水泥粉磨优化控制系统
水泥厂DCS集散控制系统

水泥厂DCS集散控制系统我公司集多年来自动化系统项目实施经验开发的水泥厂Weith-DCS01集散控制系统采用施耐德、ABB、西门子等公司功能先进的PLC作为核心控制器,上位机采用功能丰富的Vijeo Citect、Wincc、PPA等人机界面软件,Weith-DCS01型集散控制系统系统按照“分散控制、分散操作、集中调度管理”的要求进行设计,系统具有全自动逻辑控制、在线工艺状态显示及参数记录、运行故障诊断记录、生产报表显示记录等功能。
水泥生产的工艺过程,可以简要地概括为“三磨一烧”,即首先将原料粉磨成生料,然后经过煅烧形成熟料,再将熟料粉磨成水泥。
从砂岩库、石灰石库、钢渣库、粉煤灰库经过定比配料系统混合成原料粉,传送系统将原料粉传送进生料磨机进行生料制备,制备好的生料进均化库。
均化库里的生料通过定量给料机将生料送进预热器预热后进回转窑系统煅烧成熟料。
煅烧后的熟料经过冷却破碎后即可以送入成品站的成品磨机磨成成品水泥。
水泥生产工艺设备单机容量大,生产连续性强、对快速性和协调性要求高。
为了提高企业生产效率和竞争力,自动控制的实施至关重要。
我公司研制开发的Weith-DCS集散控制系统能够很好的满足水泥行业以开关量为主,模拟量为辅且伴有少量回路调节的控制要求。
原料破碎及储存系统入料刮板输送机采用变频调速调节破碎机的喂料量,喂料量的自动控制,以破碎机功率的变化来自动调节板喂机的速度,使其速度保持在满足要求的范围内运行,不至于由于板喂机的速度过高使石灰石料仓的料卸空,来料直接落在板喂机上,对设备起到一定的保护作用。
原料输送采用“逆流程启动,顺流程停车”原则对设备进行控制。
图1 原料破碎及储存系统流程原料配料系统生料质量控制(QCS)系统由在线钙铁荧光分析仪、计算机、调速电子皮带秤等组成。
智能在线钙铁荧光分析仪可进行自动取样、制样,并进行连续测定,由QCS系统进行配料计算,并通过DCS对电子调速皮带秤下料量进行比例调节和成分控制,使生料三率值保持在目标值附近波动。
水泥粉磨系统辊压机操作控制的几点经验

平 均 采 购价 格 37 4 / 算 ,购 买 助磨 剂 费 用 为 4 冗 t 计 197 万元 。抵 消液 体 助磨 剂成 本及 研 发成 本 等费 4. 6 用 后 ,全年 可增 加直接 经 济效益 5.4 02万元 。
观察 ,发 现边 料溜 子物 料多 且下不 及 ,物料堆 积 到
分料 阀转 轴 附近 ,从分 料 阀的转 轴下部 串人成 品溜
子。
动辊 固定辊
/ /
动 、定 辊
图 1 动 辊 侧 挡 料 调 节 板 的 原 位 置
动辊侧 挡料 调节 板
/ \ ) / /
l\/
辊 缝 的 限制 ,液压 缸 内 的液压 油 的体 积 是一 定 的 , 辊 缝 增大 ,液压缸 被 压缩 ,油 压也 达不 到 作压 力 丁 一
82 M Pa。 .
量提高了1. 31 %,系统粉磨电耗降低 了1. 6 %。 6
( 收稿 日期 :2 1— 10 ) 020— 8
由于初 始辊缝 决定 液压缸 的体积 ,初始 辊缝 确定为1 r  ̄ 0mn ,液压缸体积不变 ,工作辊缝一般 N 为2 m~ 8m 6m 2 m,变化不大。因此我们认为初 始
经 过辊 压 机 动 、定 辊 碾 压 的物 料 形 成 料饼 , 在 两 辊 间 的下 部 出来 ,由于 两 辊 间 进 料 充 分 ,物 料被 碾压 的效 果好 ,边 部 的物料碾 压效 果不及 中部
物料 , 分料阀的作用是将碾压效果好与不好的物料
进 行 分离 ( 3)。由于 一 直认 为 分料 阀开度 越 小 图 越 好 ,故一 度将 分料 阀开度 调整 到2 %,结果 成 品 0 中一直 含有 1 左 右 的粗 物料 。打 开辊 压机 侧 门 0mm
水泥厂控制课程设计
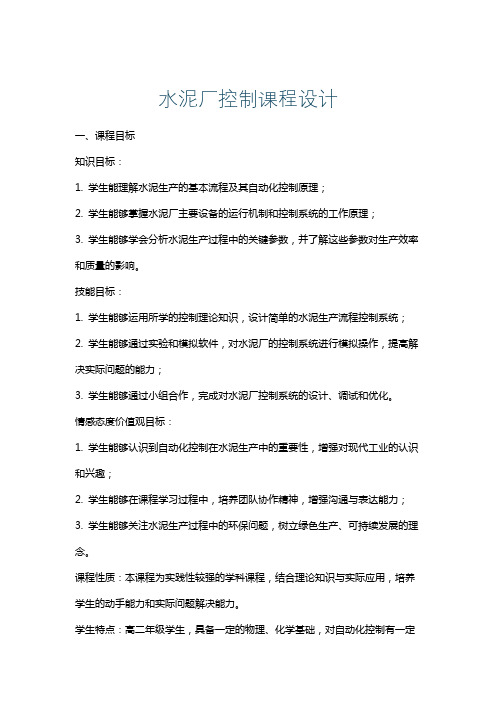
水泥厂控制课程设计一、课程目标知识目标:1. 学生能理解水泥生产的基本流程及其自动化控制原理;2. 学生能够掌握水泥厂主要设备的运行机制和控制系统的工作原理;3. 学生能够学会分析水泥生产过程中的关键参数,并了解这些参数对生产效率和质量的影响。
技能目标:1. 学生能够运用所学的控制理论知识,设计简单的水泥生产流程控制系统;2. 学生能够通过实验和模拟软件,对水泥厂的控制系统进行模拟操作,提高解决实际问题的能力;3. 学生能够通过小组合作,完成对水泥厂控制系统的设计、调试和优化。
情感态度价值观目标:1. 学生能够认识到自动化控制在水泥生产中的重要性,增强对现代工业的认识和兴趣;2. 学生能够在课程学习过程中,培养团队协作精神,增强沟通与表达能力;3. 学生能够关注水泥生产过程中的环保问题,树立绿色生产、可持续发展的理念。
课程性质:本课程为实践性较强的学科课程,结合理论知识与实际应用,培养学生的动手能力和实际问题解决能力。
学生特点:高二年级学生,具备一定的物理、化学基础,对自动化控制有一定的了解,但实际操作经验较少。
教学要求:教师需结合课本知识,注重理论与实践相结合,引导学生运用所学知识解决实际问题。
在教学过程中,关注学生的个体差异,鼓励学生主动参与,提高学生的实践操作能力和团队协作能力。
通过课程目标的分解和实施,确保学生能够达到预期的学习成果。
二、教学内容1. 理论知识:(1)水泥生产流程:熟料制备、水泥磨粉、成品包装等;(2)自动化控制原理:反馈控制、PID控制、DCS系统等;(3)水泥厂主要设备:生料磨、回转窑、水泥磨等及其控制系统;(4)关键参数分析:温度、压力、湿度等对水泥生产的影响。
2. 实践操作:(1)使用模拟软件进行水泥生产流程的模拟操作;(2)设计并实现简单的水泥生产控制系统;(3)对水泥厂控制系统的调试、优化和故障排查。
3. 教学大纲:第一周:水泥生产流程及自动化控制原理介绍;第二周:水泥厂主要设备及其控制系统讲解;第三周:关键参数分析及控制策略;第四周:实践操作(模拟软件操作、控制系统设计);第五周:课程总结与展示。
水泥粉磨过程质量控制方法
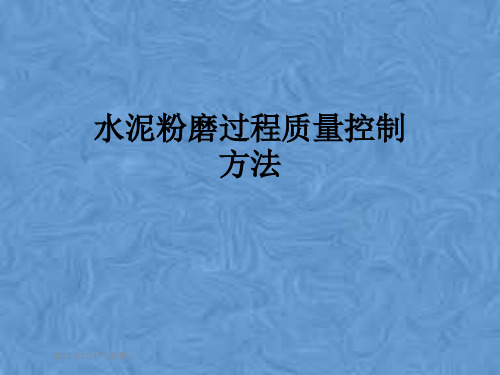
表2 不同粒径水泥颗粒完全水化时间
颗粒粒径/μm 1
3
5
7
10
20
完全水化时间/d 0.0039 0.316 2.44 9.38 39.1 625
颗粒粒径/μm 30 完全水化时间/a 8.7
40
45
50
60
80
27.4 43.9 66.9 138.7 438.4
1 水泥粒度分布的要求
水泥强度的本质 假如不考虑客观条件的限制,在水泥石
1 水泥粒度分布的要求 1.3 熟料、水泥的最佳粒度分布
1.3.1 熟料的水化速率 一定时间熟料水化深度与水化时间的关系可用下式表示:
X 2t 0.25
式中:X——水化深度,μm; t——水化时间,d。
假定水泥颗粒为球形,按上式计算的不同粒径水泥颗 粒完全水化的时间见表2。
1 水泥粒度分布的要求
2 水泥粒度分布与性能的关系
4.5
凝结时间/h
4.0 初凝时间 终凝时间
3.5
3.0
2.5
2.0 0.9
1
1.1
1.2
1.3
均匀性系数
图8 凝结时间与均匀性系数的关系
2 水泥粒度分布与性能的关系
1. 均匀性系数提高0.1,3d、7d、28d抗压强度分别提高 1.6MPa、3.6MPa、4.7MPa。
混合材料与熟料混 合后水泥符合 Fuller曲线
水泥粉体颗粒堆 积密度的要求
1 水泥粒度分布的要求
1.2 最佳粒度分布的实现
前述粒度分布要求只能采用分别粉磨方式实现! 混合粉磨必须在水化速率/程度、堆积密度之间取 舍,不存在最佳粒度分布。
1 水泥粒度分布的要求
1.3 混合粉磨的最佳粒度分布——伪命题
【探究】辊压机联合粉磨系统的操作控制

【探究】辊压机联合粉磨系统的操作控制天津振兴水泥有限公司二线水泥粉磨系统采用TRP1400×1400辊压机联合粉磨系统。
该系统于2004年5月建成,几年的生产实践证明该系统年运转率可达80%以上,月最高运转率达96%以上。
本文仅就该系统的生产经验进行介绍。
1工艺流程物料经皮带秤由混料皮带输送至喂料斗提,经1.4 m皮带进入稳料承重仓内,物料从小仓底部卸出以料柱形式进入辊压机,被辊压过的料饼经喂料斗提进入V型选粉机打散分选,经循环风机风选后(实际生产过程中根据磨机能力通过循环风机阀门来控制入磨物料量)的细颗粒被六筒旋风收尘器收集,粗料落入称重仓重新喂入辊压机循环辊压,使物料得到挤压破碎再与新物料一起入斗式提升机进入V型选粉机分选,细颗粒入磨,粗颗粒再次被挤压破碎,周而复始;出V型选粉机的细颗粒被六筒旋风收尘器收集,通过下料溜子入磨粉磨,物料通过出磨斗提进入O-sepa选粉机分选,成品经布袋收尘器收集入库,粗颗粒经回粉皮带入磨继续粉磨。
表1是该系统设备的相关参数。
2参数控制与运行调整2.1 物料粒度的控制辊压机对物料的粒度要求比较严格,粒度过大或过小都会影响系统的正常运转。
如果物料细粉较多,则物料通过辊压机速度就快,形不成足够的料饼,物料受到的压力小,导致辊压后的物料成品率低,影响台产;物料粒度过大时容易造成辊压机产生振动或跳停,因此在正常生产过程中要注意保持熟料仓的料位,避免因物料离析形成的物料颗粒变化对生产产生影响。
2.2 研磨体级配的调整由于物料经辊压破碎后,入磨物料的粒度(比表面积)已经达到160~200 m2/kg,达到了不带辊压机的闭路粉磨系统的粉磨能力,因此磨内研磨体级配要进行合理优化。
最初按设计给定的级配进行生产,出磨水泥细度在0.1%~0.2%之间(0.08 mm方孔筛),现场取样做循环负荷测定,过粉磨现象严重。
2008年利用大修机会对级配重新进行调整(表2),调整后出磨水泥细度在0.7%~1.0%之间,磨机产量明显提高。
辊压机设备及系统的优化升级改造在水泥磨中的应用

E:系统电 耗自配料库底计 量秤开始至 水泥成品 入库止 .
图 4 专 业 人 员 现 场 测 绘
用 ,但与之 配 套的原有 2台 3.2m×13m开流 球磨 机简体 部 分存 有裂缝 不易修 复,存 在安 全隐患 ,故予以淘汰,改 用 已经停 运 的原2号 系统 西3.8m×13m球 磨 机与2台辊压 机组 成 “二拖 一”的联合 粉磨 系统 ,这 样既能节约改造投 资 ,又 能最 大 限 度 的利 用 现有 资 产,达 到 系统 的稳 定运 行,降低运行成本 的 目的。设 备改造 和系统 优化的措 施包 括 以下内容。
⑩
收尘 器
96—6
尘 器 n
一
.
风
一
⑩
一v选 (vx6817)
=称重仓 一
击3.2m×13m
水泥 磨
去水 泥储存 系统
来自配 料系统
辊压机 (CLF150-90)
图3 拆 卸 后 的CLF1 50—90辊压 机 机架
图 1 原 粉 磨 系统 工艺 流程 图
水泥粉磨过程质量控制方法
水泥粉磨过程质量控制方法一、原材料控制1、石灰石控制:石灰石作为水泥生产的主要原料之一,其品质直接决定了熟料的质量。
在水泥粉磨过程中,应对石灰石进行严格的化学成分和物理性能检测,确保其质量稳定。
2、煤粉控制:煤粉是水泥粉磨过程中的重要燃料,直接影响水泥熟料的烧结过程和燃烧效果。
应对煤粉进行颗粒大小、挥发分和灰分等指标的检测,确保其质量稳定。
3、矿渣粉控制:矿渣粉作为水泥生产的主要辅料之一,对水泥产品的强度发展和后期硬化过程有着重要影响。
应对矿渣粉进行细度、水化活性指标和化学成分等指标的检测,确保其质量稳定。
二、操作控制1、料层厚度控制:水泥粉磨过程中,适当调节磨辊与磨盘之间的料层厚度,可保证研磨效果的均匀性和稳定性。
应根据生产经验,结合设备的磨矿压力和转速等参数,控制料层良好的分布状态。
2、进出料温度控制:水泥粉磨过程中,进料的温度直接影响磨矿系统的温度分布和研磨效果。
应通过合理的冷却措施,控制进料温度在适宜的范围内,避免热损失和磨矿系统过热。
3、磨矿系统压力控制:水泥粉磨过程中,磨矿系统的压力直接影响研磨效果和能耗。
应根据水泥原料的特性和生产工艺要求,合理调节磨矿系统的压力,保持研磨过程的稳定性。
4、出料粒度控制:水泥粉磨过程中,出料粒度是衡量水泥产品质量的重要参数之一、应根据产品要求,调整出料端的细度调节阀和分选风机的工作状态,控制出料粒度的均匀性和稳定性。
三、设备维护1、磨盘和研磨滚筒的磨损控制:水泥粉磨过程中,磨盘和研磨滚筒的磨损直接影响研磨效果和能耗。
应根据设备的工作状态和磨损情况,定期进行检修和更换,保证设备的正常运行。
2、皮带和链条的张紧控制:水泥粉磨过程中,皮带和链条的张紧状态直接影响设备的传动效率和可靠性。
应定期检查和调整皮带和链条的张紧程度,防止运行中的松动和脱落现象。
3、润滑油和润滑脂的添加控制:水泥粉磨过程中,磨矿系统的润滑状态直接影响设备的摩擦和磨损情况。
应定期检查润滑油和润滑脂的添加量和质量,确保设备的正常润滑。
MLS(MPS)立式磨的控制
摘要:MLS(MPS)立式磨的控制关键在于磨内风量、风速、风温、拉紧力大小、分离器转速·料层厚度、磨机振动、吐渣、压差的控制。
这些万面控制的好坏直接影响到它的粉碎效果和分离效果.MLS(MPS)立式磨是利用料床粉碎原埋进行粉磨物料的一种研磨机械。
现已被广泛应用于水泥、煤炭.电力等行业.我厂MLS(MPS)立磨是一种全风扫式磨机,入磨物料经过挤压,在离心力的作用下甩出盘边沉落到喷口环处,靠该处的高速风将其吹起、吹散,金属,重矿石将沉降到喷口环下排出。
细粉带到立磨上部,经分离器选分,成品随同气体迸人收尘器收集起来,粗粉又循环回来。
粗粉、粗颗粒被抛起,随着风速的降低,使其失去依托,沉降到盘面上,靠离心力迸人压磨轨道进行新一轮的循环,在多次循环中,颗粒与气体之间传热使水分蒸发。
因此,MLS(MPS)立式磨集物料的粉磨、输送、选粉、烘干以及分离金属块和重矿石等诸多优点于一身。
正常条件下,只要通过短期的工艺调试,立磨都能平稳地运转。
但是,如何优化工艺参数保证质量、确保安全、提高产量、降低能耗、提高运转率、不断提高经济效益是立式磨的管理和操作的中心问题。
下面针对这些问题,进行简要的探讨。
1磨内的通风及进出口温度的控制1.1入磨风的来源及匹配人磨热风大多采用回转窑系统的废气,也有的工艺系统采用热风炉提供热风,为了调节风温和节约能源。
在入磨前还可掺入冷风和循环风。
采用热风炉供给热风的工艺系统,为了节约能源,视物料含水清;步己可掺入20%~50%的循环风。
而采用预分解窑废气作热风源的系统,希望废气能全部人磨利用。
若有余量则可通过管道将废气直接排人收尘器。
如果废气金部人磨仍不够,可根据人磨废气的温度博况,确定掺入郡分冷风或循环风.1.2风量、风速及风温的控制1·2·1风量的选定原则(I)出磨气体中的含尘(成品)浓度应在550-750G/M3之间,一般应低于700 G/M3。
(2)出磨管道风速一般要大于18m/s,并避免水平布置。
水泥厂技术降本十个重点
检验喂料
粒径 湿度 温度 易磨性
选粉机效率 – 循环负荷测 试
设定充球量目旳并进行定 时旳检验,使料位与球位处 于同一种水平面
助磨剂优化
降低漏风 ( 加热磨机 )
KPIs 产量tph 磨机驱动功率和kWh/t – 每七天 水泥磨功率指示器
跟踪提升机旳功率-保持循 环负荷
测量并保持磨机旳风量
优化袋收尘 旳打扫功能
Total pressure kPa
Volume m3/s
叶轮设计
17
有效旳气体处理 (2) – 行动
▪ 气体处理系统设计数据旳定位
▪ 风机和系统设计数据 / 图纸 / 性能曲线 / 阀门详细数据
▪ 经过现场测试检验风机性能, 效率和系统
▪ 决定风机效率而且与风机曲线进行对比
• 测量是否是根据曲线进行旳? • 风机旳运营是否在最高效率?
最大程度降低游 离硅旳筛余量 45µm (<2.5%)
27
质量掌控对电能旳影响 (2)
▪ 优化熟料活性旳计划
▪ 最大程度降低生料粉磨电力旳上升 ▪ 确保易烧性处于良好旳范围内 ▪ 最大程度节省水泥粉磨电能 ▪ 经过硫酸盐处理确保碱金属旳饱和度
▪ 在水泥硫酸盐含量最佳情况下进行操作
▪ 使用统计公式对存在旳SO3含量挑战 ▪ 进行工业试验确保最佳情况
▪ 降低停车数量– 停车和开车会大大提升电耗 ▪ 优化设备旳“连续”空转和“预开启”次数
▪ 审查停车程序降低“连续”空转时间 ▪ 审查车间开启设备旳SOP,降低设备预开启次数
尤其注意风机、输送设备和收尘器(但是也检验压缩空气清堵和空气炮旳程序) ▪ 进行修改之前对潜在旳负面影响进行评估,确保没有安全隐患和可靠性风险。 ▪ KPI’s: ▪ 可靠性系数 % 和 MTBF小时 ▪ 正常生产期间旳负荷在车间断电旳时候旳状态% (kW) ▪ 目旳是使年kWh/t接近于正常生产旳 kWh/t
水泥联合粉磨系统的开路与闭路工艺比较
水泥联合粉磨系统的开路与闭路工艺比较摘要:辊压机水泥粉磨系统中,球磨机的运行方式历来有开路和闭路两种工艺。
一般认为,早期的普通球磨机开流系统,由于磨内过粉磨现象严重,物料流速难于控制,在很大程度上起到弱化粉磨效率的作用,故而产能较低,能耗较大;而带有选粉机的闭路磨系统可以及时选出合格成品,对改善磨内工况、遏制过粉磨现象十分有效,因而粉磨效率相对更高。
但随着水泥粉磨技术的持续发展,挤压联合粉磨系统的辊压机,提供给球磨机的入磨粒度通常只有0.2mm~0.5mm甚至更细,这给以小段研磨体和磨内筛分装置为特征的高细磨高产节能创造了有利条件,这种情况下,高细磨开路和闭路工艺的特点变化,很是值得探讨。
关键词:水泥联合粉磨系统的开路与闭路工艺比较引言水泥行业作为我国主要的高能耗、高排放产业一直是工业领域节能减排的重点和难点,物料粉磨则是水泥行业高能耗环节,大力降低水泥粉磨过程中的过高能耗,对推动节能减排工作至关重要。
为了降低生产电耗,虽然我们对开路磨系统进行了多次局部技术改造,但由于受到生产工艺限制,取得的节能降耗效果不太理想。
为了落实《水泥单位产品能源消耗限额》(GB16780—2012)和中国建材《十三五(2016—2020)水泥行业节能减排目标、计划和措施》,实现节能降耗增效最大化,技术人员对现有生产工艺进行了深入分析研究,经查阅相关技术文献获知,采取开路磨联合粉磨工艺虽然可以实现节能降耗,但是,由于受到工艺性能整体约束,节能降耗效果与闭路磨联合粉磨工艺相比还存在很大差距,而采用闭路粉磨系统是水泥粉磨工艺的必然趋势.1基本工艺流程对比2产品性能对比2.1 产品细度及比表面积开路磨系统由于磨内流速较低,磨内不可避免地存在一定程度的过粉磨现象,加之需要严格控制出磨成品中的>80μm粗颗粒,磨内料速不可能太快,因此成品中的微细粉含量较闭路磨多一些,出磨比表面积往往较高;而闭路磨通过选粉机分选成品,磨机负担相对较小,磨内料速容易控制,成品细度略有变化.2.2产品温度两种工艺在稳定运行条件下,通过实测标定表明,闭路磨的成品水泥温度比开路磨约低20℃~30℃,说明闭路磨由于各风路系统的作用,对降低水泥的成品温度起到很大效果,也说明挤压联合粉磨系统采用闭路磨工艺,更能适应当前市场尤其是某些特种水泥的低温生产、低温储存的高标准要求。
- 1、下载文档前请自行甄别文档内容的完整性,平台不提供额外的编辑、内容补充、找答案等附加服务。
- 2、"仅部分预览"的文档,不可在线预览部分如存在完整性等问题,可反馈申请退款(可完整预览的文档不适用该条件!)。
- 3、如文档侵犯您的权益,请联系客服反馈,我们会尽快为您处理(人工客服工作时间:9:00-18:30)。
水泥粉磨优化控制系统一、背景介绍对水泥粉磨系统的研究一直在不断的进行着,如何提高磨机的粉磨效率、提高水泥产品质量、使生产过程节能降耗一直是研究的重点,水泥粉磨过程的耗能巨大,尤其是耗电情况十分严重,由于操作人员对磨机的操作存在滞后性、不确定性、盲目性等缺点,导致粉磨系统的效率较低,进一步增加了粉磨系统的电耗。
粉磨系统操作复杂,磨机的工况也是随着现场的干扰而不断变化的,导致现场经常出现粉磨系统的不稳定情况的发生,比如称重仓仓满溢料、球磨机饱磨、球磨机空磨、皮带秤跳停、旋风筒堵料等,如果操作员不能够及时的发现并采取相应的处理措施,就会导致粉磨系统设备的保护跳停,进而必须将整个粉磨系统停下来进行处理,严重的影响了水泥的生产,对水泥的发货造成影响,从而影响了水泥厂的效益。
所以在粉磨系统运行时一定要避免极端情况的发生,如果因为操作员的操作出现了停产的情况则要对相应的操作员进行处罚,责任到人。
因此,如果能够对粉磨系统采用自动控制代替人工的操作,就能够避免出现极端的情况,并且能够使粉磨系统长时间处于稳定工况,在节约了电耗的同时,能够保护设备并且减少操作人员的劳动强度,具有一定的实用价值。
据统计,我国水泥工业发展较快,水泥产量逐年递增,自1985年起,我国水泥产量连续26年位居世界第一位,2011年总产量达到20.6亿吨,占到世界水泥总产量的50%之多,最近5年内我国水泥年产量及年平均增长率见表1.1,2007年到2011年年平均增长率超过11%,如果通过采用自动控制系统能够将水泥的吨电耗降低1%左右,带来的经济效益是相当可观的。
表1 我国水泥年产量.年份2007 2008 2009 2010 2011年产量/亿吨13.5 14.5 16.4 18.7 20.6年平均增长率/% 7.4 13.1 14.0 10.21、水泥粉磨系统简介在水泥的生产过程中,水泥制备的最后一个环节就是水泥的粉磨,通过水泥的粉磨环节能够将水泥熟料以及外加的原材料粉磨至适宜的粒度,使水泥的细度与比表面积达到国家标准,粉磨出的质量较好的水泥具有较大的水化面积,水化速率快,能够满足水泥浆体凝结与硬化要求。
水泥粉磨系统按照工艺流程主要分为三种:开路粉磨系统、闭路粉磨系统、联合粉磨系统,按照设备使用方式可以分为:辊压机-球磨机粉磨系统、球磨机粉磨系统、立磨-球磨机粉磨系统、卧式辊磨粉磨系统等系统。
目前大多数水泥厂还是采用联合粉磨系统,这种粉磨系统具有产量高,能耗低的优点,但是设备投资大,操作系统复杂。
在粉磨系统中,水泥球磨机是粉磨系统最重要的设备,磨机具有非线性、大滞后、强耦合等特点,所以对球磨机的控制必须要考虑到这些特点,同时磨机是一种能耗大、效率低的设备,最大限度的降低电耗、降低生产成本,是每个水泥厂进行优化改进的目标。
2、水泥粉磨系统自动控制研究现状粉磨技术发展主要历经了设备的大型化阶段和粉磨技术发展两个阶段,并且预分解窑系统不断向大型化方向发展,同时球磨机系统也向大型化方向发展。
粉磨系统采用大型钢球磨机不但提高了粉磨的效率减少了设备的损耗,同时能够简化工艺流程,减少辅助设备,在一定程度上降低了产品成本。
虽然大部分水泥企业都采用较先进的圈流磨系统,但由于开流磨具有自身的优点,仍然有较多水泥厂、粉磨站采用开流磨系统。
在粉磨设备不断向大型化发展的同时,磨机内钢球、磨机衬板以及磨盘的耐磨性也在不断的提升,这就减少了更换钢球以及其他易磨损设备的频率,提高了设备的使用寿命,节省了成本。
对水泥助磨剂的研究与使用也在不断的发展中,助磨剂的添加能够减少物料的结块以及减少物料对磨内钢球的黏糊程度,助磨剂重要的作用越来越受到重视。
如何降低磨机内物料的温度也是重要的研究内容,磨机内物料的温度过高会导致物料的黏结,降低了粉磨效率,并且使部分添加剂脱水,影响水泥的质量,降低温度可以通过向球磨机喷水的方式解决,也可以采用通风系统对磨机内物料进行冷却。
除了上述发展外,水泥粉磨系统大都采用自动化喂料、仪表和计算机集散控制系统(Distribute Control System,简称DCS)控制生产过程,采用DCS进行系统的控制,整个生产过程参数,比如:风机转速、料位、喂料量、提升机电流、风压等参数以及设备运行情况均能在中控室实时的反应,操作员能够在中央控制室通过计算机实现对现场设备进行调节,一定程度上保证了粉磨系统的稳定运行。
对水泥厂粉磨系统进行自动化方向的改造,不断减少操作员的手动操作,提高粉磨系统的自动化程度,提升了企业竞争力的同时能够降低企业的生产成本,具有广阔的应用前景。
二、粉磨系统工艺流程及控制方法1、工艺流程本控制系统研究的对象为山东水泥厂平阴线的粉磨系统,平阴水泥生产线采取的粉磨工艺为带辊压机的圈流式联合粉磨系统,系统采用了ABB公司的Control Builder F 软件进行底层的编程,现场的操作员通过上位机显示的现场设备示意图对各个粉磨系统设备参数进行操作,包括各个设备的启动停止、改变各个风机的转速、改变阀门的开度等。
现场的DCS控制界面如图2所示。
图2 水泥粉磨系统上位机界面从图2可见,整个联合粉磨系统生产线是非常复杂的,使用的设备和需要考虑的变量都是很多的,现场采用的传感器也很多,每一个传感器都能实时的将现场设备的情况反映到上位机的界面上,中控制的粉磨系统的操作员就能实时的了解到各个设备的运转状况,对需要进行调整的设备采取远程的控制。
为了便于分析粉磨系统的工艺流程,将工艺流程图简化如图3所示,图3工艺流程简图水泥生产常用的原材料主要有:熟料、石膏、矿渣、粉煤灰、石灰石等,这些原材料按照一定的配比混合后在入磨提升机的带动下进入到V型选粉机,V型选粉机对物料进行粗选粉,细颗粒的物料被循环风机产生的风力带入到旋风筒中,较粗的物料落入到称重仓中,称重仓也叫缓冲仓,主要用来对物料进行缓冲,使进入辊压机的物料能够平稳没有很大的冲击力,并且使物料在称重仓中能够充分的混合,缓冲之后物料从称重仓出来进入辊压机两辊间进行挤压,经过挤压大颗粒的物料被破碎成细小的颗粒,再次经过入磨提升机的带动进行循环。
旋风筒也起到缓冲的作用,使细颗粒物料能够平稳的进入磨机中粉磨,经过磨机粉磨后物料由磨尾卸下,再通过出磨提升机带动下送至选粉机,合格的水泥直接在入库提升机的带动下进入水泥库保存,不合格的水泥则再次回到磨机内粉磨,形成了一个圈流粉磨系统。
根据以上的工艺分析,可以将粉磨系统分为两个相互联系的回路,第一个回路由喂料、入磨提升机、V型选粉机、称重仓、辊压机和循环风机组成的,主要就是通过辊压机的作用对物料进行一次预粉磨。
第二个回路是由循环风机、旋风筒、尾卸式管球磨机、出磨提升机、选粉机组成的,通过磨机的粉磨,能够得到合格的水泥。
下面根据现场的实际生产情况,说明一下粉磨系统的控制难点。
(1)粉磨系统球磨机的工况经常发生变化,会出现饱磨、空磨等极端的磨况,而理想的状态是磨机处于最佳出力的正常工况,磨机的工作特性曲线如图4所示。
ⅠⅡⅢ图4 磨机的工作特性曲线水泥球磨机运行特性曲线如图4所示,图中包括磨机的功率特性、出力特性、音频特性等。
将图划分为三个区域,当磨机工作在I区域时,磨机粉磨功率会根据磨内物料的增多而增大,效率逐渐增大,但此时磨机内的物料过少,磨机内钢球之间的无效碰撞增加,浪费了能量和电能,磨机内的物料容易产生过粉磨现象,磨机易出现空磨,应该避免这种工况。
磨机工作在II区域时,磨机处于正常工况,磨内负荷较理想,磨机工作在此区域时效率最高,粉磨效果最好,操作员应该将磨机的工况控制在此区域。
磨机处在III区域时,磨机内物料量过多,物料得不到充分的粉磨,导致选粉机的回料量增大,进而导致磨机内的物料继续增多,磨机极易出现饱磨状况,影响了水泥的质量与粒度,操作人员应该避免磨机出现这种工况。
通过对磨机工况的分析可见磨机的工况较多,对磨机进行有效的控制就要考虑到磨机可能处于的各种工况,并且避免极端工况的发生,这是进行自动控制的难点之一。
(2)现场生产的水泥经常需要转产,平阴粉磨线共生产五种型号的水泥:复合32.5水泥(PC32.5)、普通32.5水泥(PO32.5)、普通42.5水泥(PO42.5)、低碱42.5水泥、普通52.5水泥(PO525),其中PO32.5的水泥发货量最大,其次为PC42.5水泥,发货量最少的为PC52.5,所以根据发货量的不同,调度需要根据水泥库中的库存安排中控室操作员进行转产操作,现场经常转产,尤其在是发货旺季,水泥库中水泥库存较少,水泥需要通过转产来调节发货,以达到一定的供需平衡。
转产主要包括:32.5转普通42.5,普通42.5转32.5,普通42.5转低碱42.5。
水泥转产的时候,要调节各种原材料的配比,改变喂料量,调节收尘风机,调节选粉机,这一系列的改动需要在1-2分钟之内完成,短时间内粉磨系统产生了大波动,称重仓仓重开始迅速变化,出磨提升机电流也大幅度波动,所以如何对转产进行有效的控制是实现粉磨系统自动控制的难点之一。
(3)天气以及环境的变化,相对于其他月份,7、8月份处于雨季,雨季空气湿度较大,会对原材料的含水量产生较大影响,导致原材料的易磨性改变,此时工况变化较剧烈,对水泥的质量和产量都有较大影响。
除了空气湿度的影响外,温度的变化也对磨机的控制有着重要的影响,环境温度较高的时候,磨机内物料温度高,物料水分挥发的快,易磨性好,但是如果温度超过95℃以上,会导致部分物料的遇热分解,对水泥成品的质量产生影响,所以磨机内温度不能过高,相反如果环境温度过低,则会导致物料易磨性变差,影响磨机的工况。
这个因素在进行控制器的设计中也要考虑到。
2、控制方法本控制系统以山东水泥厂平阴线的联合粉磨系统为研究对象,经过在水泥生产现场的长时间的实地考察同时与现场的操作人员长期的讨论研究后,总结该条水泥生产线控制的难点与需要解决的问题,得出了整个粉磨系统的建模与控制方案。
由于获得系统相对准确的模型是对系统进行有效控制的关键,所以要采取不同的方法计算系统的模型,比较分析后才能得出最佳的获取模型的方法。
根据从现场获取的大量的设备运行数据,从这些数据中找到最能体现系统运行状况的相关变量,再根据不断的仿真比较,采取加权最小二乘方法获取系统模型,此模型精度较高,可以作为控制用模型。
将获取到的系统较精确的模型用于预测控制,预测控制器采用动态矩阵控制(Dynamic Matrix Control,即DMC)算法,控制器的输入为出磨提升机电流,输出为循环风机的转速,预测控制是一个不断滚动优化的过程,每过一个控制周期都会计算出一个风机的转速,经过现场的不断试验,发现随着时间的延长,粉磨系统的模型精度会降低,这与现场的干扰有关,为了弥补模型的精度避免出现模型失配的情况,采用模型的在线计算与模型在线更新,确保每个控制周期的模型精度。