浅谈车床装夹零件变形对精度的影响
车床同心度超差的原因-概述说明以及解释

车床同心度超差的原因-概述说明以及解释1.引言1.1 概述概述部分内容:车床同心度是指车床加工过程中,工件在转动时中心轴与车床主轴旋转轴线的偏差。
同心度超差是车床加工中常见的问题之一,其影响着工件的加工质量和精度。
出现同心度超差的原因有很多,包括机械结构问题、工艺参数不合理、设备老化等。
首先,机械结构问题是导致车床同心度超差的主要原因之一。
车床的精度与机械结构的稳定性密切相关。
如果车床主轴、进给系统、工作台等部件存在松动或磨损等问题,就容易导致同心度超差。
此外,车床的刚性和稳定性也会对同心度产生影响。
如果车床刚性不足或者存在振动等问题,同样会导致同心度超差。
其次,工艺参数不合理也是导致车床同心度超差的原因之一。
在车床加工的过程中,一些工艺参数的选择可能不当,例如切削速度、切削深度、进给量等。
如果这些参数设置不合理,就容易导致加工过程中出现切削力不均匀、刀具振动等问题,从而影响工件的同心度。
此外,设备老化也会导致车床同心度超差。
随着使用时间的增长,车床各个部件会出现磨损、松动等现象,导致机械结构不稳定,进而影响同心度。
因此,定期检查和维护车床是保持其正常运行和准确加工的关键。
及时更换磨损严重的零部件,保持设备的精度和稳定性。
综上所述,车床同心度超差是车床加工中常见的问题,其原因多种多样。
机械结构问题、工艺参数不合理、设备老化等都可能导致同心度超差的发生。
为了提高车床的同心度,必须注重机械结构的稳定性和刚性、合理选择工艺参数,并定期检查和维护设备,以保持车床的正常运行和高精度加工能力。
1.2文章结构文章结构部分的内容可以是:文章结构部分旨在介绍整篇文章的组织架构,使读者能够清晰地了解整个文章的内容安排。
本篇文章按照以下结构进行组织:引言、正文和结论。
引言部分概述了本文的主要内容,并提出了车床同心度超差的问题。
引言部分将对车床的同心度进行简要的概述和解释,以引起读者的兴趣并了解这个问题的重要性。
正文部分将围绕车床同心度超差的原因展开讨论。
数控机床加工误差原因及对策分析

数控机床加工误差原因及对策分析数控车床为零件加工的主要方式,对于零件加工具有较高的自动化水平,但是就实际情况来看,零件加工经常会因为设备自身或者操作不当等因素限制,而造成工件精度达不到专业要求,存在一定误差。
零件加工精度最终由机床刀具与零件间相对位移误差决定,因此需要确定加工误差存在的原因,以降低误差为面对,采取措施进行优化。
本文选择经济性数控机床为对象,就其加工误差与优化对策进行了简要分析。
标签:数控机床;加工误差;补偿0 引言数控机床零件加工经常会因为各项因素的影响而出现误差,即加工后零件实际几何参数与设计几何参数间存在一定偏差,导致零件精确度不能满足设计要求,最终只能作为不合格或者废品处理。
以提高数控机床加工精确度为的目的,需要对各类加工误差原因进行分析,有针对性的采取措施进行处理,对存在的误差进行有效补偿。
1 数控机床加工误差分析经济性数控车床对零件的加工,应用为步进电机开环伺服系统或者半闭环伺服系统来驱动刀具,在这个过程中就会因为受各项因素的影响而存在加工误差。
一方面,数控机床自身因素。
主要是因为数控机床所用构件精确度较低,以及机床装配过程中存在误差,导致零件加工后精确度达不到设计要求。
针对此种误差原因,一般可以就高精度零部件进行更换,以及在装配环节做好控制,争取提高机床自身精确度。
另外,对于部分技术能力可以达到要求的企业,还可以选择对步进电机构成的开环伺服系统进行适当的改造,使其成为闭环伺服系统,来提高零件加工精度[1]。
另一方面,工艺操作因素。
部分零件在加工过程中,会因为机床以及零件本身的热变形,造成切削、振动、装夹、磨损等细节存在误差。
想要对此类误差进行补偿,需要建立补偿模型在CNC系统内补偿,实施难度比较大,对提高数控机床零件加工精确度需要重点研究。
2 数控机床加工误差原因与对策分析2.1 数控机床自身原因2.1.1 控制系统误差(1)开环控制系统。
开环控制系统并未设置反馈装置,数控信号为单向流程,并不能对移动部件实际位移量进行测量与反馈,进而会影响对加工过程中所存误差的调整。
数控车床盘类零件工装夹具设计

数控车床盘类零件工装夹具设计摘要:随着工业科技的高速发展,当今各行各业对各种产品零件的需求也层出不穷。
在零件的机械加工中单靠传统的常规装夹方式很难满足实际生产中一些零件的加工,因此,必须要为产品零件设计能顺利完成其装夹进行加工且成本低、加工效率高、满足精度要求的夹具。
文章对机床夹具中圆偏心夹紧装置的设计进行了研究分析,以供参考。
关键词:机床夹具;夹紧装置;设计前言机床夹具行业迄今已发展起来,可分为三个阶段。
第一阶段主要由夹具和人的组合来表示。
此时,夹具主要用作人体加速和完善加工过程的简单辅助工具。
在第二阶段,夹具成为人与机床之间的桥梁。
夹具的功能发生变化,主要用于工件的定位和夹紧。
人们越来越认识到操作者和机床性能的提高密切相关,因此夹具备受关注;第三阶段是夹具和机床的组合,夹具成为机床的一部分并成为加工不可或缺的工艺设备。
在夹具设计过程中,设计人员主要考虑加工零件定位和夹紧问题。
然而,夹具设计经常遇到一些小问题。
如果这些问题处理不当,会给夹具的使用带来很多不便,甚至影响工件的加工精度。
我们总结了多年来设计夹具时遇到的一些小问题:①清理根部的问题,在设计夹具端面和定位内孔时,会遇到清除根部的问题。
具体定位端面和定位外圆。
当端面和定位外圆被分成两个主体时,不会引起这个问题。
应根据工件的结构确定是否应移除夹具。
如果零件定位内孔的倒角很小或没有倒角,则必须清除根部。
如果零件定位孔的倒角很大或没有孔,则不需要根部,并且接头可以是圆形的。
当定位端面和外圆时,它与上面相同。
②让刀问题,当设计用于盘式工具(例如铣刀,砂轮等)的夹具时,应考虑铣刀或砂轮切削或磨削后铣刀或砂轮的退回位置。
铣刀或砂轮的位置应根据所用铣刀或砂轮的直径确定,并应超过刀具半径。
③更换问题,在设计一系列具有相同或相似结构和不同尺寸的产品零件和夹具时,为了降低生产成本并提高夹具的利用率,夹具通常设计为通用夹具,仅替换一个或几个部分。
1 机床夹具中定位与夹紧的研究1.1工件定位方案机床夹具的组成主要有以下几个部分组成:(1)定位元件,是夹具中确定工件位置的装置,主要的定位结构有支撑钉、V形块等;(2)夹紧装置,该装置是对工件进行夹持,保持工件在加工的时候不发生移动;(3)导向、对刀装置,是保证零件在加工的时候具有正确的位置;(4)夹具体,该装置是夹具的整个基础,是承载各种零件的基座;(5)其他装置,上下料装置、顶出器等。
零件装夹变形分析与解决措施

零件装夹变形分析与解决措施零件变形主要表现在装夹变形;切削力、切削热使零件产生变形;加工方法和技巧不当使零件产生变形;材料应力释放零件原因导致的变形等。
如果在生产过程中工件产生变形,那么肯定就会影响工件的形位精度,尺寸精度以及表面粗糙度,所以提高易变形零件加工质量和加工效率的关键就是装夹方法以及车削,铣削时的加工方法和技巧。
标签:装夹方法;刀具选择;切削用量1 为什么会产生零件装夹变形我们在加工生产中会遇到各种各样的问题,譬如在加工薄壁易变型零件时,就必须根据其不同的特点,找出薄弱环节,选用不同的工艺方法和夹紧方法来保证加工要求。
很多时候我们要具体问题具体分析,找到切实可行的办法来应对遇到的实际问题。
1.1 工件装夹不当为什么会产生变形?在我们生产实际操作中,如果我们采用三爪卡盘夹紧薄壁外圆,就会由于夹紧面积过小,夹紧力不均匀分布,那么拆卸以后,被卡爪夹紧部分就可能因弹性变形而涨大,最终导致零件出现多角形变化。
1.2 相对位置调整时候偏差,产生壁厚不均的现象经过多年的工作实践,我发现由于夹具、刀具,工件和机床主轴旋转中心的位置调整相对不准确,导致工件几何形状变化和壁厚不均匀现象。
我们遇见很多薄壁零件对于均匀性要求非常高,但对其尺寸精度要求却不高这种现象。
此时工件如果采用常规刚性定位,就会误差非常大,壁的厚度很容易超差。
这样工件在装夹过程中,假设我们没有根据实际特性,也就是工件刚度较低(薄壁件),或者不注意夹紧力的方向和施力点,那么支撑点和压紧点不能够重合就形成力矩效应,最终会引起零件变形。
1.3 为什么要强调零件壁厚差重要性有一部分薄壁零件对均匀性要求非常高,而对其尺寸精度要求却不高。
这种工件和彩刚性定位,就会误差很大,壁厚非常容易超差。
在装夹过程中的工件,假设刚度较低(薄壁件)或者夹紧力方向,施力点选择不恰当,支撑点与压紧点不重合必然形成力矩效应将会引起零件变形。
1.4 选用什么样的刀具至关重要我们选择什么样的刀具,会直接影响零件精度以及表面粗糙度。
浅析薄壁零件加工中变形振动分析和消振措施

薄壁零件加工中变形振动分析和消振措施摘要:车削过程中,工艺系统由于受到各种力的作用,工件和刀具之间常会发生相对振动。
它不仅使加工表面产生波纹,严重恶化加工精度和表面质量。
特别是最后一刀精车,当切削速度提高,常常会发生刺耳的响声,使车削无法继续加工下去。
所以,在加工薄壁零件中,不仅要考虑装夹中工件受力变形的问题,还要注意解决加工中振动问题关键词:薄壁零件加工变形振动措施车削薄壁零件在加工中很容易出现问题,如果我们在加工中善于总结经验,就能在加工中找出它的共性、个性和矛盾突出点。
变被动为主动。
从而才能够加工出合格的产品。
要想解决薄壁零件加工中出现的问题,我想从以下几个方面来加以分析。
一、薄壁零件装夹分析1、薄壁零件的加工特点薄壁零件以日益广泛地应用个工业部门生产机器零件中,车削薄壁零件的关键是变形、振动问题。
工件产生变形振动的原因大多是由于切削力、夹紧力、定位误差和弹性变形。
其中影响最大的是切削力和夹紧力。
我们在实践过程中减小切削力和切削热主要采取方法是:合理地选择切削用量、合理地选择刀具几何角度、减小夹紧力引起的变形,主要改变和改善夹紧力对零件的作用。
2、车削薄壁零件时采用的装夹方式以上讲的薄壁零件加工特点是车削中变形和振动问题。
由于薄壁零件的刚性差,车削中容易变形。
所以在装夹时要考虑到夹紧力的方向和着力点。
夹紧力的方向应选择在有利于减小夹紧力的部位。
如薄壁零件为套类,则可将径向夹紧力改为轴向夹紧力;薄壁零件为盘类,则可该轴向夹紧力为径向夹紧力;当薄壁零件径向和轴向刚性都很差时,保证夹紧力方向与切削力方向一致,就能使较小夹紧力起到较大夹紧力的作用。
还要夹紧力着力点应落在支承点正对面和切削力部位的附近以减小变形振动。
二、减小薄壁套装夹中变形的措施1、合理确定夹紧力的大小、方向、作用点。
粗、精车加工分开,当粗精车加工使用同一夹具时,粗加工余量大,切削力大。
因而需要较大的夹紧力。
而精车时余量小,切削力小,所需要的夹紧力也就小。
7.4工艺系统受力变形引起的加工误差2
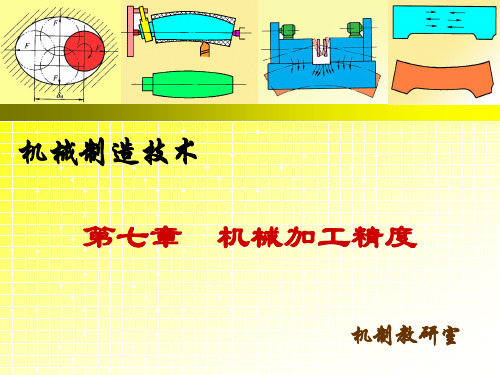
工艺系统的受力变形引起的加工误差 在内圆磨床上用横向切 入磨孔时, 入磨孔时,由于内圆磨头 工 艺 系 统 刚 度 分 析 主轴弯曲变形, 主轴弯曲变形,磨出的孔 会带有锥度的圆柱度误差 。精度外圆一般到磨削后 期需进行无进给磨削, 期需进行无进给磨削,多 次无进给磨削消除工艺系 统受力变形。 统受力变形。
LOGO
机械制造技术
第七章
机械加工精度
机制教研室
LOGO
第七章 机械加工精度
第四节 工艺系统受力变形引起的 加工误差
第四节 工艺系统受力变形引起的加工误差
一 本 节 教 学 内 容
一
工艺系统刚度分析
二 工艺系统受力变形对加工精度的影响 三 减小工艺系统受力变形的措施
第四节 工艺系统受力变形引起的加工误差
工 艺 系 统 刚 度 分 析
车床刀架部件静刚度曲线
(三)机床部件的刚度及特点 从机床静刚度曲线可以看出: 从机床静刚度曲线可以看出: 1)刚度曲线不是直线,力和变形不成线性关系。 刚度曲线不是直线,力和变形不成线性关系。 工 这表明部件的变形不单纯是弹性变形。 这表明部件的变形不单纯是弹性变形。 艺 系 统 刚 度 分 析
(四)影响机床部件的刚度的因素
工 艺 系 统 刚 连接表面间的接触变形 度 零件接触面在外力作用下抵抗接触变形的能力称 分 接触刚度。影响接触刚度的主要因素是接触表面的 析 为接触刚度。影响接触刚度的主要因素是接触表面的 粗糙度、表面形状误差、材料的硬度等 粗糙度、表面形状误差、材料的硬度等。
(四)影响机床部件的刚度的因素 2.部件中薄弱零件的影响 2.部件中薄弱零件的影响 工 艺 系 统 刚 度 分 析 如果部件中有某些刚度 很低的零件时, 很低的零件时,受力后这些 低刚度零件会产生很大的变 使整个部件的刚度降低。 形,使整个部件的刚度降低。 如图所示, 如图所示,由于床鞍部件中 的楔铁细长、刚性差, 的楔铁细长、刚性差,不易 加工平直, 加工平直,加上使用接触不 在外力作用下, 良,在外力作用下,就会产 薄弱零件变形示意图 生很大变形, 生很大变形,使部件刚度大 大降低。 大降低。
数控加工中产品变形控制策略研究

数控加工中产品变形控制策略研究摘要:数控车床是实现自动化加工的重要手段,可以通过编程的方式对零件进行加工,具有极高的生产效率。
然而,一旦生产过程变得复杂化,零件的加工就会产生产品变形,对零件的成品效果造成极大的影响,因此,需要采取有效的控制手段,对数控车床加工精度控制策略进行优化。
基于此,本篇文章对数控加工中产品变形控制策略进行研究,以供参考。
关键词:数控加工;产品变形;控制策略引言对于在机械加工中存在的产品变形问题,操作人员需要充分考虑各个方面的情况,无论是管理、还是切削的工具、材料以及数控机床的设置等,都需要进行科学的选择,从而不断的提升数控机械加工的精度,从而保证零部件的加工质量,提高生产效率。
一、提高数控加工中产品变形控制的意义随着各种科学技术的发展,也让数控加工技术在逐渐的成熟中,在进行加工时,包含了大量的数控原理,在加工中非常灵活,第一个加工的细节变化都非常留意,充分体现了数控加工的严谨性,另外,对于加工的对象和方法也能根据具体的情况进行不同的选择,从而发挥数控机床的优势,这样就大大提升了车削加工的效率,并且有效的提升了机械的加工质量,并且对于零部件加工的质量也有着很大的影响。
虽然已经在数控加工工艺的技术应用取得了一定的成绩,但是在实际应用的过程当中,仍然会出一些新的问题,从而导致加工产品变形的影响,面对这种情况,就需要对于加工过程中影响的各种因素进行详细的分析,从而提升数控机械加工的质量,更好的提高加工部件的精度。
二、影响数控加工精度的因素(一)电气伺服系统的影响在利用数控车床对零部件进行加工时,电气伺服系统主要是提供车床运转的工作。
在对零部件进行加工时,需要控制零部件与刀具之间的位置,这时就需要伺服电机运转以驱动滚珠丝杠的前移或者后退,在进行两者之间位置调节时,若伺服驱动与滚珠丝杠之间出现传动误差,则会对零部件的变形产生较大的影响,甚至工件失效。
(二)编程误差的影响根据图纸在数控机床上进行编程时,会存在编程误差,这主要是由于数控机床内部的数学逻辑问题导致的,对于这种编程误差通常采用插值法或者直接提高数控车床的分辨率,从而降低误差,提高精度。
毕业论文 车床论文

前言随着科技的发展,数字化机械设备不断占领市场,尤其是金属切削中的数控机床已经成为时代的先驱,引领潮流。
但有着悠久历史的普通成床,特别是它不甘落后,继续想着明昂首阔步的精神,是值得我们去改造的。
本篇论文的指导思想:包括车床的历史发展及卧式车床的相关知识;车床主轴的加工工艺及检验装配;使用后对机床的保养及维护;对废置主轴重新修理再利用。
相对于数控车床,普通车床对于手工操作要求更高一些,主要体现个人的技术水平,而且有些零件的加工工序还需要它来加工的,还有就是它的加工价格比较便宜,所以它不会很快消失,那么增加它的使用寿命,进而提高它的业绩,希望它跟好的走向明天。
第1章概论1.1 车床的历史及发展1.1.1 车床的历史公元前二千多年出现的树木车床是机床最早的雏形。
工作时,脚踏绳索下端的套圈,利用树枝的弹性是工件有绳索带动旋转,手拿贝壳或石片等作为刀具,沿板条移动工具的切削工作。
中世纪的弹性杆棒车床运用的仍是这一原理。
十五世纪由于制造钟表和武器的需要,出现了钟表匠用的螺纹车床和齿轮加工车床,以及水力驱动的炮筒鏜床。
1500年左右,意大利让人奥纳多.达芬奇曾绘制过车床,鏜床,纹加工机床和内圆磨床的构想草图,其中已有曲柄,飞轮,顶尖和轴承等新机构。
中国明朝出版的《天工开物》中也载有磨床的结构,用脚踏的方法是铁盘旋转,加上沙子和水剖切玉石。
1979年,英国人莫兹利创造成的车床由丝杆转动刀架,能实现机动进给和车削螺纹,这是机床结构的一次重大变革。
莫兹利也因此被称为“英国机床工业之父”。
随着电动机的发明,机床开始先采用电动机集中驱动,后有广泛使用单独电动机驱动。
二十世纪初,为了加工精度更高的工件,夹具和螺纹加工工具,相继创造出坐标鏜床和螺纹磨床。
同时为了适应汽车和轴承等工业大量生产的需要,有研制成能自动更换刀具,以进行多工序加工的加工中心。
从此,随着电子技术和计算机的发展和应用,使机床在驱动方式,控制系统功能等方面都发生显著变革。
- 1、下载文档前请自行甄别文档内容的完整性,平台不提供额外的编辑、内容补充、找答案等附加服务。
- 2、"仅部分预览"的文档,不可在线预览部分如存在完整性等问题,可反馈申请退款(可完整预览的文档不适用该条件!)。
- 3、如文档侵犯您的权益,请联系客服反馈,我们会尽快为您处理(人工客服工作时间:9:00-18:30)。
仅用于圆度误差的计算, 直径 误差相对太小, 可不计 当计算直径误差时, 根据所求 变形方向不同, # 应带正负号
" - $ 受力简图 图!
" 7 $ 回弹变形图 四点夹紧示意图
圆度误差为: ! L & Q ! " T !B T U T !" Q S T $ L %M %&&# " OPH Q R@ $ " ;; $ "Z$
$M N &O &&!K ’ BP* Q RG $S N &O &&!" ’ BP* Q RG $M! N &O &,() ’ BP* Q RG -
’ DD ’ DD ’ DD -
’!’#’*-
!!!!!!!!!!!!!!!!!!!!!!!!!!!!!!!!!!!!!!!!!!!!!!!!!!!!!!!!!!!!!!!!!!!!!!!!!!!!!!!!!!!!!!!!!!!!
"
消除活塞与气门、 缸盖撞击的几点意见
无论什么原因造成的撞击,都将随着使用时间的增加,
愈来愈严重, 而决不会自行消除。 所以, 对这一故障必须及时 排除, 不然会造成更大损失。 应修改最小余隙尺 ! 对于因最小余隙小而造成的撞击, 寸。另外, 也可在局部部位消瘦进、 排气凸轮, 使气门在凸轮 转角 !#$ % #&$间开启度略小些, 避免活塞与气门的撞击。
H
两种夹紧方式的比较
例: 工件材料为锻钢 D& L !%%;;\ D! L &S%;;\ G L ’%;;, 采用三点夹紧。从表 & 中查得 # L &M SN ] &%H W Q ; 将各值代 入 " - $ 式, 得: ! L #" G)H Q PH $ L &M SN ] &%H ] "’% ] H%H Q Z’H $ L H!J’ V W Q &% I !;; X 据有关资料介绍, 如果采用 ^!S 螺栓夹紧, 扳手长度为 H&%;;\ 加在扳手上的力 !%%W,可产生夹紧力 O L !’S!#W\ 按 " 7 $ 式计算: ! L O Q ! L !’S!# Q H!J’ L JM J# &% I ! :;。 其直 可见, 圆度误差已接近 %M %Z;;。如改为四点夹紧, 径误差也有近 %M %&;;。这对于精度要求较高的工件已有影 响。 如若采用车床加工, 按一般操作者的习惯, 其扳手长度及 所加力均可能超过以上数据, 实际变形还要增加。 显然, 预先 知道了变形与力的关系及可能产生变形量的大小, 就可以在 安排工艺、 设计夹具时考虑限制扳手长度或施力大小, 以保 证所加工产品的质量。
有效地减少零件夹紧变形对加工精度的影响。 【关键词 】 夹紧 【中图分类号 】 H[,&
机械产品中有许多薄壁短圆筒形零件。 车削其内外圆时 均需夹紧, 并产生有夹紧变形。对于精度要求较高的零件夹 紧, 变形问题是零件超差的重要原因。如果能预先计算出其 变形量的大小, 就能为正确地制订工艺路线、 设计工装和测 量方法提供依据。车床上常用三爪卡盘和四爪卡盘装夹零 件, 一般说来, 变形较大。本文主要讨论两种夹紧情况。
第 # 期 ’ 总第 )# 期 T9A # ’ UV< T9A )# -
机 械 管 理 开 发 <RWXYTGWYZ <YTY[R<RTH YT/ /R\RZ]B<RTH
#&&! 年 , 月 <6MA #&&!
பைடு நூலகம்
浅谈车床装夹零件变形对精度的影响
丁立军
【摘 要 】 指出车床上三爪夹紧和四爪夹紧时, 夹紧力与变形之间的关系, 为薄壁零件工艺路线中夹紧方式的制订提供依据, 可以 变形 加工 精度 【文献标识码 】 J 【文章编号 】 !&&* . KK*L ’ #&&! - &# . &&!! . &#
" 加强全面质量管理,严格控制零件处在公差范围内, 以保证产品质量。 不合格零件不进行 # 加强装配调整过程中的检验工作。 装配。 要严格检查压缩余隙、 配气相位等防止撞击发生; 严格 检查气门间隙,因为气门高出缸盖下平面尺寸增大,造成它 们与活塞撞击。
’ 作者: 孙克明, 男, !(") 年生, !()( 年生毕业于山西农业大学, 现任山西省农业机械工业总公司董事长, 总经理, 高级工程师; 何忠 现任山西临汾机 良, 男, !()* 年生, !(+, 年毕业于山西省农业大学, 械制造有限公司技术科科长, 工程师。通讯地址: 太原市新建路 "# 号。邮编: &*&&&# -
!
三点夹紧
加工内孔时, 三点夹紧的受力简图见图 ! ’ 6 - , 工件被夹
’ 6 - 受力简图 图!
’ @ - 回弹变形图 三点夹紧示意图
紧时产生了变形, 若车削加工后把孔看作理想但卸活后 ’ 由 孔因工件的回弹, 变形使工件孔的最终几何 于夹紧力消失 - , ’ 公式推导略 形状如图 ! ’ @ - 所示。图中各变形量:
・!!・
第 ! 期 " 总第 #! 期 $
机
械
管
理
开
发
!%%& 年 ’ 月
!B! L I %M %’JN " OPH Q R@ $ 圆度误差为:
" ;; $
"S$
S
计算举例
若令 " & $ [ " Z $ 式中的 ! L %M %&;; 将常量合并为一系数
"’$ ! L T !B& T U T !B! T L %M &&J’ " OPH Q R@ $ 式中: — 夹紧力 V W X ; — 工件的弹性模量 V W Q ;;! X O—— R—— — 工件沿法线方向断开后的截面,对其中性层的轴 @—— "S$ 惯性矩 V ;;S X ; — 中性层半径, 一般取平均半径 V ;; X ; P—— 式中的负号表示 !B! 沿直径方向缩小。
・&!・
则可将各式整理为: #, ! L # " G)H Q PH $ " W Q &% I ! ;; $
"-$ 式中: — 工件截面的高度 " ;; $ ; G—工件厚度 " ;; $ ; )—— !
表示为每变形 %M %&;; 所需的作用力。 当已知夹紧力 O, 则可 从下式求变形: !LOQ ! O L !・ ! " &% I ! ;; $ "W$ "7$ ":$ 已知变形求夹紧力, 则有: 为方便应用,将几种常用材料的 " - $ 式中系数 # 列成 表。
责编: 武俊天
" 收稿日期: !%%& I %H I &’ $
古
工
!" #$%&’(") *+,-.&%/(-" %"0 1,,+2/(-" -, 1223.%24 5-.6(") -" 7%/8+9
*(") 7(:3"
〔1;9/.%2/〕()*+ ,-,./ ,01 23/4-/5 - 6*.4 -7301 /.8-1*39+)*, 7.14..9 :8-;,*9< 23/:. -95 5.23/;-1*39 39 1)/.. =-4 :)0:> -95 230/ =-4 :)0:> 39 - 8-1).? @1 :0+13;*A.+ -95 ,/36*5.+ - /.2./.9:. 23/ :011*9< 32 1)*99./ 4-88 ,-/1+ -95 ,/.6.91 5.23/;-1*39 2/3; -22.:1*9< ;-:)*9*9< -::0/-:B .22*:*.918B? 〔<+4 =-.09〕 C8-;,*9< D.23/;-1*39 E::0/-:B 〔#7# "3&;+.〕 (F’% 〔*-23&+"/ 2-0+〕 G 〔1./(2$+ >*〕&%%H I JJHK " !%%& $ %! I %%&& I %!
表& 夹紧方式 锻钢 三点式 四点式 &M SN &’M & 铸钢 &M !S &!M # 铸铁 &M %# &%M Z 公式 " - $ 中的系数 # 值表 材 质 备 注 " &%H W Q ;; $ 单位:
!
四点夹紧
四点夹紧时工件, 在卸活后, 同样产生回弹变形。 其受力
简图与回弹变形情况见图 ! 。图中各变形量为: !B L !Y L %M %&!! " OPH Q R@ $ " ;; $ !" Q S L I %M %&%Z " OPH Q R@ $ " ;; $ "#$ "J$
" 作者: 男, 本 &N## 年生, &NZJ 年毕业于太原工业大学机械系, 科,现为太原矿山机器集团有限公司通用设备分公司技术经理,工 程师。邮编: %H%%%N $
分析 " & $ [ " Z $ 式可知: 三点夹紧所产生的圆度误差较其 直径误差高两个数量级, 故对三点夹紧来讲, 主要是圆度误 差的影响。 四点夹紧所产生的圆度误差与其直径误差相差无 几。 在夹紧力相同的情况下, 以圆度误差而言, 四点夹紧方式 仅是三点夹紧方式所产生的误差十分之一左右。 以这个变形 问题来说, 四点夹紧较三点夹紧优越, 也可推知, 多点夹紧所 产生的变形较小。 对于夹紧变形问题, 四点夹紧要注意直径方向的尺寸误 差及圆度误差, 而三点夹紧要特别注意圆度误差。因为三点 夹紧所产生的圆度误差是变形互补的关系, 见图 & " 7 $ 。 用百 分表测内径是测不出这种误差的, 而百分表测内径又是一般 工厂主要的测量方法, 这样就可能发生不合格产品 " 圆度已 超差 $ 而误判为合格产品, 使产品质量下降。 所以我们完全有 必要采用前面推荐的公式预先进行计算,以便合理安排工 艺, 保证产品质量。 需要提醒的是, 无论是三点夹紧还是四点夹紧, 对于壁 虽较厚但内径较大的零件, 直观认为可能变形不大, 但实际 上一般的夹紧力即可产生较为明显的变形。