光学元件表面浅划痕长度的定量检测研究
光学元件表面缺陷
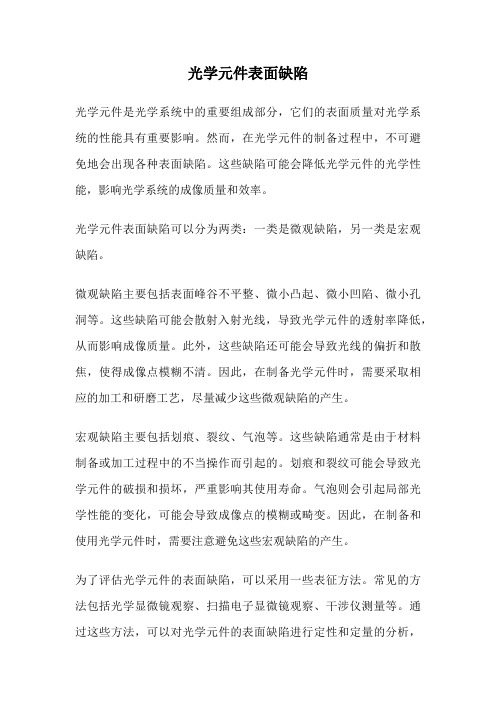
光学元件表面缺陷光学元件是光学系统中的重要组成部分,它们的表面质量对光学系统的性能具有重要影响。
然而,在光学元件的制备过程中,不可避免地会出现各种表面缺陷。
这些缺陷可能会降低光学元件的光学性能,影响光学系统的成像质量和效率。
光学元件表面缺陷可以分为两类:一类是微观缺陷,另一类是宏观缺陷。
微观缺陷主要包括表面峰谷不平整、微小凸起、微小凹陷、微小孔洞等。
这些缺陷可能会散射入射光线,导致光学元件的透射率降低,从而影响成像质量。
此外,这些缺陷还可能会导致光线的偏折和散焦,使得成像点模糊不清。
因此,在制备光学元件时,需要采取相应的加工和研磨工艺,尽量减少这些微观缺陷的产生。
宏观缺陷主要包括划痕、裂纹、气泡等。
这些缺陷通常是由于材料制备或加工过程中的不当操作而引起的。
划痕和裂纹可能会导致光学元件的破损和损坏,严重影响其使用寿命。
气泡则会引起局部光学性能的变化,可能会导致成像点的模糊或畸变。
因此,在制备和使用光学元件时,需要注意避免这些宏观缺陷的产生。
为了评估光学元件的表面缺陷,可以采用一些表征方法。
常见的方法包括光学显微镜观察、扫描电子显微镜观察、干涉仪测量等。
通过这些方法,可以对光学元件的表面缺陷进行定性和定量的分析,从而评估其光学性能。
针对光学元件表面缺陷问题,有一些解决方法和措施可供选择。
首先,可以通过优化材料制备和加工工艺,降低缺陷的产生。
例如,采用高纯度材料、精细的研磨和抛光工艺,可以有效减少微观缺陷的产生。
其次,可以采用表面修复技术,对已有的缺陷进行修复和磨光,提高光学元件的表面质量。
此外,还可以采用涂层技术,在光学元件表面形成一层保护膜,减少缺陷的散射和反射,提高光学元件的透射率。
光学元件表面缺陷是影响光学系统性能的重要因素之一。
了解和解决光学元件表面缺陷问题,对于提高光学系统的成像质量和效率具有重要意义。
通过优化制备工艺、采用表面修复技术和涂层技术等手段,可以减少和修复表面缺陷,提高光学元件的表面质量和光学性能。
光学面型检测标准

光学面型检测标准一、检测标准概述光学面型检测是光学元件质量检测的重要环节,其目的是确保光学元件的表面质量符合设计要求和实际应用需求。
本标准主要规定了光学面型的检测标准,包括表面粗糙度、表面平整度、表面缺陷和表面镀膜等方面的检测要求和方法。
二、光学面型检测标准1. 光学面型应符合设计要求,表面光滑、平整,无划痕、裂纹、气泡等缺陷。
2. 光学面型的尺寸精度应符合相关标准,如《光学零件尺寸公差》等。
3. 光学面型的表面粗糙度应符合设计要求,一般要求在Ra 0.05-0.2之间。
4. 光学面型的表面平整度应符合设计要求,一般要求在λ/4以内(λ为测试波长)。
三、表面粗糙度检测标准1. 表面粗糙度应采用轮廓仪进行测量,测量范围应覆盖整个表面。
2. 测量时应选用合适的测量参数,如采样长度、评定长度等,确保测量结果的准确性。
3. 表面粗糙度的合格标准应符合设计要求,一般要求在Ra 0.05-0.2之间。
四、表面平整度检测标准1. 表面平整度应采用干涉仪进行测量,测量时应避免外界干扰,如振动、气流等。
2. 测量时应根据不同的表面形状和材料选择合适的测试条件,如干涉仪型号、光源波长等。
3. 表面平整度的合格标准应符合设计要求,一般要求在λ/4以内(λ为测试波长)。
五、表面缺陷检测标准1. 表面缺陷应采用显微镜或自动外观检测设备进行观察和检测。
2. 检测时应根据不同的缺陷类型和大小选择合适的放大倍数和观察角度。
3. 表面缺陷的合格标准应符合设计要求和相关标准,如《光学零件外观缺陷公差》等。
六、表面镀膜检测标准1. 表面镀膜应采用光谱仪、电子显微镜等设备进行检测,了解膜层的厚度、硬度、反射率等性能指标。
2. 检测时应选择合适的测试条件和测试点分布,确保测试结果的代表性。
3. 表面镀膜的合格标准应符合设计要求和相关标准,如《光学零件表面镀膜技术条件》等。
七、光学面型检测方法1. 采用轮廓仪进行表面粗糙度测量时,应按照仪器使用说明书进行操作,并选择合适的测量参数。
光学6040外观标准划痕
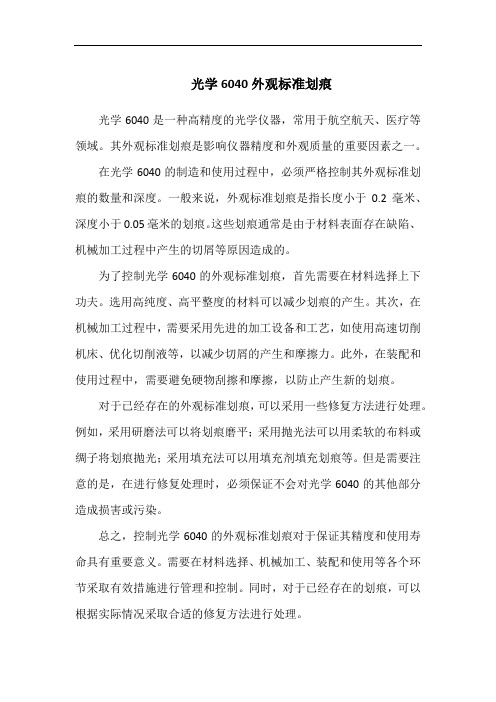
光学6040外观标准划痕
光学6040是一种高精度的光学仪器,常用于航空航天、医疗等领域。
其外观标准划痕是影响仪器精度和外观质量的重要因素之一。
在光学6040的制造和使用过程中,必须严格控制其外观标准划痕的数量和深度。
一般来说,外观标准划痕是指长度小于0.2毫米、深度小于0.05毫米的划痕。
这些划痕通常是由于材料表面存在缺陷、机械加工过程中产生的切屑等原因造成的。
为了控制光学6040的外观标准划痕,首先需要在材料选择上下功夫。
选用高纯度、高平整度的材料可以减少划痕的产生。
其次,在机械加工过程中,需要采用先进的加工设备和工艺,如使用高速切削机床、优化切削液等,以减少切屑的产生和摩擦力。
此外,在装配和使用过程中,需要避免硬物刮擦和摩擦,以防止产生新的划痕。
对于已经存在的外观标准划痕,可以采用一些修复方法进行处理。
例如,采用研磨法可以将划痕磨平;采用抛光法可以用柔软的布料或绸子将划痕抛光;采用填充法可以用填充剂填充划痕等。
但是需要注意的是,在进行修复处理时,必须保证不会对光学6040的其他部分造成损害或污染。
总之,控制光学6040的外观标准划痕对于保证其精度和使用寿命具有重要意义。
需要在材料选择、机械加工、装配和使用等各个环节采取有效措施进行管理和控制。
同时,对于已经存在的划痕,可以根据实际情况采取合适的修复方法进行处理。
芯片生产中划痕缺陷的检测与分析
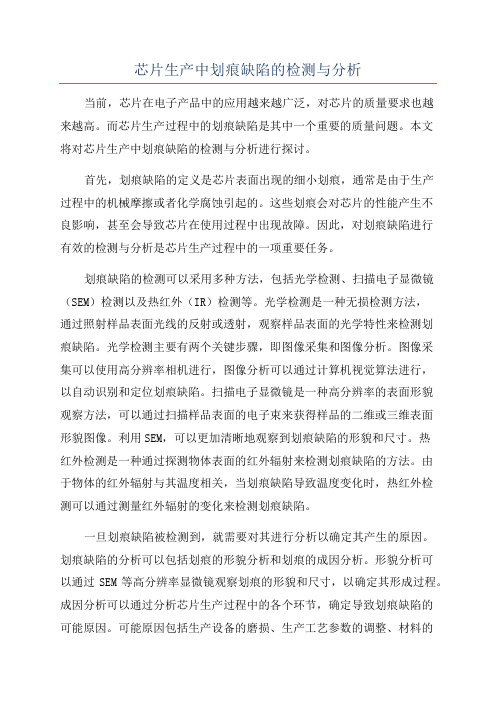
芯片生产中划痕缺陷的检测与分析当前,芯片在电子产品中的应用越来越广泛,对芯片的质量要求也越来越高。
而芯片生产过程中的划痕缺陷是其中一个重要的质量问题。
本文将对芯片生产中划痕缺陷的检测与分析进行探讨。
首先,划痕缺陷的定义是芯片表面出现的细小划痕,通常是由于生产过程中的机械摩擦或者化学腐蚀引起的。
这些划痕会对芯片的性能产生不良影响,甚至会导致芯片在使用过程中出现故障。
因此,对划痕缺陷进行有效的检测与分析是芯片生产过程中的一项重要任务。
划痕缺陷的检测可以采用多种方法,包括光学检测、扫描电子显微镜(SEM)检测以及热红外(IR)检测等。
光学检测是一种无损检测方法,通过照射样品表面光线的反射或透射,观察样品表面的光学特性来检测划痕缺陷。
光学检测主要有两个关键步骤,即图像采集和图像分析。
图像采集可以使用高分辨率相机进行,图像分析可以通过计算机视觉算法进行,以自动识别和定位划痕缺陷。
扫描电子显微镜是一种高分辨率的表面形貌观察方法,可以通过扫描样品表面的电子束来获得样品的二维或三维表面形貌图像。
利用SEM,可以更加清晰地观察到划痕缺陷的形貌和尺寸。
热红外检测是一种通过探测物体表面的红外辐射来检测划痕缺陷的方法。
由于物体的红外辐射与其温度相关,当划痕缺陷导致温度变化时,热红外检测可以通过测量红外辐射的变化来检测划痕缺陷。
一旦划痕缺陷被检测到,就需要对其进行分析以确定其产生的原因。
划痕缺陷的分析可以包括划痕的形貌分析和划痕的成因分析。
形貌分析可以通过SEM等高分辨率显微镜观察划痕的形貌和尺寸,以确定其形成过程。
成因分析可以通过分析芯片生产过程中的各个环节,确定导致划痕缺陷的可能原因。
可能原因包括生产设备的磨损、生产工艺参数的调整、材料的质量等。
通过分析划痕缺陷的形貌和成因,可以采取相应的措施来减少或消除划痕缺陷的产生,提升芯片的质量。
总之,芯片生产中划痕缺陷的检测与分析是芯片生产过程中的一项重要任务。
通过采用光学检测、SEM检测和热红外检测等方法,可以有效地检测划痕缺陷。
光学加工磨削实验报告(3篇)

第1篇一、实验目的1. 了解光学加工磨削的基本原理和工艺过程;2. 掌握光学加工磨削的常用设备和工具;3. 学会光学零件的磨削加工方法,提高磨削精度;4. 掌握光学加工磨削的质量检测方法。
二、实验原理光学加工磨削是利用磨料在高速旋转的磨具上,对光学零件表面进行磨削加工,以达到所需的光学性能。
磨削加工过程中,磨料与工件表面的摩擦、切削、抛光等作用,使工件表面达到一定精度和表面质量。
三、实验仪器与材料1. 实验仪器:光学磨床、砂轮、磨具、光学零件、测量仪器等;2. 实验材料:光学玻璃、光学塑料等。
四、实验步骤1. 砂轮准备:根据加工要求选择合适的砂轮,检查砂轮的形状、尺寸、硬度等是否符合要求;2. 磨具准备:根据工件形状、尺寸和磨削要求,选择合适的磨具;3. 工件准备:对工件进行清洗、去毛刺等处理,确保工件表面平整、无污染;4. 装夹工件:将工件安装在磨床上,调整好位置,确保工件在磨削过程中稳定;5. 磨削加工:启动磨床,调整磨削参数(如磨削速度、进给量、磨削深度等),进行磨削加工;6. 检测质量:磨削完成后,对工件进行质量检测,包括形状、尺寸、表面质量等;7. 后处理:对合格的光学零件进行清洗、烘干、检测等后处理。
五、实验结果与分析1. 实验结果:本次实验中,所加工的光学零件表面平整、光滑,符合设计要求;2. 分析:(1)磨削过程中,合理选择磨削参数对提高加工精度至关重要;(2)磨削过程中,磨具的选用和调整对加工质量有直接影响;(3)磨削完成后,对工件进行质量检测,确保加工质量。
六、实验结论1. 光学加工磨削是一种重要的光学零件加工方法,具有加工精度高、表面质量好等优点;2. 在光学加工磨削过程中,合理选择磨削参数、磨具和装夹方式对提高加工质量具有重要意义;3. 通过本次实验,掌握了光学加工磨削的基本原理、工艺过程和操作技能,为今后的光学加工工作奠定了基础。
七、实验注意事项1. 确保实验过程中安全,严格遵守实验操作规程;2. 注意磨削过程中的温度控制,避免工件变形;3. 适时调整磨削参数,确保加工质量;4. 严格按照实验步骤进行操作,确保实验结果的准确性。
光学元件表面疵病定量检测方法 显微散射暗场成像法
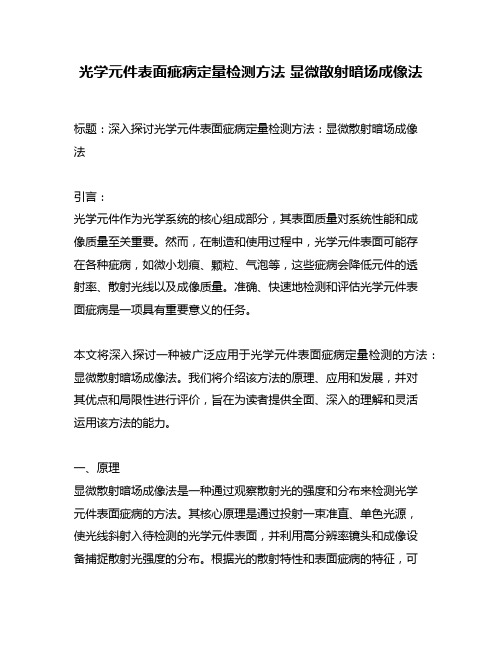
光学元件表面疵病定量检测方法显微散射暗场成像法标题:深入探讨光学元件表面疵病定量检测方法:显微散射暗场成像法引言:光学元件作为光学系统的核心组成部分,其表面质量对系统性能和成像质量至关重要。
然而,在制造和使用过程中,光学元件表面可能存在各种疵病,如微小划痕、颗粒、气泡等,这些疵病会降低元件的透射率、散射光线以及成像质量。
准确、快速地检测和评估光学元件表面疵病是一项具有重要意义的任务。
本文将深入探讨一种被广泛应用于光学元件表面疵病定量检测的方法:显微散射暗场成像法。
我们将介绍该方法的原理、应用和发展,并对其优点和局限性进行评价,旨在为读者提供全面、深入的理解和灵活运用该方法的能力。
一、原理显微散射暗场成像法是一种通过观察散射光的强度和分布来检测光学元件表面疵病的方法。
其核心原理是通过投射一束准直、单色光源,使光线斜射入待检测的光学元件表面,并利用高分辨率镜头和成像设备捕捉散射光强度的分布。
根据光的散射特性和表面疵病的特征,可以在暗场成像中观察到疵病的形态和分布情况。
通过对散射光的分析和处理,可以定量评估光学元件表面疵病的严重程度。
二、应用显微散射暗场成像法在光学元件表面疵病定量检测中具有广泛的应用。
该方法可以用于研究不同类型的疵病对光学元件性能的影响。
通过定量地分析和比较散射光的强度和分布,可以评估不同疵病的散射特性以及其对光传输的影响。
显微散射暗场成像法可以用于表面疵病的实时监测和评估。
通过与图像处理算法相结合,可以实现对疵病数量、大小和形态的快速检测和测量。
该方法还可以用于光学元件的质量控制和品质检验。
通过与标准比对,可以根据散射光的强度和分布,定量地评估光学元件的表面疵病情况是否符合要求。
三、优点和局限性显微散射暗场成像法作为一种光学元件表面疵病定量检测方法,具有以下优点:非接触性检测使得该方法适用于不同类型和形状的光学元件;高分辨率的成像设备和图像处理算法可以实现对微小疵病的精确定位和定量测量;该方法的检测速度快、操作简便,适用于工业生产中的在线检测和实时监测。
光学元件的表面划痕及其对入射激光的调制作用
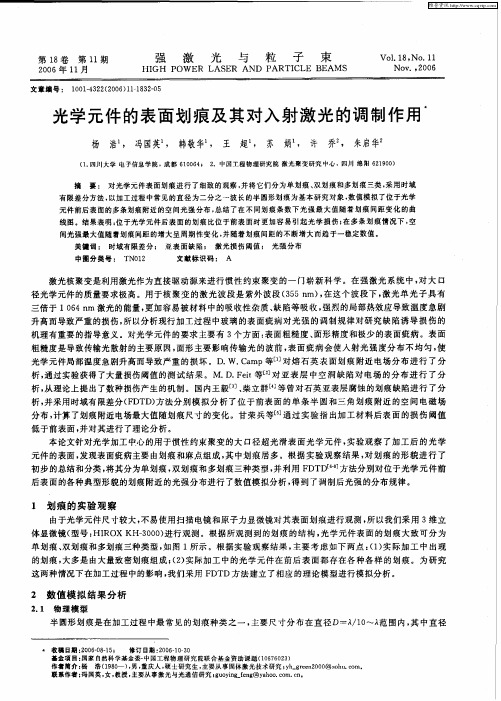
l 划 痕 的 实 验 观 察
由于光学元 件尺 寸较大 , 不易使 用 扫描 电镜 和原子 力显微 镜对 其表 面划 痕进行 观 测 , 以我们采 用 3维 立 所 体 显微镜 ( 型号 ; ROXKH一0 0进行 观测 根据 所观测 到 的划痕 的结构 , 学元件 表 面 的划痕 大 致 可分 为 HI 3 0) 光 单 划痕 、 双划痕 和多 划痕三种 类型 , 图 1所 示 。根据 实验 观察 结 果 , 如 主要 考 虑 如下 两点 :1实 际 加 工 中 出现 () 的划痕 , 大多 是 由大 量致密 划痕组 成 ;2实 际加 工 中的光 学元 件在 前 后 表 面都 存在 各 种各 样 的划 痕 。为研 究 ()
这 两种 情况下 在加工 过程 中的影 响 , 们采用 F D方法建 立 了相应 的理 论模 型进 行模 拟分析 。 我 DT
2 数 值 模 拟 结 果 分 析
2 1 物 理模型 .
半 圆形划 痕 是在加 工过 程 中最常 见 的划 痕种类 之一 , 主要尺 寸分 布 在 直 径D= 1~ 围 内 , 中直 径 /O 范 其
低 于前 表面 , 对其进 行 了理论 分析 。 并 本论 文针对 光学 加工 中心 的用 于惯性 约束 聚 变的大 口径超 光 滑表 面 光学 元 件 , 实验 观察 了加 工后 的 光 学
元 件的表 面 , 发现 表 面疵病主要 由划 痕 和麻点 组成 , 中划 痕 居多 。根 据实 验 观察 结 果 , 其 对划 痕 的 形貌 进 行 了 初 步 的总结 和分类 , 其分 为单 划痕 , 划痕 和 多划痕 三种类 型 , 利用 F TD ] 法分别 对位于 光学 元 件 前 将 双 并 D  ̄8 _方 后 表面 的各种 典型形 貌的划痕 附近 的光 强分 布进行 了数 值模 拟分 析 , 到 了调 制后光 强 的分 布规 律 。 得
光学元件表面质量的检测与评价技术研究
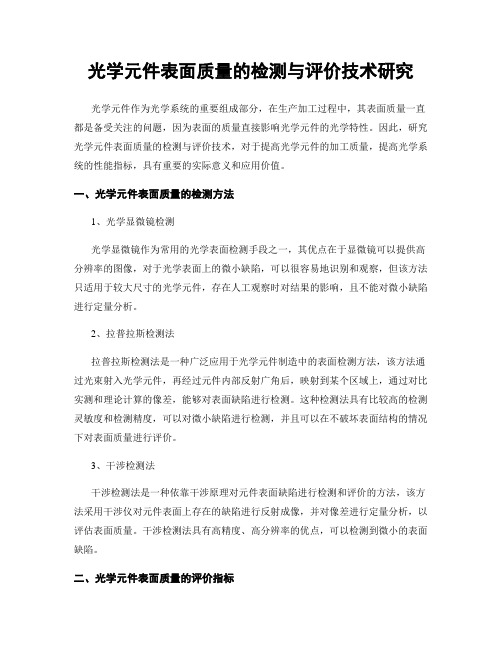
光学元件表面质量的检测与评价技术研究光学元件作为光学系统的重要组成部分,在生产加工过程中,其表面质量一直都是备受关注的问题,因为表面的质量直接影响光学元件的光学特性。
因此,研究光学元件表面质量的检测与评价技术,对于提高光学元件的加工质量,提高光学系统的性能指标,具有重要的实际意义和应用价值。
一、光学元件表面质量的检测方法1、光学显微镜检测光学显微镜作为常用的光学表面检测手段之一,其优点在于显微镜可以提供高分辨率的图像,对于光学表面上的微小缺陷,可以很容易地识别和观察,但该方法只适用于较大尺寸的光学元件,存在人工观察时对结果的影响,且不能对微小缺陷进行定量分析。
2、拉普拉斯检测法拉普拉斯检测法是一种广泛应用于光学元件制造中的表面检测方法,该方法通过光束射入光学元件,再经过元件内部反射广角后,映射到某个区域上,通过对比实测和理论计算的像差,能够对表面缺陷进行检测。
这种检测法具有比较高的检测灵敏度和检测精度,可以对微小缺陷进行检测,并且可以在不破坏表面结构的情况下对表面质量进行评价。
3、干涉检测法干涉检测法是一种依靠干涉原理对元件表面缺陷进行检测和评价的方法,该方法采用干涉仪对元件表面上存在的缺陷进行反射成像,并对像差进行定量分析,以评估表面质量。
干涉检测法具有高精度、高分辨率的优点,可以检测到微小的表面缺陷。
二、光学元件表面质量的评价指标1、表面粗糙度表面粗糙度是评价光学元件表面质量的一个重要指标,通常采用Ra值来表示,该值表示镜面表面与一条均方根偏差等于等于它的平均线之间的平均高度差。
其值越小表明表面越光滑,表面粗糙度对于光学元件的光学特性影响非常明显,因此对于专业的光学元件生产厂家来说,表面粗糙度的控制非常重要。
2、表面平整度表面平整度也是评价光学元件表面质量的重要指标之一,它用于评价元件表面的轮廓曲线,反映了元件表面在宏观尺度上的平坦程度,通常可以通过表面形貌分析仪或立体扫描仪检测获得。
3、表面平行度表面平行度表示光学元件表面对于相应平面(通常为基准平面)的垂直度。
- 1、下载文档前请自行甄别文档内容的完整性,平台不提供额外的编辑、内容补充、找答案等附加服务。
- 2、"仅部分预览"的文档,不可在线预览部分如存在完整性等问题,可反馈申请退款(可完整预览的文档不适用该条件!)。
- 3、如文档侵犯您的权益,请联系客服反馈,我们会尽快为您处理(人工客服工作时间:9:00-18:30)。
(c)阈值=0.18 划痕总长11.7mm
(d)阈值=0.21 划痕总长7mm
(e)阈值=0.23 划痕总长5mm
(f)阈值=0.25 划痕总长4.2mm
Figure 4. Change of the total length of scratch with different binaryzation threshold 图 4. 不同二值化阈值划痕总长变化情况
3. 实验研究
图3显示了疵病散射像灰度值与疵病深度的关系,图3(a)为利用显微散射暗场成像技术拍摄到的光学
48
入射光
CCD 成像系统
反射光
光学元件表面浅划痕长度的定量检测研究
入射光
CCD 成像系统 反射光
无疵病
Figure 1. Principle of dark-field scattering imaging microscopy 图 1. 显微散射暗场成像原理
4. 解决方案
虽然在图4(b)所示的二值化图像中,可以通过人工判读的方式获得浅划痕的准确长度,但是由于其中 存在大量的背景噪声,疵病定量检测分析软件将无法将划痕信息与背景噪声进行有效区分,从而导致疵 病信息的误判,导致数据处理不能正常进行。而若采用较高的二值化阈值——如0.25,二值化图像中在 去除背景噪声的同时,也会丢失大量划痕的特征信息,使得由疵病定量检测分析软件得到的划痕长度远 小于其实际值。
Fanglan Zheng, Deqiang Yu*, Hongzhen Jiang, Dong Li, Xu Liu, Yong Liu, Xiaoyu Yang, Bo Chen
Research Center of Laser Fusion, CAEP, Mianyang Sichuan Email: *yudeqiang2492927@ Received: May 29th, 2015; accepted: Jun. 20th, 2015; published: Jun. 23rd, 2015
摘要
对于光学元件表面的浅划痕缺陷,在利用显微散射暗场成像技术对其进行定量检测的过程中,由于其成 像亮度与背景光强非常接近,因此对疵病图像直接进行二值化处理将无法有效提取其中的划痕特征,从 而影响定量检测结果的准确性。为了解决上述问题,提出了一种对于浅划痕长度的准确定量分析方法, 其通过将疵病图像与背景图像相减后得到目标图像,进而对目标图像进行二值化处理和分析即可得到浅 划痕的准确长度信息。该方法对于光学元件表面疵病的定量检测具有重要的意义和应用。
Keywords
Length of Scratch, Microscopic Scattering Dark-Field Imaging Technique, Binary-State Disposal Process, Quantitative Measurement
光学元件表面浅划痕长度的定量检测研究
2. 检测原理
显微散射暗场成像原理如图1所示,光束入射至无疵病的光学元件表面时,出射光束按镜面反射原理 直接出射,CCD采集的图像为均匀的暗场图像;当光束入射至含有疵病的表面时将被疵病所散射,CCD 将采集到疵病的散射像。通过对散射像进行数字图像处理分析得到待检光学元件表面疵病的实际尺寸, 并根据位移系统的记录坐标情况明确相应疵病的位置。
郑芳兰,于德强*,姜宏振,李 东,刘 旭,刘 勇,杨晓瑜,陈 波
中国工程物理研究院激光聚变研究中心,四川 绵阳 Email: *yudeqiang2492927@
*通讯作者。
47
光学元件表面浅划痕长度的定量检测研究
收稿日期:2015年5月29日;录用日期:2015年6月20日;发布日期:2015年6月23日
Abstract
During the process of quantitatively measuring the shallow scratches defects on the optics surface using microscopic scattering dark-field imaging technique, because the imaging brightness of defect is close to the background intensity, the characteristic of shallow scratches can’t be effectively analyzed by directly disposing the defect image with binary-state process, which will influence the accuracy of the quantitative measurement result. For solving the above problem, a method for accurately measuring the length of the shallow scratches is proposed. By subtracting the defect image with the background image, the target image is obtained. Then the accurate length information can be acquired by disposing the target image with binary-state process. This method has important significance and application for the quantitatively measuring the defects on optics surface.
Copyright © 2015 by authors and Hans Publishers Inc. This work is licensed under the Creative Commons Attribution International License (CC BY). /licenses/by/4.0/
49
光学元件表面浅划痕长度的定量检测研究
元件表面上一条典型的浅划痕疵病图像,图3(b)为图3(a)中标记区域内划痕深度的轮廓仪测量结果,可以 看到,不同位置处划痕散射像的灰度值存在较大差异,该差异的变化趋势与划痕的深度走向基本一致, 即散射像的灰度值与划痕深度成正比。当图像的二值化分析阈值设置为0.25时(对应散射像灰度值为63), 深度大于图3(b)中红线标识位置的划痕像素灰度值将处理为1,即判断该位置有疵病;而深度小于该红线 标识的位置时二值化处理结果为0,即判断该位置无疵病。当采用0.16作为二值化分析阈值时(对应散射像 灰度值为40),如图3(b)中虚线标识位置所示,二值化处理后深度大于粗糙度RMS值的像素均被处理为1, 即被视为有疵病,此时,大量与元件元件粗糙度RMS一致的像素作为背景噪声出现在二值化处理后的结 果中。
对于上述疵病图像(如图4(a)所示),通过人工判读的方式得到其划痕总长为12 mm (将疵病图像导入 Matlab软件,沿划痕长度方向计算其像素数目,划痕长度 = 像素数目 × 像素尺寸)。为分析二值化阈值 (疵病信息灰度值/255)对检测结果的影响,分别采用0.16,0.18,0.21,0.23,0.25的阈值对图4(a)进行二 值化处理,结果分别如图4(b)~(f)所示。对二值化后的图像,采用与图4(a)中相同的划痕长度计算方法, 分别计算图4(b)~(f)中二值化后划痕的总长分别为12 mm,11.7 mm,7 mm,5 mm,4.2 mm。实验分析表 明:当二值化阈值小于0.18时,二值化后划痕总长与原图总长基本一致,但会引入的背景噪声,导致疵 病总数比原图多;当二值化阈值大于0.18时,背景噪声逐渐消失,但随着二值化阈值增加划痕总长减少。
+20.00
+0.00
Height (nm)
−20.00
−40.00
−60.00 0
100
200
300
400
Distance (μm)
(a)
(b)
Figure 3. Relationship between the scratch depth and the gray value of the defect image. (a) Defect image; (b) Scratch depth in Figure 3(a) measured by contourgraph 图 3. 划痕深度与散射像灰度值的对应关系。(a) 疵病图像;(b) 轮廓仪测得图(a)划痕的深度
对于利用显微散射暗场成像原理采集到的表面疵病图像,其定量检测处理的流程如图2所示,首先, 读取光学元件表面低倍疵病图像;再对其进行二值化处理,其中二值化结果为1或者0分别表明该位置有 无疵病;当判断有疵病时,计算该疵病长度,并对该疵病进行高倍成像以计算宽度。由图2可知,二值化 的结果直接关系着疵病有无的判别,该环节对定量检测结果有极大影响。若选取的二值化阈值过低或者 过高,将会导致疵病信息的误判或漏检。
50
光学元件表面浅划痕长度的定量检测研究
(a)
(b)
(c)
Figure 5. Extraction method of characteristic information of shallow scratches 图 5. 浅划痕特征信息的提取方法
疵病
读取低倍(1X子孔径 扫描图像)
二值化处理
结果为1? Y 有疵病,计算总长
N 无疵病
进行高倍扫描成像计算 宽度
Figure 2. Disposal process of software for the quantitative measurement on surface defects 图 2. 表面疵病定量检测系统软件处理流程