镜面加工
镜面加工
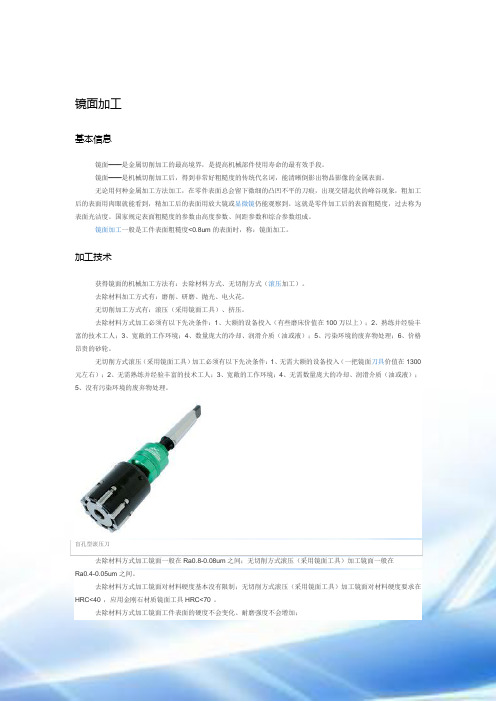
镜面加工基本信息镜面——是金属切削加工的最高境界,是提高机械部件使用寿命的最有效手段。
镜面——是机械切削加工后,得到非常好粗糙度的传统代名词,能清晰倒影出物品影像的金属表面。
无论用何种金属加工方法加工,在零件表面总会留下微细的凸凹不平的刀痕,出现交错起伏的峰谷现象,粗加工后的表面用肉眼就能看到,精加工后的表面用放大镜或显微镜仍能观察到。
这就是零件加工后的表面粗糙度,过去称为表面光洁度。
国家规定表面粗糙度的参数由高度参数、间距参数和综合参数组成。
镜面加工一般是工件表面粗糙度<0.8um的表面时,称:镜面加工。
加工技术获得镜面的机械加工方法有:去除材料方式、无切削方式(滚压加工)。
去除材料加工方式有:磨削、研磨、抛光、电火花。
无切削加工方式有:滚压(采用镜面工具)、挤压。
去除材料方式加工必须有以下先决条件:1、大额的设备投入(有些磨床价值在100万以上);2、熟练并经验丰富的技术工人;3、宽敞的工作环境;4、数量庞大的冷却、润滑介质(油或液);5、污染环境的废弃物处理;6、价格昂贵的砂轮。
无切削方式滚压(采用镜面工具)加工必须有以下先决条件:1、无需大额的设备投入(一把镜面刀具价值在1300元左右);2、无需熟练并经验丰富的技术工人;3、宽敞的工作环境;4、无需数量庞大的冷却、润滑介质(油或液);5、没有污染环境的废弃物处理。
盲孔型滚压刀去除材料方式加工镜面一般在Ra0.8-0.08um之间;无切削方式滚压(采用镜面工具)加工镜面一般在Ra0.4-0.05um之间。
去除材料方式加工镜面对材料硬度基本没有限制;无切削方式滚压(采用镜面工具)加工镜面对材料硬度要求在HRC<40°,应用金刚石材质镜面工具HRC<70°。
去除材料方式加工镜面工件表面的硬度不会变化、耐磨强度不会增加;优点无切削方式滚压(采用镜面工具)加工镜面有以下优点:1、提高表面粗糙度,粗糙度基本能达到Ra≤0.08um左右。
镜面cnc加工的原理

镜面cnc加工的原理
镜面CNC加工的原理主要有:
1. 精密数控系统
采用Closed Loop反馈系统,实时监控主轴转速、进给速率等参数,确保加工精度。
2. 高速主轴
主轴采用气浮或磁浮结构,转速高、噪音低、运转平稳,有利于镜面加工。
3. 刃具振动
利用振动切削原理,使刀具产生高频率低幅度振动,减少切削抖动,获得更精细表面。
4. 陶瓷刀具
使用陶瓷刀具,硬度高、热稳定性好,高速切削下仍保持切削刃锋利,确保加工质量。
5. 精密铣削
采用小步长、低进给速率进行精密镜面铣削,每次切削量小,去除金属微小,直至获得光洁表面。
6. 自动抛光
采用自动抛光装置,进行多级超精密抛光,以达到纳米级表面粗糙度。
7. 温控系统
加工区域设置恒温系统,防止温变导致工件尺寸误差。
综合运用上述技术手段,使镜面CNC加工达到精度控制在微米甚至纳米量级,实现工件镜面质量。
镜面加工合同协议书
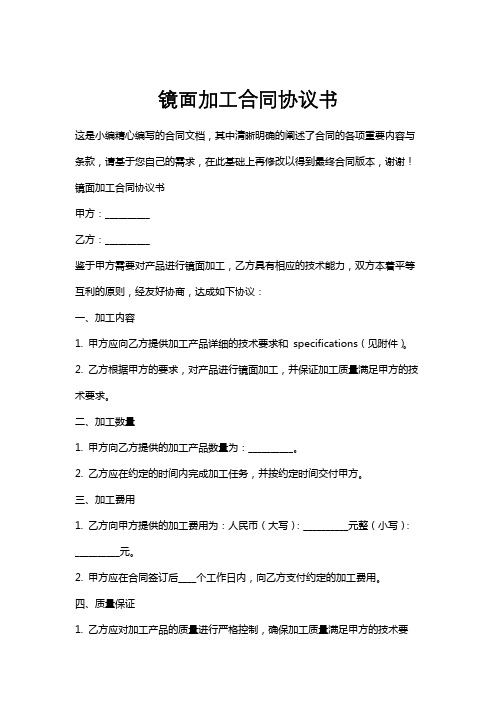
镜面加工合同协议书这是小编精心编写的合同文档,其中清晰明确的阐述了合同的各项重要内容与条款,请基于您自己的需求,在此基础上再修改以得到最终合同版本,谢谢!镜面加工合同协议书甲方:__________乙方:__________鉴于甲方需要对产品进行镜面加工,乙方具有相应的技术能力,双方本着平等互利的原则,经友好协商,达成如下协议:一、加工内容1. 甲方应向乙方提供加工产品详细的技术要求和 specifications(见附件)。
2. 乙方根据甲方的要求,对产品进行镜面加工,并保证加工质量满足甲方的技术要求。
二、加工数量1. 甲方向乙方提供的加工产品数量为:__________。
2. 乙方应在约定的时间内完成加工任务,并按约定时间交付甲方。
三、加工费用1. 乙方向甲方提供的加工费用为:人民币(大写):__________元整(小写):__________元。
2. 甲方应在合同签订后____个工作日内,向乙方支付约定的加工费用。
四、质量保证1. 乙方应对加工产品的质量进行严格控制,确保加工质量满足甲方的技术要求。
2. 乙方应在加工完成后,提供产品质量检测报告,以确保加工产品质量。
五、交付及验收1. 乙方应按照约定的时间、地点和方式,向甲方交付加工产品。
2. 甲方应在收到加工产品后,按照约定的时间、地点和方式,对加工产品进行验收。
3. 如甲方对加工产品质量有异议,应在验收合格后____个工作日内,书面通知乙方,并提供详细的技术检测报告。
乙方应在收到异议通知后,根据甲方的要求进行处理。
六、违约责任1. 如乙方未按照约定的时间、地点和方式,交付加工产品,甲方有权要求乙方支付违约金,违约金为加工费用的____%。
2. 如甲方未按照约定的时间、地点和方式,向乙方支付加工费用,乙方有权拒绝交付加工产品,并要求甲方支付逾期付款违约金,违约金为应付款项的____%。
七、争议解决1. 本合同的签订、履行、解释及争议解决均适用中华人民共和国法律。
注塑 镜面加工工艺

注塑镜面加工工艺
注塑镜面加工工艺是指在注塑成型过程中对塑料制品进行表面镜面处理的工艺。
注塑是一种塑料制品加工方法,通过将熔化的塑料注入模具中,经过冷却后形成所需的塑料制品。
而镜面加工则是对塑料制品表面进行抛光和处理,使其具有光滑、平整、反光等特性。
在注塑镜面加工工艺中,首先需要选择适合镜面加工的塑料原料,如PC(聚碳酸酯)、PMMA(聚甲基丙烯酸甲酯)等具有良好透明度和抗刮擦性能的塑料。
其次,在注塑成型过程中,需要控制好注塑温度、压力和速度等参数,以确保塑料充分填充模具并保持表面光滑。
另外,模具的设计和制造也对镜面加工起着至关重要的作用,模具表面的光洁度和精度会直接影响最终制品的表面质量。
在注塑成型后,进行镜面加工时通常会经过以下步骤,首先是去除注塑制品表面的毛刺和瑕疵,可以采用打磨、抛光等方法进行处理;然后进行表面镜面处理,常用的方法包括喷涂、真空镀膜、光学膜等,以提高制品的透明度和光泽度;最后进行质量检验,确保制品表面没有气泡、划痕等缺陷。
总的来说,注塑镜面加工工艺需要综合考虑原料选择、注塑成型、模具设计、表面处理等多个环节,以确保最终制品具有高质量的镜面效果。
这种工艺广泛应用于电子产品外壳、汽车灯具、家居用品等领域,为塑料制品赋予了更加美观和高端的外观。
内孔镜面加工工艺

内孔镜面加工工艺
内孔镜面加工工艺可以采用磨粒流抛光技术。
磨粒流抛光是一种纯物理抛光方式,利用弹性软磨料进行挤压研磨,提升内壁光洁度。
具体来说,弹性软磨料经过增压系统后,挤压进入工件孔内,进行精细研磨。
这种工艺可以兼顾效率与成本,比如一些拉拔模具内孔抛光非常费时,而采用磨粒流抛光可以在5分钟内将拉拔模具内孔研磨至镜面状态,公差损失小(1-2个μ),抛光效果均匀,且可现场试样。
如需更多与内孔镜面加工工艺相关的信息,建议咨询专业技术人员或查阅相关论坛。
金刚石刀具镜面加工工艺流程

金刚石刀具镜面加工工艺流程英文回答:Diamond tool mirror processing is a complex and precise process that requires careful planning and execution. The process involves several steps, including rough grinding, fine grinding, polishing, and final finishing. Each step plays a crucial role in achieving the desired mirror-like finish on diamond tools.The first step in the process is rough grinding. This involves using a coarse diamond grinding wheel to remove excess material and shape the tool. The rough grinding stage is essential for creating the initial shape of the tool and removing any imperfections or irregularities.After rough grinding, the tool moves on to the fine grinding stage. This step involves using a finer diamond grinding wheel to further refine the shape and surface of the tool. Fine grinding helps to smooth out any remainingroughness and prepares the tool for the polishing stage.Polishing is the next step in the process. It involves using a polishing pad or wheel with a diamond abrasive to create a smooth and reflective surface on the tool. Polishing is a critical step in achieving the desired mirror-like finish. It requires precision and careful control of pressure and speed to ensure a consistent and high-quality result.Finally, the tool undergoes final finishing. This step involves inspecting the tool for any remaining imperfections and making any necessary adjustments ortouch-ups. It may involve using finer polishing pads or wheels to achieve the desired level of smoothness and reflectivity.Overall, the process of diamond tool mirror processing requires skill, precision, and attention to detail. It is a combination of art and science, with each step contributing to the final result. By carefully following the process and using the right tools and techniques, a mirror-like finishcan be achieved on diamond tools.中文回答:金刚石刀具的镜面加工是一个复杂而精确的过程,需要仔细的规划和执行。
沙迪克火花机镜面加工的流程

沙迪克火花机镜面加工的流程沙迪克火花机是一种高精度加工设备,广泛应用于模具制造、航空航天等领域,其镜面加工能力尤为突出。
本文将介绍沙迪克火花机镜面加工的流程。
步骤一:准备工作在开始加工之前,需要对沙迪克火花机进行检查和准备。
首先,检查设备的电气和机械系统是否正常,是否配备了合适的加工刀具、夹具和夹具螺丝等。
其次,需在工件表面涂上导电涂层,以便在加工过程中形成放电通路。
步骤二:设定参数设定参数是进行加工前的重要步骤,它直接决定加工效果和工件质量。
首先,需要设定沙迪克火花机的加工路径、放电频率、电压和脉冲持续时间等参数。
其次,还需根据工件的材料、形状和表面粗糙度等因素,灵活地调整加工参数。
步骤三:加工操作加工操作是整个加工流程中最核心的环节。
在加工过程中,需严格按照设定参数进行操作,精细调整每一步参数。
首先,将待加工的工件固定到加工台上,并使用夹具进行固定。
然后,启动沙迪克火花机,并让它按照设定路径进行加工。
在加工过程中,需要时刻观察加工状态,检查工件表面的粗糙度和形状是否符合要求。
如果发现加工过程中出现了问题,需要及时调整加工参数或对工件进行修整。
步骤四:清洁和检验加工完成后,需要对工件进行清洁和检验。
首先,使用除油剂清洗工件表面上的导电涂层和松动的金属屑。
然后,使用高精度测量仪器对工件进行检验,检查工件表面平整度、光洁度和尺寸精度等指标是否满足要求。
结论沙迪克火花机镜面加工是一种高效、精度极高的加工方式,广泛应用于模具制造、航空航天等领域。
加工过程中,需要严格遵守加工流程和设定参数,确保加工质量和效率。
一种椭球反射镜面加工流程

一种椭球反射镜面加工流程First of all, the process of machining ellipsoidal reflector mirrors involves several steps that are crucial to achieving the desired outcome. 首先,椭球反射镜面加工过程涉及多个关键步骤,对于实现理想的效果至关重要。
One of the initial steps is to select the appropriate material for the mirror, taking into consideration factors such as the desired reflectivity, durability, and overall quality. 最初的步骤之一是选择适合镜面的材料,考虑到诸如所需的反射率、耐久性和总体质量等因素。
The material chosen will have a significant impact on the performance and effectiveness of the final mirror product. 所选择的材料将对最终镜面产品的性能和效果产生重要影响。
Once the material is selected, the next step is to shape and mold the mirror into the desired ellipsoidal form. 选定材料后,下一步是将镜面塑造成期望的椭圆形状。
This process can be challenging, requiring precision and attention to detail to ensure the mirror's shape meets the necessary specifications. 这个过程可能具有挑战性,需要精确和细致的工作,以确保镜面的形状符合必要的规格要求。
- 1、下载文档前请自行甄别文档内容的完整性,平台不提供额外的编辑、内容补充、找答案等附加服务。
- 2、"仅部分预览"的文档,不可在线预览部分如存在完整性等问题,可反馈申请退款(可完整预览的文档不适用该条件!)。
- 3、如文档侵犯您的权益,请联系客服反馈,我们会尽快为您处理(人工客服工作时间:9:00-18:30)。
镜面加工基本信息镜面——是金属切削加工的最高境界,是提高机械部件使用寿命的最有效手段。
镜面——是机械切削加工后,得到非常好粗糙度的传统代名词,能清晰倒影出物品影像的金属表面。
无论用何种金属加工方法加工,在零件表面总会留下微细的凸凹不平的刀痕,出现交错起伏的峰谷现象,粗加工后的表面用肉眼就能看到,精加工后的表面用放大镜或显微镜仍能观察到。
这就是零件加工后的表面粗糙度,过去称为表面光洁度。
国家规定表面粗糙度的参数由高度参数、间距参数和综合参数组成。
镜面加工一般是工件表面粗糙度<0.8um的表面时,称:镜面加工。
加工技术获得镜面的机械加工方法有:去除材料方式、无切削方式(滚压加工)。
去除材料加工方式有:磨削、研磨、抛光、电火花。
无切削加工方式有:滚压(采用镜面工具)、挤压。
去除材料方式加工必须有以下先决条件:1、大额的设备投入(有些磨床价值在100万以上);2、熟练并经验丰富的技术工人;3、宽敞的工作环境;4、数量庞大的冷却、润滑介质(油或液);5、污染环境的废弃物处理;6、价格昂贵的砂轮。
无切削方式滚压(采用镜面工具)加工必须有以下先决条件:1、无需大额的设备投入(一把镜面刀具价值在1300元左右);2、无需熟练并经验丰富的技术工人;3、宽敞的工作环境;4、无需数量庞大的冷却、润滑介质(油或液);5、没有污染环境的废弃物处理。
去除材料方式加工镜面一般在Ra0.8-0.08um之间;无切削方式滚压(采用镜面工具)加工镜面一般在Ra0.4-0.05um之间。
去除材料方式加工镜面对材料硬度基本没有限制;无切削方式滚压(采用镜面工具)加工镜面对材料硬度要求在HRC<40°,应用金刚石材质镜面工具HRC<70°。
去除材料方式加工镜面工件表面的硬度不会变化、耐磨强度不会增加;优点无切削方式滚压(采用镜面工具)加工镜面有以下优点:1、提高表面粗糙度,粗糙度基本能达到Ra≤0.08um左右。
2、修正圆度,椭圆度可≤0.01mm。
3、提高表面硬度,使受力变形消除,硬度提高HV≥40°4、加工后有残余应力层,提高疲劳强度提高30%。
5、提高配合质量,减少磨损,延长零件使用寿命,但零件的加工费用反而降低。
转载别人的镜面粗糙度说说表面粗糙度的计算,以及"镜面效果" 表面粗糙度现在越来越受到各行业的重视,论坛里也经常问及如何提高表面粗糙度的帖子.今天讲一下关于车削的表面粗糙度.图片上面有车削表面粗糙度的计算方式,只需要将切削参数代入即可计算出可能最高的"表面粗糙度"(以下发言全部以粗糙度低为细,粗糙度高为粗)车削表面粗糙度=每转进给的平方*1000/刀尖R乘8以上计算方式是理论上的可能达到最坏的的效果,实际上因刀具品质、机床刚性精度、切削液、切削温度、切削速度、材料硬度等等原因,会将粗糙度提高或者降低的,如果你用上面的计算方式计算出来的粗糙度都不能满足想达到的效果,请先更改切削参数。
但进给一般和切深有着密切的关系,一般进给是切深的10%~20%之间,排削的效果是最好的切削深度,因为屑的宽度和厚度最合比例以上公式的各个参数我下面详细一项项解释一下对粗糙度的影响,如有不正请指点:1:进给——进给越大粗糙度越大,进给越大加工效率越高,刀具磨损越小,所以进给一般最后定,按照需要的粗糙度最后定出进给2:刀尖R——刀尖R越大,粗糙度越降低,但切削力会不断增大,对机床的刚性要求更高,对材料自身的刚性也要求越高。
建议一般切削钢件6150以下的车床不要使用R0.8以上的刀尖,而硬铝合金不要用R0.4以上的刀尖,否则车出的的真圆度、直线度等等形位公差都没办法保证了,就算能降低粗糙度也是枉然!3:切削时要计算设备功率,至于如何计算切削时所需要的功率(以电机KW的80%作为极限),下一帖再说。
要注意的时,现在大部分的数控车床都是使用变频电机的,变频电机的特点是转速越高扭力越大,转速越低扭力越小,所以计算功率是请把变频电机的KW除2比较保险。
而转速的高低又与切削时的线速度有密切关系,而传统的普车是用恒定转速/扭力的电机依靠机械变速来达到改变转速的效果,所以任何时候都是“100%最大扭力输出”,这点比变频电机好。
但当然如果你的主轴是由昂贵的恒定扭力伺服电机驱动,那是最完美的选择上面说得有点乱了,现在先举个例计算一下表面粗糙度:车削45号钢,切削速度150米,切深3mm,进给0.15,R尖R0.4,这是我很常用的中轻切削参数,基本上不是光洁度要求非常之高的工件一刀不分粗精切削直接车出表面,计算表面粗糙度等于0.15*0.15/0.4/8*1000=粗糙度7.0(单位微米)。
如果有要求光洁度要到0.8的话,切削参数变化如下:刀具不变依旧上面0.4的刀片,切削参数进给0.05,切深要视乎刀具的断削槽而定,通常如果进给定了,那切深只会在一个很窄的范围(上面不是说过切深和进给很大关系嘛)——当切深在一定范围之内才会有最良好的排屑效果!当然你不介意拿个沟子一边车一边沟屑的话又另当别论!:lol我大约会按照进给的10倍起定切深,也就是0.5mm,此时0.05*0.05/0.4/8*1000=0.78微米,也就是粗糙度达到0.8了。
至于粗糙度的表示方法:RY是测量出最大粗糙度,RA是算术计法将整个工件的表面粗糙度平均算,而RZ则是取10点再平均算,一般同一工件用RA计算粗糙度应该是最低的,而RY肯定是最大的,如果用RY的计算公式可以达到比RA 要求更低的数字,基本上车出来就可以达到标注的RA要求了。
另外理论上带修光刃的刀具最大可能将粗糙度降低一半,如果上面车出0.8光洁度的工件用带修光刃的刀片粗糙度就最小可能是0.4以上是书本摘录的理论知识综合个人经验所书,以下再说说一些我个人感觉的理论,这些书本上我没见过的:1:车床可以达到的最小粗糙度,首要原因是主轴精度,按照最大粗糙度计算的方法,如果你的车床主轴跳动精度是0.002mm,也就是2微米跳动,那理论上是不可能加工出粗糙度会低于0.002毫米粗糙度(RY2.0)的工件,但这是最大可能值,一般平均下来算50%好了,粗糙度1.0的工件可以加工出!再结合RA的算法一般不会得出超过RY值的50%,变成RA0.5,再计算修光刃的作用降低50%,那最终主轴跳动0.002的车床极限是可以加工出RA0.2左右的工件!最后说说“镜面效果”,一般镜面效果在超“精密研磨”定义为RA0.01或者以下的工件,我见过很多次,各大机床展览时各大材料公司就会展示出这些表面研磨到和镜子肉眼看下去没任何区别的金属块,反正你回家把衣柜的镜子擦干净了,对着上面看看是什么样子就知道真正的镜面金属是啥样子了。
:lol :lol :lol 但这些是基本上磨床都没可能直接加工出——一般靠研,也就是抛光得到的。
磨床能直接加工出RA0.1以下的就算镜面了,车床、铣床能直接加工出RA0.5以下也算镜面了,现在论坛上关于镜面切削效果的帖子99%能低于RA1.0已经完全满足他们的镜面需求了9加工方法表面特征表面粗糙度(Ra)数值加工方法举例明显可见刀痕Ra100、Ra50、Ra25、粗车、粗刨、粗铣、钻孔微见刀痕Ra12.5、Ra6.3、Ra3.2、精车、精刨、精铣、粗铰、粗磨看不见加工痕迹,微辩加工方向Ra1.6、Ra0.8、Ra0.4、精车、精磨、精铰、研磨暗光泽面Ra0.2、Ra0.1、Ra0.05、研磨、珩磨、超精磨、抛光1、表面粗糙度(surface roughness)加工表面上具有的较小间距和峰谷所组成的微观几何形状特性。
它是互换性研究的问题之一。
表面粗糙度一般是由所采用的加工方法和其他因素所形成的,例如加工过程中刀具与零件表面间的摩擦、切屑分离时表面层金属的塑性变形以及工艺系统中的高频振动等。
由于加工方法和工件材料的不同,被加工表面留下痕迹的深浅、疏密、形状和纹理都有差别。
表面粗糙度与机械零件的配合性质、耐磨性、疲劳强度、接触刚度、振动和噪声等有密切关系,对机械产品的使用寿命和可靠性有重要影响。
一般标注采用Ra。
Ra(轮廓算术平均偏差):在取样长度L内轮廓偏距绝对值的算术平均值。
2、表面光洁度表面粗糙度的另一称法。
表面光洁度是按人的视觉观点提出来的,而表面粗糙度是按表面微观几何形状的实际提出来的。
80年代后,以为与国际标准(ISO)接轨,中国采用表面粗糙度而废止了表面光洁度.在表面粗糙度国家标准GB3505-83、GB1031-83颁布后,表面光洁度的已不再采用。
其实,两者主要是名字不同,且有相应的对照表.粗糙度有测量的计算公式,而光洁度只能用样板规对照,相对来说,用粗糙度表示更科学严谨了。
如何提高表面光洁度与表面粗糙度在机床上,用普通刀具将工件尺寸加工到基本到位后,再用豪克能金属表面加工设备的豪克能刀具代替原普通刀具再加工一遍,即可使被加工工件表面光洁度提高3级以上(粗糙度Ra值轻松达到0.2以下);且工件的表面显微硬度提高20%以上;并大大提高了工件的表面耐磨性和耐腐蚀性。
12表面光洁度与表面粗糙度对照表光洁度(旧标)粗糙度级别Ra(μm)Ra(μm)方案1方案2方案3▽140~805010080▽220~40255040表面状况=明显可见的刀痕加工方法=粗车、镗、刨、钻应用举例=粗加工后的表面,焊接前的焊缝、粗钻孔壁等▽310~2012.52520表面状况=可见刀痕加工方法=粗车、刨、铣、钻应用举例=一般非结合表面,如轴的端面、倒角、齿轮及皮带轮的侧面、键槽的非工作表面,减重孔眼表面▽45~10 6.312.510表面状况=可见加工痕迹加工方法=车、镗、刨、钻、铣、锉、磨、粗铰、铣齿应用举例=不重要零件的配合表面,如支柱、支架、外壳、衬套、轴、盖等的端面。
紧固件的自由表面,紧固件通孔的表面,内、外花键的非定心表面,不作为计量基准的齿轮顶圈圆表面等▽5 2.5~5 3.2 6.35表面状况=微见加工痕迹加工方法=车、镗、刨、铣、刮1~2点/cm^2、拉、磨、锉、滚压、铣齿应用举例=和其他零件连接不形成配合的表面,如箱体、外壳、端盖等零件的端面。
要求有定心及配合特性的固定支承面如定心的轴间,键和键槽的工作表面。
不重要的紧固螺纹的表面。
需要滚花或氧化处理的表面▽6 1.25~2.5 1.6 3.2 2.5表面状况=看不清加工痕迹加工方法=车、镗、刨、铣、铰、拉、磨、滚压、刮1~2点/cm^2铣齿应用举例=安装直径超过80mm的G级轴承的外壳孔,普通精度齿轮的齿面,定位销孔,V型带轮的表面,外径定心的内花键外径,轴承盖的定中心凸肩表面▽70.63~1.250.8 1.6 1.25表面状况=可辨加工痕迹的方向加工方法=车、镗、拉、磨、立铣、刮3~10点/cm^2、滚压应用举例=要求保证定心及配合特性的表面,如锥销与圆柱销的表面,与G级精度滚动轴承相配合的轴径和外壳孔,中速转动的轴径,直径超过80mm的E、D级滚动轴承配合的轴径及外壳孔,内、外花键的定心内径,外花键键侧及定心外径,过盈配合IT7级的孔(H7),间隙配合IT8~IT9级的孔(H8,H9),磨削的齿轮表面等▽80.32~0.630.40.80.63表面状况=微辨加工痕迹的方向加工方法=铰、磨、镗、拉、刮3~10点/cm^2、滚压应用举例=要求长期保持配合性质稳定的配合表面,IT7级的轴、孔配合表面,精度较高的齿轮表面,受变应力作用的重要零件,与直径小于80mm的E、D级轴承配合的轴径表面、与橡胶密封件接触的轴的表面,尺寸大于120mm的IT13~IT16级孔和轴用量规的测量表面▽90.16~0.320.20.40.32表面状况=不可辨加工痕迹的方向加工方法=布轮磨、磨、研磨、超级加工应用举例=工作时受变应力作用的重要零件的表面。