金刚石刀具的选用
单晶金刚石刀具的应用
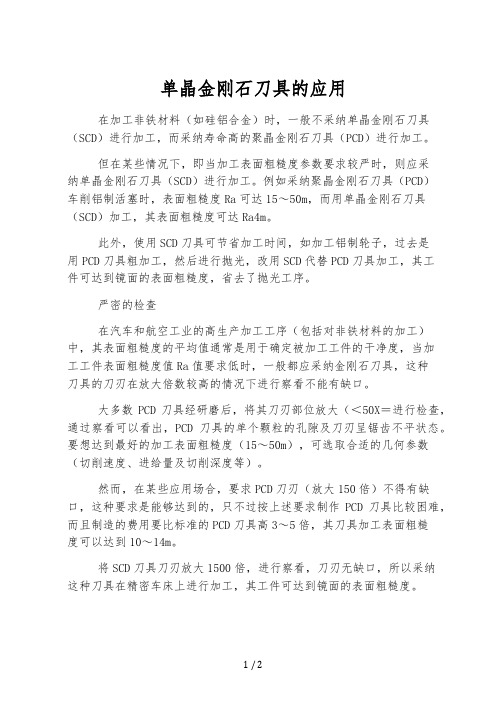
单晶金刚石刀具的应用在加工非铁材料(如硅铝合金)时,一般不采纳单晶金刚石刀具(SCD)进行加工,而采纳寿命高的聚晶金刚石刀具(PCD)进行加工。
但在某些情况下,即当加工表面粗糙度参数要求较严时,则应采纳单晶金刚石刀具(SCD)进行加工。
例如采纳聚晶金刚石刀具(PCD)车削铝制活塞时,表面粗糙度Ra可达15~50m,而用单晶金刚石刀具(SCD)加工,其表面粗糙度可达Ra4m。
此外,使用SCD刀具可节省加工时间,如加工铝制轮子,过去是用PCD刀具粗加工,然后进行抛光,改用SCD代替PCD刀具加工,其工件可达到镜面的表面粗糙度,省去了抛光工序。
严密的检查在汽车和航空工业的高生产加工工序(包括对非铁材料的加工)中,其表面粗糙度的平均值通常是用于确定被加工工件的干净度,当加工工件表面粗糙度值Ra值要求低时,一般都应采纳金刚石刀具,这种刀具的刀刃在放大倍数较高的情况下进行察看不能有缺口。
大多数PCD刀具经研磨后,将其刀刃部位放大(<50X=进行检查,通过察看可以看出,PCD刀具的单个颗粒的孔隙及刀刃呈锯齿不平状态。
要想达到最好的加工表面粗糙度(15~50m),可选取合适的几何参数(切削速度、进给量及切削深度等)。
然而,在某些应用场合,要求PCD刀刃(放大150倍)不得有缺口,这种要求是能够达到的,只不过按上述要求制作PCD刀具比较困难,而且制造的费用要比标准的PCD刀具高3~5倍,其刀具加工表面粗糙度可以达到10~14m。
将SCD刀具刀刃放大1500倍,进行察看,刀刃无缺口,所以采纳这种刀具在精密车床上进行加工,其工件可达到镜面的表面粗糙度。
在采纳PCD刀具加工非铁和非金属材料不能达到所要求的加工表面粗糙度时,可在加工中心上用SCD刀具加工,省去以住的抛光工序。
金刚石刀头如其它刀具材料一样,SCD刀具不是对每种加工都适合,在选择时应考虑以下几点:切削深度:SCD刀具刃口很锋利,当采纳大切深进行加工时,其加工效果不够明显,这在很大程度上取决于工件材料、切削速度和进给量,所以切削深度大于0.02mm时,不宜采纳SCD刀具进行加工,最好先用PCD刀具进行粗加工,然后用SCD刀具进行精加工。
论述金刚石刀具超精密切削的机理丶条件和应用范围

金刚石刀具超精密切削的机理丶条件和应用范围
金刚石刀具是超精密切削中常用的刀具材料,其切削机理、条件和应用范围如下:
1.切削机理:
⏹金刚石刀具的切削刃非常锋利,在切削过程中能够实现“切入式切削”,
使切削力大大减小。
⏹金刚石的硬度极高,切削时不易被工件材料磨损,能够保持良好的切削刃
形状。
⏹金刚石的传热性能极佳,能够快速地将切削热量传递出去,从而降低切削
温度,减少热损伤。
1.切削条件:
⏹刀具刃口半径:为了实现超精密切削,需要将刀具的刃口半径减小到亚微
米级,以提高切削的精度和表面粗糙度。
⏹切削用量:为了减小切削力和热量,需要选择较小的切削深度和进给速度,
以提高切削效率。
⏹工件材料:金刚石刀具适用于加工各种硬材料,如淬火钢、硬质合金等。
但是,对于一些韧性较大的材料,需要进行预处理或选择其他刀具材料。
1.应用范围:
⏹金刚石刀具广泛应用于超精密切削领域,如光学零件、轴承、硬盘磁头、IC
芯片等高精度、高表面质量的零件加工。
⏹在加工过程中,金刚石刀具还可以用于制作各种微细结构,如微孔、微槽
等。
综上所述,金刚石刀具的超精密切削需要满足一定的条件,并具有广泛的应用范围。
金刚石刀具知识点

⾦刚⽯⼑具知识点⼑具基础知识⼀、⼑具材料应具备的性能;A,⾼的硬度和⾼耐磨性1.硬度是⼑具材料应具备的基本特性2.耐磨性是指材料抵抗磨损的能⼒。
B,⾜够的强度和韧性1.强度是⼑具材料抵抗破坏的能⼒2,韧性是指材料发⽣断裂时外界做功的⼤⼩。
3.⾼的耐热性和热传性4.良好的⼯艺性和经济性1)切削性能⽬前⼑具材料分四⼤类:⼯具钢、硬质合⾦、陶瓷及超硬⼑具材料等。
常⽤的⼑具材料⼀、⼯具钢1. 碳素⼯具钢碳素⼯具钢是含碳量为0.65%~1.3%的优质碳素钢。
常⽤的钢号有T7A、T8A等。
耐热温度:200℃~300℃。
2. 合⾦⼯具钢1868年,英国的穆舍特制成含钨的合⾦⼯具钢。
在碳素⼯具钢中加⼊适当的元素铬(Cr)、硅常⽤的合⾦⼯具钢有9CrSi,CrWMn等(Si)、锰(Mn)、钒(V)、钨(W)等炼成的。
耐热温度:325℃~400℃。
主要⽤于制造细长的或截⾯积⼤、刃形复杂的⼑具。
⼆,⾼速钢⾼速钢是⼀种富含钨(W)、铬(Cr)、钼(Mo)、钒(V)等元素的⾼合⾦⼯具钢。
美国的F.W.泰勒和M.怀特于1898年创制的。
含碳量⼀般在0.70~1.65%之间。
耐热温度:500℃~650℃。
⾼速钢的抗弯强度是硬质合⾦的3~5倍,冲击韧性是硬质合⾦的6~10倍1.普通⾼速钢(HSS)2.钨系⾼速钢:W18Cr4V (W18)3.具有较好的综合性能,可制造复杂刃型的⼑具。
但由于钨是稀有⾦属,现在很少使⽤。
4.钨钼系⾼速钢:W6Mo5Cr4V2 (M2)5.M2的碳化物颗粒⼩,分布均匀,具有较⾼的抗弯强度、塑性、韧性和耐磨性。
⼜因为钼的存在,使其热塑性⾮常好。
2. ⾼性能⾼速钢(HSS-E)⾼性能⾼速钢是在普通⾼速钢中增加⼀些碳、钒及添加钴(Co)、铝等元素的新钢种。
钴⾼速钢:W2Mo9Cr4VCo8 (M42)⼀种含钴的超硬⾼速钢,常温硬度67HRC-69HRC,具有良好的综合性能。
铝⾼速钢:W6Mo5Cr4V2Al在M2的基础上加Al、增C,提⾼了钢的耐热性和耐磨性。
CVD金刚石刀具材料的制备、性质与应用
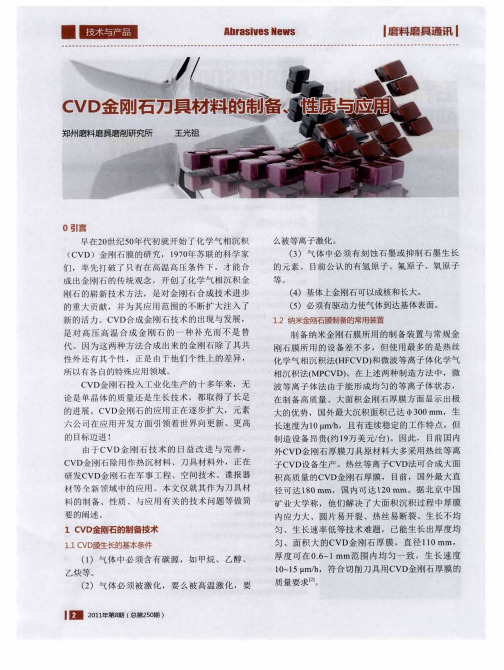
Ar ises b seNw av
■ 叠 曩 ■ 团 嗣
传 统 的CVD法 是 以 大 量 氢 气 为 主 要 反 应 气
体 ,同 时加 入 少 量 的碳 源 气 体 ( 于5 ,沉积 出 少 %)
33要解 决大面 积沉 积 过程 中厚 膜 内应力 大 、圆 片 . 易开 裂 、热 丝 易 断裂 、生 长 不均 匀 、生 长速 率低 等 技术 难题 ,长 期 以来 一直 困扰 着制造 商 。 34C D金 刚石 厚膜 与硬质 合 金基体 之 间 的焊 接 强 . V
Notn 司宣 称 ,其 牌 号 为Dima a 的C r 公 o a P k VD
36干 切 削是 未来 切 削的主 要方 向。随 着切 削速 度 . 的提 高 (20 0m/ n 9 0 mi ),C VD厚膜 切 削刀具 会 成 为干 式高速 切 削某些新 材料 的首 选工 具 。 ]
10 2 0 t %~ 0 % 源自 0美 国NotnFl 司推 出的牌 号 为Dima a r i o m公 a Pk 的C D金 刚石 复 合片 ,也 是03 V - mm或 05mm厚度 . 的C VD金 刚石 层 焊 接 到硬 质 合 金 基底 上 ,刀 片 总 厚度 为 1 .mm,可 根据 用户 需要 提供 各种 形状 。 6
小 晶粒 尺 寸 。在 纳 米 金 刚石 生 长 中 ,C 是 重 要 的 2 参与 者与 决定 性 的成分 。 J
度 ,是 决 定C VD刀具 用 于 断续 切 削 这种 高 要 求机
械 加工 的关键 。
C VD金 刚 石 用 于 切 削有 两 种 形 式 : 聚 晶质 C VD金 刚 石 薄膜 和 单 晶质 C 金 刚石 厚膜 ,可切 VD 割成 不 同形状 。单 晶 质C VD金 刚 石 切割 工 具 主要 用于 加 工 强 度 高而 质 量 轻 的结 构材 料 ,如 金 属基 体 复合 材 料( MMC ) ,存 在 的 问题是 不能制 成 形 S等
金刚石(PCD)铰刀的产品介绍及应用

量,是对金刚石铰刀寿命有很大的影响。 ⑥ 前导向部:前导部是考虑与加工前的孔,其中最小间隙为10--20米欧。
同时还需要注意冷却槽的设计 金刚石铰刀铰孔时,若热量和切屑来不及排出,刀体将发热膨胀,孔的加工质量会明显降低,严重时还会发生“咬死”刀现象。
内镀法
金刚石铰刀内镀的方法: 采用稳定材料制造一个与铰刀外形相反的
高精度内孔胎模,将金刚石磨粒电镀在胎模内表 面,加厚形成电镀层,再将镀层与刀杆粘结在一 起。
金刚石颗粒的顶端整齐,规则地排列在模具 的内表面上,等高性和均匀性较好;
无需修磨,微刃锋利;
所加工孔的尺寸精度和几何精度较高,表面 粗糙度较小,使用寿命较长。
2 PCD铰刀
PCD铰刀的定义及优势
PCD铰刀,一般根据直径大小,采用合金基体或者钢制基体。刃数为2刃或2刃以上。此类刀具主要用于加工公 差要求比较严格,光洁度要求比较高的孔,通孔盲孔均可加工。此类刀具加工的孔,光洁度最高可达Ra0.1以内。
PCD铰刀的优势
具有超高硬度和耐磨性; 具有超长刀具使用寿命; 切削性能稳定,加工效率高; 提高尺寸精度和工艺可靠性。
备注:一般直径15mm左右的可以做成可调式金刚石铰刀,但由于国内市场,可调式金刚石铰刀精度没有固定时金刚 石铰刀好,如果要求精度较高的情况下, 建议选择固定式金刚石铰刀
金刚石铰刀的组成结构及优势
金刚石铰刀的优势
镀层结合力,金刚石粘结牢度,金刚石颗粒分布均匀,外观质量高; 金刚石铰刀前后导向外圆度达到0.005mm,圆柱度为0.005mm/100mm,前导向外圆粗糙度Ra0.63微米, 后导向外圆粗糙度Ra0.16um,刀柄与前后导向部分的同轴度达到0.015mm; 被铰孔工件圆柱度小于0.003,粗糙度可达Ra0.4-0.2,精度高,效率高,使用寿命长; “量体裁衣”式服务,规范化流程,为客服创造的价值超越契约。
金刚石刀具

金刚石刀具金刚石刀具具有极高的硬度和耐磨性、低摩擦系数、高弹性模量、高热导、低热膨胀系数,以及与非铁金属亲和力小等优点。
可以用于非金属硬脆材料如石墨、高耐磨材料、复合材料、高硅铝合金及其它韧性有色金属材料的精密加工。
金刚石刀具类型繁多,性能差异显著,不同类型金刚石刀具的结构、制备方法和应用领域有较大区别。
天然金刚石刀具目前主要用于紫铜及铜合金和金、银、铑等贵重有色金属,以及特殊零件的超精密镜面加工,如录相机磁盘、光学平面镜、多面镜和二次曲面镜等。
但其结晶各向异性,刀具价格昂贵。
PCD的性能取决于金刚石晶粒及钴的含量,刀具寿命为硬质合金(WC基体)刀具的10~500倍。
主要用于车削加工各种有色金属如铝、铜、镁及其合金、硬质合金和耐磨性极强的纤维增塑材料、金属基复合材料、木材等非金属材料。
切削加工时切削速度、进给速度和切削深度加工条件取决于工件材料以及硬度。
人造聚晶金刚石复合片(PDC)性能和应用接近PCD刀具,主要用在有色金属、硬质合金、陶瓷、非金属材料(塑料、硬质橡胶、碳棒、木材、水泥制品等)、复合材料等切削加工,逐渐替代硬质合金刀具。
由于金刚石颗粒问有部分残余粘结金属和石墨,其中粘结金属以聚结态或呈叶脉状分布会减低刀具耐磨性和寿命。
此外存在溶媒金属残留量,溶媒金属与金刚石表面直接接触。
降低(PDC)的抗氧化能力和刀具耐热温度,故刀具切削性能不够稳定。
金刚石厚膜刀具制备过程复杂,因金刚石与低熔点金属及其合金之间具有很高的界面能。
金刚石很难被一般的低熔点焊料合金所浸润。
可焊性极差,难以制作复杂几何形状刀具,故TDF焊接刀具不能应用在高速铣削中。
金刚石涂层刀具可以应用于高速加工,原因是除了金刚石涂层刀具具有优良的机械性能外,金刚石涂层工艺能够制备任意复杂形状铣刀,用于高速加工如铝钛合金航空材料和难加工非金属材料如石墨电极等。
显示为纯金刚石。
ND是目前已知矿物中最硬的物质,主要用于制备刀具车刀。
天然金刚石刀具精细研磨后刃口半径可达0.01~0.002µm。
金刚石刀具标准

金刚石刀具标准引言金刚石是一种无色晶体,硬度排名世界第一。
由于其优异的硬度和耐磨性能,金刚石被广泛用作工业材料,特别是在切削和磨削工具领域。
本文将介绍金刚石刀具的标准,包括金刚石刀具的分类、性能要求、测试方法以及标准化组织。
一、金刚石刀具的分类根据金刚石刀具的用途和结构,金刚石刀具可以分为以下几类:1.金刚石砂轮:用于磨削和抛光材料的表面,例如金属、玻璃、陶瓷等。
2.金刚石锯片:用于切割各种材料,如石材、玻璃、陶瓷、金属等。
3.金刚石钻头:主要用于钻孔,可钻取混凝土、砖石、岩石等硬质材料。
4.金刚石刀片:用于切割各类材料,如金属、玻璃、陶瓷、塑料等。
二、金刚石刀具的性能要求由于金刚石具有高硬度、高耐磨性和高热导率等特点,金刚石刀具在使用过程中需要具备以下性能:1.高硬度:金刚石刀具应具有足够的硬度,以确保在切割和磨削过程中不易磨损。
2.高耐磨性:金刚石刀具应具有出色的耐磨性能,能够承受长时间的使用而不损坏。
3.高热导率:金刚石刀具应具备良好的热导率,以便及时散热,防止刀具过热。
4.良好的切削性能:金刚石刀具应具备良好的切削性能,以确保切削效果稳定。
三、金刚石刀具的测试方法为确保金刚石刀具的质量和性能符合标准要求,需要进行相应的测试。
以下是常用的金刚石刀具测试方法:1.硬度测试:通过Vickers硬度测试仪进行硬度测试,以确定金刚石的硬度。
2.耐磨性测试:使用标准化的磨损测试设备,在一定条件下进行耐磨性测试,评估金刚石刀具的耐磨性能。
3.热导率测试:采用热导率测试仪,测试金刚石刀具的热导率,以评估其散热性能。
4.切削性能测试:使用特定的材料进行切削实验,通过切削力、表面质量等指标评估金刚石刀具的切削性能。
四、金刚石刀具标准化组织金刚石刀具的制定和管理工作需要一个专门的标准化组织来制定和推广相关标准。
以下是一些国际上常用的金刚石刀具标准化组织:1.国际电工委员会(IEC):IEC负责制定和推广有关电气、电子和相关技术的国际标准,其中包括金刚石刀具的相关标准。
超精密切削加工与金刚石刀具(精密加工

2.5 切削刃锋锐度对切削变形、加工表面质量的影 响
三、切削刃锋锐度对切削变形和切削力的影响
2021/5/1
锋锐车刀切削变形系数明显低于 较钝的车刀。 刀刃锋锐度不同,切削力明显不 同。刃口半径增大,切削力增大, 即切削变形大。背吃刀量很小时, 切削力显著增大。因为背吃刀量很 小时,刃口半径造成的附加切削变 形已占总切削变形的很大比例,刃 口的微小变化将使切削变形产生很 大的变化。所以在背吃刀量很小的 精切时,应采用刃口半径很小的锋 锐金刚石车刀。
(FN ) Ff cos FP sin
A点为极限临界点,极限最小切削厚度 hDmin 应为
hDmin rn(1 cos ) rn1
2021/5/1
第2章 超精密切削与金刚石刀具
2.1超精密切削时刀具的切削速度、磨损和耐用度 2.2超精密切削时积屑瘤的生成规律 2.3切削参数变化对加工表面质量的影响 2.4刀刃锋锐度对切削变形和加工表面质量的影响 2.5超精密切削时的最小切削厚度 2.6金刚石刀具晶面选择对切削变形和加工表面质
2021/5/1
2.2 超精密切削时刀具的磨损和寿命
后刀面 前刀面
2021/5/1
图2-2:切削刃正常磨损;
图 2-3 : 图 a 是 刀 刃 磨 损 的 正常情况,图b是剧烈磨损 情况,可以看到磨损后成 层状,即刀具磨损为层状 微小剥落;
图2-4:图中所示沿切削速 度方向出现磨损沟槽,由 于金刚石和铁、镍的化学 和物理亲和性而产生的腐 蚀沟槽;
2.3 超精密切削时积屑瘤的生成规律
2、进给量f和背吃刀量 p的影响
• 由图2-7可以看出在进给量很小时,积屑瘤的高度很大,在 f=5μm/r时,h0值最小,f值再增大时,h0值稍有增加。
- 1、下载文档前请自行甄别文档内容的完整性,平台不提供额外的编辑、内容补充、找答案等附加服务。
- 2、"仅部分预览"的文档,不可在线预览部分如存在完整性等问题,可反馈申请退款(可完整预览的文档不适用该条件!)。
- 3、如文档侵犯您的权益,请联系客服反馈,我们会尽快为您处理(人工客服工作时间:9:00-18:30)。
金刚石刀具的种类与选用摘要:简要介绍了金刚石材料的的主要性能特点?并对近几年来正在迅速发展的金刚石切削刀具的特点、性能、种类及其选用方法作了较为详细的叙述。
关键词:天然金刚石聚晶金刚石PCI刀具CVD刀具切削性能刀具寿命目前世界上金刚石的年耗量大约以8%——10%的速度增长?有人预言21世纪将是金刚石全面应用的时代,我国对人造金刚石的研究与应用始于20世纪70年代,并于1969年在贵阳建造了第1个人造金刚石及其制品的专业生产厂——第六砂轮厂。
从1970——1990年,人造金刚石年产量从46万克拉增至3500万克拉。
20世纪90年代前后,从国外引进了先进设备及金刚石生产技术,产量迅速增,1997年我国人造金刚石年产量已达到5亿克拉左,生产量位居世界首位。
金刚石是碳的同素异形体,是目前已知的最硬物质?其显微硬度可达HV10000,作为刀具材料,也是目前最硬的,并已得到广泛应用。
在合适的切削加工条件下,金刚石刀具比高速钢、硬质合金、陶瓷和聚晶立方氮化硼等刀具的使用寿命都要长。
特别是用金刚石刀具切削加工铜、铝等有色金属和非金属耐磨材料时特别有效?其切削速度可比硬质合金刀具高一个数量级,例如铣削铝合金的切削速度为3000——4000m/min,甚至可达到7000m/min,且这时的金刚石刀具使用寿命也比硬质合金刀具高几十、甚至几百倍。
金刚石刀具不但可用于一般的车、镗、铣削,还成功地用于精密孔的加工前保证光刻胶线宽与设计一致,并且在需要电铸的部位光刻胶显影干净,在电铸时调整电铸条件和参数得到最佳的电铸效果?只有满足以上工艺要求制备的微弹簧才能获得较好的力学性能。
当微弹簧所受拉力增大,便脱离弹性阶段,此时拉力-伸长曲线进入第2段,变为非线形金刚石刀具的种类较多,可分为:单晶金刚石刀具、聚晶金刚石(PCD)、聚晶金刚石复合片(PCD)、CVD金刚石刀具和电镀金刚石刀具。
单晶金刚石刀具单晶金刚石有天然的(ND)和人工合成的2种(单晶金刚石用作切削刀具必须是大颗粒的,一般其质量要大于0.1g其最小直径和长度均不得小于3mm,单晶金刚石刀具主要用于对表面粗糙度、几何形状精度和尺寸精度有较高要求的精密加工领域。
天然单晶金刚石是金刚石中最耐磨的材料(它本身质地细密,经过精细研磨,切削刃的刃口圆弧半径可小到0.010——0.002um。
但天然单晶金刚石较脆,其结晶各向异性,不同晶面或同一晶面不同方向的晶体硬度均有差异,在进行刃磨和使用时必须选择合适的方向,使用条件较为苛刻,且资源有限,价格十分昂贵(天然单晶金刚石刀具主要用于某些有色金属的超精密切削加工或用于黄金首饰的生产加工中。
人工合成单晶金刚石的尺寸、形状和性能都具有良好的一致性,目前由于高温、高压技术日趋成熟,能够制备一定尺寸的人工合成单晶金刚石,南非DC Boors公司和美国生产的合成单晶金刚石颗粒尺寸可达9——10mm,使人工合成单晶金刚石的应用在工业生产中得到了迅速的发展。
尤其在加工高耐磨的层状木板时,其切削性能要优于PCD金刚石,不会引起刃口的过早钝化。
聚晶金刚石及其复合刀片(PCD/CC)PCD是在高温、高压下,利用钴等金属结合剂将许多金刚石单晶粉聚晶成多晶体材料。
其硬度虽然稍低于单晶金刚石,但它是随机取向的金刚石晶粒的聚合,属各向同性,用作切削刀具时可以任意取向刃磨,而无需像刃磨天然金刚石那样必须选用最佳的解理面作为前刀面。
而且PCD原料来源丰富,其价格只有ND的几十分之一至十几分之一。
在切削时,切削刃对意外损坏不很敏感,抗磨损能力也较强,可长时间保持锋利的切削刃,加工时可采用很高的切削速度和较大的切深,例如在车削或镗削铝合金、黄铜、青铜及其合金时,切削速度为300——1000m/min,进给量为0.05——0.5mm/r切深可达10mm,使用寿命一般高于WC 基硬质合金刀具10——500倍,已成为传统WC基硬质合金刀具的高性能替代品。
为提高PCD刀片的韧性和可焊性,可用硬质合金为基底,在其表面烧结或压制一层0.5_——1mm厚的PCD而组成金刚石复合刀片(PCD/CC)。
PCD/CC可用钎焊或机夹方式制作刀具。
由于其可焊性好,重磨容易,成本低,故应用广泛"。
英国Smith公司研制的多层金刚石复合刀片,其顶层金刚石浓度为100%,往内逐步下降!同时硬质合金逐渐增加!到衬底全部为硬质合金。
这种复合刀片的强度高!抗冲击性能好!特别适用于大切深、有冲击载荷的加工使用。
日本住友电工公司采用铁基合金作基体,所制造的金刚石复合刀片钻头因PCD 与钢刀体有亲和作用,可保证复合刀片与刀体的连结更为牢固。
PCD的性能与金刚石晶粒尺寸大小及结合剂的含量有关。
DC Boors公司生产的PCD复合刀片有关002、010和025几种!晶粒的平均尺寸分别为2um、10um、25um。
晶粒尺寸越大,耐磨性越好,刀具寿命越高,但切削刃较粗糙,刃口质量差;中晶粒(如DC Boors公司生产的010)一般作为机械加工的通用牌号细晶粒刀具的切削刃的刃口钝圆半径r小(一般PCD刀具的r为1——2um),易加工出良好的零件表面纹理,加工表面质量好。
因而目前聚晶的晶粒不断细化,并已有1um以下的细晶,需根据粗、精加工等不同工序的要求,选用不同大小的晶粒。
但我国学者研究证实!聚晶体刀具在微量切削时,具有“多点切削、单点成形”的特点,因此只要采取一定的工艺措施!用粗晶粒(70——30um)聚晶刀具也同样有可能切出超精密的加工表面。
因金刚石与铁之间有化学反应,故一般不推荐PCD刀具加工黑色金属材料,PCD.刀具可用来加工含铁的双金属复合材料。
例如,美国一家汽车配件厂用PCD复合刀片制作的直径为305mm机夹盘铣刀加工铝和铸铁的双金属气缸体时,切削速度为305m/min,每齿进给量为0.1mm,切深为5mm,加工5000个气缸体后,刀片才需转位1次。
需要指出,PCD刀具的刃口锋利性和加工表面质量均不如ND,同时其可加工性差,磨削比小,刀头刃形难以任意成形,至今还不能方便地制造带断屑槽可转位刀片和立铣刀等几何形状复杂的产品。
化学气相沉积(CVD)金刚石刀具CVD金刚石是一种高抗磨性的纯金刚石材料,不含结合剂,它是在低于1000C的温度和低压(<0.1MPa)条件下制备的。
CVD金刚石有2种形式CVD薄膜(CD)和CVD厚膜(TFD) CD是用CVD工艺,在硬质合金基(常用K类合金)上沉积一层厚度小于50um(通常为10——30um),由多晶组成的膜状金刚石而成"因基体易于制成复杂形状,故适用于几何形状复杂的刀具,如丝锥、钻头、立铣刀和带断屑槽可转位刀片等。
国际工具市场上已有CD刀具的产品(如瑞典Sandvik公司的CD1810和美国Kcnnamctal公司的KCD25等牌号),用于有色金属及非金属材料的高速精密加工!刀具寿命比未涂层的硬质合金刀具提高近十倍!有些甚至数十倍,但CD刀具不适于加工带有硬质颗粒的金属基复合材料,因为硬质颗粒会在很短时间内将刀具表面涂层磨穿。
所以尽管CD刀具的价格比同类PCD刀具要低,且由于金刚石薄膜与基体材料间的黏着力较小,限制了它的广泛应用!到目前为止,CD刀具的市场份额不是很大。
TFD是沉积厚度可达1mm、甚至达5mm的无衬底金刚石厚膜!根据需要再将厚膜切割成一定形状的小块,然后钎焊到所要求的基体材料上制成刀具使用。
TFD由于较好地解决了金刚石膜与基体材料间的黏着力问题,且厚膜刀具刃磨方便,可获得良好的表面粗糙度和极小的刃口半径。
TFD还有很好的综合性能,它没有天然金刚石各向异性的缺点;与PCD 相比较,因PCD内含有钴等金属结合剂,会降低硬度!对腐蚀敏感(特别是在加工塑料时),钴在高温下会加速金刚石向石墨转变,故PCD适于粗加工和要求刀具有较高断裂韧性的场合。
而TFD为纯金刚石材料,不添加任何复合材料,因此具有更高的硬度、热导率、致密性、刃口锋利性、耐磨性(为PCD的1——4倍)、耐高温性、化学稳定性以及更小的摩擦因数,故可采用比PCD刀具更高的切削速度,韧性则稍低于PCD。
且容易在切削中产生微观裂纹,甚至发展成崩刃。
国外、国内都已有TFD的商品,如Dc Bccrs公司的.DIAFILM品牌,国内北京天地公司超硬材料工具厂生产的TFD产品。
尽管目前TFD刀具的价格较贵,但随着制造工艺的完善!生产成本的降低,今后有望可替代昂贵的天然金刚石刀具及部分PCD刀具。
3种人造金刚石各有特点,在一定程度上能相互补充,须根据不同具体情况,以及它们的性能价格比加以选用。
通常PCD刀具适合于粗加工和要求刀具有较高断裂韧性的场合,CVD厚膜和单晶金刚石刀具多用于高速精加工和半精加工等场合。
电镀金刚石刀具电镀金刚石刀具是用电镀金属镍、铜和钴等作结合剂,把大量金刚石的细小颗粒包镶在一定尺寸和几何形状的刀具基体表面上,再经过适当修磨而制成。
此法制造工艺简单,只需要电镀设备即可。
使用表明,用其可成功地加工尺寸精度和几何形状精度都小于2um表面粗糙度达R0.4——0.2um的孔,且加工出的孔尺寸分散度小。
该刀具还具有使用寿命长(平均每把刀具可加工1——2万个工件)、加工效率高的特点。
例如!,用于液压随动系统和燃油系统精密偶件的阀孔、机械和精密仪表中各种精密孔,目前生产上的最终工序大多用这种铰刀加工。
金刚石刀具的非常规使用通常很少应用金刚石刀具加工灰铸铁,以避免金刚石与铸件中的铁元素产生化学反应。
然而这种情况只有在高温时才会发生。
例如,用PCD刀具切削时,当温度达到650C时,金刚石会在空气中开始氧化,而达到700——800时它将石墨化。
在低温时,这些材料之间是不会发生反应的。
所以,只要选用低的切削速度,使切削温度保持在一定范围内,金刚石刀具是完全可以加工铸件的。
金刚石刀具的使用机械加工的一次飞跃,正确地选用金刚石刀具会让它飞的更高!。