2013年IE改善案例:精益车间物流改善-彭新华
精益物流管理改善案例

精益物流管理改善案例在精益生产改善中,要实现一个流的改善,除了完成制造流程的改善,还必需完成物流管理的改善,即供应商的物流管理改善。
物流改善是一种高端流程改善,分为内部物流改善和外部物流改善两种。
下面通过某汽车厂供应商的改善案例,来说明“一个流”内部物流改善的基本特点。
这家汽车厂是负责电装零件的硬模制造,其制造方法完全是批量式生产,以500~700个零件为一个批次装入托盘,用叉车搬运。
该厂的经营状况很不好,是赤字经营,因此期望借助体制变革来改善经营的状态。
于是,该厂开头了“一个流”改善活动。
1、改善前改善前的加工工艺和流淌方法,其主要特征是:·布局:是将内容相同的工作集中起来的“工作车间型”布局。
·流淌方法:以500个~700个零件为单位的批量搬运。
·作业者:只能操作单一工序的单能工。
·机械:有与批量大小相匹配的大型机械若干。
我们再看一下这种状况下模具产品A的基本生产规格数据:人员12名,制造周期3天。
这种状况下会产生3天的半成品库存,工件在各工序之间的移动由特地的搬运工用叉车搬运。
在这种制造方式中,问题最大的是大型喷砂机,工厂内全部的零件最终都会集中到这台喷砂机,造成它四周的半成品积累如山。
另外,由于是大批量,同时进行喷砂处理,所以在喷砂时工件简单相互碰撞,从而导致出现许多划伤、打痕的不良品。
而为了区分良品和不良品,在喷砂完成后还需要进行检查,于是又增加了检查工作。
2、改善后以产品A为样板,终止一直以来的“工作车间型”布局,切换成重视产品流程的“流水化”布局;另外,将人工去除毛刺的工序全部终止,改成使用压机及多轴钻床的机械作业。
通过这些方法,将人工作业彻底革除。
改善流程方法的要点如下:·布局:采用重视产品流淌的“流淌化”布局,实行流水线化。
·流淌方法:以500个为单位进行批量制造,从压合到出货全部采用单个流淌。
·作业者:可以操作从压合到出货的全部7个工程,成为多能工。
车间精益改善案例
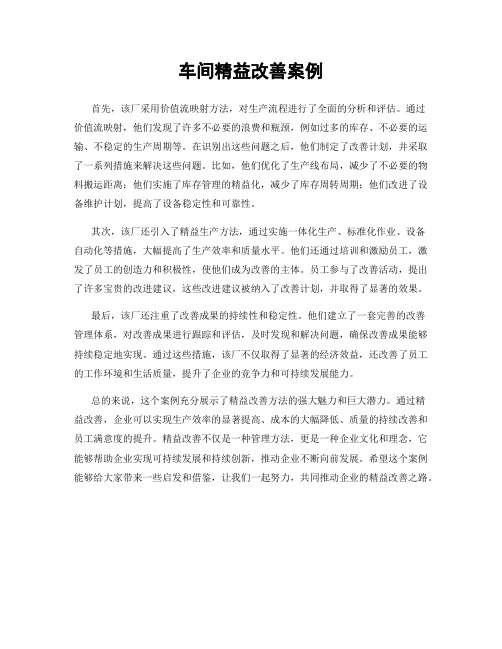
车间精益改善案例
首先,该厂采用价值流映射方法,对生产流程进行了全面的分析和评估。
通过
价值流映射,他们发现了许多不必要的浪费和瓶颈,例如过多的库存、不必要的运输、不稳定的生产周期等。
在识别出这些问题之后,他们制定了改善计划,并采取了一系列措施来解决这些问题。
比如,他们优化了生产线布局,减少了不必要的物料搬运距离;他们实施了库存管理的精益化,减少了库存周转周期;他们改进了设备维护计划,提高了设备稳定性和可靠性。
其次,该厂还引入了精益生产方法,通过实施一体化生产、标准化作业、设备
自动化等措施,大幅提高了生产效率和质量水平。
他们还通过培训和激励员工,激发了员工的创造力和积极性,使他们成为改善的主体。
员工参与了改善活动,提出了许多宝贵的改进建议,这些改进建议被纳入了改善计划,并取得了显著的效果。
最后,该厂还注重了改善成果的持续性和稳定性。
他们建立了一套完善的改善
管理体系,对改善成果进行跟踪和评估,及时发现和解决问题,确保改善成果能够持续稳定地实现。
通过这些措施,该厂不仅取得了显著的经济效益,还改善了员工的工作环境和生活质量,提升了企业的竞争力和可持续发展能力。
总的来说,这个案例充分展示了精益改善方法的强大魅力和巨大潜力。
通过精
益改善,企业可以实现生产效率的显著提高、成本的大幅降低、质量的持续改善和员工满意度的提升。
精益改善不仅是一种管理方法,更是一种企业文化和理念,它能够帮助企业实现可持续发展和持续创新,推动企业不断向前发展。
希望这个案例能够给大家带来一些启发和借鉴,让我们一起努力,共同推动企业的精益改善之路。
IE改善手法

–利用記號以圖表可以讓人更容易理解。
IE精益网 17
5W1H表
項目 對象 作業者 目的
場所、位置 時間、日期 方法
質問5W1H 什麼(What) 誰(Who) 為什麼(Why)
何時(When) 如何(How)
IE精益网
? ? ?
? ?
18
IE精益网
22
簡化
•這裡既包括將復雜的流程加以簡化,也 包括簡化每道工序的內容,例如:
–減少各種繁瑣程序,減少各種復雜性 –使用最簡單的動作來完成工作 –簡化不必要的設計結構,使工藝更合理 –作業方法力求簡化 –運送路線,信息傳遞路線力求縮短
23
IE精益网
板材切斷
工 藝 分 解
搬入構件
放好構件A 放好構件B 進行焊接 取出成品
汽 車 的 車 身
成型 點焊自動焊 焊接 檢查制品 組裝 搬往下工序 涂覆
取構件B 搬到夾具上
搬運 校正位置
安放好
分 析 技 術
工序分析 作業分析 動作分析
IE精益网
12
如何降低生產成本
廠 址 選 擇 分 析
IE精益网 26
身體使用原則
• 雙手同時開始並同時完成其動作 • 除規定的休息時間外,雙手不應同時空閑 • 雙臂的動作應對稱、反向並同時動作 • 手的動作應以最低等級(如手指動)而又能獲得滿意的 結果為好 • 盡量利用物體的慣性、重力等,如需用體力加以阻止 時,應將其減至最小程度 • 變急劇轉換方向為連續曲線運動 • 彈道式的運動路線,比受限制、受控制的運動輕快、 確實; • 建立輕松自然的動作節奏(或節拍),可使動作流利、 自發。 27
精选现场IE改善案例分析

扑克牌游戏规则
1、每个分厂安排4个人(厂长、工艺、作业长、班长) 2、小组内部自己安排4个人的工作 3、要求是将52张扑克牌按同一花色、从大到小的排成一排 4、时间最少的小组获胜 5、开始和结束计时以固定的人员手敲桌子为准 6、游戏开始由工作人员将牌洗好
评分标准
1.2.3.4名分别100.80.60.40分错 一张牌,扣10分
电装7人线标准工时
请 计 算 平 衡 率
6、生产线平衡分析的方法
1、确定对象与范围 2、用作业分析把握现状 3、测定各工程的净时间 4、制作速度图标 5、计算平衡 6、分析结果,制定改善方 案
7、改善瓶颈岗位
(1)改善的4大原则
1)减少动作次数 2)同时使用双手 3)缩短移动距离 4)使动作变得轻松
4、工时测定分析(蓝色为作业的时间红色为失去平
衡的时间)
5、生产线平衡的计算
生产平衡率(%)=各工程净时间总计/(时间最长工程*人 员数)*100%
如上图表中,生产线平衡率=1505/(90*19)*100%=88% 不平衡率%=100%-平衡率(%) 对生产线来说,不平衡率越小越好,一般控制5%-13%之间,
(2)IE动作改善的4原则:
• ECRS原则 1.Eliminate —取消 2、Combine —合并 3、Rearrange —重排 4、Simplify —简化
(3)ECRS法运用图示简介
生产线平衡—例1:缩短生产节拍
提升生产速度,维持人手不变
缩短生产节拍 将工序2里一部 分可抽离的时间 转至3工序里, 以缩短整体的生 产节拍
至少要控制在15%以下
• 请大家观看电子分厂电装3人柔性线视频
1、一边看一边测试,最后计算平衡率 2、计算一下线小时理论产量 3、提出提升线平衡的思路方法
运用IE手法改善电子产品制造车间物流规划

运用IE手法改善电子产品制造车间物流规划作者:张慧梅康雪春来源:《价值工程》2011年第26期To Improve the Logistics Planning of Electronics Manufacturing Plant by IE ApproachZhang Huimei Kang Xuechun(①Mianyang Vocational and Technical College,Mianyang 621000,China;②Sichuan Changhong Electric Co.,Ltd.,Mianyang 621000,China)摘要:针对装配型电子产品制造企业车间物流特点,根据物流路径最短及成本最低原则并运用工业工程的原理,研究和分析了现有的电子产品车间规划,获得了较优车间布置方案,达到成功缩减物流动线以及节约车间空间的目的,提高了生产率。
Abstract: Based on the logistics characteristics of assemble electronic products manufacturing plant, according to the principles of shortest path, lowest cost andindustrial engineering, the paper researched and analyzed the existing electronic products plant planning, received the better plant layout plan, successfully reduced the material flow lines, saved the floor space and improved productivity.关键词:车间物流车间布局改善Key words: workshop logistics;plant layout;improve中图分类号:F251 文献标识码:A文章编号:1006-4311(2011)26-0022-010引言企业物流贯穿企业生产和经营的全过程,物流路线不合理,运行节奏不协调。
物流工艺流程优化与改进

总结词
01
通过引入精益生产理念,优化物料流和信息流,提高生产效率
物料流优化
02
采用拉动式生产方式,根据实际需求安排生产和物料供应,减
少库存积压和浪费。
信息流优化
03
建立生产管理信息系,实时收集和分析生产数据,提高生产
计划的准确性和灵活性。
案例三:某快递公司的分拣中心优化
总结词
通过引入机器人技术和自动化分拣系统,提高分 拣效率
供应链协同的深化
信息共享
加强供应链各环节的信息共享,提高信息传递的准确性和及时性 。
协同计划与预测
通过供应链协同平台,实现各环节的计划和预测协同,提高预测准 确性和资源利用率。
快速响应
提高供应链的快速响应能力,及时应对市场变化和突发事件,降低 运营风险。
定制化服务的兴起
01
个性化需求
随着消费者需求的多样化,物流 服务也需要满足消费者的个性化 需求。
促进经济发展
物流业是国民经济的重要 组成部分,优化物流工艺 流程有助于推动经济发展 。
物流工艺流程的历史与发展
历史回顾
从早期的运输和仓储发展到现代的供 应链管理,物流工艺流程经历了多个 阶段。
发展趋势
随着科技的不断进步和应用,物流工 艺流程正朝着智能化、自动化、绿色 化的方向发展。
Part
02
物流工艺流程优化方法
VS
提升仓储管理
采用先进的仓储管理系统和技术,实现快 速、准确的货物存储和检索,提高仓储效 率。
降低物流成本
优化库存管理
通过合理的库存控制和预测,降低库存成本,减少资金 占用。
降低运输成本
通过合理的运输计划和调度,降低运输成本,提高运输 效益。
精益生产在生产物流优化的应用案例
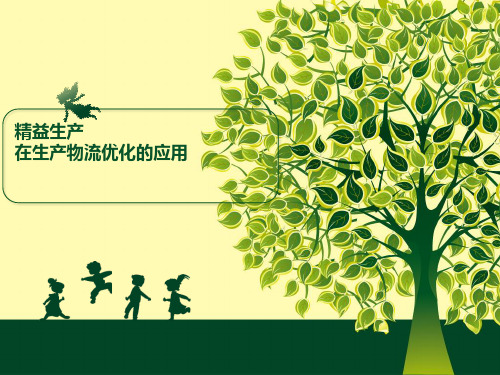
适配卡产品的产线现状分析
3.生产计划分析 目前的生产形式是按订单批量生产,生产计划按周滚 动安排,车间主管每日安排各个生产线的生产计划。
P 公司板卡厂价值流程图现状分析
P 公司
问题改善方向
从以上分析的问题得出,目前板卡企业适配卡的 生产物流以不适合适配卡的这种多品种小批量的生 产模式。
考虑从以下几个方面解决: (1)物料供料流程的整合。 (2)生产线体改造。
(1) 一个看板容器在单元存放和消耗时间 t1 (2) 运输等待时间 t2 (3) 运输到单元时间 t3 (4) 回收空容器时间 t4 (5) 重新填满空容器时间 t5
在本案例中以 AMP-JAN 机种为例:t1=12min,t2=5min, t3=5min,t4=3min,t5=5min,则 T=12+5+5+3+5=30min, 即以每半小时对店面补货送待测机板。 3.看板数量的计算
生产物流的研究方面: 车间布局方面 车间调度方面 仓储优化方面
案例背景介绍
P 公司是一个以生产电子产品为主的高新技术企业,P 公司的板卡厂位于 P 企业的六号厂,主要制造电脑板卡产 品(主板、显卡、其它适配卡)。对于不同型号、不同配 置的电脑所使用的主板、显卡、适配卡不尽相同,根据实 际配置,一个型号的主板可能会搭配不同的适配卡,因此 适配卡种类繁多,月生产 65~75 种。
改进的价值流图
通过对以上生产物流的优化,包括物料流程优化和生产流程 优化,缩短了整个生产周期,由原来的 L/T 9.28D 缩短至 7.59D,提升了产品的整体价值,如图
小结
首先对适配卡生产的物流现状、产品特点、流程特点进 行了较为详细的剖析。发现物料发料过程冗长,料件重复对 点;传统的直线型生产流水线的作业方式无法适应多品种小 批量产品的多样化生产、切换次数频繁、换线时间长、出货 周期长等问题。
生产现场IE改善实例

∮6长4700mm 从表层挖掘影响该车型的质量问题。
方向机、驾驶室后平台支架、七芯线缆原在内饰分装调整到了试制分装
另需加一个三通 底盘管路偶尔有短的
现场问题
空调线与驾驶室线为母母配合,改 空调安装共改两个接头
现场问题
驾驶室方面: 气喇叭管子盘在上面没有顺下来 膨胀水箱软管长(有的长1米多)
深入现场找出长期影响装配作业的实际问题并加以解决,以降低职工劳动强度、减少无效作业。
∮12长1100mm 班组长的权威、团队的协作问题。
25日对生产过程进行了粗放性的测时,当第12台驾驶室装配时生产节拍又恢复到了100余分钟。
∮8长2300mm 方向机、驾驶室后平台支架、七芯线缆原在内饰分装调整到了试制分装
15
落驾驶室
5
装方向机 7
12
安装后踏板 10
加注液压油 起驾驶室
5
连接油门线 5
等待
连接电线
连接变速箱 线
封驾驶室盘
11
20
15
5
连接制动总阀 连接手制动 安装挂车
管路
管路
阀管路
10
20
5
等待
连接方向机 转向油管
固定管路
10
30
10
连接上水 管(跨工
位)
15 装隔热板 (跨工位)
10
装保险杠 灯(跨工
公司要求本批广州订单23日上线、25日下线完成,生 产任务量远超当前实际产能。
以上海参展车辆为标准,全面提升码头车外观质量与装 调质量,进一步提升特种车公司码头车在港口市场的竞争 力与影响力。
改善过程与效果
本批订单自22日开始上线,由于车架总成改进后考虑不周,造成过板接头无法 装配,影响4小时,故22日基本未生产。
- 1、下载文档前请自行甄别文档内容的完整性,平台不提供额外的编辑、内容补充、找答案等附加服务。
- 2、"仅部分预览"的文档,不可在线预览部分如存在完整性等问题,可反馈申请退款(可完整预览的文档不适用该条件!)。
- 3、如文档侵犯您的权益,请联系客服反馈,我们会尽快为您处理(人工客服工作时间:9:00-18:30)。
A工厂订单xxx台(60%为门头,平均每台梯16个)
B工厂订单xxx个/月
80%工厂自制
=
目前的产能无法满足未来订单的需求
标题 日期 地点 作者 10
精益项目-车间物流改善
M1、物料流
M2、物料信息
门头现时成品包装方式
日包装计划
木箱生产转运计划
仓库备料 检查
序号 1 2 3 4 5
工序 开箱 放底层附件 将门头放入包装箱 放上层附件 封箱 total:
A2、物料分析
A3、包装分析
Why?
1 每个零件需求规划 PFEP
2 每工位需求分析 PFES
3 完成物料存放计划
A4、拉动式系统设计
4 每零件运输路径设定
5 完成物料管理程序
=
6 确定所需人力资源
标题 日期 地点 作者 16
精益项目-车间物流改善
A1、产能分析
A2、物料分析
每个零件规划 (PFEP)
标题 日期 地点 作者 2
精益项目-车间物流改善
D1、项目背景陈述
D2、确定范围、目标
D3、团队组建
D4、项目计划
项目背景:随着市场需求,2013-2014年度订单的增加,目前的产能&仓库面积已经难于 满足未来订单需求,必须在有限的空间内优化生产流程、提高产能,保证生产计划按时完 成,从而确保按时发运,因此车间物流的改善迫在眉睫。
差异
21天 21天
26天 26天
通过生产节拍的提升、产线的增加,改善后的 门头产能已满足2014年订单预测的需求
精益项目-车间物流改善
A1、产能分析
M2、物料分析
M3、包装分析
M4、拉动式系统设计
产线增加需重 新调整布局
=
标题 日期 地点 作者 15
精益项目-车间物流改善
A1、产能分析
精益物流系统规划
A3、包装分析
A4、拉动式系统设计
标题 日期 地点 作者 17
精益项目-车间物流改善
A1、产能分析
A2、物料分析
A3、包装分析
A4、拉动式系统设计
物料规划
A类
特性
高库存资金 65-80% 体积大 非通用
库存策略
按需订购 供应商库存管理-VMI 低安全库存
储存方式
B类
中库存资金 10-15% 体积小
标题 日期 地点 作者 9
精益项目-车间物流改善
M1、物料流
门头生产线现时产能
M2、物料信息
M3、产品信息
D4、包装信息
产线
门头 装配线
名称
生产线1 生产线2 产能 2013年平均需求 2013年最高需求 2014年平均需求
生产节拍min 工作时间min 人力/班
班数
total 人力
2014年预测:
=
标题 日期 地点 作者 12
精益项目-车间物流改善
A1、产能分析
生产节拍提高
A2、物料分析
A3、包装分析
A4、拉动式系统设计
工位2上的安全开关组装: 线缆: 开关触点: 开关外壳:
改善方向: 由供应商装配后直接到工位安装 工序重排后生产节拍由6min/件降到5min/件
剥线、接线、外壳 组装的工序时间约 4min
标题 日期 地点 作者 3
精益项目-车间物流改善
D1、项目背景陈述
D2、确定范围、目标
D3、团队组建
D4、项目计划
项目范围: 门头生产线 结合供应链整合项目整合门头物料外部跟内部物料的改善
当前数据:
产线
S8门头 生产线
人力 /Line
产能 /Line
班次
线数
总产能 /day
总面积 /m2
总人数
目前生产工序分析
A2、物料分析
A3、包装分析
A4、拉动式系统设计
工位1: 锁勾安装
导轨安装
工位2: 开关组件安装
接线盒安装
工位3: 门挂板安装
厅门锁安装
工位4: 钢丝绳安装
线上4个工位中,工位2要在线上进 行开关组件的组装,再进行安装。
预装
预装工位: 门锁组件预装 绳架预装触点开关 门挂板预装
单位面积产出
人均产出
单位面积产出=
产能 面积
=
人均产出=
产能 线上总人数
=
标题 日期 地点 作者 4
精益项目-车间物流改善
D1、项目背景陈述
D2、确定范围、目标
项目目标:
D3、团队组建
D4、项目计划
终极目标
目标
现状ቤተ መጻሕፍቲ ባይዱ
=
=
标题 日期 地点 作者 5
精益项目-车间物流改善
D1、项目背景陈述
D2、确定范围、目标
D3、团队组建
小组建立:
项目组长
D4、项目计划
A部门
B部门
C部门
D部门
=
=
标题 日期 地点 作者 6
精益项目-车间物流改善
D1、项目背景陈述
D2、确定范围、目标
D3、团队组建
D4、项目计划
=
=
标题 日期 地点 作者 7
精益项目-车间物流改善
M1、物流信息
M2、物料信息
门头物料车间物流状况
M3、产品信息
=
生产节拍 6min→5min
产能 提高16.7%
标题 日期 地点 作者 13
精益项目-车间物流改善
A1、产能分析
A2、物料分析
增加生产线
提高生产节拍后,产能与需求差异极大, 考虑设计一条生产线
=
标题 日期 地点 作者 14
A3、包装分析
A4、拉动式系统设计
现时产能
目标 差异
改善后产能
(预计) 目标
D4、包装信息
自制物料
360米
外购物料
170米
标题 日期 地点 作者 8
= =
精益项目-车间物流改善
M1、物料流
M2、物料信息
门头物料现时包装方式
M3、产品信息
D4、包装信息
560x450x200塑胶筐
纸箱包装(厅门门锁)卡板来料(如线缆,导轨)
个别包装方式 存在反复拆装 的浪费
=
包装方式多 样,不统一
交流 分享 互助 精益项目-车间物流改善
追求卓越、持续改善!
进步
精益项目-车间物流改善
Lean Project-Shop Floor Logistics
彭新华 2013.12.29
标题 日期 地点 作者 1
精益项目-车间物流改善
D
M
目录
A
Contents
I
C
定义阶段 测量阶段 分析阶段 改进阶段 控制阶段
通用
C类
低库存资金 0-5% 体积极小
通用
标准安全库存 设置订购点 A-B补料拉动
按包装箱设安全库存 定期采购 低采购工作量
标题 日期 地点 作者 18
精益项目-车间物流改善
A1、产能分析
A2、物料分析
时间min 10 5 60 5 10 90
M3、产品信息
M4、包装信息
拼装木箱(10min)
将护脚板+地坎托架放 入底层(拍照)(5min)
钉封条,盖板,包角等 封箱(10min)
放入上层附件 (5min)
=
门头装入 包装箱(10*6min)
标题 日期 地点 作者 11
精益项目-车间物流改善
A1、产能分析