密闭鼓风炉炼铅锌技术改进及展望
氧气底吹熔炼—鼓风炉还原炼铅新技术
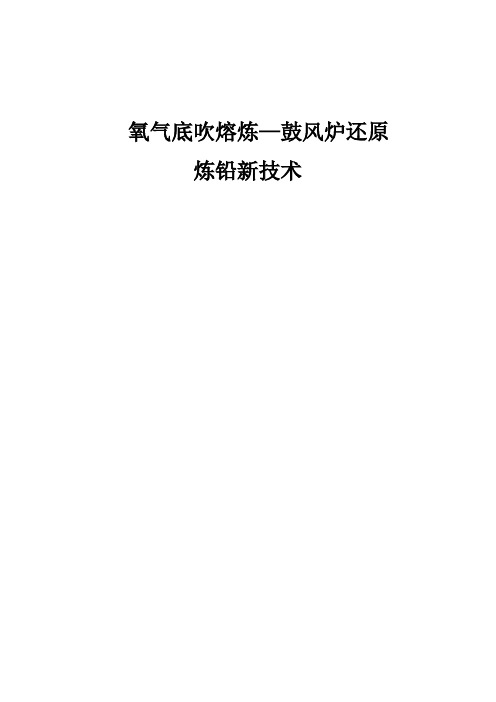
氧气底吹熔炼—鼓风炉还原炼铅新技术氧气底吹熔炼—鼓风炉还原炼铅法一、氧气底吹熔炼—鼓风炉法简介氧气底吹熔炼—鼓风炉还原炼铅法工艺流程为:熔剂、铅精矿或二次铅原料及铅烟尘经配料、制粒或混捏后进行氧气底吹熔炼,产出烟气、一次粗铅和铅氧化渣,烟气经余热锅炉回收余热和电收尘器收尘后采用二转二吸工艺制酸,尾气排放,铅烟尘返回配料。
铅氧化渣经铸块后与焦块、熔剂块混合后入鼓风炉进行还原熔炼,产出炉渣、烟气和粗铅,烟气经收尘后放空,铅烟尘返回配料。
工艺主要设备包括可旋转式氧气底吹熔炼炉,多元套管结构氧枪(多通道水冷高温喷镀耐磨底吹氧枪),特殊耐磨材质的氧枪口保护砖,浅层分格富铅渣速冷铸渣机(铅氧化渣铸渣机),带弧型密封罩和垂直模式壁中压防腐余热锅炉,全封闭铅烟尘输送配料等, 新型结构鼓风炉(双排风口大炉腹角高料柱)等。
工艺的核心设备是氧气底吹熔炼炉。
熔炼炉炉型结构为可回转的卧式圆筒形,在炉顶部设有2~3 个加料口,底侧部设有3~6 个氧气喷入口,炉子两端分别设一个虹吸放铅口和铅氧化渣放出口。
炉端上方设有烟气出口。
铅精矿的氧化熔炼是在一个水平回转式熔炼炉中进行的。
铅精矿、铅烟尘、熔剂及少量粉煤经计量、配料、圆盘制粒后, 由炉子上方的气封加料口加入炉内, 工业纯氧从炉底的氧枪喷入熔池。
氧气进入熔池后, 首先和铅液接触反应, 生成氧化铅(PbO ) , 其中一部分氧化铅在激烈的搅动状态下, 和位于熔池上部的硫化铅(PbS) 进行反应熔炼, 产出一次粗铅并放出SO 2。
反应生成的一次粗铅和铅氧化渣沉淀分离后, 粗铅虹吸或直接放出,铅氧化渣则由铸锭机铸块后, 送往鼓风炉工段还原熔炼, 产出二次粗铅。
出炉SO 2 烟气采用余热锅炉或汽化冷却器回收余热, 经电收尘器收尘, 送硫酸车间处理。
熔炼炉采用微负压操作, 整个烟气排放系统处于密封状态, 从而有效防止了烟气外逸。
同时, 由于混合物料是以润湿、粒状形式输送入炉的, 加上在出铅、出渣口采取有效的集烟通风措施, 从而避免了铅烟尘的飞扬。
炼铜密闭鼓风炉设计构想及操作改进综述

炼铜密闭鼓风炉设计构想及操作改进综述炼铜密闭鼓风炉设计构想及操作改进综述一、引言在当今现代化工业领域,炼铜密闭鼓风炉(hereinafter referred toas "密封炉")在铜矿冶炼过程中起到至关重要的作用。
密封炉的设计构想和操作改进对于提高冶炼效率、降低能耗和环境污染具有重要意义。
本文将基于这一背景,对炼铜密闭鼓风炉的设计和操作进行综述,以期为读者深入理解该主题提供有价值的信息。
二、背景介绍密封炉作为一种冶炼设备,其目标是在保持高温下对铜矿进行还原冶炼,从而提取纯铜。
在过去的几十年里,人们致力于研究和改进密封炉的设计和操作,以提高冶炼效率和减少环境污染。
然而,尽管有了一些令人鼓舞的进展,但仍然存在一些挑战和问题,需要我们进一步加以研究和改进。
三、设计构想1. 采用高效的燃烧系统:密封炉的燃烧系统是影响其冶炼效率和能耗的重要因素。
我们可以尝试运用新型的燃烧技术,如气体切割和高效的燃烧器设计,以提高炉内温度的均匀性和燃烧效率。
2. 优化炉体结构:密封炉的炉体结构也是一个需要关注的重要方面。
我们可以通过改善炉体的隔热性能、优化炉内流动状况等措施,提高炉内的能量利用率,减少能耗。
3. 引入先进的自动控制系统:在密封炉的操作过程中,引入先进的自动控制系统,在实时监测炉内参数的基础上,通过智能算法对炉内温度、氧气含量等进行调控,以实现最佳冶炼效果和能耗控制。
4. 强化炉内废气处理:炉内废气的处理对于环境保护至关重要。
我们可以尝试引入高效的除尘设备、脱硫装置等,以降低废气中的污染物含量,并在后续的处理过程中实现资源的回收和利用。
四、操作改进1. 优化炉内料层结构:密封炉冶炼过程中,合理控制炉内料层的结构和粒度分布,可以有效提高冶炼效率。
我们可以尝试通过控制料层的投料速度、运行参数等手段,提高炉内温度的均匀性和物料的还原速度。
2. 加强炉内温度监测:密封炉的温度是影响冶炼效果的重要因素。
韶冶铅锌密闭鼓风炉系统(I)技术改造及效果

第 2 卷第 2 1 期
20 0 7年 6月
茵毛 詹
Ja KiNo fr u tl in x ner sMeas o
Vo .1No2 12 , .
J n. 0 7 u 2 O
文 章编 号 :05 21( 0) —080 10—72 07 2 04 —3 2 0
12 风炉 改造 . 1 热
术改造 . 特别是 18— 9 2 9 0 18 年的环保治理和 18— 9 5 18 年改扩建 , 99 铅锌生产能力达到 7 万 t19 年 . 5 ,90
成功完成了以烧结机为主体的技术改造后 ,一系统 形 成年产 铅锌 1 0万 t 的综 合生 产 能力 。
为了进一步提 高 IF生产 能力 .使韶冶年铅锌 S 金 属产 品达 到 3 0万 t 20 , 06年底 韶 冶 对 一系 统 铅 锌密闭鼓风炉进行 了为期 5 6d的技改性大修 。 完成 了以铅锌密闭鼓风炉为核心的技术改造 ,从而达到 扩大产能 。 降低生产成本 , 加强资源综合利用和节能
置, 以备 后 期对 炉 身外 壳 的保 护 , 长 其 使用 寿 命 , 延
改善了喷淋布水装置 , 炉身内衬仍为红柱石砖 ; 更换
了热风 总管 ( 文丘 里人 孔 处至 鼓 风炉段 ) 砌体 和钢 结 构 ;更换 了炉 缸外 壳 和砌 体 ;加 固 了鼓 风炉 主次砼 梁 : 高了炉 顶平 台 : 修 了 二次风 管路 等f 加 检 】 1 。
5 0 m. 0 m 延长 了槽 底 使用 寿命 , 保 三年 一 大 修 目标 确
的实现 。
注: 4月份 因来 料 不 足 减 风 平 衡
1 电热前床等方面的改 壳 结构 ,彻 底 地解 决 了安全 隐患 问题 ;烟 化 炉 收尘 改造 成 二系 统
对铅冶炼技术及进步的展望

对铅冶炼技术及进步的展望铅冶炼技术是确保铅金属产量的重要载体。
本文从常见的铅冶炼技术入手,分析了铅冶炼技术中较为先进的闪速炼铅技术,并对其未来的进步进行了展望。
旨在与同行进行业务交流,以不断促进铅冶炼企业经济效益的最大化,从而更好地满足低碳背景下我国经济发展发展对铅金属消费的需要。
标签:铅冶炼技术闪速炼铅技术进步展望目前,已经进入节能环保的新时期,如何在确保达到节能目标的同时保证铅产量的需要,已成为新时期背景下的铅冶炼企业共同面临的问题。
因而在做好铅冶炼技术分析的基础上,还应对现有的铅冶炼技术进行改进,进而促进铅冶炼技术进步的同时达到上述的双重目标。
基于此,笔者结合自身工作实践,就此展开以下几点探究性的分析。
1基于铅冶炼技术现状的几点概述1.1常见的铅冶炼技术在我国铅冶炼行业中,常见的铅冶炼技术主要有以下几种:一是利用烧结—鼓风炉进行铅冶炼;二是卡尔多炉铅冶炼技术;三是澳斯麦特铅冶炼技术;四是氧气底吹熔池铅冶炼技术;五是水口山铅冶炼技术;六是基夫赛特铅冶炼技术;七是HUAS闪速铅冶炼技术。
其中,烧结—鼓风炉铅冶炼技术最为落后,且能耗大,但由于经济性强,因而目前仍广泛应用,而基夫赛特铅冶炼技术和HUAS 闪速铅冶炼技术是最为先进的铅冶炼技术。
1.2闪速铅冶炼技术的特点在上述的多种铅冶炼技术中,基夫赛特铅冶炼技术和HUAS闪速铅冶炼技术均属于闪速炼铅技术。
因而为了促进铅冶炼技术的发展,就必须加强对闪速炼铅技术的改进,但是在改进之前,必须对其特点有一个基本的认识。
就笔者多年的工作实践来看,该技术具有的特点主要体现在以下几个方面:一是对原料具有较强的适应性。
在应用过程中,不仅可以利用闪速熔炼炉对品位较低的铅精矿进行直接处理,而且还能在对铅精矿进行处理的同时配以相应的锌浸出渣,进而达到铅锌联合生产的目的。
二是烟气量很小。
在利用闪速铅冶炼技术进行铅冶炼时,由于主要选用高富氧、纯氧等进行冶炼,不仅能够降低氮气升温过程中热量的消耗,而且能有效的降低烟气量,尤其能将氧气中二氧化硫的浓度提升[1]。
铅锌矿的矿石加工与冶炼技术改进
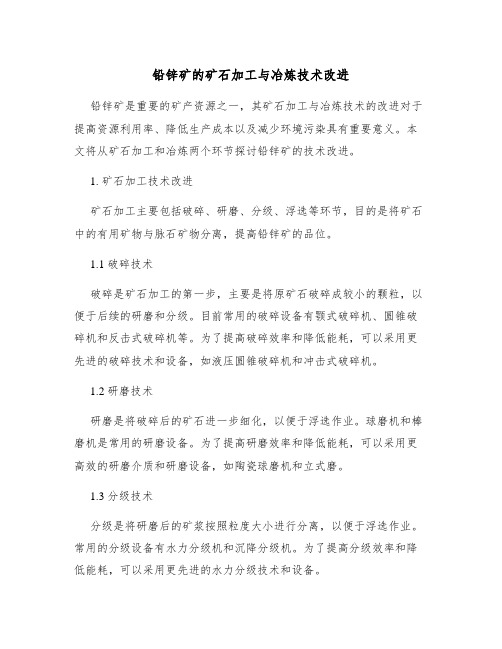
铅锌矿的矿石加工与冶炼技术改进铅锌矿是重要的矿产资源之一,其矿石加工与冶炼技术的改进对于提高资源利用率、降低生产成本以及减少环境污染具有重要意义。
本文将从矿石加工和冶炼两个环节探讨铅锌矿的技术改进。
1. 矿石加工技术改进矿石加工主要包括破碎、研磨、分级、浮选等环节,目的是将矿石中的有用矿物与脉石矿物分离,提高铅锌矿的品位。
1.1 破碎技术破碎是矿石加工的第一步,主要是将原矿石破碎成较小的颗粒,以便于后续的研磨和分级。
目前常用的破碎设备有颚式破碎机、圆锥破碎机和反击式破碎机等。
为了提高破碎效率和降低能耗,可以采用更先进的破碎技术和设备,如液压圆锥破碎机和冲击式破碎机。
1.2 研磨技术研磨是将破碎后的矿石进一步细化,以便于浮选作业。
球磨机和棒磨机是常用的研磨设备。
为了提高研磨效率和降低能耗,可以采用更高效的研磨介质和研磨设备,如陶瓷球磨机和立式磨。
1.3 分级技术分级是将研磨后的矿浆按照粒度大小进行分离,以便于浮选作业。
常用的分级设备有水力分级机和沉降分级机。
为了提高分级效率和降低能耗,可以采用更先进的水力分级技术和设备。
1.4 浮选技术浮选是铅锌矿加工的关键环节,主要是通过添加浮选剂使有用矿物与脉石矿物分离。
浮选设备有机械搅拌式浮选机和无机械搅拌式浮选机。
为了提高浮选效率和降低能耗,可以采用更先进的浮选技术和设备,如高效浮选柱和空气注入式浮选机。
2. 冶炼技术改进冶炼是将矿石加工后的精矿转化为金属铅和金属锌的过程。
目前常用的冶炼方法有火法冶炼和湿法冶炼。
2.1 火法冶炼技术改进火法冶炼是传统的铅锌冶炼方法,主要包括烧结、熔炼、吹炼和精炼等环节。
为了提高火法冶炼的效率和降低能耗,可以采用更先进的燃烧技术和设备,如高温燃烧炉和富氧燃烧技术。
2.2 湿法冶炼技术改进湿法冶炼是近年来发展起来的铅锌冶炼方法,主要包括硫酸化浸出、电积和精炼等环节。
为了提高湿法冶炼的效率和降低能耗,可以采用更先进的浸出技术和设备,如高效搅拌槽和电积槽。
我国铅锌冶炼现与专业技术发展方向

我国铅锌冶炼现状与技术发展方向1、铅冶炼现状在过去的十年里,我国的铅冶炼行业发展迅速。
2005年全国生产精铅237.8万吨,较1996年的70.62万吨,增加了167.18万吨。
同期世界铅的年产量,由1996年的578.5万吨至2005年达746.88万吨,仅增加了168.38万吨,可见在此期间世界铅产量的增长99%以上是由我国完成的。
我国铅产量近10年间年均递增14.9%,增长速度为世界之最。
根据资料统计,目前全国建成铅冶炼厂400多家,其中2005年精铅产量在10万吨以上的冶炼厂有3家,年产5~10万吨的8家,3万t/a以上的18家,其总产量约为133万吨,占全国精铅总产量的56%。
见表1。
我国传统的铅冶炼工艺所产铅量占总产量的85%,除株洲冶炼厂、河南豫光、金利、豫北、万洋、焦作东方、内蒙林东等冶炼厂采用烧结机外,其余均采用烧结锅或烧结盘进行烧结。
采用烧结-鼓风炉炼铅锌的ISP工艺,在国内有4家,五条生产线在生产,其中韶关冶炼厂两条、白银、葫芦岛锌厂、青海煌中县各有一条。
烧结机-鼓风炉炼铅工艺应用比较成熟,但低浓度二氧化硫烟气回收难度较大,株洲冶炼厂引进托普索制酸技术,河南豫光金铅集团、豫北金属冶炼厂和济源万洋冶炼集团等均采用非稳定态制酸技术。
但受工艺条件和设备的限无组织排放和铅尘污染仍未得到有效控制。
至于尚在生产的烧结锅-鼓制,SO2风炉炼铅工艺(国家2000年起明令禁止生产) SO及铅尘污染尤为严重。
2表1 2005年我国年产精铅3万t以上企业名录近几年,随着国家对环保要求日趋严格,新的炼铅方法在我国逐步得到推广应用,如云南曲靖引进的艾萨法(ISA)、西北矿业公司引进的卡尔多(Kaldo)法等炼铅工艺都已投产。
特别是我国自主开发的氧气底吹-鼓风炉还原炼铅新工艺推广速度很快,除河南豫光金铅集团、安徽池州、湖南水口山等4套装置已成功投产外,河南灵宝凌冶股份有限公司已于今年8月份点火烤炉,云南祥云飞龙实业有限公司已于9月20日投产。
密闭鼓风炉铅锌冶炼工艺以天然气替代恩德炉煤气改造实践及节能探索

中 图 分 类 号 :TF806.21 文 献 标 识 码 :A
1 概 述
我国某厂铅锌冶炼分厂采用I.S.P 密闭鼓风炉 冶炼生产工艺,主 要 产 品 为 精 锌 (6 万t/a)、精 铅 (3 万 t/a)和 硫 酸 (13 万 t/a)等 。 该 工 艺 生 产 系 统 主 要 有 返 烟 烧 结 、烟 气 制 酸 、鼓 风 炉 熔 炼 、炉 渣 贫 化 、锌 精 馏和铅电解工序。改造前各用气点燃料为恩德粉煤 气 化 炉 煤 气 ,其 中 精 馏 塔 、鼓 风 炉 、烧 结 机 、熔 铅 锅 等 主要燃气点160余 个,改 造 前 每 年 使 用 煤 气 折 合 粉 煤量达9 万 t 左 右,粉 煤 气 化 炉 年 煤 尘 产 出 量 达 1.35万 t以上,环保状 况 不 容 乐 观。 随 着 国 家 对 冶 炼企业清洁生产工 作 的 深 入 推 进,该 厂 现 有 的 煤 气 生产工艺已经无法 适 应 环 保 工 作 要 求,将 现 有 热 源 改用清洁的天然气做为热源势在必行。
能源单价 (元/t) 595.64 595.64
单位产品耗煤成本 (元/t) 878 304
注 :表 中 能 源 单 价 为 粉 煤 单 价 与 煤 气 加 工 费 之 和 。
2.1 精 锌 馏 塔 改 造 锌精 馏 塔 是 锌 精 炼 的 主 体 设 备,分 为 铅 塔 和 镉
塔 ,根 据 生 产 需 求 按 组 立 排 布 ,单 塔 瞬 时 燃 气 量 一 般
第 34 卷 第 1 期 2018 年 02 月
有 色 矿 冶 犖犗犖-犉犈犚犚犗犝犛 犕犐犖犐犖犌犃犖犇 犕犈犜犃犔犔犝犚犌犢
我国铅锌冶炼主要工艺与技术水平技术前沿中国标准物质网

我国铅锌冶炼主要工艺与技术水平技术前沿中国标准物质网1)粗铅冶炼工艺目前世界上粗铅的生产方法主要采用火法,湿法炼铅尚未实现工业化。
火法炼铅可分为传统炼铅法和直接炼铅法。
传统炼铅法包括烧结一鼓风炉熔炼法、电炉熔炼法等。
(1)底吹一鼓风炉炼铅工艺(SKS法)铅精矿、铅烟尘、熔剂及少量粉煤经计量、配料、制粒后,由炉子上方的加料口加入炉内;工业氧气从炉底的氧枪喷入熔池,氧气进入熔池后,首先和铅液接触反应,生成氧化铅,其中一部分氧化铅在激烈地搅动状态下和位于熔池上部的硫化铅进行交互反应生成一次粗铅、氧化铅和二氧化硫;所生成的一次粗铅和铅氧化渣沉淀分离后,粗铅虹吸或直接放出;铅氧化渣则由铸锭机铸块后,送往鼓风炉还原熔炼,产出二次粗铅。
氧化熔炼产生的SO2烟气经余热锅炉和电收尘器后送硫酸车间制酸。
(2)富氧底吹+液态高铅渣直接还原熔炼工艺该工艺的前面氧化炉熔炼部分与SKS法等熔炼工艺基本相同,还原炉采用富氧熔炼炉替代了鼓风炉,取消了铸渣机,用溜槽将氧化炉和还原炉进行连接。
氧化炉产生的液态高铅渣经溜槽直接进入还原炉进行还原熔炼,有效利用高铅渣的显热,还原炉内加煤粒或焦炭,采用天然气或煤或煤气等进行还原熔炼。
还原炉产出二次粗铅送后续的精炼系统,还原炉渣送后续的烟化炉处理,回收锌。
(3)基夫赛特直接炼铅工艺(Kivcet法)铅精矿、含铅锌渣料、熔剂及少量煤经计量、配料、干燥及磨矿后,混合炉料由反应塔顶的炉料一氧气喷嘴喷入炉内,进行工业纯氧熔炼,在一个熔炼炉中完成氧化、还原过程直接产出粗铅。
基夫赛特炉有反应塔、电热区和竖烟道三个主要部分,设置在同一固定的炉床上,反应塔和电热区由隔墙分开。
炉料在反应塔内完成硫化物的氧化反应并使炉料颗粒熔化,产出金属氧化物、金属铅滴和其他成分所组成的熔体,熔体在通过熔池表面的焦炭过滤层时,大部分氧化铅被还原成金属铅而沉降到熔池底部,熔体流经水冷隔墙下通道进入电热区:在电热区,部分氧化锌被加入电热区的焦炭还原挥发,同时渣、铅进一步沉降分离,然后分别通过渣口和放铅口放出。
- 1、下载文档前请自行甄别文档内容的完整性,平台不提供额外的编辑、内容补充、找答案等附加服务。
- 2、"仅部分预览"的文档,不可在线预览部分如存在完整性等问题,可反馈申请退款(可完整预览的文档不适用该条件!)。
- 3、如文档侵犯您的权益,请联系客服反馈,我们会尽快为您处理(人工客服工作时间:9:00-18:30)。
作者简介:王志刚(1962-),男,高级工程师,从事有色冶炼工艺设计与试验研究。
・冶 炼・密闭鼓风炉炼铅锌技术改进及展望王志刚(长沙有色冶金设计研究院,湖南长沙 410011)摘 要:阐述密闭鼓风炉炼铅锌技术在鼓风烧结、ISF 熔炼及配套设施方面的主要技术改进。
并对ISP 技术发展进行了展望。
关键词:ISP ;烧结;熔炼;技术改进中图分类号:TF806121 文献标识码:A 文章编号:1003-5540(2003)06-0019-04 密闭鼓风炉炼铅锌技术(简称ISP )是由英国帝国熔炼公司于五十年代发明的在一台密闭鼓风炉内同时熔炼铅、锌的方法。
该技术具有对原料适应性强、有价金属选冶综合回收率高、能源综合利用率高、易于实现过程的自动化以及“三废”治理效果显著等优点。
所以,越来越多的国家已把它作为现代有色冶金的主要生产手段和先进工艺。
至九十年代末,先后在13个国家建了18座铅锌密闭鼓风炉,产量已占世界铅锌总产量的14%以上。
近十年来,ISP 技术日趋完善,耗炭系数由0.76降至0.66,单台炉子年粗铅锌产量不断增加,原来产粗锌铅5×104t 的标准炉,现已达到112×105t ,有的仅产粗锌就已超过1×105t 。
我国工程技术人员从20世纪60年代开始对ISP 生产工艺和设备进行研究,在消化吸收国外技术的基础上,进行了许多技术改进,达到了提高生产能力、降低生产成本、提高经济效益、改善环境和操作条件的目的。
1 主要技术改进近年来,我国工程技术人员对ISP 生产工艺和设备不断技改创新,各项指标大幅提高,节能降耗效果明显,基本达到国际先进水平。
现将韶关冶炼厂(简称韶冶)ISP 工艺及设备所作的技术改造主要内容简述如下:1.1 鼓风烧结工艺改进1.1.1 全返烟烧结铅锌焙烧普遍采用鼓风返烟烧结,以提高烟气中SO 2浓度。
为了提高烧结料中硫汞的利用率,减少其对环境的污染,韶冶已将含硫、汞较低的烧结机尾的通风排气返回烧结,作为新鲜空气使用。
通常这部分气体中SO 2浓度较低,仅013%~2%,含O 220%左右。
将这部分烟气返回烧结机中部,可提高制酸烟气中SO 2浓度。
由于机尾气量较大,故不能全部返烟。
11112 加大主反应区的鼓风强度烧结机3#~5#风箱为烧结焙烧化学反应的主要区域,若鼓风能力不足,则料层中氧的分压较低,炉料反应时间短,焙烧反应不完全,导致炉料温度不够,使得主体相ZnO 、ZnFe 2O 4生成量不足,最终降低烧结块强度,影响烧结块产量、质量。
韶冶原此区域鼓风强度仅13~14m 3/m 21min ,后加大到约18m 3/m 21min ,从而加快炉料的焙烧速度,提高炉料脱硫的彻底性,为提高料层厚度创造了条件。
改进前后的生产情况表明,烧结块Pb 、S 、CaO/SiO 2合格率增加2%~3%,其软熔温度提高200℃以上。
11113 烧结配料顺序的改进ISP 原常规的配料顺序为“干精矿→杂料→熔剂→返粉”。
生产实践证明,制粒效果不太理想。
韶冶二系统改配料顺序为“返粉→杂料→熔剂→干精矿”,这样可使返粉作为制粒的核心,其他物料均匀地包在外面,从而避免或减少了皮带的粘结,改善了制粒效果和物料的透气性,为高料层作业创造了条件,进而提高了烧结机的脱硫能力和产块率、保证了烧结块的质量,取得了较好的效果。
112 烧结设备改进虽然我国铅锌烧结机本体采用了刚性滑道密91第19卷第6期2003年12月湖南有色金属HUNAN NONFERROUS METAL S封,但头、尾部密封有待改进。
国内烧结机尾部烟气量高出日本八户冶炼厂一倍多,因此不能全部返烟,不得不设置庞大的收尘及烟气治理系统。
从烟罩到电除尘出口处的漏风率为20%(日本八户为1213%),而烧结成品烟气SO2浓度(大烟罩出口)仅为5%~6%,比八户低4%~6%,加大了制酸的负担和难度。
另外国内烧结机单位面积生产能力也较低,返粉破碎、混合制粒效果不太理想。
针对这些不足,结合最近设计的两个ISP冶炼工程对烧结设备进行了设计改进。
11211 烧结机主要改进烧结机主传动采用最先进PF T结构,传动更稳定可靠,结构紧凑,重量减轻50%~60%;改进布料形式,确保台车料面分布更均匀,从而有效地减少了风量的边缘效应,使台车断面烧结速度趋于一致;设计新式高挡板台车,以适应厚料层、慢车速烧结工艺的需要;台车与风箱之间采用新的刚性滑道结构,烟罩与台车间采用迷宫密封;改进台车材质和结构,增加台车刚度,以增强抗热变形的能力,使台车滑板和滑道面紧密贴合;机尾增设锁气装置,提高密封效果;合理减少炉篦条厚度,增强台车透气性。
通过一系列改进和优化,将进一步减少烧结机的漏风,有利于提高成品烟气SO2浓度和实现机尾烟气的全返烟烧结,并使作业率进一步提高。
11212 圆筒混合制粒机主要改进圆筒制粒机和圆筒混合机主传动采用新的BF 型柔性传动或实心胶轮传动,运行平稳、可靠、震动少、噪音小,维修方便;采用稀土含油尼龙材料作衬板,始终保持内衬表面形成一层料衬,并且不会逐渐增厚,档轮结构形式以及喷水系统设计也作了较大改进,以期强化制粒功能,延长圆筒寿命。
11213 破碎设备主要改进单辊破碎机采用柔性传动,爪盘采用螺旋排列,以克服烧结机间断卸料引起的冲击荷载;轴及轴承座均采用水冷,以减少其热变形;锤头表面堆焊耐磨材料以提高其耐磨性。
改进齿辊破碎机齿形结构,加大弹簧保护装置的弹簧调速范围,使于调整,确保两辊间隙稳定,降低物料过粉碎,使其粒度均匀。
光辊破碎机采用双电机驱动,液压保护,辊皮采用便于装卸的组合式结构,选用高硬度耐磨材料。
通过这一系列设计改进,将提高破碎设备的传动效率,并使其运行平稳,维修方便,延长使用寿命。
113 鼓风炉熔炼改进11311 ISF技术改进密闭鼓风炉(ISF)是ISP的技术核心,只有ISF 运行正常,前后工艺和设备才能发挥作用。
围绕着ISF的炉缸、炉壳、炉身、炉喉、炉顶、风口等主要部件实施了多次改进。
主要内容是:采用喷淋炉壳代替水套炉壁,减簿炉墙厚度,减少炉腹角,使鼓风炉风口区截面积由10m2扩大到16108m2;加深炉缸,以减少放铅次数即减轻劳动强度;从提高炉子的反应性和减少炉体熔损的危险性综合考虑,优化风口设计;改进炉顶结构及材质,延长炉顶寿命;扩大炉喉口,加大斜坡烟道的角度并改变其结构,减少结瘤,方便操作。
通过一系列改进和完善,使产量增加25%以上,焦率降低315%,送风率提高1145%,炉大修周期由1a改为2a。
11312 铅雨冷凝器技术改进铅雨冷凝器是与鼓风炉配套的关键设备,其功能是利用挥扬的铅雨将炉气带出的锌蒸汽迅速冷凝成液态锌。
冷疑效率的高低直接影响锌的直收率。
冷凝器的材质和结构的合理性不仅对使用寿命和清理周期影响很大,而且对安全生产有重要影响(存在着低热值煤气泄露中毒、爆炸的危险)。
因此,在对ISF实施改进时,也改进了冷凝器横跨烟道的结构,以减少烟道结瘤,延长清理周期;内衬采用优质耐热混凝土,特别是转子下部采用高耐热混凝土,防止液态金属铅的腐蚀而造成漏铅;改进盖板及壳体的材质,防止受热变形和裂痕。
改进后的生产实践表明,冷凝分离效率提高215%以上,浮渣减少118%,兰粉率降低115%,内衬寿命延长一倍,达4a以上。
11313 冷却流槽技术改进冷却流槽是冷凝器的配套设备,其作用是将冷凝器排出的铅锌混合液体(530℃)经冷却流槽冷却至450℃,再送分离系统进行铅锌分离。
原来采用水套式冷却流槽,存在着冷却效果差,冷却温度不易控制,耗水量大,易损坏,水套更换和浮渣清除极其困难的缺点。
为此,改为浸没式冷却流槽,其浸入液体深度、水流速度均可调,使用组数可灵活改变,前端还设有扒渣机。
使用情况表明,冷却效果明显提高,冷却水量比水套式流槽减少35%~40%,流槽使用寿命延长3a。
11314 分离系统技术改进分离系统是冷凝器不可缺少的配套系统,由冷却流槽送来的铅锌混合液在此进行铅锌分离,铅液02湖南有色金属第19卷返回冷凝器,粗锌液送锌精馏精炼。
生产中发现熔析槽经常结瘤堵死通道,因而技改中将其取消,并重新分配熔剂槽、分离槽、贮锌槽的面积,既得到最佳分离效果,又保证了熔炼与精炼合理衔接;将各槽外壳和机架整体加固,顶盖板内衬改用耐热混凝土浇铸;将煤气燃烧器全部改用颜氏烧嘴。
这些改进起到了节能降耗、方便操作的效果,各槽的使用寿命也延长3a以上。
11315 电热前床技术改进电热前床的作用是将鼓风炉排出的渣铅混合物在其内分离,得到粗铅产品,同时也满足了与鼓风炉配套的烟化炉间断操作的需要。
随着生产能力的扩大,原有电热前床不能满足生产要求,同时也存在着炉墙、炉顶、进渣和放渣流槽寿命短,电极夹持和升降装置调控欠灵等问题。
为此将前床面积扩大到1915m2,并对其骨架、外壳进行修改和加固,内衬材料改为铝铬钛砖;进、放渣流槽改为水套式结构,内衬改用铬镁砖;电极夹持、转动装置和升降平台作相应修改。
经改进后,不但满足了ISF扩产需要,又满足了烟化炉的生产要求,而且渣铅分离效果好,渣含铅降至1%以下,使用寿命延长至3a以上。
11316 炉气净化系统技术改进ISF冷凝炉气(含CO、CO2和尘粒)经直升烟道进入洗涤塔和湍球塔净化后,得到低热值煤气,再经升压后送用户使用。
技改中将洗涤塔下部的挖泥船取消,改为搅拌槽,使蓝粉直接进入浓密池,再以底流形式送烧结的冷却圆筒,以代替圆筒补充水。
同时改进洗涤塔和湍球塔的结构,既满足了ISF扩产的需要,又降低了低热值煤气的含尘量,提高了煤气质量及利用率。
114 炉渣烟化改进电热前床排出的渣含锌8%、铅1%,尚有回收价值。
在烟化炉挥发,并经收尘系统捕集后,可回收铅锌。
与韶冶合作开发出烟化炉-余热锅炉-体化装置,用其取代传统的烟化炉、余热锅炉结构。
此装置在韶冶二系统的应用表明,各项指标远优于传统烟化炉,主要有如下特点:11余热回收量高,比传统烟化炉、余热锅炉多产两倍蒸汽。
21劳动强度降低,操作环境得到改善。
一体化装置是将烟化炉与余锅炉设计成一个整体,烟化炉上部成为余热锅炉的辐射室,炉顶适当加高,取消了烟化炉烟气进余热锅炉的斜烟道,从而省去斜烟道集灰的清理工作。
31产品质量提高。
由于炉顶升高,飞溅的熔渣重新落入熔池的几率增加,带入余热锅炉对流室的熔渣量减少,既减轻锅炉粘结程度,又提高了烟化氧化锌产品质量。
41渣处理能力提高。
与韶冶一系统同规格传统烟化炉相比,渣处理能力提高30%以上。
51烟化炉使用寿命延长。
韶冶一系统烟化炉下部水套使用近3个月,一体化装置采用新的炉体结构和材质后,下部水套使用寿命达1a以上,与ISF同步作业率大大提高。
61余热锅炉烟气温度降低。
由于一体化装置的余热回收率提高,经省煤器出口的烟气温度为250℃左右,可直接进入布袋收尘器。