及毛刺的严重程度等因素来调整切削参数。
过大的切削深度可能会导致材料表面的额外毛刺,而过小的切削速度则可能不能有效去除毛刺。
因此,合理设置切削参数是确保材料去毛刺质量的重要步骤。
另外,选择合适的去毛刺工艺也是解决毛刺问题的一种重要方法。
在数控机床加工中,常用的去毛刺工艺包括剪切、刨削、研磨和抛光等。
剪切适用于相对较薄的板材,可以快速去除毛刺;刨削适用于表面硬度较高的材料,可以去除较大的毛刺;研磨和抛光适用于表面较为平整的材料,能够获得更好的光洁度。
根据具体材料的特性和要求,选择合适的去毛刺工艺以确保达到预期的去毛刺效果。
此外,合适的夹具和夹紧力也对材料去毛刺起着重要作用。
夹具的作用是保持材料的稳定性和固定性,以避免在切削过程中产生振动和变形。
夹紧力的大小要根据材料的硬度和形状来确定,过大的夹紧力可能会导致变形和破裂,而过小的夹紧力可能会导致材料在切削过程中的不稳定性。
因此,选择合适的夹具和夹紧力可以有效地提高材料去毛刺的质量。
此外,及时清理切屑也是材料去毛刺的重要环节。
在加工过程中,会产生大量的切屑和废料,如果不及时清理,可能会造成刀具的堵塞和破损。
因此,在进行材料去毛刺时,要及时清理切屑,以保持切削过程的顺畅进行,并确保材料去毛刺的质量。
去毛刺工艺

毛刺去除作业规范
1、目的
规范作业动作,提高工作效率,确保产品品质和人员安全2、适用范围:
各车间生产部门
3、作业内容
毛刺的判定:手摸无扎手刺手感。
去毛刺工具:锉刀,刮刀,倒角刀,倒角机等
去毛刺作业方法; 1、当产品毛边超规需去毛边,首先考虑用倒角机,若毛边少只需适用锉刀捎带一下时,小工件用锉刀45°锉除,较长工件则用刮刀从起点至终点一次完成,不可断断续续导致出现锯齿,毛边不顺滑等不良
2、使用锉刀去边时,锉刀与产品毛边成45°来回一次降毛边去好,不能中途停顿,断断续续,这样会将产品边缘锉成锯齿不光滑而影响产品品质,确保无刮手感觉。
4、主要职责与权限
上道工序交于下道工序时,必须确保本工序加工部分无毛刺毛边
即日起施行,请各位认真贯彻执行。
三山海口
2014-07-05。
巧去机械加工毛刺
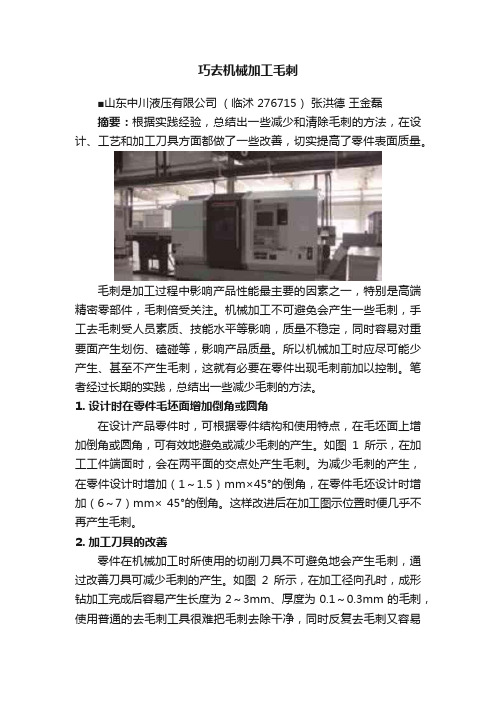
巧去机械加工毛刺■山东中川液压有限公司(临沭 276715)张洪德王金磊摘要:根据实践经验,总结出一些减少和清除毛刺的方法,在设计、工艺和加工刀具方面都做了一些改善,切实提高了零件表面质量。
毛刺是加工过程中影响产品性能最主要的因素之一,特别是高端精密零部件,毛刺倍受关注。
机械加工不可避免会产生一些毛刺,手工去毛刺受人员素质、技能水平等影响,质量不稳定,同时容易对重要面产生划伤、磕碰等,影响产品质量。
所以机械加工时应尽可能少产生、甚至不产生毛刺,这就有必要在零件出现毛刺前加以控制。
笔者经过长期的实践,总结出一些减少毛刺的方法。
1. 设计时在零件毛坯面增加倒角或圆角在设计产品零件时,可根据零件结构和使用特点,在毛坯面上增加倒角或圆角,可有效地避免或减少毛刺的产生。
如图1所示,在加工工件端面时,会在两平面的交点处产生毛刺。
为减少毛刺的产生,在零件设计时增加(1~1.5)mm×45°的倒角,在零件毛坯设计时增加(6~7)mm× 45°的倒角。
这样改进后在加工图示位置时便几乎不再产生毛刺。
2. 加工刀具的改善零件在机械加工时所使用的切削刀具不可避免地会产生毛刺,通过改善刀具可减少毛刺的产生。
如图2所示,在加工径向孔时,成形钻加工完成后容易产生长度为2~3mm、厚度为0.1~0.3mm的毛刺,使用普通的去毛刺工具很难把毛刺去除干净,同时反复去毛刺又容易划伤内孔表面,造成工件报废。
经过反复试验验证,设计了钻尖尾部为180°的成形钻来加工图示工件的径向孔。
改善后的刀具加工完成的工件,交叉孔处产生较小毛刺,用毛刷就能轻松去除,适用于大批量零件生产使用。
图1图23. 改善加工工艺零件的加工工艺也是影响毛刺产生的很重要的因素,合理的加工工艺能减少毛刺的产生,例如一些交叉孔较多的阀体、阀块等零件的加工,合理的孔加工顺序能有效地减少毛刺的产生。
如图3所示,改善前的孔加工顺序为①→②→③,在孔③加工完成后就容易在图示位置产生毛刺,且较难去除,影响零件的质量。
浅谈机械零件去毛刺工艺
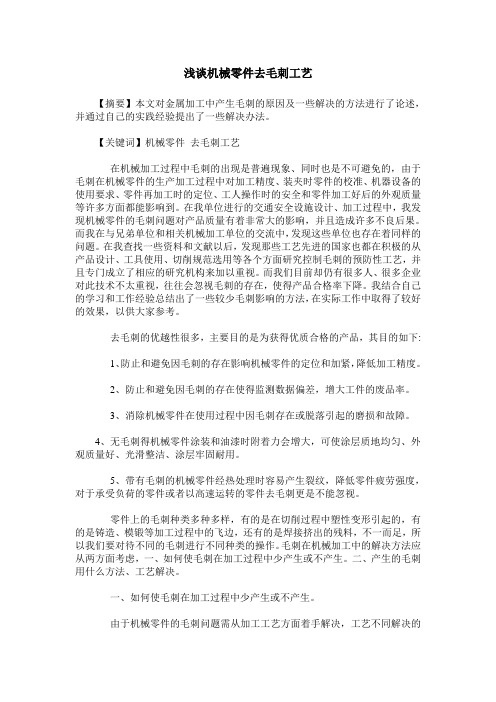
浅谈机械零件去毛刺工艺【摘要】本文对金属加工中产生毛刺的原因及一些解决的方法进行了论述,并通过自己的实践经验提出了一些解决办法。
【关键词】机械零件去毛刺工艺在机械加工过程中毛刺的出现是普遍现象、同时也是不可避免的,由于毛刺在机械零件的生产加工过程中对加工精度、装夹时零件的校准、机器设备的使用要求、零件再加工时的定位、工人操作时的安全和零件加工好后的外观质量等许多方面都能影响到。
在我单位进行的交通安全设施设计、加工过程中,我发现机械零件的毛刺问题对产品质量有着非常大的影响,并且造成许多不良后果。
而我在与兄弟单位和相关机械加工单位的交流中,发现这些单位也存在着同样的问题。
在我查找一些资料和文献以后,发现那些工艺先进的国家也都在积极的从产品设计、工具使用、切削规范选用等各个方面研究控制毛刺的预防性工艺,并且专门成立了相应的研究机构来加以重视。
而我们目前却仍有很多人、很多企业对此技术不太重视,往往会忽视毛刺的存在,使得产品合格率下降。
我结合自己的学习和工作经验总结出了一些较少毛刺影响的方法,在实际工作中取得了较好的效果,以供大家参考。
去毛刺的优越性很多,主要目的是为获得优质合格的产品,其目的如下:1、防止和避免因毛刺的存在影响机械零件的定位和加紧,降低加工精度。
2、防止和避免因毛刺的存在使得监测数据偏差,增大工件的废品率。
3、消除机械零件在使用过程中因毛刺存在或脱落引起的磨损和故障。
4、无毛刺得机械零件涂装和油漆时附着力会增大,可使涂层质地均匀、外观质量好、光滑整洁、涂层牢固耐用。
5、带有毛刺的机械零件经热处理时容易产生裂纹,降低零件疲劳强度,对于承受负荷的零件或者以高速运转的零件去毛刺更是不能忽视。
零件上的毛刺种类多种多样,有的是在切削过程中塑性变形引起的,有的是铸造、模锻等加工过程中的飞边,还有的是焊接挤出的残料,不一而足,所以我们要对待不同的毛刺进行不同种类的操作。
毛刺在机械加工中的解决方法应从两方面考虑,一、如何使毛刺在加工过程中少产生或不产生。
机械生产零件加工如何去掉毛刺
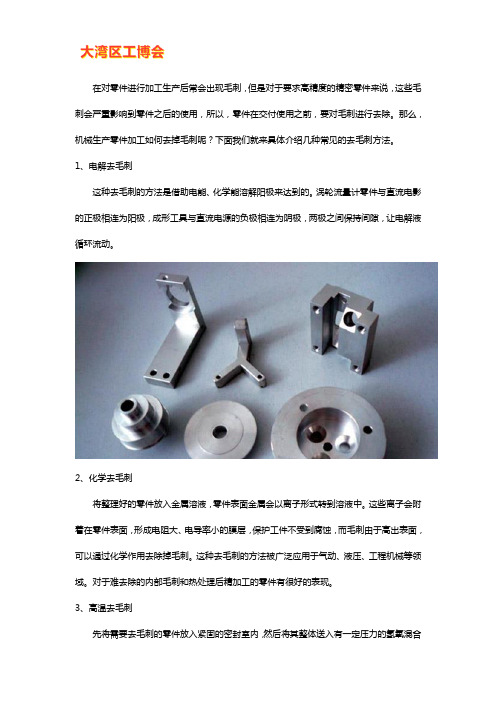
在对零件进行加工生产后常会出现毛刺,但是对于要求高精度的精密零件来说,这些毛刺会严重影响到零件之后的使用,所以,零件在交付使用之前,要对毛刺进行去除。
那么,机械生产零件加工如何去掉毛刺呢?下面我们就来具体介绍几种常见的去毛刺方法。
1、电解去毛刺这种去毛刺的方法是借助电能、化学能溶解阳极来达到的。
涡轮流量计零件与直流电影的正极相连为阳极,成形工具与直流电源的负极相连为阴极,两极之间保持间隙,让电解液循环流动。
2、化学去毛刺将整理好的零件放入金属溶液,零件表面金属会以离子形式转到溶液中。
这些离子会附着在零件表面,形成电阻大、电导率小的膜层,保护工件不受到腐蚀,而毛刺由于高出表面,可以通过化学作用去除掉毛刺。
这种去毛刺的方法被广泛应用于气动、液压、工程机械等领域。
对于难去除的内部毛刺和热处理后精加工的零件有很好的表现。
3、高温去毛刺先将需要去毛刺的零件放入紧固的密封室内,然后将其整体送入有一定压力的氢氧混合气体中,点火使混合气体爆炸,放出热量,将零件的毛刺烧掉,不会伤及零件。
4、滚磨去毛刺将零件与磨料一同放入封闭的滚筒中,在滚筒转动的过程中,动态扭矩传感器、零件与磨料一起产生磨削,去除毛刺。
磨料可以用石英砂、木屑、氧化铝、陶瓷以及金属环等等。
5、手工去毛刺这种方法比较传统也是最费时、费力的。
主要是通过人工用钢锉、砂纸、磨头等工具进行打磨。
现在生产中最常用的是修边刀,它以逐步取代了这些传统的方法,使用起来更加简单方便,有效节约了成本,而且环保。
6、超声波去毛刺这种去毛刺的方法主要是通过超声波产生的超声能量注入液体中,振动处于稀疏状态的液体时,会撕裂成很小的空穴,这些空穴在破裂的时候产生的大气压瞬间压力去除掉零件上的毛刺。
超声波去毛刺并不适合所有的类型,它对于肉眼观察不到的围观毛刺有很好的表现,但是对于肉眼可见的、粘结性强的毛刺来说这种方法是行不通的。
- 1、下载文档前请自行甄别文档内容的完整性,平台不提供额外的编辑、内容补充、找答案等附加服务。
- 2、"仅部分预览"的文档,不可在线预览部分如存在完整性等问题,可反馈申请退款(可完整预览的文档不适用该条件!)。
- 3、如文档侵犯您的权益,请联系客服反馈,我们会尽快为您处理(人工客服工作时间:9:00-18:30)。
机械加工里去毛刺有几种方法?
发布时间:2013-07-05 新闻来源:深圳艺卓公司
现如今随着各行业对毛刺去除是越来越重视,在CNC精密零件加工里毛刺这个小东西虽然不大,但却是直接影响到产品的品质所以,去毛刺的方法也层出不穷。
现在常用的修边 / 去毛刺主要有这么几种:
1. 手工去毛刺传统的方式是钢锉,砂纸,磨头打磨;而修边刀逐步取代了这些传统的方法,使用起来简单方便,不需要技术处理,节约成本并且环保。
2. 化学去毛刺。
用电化学反应原理,对金属材料制成的零件自动地、有选择地完成去毛刺作业。
它可广泛用于气动、液压、工程机械、油嘴油泵、汽车、发动机等行业不同金属材质的泵体、阀体、连杆、柱塞针阀偶件等零件的去毛刺加工。
适用于难于去除的内部毛刺、热处理后和精加工的零件。
3. 电解去毛刺利用电解作用去除金属零件毛刺的一种电解加工方法,英文简称 ECD 。
将工具阴极(一般用黄铜)固定放置在工件有毛刺的部位附近,两者相距一定的间隙(一般为 0.3 ~ 1 毫米)。
工具阴极的导电部分对准毛刺棱边,其他表面用绝缘层覆盖起来,使电解作用集中在毛刺部分。
加工时工具阴极接直流电源负极,工件接直流电源正极。
压力为 0.1 ~ 0.3 兆帕的低压电解液 ( 一般用硝酸钠或氯酸钠水溶液 ) 流过工件与阴极之间。
当接通直流电源后,毛刺便产生阳极溶解而被去除,被电解液带走。
电解液有一定腐蚀性,工件去毛刺后应经过清洗和防锈处理。
电解去毛刺适用于去除零件中隐蔽部位交叉孔或形状复杂零件的毛刺,生产效率高,去毛刺时间一般只需几秒至几十秒。
这种方法常用于齿轮、花键、连杆、阀体和曲轴油路孔口等去毛刺,以及尖角倒圆等。
缺点是零件毛刺的附近也受到电解作用,表面会失去原有光泽,甚至影响尺寸精度。