2.4金刚石刀具解析
论述金刚石刀具超精密切削的机理丶条件和应用范围

金刚石刀具超精密切削的机理丶条件和应用范围
金刚石刀具是超精密切削中常用的刀具材料,其切削机理、条件和应用范围如下:
1.切削机理:
⏹金刚石刀具的切削刃非常锋利,在切削过程中能够实现“切入式切削”,
使切削力大大减小。
⏹金刚石的硬度极高,切削时不易被工件材料磨损,能够保持良好的切削刃
形状。
⏹金刚石的传热性能极佳,能够快速地将切削热量传递出去,从而降低切削
温度,减少热损伤。
1.切削条件:
⏹刀具刃口半径:为了实现超精密切削,需要将刀具的刃口半径减小到亚微
米级,以提高切削的精度和表面粗糙度。
⏹切削用量:为了减小切削力和热量,需要选择较小的切削深度和进给速度,
以提高切削效率。
⏹工件材料:金刚石刀具适用于加工各种硬材料,如淬火钢、硬质合金等。
但是,对于一些韧性较大的材料,需要进行预处理或选择其他刀具材料。
1.应用范围:
⏹金刚石刀具广泛应用于超精密切削领域,如光学零件、轴承、硬盘磁头、IC
芯片等高精度、高表面质量的零件加工。
⏹在加工过程中,金刚石刀具还可以用于制作各种微细结构,如微孔、微槽
等。
综上所述,金刚石刀具的超精密切削需要满足一定的条件,并具有广泛的应用范围。
金刚石材料刀具简介

金刚石材料刀具简介可以制成切削刀具的金刚石材料有天然单晶金刚石、人造单晶金刚石、化学气相沉积法(CVD)金刚石厚膜、人造聚晶金刚石复合片等。
1、天然单晶金刚石天然单晶金刚石是一种各向异性的单晶体。
硬度达HV9000-10000,是自然界中最硬的物质。
这种材料耐磨性极好,制成刀具在切削中可长时间保持尺寸的稳定,故而有很长的刀具寿命。
天然金刚石刀具刃口可以加工到极其锋利。
可用于制作眼科和神经外科手术刀;可用于加工隐形眼镜的曲面;可用于切割光导玻璃纤维;用于加工黄金、白金首饰的花纹;最重要的用途在于高速超精加工有色金属及其合金。
如铝、黄金、巴氏合金、铍铜、紫铜等。
用天然金刚石制作的超精加工刀具其刀尖圆弧部分在400倍显微镜下观察无缺陷,用于加工铝合金多面体反射镜、无氧铜激光反射镜、陀螺仪、录像机磁鼓等。
表现粗糙度可达到Ra(0.01-0.025)μm。
天然金刚石材料韧性很差,抗弯强度很低,仅为(0.2-0.5)Gpa。
热稳定性差,温度达到700℃-800℃时就会失去硬度。
温度再高就会碳化。
另外,它与铁的亲和力很强,一般不适于加工钢铁。
2、人造单晶金刚石人造单晶金刚石作为刀具材料,市场上能买到的目前有戴比尔斯(DE-BEERS)生产的工业级单晶金刚石材料。
这种材料硬度略逊于天然金刚石。
其它性能都与天然金刚石不相上下。
由于经过人工制造,其解理方向和尺寸变得可控和统一。
随着高温高压技术的发展,人造单晶金刚石最大尺寸已经可以做到8mm。
由于这种材料有相对较好的一致性和较低的价格,所以受到广泛的注意。
作为替代天然金刚石的新材料,人造单晶金刚石的应用将会有大的发展。
3、人造聚晶金刚石人造聚晶金刚石(PCD)是在高温高压下将金刚石微粉加溶剂聚合而成的多晶体材料。
一般情况下制成以硬质合金为基体的整体圆形片,称为聚晶金刚石复合片。
根据金刚石基体的厚度不同,复合片有1.6mm、3.2mm、4.8mm等不同规格。
而聚晶金刚石的厚度一般在0.5mm左右。
金刚石刀具刃口的钝化原理
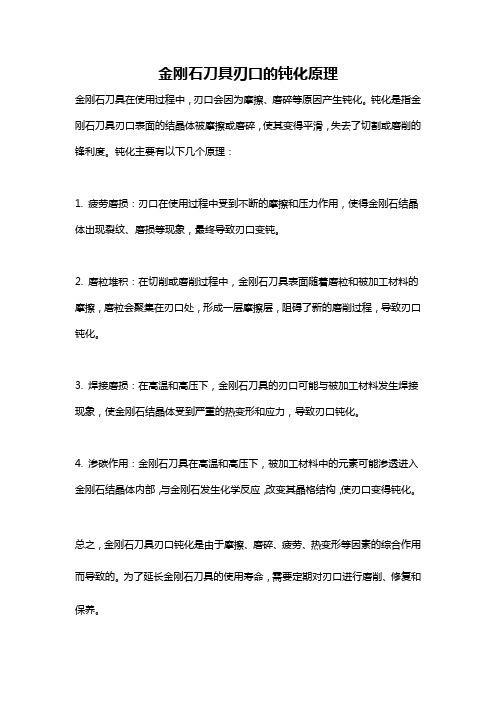
金刚石刀具刃口的钝化原理
金刚石刀具在使用过程中,刃口会因为摩擦、磨碎等原因产生钝化。
钝化是指金刚石刀具刃口表面的结晶体被摩擦或磨碎,使其变得平滑,失去了切割或磨削的锋利度。
钝化主要有以下几个原理:
1. 疲劳磨损:刃口在使用过程中受到不断的摩擦和压力作用,使得金刚石结晶体出现裂纹、磨损等现象,最终导致刃口变钝。
2. 磨粒堆积:在切削或磨削过程中,金刚石刀具表面随着磨粒和被加工材料的摩擦,磨粒会聚集在刃口处,形成一层摩擦层,阻碍了新的磨削过程,导致刃口钝化。
3. 焊接磨损:在高温和高压下,金刚石刀具的刃口可能与被加工材料发生焊接现象,使金刚石结晶体受到严重的热变形和应力,导致刃口钝化。
4. 渗碳作用:金刚石刀具在高温和高压下,被加工材料中的元素可能渗透进入金刚石结晶体内部,与金刚石发生化学反应,改变其晶格结构,使刃口变得钝化。
总之,金刚石刀具刃口钝化是由于摩擦、磨碎、疲劳、热变形等因素的综合作用而导致的。
为了延长金刚石刀具的使用寿命,需要定期对刃口进行磨削、修复和保养。
第2章超精密切削与金刚石刀具详解
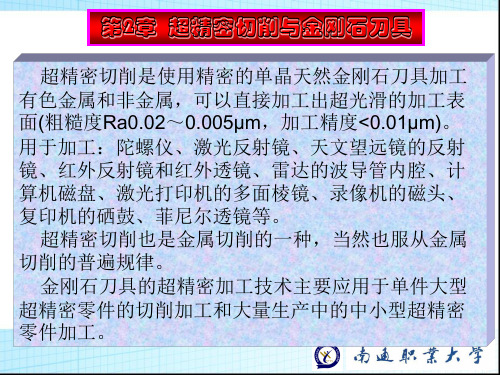
• 1)极高的硬度、极高的耐磨性和极高的弹性模量。 • 2)刃口能磨得极其锋锐,刃口半径值极小,能实现超薄切削厚度。 • 3)刀刃无缺陷,切削时刃形将复制在被加工表面上,从而得到超光滑的 镜面。 • 4)与工件材料的抗粘性好、化学亲和性小、摩擦系数低,以得到极好的 加工表面完整性。 • 不可替代的超精密切削刀具材料:单晶金刚石。
刃口半径为0.6μm、0.3μm
刃口锋锐度对加工表面有一 定的影响,相同条件下(背 吃刀量、进给量),更锋锐 的刀具切出的表面粗糙度更 小;速度的影响不是很大。
2.4 刀刃锋锐度对切削变形和加工表面质量的影响
二、刀刃锋锐度对切削变形和切削力的影响
锋锐车刀切削变形系数明显低于 较钝的车刀。 刀刃锋锐度不同,切削力明显不 同。刃口半径增大,切削力增大, 即切削变形大。背吃刀量很小时, 切削力显著增大。因为背吃刀量很 小时,刃口半径造成的附加切削变 形已占总切削变形的很大比例,刃 口的微小变化将使切削变形产生很 大的变化。所以在背吃刀量很小的 精切时,应采用刃口半径很小的锋 锐金刚石车刀。
2.7 刀具的要求及金刚石的性能和晶体结构
二、金刚石晶体的性能
• • • • 硬度最高,各向异性,不同晶向的物理性能相差很大。 优质天然单晶金刚石:多数为规整的8面体或菱形12面体,少数为6面立方体 或其他形状,浅色透明,无杂质、无缺陷。 大颗粒人造金刚石在超高压、高温下由子晶生长而成,并且要求很长的晶体 生长时间。 人造单晶金刚石已用于制造超精密切削的刀具。
2.3 切削参数变化对加工表面质量的影响
一、切削速度、进给量、修光刃和背吃刀量的影响
3、修光刃的影响
修光刃长度常取0.05~ 0.20mm。 修光刃的长度过长,对 加工表面粗糙度影响不 大。 修光刃有直线和圆弧两 种,加工时要精确对 刀,使修光刃和进给方 向一致。圆弧刃半径一般 取2~5mm。
金刚石刀具在数控机床中的应用

金刚石刀具在数控机床中的应用随着科技的不断进步和发展,数控机床在工业领域中扮演着重要的角色。
数控机床的出现大大提高了生产效率和加工质量,而金刚石刀具作为一种高性能的切削工具,在数控机床中的应用也越来越广泛。
本文将探讨金刚石刀具在数控机床中的应用,并分析其优势和挑战。
一. 金刚石刀具的基本特性金刚石刀具由金刚石颗粒和金属粉末经压制、烧结等工艺制成,具有极高的硬度、耐磨性和热稳定性。
这些特性使得金刚石刀具在切削加工中具备以下优势:1. 高硬度:金刚石刀具的硬度仅次于金刚石,可用于切削超硬材料如陶瓷和高硬度合金等。
2. 耐磨性:金刚石刀具具有出色的耐磨性,可在切削过程中保持较长的使用寿命。
3. 热稳定性:金刚石刀具具有良好的热稳定性,可承受高温切削环境下的工作,不易变形。
二. 金刚石刀具在数控机床中的应用领域1. 切削加工金刚石刀具广泛应用于数控机床的切削加工领域,包括车削、铣削、钻削、磨削等。
由于金刚石刀具的高硬度和耐磨性,可用于加工硬度较高的材料,如钛合金、高速钢等。
同时,金刚石刀具还能够提供更高的加工精度和表面质量。
2. 精密加工在数控机床的精密加工中,金刚石刀具的应用更能体现出其独特的优势。
例如,在汽车零部件的精密加工过程中,采用金刚石刀具可以实现更高的加工精度和更好的表面质量。
3. 工具磨损监测由于金刚石刀具的耐磨性较高,因此可以通过监测金刚石刀具的磨损情况,准确地评估刀具的使用寿命。
这对机床的保养和刀具的及时更换具有重要意义,可降低生产成本,并提高生产效率。
三. 金刚石刀具在数控机床中的挑战虽然金刚石刀具在数控机床中有广泛的应用前景,但面临着一些挑战和限制:1. 成本高昂:金刚石刀具的制造成本较高,所以其售价也相对较高,这给广泛应用带来了一定的限制。
2. 技术要求高:金刚石刀具的加工工艺复杂,需要高精度和高温高压的条件,所以其生产过程要求较高的技术水平。
3. 刀具表面质量难以保证:由于金刚石刀具的硬度很高,常规的抛光或修整技术难以完成对其表面的加工,从而可能会影响到加工表面质量。
金刚石刀具及超硬刀具的区别及优缺点【全面解析】

金刚石刀具与超硬刀具的区别及优缺点内容来源网络,由“深圳机械展(11万㎡,1100多家展商,超10万观众)”收集整理!更多cnc加工中心、车铣磨钻床、线切割、数控刀具工具、工业机器人、非标自动化、数字化无人工厂、精密测量、数控系统、3D打印、激光切割、钣金冲压折弯、精密零件加工等展示,就在深圳机械展.金刚石刀具优缺点超硬刀具的优缺点超硬材料具有优异的机械性能、物理性能和其他性能,其中有些性能很适合于刀具。
具有很高的硬度天然金刚石的硬度达10000HV;CBN的硬度达7500HV。
与其他硬物质相比,SiC硬度为3000~3500HV,A12O3为2700HV,TiC为2900~3200HV,WC为2000HV,Si3N4为2700~3200HV;作为刀具材料用的硬质合金,其硬度仅为1100~1800HV。
具有很好的导热性天然金刚石的热导率达2000W/m-1*K-1,CBN的热导率达1300W/m-1/K-1。
紫铜的导热性很好,其热导率仅为393W/m-1*K-1;纯铝为226W/m-1*K-1,故金刚石与CBN的热导率分别是紫铜的5倍和3.5倍,是纯铝的8倍和5倍。
硬质合金的热导率仅为35~75W/m-1*K-1。
具有很高的杨氏模量天然金刚石的杨氏模量达1000GPa,CBN的杨氏模量在720GPa。
而SiC、Al2O3、WC、TiC的杨氏模量仅分别为390、350、650、330GPa。
物质的杨氏模量大就是刚性好。
具有很小的热膨胀天然金刚石的线膨胀系数为1×10-6/K,CBN的线膨胀系数为(2.1~2.3)×10-6/K。
而硬质合金的线膨胀系数为(5~7)×10-6/K。
具有较小的密度天然金刚石的密度为3.52g/cm3,CBN的密度为3.48g/cm3。
与Al2O3、Si3N4的密度接近。
具有较低的断裂韧性天然金刚石的断裂韧性为3.4MPa/m0.5,CBN与之接近。
金刚石刀具

金刚石刀具
刀具是一种切削金属或非金属材料的工具,刀具应具有足够的硬度、强度、韧性和耐磨性。
由于金刚石能在长时间内保持锐利,当使用得很仔细而又很恰当使,刃口不易损坏,另外金刚石的线膨胀系数很小,比硬质合金低几倍,因此它不会产生很大的热变形,即由切削热引起的刀具尺寸变化甚微,这对尺寸精度要求很高的精车刀来说是非常重要的。
用金刚石车刀加工时,一次加工就能达到就能达到低粗糙度、高精度,避免了以前为达到这些要求而进行很多复杂费时的工序,从而大大提高了生产率,降低了成本。
金刚石刀具可用来对有色金属及其合金以及非金属材料进行高速精细车削及镗孔。
例如精密切削无氧铜、超硬铝、镁及镁合金等有色金属以及塑料、硬橡胶、石墨等,加工尺寸精度可达到一级几何形状精度3 ~ 5μm,加工表面粗糙度可达0.01 ~ 0.08μm。
金刚石刀具也用来加工预烧后的硬质合金毛坯。
金刚石刀具也存在了一些缺点:
(1)耐热性较低,一般切削温度不能超过700 ~800 ℃;
(2)金刚石强度低,对振动很敏感,只适合于精加工;
(3)一般不适合于加工钢铁材料,因为金刚石和铁有很强的化学亲和力。
近年来,金刚石刀具在加工钢铁材料方面开始取得较好的进展
金刚石刀具种类打字可分为三类
(1)一般车刀,它和普通车刀一样,有外圆、断面、内圆用车刀,做成铣刀还可以进行平面切削;
(2)雕刻用车刀,在切入式切削中可以加工钟表等装饰品;
(3)特殊用车刀,包括完全镜面加工用车刀,辊光用工具等。
金刚石刀具的磨损机理

金刚石刀具的磨损机理引言:由于金刚石材料的高硬度和各向同性使其磨损非常缓慢。
是一种理想的刀具材料。
为了充分发挥PCD刀具的切削性能,世界各国先后投入大量人力物力对PCD刀具进行研究。
1、金刚石刀具的磨损形态金刚石刀具的磨损形态常见于前刀面磨损、后刀面磨损和刃口崩裂。
1、金刚石刀具的磨损机理金刚石刀具的磨损机理比较复杂,可分为宏观磨损与微观磨损。
前者以机械磨损为主,后者以热化学磨损为主。
宏观磨损的基本规律如图,早期磨损迅速,正常磨损十分缓慢。
通过高倍显微镜观察,刃口质量越差及锯齿度越大,早期磨损就越明显。
这是因为金刚石刀刃圆弧采用机械方法研磨时,实际得到的是不规则折线如图,在切削力作用下,单位折线上压力迅速增大,导致刀刃磨损加快。
另一个原因是,当金刚石刀具的刃磨压力过大或刃磨速度过高,及温度超过某一临界值时,金刚石刀具表面就会发生氧化与石墨化,使金刚石刀具表面的硬度降低,形成硬度软化层。
在切削力作用下,软化层迅速磨损。
由此可见,金刚石刀具刃磨质量的高低会严重影响它的使用寿命与尺寸精度的一致性。
当宏观磨损处于正常磨损阶段,金刚石刀具的磨损十分缓慢,实践证明,在金刚石的结晶方向上的磨损更是缓慢。
随着切削时间的延长,刀具仍有几十至几百纳米的磨损,这就是微观磨损。
通过高倍显微镜长期观察以及用光谱与衍射分析后,金刚石刀具的微观磨损原因可能有以下3个:1随着切削时间的不断延长,切削区域能量不断积聚,温度不断升高,当达到热化学反应温度时,就会在刀具表面形成新的变质层。
变质层大多是强度甚差的氧化物与碳化物,不断形成,不断随切屑消失,逐渐形成磨损表面。
2金刚石晶体在切削力特别是承受交变脉冲载荷持续作用下,一个又一个C原子获得足够的能量后从晶格中逸出,造成晶体缺陷,原子间引力减弱,在外力作用下晶格之间发生剪切与剥落,逐渐形成晶格层面的磨损,达到一定数量的晶格层面磨损后就会逐渐形成刀具的磨损表面。
3金刚石刀具在高速切削有色金属及其合金时,在长时间的高温高压作用下,当金刚石晶体与工件的金属晶格达到分子甚至原子之间距离时,引起原子之间相互渗透。
- 1、下载文档前请自行甄别文档内容的完整性,平台不提供额外的编辑、内容补充、找答案等附加服务。
- 2、"仅部分预览"的文档,不可在线预览部分如存在完整性等问题,可反馈申请退款(可完整预览的文档不适用该条件!)。
- 3、如文档侵犯您的权益,请联系客服反馈,我们会尽快为您处理(人工客服工作时间:9:00-18:30)。
金刚石晶体的面网及原子排列形式
晶体内部分布有原子的面叫作晶面,也称面网
面网上原子排列形式、原子排列密度及面网间的 距离不同将造成晶体的不同晶向性能差异甚大。 三个重要晶面的原子排列形式—最小单元
金刚石晶体的面网密度及面网距
面网的单位面积上的原子数称为面网密度
三个晶面的面网密度之比为 : (100)(110)面网的分布是均匀的, (111)面网间 距一宽一窄交替看成加厚面网,宽间距即 (111)面间距 (100):(110):(111)=1:1.414:1.154
金刚石刀具结构
常把金刚石固定在小刀头上,小刀头用螺钉压板固定
在刀杆上,也有将金刚石直接固定在车刀刀杆上。
金刚石在刀头上的固定方法
1.较大颗粒的金刚石上下面磨平用压板固定在小刀头上 2.粉末冶金法固定 3.粘接或钎焊固定 金刚石放在合金粉末中,加压真空 粘接剂固定强度不高,金刚石易掉, 烧结,使金刚石固定在小刀头内。应用较多价格较高 钎焊法固定较好,钎料配方及工艺处于研究阶段。
5.金刚石刀具设计的主要问题
优选切削部分的几何形状
前后刀面选择最佳晶面
确定刀具结构及金刚石的固定方法
金刚石刀具切削部分的几何形状
国内多用 直线修光 刃,制造 容易,但
要求对刀
良好,修 光刃应严
格与进给
方向一致
金刚石刀具切削部分的几何形状
国外多用圆弧修光刃,对刀容易使用方便,但
制造研磨费事。推荐圆弧半径R=0.5~1.5mm
金刚石刀具的研磨加工
粗研
一颗单晶金刚石毛坯,要做成精密刀具,先 要晶体定向,确定前后刀面位置,确定需磨去的部分。
仔细检查内部有无缺陷。采用高速旋转铸铁盘加金刚
石微粉进行粗研磨。费时很长,要研究提高其效率, 找准好磨方向,压力9~12N,先用较粗再用细的微粉
精研
是制造金刚石刀具的关键工序,主要考虑提 高研磨质量,使切削刃更锋利。研磨盘小圆周处加细
100晶面的激光衍射图像
垂直(100)晶面的轴称为4次对称轴 垂直(111)晶面的轴称为3次对称轴
垂直(110)晶面的轴称为2次对称轴
110晶面的激光衍射图像
金刚石的三个重要晶面
(100)晶面:正方形,三个面,三根四次对称轴;
(111)晶面:三角形,八个面,四根三次对称轴; (110)晶面: 菱形,六个面,六根二次对称轴
金刚石刀具前后刀面晶面的选择
国外制造的金刚石刀具,前、后刀面有选用
(100)晶面,也有选用(110)晶面,介绍
不详。 国内制造的金刚石刀具,一般前、后刀面都采 用(110)晶面(±3°),研磨效率高,容易
磨出锋利的刀刃。也有推荐(100)晶面,认为
摩擦系数小,刀刃微观强度高,微崩刃机率小
金刚石刀具结构及金刚石固定方法
四、金刚石刀具
超精密加工的重要特征是超微量切除,背吃刀量可在 0.75μm以下,相当于从材料晶格上逐个地去除材料, 只有切削力超过晶体内部的原子结合力才能产生切削 作用,而加工极限又受刀具刃口圆弧半径的限制。 1. 超精密切削对刀具的要求 1)极高的硬度、耐磨性和极高的弹性模量; 2)刃口能磨得极其锋利,刃口半径ρ 值ห้องสมุดไป่ตู้小; 3)刀刃无缺陷,以得到超光滑的镜面; 4)与工件材料的抗粘结性好、化学亲和性小、摩擦
为了充分发挥金刚石刀具的切削性能和保证
加工质量,设计和制造金刚石刀具时须正确
选择晶体方向。
金刚石晶体定向方法有:
1.人工目测定向
适于优质规整晶体,方便精度低
2.X射线晶体定向
3.激光晶体定向
X光衍射图像精度高价高有害健康
价格低1/10,操作简便足够的精度
金刚石晶体的激光定向
利用金刚石在不同晶面上对激光反射形成的 衍射图像不同而进行定向。
3.金刚石各晶面的好磨难磨方向
不同晶面耐磨性不同,且同一晶面上不同方向耐
磨性亦有很大差别。金刚石的耐磨性可用它的相对 磨削率来表示。
110
100 111
在高磨削率方向,(100):(111):(110)=5.8:1:12.8
对金刚石研磨时,各晶面均有 “好磨”和“难磨”方向
4.正确选择金刚石晶体方向
微粉用于精研,采取逆磨,即沿刃口指向刀体内的方
向研磨,切削刃承受压应力,得到锋利完好的刃口。
不重磨精密金刚石刀具
金刚石刀具的制造研磨及用钝重磨,是一项
保密性很强,难度很大的技术。国外多数使
用厂不自己磨刀,用钝后送回制造厂重磨。
国外有些公司推出一次性使用不重磨的精密
金刚石刀具。使用小颗粒金刚石,价格便宜。
三个晶面的实际面网密度之比为: (100):(110):(111)=1:1.414:2.308
金刚石晶体(111)晶面硬度和耐磨性最高
金刚石的解理现象
由固体物理学理论知,原子密度较大的晶面 之间的距离也较大,面间原子结合力弱,受 力时可沿平行该面方向平整的劈开,该现象 称为解理现象。
金刚石晶体可沿解理面 (111)平整的劈开两半 研究表明金刚石的破 损磨损主要形式是微 观解理。
金刚石钎焊在硬质合金刀片上,用螺钉夹固 在车刀刀杆上。金刚石由制造厂磨得很锋利, 使用厂用钝后不再重磨。
生长而成。
2.金刚石的晶体结构
金刚石晶体属于立方晶系,天然单晶多为
8面体和12面体,人造单晶常为6面体8面
体和12面体 金刚石晶体具有各向异性和解理现象,不 同晶向的物理性能相差很大。 金刚石晶体有三个主要晶面:(100)(110) (111)。
金刚石晶体的晶轴
111晶面的激光衍射图像
系数低,以得到极好的加工表面完整性。
单晶金刚石
天然单晶金刚石具有优异的特性,虽然价格较贵 但被公认为理想的、无法代替的超精切刀具材料 人造金刚石1954年美研
制成功,细颗粒(制砂
轮)→聚晶金刚石→大 颗粒单晶金刚石。
大颗粒人造单晶金刚石
是在超高压(500MPa) 高温(1300℃)下由子晶