10第十讲 残余应力
第十章_残余应力测量-精品

tg22312 12
2019/8/12
11
钻孔附加应变的测量
钻孔附加应变需要用经过充分退火的零应力块预先 测量
常见材料和残余应力应变花的钻孔附加应变已经测 出,可以查表。
它实际上与钻孔人的技术、钻头锋利程度、钻头的 钻孔次数都有极大的关系
2019/8/12
12
10-5 试验技术
2019/8/12
1
2、降低构件的尺寸稳定性和加工精度 残余应力与工作应力叠加后达到屈服,发生 塑性变形
金属加工使残余应力释放,发生变形
3、受压构件提前失效 两种应力叠加使构件局部先达到临界应力而失 稳
4、结构疲劳强度受影响 一般使交变载荷下的疲劳强度降低,
但:残余压应力使疲劳强度大大提高。如链条
2019/8/12
14
10-6 误差
1、应变计灵敏系数极其分散度 2、应变计热输出 3、钻孔对中偏差 4、孔径、孔深偏差 5、附加应变 6、沿表明、厚度方向的应力梯度
残余应力的误差一般可以达到5~10%,甚 至更大。
2019/8/12
15
喷沙打孔
用气沙混合气流磨蚀--喷沙打孔 采用回转喷嘴打孔装置 孔径: 1~3mm 附加应变: 2.9±2.1 μm/m 45#钢 -1.9 ±5.6 μm/m 不锈钢
按平面应力状态的广义虎克定律有 沿贴片方向的释放应变 r E1(r)
r E 1 {1 22 [ ( 1 )a r 2 2 ]1 22 [ 3 ( 1 )a r 4 4 4 r a 2 2 ]c2 o }s
引入释放系数
A(1)
10-5-1 应变计
如右下图专用残余应力应变计 各片应变计到中心距离相同
(完整版)残余应力

残余应力(Residual Stress)消除外力或不均匀的温度场等作用后仍留在物体内的自相平衡的内应力。
机械加工和强化工艺都能引起残余应力。
如冷拉、弯曲、切削加工、滚压、喷丸、铸造、锻压、焊接和金属热处理等,因不均匀塑性变形或相变都可能引起残余应力。
残余应力一般是有害的,如零件在不适当的热处理、焊接或切削加工后,残余应力会引起零件发生翘曲或扭曲变形,甚至开裂。
或经淬火、磨削后表面会出现裂纹。
残余应力的存在有时不会立即表现为缺陷,而当零件在工作中因工作应力与残余应力的叠加,使总应力超过强度极限时,便出现裂纹和断裂。
零件的残余应力大部分都可通过适当的热处理消除。
残余应力有时也有有益的方而,它可以被控制用来提高零件的疲劳强度和耐磨性能。
[1]工件在制造过程中,将受到来自各种工艺等因素的作用与影响;当这些因素消失之后,若构件所受到的上述作用与影响不能随之而完全消失,仍有部分作用与影响残留在构件内,则这种残留的作用与影响。
也称残余应力。
残余应力是当物体没有外部因素作用时,在物体内部保持平衡而存在的应力。
凡是没有外部作用,物体内部保持自相平衡的应力,称为物体的固有应力,或称为初应力,亦称为内应力。
测试仪器编辑残余应力分析仪其原理是基于著名的布拉格方程2dsinθ=nλ :即一定波长的X射线照射到晶体材料上,相邻两个原子面衍射时的X射线光程差正好是波长的整数倍。
通过测量衍射角变化Δθ从而得到晶格间距变化Δd,根据胡克定律和弹性力学原理,计算出材料的残余应力。
应力方程根据弹性力学理论, 在宏观各向同性晶体材料上角度φ和ψ(见图1)方向的应变可以用如下方程表述:(图1)正应力和剪切应力应力分量σφ和τφ为方向Sφ上正应力和剪切应力:含剪切应力的应力方程和曲线如果在垂直于试样表面上的平面上有剪应力存在(τ13≠0和/或τ23≠0),则εφψ与sin2ψ的函数关系是一个椭圆曲线,在ψ> 0和ψ<0是图形显示为“ψ分叉”(见图3)。
残余应力的分类
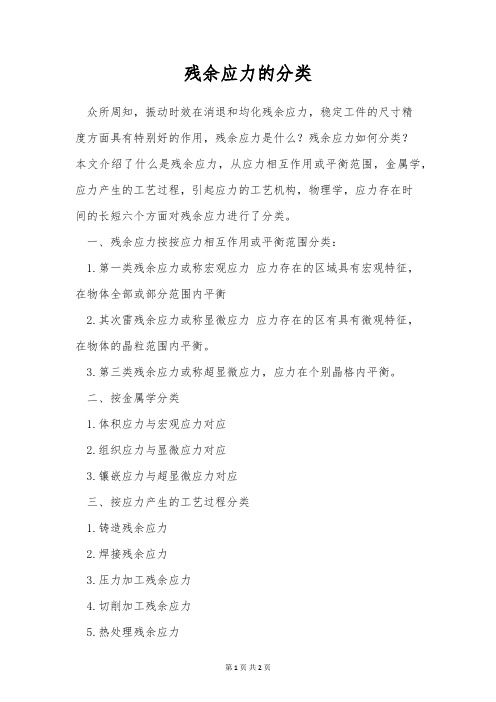
残余应力的分类众所周知,振动时效在消退和均化残余应力,稳定工件的尺寸精度方面具有特别好的作用,残余应力是什么?残余应力如何分类?本文介绍了什么是残余应力,从应力相互作用或平衡范围,金属学,应力产生的工艺过程,引起应力的工艺机构,物理学,应力存在时间的长短六个方面对残余应力进行了分类。
一、残余应力按按应力相互作用或平衡范围分类:1.第一类残余应力或称宏观应力应力存在的区域具有宏观特征,在物体全部或部分范围内平衡2.其次雷残余应力或称显微应力应力存在的区有具有微观特征,在物体的晶粒范围内平衡。
3.第三类残余应力或称超显微应力,应力在个别晶格内平衡。
二、按金属学分类1.体积应力与宏观应力对应2.组织应力与显微应力对应3.镶嵌应力与超显微应力对应三、按应力产生的工艺过程分类1.铸造残余应力2.焊接残余应力3.压力加工残余应力4.切削加工残余应力5.热处理残余应力6.镀层残余应力7.表面硬化处理残余应力8.校直残余应力等本文主要从引起应力的工艺机构,物理学,应力存在时间的长短对残余应力进行分类。
按引起应力的工艺机构分类 1.结构应力由于结构设计、几何外形和尺寸等缘由而引起的零件残余应力2.工艺应力由于零件制造工艺和使用过程中的某些缘由而引起的残余应力按物理学分类 1.热应力或温度应力由于零件不匀称的冷却或加热过程中温度梯度的影响,使零件产生不匀称的收缩或膨胀所引起的残余应力。
2.相变应力由于金属材料进行相变或集中过程而形成的的应力3.加工应力零件加工时,受切削力的作用所产生的塑性变形而引起的残余应力按应力存在的长短分类 1.临时应力在零件制造工艺过程中发生又随工艺过程的结束而消逝的应力2.永久性应力在零件制作过程的某一阶段产生,但当此过程结束后,一部分应力仍旧保留在零件内部而形成的残余应力。
残余应力
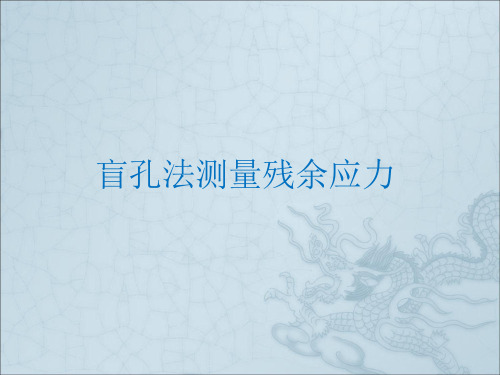
残余应力不可能完全消除。例如对于一些铸造机床的 床身,要想自然消除残余应力,需要很长的时间,但是仍 然不能完全消除。特别是对于一些大型的焊接件,例如桥 梁,船舶,更没有办法通过热处理来消除残余应力,但是 这些构件对于安全性要求有很高,因此有必要对残余应力 进行研究。
1.2 残余应力的测量方法
残余应力的测量方法可分为机械释放测量法和非破坏 无损伤测量法两种。机械释放测量法,是将具有残余应力 的部件从构件中分离或切割出来使应力释放,然后测量其 应变的变化求出残余应力。它主要包括盲孔法、切条法、 逐层去层法等。其特点是测量的精度较高,但对构件的损 伤较大。非破坏性方法,包括X射线衍射法、中子衍射法、 磁性法、超声波法等。其特点是对被测构件无损害,但成 本较高。 其中以盲孔法发展较为成熟,近年来科学工作者对其 做了大量的工作,从测量原理到实际操作中的各种工艺因 素、误差来源等进行了深入的研究,使其日趋完善,目前 已成为工程上最通用的残余应力测量方法。
1
co s 2 sin 2 B
(f)
由(d)式可以得到
1 2 ( ) 2 2A 1
1
(g )
联立(f)和(g)式,得
1 1 2 ( ) 1 2 4A 1 2 B co s 2 sin 2 1 1 1 2 ( ) 2 2 4A 1 2 B co s 2 sin 2
2 .1 .5 b
式中A、B成为应变释放系数。释放应变表达式(2.1.5a) 式可以写成
r A ( ) B ( ) co s 2
1 2 1 2
(2 .1 .6)
1 2
对图2.1.2所示的残余应变计, , 则三个敏感栅方向的释放应变分别为
第十章_残余应力测量-精品
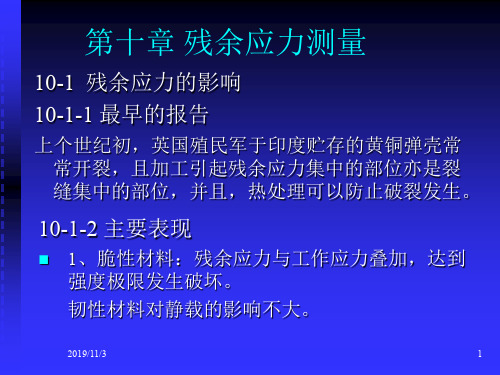
2019/11/3
10
10-4 附加应变
钻孔加工会由于挤压切削而产生钻孔附加应变,它 与由残余应力而产生的释放应变一起被测到,即:
仪s F 附加应变
附加应变需要预先去掉 释放应变
s 仪F
再代入残余应力的计算 式中
1 ,2 1 4 A 2 4 1 B(1 2 )2 [23 (1 2 )2]
20ห้องสมุดไป่ตู้9/11/3
16
1、
09045135
2、
2019/11/3
17
应力状态 r01 221 22co2s
01 221 22co2s
钻通孔后应力r0
12
2
sin2
r11 22(1 a r2 2)1 22(1 3 r a 4 4 4 a r2 2)c2 os
11 2 2(1a r2 2) 1 2 2(13 r a 4 4)co 2 s
3
r 2 A (1 2 ) B (1 2 )c2 os290
r3 A (12 ) B (12 )s2 in3 225
可以解出 1 ,2 1 4 A 2 4 1 B(1 2 )2 [23 (1 2 )2] tg22312 12
2、磁测法
应力使晶格发生形变,导致磁导率、电阻率等发生变化,测量 它们即可得残余应力。
特点:真正无损,设备简单,使用方便,可以深入有限厚 度的材料;但是仅对铁磁材料才能用,空间分辨区域较大 --与探头直径相当。
精度:以90%置信度,绝对误差可小于σs/7
2019/11/3
3
3、声弹性方法 利用应力对超声波波速的影响,通过建立应力- 声速关系来计算物体的内部应力。
残余应力

减小材料在加工和处理过程中所产生的不均 匀变形;
对加工件进行热处理;
进行机械处理。
2020/6/16
19
Lesson Ten
减小不均匀变形
正确选定变形的温度-速度制度 减小金属表面上的外摩擦 合理设计加工工具形状 尽可能保证变形金属的成分及组织均匀 ……
2020/6/16
20
Lesson Ten
侵蚀试样所用的溶液,对于含锡青铜可用水 银及含水银的盐类,对于钢可用弱碱及硝酸 盐类。
2020/6/16
34
Lesson Ten
在判断应力的形式时,若出现横向裂纹,则 可认为是纵向应力作用的结果,若出现纵向 裂纹,可认为是横向应力作用的结果。在实 际中准确地确定裂纹出现的时间比较困难, 不过与其它机械法相比较,还是可以定性地 看出破裂时间与残余应力的关系。
X射线法
Lesson Ten
在X射线法中可包括有劳埃法和德拜法。
在劳埃法中可根据干扰斑点形状的变化来定 性地确定残余应力。当无残余应力存在时, 各干扰斑点呈点状分布。有残余应力时,各 干扰斑点伸长,呈“星芒”状。
2020/6/16
40
Lesson Ten
铝晶体的劳埃图
(a)铝晶体未变形的劳埃图;(b)铝晶体塑性变形后的劳埃图
2020/6/16
Lesson Ten
30
Lesson Ten
根据公式
1 r 和 2 r 绘制这些数值与钻孔剖面积F的关系曲线。
并用作图法求出此曲线上任一点的导数
d1 和 d 2 。
dF
dF
2020/6/16
31
Lesson Ten
变形与钻孔横断面积关系
2020/6/16
残余应力的产生与消除
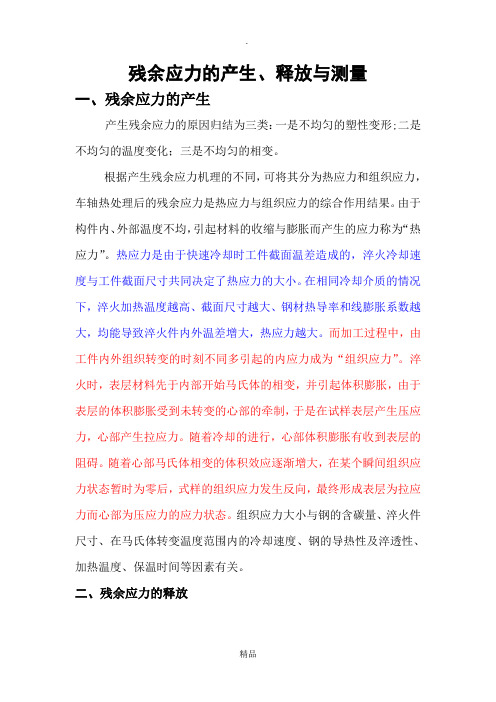
残余应力的产生、释放与测量一、残余应力的产生产生残余应力的原因归结为三类:一是不均匀的塑性变形;二是不均匀的温度变化;三是不均匀的相变。
根据产生残余应力机理的不同,可将其分为热应力和组织应力,车轴热处理后的残余应力是热应力与组织应力的综合作用结果。
由于构件内、外部温度不均,引起材料的收缩与膨胀而产生的应力称为“热应力”。
热应力是由于快速冷却时工件截面温差造成的,淬火冷却速度与工件截面尺寸共同决定了热应力的大小。
在相同冷却介质的情况下,淬火加热温度越高、截面尺寸越大、钢材热导率和线膨胀系数越大,均能导致淬火件内外温差增大,热应力越大。
而加工过程中,由工件内外组织转变的时刻不同多引起的内应力成为“组织应力”。
淬火时,表层材料先于内部开始马氏体的相变,并引起体积膨胀,由于表层的体积膨胀受到未转变的心部的牵制,于是在试样表层产生压应力,心部产生拉应力。
随着冷却的进行,心部体积膨胀有收到表层的阻碍。
随着心部马氏体相变的体积效应逐渐增大,在某个瞬间组织应力状态暂时为零后,式样的组织应力发生反向,最终形成表层为拉应力而心部为压应力的应力状态。
组织应力大小与钢的含碳量、淬火件尺寸、在马氏体转变温度范围内的冷却速度、钢的导热性及淬透性、加热温度、保温时间等因素有关。
二、残余应力的释放针对工件的具体服役条件,采取一定的工艺措施,消除或降低对其使用性能不利的残余拉应力,有时还可以引入有益的残余压应力分布,这就是残余应力的调整问题。
通常调整残余应力的方法有:①自然时效把工件置于室外,经气候、温度的反复变化,在反复温度应力作用下,使残余应力松弛、尺寸精度获得稳定。
一般认为,经过一年自然时效的工件,残余应力仅下降2%~10%,但工件的松弛刚度得到了较大地提高,因而工件的尺寸稳定性很好。
但由于时效时间过长,一般不采用。
②热时效热时效是传统的时效方法,利用热处理中的退火技术,将工件加热到500~650℃进行较长时间的保温后再缓慢冷却至室温。
第十讲残余应力

41
激励机床系统产生振动运动的交变力是由切削过程产生的。 切削过程同时又受机床系统的振动运动控制,机床系统的振
动运动一旦停止,动态切削力随之消失。 如果切削过程很平稳,即使有自激振动条件,没有交变的动
态切削力,自激振动不可能产生。 偶然性外界干扰(工件材料硬度不均匀、加工余量有变化等
)总是存在,其产生的切削力变化,使系统产生振动运动。
29
30
例题: 试解释磨削淬火钢时,磨削表面层的应力状态与磨削深 度的试验曲线。
31
参考: 当ap<0.01时,表面强化的冷态塑性变形引起表层比容 增大占主导地位,故表层有较小的压应力(负)。
当0.01<ap<0.05时,磨削表面温升增高,此时表层热作用, 高温塑性变形及表层的回火组织(索氏体或屈氏体)都使表层 的比容缩小,故表层产生较大的拉应力(正)。
Fy Fa Fv 假设 Fv 具有负摩擦特性,即 vm 越大,Fv 越小。
O1 为振入运动的平衡点,即:(Fyo1 Fao1 Fvo1) F弹o1 B点为振入运动的终止点:y&B 0
4
三 表层金属的残余应力 (一)原因
刀具切金属---表层金属的纤维被拉长---刀具后刀面与 已加工表面的摩擦加大这种拉伸作用。
刀具切离后---拉伸弹性变形恢复---拉伸塑性变形不能 恢复---表层金属的拉伸塑性变形---受到相连里层未发生塑 性变形金属的阻碍---表层产生压缩残余应力---里层拉伸残 余应力。
切削过程中的冲击等(切入、切出产生冲击,加工断续表面发 生周期性冲击)
39
(二) 强迫振动的特性 频率: 与干扰力的频率相同,或者是干扰力频率的整数倍。 幅值:与干扰力幅值、工艺系统动态特性有关。
- 1、下载文档前请自行甄别文档内容的完整性,平台不提供额外的编辑、内容补充、找答案等附加服务。
- 2、"仅部分预览"的文档,不可在线预览部分如存在完整性等问题,可反馈申请退款(可完整预览的文档不适用该条件!)。
- 3、如文档侵犯您的权益,请联系客服反馈,我们会尽快为您处理(人工客服工作时间:9:00-18:30)。
5
温度 1层高于tp(高塑性温度) 2层在tn(室温)和tp之 间 1层低于tp
变化 1层处于完全塑性状态 2层受热后自由膨胀,产生瞬时压缩残余应力, 而3层则产生瞬时拉伸残余应力。如4-19b所示 1层转变为不完全塑性状态,收缩产生拉伸残 余应力,2内压缩残余应力增大,如4-19c所
示
1层继续冷却 1层继续收缩,拉伸应力加大,2层的压缩应力
,
28
参考: () 考 虑 刀 具 几 何 形 状 加 工 表 面 上 的 复 映 , 1 只 在 可 按 刀 尖 残 留 面 积 的算 公 式 求 , 计 f f Rz , ' ctgK r ctgK r f Rz ( ctgK r ctgK r ) 0.012mm / r
'
焊缝等。
22
四 表面强化工艺
(二)滚压加工
淬硬和精细研磨滚轮、滚珠----常温挤压---凸起
部分向下压---凹下部分往上挤----前工序留下的
波峰压平---修正工件表面的微观几何形状----金
属组织细化---形成压缩残余应力
23
24
例题: 为什么机器上许多静止连接的接触表面(车床床 头箱与床身结合面,过盈配合的轴与孔表面等), 往往都要求较小的表面粗糙度,而有相对运动的 表面又不能对粗糙度要求过小?
有自激振动条件--持续振动运动。 电动机--通过动态切削--传能量到振动系统。 自激振动特点: 1)没有外力(相对切削过程)干扰下产生的。 2)频率接近于系统固有频率(强迫振动不同)。
3)不因阻尼存在而衰减(自由振动会)。
自激振动模型
振入:一个振动周期里,背吃刀量由小到大的 过程。 A->B
振出:一个振动周期里,背吃刀量由大到小的 过程。 B->C
正前角车刀,45钢在所有切削速度下,表层产生拉伸残余应
力。但是其他材料并不如此。
低速车削---切削热主导---表层拉伸残余应力 切削速度提高---表层温度达到淬火温度---局部淬火---比
容增大---金相组织变化---拉伸残余应力减少。
高速切削---表层淬火充分---比容增大---金相组织变化主
导---表层压缩残余应力。
10
影响车削表层金属残余应力的工艺因素
2 进给量的影响
进给量加大---表层金属塑性变形增加---切削区热 量增加---残余应力数值和扩展深度均增大 3 前角的影响 前角对表层金属残余应力的影响极大。
见图4-22
11
12
影响磨削残余应力的工艺因素
磨削加工:塑性变形严重、热量大、工件表面温度高,热因素和塑
40
(二) 强迫振动的特性
干扰力频率接近工艺系统某一固有频率,幅值明显增大。
干扰力频率与工艺系统某一固有频率相同,系统共振。
改变运动参数或工艺系统的结构----干扰力频率发生变化或 工艺系统某阶段固有频率发生变化----干扰力频率远离固有 频率----强迫振动幅值明显减少。
41
激励机床系统产生振动运动的交变力是由切削过程产生的。
( 2) 实 际 切 削 加 工 时 , 由 物 理 因 素 ( 如 塑 性 变 , 于 形 切 削 热 , 刀 瘤 及 鳞 刺) 的 参 与 及 系 统 的 振会 等 动 改 变 刀 尖 残 留 面 积 的廓 形 状 , 并 加 大 表 面平 度 轮 不 的 平 均 高 度 z。 R
29
30
例题: 试解释磨削淬火钢时,磨削表面层的应力状态与磨削深 度的试验曲线。
序的加工方法。
交变载荷作用---表面存在局部微观裂纹---拉应力会使 原生裂纹扩大,导致零件断裂---从抗疲劳破坏考虑--最终工序应产生压缩残余应力为好
19
工作条件
破坏形式
表面应力引起 原因
加工时 对策
最终 加工方法 磨削 -> 淬火 镀铬, 镀铜, 车削* 镀铬, 镀铜, 车削*
交变载荷
断裂
表面存在局部 表面压残余应力 微观裂纹 见图 4-24a 综合作用 见图 4-24b 综合作用
25
参考:
由于静止连接的接触表面的粗糙度影响接触刚度及配合 性质,因此接触表面要求较小的表面粗糙度。
对有相对运动的表面,当表面很光滑时,由于润滑油 被挤出,表面间分子亲和力大,产生“咬焊”作用。表面间 产生相对运动会加剧磨损,所以磨损不但有机械作用,而且 有分子作用。因此有相对运动的表面对粗糙度不能要求过小。 因而零件表面粗糙度存在一个最佳范围,它取决于使用要求, 工作条件及零件材料等。
性变形对磨削表面残余应力影响都很大。
热因素主导---表面拉伸残余应力 塑性变形主导---表面压缩残余应力 工件表面温度超过相变温度又充分冷却---淬火烧伤---金相组织变 化主导---表面压缩残余应力。
精细磨削---塑性变形主导---表面压缩残余应力。
13
1 磨削用量的影响
14
1 磨削用量的影响
相对滑动
磨损
表面拉残余应力 残余应力小
表面层下h深处 压应力 残余应力小
ห้องสมุดไป่ตู้相对滚动
磨损
20
21
四 表面强化工艺
定义:通过冷加工方法使表面层金属发生冷态塑性变形,以降 低表面粗糙度值,提高表面硬度,并在表面产生压缩残余应力。 (一)喷丸强化 大量快速运动珠丸----打击工件表面----表面产生冷硬层、 压缩残余应力----提高疲劳强度、使用寿命。 主要用于形状复杂工件:板弹簧、螺旋弹簧、连杆、齿轮、
4
三 表层金属的残余应力 (一)原因
刀具切金属---表层金属的纤维被拉长---刀具后刀面 与已加工表面的摩擦加大这种拉伸作用。
刀具切离后---拉伸弹性变形恢复---拉伸塑性变形不 能恢复---表层金属的拉伸塑性变形---受到相连里层未发 生塑性变形金属的阻碍---表层产生压缩残余应力---里层 拉伸残余应力。
持续自激振动的原因
Fy Fa Fv
假设 Fv 具有负摩擦特性,即 vm 越大,v 越小。 F
(F O1 为振入运动的平衡点,即: yo1 Fao1 Fvo1 ) F弹o1
31
参考:
当ap<0.01时,表面强化的冷态塑性变形引起表层比
容增大占主导地位,故表层有较小的压应力(负)。 当0.01<ap<0.05时,磨削表面温升增高,此时表层热作用, 高温塑性变形及表层的回火组织(索氏体或屈氏体)都使表层 的比容缩小,故表层产生较大的拉应力(正)。
当ap>0.05~0.06时,由于磨削表层温升很高,且冷却速度
26
例题: 车 削 一 铸 铁 零 件 的 外 表 面 , 若 走 刀 量 0.5mm / r , 圆 f 车 刀 刀 尖 的 圆 弧 半 径 4mm, 问 能 达 到 的 加 工 表 面 r 粗糙度?
参考: 由于铸铁件加工表面的塑性变形很小,故工 层 加 表面粗糙度主要取决几何因素引起的刀尖留 于 残 面积。 Rz ( 残 留 面 积 高 度 按 下 式 计 算 : )可 f 2 0.5 2 Rz 0.0078mm 8r 8 4
F 切削力:切削过程中工件对刀具的作用力。 y
Fy Fa Fv Fa 是工件表面层金属的弹、塑性 F 变形产生的抗力。 背吃刀量a越大,a 越大。 Fv是刀具与切屑间的摩擦力。
F 弹力:切削过程中振动系统对刀具的作用力。 弹 F弹 F弹 方向始终向左;背吃刀量a越大, 越小。
相对滑动速度:切屑相对于刀具的相对速度。 vm v0 y 振入取+ ;振出取v0 切屑高开工件的速度; y 刀具振动速度。
机械制造工艺过程 第十讲
1
2
第一部分
1 表层金属的残余应力
2 表面强化工艺
3 实战演练
3
三 表层金属的残余应力 (一)原因 机械加工---表层金属塑性变形---表层金属的 比容增大。
塑性变形只在表层产生---表层金属比容增大和 体积膨胀---受到相连里层金属的阻碍---在表层产 生压缩残余应力---里层金属中产生拉伸残余应力。
27
例题: 高 速 精 镗 内 孔 时 , 采锋 利 的 尖 刀 , 刀 具 的 主 用 偏 角K r 45o , 副 偏 角 r 20o , 要 求 加 工 表 面 粗 糙 K 度Rz 3.2( um ), 试 求 : () 不 考 虑 工 件 材 料 塑 变 形 对 表 面 粗 糙 度 影 响 1 当 性 时 , 计 算 应 采 用 的 走量 为 多 少 ? 刀 () 分 析 实 际 加 工 表 面糙 度 与 计 算 求 的 粗 糙 度 2 粗 是否相同,为什么?
造成机床或者夹具间的连接部分松动,刚度和精度下降; 发出噪声,影响工人健康。
38
一 机械加工中的强迫振动 机内振源: 机床旋转件的不平衡(电动机转子、离合器、卡盘、砂轮等) 机床传动机构的缺陷(齿轮、带、链传动的不均匀)
往复运动部件的惯性力(油泵排除的压力油---脉动---空穴)
切削过程中的冲击等(切入、切出产生冲击,加工断续表
17
2 工件材料的影响 工件材料强度高、导热性差、塑性低---拉伸残余应力倾向大。 1)碳素工具刚T8比工业铁强度高、材料变形阻力大 2)磨削时发热量大,导热性差于工业铁,磨削热容易集中于表
层
3)再加上塑性低,热因素作用明显,拉伸残余应力倾向比工业
铁大。
18
工件最终工序加工方法的选择
工件表面残余应力的数值及性质主要取决于工件最终工
负摩擦原理、切削力滞后原理
5 机械加工振动的诊断技术
6 机械加工振动的防治
机械振动
机械振动是指工艺系统或系统的某 些部分沿直线或者曲线并经过其平衡位 置的往复运动。