1000MW超超临界机组技术发展的探讨
1000MW超超临界机组节能降耗技术探讨

1000MW超超临界机组节能降耗技术探讨
超超临界机组是目前发电领域中的新兴技术,具有较高的发电效率和节能降耗的潜力。
本文将探讨一些与1000MW超超临界机组节能降耗相关的技术。
1000MW超超临界机组的高效燃烧技术是节能降耗的一个重要方面。
采用先进的燃烧器设计和燃料预混合技术,可以提高燃烧效率并降低燃料消耗量。
优化燃烧过程,减少燃烧
产物对环境的影响,也是节能降耗的一个关键方面。
1000MW超超临界机组的余热利用技术也是节能降耗的重要手段。
通过对锅炉废气余热和冷却水余热的充分利用,可以提高机组的效率并减少热能的浪费。
采用烟气余热锅炉和
废热回收装置,可以将废气中的余热回收利用,用于再生蒸汽发生器的加热或供热。
1000MW超超临界机组的节水技术也是节能降耗的重要措施。
通过优化锅炉和蒸汽循环系统的设计,减少水的消耗量,可以降低机组的水耗率。
采用再生水回收系统,对废水进
行处理和再利用,可以最大限度地减少用水量。
改善机组的运行和维护管理也是节能降耗的关键。
定期对机组进行巡检和维护,及时
清理灰尘和沉积物,保持机组的高效运行状态。
优化运行参数和控制策略,提高机组的运
行稳定性和效率。
1000MW超超临界机组的节能降耗技术包括高效燃烧技术、余热利用技术、节水技术以及运行和维护管理等方面。
通过采用这些技术,可以进一步提高机组的发电效率,降低能
源消耗,实现可持续发展。
1000MW超超临界机组节能降耗技术探讨

1000MW超超临界机组节能降耗技术探讨随着经济的快速发展和能源需求的不断增加,电力行业的发展也在不断提升,特别是超超临界机组,成为新一代发展趋势。
但是,在大规模应用的同时,其高能耗也不容忽视,因此需要遵循节能减排的方向,实现超临界机组的节能降耗,为可持续发展做出贡献。
为了解决超超临界机组的能耗问题,国外和国内的研究机构和厂家开展了多项技术研究和应用实践。
其中,以下几个方面是目前超超临界机组节能降耗的主要技术:1.针对燃烧系统的优化设计。
通过优化炉膛结构、改进喷煤技术等手段,提高燃烧效率,减少燃料消耗,从而降低能耗。
2.热损失的全面控制。
在锅炉、汽轮机、发电机等部件中,采用降低热损失的材料和技术,如高密度绝缘材料、超低温级减少热辐射等,以降低设备自身的能耗。
3.先进的控制策略。
通过优化控制方法和参数,如调整煤粉粒度、优化水泵、汽轮机转速等,使设备运行更加稳定和高效,进一步减少能耗。
4.余热回收和利用。
在余热回收系统中,通过采用多级利用、废气余热回收等技术,将余热充分回收利用,降低燃料消耗。
5.空气预热技术的应用。
通过采用燃烧前空气预热、排烟回收等技术,降低锅炉供风系统的能耗,提高热效率。
以上技术将通过科学的应用实践和创新,促进超超临界机组的节能目标和降低成本,较大程度推动中国能源行业的转型升级和环境保护工作。
未来,超超临界机组节能降耗技术的发展方向将更加多元化和创新化。
1.针对热损失的新材料研发。
将开展全领域、全方位的热损失研究,并将基于新材料、新技术的研发应用于实际生产,不断降低超超临界机组的能耗。
2.高效新型微粒燃烧技术的应用。
将新型微粒燃烧技术应用于石油燃烧、生物质燃烧等,推广和应用高效的燃烧技术,提高燃料利用效率和热效率。
3.大数据技术的应用。
将大数据技术应用于电力系统管理、调度和优化,实现目标的动态调整,并对运行数据进行深度挖掘和分析,指导精准的运行优化。
4.智能化控制技术的发展。
加强机器人降耗技术研究,实现设备的自主运行、维护和保养,为超超临界机组的能效提供坚实支持。
1000MW超超临界机组节能降耗技术探讨
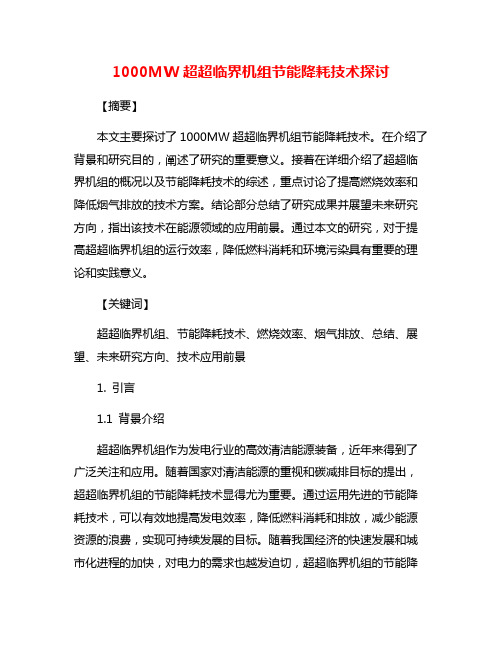
1000MW超超临界机组节能降耗技术探讨【摘要】本文主要探讨了1000MW超超临界机组节能降耗技术。
在介绍了背景和研究目的,阐述了研究的重要意义。
接着在详细介绍了超超临界机组的概况以及节能降耗技术的综述,重点讨论了提高燃烧效率和降低烟气排放的技术方案。
结论部分总结了研究成果并展望未来研究方向,指出该技术在能源领域的应用前景。
通过本文的研究,对于提高超超临界机组的运行效率,降低燃料消耗和环境污染具有重要的理论和实践意义。
【关键词】超超临界机组、节能降耗技术、燃烧效率、烟气排放、总结、展望、未来研究方向、技术应用前景1. 引言1.1 背景介绍超超临界机组作为发电行业的高效清洁能源装备,近年来得到了广泛关注和应用。
随着国家对清洁能源的重视和碳减排目标的提出,超超临界机组的节能降耗技术显得尤为重要。
通过运用先进的节能降耗技术,可以有效地提高发电效率,降低燃料消耗和排放,减少能源资源的浪费,实现可持续发展的目标。
随着我国经济的快速发展和城市化进程的加快,对电力的需求也越发迫切,超超临界机组的节能降耗技术的研究和应用具有重要的现实意义与战略意义。
本文将重点探讨1000MW超超临界机组的节能降耗技术,探索如何提高其燃烧效率和降低烟气排放,为我国清洁能源发展和节能减排工作提供参考和借鉴。
1.2 研究目的研究目的是为了探讨如何利用1000MW超超临界机组节能降耗技术,提高燃烧效率和降低烟气排放,从而实现资源的有效利用和环境保护。
通过深入研究超超临界机组的节能降耗技术,我们可以进一步推动我国电力行业的可持续发展,提高能源利用效率,减少对环境的影响。
通过本研究,我们希望能够找到更加有效和可行的技术方案,为超超临界机组节能降耗提供理论支撑和技术指导,为我国电力行业的发展做出积极贡献。
通过本文的探讨,我们可以深入了解超超临界机组的节能降耗技术现状和发展趋势,为相关领域的研究人员和工程技术人员提供参考和借鉴,促进技术创新和产业升级。
1000MW超超临界机组节能降耗技术探讨

1000MW超超临界机组节能降耗技术探讨
随着能源需求的增加和环境保护意识的提高,节能降耗技术在发电行业中变得越来越重要。
而1000MW超超临界机组作为目前发电行业中最高效的发电装备之一,更需要采用有效的节能降耗技术来提高其运行效率和减少能源消耗。
对于1000MW超超临界机组而言,优化燃烧过程是节能降耗的关键。
通过燃烧装置结构的优化设计,可以提高燃烧效率和燃烧稳定性,减少燃料的消耗量。
在燃烧过程中,合理调节燃烧辅助设备,如燃烧机、风机等,可以提高燃烧效率,减少能源的浪费。
热力系统优化也是节能降耗的重要手段。
1000MW超超临界机组的热力系统包括锅炉、汽轮机、凝汽器等组件,对其中的各个环节进行优化可以提高热能的利用效率。
通过合理设计锅炉水冷壁结构和提高锅炉排烟温度,可以减少烟气的热损失;通过增加凝汽器效率和改进汽轮机腔式系统可以提高汽轮机的膨胀能力,减少能源的损耗。
在设备选择上,也可以采用先进的材料和技术来提高机组的效率。
比如采用高效的超级临界锅炉技术、高温材料和陶瓷材料等,可以提高机组的热效率和机械效率,减少能源的消耗。
智能化技术的引入也可以提升机组的节能降耗能力。
通过建立智能化控制系统,对机组进行实时监测和优化调节,可以更精确地控制机组的运行参数,减少能源的浪费。
通过大数据分析和人工智能技术,可以对机组的运行状况进行预测和优化,进一步提高机组的效率和节能降耗能力。
1000MW超超临界机组的节能降耗技术可以从优化燃烧过程、热力系统优化、设备选择和智能化技术等方面进行探讨和应用。
这些技术的引入和应用,有助于提高机组的效率和节能降耗能力,推动发电行业的可持续发展。
1000MW超超临界机组节能降耗浅析
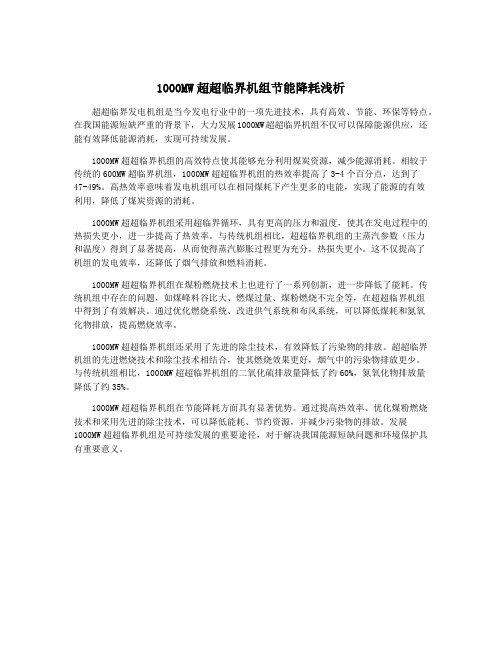
1000MW超超临界机组节能降耗浅析超超临界发电机组是当今发电行业中的一项先进技术,具有高效、节能、环保等特点。
在我国能源短缺严重的背景下,大力发展1000MW超超临界机组不仅可以保障能源供应,还能有效降低能源消耗,实现可持续发展。
1000MW超超临界机组的高效特点使其能够充分利用煤炭资源,减少能源消耗。
相较于传统的600MW超临界机组,1000MW超超临界机组的热效率提高了3-4个百分点,达到了47-49%。
高热效率意味着发电机组可以在相同煤耗下产生更多的电能,实现了能源的有效利用,降低了煤炭资源的消耗。
1000MW超超临界机组采用超临界循环,具有更高的压力和温度,使其在发电过程中的热损失更小,进一步提高了热效率。
与传统机组相比,超超临界机组的主蒸汽参数(压力和温度)得到了显著提高,从而使得蒸汽膨胀过程更为充分,热损失更小。
这不仅提高了机组的发电效率,还降低了烟气排放和燃料消耗。
1000MW超超临界机组在煤粉燃烧技术上也进行了一系列创新,进一步降低了能耗。
传统机组中存在的问题,如煤峰料谷比大、燃煤过量、煤粉燃烧不完全等,在超超临界机组中得到了有效解决。
通过优化燃烧系统、改进供气系统和布风系统,可以降低煤耗和氮氧化物排放,提高燃烧效率。
1000MW超超临界机组还采用了先进的除尘技术,有效降低了污染物的排放。
超超临界机组的先进燃烧技术和除尘技术相结合,使其燃烧效果更好,烟气中的污染物排放更少。
与传统机组相比,1000MW超超临界机组的二氧化硫排放量降低了约60%,氮氧化物排放量降低了约35%。
1000MW超超临界机组在节能降耗方面具有显著优势。
通过提高热效率、优化煤粉燃烧技术和采用先进的除尘技术,可以降低能耗、节约资源,并减少污染物的排放。
发展1000MW超超临界机组是可持续发展的重要途径,对于解决我国能源短缺问题和环境保护具有重要意义。
1000MW超超临界机组AGC和一次调频响应改进探讨
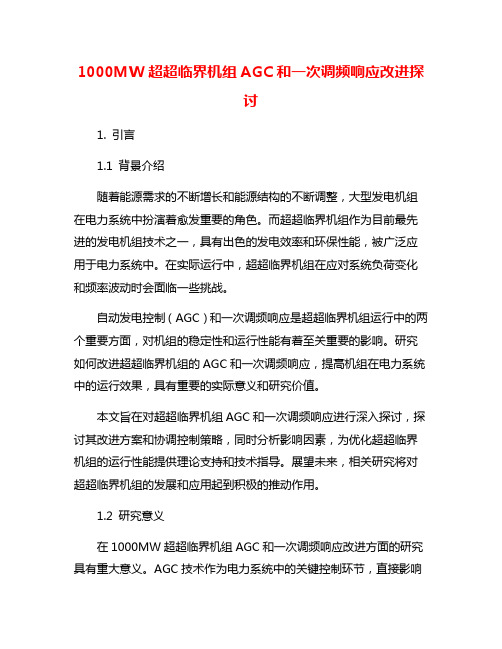
1000MW超超临界机组AGC和一次调频响应改进探讨1. 引言1.1 背景介绍随着能源需求的不断增长和能源结构的不断调整,大型发电机组在电力系统中扮演着愈发重要的角色。
而超超临界机组作为目前最先进的发电机组技术之一,具有出色的发电效率和环保性能,被广泛应用于电力系统中。
在实际运行中,超超临界机组在应对系统负荷变化和频率波动时会面临一些挑战。
自动发电控制(AGC)和一次调频响应是超超临界机组运行中的两个重要方面,对机组的稳定性和运行性能有着至关重要的影响。
研究如何改进超超临界机组的AGC和一次调频响应,提高机组在电力系统中的运行效果,具有重要的实际意义和研究价值。
本文旨在对超超临界机组AGC和一次调频响应进行深入探讨,探讨其改进方案和协调控制策略,同时分析影响因素,为优化超超临界机组的运行性能提供理论支持和技术指导。
展望未来,相关研究将对超超临界机组的发展和应用起到积极的推动作用。
1.2 研究意义在1000MW超超临界机组AGC和一次调频响应改进方面的研究具有重大意义。
AGC技术作为电力系统中的关键控制环节,直接影响着系统的稳定性和可靠性。
通过对AGC技术进行改进,可以提高电力系统的调节能力,降低系统频率波动,保证系统运行的稳定性。
一次调频响应改进方案的研究可以有效提高电力系统的频率响应速度和精度,使系统在频率扰动下更快地恢复到平衡状态,减少系统频率稳定性风险。
AGC和一次调频响应的协调控制策略能够更好地优化系统运行效果,提高系统的整体性能和经济性。
对1000MW超超临界机组AGC和一次调频响应改进的研究不仅有助于提高电力系统的稳定性和可靠性,还能够为电力系统的智能化和高效化发展提供技术支撑和理论指导。
展望未来,进一步深入研究这些方面将有助于推动电力系统的发展和升级。
2. 正文2.1 AGC技术概述AGC,即Automatic Generation Control,是自动发电控制系统。
它通过监测电网负荷变化和电厂内部运行情况,实时调节机组的输出功率,以使电网频率、有功功率与无功功率保持在稳定状态。
1000MW超超临界机组节能降耗技术探讨

1000MW超超临界机组节能降耗技术探讨
1000MW超超临界机组是一种高效、大容量的电力机组,拥有较高的发电效率和较低的燃烧损耗。
为了进一步提高其节能降耗效果,需要探索适合的技术方法。
提高燃烧效率是降低能耗的重要途径。
通过优化燃烧系统,如采用先进的燃烧器设计,调整燃烧过程参数,使燃料燃烧更充分,减少燃料在机组中的损耗。
采用先进的燃烧控制
技术,如智能控制系统,能够实时监测和调整燃烧参数,提高燃烧效率,进一步降低能
耗。
减少热损耗是提高节能效果的关键。
可以通过优化锅炉热力系统进行热损耗控制。
采
用高效的余热回收技术,将烟气中的余热转化为可再利用的能源,如用于加热水,提高循
环水温度,减少新水加热能耗;采用节能的换热设备和绝缘材料,减少热量传递和散失;
合理设置锅炉水循环系统,减少管道阻力和泵耗,提高热效率。
优化汽机组的运行管理也是节能降耗的重要手段。
通过运行优化和调整基准,控制机
组运行在最佳工况下,提高整体发电效率。
定期进行维护保养,保持设备的良好状态,减
少能源损耗。
引入先进的自动化监控系统,实现机组运行的自动化控制和优化调度。
通过实时监测
和数据分析,提高运行效率,降低能耗。
利用先进的数字化技术,如大数据分析、人工智
能等,优化机组调度和能源利用,实现智能化节能降耗管理。
1000MW超超临界机组的节能降耗技术包括优化燃烧系统、减少热损耗、优化运行管理和引入自动化监控系统等。
通过这些技术手段的综合应用,可以进一步提高机组的发电效率,降低能耗,实现节能降耗的目标。
1000MW超超临界机组节能降耗技术探讨

1000MW超超临界机组节能降耗技术探讨随着我国经济的快速发展,能源的需求量也在不断增加。
因此,能源的节约和降耗成为一项必不可少的工作。
随着超超临界技术的不断发展,其在节能降耗方面的应用也越来越广泛。
超超临界技术是一种高效的燃煤发电技术,其主要优势在于温度和压力的提高,能够充分利用煤的热值,提高发电效率。
同时,超超临界技术还具有低排放、减少碳排放等环保优势。
但是在实际运行过程中,仍然存在着一些能耗的问题。
首先,超超临界机组中的输送系统是非常耗能的。
在给煤机组中,煤的输送成本和能耗占据了整个机组能耗的较大一部分。
而且在输送过程中还会发生煤粉飞扬、堵塞等问题,造成一定的能源浪费。
其次,在煤粉的燃烧过程中也存在着能源损失。
燃烧过程中,煤粉的燃烧不完全会导致烟气中含有大量的未燃尽物质,这些物质不仅对环境造成污染,而且也会导致能量的浪费。
而且燃烧温度过高也会导致烟气中氮氧化物等有害气体的生成,对环境造成危害。
因此,在超超临界机组运行过程中,必须采取一些措施来进行节能降耗。
可以通过对输送系统的优化改进来减少能源损失,如采用密闭输送系统、优化管道布局、采用节电电机等。
同时,也可以通过对煤粉燃烧过程的优化来提高燃烧效率,减少未燃尽物质的生成,如采用高效燃烧器、优化燃烧过程等。
还可以通过余热回收技术来进一步降低机组的能耗。
在超超临界机组中,烟气中含有大量的余热,可以通过余热回收、废气热利用等技术来提高能量利用效率,并减少二次污染的产生。
同时,还可以采用热泵技术等技术来实现废热的转化利用,从而进一步降低机组的能耗。
总之,超超临界机组的节能降耗工作是一项长期而复杂的工作,需要在科技、设计、运行等多个层面进行综合考虑。
通过不断的技术升级和改进,可以不断提高机组能效,减少能源浪费,为可持续发展做出贡献。
- 1、下载文档前请自行甄别文档内容的完整性,平台不提供额外的编辑、内容补充、找答案等附加服务。
- 2、"仅部分预览"的文档,不可在线预览部分如存在完整性等问题,可反馈申请退款(可完整预览的文档不适用该条件!)。
- 3、如文档侵犯您的权益,请联系客服反馈,我们会尽快为您处理(人工客服工作时间:9:00-18:30)。
1000MW超超临界机组技术发展的探讨
摘要:根据我国对超超临界机组的技术认证,推荐超超临界汽轮机进口参数为25MPa、600/600℃,相应锅炉的设计参数为26.25MPa、605/603℃,锅炉蒸发量的选取一般与汽轮机的VWO工况相匹配。
目前我国超超临界机组已步入世界先进行列,1000MW超超临界机组采用单轴技术,蒸汽参数为25~27MPa、600/600℃,已达到世界顶级水平。
三大主要设备锅炉、汽机、发电机的生产厂家努力发展超超临界技术,促进1000MW超超临界机组技术的国产化,为我国大火电建设提供了有力的支持。
关键词:1000MW超超临界;机组技术;发展探讨
引言
我国燃煤火电机组技术发展已进入超超临界参数的时代,从长远发展趋势分析,一是常规火电机组将继续提高蒸汽参数,压力超过30 MPa ,温度超过700 ℃,机组的效率有望超过50% ;二是采用煤气化-联合循环发电方式,机组效率可以达到60%,这 2 种技术目前都处在发展之中。
现将我国1000MW 超超汽轮机技术概况分述如下。
1汽轮机本体概况
本文以某电厂二期工程#4机组为例,该机组由东方汽轮机有限公司提供,本期工程为2×1000MW国产超超临界抽凝供热机组。
汽轮机布置在15.5m运转层,为超超临界、一次中间再热、四缸、四排汽、单轴、单抽、抽凝式汽轮机,型号:C1000/908-26.25/600/600。
汽轮机组包括两台低压缸和高、中压缸各一台。
高压缸由一个单列调节级和八个压力级构成;中压缸双分流,各由六个压力级构成;低压缸四分流,各由六个压力级构成。
总热力级21级,结构级45级。
采用自密封系统(SSR),高、中压汽封漏汽供低压缸轴封封汽用,多余蒸汽溢流至八号低加,封汽用蒸汽不足时由新蒸汽补充。
调节方式为复合调节(可实现部分进汽或全周进汽),控制系统采用高压抗燃油数字电液调节系统(DEH)。
2汽轮机本体安装工艺
2.1灰浆垫块施工
本机组安装采用地脚螺栓及锚固板预埋工艺,在预埋过程中必须检查、监督土建预埋质量,务必核对各设备纵横中心线应准确无误,地脚螺栓和锚固板定位尺寸、标高及垂直度均符合设计要求。
各预留孔洞的形、位尺寸均能满足设计要求,各预埋件位置正确、数量齐全、浇灌完毕。
根据厂家灰浆垫块布置图和水泥支墩的尺寸大小,划出需要凿毛的位置和凿毛平面尺寸线。
去掉混凝土表层浮浆,沿划好的线进行凿毛,凿毛深度要求露出混凝土层,表面铲毛工作应按图样所标尺寸进行,并保证不得使基础钢筋露出。
结束后,沿铲毛表面切除地脚螺栓套筒
头部。
将台板灌浆区域弄成麻面,去掉所有的杂渣,使麻面易于粘结。
2.2低压外缸拼装
低压外缸共有四段,采用平面组合的方式进行组合,利用低压缸基础作组合平台。
清扫低压外缸各水平及垂直结合面,清扫栽丝孔,除掉防腐油,清除毛刺卷边等。
依次将低压外缸调端下半、两中部下半和电端下半落在基础上就位。
用千斤顶将垂直结合面顶紧,要求高低错位小于0.05mm,用合象水平仪观测汽缸水平扬度,同时锁紧地脚螺栓、调整不锈钢垫片,水平度要求小于0.2mm/m,在此期间要消除低压外缸下半撑脚与台板的间隙(0.05mm塞尺不入),同时调整低压缸下半横向定位销间隙,并监视汽缸水平中分面的标高。
由调侧油挡洼窝水平中心处拉一条钢丝至电侧油挡洼窝水平中心,用内径千分尺测量,使调侧、电侧的油挡洼窝、低压外缸前后轴封洼窝同心,之后将低压外缸下半中部左右找正后用垫铁将锚固板纵向中心键处临时撑牢。
栽入1/3总数垂直中分面螺栓,配入偏心定位销,测量垂直结合面的错口值小于0.05mm;拧紧1/3总数垂直中分面螺栓后,测量垂直中分面的间隙,应小于0.05mm。
用百分表检查水平结合面接缝处的错口值,应在0.02mm以内。
将汽缸垂直中分面用千斤顶顶开150mm的间隙,均匀抹汽缸涂料,垂直中分面穿入另外2/3的结合面螺栓后全部锁紧,复测汽缸与台板的间隙,应小于0.05mm。
依次起吊低压外缸上半调侧、中部、电侧上半于下外缸上,穿入水平中分面定位销之后拧紧1/3水平中分面螺栓。
2.3低压缸内下缸及部套安装
安装前应确认方向,并检查缸内的滑销及销槽,做好清理、测量、记录。
将内缸和隔板依次吊入低压下缸,拉钢丝初步调整内缸和隔板与汽缸的同心度,应在0.10mm以内。
吊入低压两端下半排汽导流环。
低压内缸下半吊入外缸内,由于该缸最终定位时是靠四块支撑键支撑,而支撑键是按实际尺寸进行装配,故此时用4根顶丝临时支撑。
测量调整中分面水平,水平度要求小于0.2mm/m。
检查下缸四角支撑垫片于低压外下缸支承面间接触情况,用0.05mm塞尺应塞不入。
2.4高压、中压外缸就位安装
检查高压、中压外缸猫爪支撑面,应保证外缸相应的猫爪支承面与支承块的接触面均大于75%,且均匀分布。
配装各猫爪支承键,然后将高压、中压外缸下半吊放于前后四只猫爪支承键下,测量并记录低压汽缸扬度的变化。
检查调端距前轴承箱端面的定位尺寸,以及距A低压缸调端轴承箱定位尺寸。
用直尺及合象水平仪测量外缸、前轴承座之横向水平及纵向扬度,横向水平允许偏差小于等于0.20mm/m,并做好记录。
高压、中压外缸上、下半合上后,自由状态下中分面间隙小于0.25mm,拧紧1/3螺栓后保证间隙小于0.03mm。
2.5高压、中压内缸就位安装
吊入高压、中压内缸,测量、调整内缸的纵向和横向水平度。
横向水平允许误差小于等于0.20mm/m。
纵向水平度以转子根据洼窝找好中心后的轴径扬度为
准。
2.6是低压缸通流部分间隙的测量及调整
将清理好的内缸、低压静叶持环及进汽导流环等件依次吊入低压外缸。
将低压转子吊入汽缸、转子按“K”值定位,“K”值系转子调阀端第2级动叶进口之轴向间隙,A低压缸K值为20mm,B低压缸K值为35mm,测量通流部分各级轴向间隙。
2.7高压缸、中压缸通流部分间隙测量
依次将高压内缸、中压内缸、各平衡活塞汽封等安装就位。
将高压转子、中压转子吊入汽缸,以整定“K”值定位。
“K”值系高压第2级动叶进口之轴向间隙17mm。
测量高压、中压、低压转子联轴器平面间距离,可适当调整高压、中压外缸及转子的轴向位置,同时兼顾前轴承座与高压、中压外缸之前端面的距离。
测量通流部分各级的轴向动静间隙,并做好记录。
以整定“K”值为起始点,检查转子的轴向移动量,应符合设计要求。
2.8全实缸下轴系找中心
首先校核A低压转子扬度并以其作为基准,检查其原始记录是否有变化,若有变化,则调整到要求扬度。
对轮找中心,从基准转子检查开始,校核A低压转子与B低压转子的对轮中心。
复找高压转子、中压转子与低压转子对轮中心。
汽缸及轴承座的扬度,以汽轮机转子的扬度为基准,整个轴系的中心,以全实缸找中为准。
检查轴系中心正确后,将各临时垫片换成永久垫片。
分别复测高压转子、中压转子、低压转子与汽缸找中用基准孔的同心度,允许用各轴承支架的调整垫片来调整转子与汽缸的同心度。
A低压转子与B低压转子联轴器找中,高压转子、中压转子与A低压转子联轴器找中,外圆错位以低压转子为准,高压转子、低压转子联轴器中心放低。
联轴器中心实测高差值与制造厂规定预留值偏差不大于0.02mm,联轴器左右中心偏差不大于0.02mm,联轴器左右张口偏差不大于0.02mm。
结束语
1000MW超超临界汽轮发电机组是目前火电设备中的主力机组之一,它的安装是一项复杂的系统工程,需要综合考虑一系列的因素,严格依据相关的规范和要求来进行;安装施工人员需要不断提升自身的专业技术水平,总结经验教训,对汽轮机组安装施工工序工艺进行不断的优化和创新,对现场安装质量水平进行严格的监督,以确保机组能安全高效地运行。
参考文献
[1]吴美艳.日本橘湾火力发电厂超超临界(suc)机组概要[J].山东电力技术.2002(02):89-91.
[2]首个百万千瓦超超临界空冷机组项目启动[J].机械.2008(09):67-68.
[3]柯文石.华能玉环电厂1000MW超超临界机组的选型与特点[J].浙江电力.2005(01):45-46.。