车削加工上下料机器人
机器人上下料方案
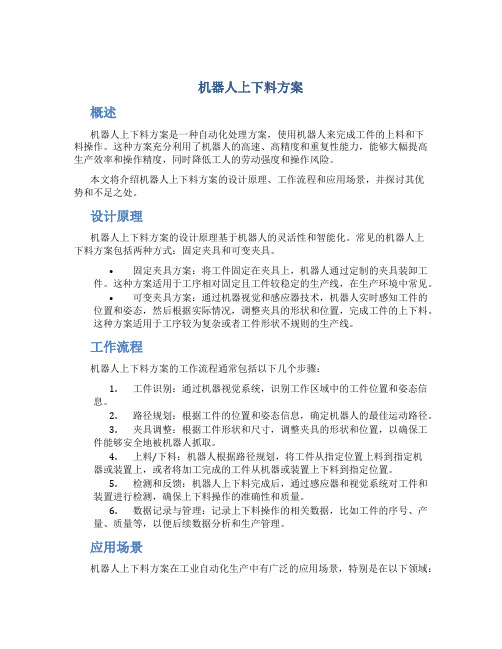
机器人上下料方案概述机器人上下料方案是一种自动化处理方案,使用机器人来完成工件的上料和下料操作。
这种方案充分利用了机器人的高速、高精度和重复性能力,能够大幅提高生产效率和操作精度,同时降低工人的劳动强度和操作风险。
本文将介绍机器人上下料方案的设计原理、工作流程和应用场景,并探讨其优势和不足之处。
设计原理机器人上下料方案的设计原理基于机器人的灵活性和智能化。
常见的机器人上下料方案包括两种方式:固定夹具和可变夹具。
•固定夹具方案:将工件固定在夹具上,机器人通过定制的夹具装卸工件。
这种方案适用于工序相对固定且工件较稳定的生产线,在生产环境中常见。
•可变夹具方案:通过机器视觉和感应器技术,机器人实时感知工件的位置和姿态,然后根据实际情况,调整夹具的形状和位置,完成工件的上下料。
这种方案适用于工序较为复杂或者工件形状不规则的生产线。
工作流程机器人上下料方案的工作流程通常包括以下几个步骤:1.工件识别:通过机器视觉系统,识别工作区域中的工件位置和姿态信息。
2.路径规划:根据工件的位置和姿态信息,确定机器人的最佳运动路径。
3.夹具调整:根据工件形状和尺寸,调整夹具的形状和位置,以确保工件能够安全地被机器人抓取。
4.上料/下料:机器人根据路径规划,将工件从指定位置上料到指定机器或装置上,或者将加工完成的工件从机器或装置上下料到指定位置。
5.检测和反馈:机器人上下料完成后,通过感应器和视觉系统对工件和装置进行检测,确保上下料操作的准确性和质量。
6.数据记录与管理:记录上下料操作的相关数据,比如工件的序号、产量、质量等,以便后续数据分析和生产管理。
应用场景机器人上下料方案在工业自动化生产中有广泛的应用场景,特别是在以下领域:1.汽车制造业:机器人上下料方案可以应用于汽车组装生产线中,用于上料、下料和装配操作。
2.电子工业:机器人上下料方案可以应用于电子器件的生产线中,实现自动化的物料搬运和装配。
3.医药行业:机器人上下料方案可以应用于药品和原料的生产线中,提高生产效率和产品质量。
机器人数控机床自动上下料项目

机器人数控机床自动上下料项目
随着工业的不断发展,机器人数控机床技术逐渐成为了机器加工技术的重要组成部分,在自动化生产中发挥着重要作用。
机器人数控机床自动上下料技术是利用机器人对数控机床进行自动上下料操作,实现自动化加工,在机械加工中发挥着重要作用。
机器人数控机床自动上下料技术大概可以分为三个技术步骤:机器人抓取、机器人运动控制和机器人坐标调整。
首先,机器人抓取技术是使用机器人进行工件的抓取,利用机器人的手臂及其传感器有效地抓取物体。
其次,机器人运动控制技术是指机器人根据需要,在安全可靠的条件下,并且满足实际需求的情况下,自动进行运动控制。
最后,机器人坐标调整技术是指在机器人抓取的物体加工过程中,能够准确控制机器人的移动,从而将物体放置到设定的坐标位置上。
机器人数控机床自动上下料技术可以极大提高工业生产效率,减少人工的操作,节省大量的时间。
此外,机器人数控机床自动上下料技术可以有效地保证工件的质量,因为机器人可以在没有人工干预的情况下实现自动上料下料,从而实现精准、高效、高精度的加工。
总的来说,机器人数控机床自动上下料技术对于工业生产有着重要的作用。
机器人机床上下料

机器人机床上下料新松公司自主设计研发的上下料机器人(机械手)与数控机床相结合,可以实现工件的自动抓取、上料、下料、装卡、加工等所有的工艺过程,能够极大的节约人工成本,提高生产效率。
针对机加工及冲压线提供机器人(机械手)搬运、检测整套解决方案。
针对两种类型的机床上下料,新松公司提供以下两个机床上下料的整线解决方案:根据机床的特点主要采取以下两种类型的上下料形式:1.桁架式机械手搬运该机械手采用双梁或单梁支撑形式,完成重载搬运、轻载高速搬运等不同种搬运需求。
该机械手具备与机床的联机功能,完成全线的生产数据跟踪及参数调用,实现全线自动生产。
2.机器人搬运采用6自由度(或者外加一个外部轴)的机器人完成机床的柔性上下料,采用视觉系统进行工件定位,机器人抓取工件给机床进行上下料。
桁架机械手解决方案桁架机械手采用新松公司自主开发的3-Axis:TypeDT-6系列产品,DT系列搬运机械手采用龙门架结构,采用双侧齿轮齿条传动方式,具有运动平稳承载能力强的特点。
DT 系列机械手应用领域极其广泛,例如在军事、机械制造业、航空航天业、食品药品生产行业、汽车制造业等。
DT系列龙门架式搬运机械手具有宽泛的应用范围,能够承受一定的冲击,搬运较重的负载,运动位置精度高,具有较大的结构刚性。
更换不同的模块能够满足多品种生产的要求。
DT系列龙门架式搬运机械手具有宽泛的运动范围。
能够以高速度、高精度搬运大负载覆盖大型的工作区域。
DT系列龙门架式搬运机械手具有6个系列的产品能够适应多种负载和速度的需求。
结合灵活柔性的模块化设计广泛应用于多种行业,多种产品及系列化产品的生产过程中。
机器人搬运解决方案机器人上下料机器人系统主要包括6自由度Robot、机械手爪、Vision定位系统、过渡平台定位系统、换手台和其它辅助设备。
随着人工成本的日益增加,自动上下料生产线的应用越来越广泛,基于此系统,可以针对其它产品进行相应手爪的开发,完成自动上下料生产线,在机械制造业、军事工业、航空航天业和食品药品生产等行业都可以得到广泛应用。
机器人给机床自动上下料设计

机器人给机床自动上下料设计随着工业化的不断发展,机器人在工业生产中扮演着越来越重要的角色。
机器人的自动化和智能化,使得它们在机床自动上下料方面具有巨大的优势。
下面将对机器人给机床自动上下料的设计进行详细的探讨。
首先,机器人给机床自动上下料的设计需要考虑以下几个方面:1.机器人的结构和配置。
机器人在机床自动上下料中扮演着重要的角色,因此它的结构和配置至关重要。
机器人需要有足够的力量和灵活的动作来完成上下料的任务。
同时,机器人的手臂和工具需要具备足够的精度和稳定性,以确保物料的准确放置和取出。
2.应用特定的机器人控制系统。
机器人控制系统是机器人实现自动上下料的核心部分。
它需要能够实时监测机器人的状态和位置,并准确控制机器人的动作。
同时,机器人控制系统还需要能够与机床的控制系统进行集成,以实现机器人和机床之间的协同工作。
3.安全性和可靠性设计。
机器人在机床自动上下料中需要与操作人员和其他设备进行紧密的协作。
因此,机器人的设计需要考虑到安全性和可靠性的因素。
例如,机器人需要具备可靠的碰撞检测和紧急停止功能,以避免与人员和设备发生碰撞。
同时,机器人还需要具备自动故障诊断和恢复功能,以保证其在故障情况下能够正常工作。
在机器人给机床自动上下料的设计中1.视觉识别技术。
机器人需要能够识别和定位待加工工件的位置和姿态。
视觉识别技术可以通过摄像头和图像处理算法来实现。
机器人可以通过处理图像数据,识别工件的位置和姿态,并将其与机床的坐标系进行转换,以准确放置和取出工件。
2.接触力控制技术。
机器人在上下料过程中需要以适当的力量进行接触。
接触力控制技术可以通过使用力传感器和反馈控制算法来实现。
机器人可以通过实时监测接触力,并调整自身的动作来确保与工件的接触力在合适的范围内。
3.数据通信和集成技术。
机器人需要与机床的控制系统进行数据通信和集成。
数据通信和集成技术可以通过使用标准的通信协议和接口来实现。
机器人可以与机床的控制系统进行数据交换,以实现机器人和机床之间的协同工作。
上下料机器人介绍

上下料机器人介绍
一、上下料机器人的基本概念
上下料机器人是一种被设计用来辅助操作人员完成上下料加工的机器人。
上下料机器人可以实现机械手臂的操作范围内的物体分类、定位、夹持、抓取和放置等功能,以提高加工效率、改善加工质量和确保安全生产
等良好效果。
二、功能介绍
1、定位功能:上下料机器人的机械手臂可以实现精确定位,根据操
作人员的要求把物体精确放置在指定位置上。
2、夹持功能:上下料机器人可以根据操作人员的要求抓取物体,由
机械手臂的各种夹紧装置用力把物体夹紧。
3、抓取功能:上下料机器人可以通过各种传感器精确测量物体的形
状和尺寸,从而准确抓取物体。
4、放置功能:上下料机器人的机械手臂可以实现负责放置物体的功能,在操作人员的要求下将物体放置在指定的位置上。
三、优势分析
1、提升产能:上下料机器人可以大大提高上下料加工的速度,从而
大大提高加工产能。
2、改善质量:上下料机器人可以实现精确定位、夹持、抓取和放置,从而改善加工质量。
3、确保安全:上下料机器人可以自动完成繁琐的上下料加工操作,从而确保安全生产。
4、节约能源:上下料机器人采用新型电机驱动技术,节约能源,减少能源消耗。
机器人给4台机床自动上下料解决方案

机器人给4台机床自动上下料解决方案1.解决方案概述该解决方案基于工业机器人和自动化系统,通过将工业机器人与机床连接,实现自动上下料的工作。
机器人负责将原料从储料区搬运到机床上,并将成品从机床上取出并放置到成品区,完成整个生产过程的自动化。
2.机器人选择在选择机器人时,需要考虑以下因素:-承重能力:机器人需具备足够的承重能力来搬运原料和成品。
-灵活性:机器人需要具备良好的灵活性,能够适应不同尺寸、重量和形状的原料和成品。
-高速度:机器人需要具备高速度的运动能力,以提高生产效率。
-操作简单:机器人的操作界面需要简单易用,方便工人进行操作和维护。
3.机床适配为了实现自动上下料,机床需要进行适配。
主要包括以下步骤:-安装夹具:准备适用于机器人搬运的夹具,确保机器人可以准确地搬运和放置原料和成品。
-添加传感器:在机床上添加传感器,用于检测机器人的位置和状态,确保机器人的动作符合机床的要求。
4.系统集成为了实现机器人与机床的连接和协作,需要进行系统集成。
主要包括以下步骤:-机器人控制系统:将机器人与机床的控制系统连接,确保机器人能够按照预定的路径和动作进行操作。
-通信协议:建立机器人与机床之间的通信协议,实现二者之间的数据交换和信息传递。
-安全控制:确保机器人在工作过程中的安全性,如安装机器人的安全防护设备和传感器,设定机器人的工作边界和安全区域等。
5.作业流程自动上下料的作业流程通常包括以下步骤:-原料准备:工人将原料放置在机器人的储料区,并设定机器人的工作参数和路径。
-机器人搬运:机器人按照预定路径和动作,将原料从储料区搬运到机床上,并进行加工。
-机床加工:机床进行自动加工过程,完成对原料的加工。
-成品搬运:机器人将成品从机床上取出并放置到成品区。
-作业监控:监控整个作业过程,确保机器人和机床的正常运行。
6.优势和应用-提高生产效率:机器人的高速度和连续工作能力,可以大幅提高生产效率。
-减少人力成本:机器人的自动化操作可以减少对人工的依赖,降低人力成本。
机器人磨床上下料方案

机器人磨床上下料方案简介机器人磨床上下料方案是一种自动化方案,旨在提高磨床操作的效率和精度。
通过引入机器人系统,可以实现自动化的上下料操作,减轻操作人员的劳动强度,提高生产效率。
方案原理机器人磨床上下料方案的基本原理是将机器人系统与磨床系统进行集成,实现上下料的自动化。
具体流程如下:1.机器人系统接收到上料命令后,机器人移动到料仓位置。
2.机器人使用夹具将待加工工件夹持住。
3.机器人将工件移动到磨床上,并将夹具释放。
4.磨床开始对工件进行磨削加工。
5.磨削完成后,机器人将工件重新夹持,并将其移回料仓位置。
6.机器人释放夹具,完成上料操作。
通过上述流程,机器人系统可以实现对磨床的自动上下料操作,从而提高生产效率和减少人工操作。
方案优势机器人磨床上下料方案具有以下优势:1.自动化操作:通过引入机器人系统,可以实现自动化的上下料操作,减少人工干预,提高生产效率。
2.高精度加工:机器人系统具有精准的定位能力,可以精确地将工件移动到磨床上进行加工,保证加工质量和精度。
3.灵活性:机器人系统可以根据不同工件的要求进行调整和适配,具有较高的灵活性,能够满足不同生产需求。
4.安全性:机器人磨床上下料方案减少了人工操作的机会,减少了意外事件的发生,提高了工作安全性。
方案应用机器人磨床上下料方案适用于各种磨床加工场景,例如金属加工、石材加工等。
它可以广泛应用于制造业中的机械加工过程中,提高生产效率和工件加工精度。
案例分析以某汽车零部件厂为例,他们在生产线上使用机器人磨床上下料方案,取得了较好的效果。
在引入机器人系统之前,他们的磨床上下料操作主要依赖人工完成,操作效率低下并且存在安全隐患。
经过引入机器人磨床上下料方案后,他们的生产效率得到明显提升,可以实现24小时连续加工,同时还减少了人工操作的错误率,提高了加工精度。
方案实施要实施机器人磨床上下料方案,需要以下步骤:1.设计方案:根据实际生产需求,设计机器人磨床上下料方案的系统结构和流程。
机床上下料机器人介绍

机床上下料机器人介绍机床上下料机器人主要由机械结构、控制系统、传感器和视觉系统组成。
机械结构包括机器人臂、末端执行器和夹具等部件,用于实现机床上下料的动作。
控制系统主要包括运动控制和路径规划等模块,用于控制机器人的运动轨迹和动作。
传感器主要用于检测工件和机械臂等状态,以实现精确定位和操作。
视觉系统主要用于识别和定位工件,以及监视机器人的运动和操作。
机床上下料机器人的工作流程一般包括以下几个步骤:首先,机器人通过视觉系统识别工件的类型和位置;然后,机器人根据工件的位置和尺寸,选择适当的夹具进行固定;接下来,机器人根据设定的路径规划算法,将工件从料架上取下,并精确定位到机床上;在机床上加工完成后,机器人再次将工件取下,并将加工好的工件放置到指定的位置上。
整个过程中,机器人会实时监测和调整自己的位置和动作,以确保上下料过程的准确性和稳定性。
1.提高生产效率:机床上下料机器人能够快速、准确地完成上下料操作,避免了人工操作的延时和误差,从而提高了生产效率。
2.提高产品质量:机床上下料机器人具有高度的重复性和稳定性,可以保证每个工件的位置和姿态的一致性,提高产品的加工精度和一致性。
3.降低劳动强度:机床上下料机器人的使用可以大大减少人工操作的需求,降低了劳动强度,提高了操作环境的安全性。
4.增强生产的灵活性:机床上下料机器人具有灵活的操作模式和路径规划能力,可以根据不同的工件和加工要求,进行自适应的上下料操作,提高了生产的灵活性和适应性。
5.降低成本:机床上下料机器人的使用可以减少人工和人力成本,提高生产效率和产品质量,从而降低了生产成本。
机床上下料机器人在各行业的应用非常广泛,特别是在汽车、航空、机械制造等领域。
随着工业自动化的不断发展,机床上下料机器人将在未来发挥更加重要的作用,并成为工业生产的重要组成部分。
同时,机床上下料机器人的技术也在不断进步和创新,未来将会有更多的智能和高效的机床上下料机器人问世,为工业生产带来更大的便利和效益。
- 1、下载文档前请自行甄别文档内容的完整性,平台不提供额外的编辑、内容补充、找答案等附加服务。
- 2、"仅部分预览"的文档,不可在线预览部分如存在完整性等问题,可反馈申请退款(可完整预览的文档不适用该条件!)。
- 3、如文档侵犯您的权益,请联系客服反馈,我们会尽快为您处理(人工客服工作时间:9:00-18:30)。
车削加工上下料机器人
有一家客户是刀具的生产厂家,该生产厂家目前由人工操作车削中心,随着劳动力成本的增加,客户想利用机器人自动上下料减少用工,同时需处理的毛坯和成品刀具种类繁多,客户首先要求在机器人抓手时应具有灵活性,还要求机器人具有稳定性和上下料的可靠性。
MartinLord根据客户的实际需要,采用库卡机器人KR45被选中担当此任务,它将毛坯料送到切削中心,并重新取出已完成切削和铣磨的刀具。
该六轴机器人用它的三点夹持器可以抓取直径为35至105mm的物件。
其气动操作的钳口可将长度为60到520mm、重量至30kg的毛坯件准确定位夹紧。
操作人员输入待加工部件的直径,并启动机器人和机床。
机床控制系统将工件的特征数据传送至机器人的控制系统。
之后,机器人控制系统计算出需要驶至的位置。
KR45通过一个传感器先测量出码垛叉车的高度,然后测量出上层托盘内第一个毛坯的直径及长度。
这些值将用于抓取。
第二次测量过程中,系统以更高的精度即±1mm进行工作。
为此,KR45将毛坯置于一个带有末端卡位的菱柱形斜槽上。
机器人测得毛坯件的直径和长度,并将此值和机床控制系统的预给值相比较。
若数据一致,则机器人将部件导入车床的夹紧装置。
否则将给出故障提示信号。
完成第一面的加工后,机器人翻转工件。
完成第二面加工后,则机器人将工件置于托盘上。
在切削中心工作期间,KR45为定位台提供下一个毛坯。
机器人用它背面头顶上伸出的吊装架将空的毛坯托盘码放在成品件位置处。
MartinLord选用的机器人是德国KUKAKR45工业机器人,该机器人具有45kg承载能力,在加工点处的精度可准确到0.15mm。
机器人的周边设备如下:
1、以PC为基础的库卡机器人控制系统KRC1,包括带有熟悉的视窗操作界面的控制面板
2、机器人手爪:专为本应用设计的、带有可更换夹持器对钳口的三点夹持器
3、工件物流托架
4、传感器
5、机器人行走导轨
6、控制器
7、电气柜
8、安全围栏及安全门
使用德国KUKA的KR45工业机器人,能为企业的项目带来以下成效:
1、过程可靠性
通过机器人控制系统和机床控制系统之间快速无误的通讯,以及机器人在操作和测量部件时的精度,可保证系统加工过程的可靠性。
2、改装时间短
用两对手动更换的夹持器对钳口为机器人进行快速改装,每对钳口相应覆盖毛坯件直径带宽的一半。
3、生产效率提高
由于灵活性和过程可靠性的提高,在使用相同数量的员工情况下,生产效率得到了明显提高。
生产高精度刀具时,自动化程度的高低对企业来说也是一个很重要的影响经济效益的因素。
4、精密度高
机器人在加工点处的精度可准确到0.15 mm。
能稳定可靠的将全部相关数据从机床控制系统传送到以PC为基础的库卡机器人控制系统KRC1上,这也是进行精确传送的前提条件之一。