制氢装置转化炉简介及制氢原理
制氢装置工艺原理

制氢装置工艺原理2013-02-27 17:21:27| 分类:默认分类| 标签:制氢|举报|字号订阅⑴轻烃蒸汽转化反应①转化反应式转化反应是指水蒸汽和烃类进入转化炉炉管通过高温的催化剂作用,进行转化反应,生成H2、C0和CO2。
反应式: CnH2n +2+nH2O=nCO+(2n+1)H2 -Q CnH2n+2+2nH2O=nCO2+(3n+1)H2 -Q ②主要参数对转化反应的影响: A 反应压力转化反应是体积膨胀的反应,提高压力对平衡不利,压力增加,转化率会降低。
但在工业实践中,转化增压有以下好处:1) 转化增压可节省动力,对制氢来说,转化增压可节省加氢压缩机的动力消耗。
2) 转化增压可以提高设备能力,操作的空间速度可以大一些,催化剂的利用率可以提高,设备制造材料较省。
3) 转化增压可以提高过剩蒸汽的热效率。
转化反应需要过量的蒸汽,高压蒸汽温度高,在变换后可回收的热能,从而降低了生产成本。
但是,对于定型装置来说,压力却不可以任意提高,只是随着阻力降的增大,前部压力被迫逐步提高到设计值。
B 反应温度因为转化反应是吸热反应,因此提高温度不仅可以加快反应速度,而且有利于反应平衡,即可以多生成CO和H2,降低转化尾气中残余CH4的含量。
但是,提高温度受到转化炉管的材料的限制。
对本装置Cr25Ni35Nb离心浇铸炉管,设计管外壁温度不允许超过 910℃,因此只能在设计允许的出口气体温度 820℃左右的一定范围内加以调节。
相反,为了延长价格昂贵的转化管的寿命,还应在满足工业氢质量的前提下,尽量采用较低的出口温度。
C 空间速度空间速度一般是进料的碳空速。
碳空速是用碳流量除以催化剂的体积来表示的。
空速对每个转化炉来说都有一定的范围,空速太大时,由于原料在催化剂床层中停留的时间太短,转化不完全,甚至会发生重烃穿透床层、引起催化剂结碳;但碳空速太小时有可能有些烃类进料在各炉管中分配不均匀,会出现炉管温度不同的现象。
天然气制氢装置转化炉介绍
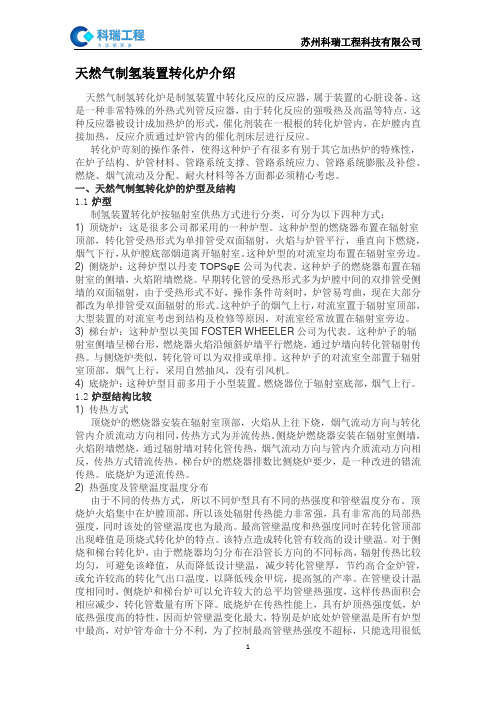
天然气制氢装置转化炉介绍天然气制氢转化炉是制氢装置中转化反应的反应器,属于装置的心脏设备。
这是一种非常特殊的外热式列管反应器,由于转化反应的强吸热及高温等特点,这种反应器被设计成加热炉的形式,催化剂装在一根根的转化炉管内,在炉膛内直接加热,反应介质通过炉管内的催化剂床层进行反应。
转化炉苛刻的操作条件,使得这种炉子有很多有别于其它加热炉的特殊性,在炉子结构、炉管材料、管路系统支撑、管路系统应力、管路系统膨胀及补偿、燃烧、烟气流动及分配、耐火材料等各方面都必须精心考虑。
一、天然气制氢转化炉的炉型及结构1.1 炉型制氢装置转化炉按辐射室供热方式进行分类,可分为以下四种方式:1) 顶烧炉:这是很多公司都采用的一种炉型。
这种炉型的燃烧器布置在辐射室顶部,转化管受热形式为单排管受双面辐射,火焰与炉管平行,垂直向下燃烧,烟气下行,从炉膛底部烟道离开辐射室。
这种炉型的对流室均布置在辐射室旁边。
2) 侧烧炉:这种炉型以丹麦TOPSφE公司为代表。
这种炉子的燃烧器布置在辐射室的侧墙,火焰附墙燃烧。
早期转化管的受热形式多为炉膛中间的双排管受侧墙的双面辐射,由于受热形式不好,操作条件苛刻时,炉管易弯曲,现在大部分都改为单排管受双面辐射的形式。
这种炉子的烟气上行,对流室置于辐射室顶部,大型装置的对流室考虑到结构及检修等原因,对流室经常放置在辐射室旁边。
3) 梯台炉:这种炉型以美国FOSTER WHEELER公司为代表。
这种炉子的辐射室侧墙呈梯台形,燃烧器火焰沿倾斜炉墙平行燃烧,通过炉墙向转化管辐射传热。
与侧烧炉类似,转化管可以为双排或单排。
这种炉子的对流室全部置于辐射室顶部,烟气上行,采用自然抽风,没有引风机。
4) 底烧炉:这种炉型目前多用于小型装置。
燃烧器位于辐射室底部,烟气上行。
1.2炉型结构比较1) 传热方式顶烧炉的燃烧器安装在辐射室顶部,火焰从上往下烧,烟气流动方向与转化管内介质流动方向相同,传热方式为并流传热。
天然气制氢装置转化炉介绍
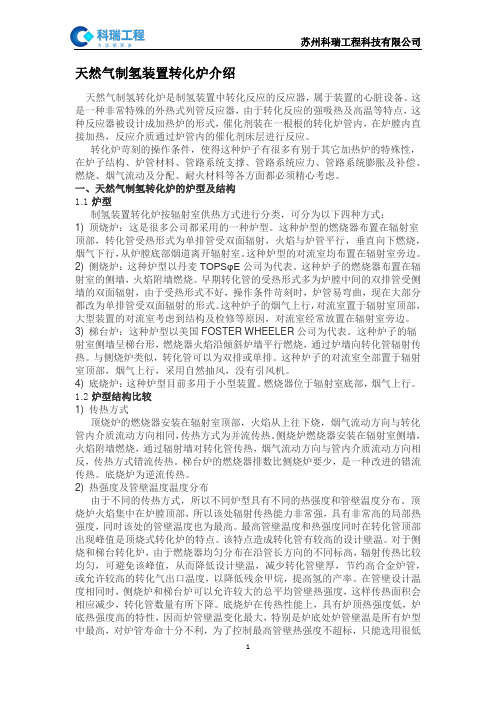
天然气制氢装置转化炉介绍天然气制氢转化炉是制氢装置中转化反应的反应器,属于装置的心脏设备。
这是一种非常特殊的外热式列管反应器,由于转化反应的强吸热及高温等特点,这种反应器被设计成加热炉的形式,催化剂装在一根根的转化炉管内,在炉膛内直接加热,反应介质通过炉管内的催化剂床层进行反应。
转化炉苛刻的操作条件,使得这种炉子有很多有别于其它加热炉的特殊性,在炉子结构、炉管材料、管路系统支撑、管路系统应力、管路系统膨胀及补偿、燃烧、烟气流动及分配、耐火材料等各方面都必须精心考虑。
一、天然气制氢转化炉的炉型及结构1.1 炉型制氢装置转化炉按辐射室供热方式进行分类,可分为以下四种方式:1) 顶烧炉:这是很多公司都采用的一种炉型。
这种炉型的燃烧器布置在辐射室顶部,转化管受热形式为单排管受双面辐射,火焰与炉管平行,垂直向下燃烧,烟气下行,从炉膛底部烟道离开辐射室。
这种炉型的对流室均布置在辐射室旁边。
2) 侧烧炉:这种炉型以丹麦TOPSφE公司为代表。
这种炉子的燃烧器布置在辐射室的侧墙,火焰附墙燃烧。
早期转化管的受热形式多为炉膛中间的双排管受侧墙的双面辐射,由于受热形式不好,操作条件苛刻时,炉管易弯曲,现在大部分都改为单排管受双面辐射的形式。
这种炉子的烟气上行,对流室置于辐射室顶部,大型装置的对流室考虑到结构及检修等原因,对流室经常放置在辐射室旁边。
3) 梯台炉:这种炉型以美国FOSTER WHEELER公司为代表。
这种炉子的辐射室侧墙呈梯台形,燃烧器火焰沿倾斜炉墙平行燃烧,通过炉墙向转化管辐射传热。
与侧烧炉类似,转化管可以为双排或单排。
这种炉子的对流室全部置于辐射室顶部,烟气上行,采用自然抽风,没有引风机。
4) 底烧炉:这种炉型目前多用于小型装置。
燃烧器位于辐射室底部,烟气上行。
1.2炉型结构比较1) 传热方式顶烧炉的燃烧器安装在辐射室顶部,火焰从上往下烧,烟气流动方向与转化管内介质流动方向相同,传热方式为并流传热。
制氢装置转化炉简介
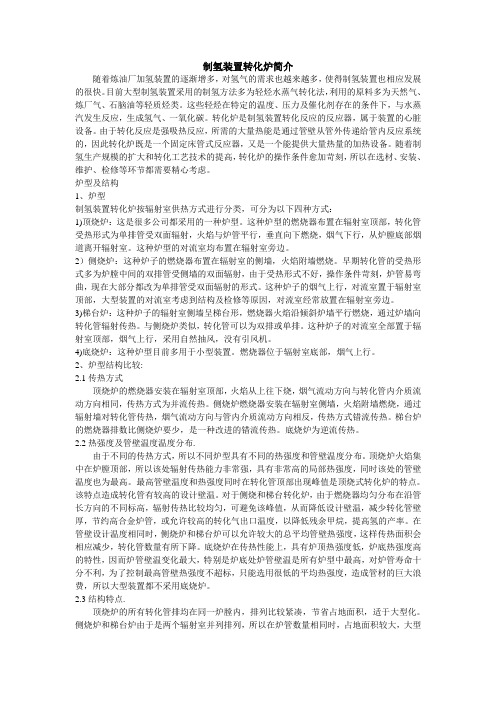
制氢装置转化炉简介随着炼油厂加氢装置的逐渐增多,对氢气的需求也越来越多,使得制氢装置也相应发展的很快。
目前大型制氢装置采用的制氢方法多为轻烃水蒸气转化法,利用的原料多为天然气、炼厂气、石脑油等轻质烃类。
这些轻烃在特定的温度、压力及催化剂存在的条件下,与水蒸汽发生反应,生成氢气、一氧化碳。
转化炉是制氢装置转化反应的反应器,属于装置的心脏设备。
由于转化反应是强吸热反应,所需的大量热能是通过管壁从管外传递给管内反应系统的,因此转化炉既是一个固定床管式反应器,又是一个能提供大量热量的加热设备。
随着制氢生产规模的扩大和转化工艺技术的提高,转化炉的操作条件愈加苛刻,所以在选材、安装、维护、检修等环节都需要精心考虑。
炉型及结构1、炉型制氢装置转化炉按辐射室供热方式进行分类,可分为以下四种方式:1)顶烧炉:这是很多公司都采用的一种炉型。
这种炉型的燃烧器布置在辐射室顶部,转化管受热形式为单排管受双面辐射,火焰与炉管平行,垂直向下燃烧,烟气下行,从炉膛底部烟道离开辐射室。
这种炉型的对流室均布置在辐射室旁边。
2)侧烧炉:这种炉子的燃烧器布置在辐射室的侧墙,火焰附墙燃烧。
早期转化管的受热形式多为炉膛中间的双排管受侧墙的双面辐射,由于受热形式不好,操作条件苛刻,炉管易弯曲,现在大部分都改为单排管受双面辐射的形式。
这种炉子的烟气上行,对流室置于辐射室顶部,大型装置的对流室考虑到结构及检修等原因,对流室经常放置在辐射室旁边。
3)梯台炉:这种炉子的辐射室侧墙呈梯台形,燃烧器火焰沿倾斜炉墙平行燃烧,通过炉墙向转化管辐射传热。
与侧烧炉类似,转化管可以为双排或单排。
这种炉子的对流室全部置于辐射室顶部,烟气上行,采用自然抽风,没有引风机。
4)底烧炉:这种炉型目前多用于小型装置。
燃烧器位于辐射室底部,烟气上行。
2、炉型结构比较:2.1传热方式顶烧炉的燃烧器安装在辐射室顶部,火焰从上往下烧,烟气流动方向与转化管内介质流动方向相同,传热方式为并流传热。
天然气制氢装置转化炉介绍
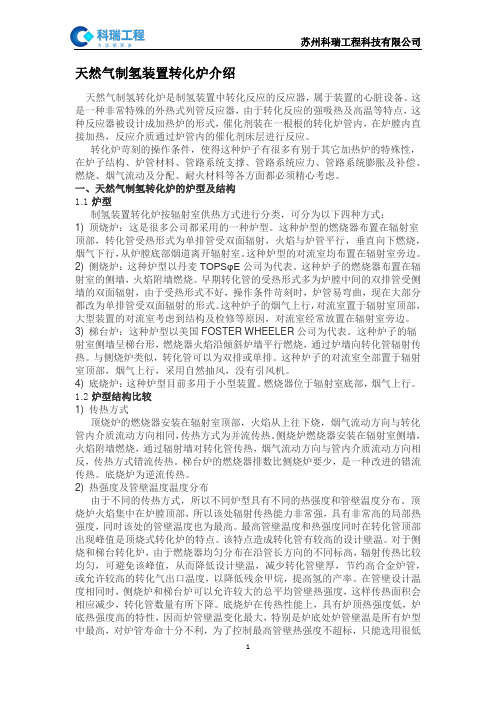
天然气制氢装置转化炉介绍天然气制氢转化炉是制氢装置中转化反应的反应器,属于装置的心脏设备。
这是一种非常特殊的外热式列管反应器,由于转化反应的强吸热及高温等特点,这种反应器被设计成加热炉的形式,催化剂装在一根根的转化炉管内,在炉膛内直接加热,反应介质通过炉管内的催化剂床层进行反应。
转化炉苛刻的操作条件,使得这种炉子有很多有别于其它加热炉的特殊性,在炉子结构、炉管材料、管路系统支撑、管路系统应力、管路系统膨胀及补偿、燃烧、烟气流动及分配、耐火材料等各方面都必须精心考虑。
一、天然气制氢转化炉的炉型及结构1.1 炉型制氢装置转化炉按辐射室供热方式进行分类,可分为以下四种方式:1) 顶烧炉:这是很多公司都采用的一种炉型。
这种炉型的燃烧器布置在辐射室顶部,转化管受热形式为单排管受双面辐射,火焰与炉管平行,垂直向下燃烧,烟气下行,从炉膛底部烟道离开辐射室。
这种炉型的对流室均布置在辐射室旁边。
2) 侧烧炉:这种炉型以丹麦TOPSφE公司为代表。
这种炉子的燃烧器布置在辐射室的侧墙,火焰附墙燃烧。
早期转化管的受热形式多为炉膛中间的双排管受侧墙的双面辐射,由于受热形式不好,操作条件苛刻时,炉管易弯曲,现在大部分都改为单排管受双面辐射的形式。
这种炉子的烟气上行,对流室置于辐射室顶部,大型装置的对流室考虑到结构及检修等原因,对流室经常放置在辐射室旁边。
3) 梯台炉:这种炉型以美国FOSTER WHEELER公司为代表。
这种炉子的辐射室侧墙呈梯台形,燃烧器火焰沿倾斜炉墙平行燃烧,通过炉墙向转化管辐射传热。
与侧烧炉类似,转化管可以为双排或单排。
这种炉子的对流室全部置于辐射室顶部,烟气上行,采用自然抽风,没有引风机。
4) 底烧炉:这种炉型目前多用于小型装置。
燃烧器位于辐射室底部,烟气上行。
1.2炉型结构比较1) 传热方式顶烧炉的燃烧器安装在辐射室顶部,火焰从上往下烧,烟气流动方向与转化管内介质流动方向相同,传热方式为并流传热。
制氢装置转化炉简介及制氢原理
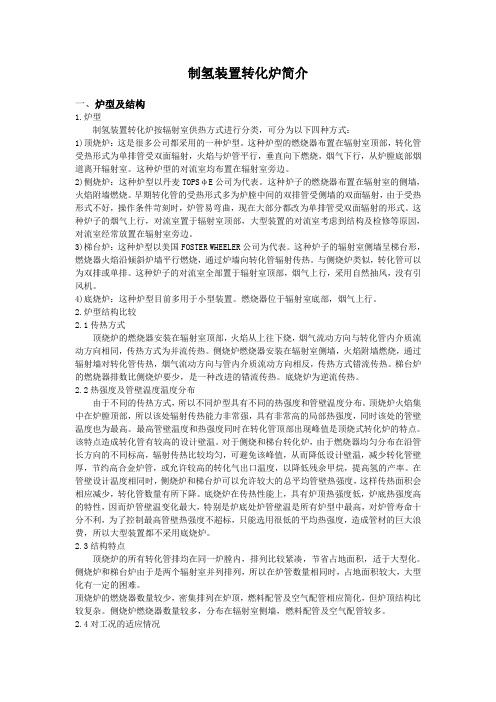
制氢装置转化炉简介一、炉型及结构1.炉型制氢装置转化炉按辐射室供热方式进行分类,可分为以下四种方式:1)顶烧炉:这是很多公司都采用的一种炉型。
这种炉型的燃烧器布置在辐射室顶部,转化管受热形式为单排管受双面辐射,火焰与炉管平行,垂直向下燃烧,烟气下行,从炉膛底部烟道离开辐射室。
这种炉型的对流室均布置在辐射室旁边。
2)侧烧炉:这种炉型以丹麦TOPSφE公司为代表。
这种炉子的燃烧器布置在辐射室的侧墙,火焰附墙燃烧。
早期转化管的受热形式多为炉膛中间的双排管受侧墙的双面辐射,由于受热形式不好,操作条件苛刻时,炉管易弯曲,现在大部分都改为单排管受双面辐射的形式。
这种炉子的烟气上行,对流室置于辐射室顶部,大型装置的对流室考虑到结构及检修等原因,对流室经常放置在辐射室旁边。
3)梯台炉:这种炉型以美国FOSTER WHEELER公司为代表。
这种炉子的辐射室侧墙呈梯台形,燃烧器火焰沿倾斜炉墙平行燃烧,通过炉墙向转化管辐射传热。
与侧烧炉类似,转化管可以为双排或单排。
这种炉子的对流室全部置于辐射室顶部,烟气上行,采用自然抽风,没有引风机。
4)底烧炉:这种炉型目前多用于小型装置。
燃烧器位于辐射室底部,烟气上行。
2.炉型结构比较2.1传热方式顶烧炉的燃烧器安装在辐射室顶部,火焰从上往下烧,烟气流动方向与转化管内介质流动方向相同,传热方式为并流传热。
侧烧炉燃烧器安装在辐射室侧墙,火焰附墙燃烧,通过辐射墙对转化管传热,烟气流动方向与管内介质流动方向相反,传热方式错流传热。
梯台炉的燃烧器排数比侧烧炉要少,是一种改进的错流传热。
底烧炉为逆流传热。
2.2热强度及管壁温度温度分布由于不同的传热方式,所以不同炉型具有不同的热强度和管壁温度分布。
顶烧炉火焰集中在炉膛顶部,所以该处辐射传热能力非常强,具有非常高的局部热强度,同时该处的管壁温度也为最高。
最高管壁温度和热强度同时在转化管顶部出现峰值是顶烧式转化炉的特点。
该特点造成转化管有较高的设计壁温。
制氢装置转化炉简介及制氢原理
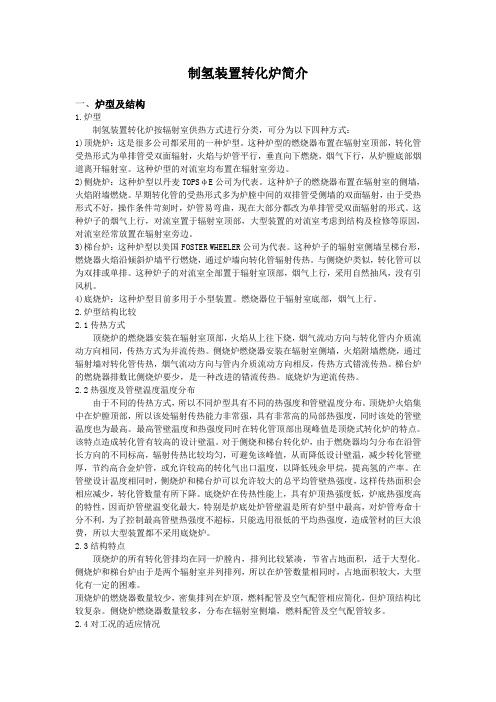
制氢装置转化炉简介一、炉型及结构1.炉型制氢装置转化炉按辐射室供热方式进行分类,可分为以下四种方式:1)顶烧炉:这是很多公司都采用的一种炉型。
这种炉型的燃烧器布置在辐射室顶部,转化管受热形式为单排管受双面辐射,火焰与炉管平行,垂直向下燃烧,烟气下行,从炉膛底部烟道离开辐射室。
这种炉型的对流室均布置在辐射室旁边。
2)侧烧炉:这种炉型以丹麦TOPSφE公司为代表。
这种炉子的燃烧器布置在辐射室的侧墙,火焰附墙燃烧。
早期转化管的受热形式多为炉膛中间的双排管受侧墙的双面辐射,由于受热形式不好,操作条件苛刻时,炉管易弯曲,现在大部分都改为单排管受双面辐射的形式。
这种炉子的烟气上行,对流室置于辐射室顶部,大型装置的对流室考虑到结构及检修等原因,对流室经常放置在辐射室旁边。
3)梯台炉:这种炉型以美国FOSTER WHEELER公司为代表。
这种炉子的辐射室侧墙呈梯台形,燃烧器火焰沿倾斜炉墙平行燃烧,通过炉墙向转化管辐射传热。
与侧烧炉类似,转化管可以为双排或单排。
这种炉子的对流室全部置于辐射室顶部,烟气上行,采用自然抽风,没有引风机。
4)底烧炉:这种炉型目前多用于小型装置。
燃烧器位于辐射室底部,烟气上行。
2.炉型结构比较2.1传热方式顶烧炉的燃烧器安装在辐射室顶部,火焰从上往下烧,烟气流动方向与转化管内介质流动方向相同,传热方式为并流传热。
侧烧炉燃烧器安装在辐射室侧墙,火焰附墙燃烧,通过辐射墙对转化管传热,烟气流动方向与管内介质流动方向相反,传热方式错流传热。
梯台炉的燃烧器排数比侧烧炉要少,是一种改进的错流传热。
底烧炉为逆流传热。
2.2热强度及管壁温度温度分布由于不同的传热方式,所以不同炉型具有不同的热强度和管壁温度分布。
顶烧炉火焰集中在炉膛顶部,所以该处辐射传热能力非常强,具有非常高的局部热强度,同时该处的管壁温度也为最高。
最高管壁温度和热强度同时在转化管顶部出现峰值是顶烧式转化炉的特点。
该特点造成转化管有较高的设计壁温。
制氢装置原理及操作综述
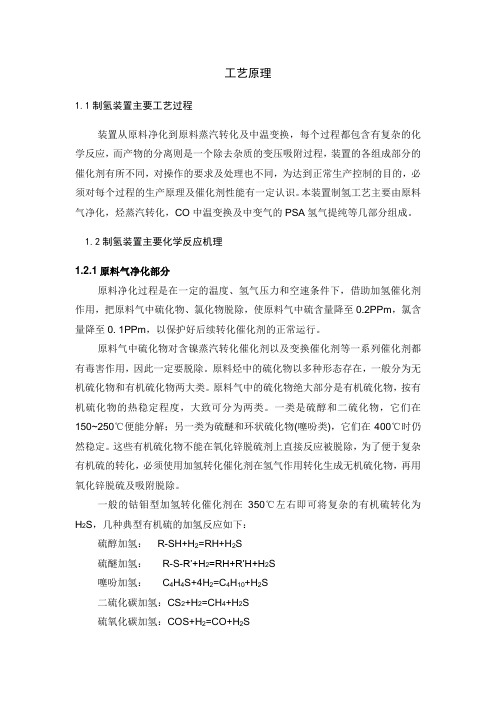
工艺原理1.1制氢装置主要工艺过程装置从原料净化到原料蒸汽转化及中温变换,每个过程都包含有复杂的化学反应,而产物的分离则是一个除去杂质的变压吸附过程,装置的各组成部分的催化剂有所不同,对操作的要求及处理也不同,为达到正常生产控制的目的,必须对每个过程的生产原理及催化剂性能有一定认识。
本装置制氢工艺主要由原料气净化,烃蒸汽转化,CO中温变换及中变气的PSA氢气提纯等几部分组成。
1.2制氢装置主要化学反应机理1.2.1原料气净化部分原料净化过程是在一定的温度、氢气压力和空速条件下,借助加氢催化剂作用,把原料气中硫化物、氯化物脱除,使原料气中硫含量降至0.2PPm,氯含量降至0. 1PPm,以保护好后续转化催化剂的正常运行。
原料气中硫化物对含镍蒸汽转化催化剂以及变换催化剂等一系列催化剂都有毒害作用,因此一定要脱除。
原料烃中的硫化物以多种形态存在,一般分为无机硫化物和有机硫化物两大类。
原料气中的硫化物绝大部分是有机硫化物,按有机硫化物的热稳定程度,大致可分为两类。
一类是硫醇和二硫化物,它们在150~250℃便能分解;另一类为硫醚和环状硫化物(噻吩类),它们在400℃时仍然稳定。
这些有机硫化物不能在氧化锌脱硫剂上直接反应被脱除,为了便于复杂有机硫的转化,必须使用加氢转化催化剂在氢气作用转化生成无机硫化物,再用氧化锌脱硫及吸附脱除。
一般的钴钼型加氢转化催化剂在350℃左右即可将复杂的有机硫转化为H2S,几种典型有机硫的加氢反应如下:硫醇加氢:R-SH+H2=RH+H2S硫醚加氢:R-S-R’+H2=RH+R’H+H2S噻吩加氢:C4H4S+4H2=C4H10+H2S二硫化碳加氢:CS2+H2=CH4+H2S硫氧化碳加氢:COS+H2=CO+H2S此处R-代表烷基,这些反应都是放热反应,平衡常数很大。
因此,只要反应速度足够快,有机硫的转化是很完全的。
除了上述有机硫加氢反应外,对于含有烯烃的制氢原料如焦化干气和催化干气,钴钼催化催还能使烯烃加氢成饱和烃,有机氮化物也可在一定程度上转化成氨和饱和烃了。
- 1、下载文档前请自行甄别文档内容的完整性,平台不提供额外的编辑、内容补充、找答案等附加服务。
- 2、"仅部分预览"的文档,不可在线预览部分如存在完整性等问题,可反馈申请退款(可完整预览的文档不适用该条件!)。
- 3、如文档侵犯您的权益,请联系客服反馈,我们会尽快为您处理(人工客服工作时间:9:00-18:30)。
制氢装置转化炉简介一、炉型及结构1.炉型制氢装置转化炉按辐射室供热方式进行分类,可分为以下四种方式:1)顶烧炉:这是很多公司都采用的一种炉型。
这种炉型的燃烧器布置在辐射室顶部,转化管受热形式为单排管受双面辐射,火焰与炉管平行,垂直向下燃烧,烟气下行,从炉膛底部烟道离开辐射室。
这种炉型的对流室均布置在辐射室旁边。
2)侧烧炉:这种炉型以丹麦TOPSφE公司为代表。
这种炉子的燃烧器布置在辐射室的侧墙,火焰附墙燃烧。
早期转化管的受热形式多为炉膛中间的双排管受侧墙的双面辐射,由于受热形式不好,操作条件苛刻时,炉管易弯曲,现在大部分都改为单排管受双面辐射的形式。
这种炉子的烟气上行,对流室置于辐射室顶部,大型装置的对流室考虑到结构及检修等原因,对流室经常放置在辐射室旁边。
3)梯台炉:这种炉型以美国FOSTER WHEELER公司为代表。
这种炉子的辐射室侧墙呈梯台形,燃烧器火焰沿倾斜炉墙平行燃烧,通过炉墙向转化管辐射传热。
与侧烧炉类似,转化管可以为双排或单排。
这种炉子的对流室全部置于辐射室顶部,烟气上行,采用自然抽风,没有引风机。
4)底烧炉:这种炉型目前多用于小型装置。
燃烧器位于辐射室底部,烟气上行。
2.炉型结构比较2.1传热方式顶烧炉的燃烧器安装在辐射室顶部,火焰从上往下烧,烟气流动方向与转化管内介质流动方向相同,传热方式为并流传热。
侧烧炉燃烧器安装在辐射室侧墙,火焰附墙燃烧,通过辐射墙对转化管传热,烟气流动方向与管内介质流动方向相反,传热方式错流传热。
梯台炉的燃烧器排数比侧烧炉要少,是一种改进的错流传热。
底烧炉为逆流传热。
2.2热强度及管壁温度温度分布由于不同的传热方式,所以不同炉型具有不同的热强度和管壁温度分布。
顶烧炉火焰集中在炉膛顶部,所以该处辐射传热能力非常强,具有非常高的局部热强度,同时该处的管壁温度也为最高。
最高管壁温度和热强度同时在转化管顶部出现峰值是顶烧式转化炉的特点。
该特点造成转化管有较高的设计壁温。
对于侧烧和梯台转化炉,由于燃烧器均匀分布在沿管长方向的不同标高,辐射传热比较均匀,可避免该峰值,从而降低设计壁温,减少转化管壁厚,节约高合金炉管,或允许较高的转化气出口温度,以降低残余甲烷,提高氢的产率。
在管壁设计温度相同时,侧烧炉和梯台炉可以允许较大的总平均管壁热强度,这样传热面积会相应减少,转化管数量有所下降。
底烧炉在传热性能上,具有炉顶热强度低,炉底热强度高的特性,因而炉管壁温变化最大,特别是炉底处炉管壁温是所有炉型中最高,对炉管寿命十分不利,为了控制最高管壁热强度不超标,只能选用很低的平均热强度,造成管材的巨大浪费,所以大型装置都不采用底烧炉。
2.3结构特点顶烧炉的所有转化管排均在同一炉膛内,排列比较紧凑,节省占地面积,适于大型化。
侧烧炉和梯台炉由于是两个辐射室并列排列,所以在炉管数量相同时,占地面积较大,大型化有一定的困难。
顶烧炉的燃烧器数量较少,密集排列在炉顶,燃料配管及空气配管相应简化,但炉顶结构比较复杂。
侧烧炉燃烧器数量较多,分布在辐射室侧墙,燃料配管及空气配管较多。
2.4对工况的适应情况顶烧炉由于在上部供热较多,所以在转化管内采用抗积碳性能好的催化剂时,可以很好的和转化反应相匹配,在反应最激烈处能供给最多的热量,燃料放热分布与反应吸热分布较协调。
但炉管纵向温度不能调节,在操作末期或催化剂积碳情况下,由于上部反应较少,管内介质温度升高很快,造成转化炉管的管壁温度升高,对炉管寿命有影响,设计管壁温度也需要取较大的裕量。
侧烧炉和梯台炉可以根据需要调节沿炉管长度方向受热的负荷,对不同工况的适应情况较好。
2.5操作情况顶烧炉的燃烧器都集中在炉顶,造成炉顶的操作条件比较恶劣,由于炉顶的温度非常高,炉顶布置又非常紧密,正常操作过程中调节燃烧器有一定难度。
侧烧炉和梯台炉的燃烧器均布置在侧墙,操作条件和缓,对正常操作好处较大。
但侧烧炉由于燃烧器数量较多,点火时花费的时间比顶烧炉要长。
二、转化管系1.转化管系流程中压蒸汽与原料气混合后进对流室的原料预热段预热,然后出对流室,经过转油线至辐射室顶部的上集合管,从上集合管分配进入各上猪尾管,再经过上猪尾管进入装有催化剂的转化管进行转化反应,转化反应完毕的转化气从转化管底部经下猪尾管导出,下猪尾管与下集合管相连,在下集合管内汇集的转化气被送至与下集合管直接相连的工艺气废热锅炉发生蒸汽并降温。
某些出口操作温度较高的转化炉没有下猪尾管,转化管直接与下集合管连接。
2.转化管系零件2.1上集合管上集合管是进气总管,主要用来将进料分配至各支管,根据原料预热温度的不同,上集合管可以采用铬钼钢、304、321等材质。
2.2上猪尾管上猪尾管是进气支管,除了用来分配进料外,主要作用是吸收转化管和上集合管以及转油线的膨胀,所以要求材料的塑性要好,主要采用奥氏体不锈钢304、321等材质。
其管径主要有φ25、φ32等规格。
2.3转化管该管直接置于炉膛内加热,由于要求良好的耐高温及抗高温蠕变性能,所以采用离心浇铸耐热合金管,早期的材质主要为HK40,后来又发展为HP40,这些年又出现了一系列新的改进型钢种。
2.4下猪尾管主要用来吸收下集合管的膨胀,采用的材质主要为Alloy 800H。
2.5下集合管根据装置规模的不同,下集合管有热壁和冷壁两种形式。
热壁下集合管的材质主要为Alloy 800H,冷壁下集合管的内壁为耐高温的衬里材料,外壁由于温度较低,可以采用普通碳钢或低合金钢。
3.转化管系的膨胀与补偿由于装置的大型化,制氢转化炉管路系统的热膨胀问题越来越突出。
大量的热膨胀问题要通过尾管和弹簧支吊架等热膨胀吸收元件和预留有足够的热膨胀空间来解决。
3.1下集合管的膨胀下集合管的膨胀分为分集合管的纵向膨胀和总集合管的水平膨胀。
对于每排炉管分集合管较短的情况,分集合管和总集合管均可采用热壁管,分集合管的纵向膨胀和总集合管的水平膨胀所形成的转化管和集合管之间的相对位移可由下尾管吸收。
转化管直接与下集合管相连时,下集合管的膨胀量可以通过安装前对转化管进行一定的冷拉量来吸收。
对于每排炉管根数较多,分集合管较长的情况,可以通过以下途径解决管路系统的膨胀问题:1)采用冷壁的总集合管,分集合管的出口设在中部并通过总集合管引出。
这样热壁分集合管的膨胀量比从端部引出减少至原来的二分之一。
2)采用复合式分集合管,既将整根热壁集合管分成若干根口径较小的小热壁集合管,进一步减少热壁管的膨胀,并节约高合金热壁管的投资。
3)采用带尾管的全冷壁集合管。
4)采用不带尾管的全冷壁集合管。
从经济性来看,以上以上方案的优劣次序为:不带尾管的全冷壁集合管,带尾管的全冷壁集合管,复合式分集合管,冷壁总集合管热壁分集合管,全热壁集合管。
不带尾管的全冷壁集合管主要用于转化气出口温度大于880℃的情况。
因为在该工况下,Cr20Ni32材质的尾管的热态许用应力为9MPa以下。
为满足二次应力的强度要求,在880℃以上的高温下要求较长的尾管,为满足一次应力的强度要求,长的尾管和低的许用应力导致繁杂的甚至是无法实现的支撑结构。
但不带尾管的全冷壁集合管催化剂的装卸都得通过转化管顶端法兰完成,当催化剂积碳时,从顶端真空吸出催化剂是有困难的。
当某根转化管发生泄露时,也无法通过同时卡死上下尾管的方式将泄露转化管切除。
3.2 转化管和转油线的膨胀为减少转化管底部和下集合管的位移差,减少高合金下尾管的长度,节约投资,转化管一般采用底部支撑,向上膨胀的方式。
同样为减少转化管顶部和上集合管的位移差,减少上尾管的长度,转油线也采用底部支撑,向上膨胀的方式。
与转油线相连的上集合管则由弹簧吊架悬挂,并随上升的膨胀向上移动。
转化管尽管采用底部支撑,但为减小转化管底部的轴向压应力,防止转化管弯曲,在转化管顶部增设弹簧吊架。
3.3上集合管的膨胀上集合管除随转油线向上移动以外,还沿轴向膨胀。
转化管向上膨胀、上集合管随转油线向上移动以及沿轴向膨胀所形成的转化管与上集合管的位移差由上尾管补偿。
三、对流室管系对流室管系主要用来预热原料、发生及过热反应用的蒸汽、回收烟气中的余热等等。
不同的工艺方案采用的对流室管系的布置方式略有不同,主要有原料/蒸汽混合过热段、蒸汽过热段、蒸汽发生段、燃烧用空气预热段。
四、转化炉主要工艺参数1.水碳比水碳比是指反应进口气体中水蒸汽分子数与烃类原料中碳原子数的比,常以S/C表示,它表征了转化操作所耗蒸汽的量。
工业上采用的水碳比要比按化学平衡计算值大。
在一定条件下,水碳比越高,甲烷平衡含量越低。
但水碳比越高,过剩蒸汽量则越大,辐射室热负荷也越大,增大了装置无用的燃料消耗。
水碳比和原料种类、催化剂类型、下游路线的选择以及经济因素有关,天然气原料的水碳比较低,石脑油原料的水碳比较高。
目前制氢装置的水碳比大概在2.5至3.5之间。
2.压力烃类蒸汽转化是体积增大的可逆反应,所以压力增加,逆反应随着增加。
但为了减少压缩功、强化后续设备的生产以及为使结构紧凑等等,目前的蒸汽转化仍然是加压蒸汽转化。
转化炉操作压力和下游设备的要求(如变压吸附等)、原料供应压力、转化管设计温度、转化管材料有关,目前制氢装置的操作压力大概在3.0MPa左右。
3.出口温度烃类蒸汽转化是吸热反应,温度增加,反应向正方向移动,残余甲烷平衡含量下降。
转化管出口温度与操作压力、转化管设计温度、转化管材料以及经济因素有关,制氢装置的转化出口温度在780℃至900℃之间。
4.原料预热温度原料预热温度即是入转化管的温度,提高原料预热温度可降低辐射室热负荷,减少燃料消耗,但原料预热温度和原料类型、管路材料、以及经济因素有关,采用天然气为原料时可以采用较高的预热温度,采用石脑油为原料时,由于原料会裂解,所以不宜采用太高的预热温度。
原料预热温度大约在450℃至650℃之间。
5.空气预热温度空气预热温度和外输蒸汽的量有关,由于转化炉发生的蒸汽量供自己使用仍然过剩,为了少发生蒸汽和少外输蒸汽,烟气的剩余热量则由空气来回收,这样空气的预热温度就会提高,但空气预热温度受NOx生成量以及经济因素的限制。
目前空气预热温度在200℃至500℃之间。
五、制氢原理⑴轻烃蒸汽转化反应①转化反应式转化反应是指水蒸汽和烃类进入转化炉炉管通过高温的催化剂作用,进行转化反应,生成H2、C0和CO2。
反应式:CnH2n+2+nH2O=nCO+(2n+1)H2 -QCnH2n+2+2nH2O=nCO2+(3n+1)H2 -Q②主要参数对转化反应的影响:A 反应压力转化反应是体积膨胀的反应,提高压力对平衡不利,压力增加,转化率会降低。
但在工业实践中,转化增压有以下好处:1)转化增压可节省动力,对制氢来说,转化增压可节省加氢压缩机的动力消耗。
2)转化增压可以提高设备能力,操作的空间速度可以大一些,催化剂的利用率可以提高,设备制造材料较省。