第四章核燃料组件
核反应堆结构-4
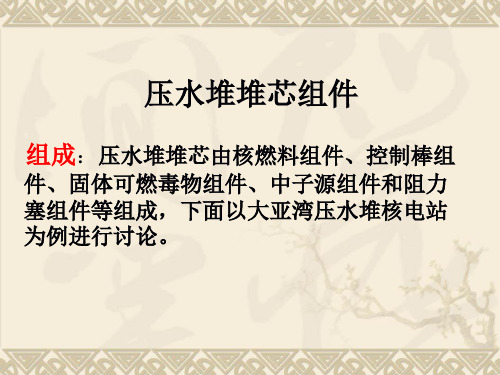
控制棒导向管 : 在标准的17×17燃料组件中,导向管占据24个栅元, 它们为控制棒插入和抽出提供导向的通道,导向管 由一整根锆-4合金管子制成.其下段在第一和第二 格架之间直径缩小,在紧急停堆时,当控制棒在导 向管内接近行程底部时,它将起缓冲作用,缓冲段 的过渡区呈锥形,以避免管径过快变化,在过渡区 上方开有流水孔,在正常运行时有一定的冷却水流 入管内进行冷却,而在紧急停堆时水能部分地从管 内流出,以保证控制棒的冲击速度被限制在棒束控 制组件最大的容许速度之内,又使缓冲段内因减速 而产生的最大压力引起导向管的应力不超过最大许 用应力.缓冲段以下在第一层格架的高度处,导向 管扩径至正常管径,使这层格架与上面各层格架以 相同的方式与导向管相连.
导向管与下管座的连接借助其螺纹塞头来实现,螺 纹塞头的端部带有一个卡紧的薄圆环,用胀管工具 使圆环机械地变形并镶入管座内带凹槽的扇形孔中; 螺纹塞头旋紧在合金端塞的螺孔中将导向管锁紧在 下管座中. 组件重量和施加在组件上的轴向载荷,经导向管传 递,通过下管座分部到堆芯下栅格板上.燃料组件 在堆芯中的正确定位由对角线上两个支撑脚上的孔 来保征,这两个孔和堆芯下栅格板上的两个定位销 相配合,作用在燃料组件上的水平载荷通过定位销 传送到堆芯支承结构上.
核燃料组件的"骨架"结构
前面已经讲到17×17型压水堆核燃料组件是由 包括定位格架,控制棒导向管,中子通量测量管, 上管座和下管座所组成的"骨架"结构和核燃料元 件组成. 定位格架 作用:燃料组件中,燃料棒沿长度方向由八层格架 夹住定位,这种定位使棒的间距在组件的设计寿期 内得以保持.格架的加紧力设计成既使可能发生的 振动减到最小,又允许有不同的热膨胀滑移,也不 致引起包壳的超应力. 结构外形:格架由锆-4合金条带制成,呈17×17正 方栅格排列,条带的交叉处用电子束焊双边点焊连 接,外条带比内条带厚,内条带的端部焊在条带上, 外条带端部由三道焊缝连接;使格架能在运输及装 卸操作过程中很好地保护燃料棒.
核燃料组件制造关键技术与成套装备_概述及解释说明

核燃料组件制造关键技术与成套装备概述及解释说明1. 引言1.1 概述核燃料组件制造是核能领域的关键环节,涉及到核电站安全运行和可持续发展。
核燃料组件作为核反应堆的重要部分,承载着控制和释放核能的任务。
因此,对于核燃料组件的制造关键技术和成套装备的研发与应用具有重要意义。
1.2 文章结构本文将首先介绍核燃料组件制造关键技术,包括制造流程、材料选择与处理以及质量控制与检测方法。
其次,我们将探讨成套装备在核燃料组件制造中的应用与发展,包括设备概述、技术创新与进展以及自动化程度提升与未来趋势。
然后,我们会深入解释说明核燃料组件制造的重要性及挑战,并从能源领域的关键地位、外界环境对制造过程的影响以及技术瓶颈与突破点三个方面进行分析。
最后,我们将总结主要观点,并对未来核燃料组件制造的发展做出展望。
1.3 目的本文旨在全面概述核燃料组件制造关键技术与成套装备的现状和发展趋势,深入探讨其重要性及挑战,并为核能领域从业人员、研究人员和政策制定者提供参考和借鉴。
通过本文的阐述,读者可以全面了解核燃料组件制造相关知识,并对未来发展方向做出准确判断。
2. 核燃料组件制造关键技术:2.1 制造流程:核燃料组件制造的主要流程包括材料选择与处理、结构设计与加工、装配和测试等环节。
首先,根据具体应用需求和安全标准,选择适合的材料作为核燃料组件的基础材料,如铀、钚等。
然后进行材料处理,包括提纯、合金化和成型等工艺,以确保材料达到所需的物理、化学性能。
接下来,在结构设计阶段,需要考虑到核燃料组件在实际运行中所承受的高温、辐射和压力等因素,并进行相应的加工工艺设计,如焊接、锻造和复合等技术。
最后,将经过加工处理的各个部分进行装配,并进行必要的测试和验证,确保核燃料组件符合规定的性能参数。
2.2 材料选择与处理:核燃料组件制造中材料选择与处理是非常重要且复杂的过程。
首先需要选择适合核反应堆使用环境下能够具备良好物理特性并耐受高温高压辐射条件的重金属元素作为基础材料。
核工业基础知识

第三章 核电站动力装置
核工业基础知识
(四)稳压器 现代大功率压水堆核电站都采用电热式稳压器。 电热式稳压器一般采用立式圆柱形结构。用来 抑制压力升高的喷雾器安置在稳压器上部蒸汽空间 的顶端。限制压力降低的电加热元件安置在稳压器 下部水空间内。
23
第三章 核电站动力装置
核工业基础知识
三、一回路辅助系统 (一)化学和容积控制系统 核电站的化学容积控制系统的作用是调节一回 路系统中稳压器的液位,以保持一回路冷却剂容积; 调节冷却剂中的硼浓度,以补偿反应堆在运行过程 中反应性的缓慢变化;通过净化冷却剂及添加化学 药剂,保持一回路的水质。 (二)主循环泵轴密封水系统 (三)硼回收系统 (四)补给水系统 (五)取样系统及分析室
9
核工业基础知识
第二章 核反应堆
反应堆本体的组成和结构
第三节
反应堆总体结构均可分为反应堆本体和回路系统 两部分。 反应堆本体通常由反应堆(压力)容器、堆芯 (活性区)、堆内构件及控制棒驱动机构等几部分组 成,如图3所示。
10
核工业基础知识
第二章 核反应堆
图 3 反 应 堆 的 构 成
11
核工业基础知识
核工业基础知识核工业基础知识前言第一章核燃料循环第二章核反应堆第三章核电站动力装置第四章核燃料的开采冶炼和浓缩第五章核燃料元件的制造第六章乏燃料后处理第七章带电粒子加速器第八章核聚变装置第九章核设施退役第十章放射性废物的贮存处理和处置核工业基础知识核工业基础知识简要介绍核燃料循环体系核反应堆核动力堆装置核燃料开采冶炼和浓缩核燃料元件制造核燃料后处理带电粒子加速器核聚变装置核设施退役及放射性三废处理处置等
18
第三章 核电站动力装置
核工业基础知识
二、一回路系统及主要设备 压水堆核电站的一回路系统除了反应堆之外的 主要设备有:蒸汽发生器、冷却剂主循环泵、稳压 器及主管道等。 (一)反应堆压力容器 压力容器是压水堆核电站中最关键的高温高压 设备。
第四章 核燃料
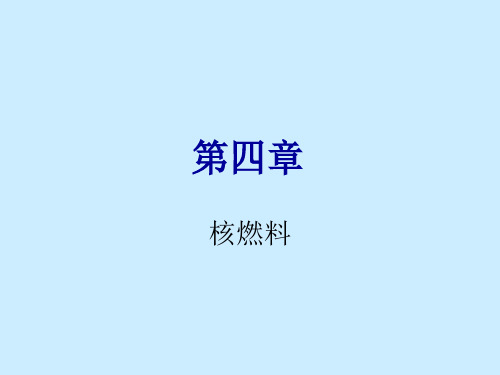
4.2.1 .1 二氧化铀的物理性能
(1)晶体结构 (2)密度 (3)熔点 (4)比热容 (5)导热率 (6)热膨胀 (7)蒸汽压
二氧化铀的晶体结构
二氧化铀的晶体结构
图4-2 铀——氧系平衡图
相图中的垂线代表化合物UO2(O/U=2.0)和
U4O9 (O/U=2.25) , O/U比较大的其它化合物 是U3O8 和UO3。
4.2 二氧化铀燃料
优点: a. 熔点高,晶体结构为面心立方(FCC),各向
同性,并且从室温到熔点没有相变。 b. 高温稳定性和辐照稳定性好。 c. 化学稳定性好,与高温水不起作用,与包壳相 容性好。 d. 在1000℃以下能包容大多数裂变气体。 e. 有适中的裂变原子密度,非裂变组合元素氧的 热中子俘获截面低(0.002靶恩)。 缺点: a. 导热系数小,使芯块的温度梯度过大。 b. 机械强度低、脆,在反应堆条件下易裂,且加 工成型困难
232 90
233 233 Th 01n 233 Th Pa 90 91 92 U T 1 2 27.4天 T 1 2 22.2分
238 92
239 239 U 01n 239 U Np 92 93 94 Pu T 1 2 2.35天 T 1 2 23.5分
铀合金
加入适量铜,可以稳定α相;
加入钼、锆、铌可以稳定γ相。 含铀量60%的锆-铀合金曾用于希平港动力反应堆,
U-ZrH用于脉冲堆,
铀- 锆合金仍是一种有希望的金属燃料。美国的快 堆一体化燃料循环研究就是用金属型的铀-钚-10%
锆合金作钠冷快中子堆燃料的。 铀-钼合金也得到很大的重视,开展了深入的研究工 作。
【2024版】第四章核能材料
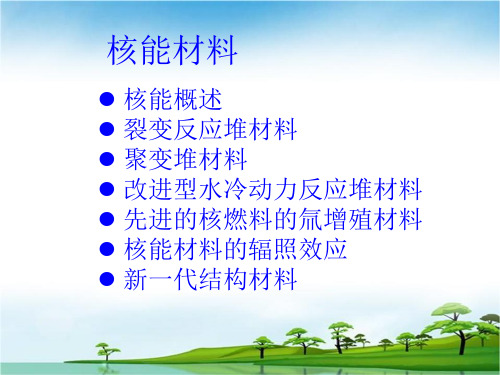
2.3裂变堆类型
裂变反应根据堆内中子能量大小,分为快中子反 应堆和热中子反应堆等堆型。以水作为慢化剂的热中 子反应堆根据氢原子中的中子数不同,可以分为轻水 堆(LWR) 、重水堆等;轻水堆根据冷却剂状态不同可 以分为压水堆、沸水堆等。
压水堆(PWR):使用加压轻水作冷却剂和慢化剂 ,水压约15.5MPa,水在堆内不沸腾,驱动汽轮发电 机组的蒸汽在反应堆以外产生,借助于蒸汽发生器实 现,蒸汽压力为6~7MPa。燃料为浓缩铀或MOX燃 料。
锆-2.5铌合金主要成分是2.5%-2.8%(质量) Nb和1000×10-6-1300×10-6O.添加Nb可以使合 金得到强化并提高耐蚀性,少量的氧也可以强化 合金,在合金重要严格的控制有害杂质氢和碳、 氯和磷。前者容易造成合金氢化开裂;后者会降 低其断裂韧性。
锆-2.5铌合金主要性能:
微观组织和断裂韧性
2 裂变反应堆材料
2.1裂变原理和裂变反 应堆 铀-235或钚-239
等重元素的原子核在 吸收一个中子后发生 裂变,分裂成两个质 量大致相同的新原子 核,同时放出2~3个 中子,这些中子又会 引发其他的铀-235或 钚-239原子核裂变, 如此形成链式反应。
反应堆结构与核燃料
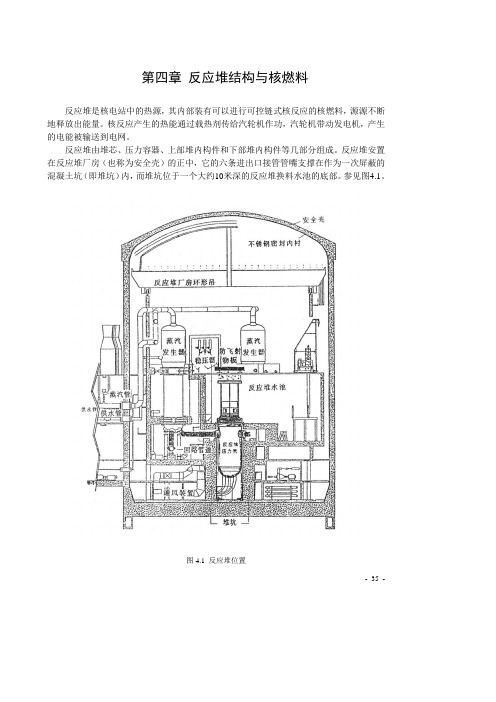
第四章反应堆结构与核燃料反应堆是核电站中的热源,其内部装有可以进行可控链式核反应的核燃料,源源不断地释放出能量。
核反应产生的热能通过载热剂传给汽轮机作功,汽轮机带动发电机,产生的电能被输送到电网。
反应堆由堆芯、压力容器、上部堆内构件和下部堆内构件等几部分组成。
反应堆安置在反应堆厂房(也称为安全壳)的正中,它的六条进出口接管管嘴支撑在作为一次屏蔽的混凝土坑(即堆坑)内,而堆坑位于一个大约10米深的反应堆换料水池的底部。
参见图4.1。
图4.1 反应堆位置- 35 -- 36 -图4.2 反应堆剖面图- 37 -图4.2是压水堆的结构简图,它可分为以下四部分:● 反应堆堆芯● 堆内构件● 反应堆压力容器和顶盖● 控制棒驱动机构4.1 反应堆堆芯4.1.1 堆芯布置核反应堆的堆芯位于压力容器中心,由157个几何形状及机械结构完全相同的燃料组件构成,核反应区高3.65m ,等效直径3.04m 。
燃料核裂变释放出来的核能立即转变成热能,并由冷却剂导出。
在典型的燃料管理方案中,初始堆芯按燃料组件浓缩度分成三个区。
所谓燃料浓缩度也称富集度或丰度,是指燃料中235U 同位素在铀的总量中所占比例。
在堆芯外区放置浓缩度高的燃料组件,浓缩度较低的燃料组件则以棋盘状排列在堆芯的内区,如图4.3所示。
通常每年进行一次换料,更换约三分之一燃料组件,称为一个燃料循环。
换料原则是将燃耗最深的燃料组件取走,在外区加入新燃料组件,而其余组件在堆芯中央重新布置,使功率分布尽可能均匀。
在第六循环之前新加入燃料的浓缩度均为3.25%。
为满足不断增长的发电需求,从第七循环开始新换燃料的富集度改为3.7% 。
按照规划,今后还将采用长燃耗循环,即18个月换料方式,届时新换燃料的富集度将提高到4.45% 。
图4.3 堆芯分区布置(第一循环)- 38 -4.1.2 燃料组件大亚湾核电站目前所用的AFA-2G 型燃料组件由骨架和燃料棒组成,呈17×17正方形栅格排列,总共有289个栅格,其中264个装有燃料棒。
第四章核能材料.解析

4.改进型水冷动力反应堆材料
4.1 压水堆堆芯新材料 压水堆堆芯部件的工作条件十分苛刻,因而 对其运行的可靠性、经济性和安全性要求越来越 高。为了满足这种要求,一方面堆芯设计不断更 新,另一方面制造部件所使用的材料也将随之改 进。目前没根据核能发展需要而开发的压水堆堆 芯新型材料最具有典型的锆合金包壳材料。水冷 动力堆堆芯的另一种改进型材料是可燃毒物材料 。研究表明,Gd2O3是一种良好的材料。
4.1.2 锆-2.5铌合金
锆-2.5铌合金主要成分是2.5%-2.8%(质量) Nb和1000×10-6-1300×10-6O.添加Nb可以使合 金得到强化并提高耐蚀性,少量的氧也可以强化 合金,在合金重要严格的控制有害杂质氢和碳、 氯和磷。前者容易造成合金氢化开裂;后者会降 低其断裂韧性。 锆-2.5铌合金主要性能: 微观组织和断裂韧性 晶粒结构由β-Zr薄膜围绕α晶粒组成。该薄膜 可以连续或轻度破损;α粒子基极基本上呈现平行 于周向的织构;位错密度等于10-14,断裂韧性大 于250MPa.m1/2。
核能就是指原子能,即原子核结构发生变化时释放出的 能量,包括重核裂变或轻核聚变释放的能量。1938年德国化 学家哈恩首次揭示了核裂变反应,他通过研究发现,铀235在中子的轰击下分裂成两个原子核,同时放出三个中 子,这一过程伴随着能量的放出,这个过程就是核裂变反 应,放出的能量就是核能。物质所具有的原子能比化学能 大几百万倍以至上千万倍。
238U和232Th资源丰富,为核能的利用提供 了广阔的材料来源。此外,由于铀238和钍232是 能够转换成易裂变核素的重要原料,且其本身在 一定条件下也可产生裂变,所以习惯上也称其为 核燃料。聚变燃料包含氢的同位素氘、氚,锂和 其它化合物等。核工程材料是指反应堆及核燃料 循环和核技术中用的各种特殊材料,如反应堆结 构材料、元件包壳材料、反应堆控制材料、慢化 剂、冷却剂、屏蔽材料等等。核材料必须置于设 有多重实体屏障的保护区内,并实行全面管制与 统计,防止损失与扩散。
第四章-核燃料
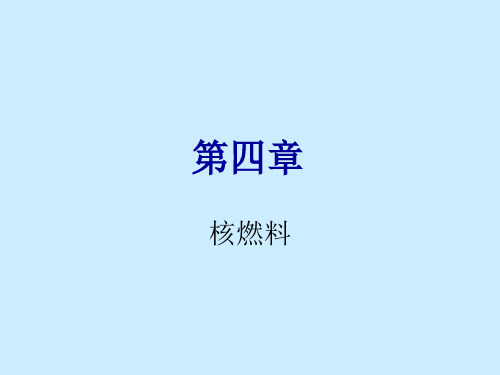
3) 弹性模量-与温度、气孔率有关。室温时约为2.1-2.3×105MPa,随温度 增加,该值呈直线下降,系数为3.09×10-2/K;随气孔率增加,弹性模 量减小。关系式如下:
EP = E0(1-2.62P)
(4-3)
式2.中26:×1P0为5M气P孔a。率,E0为室温时理论密度的UO2的弹性模量,为
4.1.2 陶瓷型燃料
铀、钚、钍与非金属元素(氧、碳、氮等) 的化合物组成了陶瓷型核燃料。由于这些燃 料有很高的熔点,无相变,与包壳和冷却剂 相容性好,辐照稳定性好等有利条件,动力 堆普遍采用这类材料作核燃料。
陶瓷型核燃料有氧化物型、碳化物型及氮化 物型。氧化物型应用最普遍。各种的性能对 比参见表4-1。
优点: a. 熔点高,晶体结构为面心立方(FCC),各向
同性,并且从室温到熔点没有相变。
b. 高温稳定性和辐照稳定性好。 c. 化学稳定性好,与高温水不起作用,与包壳相 容性好。
d. 在1000℃以下能包容大多数裂变气体。 e. 有适中的裂变原子密度,非裂变组合元素氧的 热中子俘获截面低(0.002靶恩)。 缺点: a. 导热系数小,使芯块的温度梯度过大。 b. 机械强度低、脆,在反应堆条件下易裂,且加 工成型困难
蒸汽压
UO2的汽化现象比较复杂,因为它与O/U比, 以及气氛中的氧分压等因素有关,具有一定 氧/铀比的固态UO2的汽化机制至少在2000K 以下主要是升华,蒸汽压可参见表4-2:
4.2.1.2 力学性能
UO2在常温下是脆性陶瓷体,断裂强度约为 110MPa,在韧脆转变温度(~1400℃)以上,随 着温度升高,强度急剧降低,同时出现塑性。
热膨胀
二氧化铀的热膨胀系数为10.8×10-6/℃。 2000℃以上体膨胀大大增加,体膨胀由下式 给出:
- 1、下载文档前请自行甄别文档内容的完整性,平台不提供额外的编辑、内容补充、找答案等附加服务。
- 2、"仅部分预览"的文档,不可在线预览部分如存在完整性等问题,可反馈申请退款(可完整预览的文档不适用该条件!)。
- 3、如文档侵犯您的权益,请联系客服反馈,我们会尽快为您处理(人工客服工作时间:9:00-18:30)。
•
在金属铀中由于裂变产物中的气体元素几乎都是包容而不释放出来, 所以肿胀显著。虽然研究了改善办法,但也有一定限度,即使做成浓 缩铀,如果只是单纯提高235U的浓度,由于金属学上的寿命首先就达 到了,燃耗深度也超不过几千兆瓦· 日/吨。另外,由于铀的α-β相变点 是668℃,所以燃料的中心温度被限制在这个温度以下,这也是以金属 铀作为动力堆燃料的一大缺点。由于这些原因,动力堆中目前基本不 采反应堆
对核燃料元件的要求:
•
良好的物理、化学、力学和抗辐照稳定性。燃料元件在反应堆内复杂的条件下 使用寿命达3~4年,工作及储存空间要保持外形尺寸稳定。包壳要尽可能的薄, 但应有足够的强度,并有足够的抗腐蚀性能,不与核燃料及核裂变产物发生有 害的化学作用,能够长期包容放射性物质; 所有材料的热中子吸收截面要小,且不含中子吸收截面大的杂质。 具有良好的热工水力学和热交换特性,燃料元件的结构设计要有利于热量传递, 具有较大的导热面积; 要求所有设计的燃料元件的在堆芯中能够互换位置,以利于有效的堆芯燃料管 理,并力求结构简单,易于加工; 为了尽量充分、经济地利用核能,反应堆运行应使核燃料的燃耗[又叫燃耗深度: 即单位质量的核燃料产生的核能总和,以兆瓦日/吨铀(MW· d/tU)表示]尽量高。 但过高会造成燃料元件破损,使裂变产物逸出。另外,核燃料在反应堆中由于 受到中子和γ射线的辐照,会使其尺寸“长大”,并且由于裂变产物的生成,还 会使其发生“肿胀”,设计时应注意。
(3) 提高固体燃料基休的强度,约束气泡的长大;
金属铀是没有可能达到(3)中所说的那么大的强度,所以实际上是应用(1)、 (2)两种方法。 加入合金元素可以防止肿胀,还可以改善各向异性的效果。但是加入这些 元素不但会把铀中的可裂变同位素235U稀释,还会增加中子吸收,这对于维持 持续的链式反应是不利的。因此,为了使235U含量很少的天然铀得到上述的改 善,对添加元素量作了如下表限制。
4.2.2 铀的陶瓷核燃料及其成型加工
金属铀有各向异性和低熔点两大缺点。尽管做了种种改进,但总有 限度。因此,考虑使用铀化合物的陶瓷体作为燃料,这种燃料称为 “陶瓷燃料”。 陶瓷比金属的熔点高(2865℃),耐辐照,轻水反应堆中采用的陶 瓷燃料是UO2,用熔炼加工的方法制造成形是困难的。所以一般采用 下述三种方法之中的一种来制造: (1) 把粉末压制成形,然后烧结,制成称为芯块的圆柱体; (2) 把粉末填入包壳管中,并使其振动,从而提高密度的振动密实法; (3) 把粉末装入包壳管中,然后从管外进行边转边敲打的旋锻法。 按第 (2)、(3) 种方法制成的产品,一开始作为燃料使用就会由于裂 变发热升温而产生烧结。旋锻法是把陶瓷燃料粉末填进包壳管中,易 划伤内表面,所以最近不大采用。
二氧化铀芯块的制造方法:
一般是把浓缩铀工厂提供的成品UF6(六氟化铀)加热成气体, 然后通入氨水等中,结果沉淀出ADU (重铀酸铵)等化合物,经过 过滤洗涤后,进行干燥焙烧制成U3O8,再进行氢还原制成UO2粉 末,即可对其进行成形烧结。多数情况下,二氧化铀中所含的氧 超过正常化学比1:2。这个指标用氧铀比(O/U) 表示。烧结前压制 是将加入了粘结剂的二氧化铀粉末,用20t/cm2左右的压力加压, 压制成为圆柱状生坯块。经预烧除去粘合剂以后,在氢气流中加 热到1600-1700℃进行烧结,得到的密度是理论密度的93-97%。 所谓理论密度是指熔化凝固方法所得到的密度。燃料快高度和直 径比为1~1.5。目前较多的是蝶形快,其上下面压制成凹蝶形, 以适应肿胀变形,芯块表面进行机械磨光,以保持与包壳管的间 隙。
金属铀、二氧化铀、碳化铀 的各种物理性质比较
从表中可以看到陶瓷体是立方晶, 因此没有各向异性。镕点高达2000℃以 上。但是二氧化铀的导热系数只有金属 的十几分之一。因此,对于相同的燃料 表面温度,中心温度显著变高。这样, 特意取得的高熔点这个优点在很大程度 上被抵销了。二氧化铀是离子晶体,而 碳化铀是共价键,因此碳化铀的导热系 数与金属相似。但是碳化铀在化学上是 非常活泼的,在大气中能燃烧,与水能 发生激烈的反应。因此,无论是成形加 工还是填进燃料包壳管时都必须在情性 气体中进行。在实际使用中,碳化铀燃 料的缺点是;包壳万一发生破裂,要求 冷却剂不与其发生激烈反应,因此不用 在水堆中。
金属铀的性质:
金属铀具有银白色的光泽,但是在空气中很快就氧化成为黑色,也 会被水和二氧化碳气体等腐蚀,但是氧化膜是致密的。
注:金属铀主要作为生产堆核燃料。
金属铀燃料的问题:
核燃料一经使用会生成核裂变产物。由于其中有氢、氖等气体元素,所以 如果其生成量多并且温度也足够高的时候,这些气体元素的原子就会在固体燃 料中扩散迁移而汇集起来并形成气泡,固体燃料就会像烤面包一样胀起来。这 种现象称为“肿胀”。燃料的燃耗深度越高,使用温度越高,肿胀就越显著, 这在实际应用上是一个问题。裂变产物的生成是不可避免的,防止肿胀的方法 有下述三种: (1) 防止气体原子在固体燃料中扩散; (2) 使产生气泡的点增多,许多小气泡要比少数大气泡危害小;
• • • •
“燃料元件一般是由核燃料和包壳组成的” 4.2 燃料芯体材料
作为燃料元件的芯体材料必 须含有裂变材料或增殖材料。如 果就元素的名称上看,燃料芯体 材料的成分就是铀、钚和钍三种。 其中只有钚不是天然的。实际应 用的核燃料芯体材料的形式大致 分为固体的和液体的。固体核燃 料有金属或合金以及化合物陶瓷。 液体核燃料有金属或合金以及熔 盐。
4.2.1. 金属铀燃料及其成形加工
工业上用镁或钙还原氟化物生成金属铀。此外,也有熔盐电解的 方法,但这种方法只限于要求具有特高纯度的情况,主要用来制造研 究用金属铀锭。用氟化物的金属还原法制造出来的金属铀锭,或者用 真空高频感应炉熔化,浇铸到石墨制成的铸型中而当即制成铸造燃料; 或者采用轧制、挤压或其它的塑性加工,作成燃料芯体的坯料。用轧 制方法加工铀棒燃料时,采用带槽轧辊。
第四章 核燃料元件的制造
4.1 核燃料元件概述
燃料元件是核反应堆堆芯的基本构件。 其主要的作用是: 作为核燃料的基本单元; 导出链式裂变反应产生的热量; 阻留强放射性裂变产物,防止其泄漏; 特点: 需承受很高的内、外压力,同时承受 很强的水利振动机械应力,并能耐强中子 通量和强γ射线的辐照,因此,燃料元件需 满足冶金、传热、机械等多方面的性能要 求,并要求精密设计和高精度制造。