模块二 螺纹及蜗杆加工
车削加工技术补充课件—传递螺纹及蜗杆加工---蜗杆加工知识

牙型角。 刀头宽度: 刀头宽度应小于齿根槽宽。 纵向前角: 粗车刀一般为15º左右;精车刀为了保证牙型角正确,前角
应等于0º。 纵向后角: 一般为6º~8º。 两侧刀刃后角: 考虑蜗杆旋向和导程角。右旋车刀:左侧后角为(3º~5º)
+γ,右侧后角为(3º~5º)—γ。左旋车刀则相反。 刀尖适当倒圆。
2021/5/27
三、蜗杆车刀
蜗杆车刀与梯形螺纹车刀相似,但蜗杆车刀两侧 切削刃之间的夹角应磨成两倍齿形角。因蜗杆的导程 较大,所以在刃磨蜗杆车刀时,更应考虑导程角对车 刀前角和后角的影响,另外蜗杆的精度较高,所以一般 低速车削,用高速钢车刀。高速车削时采用硬质合金 车刀。
2021/5/27
1、蜗杆车刀的角度
在装夹车刀时一般用样板找正装夹。装夹模数较大的蜗杆车 刀,容易把车刀装歪。可采用万能量角器来找正车刀刀尖角位 置;装夹车刀时应使车刀两侧刃组成的平面处于水平状态,且 与蜗杆轴线等高,下图是用万能角度尺水平装刀。
2、垂直装刀法 适于车法向直廓蜗杆
车削法向直廓蜗杆时,必须使车刀两侧切削刃组成的平 面与蜗杆齿面垂直,这种装刀方法称为垂直装刀法,如图所 示。
装夹车刀时应使车刀两侧刃组成的平面处于既过蜗杆轴 线的水平面又与齿面垂直的状态。
2021/5/27
车阿基米德蜗杆时,本应采用水平装刀法,但由于其中一 侧切削刃的后角变小,为使曲线顺利,在粗车时也可采用垂直 装刀法,但在精车时一定要采用水平装刀法,以保证齿形正确
加工螺旋升角较大的蜗杆
如果采用水平装刀法,那么车刀一侧的刀刃将变成负前 角,而两侧刀刃的后角一侧增大,另一侧减小,会影响加工精 度和表面粗糙度,而且容易引起振动和扎刀,可采用按导程角 调节刀排装刀进行车削;也可以容易满足垂直装刀的要求。刀 排开有弹性槽,不容易产生扎刀。
蜗杆加工工艺技术
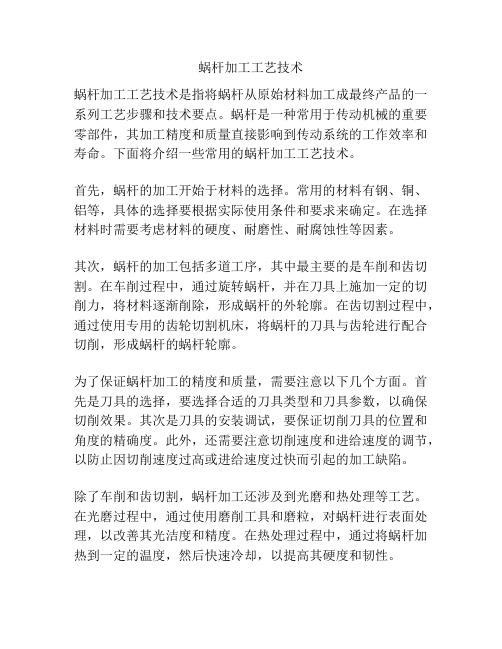
蜗杆加工工艺技术蜗杆加工工艺技术是指将蜗杆从原始材料加工成最终产品的一系列工艺步骤和技术要点。
蜗杆是一种常用于传动机械的重要零部件,其加工精度和质量直接影响到传动系统的工作效率和寿命。
下面将介绍一些常用的蜗杆加工工艺技术。
首先,蜗杆的加工开始于材料的选择。
常用的材料有钢、铜、铝等,具体的选择要根据实际使用条件和要求来确定。
在选择材料时需要考虑材料的硬度、耐磨性、耐腐蚀性等因素。
其次,蜗杆的加工包括多道工序,其中最主要的是车削和齿切割。
在车削过程中,通过旋转蜗杆,并在刀具上施加一定的切削力,将材料逐渐削除,形成蜗杆的外轮廓。
在齿切割过程中,通过使用专用的齿轮切割机床,将蜗杆的刀具与齿轮进行配合切削,形成蜗杆的蜗杆轮廓。
为了保证蜗杆加工的精度和质量,需要注意以下几个方面。
首先是刀具的选择,要选择合适的刀具类型和刀具参数,以确保切削效果。
其次是刀具的安装调试,要保证切削刀具的位置和角度的精确度。
此外,还需要注意切削速度和进给速度的调节,以防止因切削速度过高或进给速度过快而引起的加工缺陷。
除了车削和齿切割,蜗杆加工还涉及到光磨和热处理等工艺。
在光磨过程中,通过使用磨削工具和磨粒,对蜗杆进行表面处理,以改善其光洁度和精度。
在热处理过程中,通过将蜗杆加热到一定的温度,然后快速冷却,以提高其硬度和韧性。
最后,蜗杆加工还需要进行质量检测和表面处理。
通过使用专用的测量工具和设备,对蜗杆的尺寸、形状和表面质量进行检测,以确保其符合设计要求。
在表面处理中,可以进行镀铬、喷涂等处理,以提高蜗杆的耐磨性和耐腐蚀性。
综上所述,蜗杆加工工艺技术包括材料选择、车削、齿切割、光磨、热处理等一系列步骤和技术要点。
通过合理的选择和应用这些技术,可以提高蜗杆的加工精度和质量,从而提高传动系统的工作效率和寿命。
蜗杆加工工艺技术是一项复杂的机械加工工艺,要求加工过程具有高度的精度和稳定性。
下面将继续介绍相关的技术内容。
在蜗杆的加工过程中,车削是一个关键的工艺步骤。
螺纹加工方法详细讲解
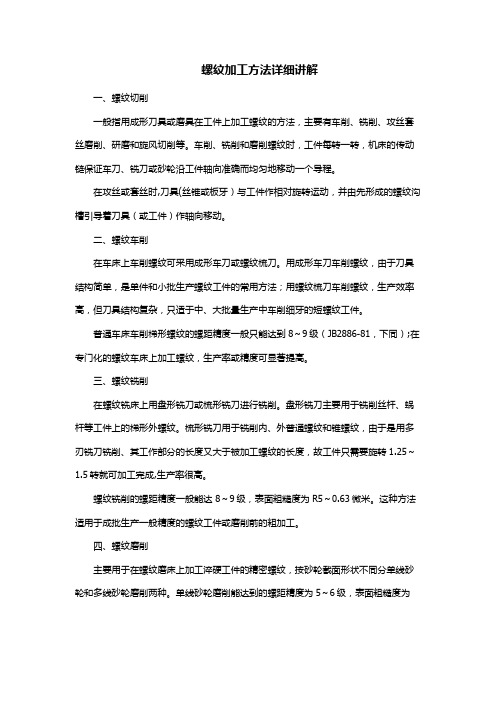
螺纹加工方法详细讲解一、螺纹切削一般指用成形刀具或磨具在工件上加工螺纹的方法,主要有车削、铣削、攻丝套丝磨削、研磨和旋风切削等。
车削、铣削和磨削螺纹时,工件每转一转,机床的传动链保证车刀、铣刀或砂轮沿工件轴向准确而均匀地移动一个导程。
在攻丝或套丝时,刀具(丝锥或板牙)与工件作相对旋转运动,并由先形成的螺纹沟槽引导着刀具(或工件)作轴向移动。
二、螺纹车削在车床上车削螺纹可采用成形车刀或螺纹梳刀。
用成形车刀车削螺纹,由于刀具结构简单,是单件和小批生产螺纹工件的常用方法;用螺纹梳刀车削螺纹,生产效率高,但刀具结构复杂,只适于中、大批量生产中车削细牙的短螺纹工件。
普通车床车削梯形螺纹的螺距精度一般只能达到8~9级(JB2886-81,下同);在专门化的螺纹车床上加工螺纹,生产率或精度可显著提高。
三、螺纹铣削在螺纹铣床上用盘形铣刀或梳形铣刀进行铣削。
盘形铣刀主要用于铣削丝杆、蜗杆等工件上的梯形外螺纹。
梳形铣刀用于铣削内、外普通螺纹和锥螺纹,由于是用多刃铣刀铣削、其工作部分的长度又大于被加工螺纹的长度,故工件只需要旋转1.25~1.5转就可加工完成,生产率很高。
螺纹铣削的螺距精度一般能达 8~9级,表面粗糙度为R5~0.63微米。
这种方法适用于成批生产一般精度的螺纹工件或磨削前的粗加工。
四、螺纹磨削主要用于在螺纹磨床上加工淬硬工件的精密螺纹,按砂轮截面形状不同分单线砂轮和多线砂轮磨削两种。
单线砂轮磨削能达到的螺距精度为5~6级,表面粗糙度为R1.25~0.08微米,砂轮修整较方便。
这种方法适于磨削精密丝杠、螺纹量规、蜗杆、小批量的螺纹工件和铲磨精密滚刀。
多线砂轮磨削又分纵磨法和切入磨法两种。
纵磨法的砂轮宽度小于被磨螺纹长度,砂轮纵向移动一次或数次行程即可把螺纹磨到最后尺寸。
切入磨法的砂轮宽度大于被磨螺纹长度,砂轮径向切入工件表面,工件约转1.25转就可磨好,生产率较高,但精度稍低,砂轮修整比较复杂。
切入磨法适于铲磨批量较大的丝锥和磨削某些紧固用的螺纹。
蜗杆轴加工
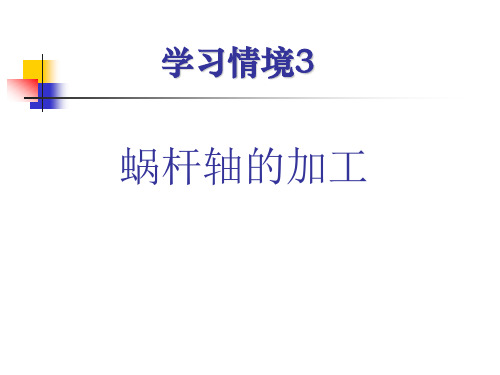
4、螺纹车削方法
1)直进法车削螺纹 2)ຫໍສະໝຸດ 进法车螺纹 3)左、右切削法车螺纹
螺纹车刀要求及安装
1、车刀的刀尖角等于螺纹牙型角α=60°; 2、其前角γ。=0°才能保证工件螺纹的牙型角,否 则牙型角将产生误差;只有粗加工时或螺纹精度要 求不高时,其前角可取 γ。=5°~20°; 3、安装螺纹车刀时刀尖对准工件中心,并用样板 对刀,以保证刀尖角的角平分线与工件的轴线相垂 直,车出的牙型角才不会偏斜。
环节三、完成任务
任务:某工厂批量生产下图所示轴零件,请为该工 件选择合适的铣削加工设备及装夹方式。
环节四、课堂小结与任务布置
小结:
铣削加工工艺范围、铣床、铣刀、铣削 加工方式及工艺特点。
课后任务:
P137 题4。
学习任务3
磨削加工认知及其应用
能力目标
能够针对不同的零件特点,正确选择磨削 加工方法
a圆柱平面铣刀 b端铣刀 c立铣刀、 d两面刃 e三面刃铣刀 f锯片铣刀、 gT形槽铣刀 h角度铣刀 I凸半圆 j凹半圆铣刀
加工复杂形成面用铣刀
四、铣削方式
铣削方式按铣刀不同可分为端铣和周铣。 端铣时切削力变化小,铣削过程平稳,加工质量 较周铣高,生产率高,但端铣适应性差,主要用于平 面铣削。 周铣能用多种铣刀铣削各种成形面,适应性广。
按不同的进给方向,又有纵磨法和横磨法之分。
① 纵磨法
原理:
磨削时工件随工作台作直线往复纵向进给运动, 工件每往复一次(或单行程),砂轮横向进给一次 。
特点:
纵磨法每次的切入量少,磨削力小,散热条件 好,但效率较低。
② 横磨法
原理:
工件不作纵向进给运动,砂轮以缓慢的速度连续或断 续地向工件作径向进给运动,直至磨去全部余量为止。
螺纹(蜗杆)的加工方法

1.蜗杆是用来配合蜗轮来传递动力的,常用于减速机构中,以传递两轴在空间90°交错的运动。
常用的蜗杆有米制(齿形角为40°)和英制(齿形角为29°)两种。
我国大多采用米制蜗杆。
如图4.13所示,阿基米德蜗杆是用刀刃角为2a=40°的梯形车刀车削出来的。
图4.13加工时刀刃处于过蜗杆轴线的水平面内,这样车削出的蜗杆轴剖面上的齿形为直线(类似于渐开线齿条)。
b)车削蜗杆的方法蜗杆和大导程螺纹车削的进刀方法有多种,如直进法、左右切削法、斜进法和切槽法等。
在数控车床上车削较大导程的蜗杆、梯形螺纹和锯齿螺纹,由于工件的齿形深,需要切除的毛坯余量多,一般是选择较低的切削速度和高速钢成形刀,使用G32和G76等指令车削,加工精度特别是表面粗糙度很难达到图纸要求,加工难度较大。
c)合理选择车削蜗杆的刀具角度,使刀具的刀尖角小于齿形角车削蜗杆刀具的刀尖角如果等于蜗杆的齿形角。
这种刀具在车削时两侧刀刃与工件侧面容易发生摩擦,甚至三个刀刃同时参加切削,易产生较大的切削力而损坏刀具。
如果选择车刀的刀尖角35 小于蜗杆的齿形角40 ,(如图2)这种车刀在车削时,可防止三个刀刃同时参加切削,减少了摩擦、切削力,能很好地避免“闷车”、“扎刀”和打刀的情况发生。
3 . 实训内容a)如图所示为40的棒料,模数为1.4mm。
齿高计算:h=2.2xm=2.9mmb)参考程序:O0002;左端外圆序号N1 G00 G40 G97 G99 M03 S600 T0101 F0.2;程序初始设置Z2.;X42.; 快进到起刀点G71 U1.5 R0.5;G71 P10 Q20 U0.3; 外圆粗车循环调用N10 G00 X10.;Z0;G01 X15. C1.;Z-27.;X20. C1.;Z-18.;X38. W-3.267;N20 W-60.; 外圆粗车循环结束G00 X100.;Z100.; 返回换刀点G00 M03 S900; 精加工X42. Z2.;G70 P10 Q20 F0.1; 外圆精加工调用G00 X100.;Z100.; 快退至换刀点M05; 主轴停转M30; 程序结束调头加工右端O0003; 程序号序号N1 G00 G40 G97 G99 M03 S600 T0101 F0.2;Z2.;X42.; 快进到起刀点G71 U1.5R0.5;G71 P30 Q40 U0.2; 外圆粗车循环调用G00 X15.;N3G01 Z0;X20. C1.;Z-18.;X38. W-3.267;W-5.; 外圆粗车循环结束N4G00 X100.;Z100.; 快退到换刀点G00 M03 S900; 外圆精加工设置X42.;Z2.; 起刀点G70 P30 Q40 F0.1; 外圆精车调用G00 X100.;Z100.; 快退到换刀点M05; 主轴停转M0; 程序暂停N2 ; 蜗杆加工G00 M03 S300 T0303;X 42.;Z-8.; 起刀点G76 P000030 Q40 R0;G76 X30.2 Z-80. P2900Q300 F4; 螺纹复合循环调用G00 X100.;Z100.; 快退到换刀点M05; 主轴停转M30; 程序结束。
蜗杆怎么加工-蜗杆的加工工艺

蜗杆怎么加工| 蜗杆的加工工艺内容来源网络,由“深圳机械展(11万㎡,1100多家展商,超10万观众)”收集整理!更多cnc加工中心、车铣磨钻床、线切割、数控刀具工具、工业机器人、非标自动化、数字化无人工厂、精密测量、3D打印、激光切割、钣金冲压折弯、精密零件加工等展示,就在深圳机械展.在经济全球化的格局下,我国制造业发展越来越迅速,齿轮的使用范围也越来越广泛,齿轮中的蜗轮蜗杆对其传递与转换的作用也是别的齿轮无法代替的。
那么蜗杆是怎么加工?它的加工工艺又是什么?本文,贤集网小编主要就是讲的这些内容!蜗杆的加工工艺1、确定毛坯的材料⑴具有优良的加工性能,能得到良好的表面光洁度和较小的残余内应力,对刀具磨损作用较小。
⑵抗拉极限度一般不低于588MPa。
⑶有良好的热处理工艺性,淬透性好,不易淬裂,组织均匀,热处理变形小,能获得较高的硬度,从而保证蜗杆的耐磨性和尺寸的稳定性。
⑷材料硬度均匀,金相组织符合标准。
常用的材料有:T10A,T12A,45,9Mn2V,CrMn 等。
其中9Mn2V有较好的工艺性和稳定性,但淬透性差;优点是热处理后变形小,适用于制作高精度零件,但其容易开裂,磨削工艺性差,蜗杆的硬度越高越耐磨,但制造时不易磨削。
2、加工定位基面的选择蜗杆定位基面:从结构上分,蜗杆有两种形式,套装蜗杆,整体蜗杆。
套装蜗杆以内孔加工基面,因此应先精加工内孔,然后以内孔为基面加工外圆及支承轴颈,螺纹的加工同样以内孔为基面,因此需要心轴。
一般精密分度蜗杆的内孔精度要求是很高的,有的需要进行研磨老保证精度。
一般精度分度蜗杆内孔应不低于1级精度,表面粗糙度不低于0.12,内孔的端面振摆应不小于0.005mm。
蜗杆装在心轴上加工时,应首先检查两端轴肩的径向跳动是否在规定允差之内,以后每道工序均应校验,在蜗杆装配时,同样要校验两端轴肩的径向跳动,心轴精度必须等于或高于与套装蜗杆相配的轴精度。
整体蜗杆以中心孔为加工基面,对中心孔的要求很高,应该有保锥,保证光洁度和接触面积,每道工序前要检查和修正中心孔,对支承轴颈应保证与中心孔同轴度和本身的几何精度,在半精加工和精加工工序前,都应检查支承轴颈的径向,跳径和端面的轴向振摆是否在公差以内。
蜗杆加工工艺与工装设计

蜗杆加工工艺与工装设计一、蜗杆加工工艺蜗杆是一种常用于传动装置中的零件,具有高精度、高可靠性和高耐磨性等特点。
蜗杆的加工工艺是指对蜗杆进行加工的一系列工艺过程。
下面将从材料选择、车削加工、热处理和磨削加工等方面介绍蜗杆的加工工艺。
1.材料选择:蜗杆通常选择高强度、高耐磨性和高韧性的材料,如45号钢、40Cr、42CrMo等。
材料的硬度要保证达到一定的标准,以保证蜗杆的传动性能。
2.车削加工:蜗杆的加工一般采用车削加工的方法。
在车削前,需要根据蜗杆的尺寸要求制定相应的车削工艺,并选择适当的车削刀具和车削参数。
蜗杆的车削一般需要进行多道次的切削,以保证蜗杆的精度和表面质量。
3.热处理:蜗杆在车削加工完成后需要进行热处理,以提高其硬度和耐磨性。
热处理一般包括淬火和回火两个步骤。
淬火后蜗杆的硬度会大幅提高,但其脆性也会增加,因此需进行回火处理以降低其脆性,提高其韧性。
4.磨削加工:磨削是蜗杆加工的最后一个步骤。
蜗杆磨削主要是为了提高其精度和表面质量。
常用的磨削方法有外圆磨削、蜗杆磨削和蜗轮磨削等。
磨削加工时需要选择合适的砂轮和磨削工艺参数,并对蜗杆进行适当的冷却,以避免高温对蜗杆的影响。
二、蜗杆工装设计蜗杆工装设计是指为了保证蜗杆加工质量和效率,设计和制造相应的工装装置。
下面将从工装的结构设计、定位与夹紧和装置制造等方面介绍蜗杆工装设计的重点。
1.结构设计:蜗杆工装的结构设计应根据蜗杆的尺寸和加工工艺要求进行设计。
工装一般由基座、定位夹具、夹紧装置和切削刀具等组成。
基座需要具备足够的刚性和稳定性,以保证工装的稳定性。
夹具和夹紧装置需要根据蜗杆的形状和尺寸进行设计,以确保其在加工过程中的固定和夹紧。
2.定位与夹紧:蜗杆在加工过程中需要进行定位和夹紧。
定位主要是确定蜗杆的加工位置和方向,通常使用定位销、定位块等来实现。
夹紧则是将蜗杆固定在工装上,通常使用夹紧器、夹爪等来实现。
定位和夹紧应根据蜗杆的加工需求和加工精度进行设计和选型。
蜗杆加工方法

在数控车床上快速车削蜗杆的方法摘要:在数控车床上车削较大导程的蜗杆、梯形螺纹和锯齿螺纹,由于工件的齿形深,需要切除的毛坯余量多,一般是选择较低的切削速度和高速钢成形刀,使用G32和G76等指令车削,加工精度特别是表面粗糙度很难达到图纸要求,加工难度较大。
针对出现的加工精度低、生产效率低等特点,说明如何有效地发挥数控车床的高精度,高速度、定位精度高、生产效率高的优势。
我们以沈阳CAK3675v 华中数控系统的车床来论述快速车削蜗杆的方法。
如图1关键词:蜗杆数控车床成形刀硬质合金宏程序蜗杆和大导程螺纹车削的进刀方法有多种,如直进法、左右切削法、斜进法和切槽法等。
以前车削蜗杆等大导程零件的方法是:选用较低主轴转速(数控车床最低速为100转/分时转动无力)和高速钢成形车刀,车削蜗杆时的生产效率低。
为解决上述问题,我认为应从刀具材料、几何形状及角度和车削方法来谈谈快速车削蜗杆和大导程螺纹的方法。
一、突破传统选择刀具的习惯,合理选择车削蜗杆的刀具角度,使刀具的刀尖角小于齿形角车削蜗杆刀具的刀尖角如果等于蜗杆的齿形角。
这种刀具在车削时两侧刀刃与工件侧面容易发生摩擦,甚至三个刀刃同时参加切削,易产生较大的切削力而损坏刀具。
如果选择车刀的刀尖角35小于蜗杆的齿形角40,(如图2)这种车刀在车削时,可防止三个刀刃同时参加切削,减少了摩擦、切削力,能很好地避免“闷车”、“扎刀”和打刀的情况发生。
二、在数控车床上使用硬质合金车刀高转速车削蜗杆成为现实以前,车削加工蜗杆和大导程螺纹,只能用高速钢车刀低速车削加工,生产效率非常低。
如果将车刀的刀尖角磨小,使车刀的刀尖角35小于蜗杆的齿形角40,可避免三个刀刃同时参加切削,切削刀显剧下降,这时可使用较高的切削速度和硬质合金车刀对蜗杆进行车削。
当工件直径、导程越大时,可获得的线速度越高,加工出的工件表面质量越好,而且生产效率明显提高。
彻底解决在数控车床不能用硬质合金刀具车削蜗杆和大导程螺纹零件。
- 1、下载文档前请自行甄别文档内容的完整性,平台不提供额外的编辑、内容补充、找答案等附加服务。
- 2、"仅部分预览"的文档,不可在线预览部分如存在完整性等问题,可反馈申请退款(可完整预览的文档不适用该条件!)。
- 3、如文档侵犯您的权益,请联系客服反馈,我们会尽快为您处理(人工客服工作时间:9:00-18:30)。
课题一 长丝杠加工
3.三针测量时,M值与轴向进给量的换 算
如图2-10所示,ab为轴向进给量,ac为半径方向 三针落差,从图上看出:
ΔM = M1- M2 = 2ac,即 ac=ΔM/ 2,设 ΔS = ab ΔS = actanα,α = 15° ΔS = 0.268ac= 0.268×ΔS = 0.134ΔM (或 ΔM = 7.46ΔS) 若 ΔM = 0.1 mm 时, ΔS = 0.134× 0.1= 0.0134 mm
二、 图样考核点
序号
考核点
1
轴的直径
2
轴的直径
3
轴的直径
4
轴的直径
5
轴的直径
6
丝杆部分的中径公差
7
轴Φ15mmmm、轴Φ18mmmm、轴Φ20mmmm、轴 Φ20mmmm、Φ22mm对中心孔的圆跳动误差
8
丝杆中径Φ19.5mm对中心孔的圆跳动误差
9
齿距误差
10
10处表面粗糙度
鉴定要求
Φ15 +0.012 mm
由挂轮箱内的挂轮架重新按要求计算和挂轮,
实现一些特殊的螺距要求。如图2-8所示。
挂轮在,挂进轮行进1行:变1换变时换,,160即30 ×工170件50挂转轮一可圈采,用
63 100
×
100 63
12mm丝杠转一圈,车出螺距为12mm的丝
杆。
课题一 长丝杠加工
二、热处理知识 1.正火 一般传动的轴类零件都必须经过正火热处理,正火是将零 件加温到临界温度以上30~50℃,保温一段时间,然后在空 气中冷却。目的是消除应力,调整硬度。细化晶粒,均匀成分, 为丝杠的调质做准备。正火一般为预先热处理,安排在粗加工 之前,调整中、低碳钢的硬度。 2.调质 淬火及高温回火称为调质,调质后,强度高,塑性、韧性 远高于正火钢,重要零件采用调质处理。丝杠调质后,全长上 弯曲不得大于1mm。调质安排在粗加工之后,半精加工之前 进行。
+0.001
Φ18 +0.012 mm
+0.001
Φ20 −0.02 mm
−0.041
Φ20 +0.015 mm
+0.001
Φ22 −0.04 mm
−0.073
Φ19.5 −0.052 mm
−0.462
0.07mm
0.20mm
(5±0.025) mm
Ra1.6µm
课题一 长丝杠加工
一、中心架支承爪失去 作用的原因
在日常生产中,中心架的使 用非常广泛,如图2-2所示。实 际应用中,经常遇到支承爪支 承工件时,不能很好地接触, 导致失去应有的作用。这主要 是由于工件直径不一样,接触 面接触不严造成的。
课题一 长丝杠加工
工件直径不一样,接触面发生了变化(见图2-3a),原支承爪的圆弧半 径小,工件现已经换成大直径,接触点只有A及B点接触,C点并未接触, A及B点会很快磨损掉,产生间隙,调整后变成大面积接触,增加摩擦面积, 增大负荷,见图2-3b放大图。图2-3c所示为原支承爪的圆弧半径大,工件 现已经换成小直径,接触点只有中心一线接触,力量不足,另外也会很快 磨损,产生间隙。
4
梯形螺纹Tr40×12-8e小
径公差
5 外圆的表面粗糙度
6 螺纹的表面粗糙度
鉴定要求
Φ40f7( −−00..00255)mm
Φ40 4h(
)mm 0
− 0.60
Φ34 8e( −−00..1663)5 mm
Φ27
4h(
)mm 0
− 0.82
Ra≤0.8μm Ra≤1.6μm
课题一 长丝杠加工
一、长丝杠加工工艺 1.保障丝杠与螺母的牙形一致 采用专用样板或对刀样板校对刃磨的螺纹车刀角度,使车 刀形状符合样板。当车刀背前角不为0°时,应通过计算修 整刀尖角。 2.机床间隙的调整 加工前应调整床鞍与导轨间隙,中、小滑板镶铁配合间隙, 对合螺母与丝杠间隙。 3.工序集中与分散原则 粗车与精车工序或工步应分开,使用跟刀架和适合的冷却 液进行粗车和精车。 4.正确的加工方法 选择正确的车削和装夹丝杠的方法,尽量减少零件的变形。
3.跟刀架支承爪在车削过程中的调整 (1)支撑爪要无间隙接触工件。 (2)跟刀架支承爪开始时支撑过松造成 工件的竹节形形状。
课题一 长丝杠加工
四、中心架过渡套筒的作用
如图2-6所示为中心架过渡套筒的应用,在细长轴弯曲时,可以在弯曲 的细长轴的外圆套上中心架过渡套筒,然后用百分表将过渡套筒的外圆轴 线找正与主轴轴线重合,如图2-6a所示。找正时,要反复调整螺丝3,每 调整一次都要用百分表找正,如此反复几次,直至找正为止。找正后,架 上中心架(见图2-6b),就可以车削了。中心架过渡套筒的作用就是可以 将弯曲的轴架在中心架上,实现被车削的目的。
课题一 长丝杠加工
一、图样分析
中滑板丝杆要满足机床中滑板转动的使用要求,在较长 丝杆上,5处外圆有公差要求。有多处沟槽,使工件刚度减 弱,更加容易振动。主要外圆表面对丝杆的同轴度有较严的 要求,保证中滑板丝杆的整体直线度要求。中滑板丝杆上轴 向尺寸繁多,注重轴向长度尺寸的公差及未注公差的准确性。
课题一 长丝杠加工
前顶尖,鸡心夹头,回转顶尖,固定合金顶尖 ,中心架,活扳手、旋具等常用工具
课题一 长丝杠加工
三、操作步骤
操作步骤 工艺要点
1. 装夹外圆
(1)车削 端面,控制长 度尺寸为730 ㎜(粗车后调 质)
钻两侧 基准中心 孔
(2)钻两 侧中心孔
(3)研磨 中心孔
加工简图
课题一 长丝杠加工
三、操作步骤
操作步骤
课题一 长丝杠加工
二、中心架支承爪间隙的调整
1.三爪中心架支承爪的调整顺序 中心架的支承一般先在下面两爪调整,轻轻调整下 面两爪的间隙,然后再调整上爪的间隙即可。 图2-4a所示为工件A点在上,B点在下,而图2-4b 所示为工件转过半圈后B点在上,A点在下,支撑 点位置未变,工件受扭曲,工件将被扭下来。中心 架的上爪一般作用为防止跳动。正确的调整方法为:
工艺要点
2.
用两顶尖装夹
−0.02
,在φ20 −0.041mm
处车基准面架上中
心架进行支撑
(1)粗车右 侧各部位
(2)粗车左 侧各部位(掉头时 ,在φ20 −−00..00241mm 的外圆上移动一下 支撑位置处
1.采用两 顶尖与鸡心 夹头的六点 定位
2.放置中 心架辅助支 撑后,掉头 进行左、右 粗车
操作步骤 工艺要点
4. 用两顶尖 1.移动中
装夹,用中心 心架辅助
架支撑Φ22−−00..00473
支撑Φ22
−0.04 −0.073
mm部位
mm部位
(1)粗车
2.精车削
Tr22螺纹
螺纹
(2)精车Tr22 螺纹
加工简图
课题一 长丝杠加工
三、操作步骤
操作步骤 工艺要点
5. 用两顶尖 掉头, 装夹,用中心 左右精车 架支撑Φ22−−00..00473 其余各部
课题一 长丝杠加工
三、跟刀架支承爪间隙的调整
1.跟刀架的结构 日常生产中,在车细长轴时经常要用到跟 刀架,如图2-5所示。其用途是:跟刀架 的支承爪紧随刀尖移动,形成三点(用二 爪跟刀架)或四点(用三爪跟刀架)支撑 工件。
2.跟刀架支承爪初始支撑 当车刀车出一段外圆后,即将跟刀架支承 爪支撑在这段外圆上。
课题一 长丝杠加工
三、梯形螺纹中 径检验方法
1.三针量针 三针测量梯形螺纹 中径时,其操作方法如 图2-9a、b所示。当螺 距较大时,千分尺的测 量杆直径细不容易同时 跨住两根量针,此时可 采用公法线千分尺,见 图2-9c所示,测量方法 见图2-9d所示,三针测 量M尺寸,见图2-9e所 示。
课题一 长丝杠加工
课题一 长丝杠加工
一、工艺分析 1.工艺要点说明 工件采用两顶尖支撑,架上中心架,中心架部位需精车出 支撑轴颈,光滑而无跳动,中心架架上后保证工件各项精度 要求。图2-1所示的中滑板丝杆是在调质后进行半精车和精车。 2.基本操作描述 车平两端面,钻中心孔,控制全长730mm→研磨两端中心 孔→两顶尖支撑,在Φ20处车一段支撑轴颈,供中心架支撑 →粗车右侧各部位→粗车左侧各部位→粗车Tr22×5LH的螺 纹→精车Tr22螺纹→精车右侧其余各部位→精车左侧其余各 部位→各部位倒角。
(1)下面两侧的支承爪先进行调整,主要调整 工件轴心线与主轴轴线同轴度,因此支撑力应均等 而且适度,轻型工件可以通过旋转调整。
(2)上爪起抗衡主切削力Fc的作用,在车削后, 没有上爪的支撑,工件与刀具之间产生的主切削力 Fc 会使工件抬起,尤其值得提出的是,下两爪调整 后可以锁紧,但上爪一般较少锁紧,准备随时调整 间隙,尤其一旦发生振动或过热咬死时,都要及时 调整上支承爪的位置。
即轴向进给 0.0134 mm 时, M 值减小 0.1 mm。 ΔM = 7.46ΔS 可以记为: M 值的落差是轴向进给 量的 7.46 倍。
同理:蜗杆 M 值的落差是轴向进给量的 5.49 倍。 普通螺纹 M 值的落差是轴向进给量的 3.46 倍。
课题一 长丝杠加工
一、工艺分析
1.注意事项 (1)需要进行工件矫直,用反击法校正零件直线度。 (2)先进行全部的粗加工。 (3)车后应将工件垂直吊起,消除内应力并防止弯曲。 (4)丝杠的两端中心孔应进行圆度、表面粗糙度的修整。 (5)采用跟刀架进行螺纹牙形的粗、精车。 2.三针计算 (1)30°梯形螺纹三针直径: dD=0.518p=0.518×12=6.216mm ,查表为6.212mm。 (2)30°梯形螺纹M值计算: M=d2+4.864dD-1.866p=34+4.864×6.212-1.866×12=41.823 mm 将则中M值径为公Φ差4值1 附++00上..6169,m为mΦ,41在.8此23范围−−00..内16635合m格m。