第5章压铸模的基本结构及分型面设计
第五章 压铸模的基本结构及分型面设计
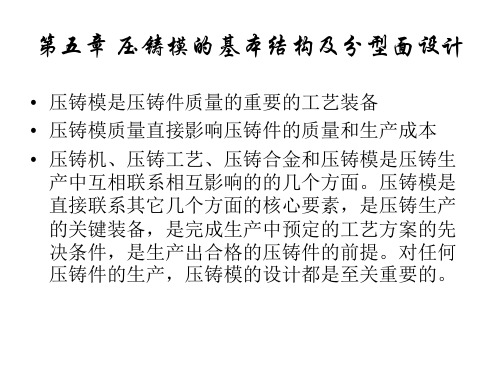
压铸模结构
3.排溢系统 主要作用是排出和储存型腔中的气体 和废料。包括排气道和溢流槽,一般直接加工在 镶块和其它零件上,也可以单独加工成形后安装 在模具上。 4.抽芯机构 用于抽出活动型芯。它要确保抽芯方 向、抽芯长度和力量满足压铸生产的要求。 5 .加热和冷却系统 用于保证模具在工作中达到工 艺要求的合适的温度。
压铸模设计内容
(结构设计)
细节设计
1)镶块尺寸的设计,对拼镶式的镶块,确定拼镶方 法,固定方法,镶块的尺寸和加工精度。 2)确定各个模具结构件的尺寸(套板、座板和支承 板)。设计中,尽量采用标准件。 3)确定型芯的数量,分割位置,尺寸和固定方法。 计算抽芯力,确定抽芯机构各部分的尺寸。
压铸模设计内容
毛坯图的内容 • 绘出与零件图相同的外形 • 注明加工余量、浇注系统和排溢系统的残 留部位 • 需加工的孔和不加工的孔的位置与尺寸 • 拔模斜度 • 总的尺寸和各部分尺寸
压铸模设计内容
(工艺设计)
毛坯图的作用 • 模具设计的根据, • 压铸件检验和清理的标准, • 下一步压铸件机械加工的工装设计的重要 依据
压铸模设计内容
(工艺设计)
对零件图进行工艺性分析 (第三章中内容) • 根据零件所选用的合金种类,分析零件的 形状、结构、精度和各项技术指标。对于 不合符压铸件生产的结构和技术要求,应 该提出修改意见,供零件设计者或生产者 修改。 • 确定机械加工部位,加工余量和加工时的 工艺措施以及定位基准等。
压铸模设计内容
(结构设计)
3)校核模具所要求的开模距离是否在压铸机 的动模安装板的行程之内。 4)校核模具的安装位置是否与压铸机相符。 5)校核压室尺寸和压室充满度。
压铸模设计内容
(结构设计)
第五章 压铸模的基本结构及分型面设计
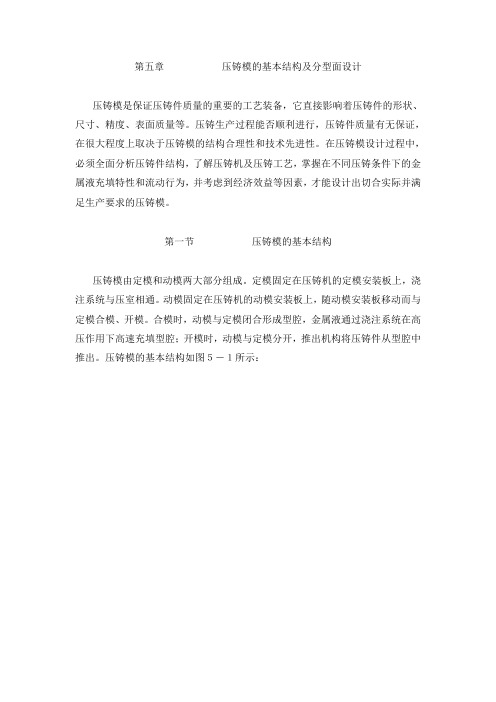
第五章压铸模的基本结构及分型面设计压铸模是保证压铸件质量的重要的工艺装备,它直接影响着压铸件的形状、尺寸、精度、表面质量等。
压铸生产过程能否顺利进行,压铸件质量有无保证,在很大程度上取决于压铸模的结构合理性和技术先进性。
在压铸模设计过程中,必须全面分析压铸件结构,了解压铸机及压铸工艺,掌握在不同压铸条件下的金属液充填特性和流动行为,并考虑到经济效益等因素,才能设计出切合实际并满足生产要求的压铸模。
第一节压铸模的基本结构压铸模由定模和动模两大部分组成。
定模固定在压铸机的定模安装板上,浇注系统与压室相通。
动模固定在压铸机的动模安装板上,随动模安装板移动而与定模合模、开模。
合模时,动模与定模闭合形成型腔,金属液通过浇注系统在高压作用下高速充填型腔;开模时,动模与定模分开,推出机构将压铸件从型腔中推出。
压铸模的基本结构如图5-1所示:图5-1压铸模的基本结构1-动模座板2-垫块3-支承板4-动模套板5-限位块6-螺杆7-弹簧8-滑块9-斜销10-楔紧块11-定模套板12-定模座板13-定模镶块14-活动型芯15-型芯16-内浇口17-横浇道18-直浇道19-浇口套20-导套21-导流块22-动模镶块23-导柱24-推板导柱25-推板导套26-推杆27-复位杆28-限位钉29-推板30-推杆固定板一、成型零件决定压铸件几何形状和尺寸精度的零件。
形成压铸件外表面的称为型腔;形成压铸件内表面的称为型芯。
如图中的定模镶块13、动模镶块22、型芯15、活动型芯14。
二、浇注系统连接压室与模具型腔,引导金属液进入型腔的通道。
由直浇道、横浇道、内浇口组成。
如图中浇口套19、导流块21组成直浇道,横浇道、内浇口开设在动、定模镶块上。
三、溢流、排气系统排除压室、浇道和型腔中的气体,储存前流冷金属液和涂料残渣的处所,包括溢流槽和排气槽,一般开设在成型零件上。
四、模架将压铸模各部分按一定规律和位置加以组合和固定,组成完整的压铸模具,并使压铸模能够安装到压铸机上进行工作的构架。
第5章 压铸模分型面设计

形式有几个研合面,给加工和研合带来了困难。
下一页
返回
5.3 分型面的选择原则
• 图5-8所示为应选择有利于成形零件加工的形式。图5-8(a)所示为蝶形 螺母。如采用Ⅰ-Ⅰ作为分型面,由于形成窄而深的型腔,用普通机 械加工很难成形,只能采用特殊的电加工方法,除了需制作电极外, 还不容易抛光。分型面设在Ⅱ-Ⅱ处,将使型腔制作变得简单,用普 通的机械加工方法即可完成。 • 图5-8(b)所示为支架类压铸件。采用Ⅰ-Ⅰ作为分型面,需设置两个相
上一页 下一页
返回
5.3 分型面的选择原则
• 5.3.4 分型面应有利于填充成形
• 为了有利于金属液的流动,在一般情况下,应将分型面设置在金属液 流的终端,如图5-13所示。图5-13(a)右图的分型面,使A处形成盲
区,容易聚集气体,出现压铸缺陷。左图的分型面设置在金属液流动
的终端,使型腔中的气体有序地排出,有利于填充成形。 • 图5-13(b)右图所示的形式虽然能起加固型腔的作用,但却堵塞了排 气通道,使气体不能有效地排出。左图采取加设有不连续的若干个斜 楔镶块,既加固了型腔,又不影响型腔的排气。
• 在图5-4(b)中,压铸件端部在型腔和型芯的夹持下很难脱出,必须在
顺序分型脱模机构的作用下,首先从Ⅰ-Ⅰ处分型,待定模型芯脱出 后,再从主分型面Ⅱ-Ⅱ处分型,使压铸件顺利脱离型腔。
上一页 下一页 返回
5.2 分型面的基本类型
• 图5-5所示的压铸件必须通过多次分型,按顺序分别脱出型芯和型腔, 才能使压铸件完全脱离模体。开模时,首先从Ⅰ-Ⅰ处分型,脱出定 模型芯,并拉断和推出浇注余料,再从Ⅱ-Ⅱ处分型,使压铸件的小 端脱出型腔。这些动作完成之后,才从主分型面Ⅲ-Ⅲ处分型,使压 铸件脱离动模型芯,推杆将含在型腔中的压铸件脱出模体。
第5章压铸模的基本结构及分型面设计介绍
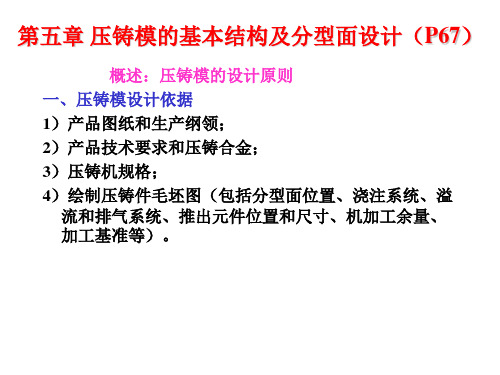
§2. 分型面设计
二、 分型面的选择 同一个压铸件,分型面选择得不同,就可以设计出 不同结构的压铸模,得到不同质量的压铸件。 如下图所示的压铸件可以作出几个不同的分型面,现就 以下四种分型加以说明 : 1、第一种分型 分型面在对称面上,型腔 处于动模和定模之间。压 铸件圆柱部分难以保证不 错位,另外还必须设置抽 芯机构,使得压铸模结构 比较复杂。
①支承与固定零件; ②导向零件; ③推出机构。 (5)抽芯机构 (6)加热与冷却系统。 其他零件,如螺栓、销钉等。
• 大型压铸模具
• 成形部分(零件)
• 模架
• 抽芯机构
• 推出机构
§2. 分型面设计
• 分型面-----压铸模的动模与定模的接触表面。 一、分型面的类型 按其形状,一般分为:平直分型面;倾斜分型面;阶梯 分型面;曲面分型面。 如下图:
本 章 完
人有了知识,就会具备各种分析能力, 明辨是非的能力。 所以我们要勤恳读书,广泛阅读, 古人说“书中自有黄金屋。 ”通过阅读科技书籍,我们能丰富知识, 培养逻辑思维能力; 通过阅读文学作品,我们能提高文学鉴赏水平, 培养文学情趣; 通过阅读报刊,我们能增长见识,扩大自己的知识面。 有许多书籍还能培养我们的道德情操, 给我们巨大的精神力量, 鼓舞我们前进。
7)确定动模、定模、镶块和和定模套板的外形 尺寸,以及导柱、导套的位置和尺寸。 8)确定核算推出行程、复位、预复位机构和尺 寸。 9)确定嵌块的装夹、固定方法和尺寸。 10)计算模具的总厚度,核对压铸机的最大和最 小开模距离。 11)按模具的外形轮廓尺寸,核对压铸机拉杠间 距。 12)按模具动模和定模板尺寸,核对压铸机安装 槽和孔的位置。 13)根据选用的压射比压,复核压铸机的锁模力。
(6)考虑压铸合金的性能。
9基本结构与分型面-26
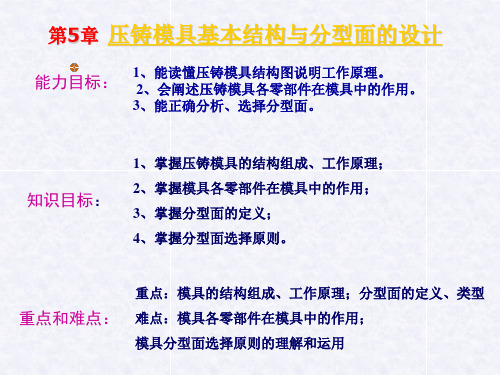
1.压铸模具的基本结构
图5-1 压铸模的基本结构形式
上一页 下一页 返回
(1)成型部分
定模与动模合拢后,构成一个压 铸件形状的空腔,称为型腔。构 成型腔的零件即为成型零件。成 型零件包括固定的和活动的镶块 与型芯。如图5-1中的件13——定 模镶块、22——动模镶块。有时 成型零件还构成浇注系统和排溢 系统的一部分,如局部的横浇道、 内浇口、溢流槽和排气槽等。
(3)全立式冷压室压铸机用压铸模 全立式冷压室压铸机用压铸模的 基本结构如图 4-13 所示。该模具 为冲头上压式压铸模,浇口套14 (即压室)设置在下模。压铸 机 工作台带动动模(上模)部分向 上移动,模具分型面打开,定量 的金属液注人浇口套中后,动模 部分向下移动合模,复位杆 使推 出机构(图 4-13 中复位杆未画出) 与压铸机下液压虹连接的压射冲 头12向上移动,金属充填模具型 腔,压铸结束;上工作 台向上移 动,压铸件包在动模型芯上一起 随动模向上移动,压铸机上的固 定顶杆(图 4-13 中未画出)与压 铸模推板2接触,带 动推杆20将 压铸件推出模外。 图4-13 全立式冷压室压铸机用压铸模
重点和难点: 难点:模具各零部件在模具中的作用;
模具分型面选择原则的理解和运用
压铸件压铸成型后,压铸件、浇注系统凝料及 余料等要从模具内取出,且要对模具进行杂物 清理,为下一次压铸作准备。因此必须将模具 分割成可以分离的两部分或几部分,这些可以 分离部分的相互接触的表面称为分型面。 通常在模具设计之前确定模具分型面,分型面 是决定模具结构的重要因素。
上一页 下一页 返回
⑤压铸件基准面尽量避免与分型面重合。此外,分型
ቤተ መጻሕፍቲ ባይዱ
面除了尽量避免与基准面重合外,也尽量不穿过压
压铸模的结构组成

•压铸成形工艺与模具设计(第2版)——第5章
•7
5.1 压铸模的基本结构
4)模 架
支承与固定零件:包括各 种套板、座扳、支承板和垫块 等构架零件,其作用是将模具 各部分按一定的规律和位置加 以组合和固定,并使模具能够 安装到压铸机上。
导向零件:引导动模和定 模合模或开模。
推出与复位机构:将压铸 件从压铸模上脱出的机构,包 括推出、复位零件,以及机构 自身的导向和定位零件。
5.2.2 分型面的选择 1. 分型面选择的基本原则 3)分型面选择应保证压铸件的尺寸精度和表面质量
(a)
(b)
分型面对压铸件尺寸精度的影响
(a)
(b)
分型面对压铸件外观质量的影响
•压铸成形工艺与模具设计(第2版)——第5章
•25
5.2 分型面设计
5.2.2 分型面的选择 1. 分型面选择的基本原则 3)分型面选择应保证压铸件的尺寸精度和表面质量
1-复位杆;2、3、31-推杆; 4-推板;5-推杆固定板; 6-推板导柱;7-推板导套; 8-动模座板;9-垫块; 10、24-圆柱销;11-支承板; 12-动模套板;13-限位块; 14、30、32、33-内六角螺钉; 15-弹簧;16-螺杆; 17-型芯滑块;18-定模套板; 19-定模座板;20-楔紧块; 21-斜销;22-动模镶块; 23-定模镶块; 25-型芯; 26-浇口套;27-浇道镶块; 28-导柱;29-导套
•压铸成形工艺与模具设计(第2版)——第5章
•5
5.1 压铸模的基本结构
5.1.1 压铸模具的基本组成部分
定模 定模与压铸机压射
机构连接,并固定在定 模安装板上,浇注系统 与压室相通。
动模 动模则安装在压铸
常见的压铸模具结构及设计

常见的压铸模具结构及设计压铸模具是利用压力将熔融金属注入模具腔中,通过冷却固化后得到所需形状的金属制品。
它由模具座、模具芯、模具板等组成,其结构设计直接影响到压铸产品的质量和生产效率,因此压铸模具的结构设计是相当关键的。
1.单向模具结构:即模具腔和模具芯的投入方向相同,熔融金属由一边流入模具腔,另一边流出。
这种结构适用于形状简单的压铸产品,生产效率较高。
但由于金属在流动过程中存在进气孔和气泡的产生,容易影响产品质量。
2.双向模具结构:即模具腔和模具芯的投入方向相反,熔融金属同时从两个方向流入模具腔,避免了进气孔和气泡的产生,使产品质量更加稳定。
但此种结构制造难度较大,因此适用于形状复杂的产品。
3.多向模具结构:即模具腔和模具芯的投入方向可以有多个选择,根据具体产品的形状和要求来设计。
这种结构适用于有多个几何孔形和复杂造型的产品。
4.滑动式模具结构:适用于有突出部分或凹陷部分的产品,模具芯和模具腔可以相对滑动,来实现产品形状的复杂性。
滑动式模具结构使得产品成型更加容易,同时也增加了模具制造的难度。
5.注射式模具结构:适用于较大规模的压铸产品生产,通过在模具腔中注入压力来驱动熔融金属充满整个模具腔,从而制造大型、复杂的产品。
在压铸模具的设计中,需要考虑以下几个方面:1.模具材料的选择:通常采用高速钢、合金钢或特殊合金作为模具材料,以保证模具的耐磨性和耐蚀性。
2.模具结构的合理性:要满足产品的形状和要求,保证产品质量和生产效率。
通过模具芯、模具腔和模具座的设计,确定模具的结构。
3.模具冷却系统的设计:合理的冷却系统设计可以缩短模具的冷却时间,提高生产效率。
同时可以有效控制模具温度,避免模具受热膨胀。
4.维修和更换模具的方便性:设计模具时要考虑到日常维修和更换部件的便利性,提高模具的使用寿命。
总结起来,压铸模具的结构设计需要根据产品形状和要求来确定,考虑到产品质量和生产效率。
同时还要合理选择模具材料,设计冷却系统,并考虑维修和更换模具的方便性。
压铸模什么样压铸模的基本结构
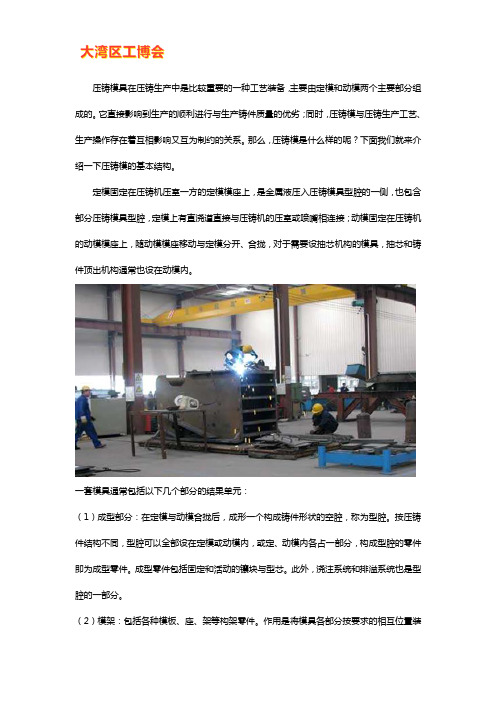
压铸模具在压铸生产中是比较重要的一种工艺装备,主要由定模和动模两个主要部分组成的。
它直接影响到生产的顺利进行与生产铸件质量的优劣;同时,压铸模与压铸生产工艺、生产操作存在着互相影响又互为制约的关系。
那么,压铸模是什么样的呢?下面我们就来介绍一下压铸模的基本结构。
定模固定在压铸机压室一方的定模模座上,是金属液压入压铸模具型腔的一侧,也包含部分压铸模具型腔,定模上有直浇道直接与压铸机的压室或喷嘴相连接;动模固定在压铸机的动模模座上,随动模模座移动与定模分开、合拢,对于需要设抽芯机构的模具,抽芯和铸件顶出机构通常也设在动模内。
一套模具通常包括以下几个部分的结果单元:(1)成型部分:在定模与动模合拢后,成形一个构成铸件形状的空腔,称为型腔。
按压铸件结构不同,型腔可以全部设在定模或动模内,或定、动模内各占一部分,构成型腔的零件即为成型零件。
成型零件包括固定和活动的镶块与型芯。
此外,浇注系统和排溢系统也是型腔的一部分。
(2)模架:包括各种模板、座、架等构架零件。
作用是将模具各部分按要求的相互位置装配和固定,并能使模具安装到压铸机上。
(3)导向零件:导向零件的作用是引导动模和定模合拢或分离,并保证分合模的精度要求。
(4)推出机构:这是将铸件从模具中推出的机构,包括顶出和复位零件,还包括机构自身的导向和定位零件。
(5)浇注系统:它是型腔与压室或喷嘴相连的通道,引导金属液按规定的方向进入模具的型腔,且直接影响金属液进入成型部分的速度和压力,由直浇道,横浇道和内浇道组成。
(6)排溢系统:排溢系统是指排气槽和溢流槽系统。
排气槽是排除压室、浇道和型腔中气体的通道;而溢流槽是储存冷金属盒涂料余烬的小空腔,溢流槽还具有调节模具温度的作用,有时在难以排气的深腔部位设置通气塞,借以改善该处的排气条件。
(7)抽芯机构:对某些铸件,当型芯抽出方向与开合模方向不一致时,还需要在模具上设抽芯机构,以便将铸件从模具中取出。
抽芯机构也是压铸模具中十分重要的结构单元,其形式是多种多样的。
- 1、下载文档前请自行甄别文档内容的完整性,平台不提供额外的编辑、内容补充、找答案等附加服务。
- 2、"仅部分预览"的文档,不可在线预览部分如存在完整性等问题,可反馈申请退款(可完整预览的文档不适用该条件!)。
- 3、如文档侵犯您的权益,请联系客服反馈,我们会尽快为您处理(人工客服工作时间:9:00-18:30)。
a.选择分型面和确定型腔的数量;
b.选择内浇口位置,确定浇注系统、溢流槽和排气槽的 布置方案;
c.确定抽芯数量,选用合理的抽芯方案;
d.确定推出元件的位置,选择合理的推出方案; e.确定动模与定模外形尺寸,以及导柱导套的位置与尺
寸; f.对带嵌件的铸件要考虑嵌件的装夹和固定; g.计算模具的热平衡温度以确定冷却与加热管道的位置
如下图所示,压铸件适合于设置环形或半环形浇口 的浇注系统,Ⅰ-Ⅰ分型面比Ⅱ-Ⅱ分型面更能满 足压铸件的压铸工艺要求。
如图所示,分型面应使压铸模型腔具有良好的溢流排
气条件,使先进入型腔的前流冷金属液和型腔内的气 体进入排溢系统排出。Ⅰ-Ⅰ分型面比Ⅱ-Ⅱ分型面 有利于溢流槽和排气槽的设置。
2、分型面选择的基本原则
先从Ⅰ-Ⅰ处分型,待定 模型芯脱出后,再从主 分型面Ⅱ-Ⅱ处型,使压 铸件顺利脱离型腔。
②三分型面 由一个主分型面和两个辅助分型面构成。 如下图c。
Ⅰ-Ⅰ处分型,脱出定模型 芯,并拉断和推出浇注余料
再从Ⅱ-Ⅱ处分型,使压铸 件的小端脱出型腔。
最后从主分型面Ⅲ-Ⅲ处分 型,使压铸件脱离动模型芯, 推杆把包在型腔中的压铸件 脱出模体。
四、压铸模总体设计的主要内容
1)按初步分析方案,布置分型面、型腔位置及 浇注系统,并相应考虑溢流槽和排气槽的布置 方案。
2)确定型芯的分割位置、尺寸和固定方法。 3)确定成型部分结构及固定方式。 4)确定推出元件的位置和尺寸。 5)计算抽芯力,确定抽芯机构结构和尺寸。 6)计算模型的热平衡,确定冷却和加热通道的
二、压铸模设计前的准备工作
1)根据产品图,对所选用的压铸合金、压铸件的形状、 结构、精度、和技术要求进行工艺性分析;确定机械 加工部位、加工余量和机械加工时所要采取的工艺措 施以及定位基准。
2)根据产品图和生产纲领确定压铸比压;计算锁型力; 估算压铸件所需要的开模力和推出力以及所需开模距 离;初步选定压铸机的型号和规格。
• 可见,分型面的选择对压铸模结构和压铸件尺 寸精度具有决定性的影响。
• 分型面的选择对压铸模结构和压铸件质量的影 响是多方面的,必须根据具体情况合理选择。
2、分型面选择的基本原则
(1)尽可能地使压铸件在开模后留在动模部分。
由于压铸机动模部分设有顶出装置,因此,必须保证压铸 件在开模时随着动模移动而脱出定模。设计时应考虑压铸 件对动模型芯的包紧力大于对定模型芯的包紧力。
• 例如,下图,利用压铸件对型芯A的包紧力略大于对 型芯B的包紧力,中间型芯及四角小型芯与型芯A设 在一起。压铸件可有Ⅰ-Ⅰ和Ⅱ-Ⅱ两个分型面供选 择,考虑到压铸机和生产操作等因素有可能增加定模 脱模阻力,采用Ⅱ-Ⅱ分型面较能保证开模时压铸件 随动模移动而脱出定模。
2、分型面选择的基本原则
(2) 有利于浇注系统、溢流排气系统的布置。
位置和尺寸。
7)确定动模、定模、镶块和和定模套板的外形 尺寸,以及导柱、导套的位置和尺寸。
8)确定核算推出行程、复位、预复位机构和尺 寸。
9)确定嵌块的装夹、固定方法和尺寸。
10)计算模具的总厚度,核对压铸机的最大和最 小开模距离。
11)按模具的外形轮廓尺寸,核对压铸机拉杠间 距。
12)按模具动模和定模板尺寸,核对压铸机安装 槽和孔的位置。
• 若压铸件外表面不允许有分型面痕迹,则应选Ⅰ-Ⅰ 作为分型面。
(4)成方案,尽量简化模具 结构、便于成型零件和模具的加工。
如图所示,压铸件若 选择Ⅰ-Ⅰ分型面,则 需要设置两个侧向插芯 机构;而选择Ⅱ-Ⅱ分 型面,就不必设置侧向 插芯机构,模具结构简 单。
入型腔的通道(由直浇道、横浇道、内浇道组成)。 (3)溢流、排气系统-----排除压室、浇道和型腔中的气
体,储存前流冷金属液和涂料残渣的处所。一般开设 在成型零件上。 (4)模架----将压铸模各部分按一定规律和位置加以组 合和固定,组成完整的压铸模具,并使之能安装到压 铸机上进行工作的构架。 它通常可分为三个部分:
和尺寸,控制和调节压铸过程的热平衡。
4)绘制压铸工艺图: 绘出铸件图形;标注机械加工余量,加工基准,脱模斜 度及其它工艺方案;定出铸件的各项技术指标。
三、设计压铸模的基本要求
• 设计模具从使用性能、工艺性能和经济性方面考虑。基本 要求如下:
1)能获得符合图样要求的压铸件; 2)能适应压铸生产的工艺要求,并在保证铸件质量和安全生
①支承与固定零件; ②导向零件; ③推出机构。 (5)抽芯机构 (6)加热与冷却系统。 其他零件,如螺栓、销钉等。
• 大型压铸模具
• 成形部分(零件)
• 模架
• 抽芯机构
• 推出机构
§2. 分型面设计
• 分型面-----压铸模的动模与定模的接触表面。
一、分型面的类型 按其形状,一般分为:平直分型面;倾斜分型面;阶梯 分型面;曲面分型面。 如下图:
分型面如图所示,型腔处于定模内。压铸件尺寸d1 与d2能达到同轴,但尺寸d在动模型芯上形成,与 d1 、d2不易保证同轴;尺寸h和H基准都在分型 面上,精度较高。
• 4、第四种分型
分型面如图所示,型腔、型芯都处在动模内。压铸 件尺寸d、d1与d2 都能达到同轴;尺寸h和H 基准都在分型面上,精度较高。但压铸件脱模较为 复杂。
第五章 压铸模的基本结构及分型面设计(P67)
概述:压铸模的设计原则 一、压铸模设计依据 1)产品图纸和生产纲领; 2)产品技术要求和压铸合金; 3)压铸机规格; 4)绘制压铸件毛坯图(包括分型面位置、浇注系统、溢
流和排气系统、推出元件位置和尺寸、机加工余量、 加工基准等)。
分型面位置、浇注系统等未标示出。
• 如图所示,若选择Ⅰ-Ⅰ分型面,压铸模的型腔较深, 机械加工较为复杂;而选择Ⅱ-Ⅱ分型面,型腔的机 械加工就比较方便。
2、分型面选择的基本原则
(5)避免压铸机承受临界载荷。
压铸件的两个面积A>B,若面积A接近压铸机所允许 的最大投影面积时,应选择Ⅰ-Ⅰ作为分型面。如图 所示:
2、分型面选择的基本原则
压铸模通常只有一个分型面,称为“单分型面”。 有时为满足工艺要求,需增加一个或两辅助分型面,称 为“多分型面”。
①双分型面 由一个主分型面和一个辅助分型面构成。 如下图a。
先从Ⅰ-Ⅰ处分型,拉 断并推出直浇道余料后, 才再从Ⅱ-Ⅱ处分型。
Ⅱ-Ⅱ为主分型面, Ⅰ-Ⅰ为辅助分型面。
①双分型面 如下图b。
1、第一种分型 分型面在对称面上,型腔 处于动模和定模之间。压 铸件圆柱部分难以保证不 错位,另外还必须设置抽 芯机构,使得压铸模结构 比较复杂。
• 2、第二种分型
分型面如图所示,型腔处于动模和定模之间。压铸件 尺寸d与d2能达到同轴,但它们与d1不易保证同轴; 尺寸H精度偏低。
• 3、第三种分型
(3)保证压铸件的尺寸精度和表面质量。
分型面应避免与压铸件基准面相重合,尺寸精度要求 高的部位和同轴度要求高的外形或内孔,应尽可能设置 在同一半模(动模或定模)内。
• 如图所示,A为压铸件基准面,应选Ⅰ-Ⅰ作为分型 面,这样即使分型面上有毛刺、飞边,也不会影响基 准面的精度。
• 如下图所示,若压铸件外表面不允许留脱模斜度,为 减少机加工量应选Ⅱ-Ⅱ作为分型面;
(6)考虑压铸合金的性能。
压铸合金的性能影响压铸工艺性。同一几何尺寸的 压铸件,压铸合金不同,分型面位置也不同。
如图所示,细长管状压铸件,Ⅰ-Ⅰ分型面适用于 锌合金;Ⅱ-Ⅱ分型面则适用于铝合金或铜合金。
2、分型面选择的基本原则
(7)嵌件和活动型芯应便于安装。
图(a):压铸件两端设有嵌 件。为了安装方便,将分 型面设在嵌件的轴心处。
合模前,将嵌件装在 分型面上,定位后合模。 开模时,嵌件随压铸件推 出。
本章 完
13)根据选用的压射比压,复核压铸机的锁模力。
§1. 压铸模的基本结构
压铸模由定模和动模两大部分组成。
(1)成型零件(部分)-----决定压铸件几何形状和尺寸
精度的零件。型芯----形成压铸件内表面的零件;型腔
----形成压铸件外表面的零件。 (2)浇注系统-----连接压室与模具型腔,引导金属液进
• 注塑三板模
• 注塑三板模动作动画
③组合分型面 由一个主分型面和一个或数个不同方向的 分型面构成。
§2. 分型面设计
二、 分型面的选择 同一个压铸件,分型面选择得不同,就可以设计出
不同结构的压铸模,得到不同质量的压铸件。
如下图所示的压铸件可以作出几个不同的分型面,现就 以下四种分型加以说明 :
产的前提下,尽量采用合理、先进简单的模型结构,减小 操作程序,使动作准确可靠; 3)模具构件的刚性良好,模具零件间的配合精度选用合理, 易损件拆换方便,便于维修; 4)模具上各种零件应满足各自的机械加工工艺和热处理工艺 的要求,根据零件的使用条件合理选择模具材料,以保证 模具寿命; 5)掌握压铸机的技术规范,充分发挥压铸机的生产能力,准 确选定安装尺寸; 6)在满足压铸生产要求和模具加工工艺要求的前提下,尽可 能降低压铸模的成本; 7)在条件许可下,压铸模应尽可能实现标准化、通用化,以 缩短设计和制造周期,方便管理。