二维优化排样问题研究
二维板材排样问题的递归多块布局算法
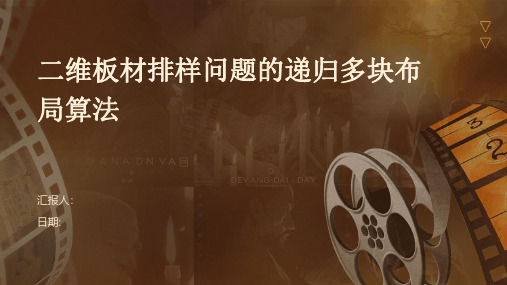
二维板材排样问题的递归多块布局算法汇报人:日期:•引言•二维板材排样问题概述•递归多块布局算法设计•算法实现与实验验证•结论与展望01引言背景意义研究背景与意义国内外研究现状及发展趋势国内研究现状国外学者则注重于采用混合整数规划、粒子群优化等算法,并结合计算机视觉、深度学习等技术进行研究。
国外研究现状发展趋势研究内容本研究旨在研究一种基于递归多块布局算法的二维板材排样方案,解决现有技术的不足之处。
方法采用理论分析、实验验证和模拟仿真相结合的方法,对算法的有效性和优越性进行验证和评估。
研究内容和方法02二维板材排样问题概述二维板材排样问题定义问题的约束条件问题定义问题特点组合爆炸局部最优陷阱问题研究现状经典算法01启发式算法02现代优化技术0303递归多块布局算法设计算法基本思想030201算法实现流程算法复杂度分析时间复杂度由于算法采用分治策略,因此其时间复杂度取决于划分数目和递归深度。
通常来说,算法的时间复杂度较高,为指数级别。
空间复杂度算法的空间复杂度取决于划分数目和每个块的零件数量。
通常来说,算法的空间复杂度也较高,与问题规模成正比。
04算法实现与实验验证算法实现细节初始布局算法流程优化布局布局调整冲突检测在Windows操作系统上,使用Python语言实现算法,并使用标准测试数据集进行验证。
实验结果通过与基准算法进行比较,验证了该算法在求解二维板材排样问题方面的优越性。
实验环境实验验证及结果分析VS结果对比与分析结果对比分析05结论与展望研究成果总结通过实验验证,该算法具有较高的效率和可行性,能够得到最优解或近似最优解。
与现有算法相比,该算法具有更快的运行速度和更好的空间利用率。
提出了一种新的递归算法,能够有效地解决二维板材排样问题。
研究不足与展望该算法在处理大型问题时,可能需要较长的运行时间和较大的计算资源。
在实际应用中,可能需要对算法进行优化和改进,以满足特定的需求和条件。
需要进一步研究该算法在其他领域的应用,例如三维板材排样、电路板布线等。
临界多边形法在二维不规则零件排样中的研究与实现

学号: 99610015硕士学位论文(学位研究生)题目临界多边形法在二维不规则零件排样中的研究与实现作者白瑞斌指导教师魏生民专业技术职务教授学科(专业)航空宇航制造工程(CAD/CAM)答辩日期2002年3月学位授予日期二○○二年•三月目录摘要 (1)Abstract (2)第一章绪论 (3)§1.1 问题描述 (3)§1.2 排样问题在工业中的广泛应用 (3)§1.3 相关研究 (4)§1.4 排样问题的研究现状以及存在的问题 (6)§1.5 本文的研究重点 (7)§1.6 论文梗概 (8)第二章基本概念和相关知识 (9)§2.1 CGAL算法库 (9)§2.2 平面排列(Planar Arrangement) (10)§2.3 CGAL库中的平面图和平面排列 (11)§2.3.1 双向边链表(DCEL) (12)§2.3.2 拓扑层与几何层 (12)§2.3.3 几何特征类(Geometric Traits) (14)§2.3.4 点的定位策略 (15)§2.3.5 迭代器(Iterator) (16)§2.3.6 CGAL中的多边形定义及其操作 (16)第三章临界多边形(NFP)的概念与求解 (19)§3.1 临界多边形(NFP)与Minkowski Sum (19)NFP (19)§3.1.1 临界多边形AB§3.1.2 Minkowski sum的定义以及它与临界多边形的关系 (20)§3.2 利用Minkowski Sum 求解NFP (20)§3.3 多边形分割(凸化)算法 (25)§3.3.1三角形化 (26)§3.3.2无Steiner点的多边形凸化 (26)§3.3.3带有Steiner点的多边形凸化 (27)§3.3.4凸化算法的改进 (30)§3.4 两个凸多边形的NFP求解 (31)§3.5 多边形合并算法 (31)§3.5.1排列合并算法 (32)§3.5.2增量合并算法 (33)§3.5.3 Divide_and_Conquer 算法 (33)第四章临界多边形在排样中的应用及其关键算法 (35)§4.1 NFP方法的零件排样过程 (35)§4.2 曲线的离散化 (36)§4.3 多边形的凸凹性判别 (36)§4.4 多边形合成算法 (37)§4.5 多边形面积 (38)第五章遗传算法及其在排样调度中的应用 (40)§5.1 遗传算法简介 (41)§5.1.1 提出背景 (41)§5.1.2 遗传算法的实施步骤 (42)§5.1.3 遗传算法的特征 (44)§5.1.4 遗传算法的应用领域 (45)§5.2 排样的调度 (45)§5.2.1 算法思想 (46)§5.2.2 调度的实现 (47)第六章开发环境和系统的结构 (56)§6.1 简单绘图系统的实现 (56)§6.2 排样零件信息管理 (57)§6.3 排样结果的人工交互 (58)§6.4 刀位计算和后置处理 (59)第七章总结与展望 (60)致谢 (62)参考文献 (63)摘要二维零件的优化排样技术广泛的应用于制造工业、服装、皮革以及建筑行业中,同时也是一个具有最高计算复杂度的NP完全问题。
带残损原材料二维优化下料问题的研究
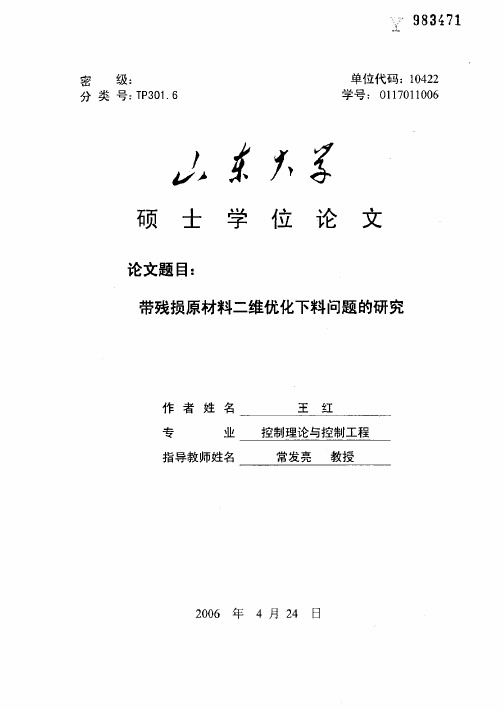
2.期刊论文遗传算法和模拟退火算法求解TSP的性能分析-计算机技术与发展2009,19(11)
旅行商问题(Traveling Salesman Problem,TSP)是一个典型的组合优化问题,并且是一个NP难题,其可能的路径总数与城市数目是呈指数型增长的,所以一般很难精确地求出其最优解,因而寻找出有效的近似求解算法就具有重要的意义.目前求解TSP问题的主要方法有模拟退火算法(Simulated
图4-9算例l第1代布局结果(h=171.43cm)
图4-10算例l第20代布局结果(h=154.31cm)
图4-11算例1第50代布局结果(h=145.2பைடு நூலகம்cm)
算例2:在1000《Im×250吣m的矩形原材料上存在残损,残损标识B=I,如图4-12(a)所示,待下料件的个数n=20,如图4-12(b)所示。取种群规模M=2n---40,双点交叉,交叉概率A=0.7,变异概率P。i=pna=O.05,初始温度T,m=100,降温系数,;o.9.进化100代,得到的最优解为h(X)=143.94,进化300代,得到的最优解为h(X)=113.52.如图4-13、4-14.所示.
(a)原材料(b)下料件
图4-1220个任意下料件实验
山东大学硕士学位论文
图4-13算例2进化100代结果(h=-143.94cm)
基于最低水平线-遗传算法的二维图形排样
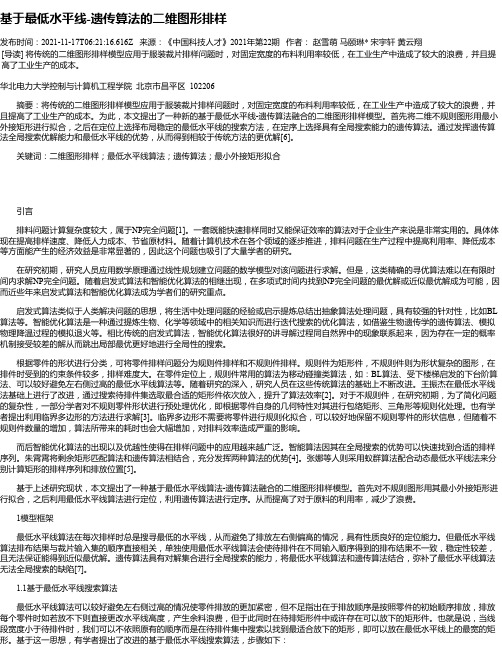
基于最低水平线-遗传算法的二维图形排样发布时间:2021-11-17T06:21:16.616Z 来源:《中国科技人才》2021年第22期作者:赵雪萌马颐琳* 宋宇轩黄云翔[导读] 将传统的二维图形排样模型应用于服装裁片排样问题时,对固定宽度的布料利用率较低,在工业生产中造成了较大的浪费,并且提高了工业生产的成本。
华北电力大学控制与计算机工程学院北京市昌平区 102206摘要:将传统的二维图形排样模型应用于服装裁片排样问题时,对固定宽度的布料利用率较低,在工业生产中造成了较大的浪费,并且提高了工业生产的成本。
为此,本文提出了一种新的基于最低水平线-遗传算法融合的二维图形排样模型。
首先将二维不规则图形用最小外接矩形进行拟合,之后在定位上选择布局稳定的最低水平线的搜索方法,在定序上选择具有全局搜索能力的遗传算法。
通过发挥遗传算法全局搜索优解能力和最低水平线的优势,从而得到相较于传统方法的更优解[6]。
关键词:二维图形排样;最低水平线算法;遗传算法;最小外接矩形拟合引言排料问题计算复杂度较大,属于NP完全问题[1]。
一套既能快速排样同时又能保证效率的算法对于企业生产来说是非常实用的。
具体体现在提高排样速度、降低人力成本、节省原材料。
随着计算机技术在各个领域的逐步推进,排料问题在生产过程中提高利用率、降低成本等方面能产生的经济效益是非常显著的,因此这个问题也吸引了大量学者的研究。
在研究初期,研究人员应用数学原理通过线性规划建立问题的数学模型对该问题进行求解。
但是,这类精确的寻优算法难以在有限时间内求解NP完全问题。
随着启发式算法和智能优化算法的相继出现,在多项式时间内找到NP完全问题的最优解或近似最优解成为可能,因而近些年来启发式算法和智能优化算法成为学者们的研究重点。
启发式算法类似于人类解决问题的思想,将生活中处理问题的经验或启示提炼总结出抽象算法处理问题,具有较强的针对性,比如BL 算法等。
智能优化算法是一种通过提炼生物、化学等领域中的相关知识而进行迭代搜索的优化算法,如借鉴生物遗传学的遗传算法、模拟物理降温过程的模拟退火等。
基于遗传算法对二维下料问题的研究

基于遗传算法对二维下料问题的研究【摘要】本文主要研究基于遗传算法对二维下料问题的优化方法。
在首先介绍了研究背景,指出二维下料问题在生产制造中具有重要意义;其次阐明了相关研究的意义,即通过优化下料过程降低材料浪费。
在首先概述了遗传算法的基本原理和特点;随后描述了二维下料问题的具体情况与挑战;然后详细介绍了基于遗传算法的优化方法,包括编码方案、遗传操作和适应度函数设计等;接着展示了实验结果并进行了分析,验证了该方法的优化效果;最后对比了不同优化方法的效果。
结论部分总结了研究成果,指出了基于遗传算法的优化方法在二维下料问题中的有效性;并展望未来的研究方向,如结合其他智能算法进行优化,提高下料效率和节约材料成本。
【关键词】遗传算法、二维下料问题、优化、实验结果、分析、效果对比、研究成果、展望未来1. 引言1.1 研究背景二维下料问题是指在一个固定大小的矩形面板上,需要摆放不同形状和大小的零部件,使得面板利用率最大化的优化问题。
这是一个在工业生产中常见的实际问题,如板材切割、纺织布料裁剪等。
传统的解决方法往往是基于经验或者启发式算法,存在着计算复杂度高、效率低、解决方案难以达到全局最优等问题。
而遗传算法是一种模拟自然选择和遗传机制的优化方法,具有全局搜索能力、适用于复杂问题等优点。
基于遗传算法对二维下料问题进行研究具有重要意义。
通过模拟自然进化过程中的选择、交叉和变异等操作,可以找到更优的零部件布局方案,将面板利用率最大化。
这不仅可以提高生产效率,减少材料浪费,还可以为工业生产提供更加智能化、高效率的解决方案。
1.2 研究意义二维下料问题是生产中常见的优化问题,通过研究如何高效地利用材料,可以减少成本、提高生产效率。
而基于遗传算法的优化方法可以帮助解决这一问题,其具有全局搜索能力和自适应性,能够找到较优的解决方案。
研究基于遗传算法的二维下料优化方法具有重要的现实意义。
通过优化下料方案,可以有效减少材料的浪费,降低生产成本,提高企业的竞争力。
机械设计中的优化排样问题研究

机械设计中的优化排样问题研究导言机械设计中的优化排样问题是一项重要的研究领域。
在实际的生产制造中,如何最大限度地提高材料利用率、减少生产成本,一直是制造企业所关注的重要问题。
而在机械设计中,对于优化排样问题的研究,可以有效地解决这一问题,并提高生产效率和减少浪费。
一、优化排样的意义优化排样是指在有限的材料或空间条件下,将多个零部件或产品合理地安排在一定区域之中,以达到最佳的材料利用率和生产效率。
这在机械设计中尤为重要,可以有效降低材料浪费,提高生产效率。
通过优化排样,可以节约成本,提升企业竞争力。
二、优化排样的方法1. 启发式算法在机械设计中,优化排样问题是一个复杂的组合优化问题,常常伴随着大规模的数据和复杂的约束条件。
为了解决这些问题,研究者们引入了各种启发式算法。
例如,遗传算法、模拟退火算法和蚁群算法等,这些算法通过模拟自然界中的现象和过程,对优化排样问题进行求解。
这些算法往往能够在较短的时间内找到接近最优解的结果。
2. 元启发式算法与启发式算法相比,元启发式算法可以进行更复杂的求解。
元启发式算法采用了多个启发式算法的组合,并通过协同工作来求解最优解。
这种方法在解决大规模的优化排样问题时,有着较好的效果。
例如,组合遗传算法与模拟退火算法,可以兼顾全局搜索和局部搜索的特性,提高了求解效率。
三、案例分析为了更好地说明优化排样在机械设计中的应用,我将以汽车制造业为例进行案例分析。
某汽车制造企业在进行车身生产时,需要通过冲压工艺将钢板进行成型。
在这个过程中,如何最大限度地减少浪费,提高生产效率,对于企业来说非常关键。
通过优化排样,可以将多个车身零部件合理安排在一块钢板上,使得钢板的利用率达到最高。
这样不仅可以减少材料浪费,还可以利用空间更加紧凑,提高生产效率。
通过引入启发式算法,可以对这个问题进行求解。
算法将对每个车身零部件进行编码,并通过一定的规则进行组装和排样。
通过不停地迭代和优化,最终可以得到近似最优的结果。
二维排样中小生境粒子群算法的研究与应用

二维排样中小生境粒子群算法的研究与应用董辉;黄胜【摘要】提出将基于小生境技术的粒子群算法引入二维不规则零件排样求解问题的方法,通过二维图形坐标离散化的方式,将不规则零件轮廓转化为一系列的坐标区间,在经典粒子群优化算法的基础上加入小生境的思想,运用基于小生境的粒子群算法来搜索排样结果.实验表明:该算法具有良好的搜索性能,它为解决二维不规则零件排样提供了有效的决策方案.【期刊名称】《浙江工业大学学报》【年(卷),期】2014(043)003【总页数】4页(P257-259,268)【关键词】小生境;粒子群;二维不规则;离散化;排样【作者】董辉;黄胜【作者单位】浙江工业大学信息工程学院,浙江杭州310023;浙江工业大学信息工程学院,浙江杭州310023【正文语种】中文【中图分类】TP3-05排样是指将多片不规则形状的零件在某个规定大小的区域中按最佳的方式进行排放的过程,并要求各个零件互不重叠.排样在造船、布匹和皮革加工业中有着广泛应用.排样效率的微小提升可带来巨大的经济效益[1].粒子群算法(PSO,全名Particle swarm optimization)是一个在连续的定义域内搜索函数极值的有效方法[2].PSO算法具有操作简单、收敛速度快的特点,但也容易陷入局部极值,搜索结果不够理想.因此许多学者提出改进型的PSO算法[3-4].小生境技术起源于遗传算法,这种方法能使基于群体的随机优化算法形成物种,从而使相应的优化算法具有发现多个最优解的能力[5].针对排样问题,提出了一种基于小生境的粒子群算法,利用其保持物种进化过程中的多样性的特点弥补了粒子群算法容易陷入局部最优的缺陷,一定程度上改善了搜索效果,在实际排样中提高了材料利用率.1 零件轮廓预处理与排样过程1.1 零件轮廓预处理由于二维不规则零件的轮廓的复杂性,可以通过将零件的不规则轮廓转化为一系列坐标区间从而脱离不规则几何轮廓的复杂性进行排样预处理[6].不规则零件的离散化几何表达即图形的扫描转换方法,其思想是:用等间距的水平扫描线与不规则多边形相交,从而得到由交点坐标组成的多边形几何轮廓上的水平线段区间,因此可以把不规则多边形看作是由一系列的水平线段区间构成[7],如图1所示.此处确定水平线间距为1 mm,即精度为1 mm.图1 几何离散化Fig.1 Geometric discretization预处理基本步骤如下:1) 将轮廓各点按顺序依次排列,形成封闭区间(如图1中顺序:a-b,b-c,c-d,d-e,e-f,f-g,g-h,h-i,i-a).2) 对各区间线段离散化,记录离散化后各点的二维坐标(x,y),轮廓线段交点记两次.3) 遍历轮廓最低点至最高点的所有水平线,从最左端沿水平线向右查找,第2n-1个点为区间线段起点,第2n个点为区间线段终点(n=1,2,3,…),如图1中区间m-n,o-p,q-r.1.2 基本排样过程采用文献[8]提出的BL(Bottom left)算法进行零件的底层排样.BL算法的基本思想:零件先从材料的左下角排入,后面的零件往右依次排入,当零件超出材料的右侧时,将零件相对于材料上移,并从左边开始重新搜索材料的剩余空间,如此循环往复,直至样片全部排入或样片溢出材料顶部时停止,即排样高度记为H.2 基于小生境的粒子群算法在粒子群算法中,所有材料样片的某个状态的集合被视为一个个体(粒子),状态包括三种:排入次序(order,1—n,n为样片总数)、旋转角度(angle,0°~360°)、镜像(mirror,关于y轴对称,0~1).那么某片材料的位置、速度信息可分别表示为x=<orderi,anglei,mirrori>,v=<v_ordi,v_angi,v_miri>.记某个粒子的适应度值F=1/H.2.1 经典PSO算法假定种群粒子个数为R,材料样片数位N,那么粒子数第i个粒子的位置可记为Xi=<xi1,xi2,…,xiN>,速度则记为Vi=<vi1,vi2,…,viN>,粒子的历史最佳位置记为Bi=<bi1,bi2,…,biN>,整个粒子群的历史最佳位置记为Gbest=<g1,g2,…,gN>.对于第i的底n块材料,其速度、位置的更新公式为(1)式中:d为迭代次数;c1,c2分别为学习因子;rand1,rand2分别为0~1之间的随机数;惯性权值w(d)随迭代次数线性递减:w(d)=wmax-wmin·d/D,其中wmax,wmin分别为最大和最小设定值,D为最大迭代次数.2.2 基于小生境的粒子群算法2.2.1 小生境思想的引入在经典PSO的基础上引入小生境的思想,假定初始种群粒子个数R=P·Q,P和Q 均为正整数,将初始种群均分为P个子群(即小生境),通过计算每个粒子的欧式几何距离,将粒子按欧式几何距离从小到大的顺序排列,依次取出粒子,每Q个组成一个子群.因此,相比于经典PSO算法,新算法需增加变量:子群的历史最佳位置,记为GSp=<gsp1,gsp2,…,gspN>(p为子群序号,P>p>0).此变量的作用类似于整个粒子群的历史最佳位置记为Gbest,作为粒子飞行的一个参考因素.若在式(1)中将Gbest项完全由Bsj替代,那么属于不同子群的粒子趋向性会有所不同,从而避免整个种群趋向于同一目标以致种群过早收敛、陷入局部极值的问题;但同时种群的收敛速度将变慢,时间效率大大降低.考虑上述问题,本方法提出的新算法将式(1)改造为(2)(3)式中:p为子群序号;q为子群中某粒子的序号.因此,p·Q+q等效于式(1)中的i,下标pqn等效于式(1)中的in.根据式(3)易得:当d>2D/3或d为偶数时,式(2)等同于式(1);否则式(1)中的种群历史最佳位置项gi(d)变为子群历史最佳位置gspn(d).由上所述可知:新的算法在前2D/3的迭代次数内时,趋向种群历史最佳位置与趋向子群历史最佳位置的操作交叉进行,这使得粒子能够在更大范围内,搜索更优解,且此操作可在一定程度上防止粒子的进化停滞(粒子信息保持不变).同时,由于种群最优解的作用,算法的收敛作用也不至于被减弱许多.在迭代的后期(后D/3),我们认为,算法已接近全局极值点,因此进行全速搜索,即不再考虑子群最优解的影响,在种群最优解的周围进行细致搜索,以期得到更优解.2.2.2 加入小生境的重置机制针对PSO算法容易陷入局部最优解的问题,新算法中加入了子群的淘汰与重置机制,当某个子群在连续n次迭代过程中都未找到更优解时,那么,认为该子群陷入了局部极值解,此时通过对子群的随机重置,可使该子群有机会跳出局部极值解,从而进一步增强了算法的全局搜索能力.2.2.3 算法流程基于小生境的粒子群算法(NPSO)流程如下:1) 随机初始化整个粒子群的初始位置与速度.2) 根据粒子的欧式几何距离将种群分成多个子群.3) 使用公式(2)更新每个粒子的速度与位置.4) 根据粒子位置使用BL算法进行排样,计算适应度值F=1/排样高度.5) 根据F的值更新粒子,子群以及整个种群的当前最优解.6) 判断子群在连续n代内的最优解是否有更新,若有,则跳到步骤8);否则执行步骤7).7) 重置该子群的位置与速度.8) 迭代次数n=n+1,判断n是否为最大迭代次数,如是,则跳出迭代过程,执行结束;否则转到步骤3)继续执行.3 仿真实验与结果分析仿真环境:硬件配置为Core 2双核,主频2.93 GHz,内存为1.96 GB;软件配置为Windows XP系统,VC 2008软件开发平台.本方法以22块不规则服装样片作为测试对象,采用宽1 200 mm,长度没有限制的长方形作为排样底板.为了测试算法的性能,使用新提出的NPSO算法与标准PSO算法[9]分别进行排样,取相同的实验参数,两种算法的最大迭代次数为500次,惯性因子w(d)=0.9-0.5d/500,种群的粒子个数为30,NPSO算法分5个子群,每个子群拥有6个粒子.本实验中样片的旋转角度以90°为基本单位.两种算法的排样过程各重复30次,实验结果如表1所示.表1 实验数据对照表Table 1 The experimental data table算法最差排样高度/mm最佳排样高度/mm平均排样高度H/mmH标准偏差平均运行时间/minPSO1 1771 1421 158.8311.375.2NPSO1 1561 1221 139.0011.295.3从表1可知:两种算法在运行时间和标准偏差上几乎相同;但从排样高度来看,NPSO要大大好于PSO.图2给出了两种算法的最佳排样方案的效果图.对比图2(a,b)可看出:使用新提出的NPSO算法比PSO算法排列的更紧凑,效果更优.图2 两种算法最佳排样效果图Fig.2 The best layout chart by two algorithms4 结束语粒子群算法思路简单,易于实现,通过对两种粒子群算法步骤的介绍和仿真实例的数据结果分析,新提出的基于小生境的粒子群算法的性能明显好于未经过改良的粒子群算法,前者在未改变时间复杂度的前提下,其全局搜索能力比后者有较大提升,弥补了粒子群算法的最大不足.通过上述仿真可知:将基于小生境的粒子群算法应用到解决二维不规则排样的问题中是可行的,而且它在实际应用中,可以有效提高材料利用率.参考文献:[1] 刘虓,叶家玮,胡金鹏.基于最小使能原理的不规则零件排样算法[J].华南理工大学学报,2011,39(8):26-41.[2] 韩毅,蔡建湖,周根贵,等.线型结构批量计划问题的粒子群算法参数方案设定[J].浙江工业大学学报,2010,38(6):683-692.[3] 盛煜翔,潘海天,夏陆岳,等.混合混沌粒子群算法在苯与甲苯闪蒸过程优化中的应用[J].浙江工业大学学报,2010,38(3):318-321.[4] 韩冬梅,王丽萍,吴秋花.基于模糊偏好的多目标粒子群算法在库存控制中的应用[J].浙江工业大学学报,2012,40(3):348-351.[5] 章军.小生境粒子群优化算法及其在分类器集成中的应用研究[D].合肥:中国科学技术大学,2007.[6] 陈勇,唐敏,童若锋,等.基于遗传模拟退火算法的不规则多边形排样[J].计算机辅助设计与图形学学报,2003,15(5):598-609.[7] 黄建江.智能数控裁床的研究与开发——二维不规则零件排样算法的设计与应用[D].无锡:江南大学,2007.[8] STEFAN J. On genetic algorithms for the packing ofpolygons[J].European Journal of Operational Research,1996,88:165-181.[9] SHI Yu-hui, EBERHART R C.A modified particle swarmoptimizer[C]//Proc IEEE World Congress on Computational Intelligence. New York: IEEE Press,1998:69-73.。
不规则货物的摆放算法研究

A
二维 优化 排样 一般 是指 在给 定 的几 何 图形上 不
型货物存放在仓库 中( 仓库高度足够 , 摆放 时货 物 不得叠放 ) 。单 就摆放而言 , 仓库相 当于多边形 板 料 , 物相 当于多边 形 排样件 , 货 如何 摆放 货 物 以提 高 仓库的利用率等 同于寻求平面最优布局 的排样 问 题 。但 是 , 物摆 放 问题 和下 料 问题 还有 许 多 不 同 货
20 SiTc . n n . 0 7 e eh E gg .
不规则货物 的摆放算法研 究
郑 彦 彭 国华 徐 利娜
( 西北工业 大学理 学院应用数学系 , 西安 7 07 ) 10 2
摘
要
货物摆放 问题不 同于传统 的排样 问题 , 不仅要 优化平 面布局 , 必须 兼顾货 物 的运 出。为解决摆 放 问题 , 结合 问 还 先
彦 ,18一 )男 , 士 , ( 93 , 硕 研究方 向 : 计算 机 图
形学 、 图像处理 。E ma : e ga2 @sh .Oa - l z nyn3 o u Cl。 lh l
结合货物 摆放 问题 和下 料 问题各 自的特点 , 通过
’ 通信作者简介 : 国华 , 16 一 ) 男 , 彭 (9 2 , 教授 , 士, 士生导师 , 博 硕
研究方 向: 计算机 图形学 、 计算机辅助几何设计、 逆向工程 。
分析总结, 可得出用下料问题做法求解摆放 问题的不 足之处: 首先, 货物放人仓库时彼此之 间不 留空 隙。
维普资讯
科
学
技
术
与
工
程
7卷
货物摆 放过密必将 导致货 物之 间的碰撞 频繁发 生 , 进 而引发循 环碰 撞使 某 些货 物 无法 运 出仓 库 。 即使货 物能运 出仓库 , 物运 出仓 库 的路 径 往 往是 固定 的 , 货 给实 际操 作带来 不便 。其 次 , 板料可 简单 看作一 个包
- 1、下载文档前请自行甄别文档内容的完整性,平台不提供额外的编辑、内容补充、找答案等附加服务。
- 2、"仅部分预览"的文档,不可在线预览部分如存在完整性等问题,可反馈申请退款(可完整预览的文档不适用该条件!)。
- 3、如文档侵犯您的权益,请联系客服反馈,我们会尽快为您处理(人工客服工作时间:9:00-18:30)。
二维不规则排样问题是众多学者研究的热点!很 多文献也提 出 了 不 同 的 方 法 来 解 决 并 取 得 了 一 些 成 果!但这些都是 准 优 解! 还 没 有 找 到 通 用 的% 标 准 的 解 决方法$ 随着计算机%智能优化技术的发展!对排样问 题的讨论研究也在不断的深入!针对实际应用中的下 料排样问题的不同特殊要求等特点!目前对排样算法 的研究有如下趋势(
.
!! 研究开发 F%#%=*,H =)L ;%?%:(U&%)$
/001 年 第 2 期
计算机系统应用
方向& 不旋转’ 邻接 D绕行一周!并且使得在绕行过程 中保持与 D发生接触!但不重叠!所得到的 1的参考点 的轨迹也是一个多边形!称这个多边形为 1相对于 D 的邻接多边形$ 文献*$%+ 提出的紧凑邻接多边 2’D形 算法主要就是从 ’L3概念演变而来的$ 刘嘉敏*$-+ 采 用单调 线 族 的 思 想 对 ’L3算 法 进 行 了 改 进$ 白 瑞 斌*$&+ 采用基于 1:88ITT的方法通过 多 边 形 的 分 割!解 决了两个凹多边形的临界多边形问题!对于实际应用 中的不规则排样起到了很好的作用$
/001 年 第 2 期
计算机系统应用
二维优化排样问题研究!
G#$#).52+-CF+6"%/#’0%+’)?>)5H%’&D=0%/%I)0%+’>.+B?#/
贾!丹!董方敏!! 三峡大学电气信息学院 湖北宜昌 --%##""
摘!要! 二维优化排样问题的广泛应用引起了国内外学者的关注"主要从各种不同的排样算法如近似算法#启发 式算法#智能优化算法等讨论了国内外排样问题的研究现状"并给出了其发展趋势$
"!影响排样的集合及工艺因素
当研究排样算法的时候!给定一组零件和原材料 板!可能需要考虑排样对象和技术工艺方面的一些因 素!这些因素会影响到问题的复杂性和算法的设计$
在几何特征方面!零件可以是比较规则的形状如 矩形零件!也可以是比较不规则的$ 零件的几何轮 廓可能是由直线构成!也可能有曲线!甚至零件内部 有洞%切除部分等等!而且切除部分也可能是规则的 或者不规则的$ 同样!原材料板块也可以是规则的
该类问题是排样问题中最难处理的!由于零件和 材料均为任意形状!增加了排样的难度!所以该类排样 问题的解决方法是要寻找一个较优的解决方法$ %5"5$ 近似算法和启发算法
&$’ 矩形包络法 此类解法的主要思想是为单个或多个不规则零件 的组合找出其最小包络矩形!然后化为矩形件的排样 问题$ 其求解包络矩形的过程是(首先求出由封闭图 形表示的零件轮廓的包容凸多边形& 即凸壳’!然后以 凸壳的每一边假设与所求矩形中的一边重合!根据顶 点左边位置即可得出此时的包络矩形!其中面积最小 者为最佳包络矩形$ 这种方法的优点是方法简单!易 于实现$ 缺点是对于高度不规则的零件会产生相当多 的浪费$ 李爱平等*$$+ 提出了一种基于包容矩形的优化 排样算法!对毛坯优化排样问题的解决有一定的帮助$ 文献*$"+ 对最小包络矩形的求取方法进行了改进!提高 了排样速度$ &"’ ’L3算法 给定一位置确定的多边形 D!使多边形 1不改变
&$’ 算法的有效结合$ 采用各种智能优化算法来 解决二维不规则排样问题是有效可取的!但不同算法 各有优缺点$ 如何对这些算法进行取长补短%有效结 合!是排样问题研究的一个重要发展趋势$
采用了基于小生境的遗传算法对排样过程进行了优 化$ 文献*$Q+ 设计了一种基于遗传模拟退火技术的启 发式排样算法!给出了一种可以忽略高度不规则形 状带来的复杂性影响的图形的几何表达方式!在很 大程度上提高了不规则形排样算法的效率$ 文献*$P+ 采用的算法和文献*$Q+ 相似!对其算法改进!并在其基 础上提出了一种快速解码的算法!引入了零件之间 的顶点特性和提出办理基线提高策略!实验结果表 明该算法解码速度快!易于实现$
"#世纪 /#年 代 以 后! 遗 传 算 法 & (I8IA7>DTF:h ?7AHW! (D’ $ 模 拟 退 火 算 法 & +7WUTGAI9 D88IGT78F! +D’ !人工神经网络 & D?A7@7>7GT’IU?GT’IA;:?j! D’’’ ! 粒子群& 3G?A7>TI+;G?W RCA7W7oI! 3+R’ 优化算法等一 些智能优化算法日益成熟!许多学者将这些算法应用 到矩形排样问题中!很好的解决了近似算法中存在的 一些缺陷!并能保证较好的优化效果$
&%’ 其它算法 很多文献为解决二维不规则排样问题!提出了不 同的算法!如基于规则推理的方法%图论方法& (?GCH )AHI:?IA7>=IAH:9<’ %平行线分割法%顶点碰撞法等$ NI8?B采 用 模 拟 人 工 排 样 的 方 法 ! 基 于 推 理 技 术 来 选 择和排放下一个零件!每次仅排一个零件!效果不是 很好$ O:;<TG89等采用图论的方法将排样问题化为 在一个已知连接图中发现极大独立集或最大权平面 子图的问题$ 陈勇等*$Q+ 采用一系列等距水平线将板 料平行线化!即利用平行线化后所得的一系列水平 线段来表示板料和零件!忽略了不规则性带来的复 杂性$ 洪灵*$P+ 将 零 件 之 间 的 顶 点 碰 撞 特 性 引 入 1M 算法中!加快了零件在 V方 向 上 的 定 位 坐 标 的 获 得$ 文献*$\+ 采用离散处理使排样优化给出与皮料和样片 的几何信息无关!解决了不规则几何轮廓约束带来 的困扰$ 文献*$/+ 采 用 了 轮 廓 离 散 化! 结 合 最 优 匹 配 算法和碰撞检测算法!对不规则形状板料的排样问 题进行研究$ %5"5" 智能优化算法 NG8和 ’G将 神 经 网 络 和 模 拟 退 火 技 术 应 用 于 不规则形状的排样件在单张矩形板料上的排样!他 们首先利用神经网络技术初始生成一个认为好的布 局!然后用模拟退火技术通过平移%旋转等动作逐步 改善这个布 局$ 文 献*"#+ 分 别 采 用 了 贪 婪 算 法%遗 传 算法%禁忌算法对二维不规则零件进行排样!讨论了 线 性 表 达 法% 边 界 表 达 法 在 描 述 图 形 时 的 优 缺 点$ 李明*"$+ 首先将 不 规 则 零 件 转 化 为 矩 形 件! 提 出 了 一 种基于模拟退火的粒子群算法!采用交叉和柯西变 异运算!提高 了 算 法 的 收 敛 速 度 和 精 度$ 侯 胡 的*""+
+W7AH是将遗传 算 法 运 用 于 排 样 问 题 求 解 的 早 期
研究者之一) E?:FI?将直接二叉树结构用于 (D编码 中!并与 1M相结合)O:;<TG89首次在矩形件排样中运 用 +D)2G8FG8详细阐述了排样问题求解的非线性方 法%遗传算法的不足以及模拟退火算法的优越性!并分 析了应用 +D求解矩形件排样问 题 的 关 键 参 数 选 取$ M:97研究了矩形 排 样 的 禁 忌 搜 索 算 法 运 用! 其 结 构 的 主要特征是 独 立 于 具 体 排 样 问 题 的 搜 索 进 度 表 和 领 域$ YGj:S<*/+ 将遗传算法和启发式算法应用于单张矩 形板料上的多边形排样问题中!其中遗传算法负责给 出一个最佳的排样顺序样!启发式算法负责排样的实 现$ KIWI<H1GSU*"+ 等同样利用遗传算法和启发式算 法给出了 多 张 矩 形 板 料 上 的 矩 形 件 排 样$ (525NG8 提出用人工神经网络和模拟退火分两步优化启发式算 法生成结果布局$ OGFT7采用人工神经网络方法%数学 规划和 (D来求解定宽无限板材的矩形件排样问题$ 宋佩华*$#+ 等将改进的近似排样算法与离散粒子群算 法结合求解矩形件排样问题!通过实验验证了算法的 有效性$ %5" 不规则形状排样
.
F%#%=*,H =)L ;%?%:(U&%)$研究开发 !*
计算机系统应用
/001 年 第 2 期
种近似方法为主*%+ !如基于一维装箱的 LLO算法%1LO 算法!基于最左最下原则的算法& 1:AA:W MI@A!1M’ %双 向背包算法% 相 近 图 形 组 合 算 法% 动 态 规 划 算 法 等$ 1I?jIB和 2:@@WG8*-!&+ 对基于装 箱 的 各 种 算 法 的 性 能 进行了分析!二维排样问题可以归结为以零件排放状 态为结点!以废料增加为权值的带权有向图的最短路 径问题!属 于 集 覆 盖 问 题$ 1GjI?*Q+ 提 出 的 经 典 的 1M 算法!若排样图中任何一个矩形件在不干涉和不超出 板材边界的情况下!均不能向下%向左移动!则满足 1M 条件$ 2HGoITTI提 出 了 该 算 法 的 一 种 改 进 L1M& L787AI 1:AA:W )MI@A’ !在基于最低水平线的空闲区域中搜索 适合的区域$ O3& O7@@I?I8>I3?:>I<<’ 算法的基本想法 是计算可排放点与板材 1M角点的距离!尽量选取距离 小且足够放下的未用面积区域进行排放$ 在综合考虑 1M算法与 O3算法的基础上!贾志欣*P+ 提出了一种基 于零件最高轮廓线的最低水平线法来排放零件$ 赵 晖*\+ 等提出了一种带有启发式策略的动态规划算法! 并设计了和开发了一个基于该算法的矩形件优化排样 系统$
矩形!也可以是高度不规则的特殊形状!甚至带有缺 陷的区域$
除了排样对象的几何特征因素!还有以下几个加 工工艺方面的因素!例如在冲裁加工中!需要有不同的 冲裁间隙& 冗余’ !这个在冲压生产中是留作零件之间 的连接间隙!在非传统的剪裁切割生产中需要留作切 口的间隙和加工损耗$ 排样时!要求工件之间以及工 件与板料周边之间留有搭边!用于排样运算的不是工 件的原始图形!而是 $."搭边值后的图形$ 采用计算 机排样!就需要将加 $."搭边值后的几何图形信息化$ 另外!可能由于 再 加 工 的 需 要! 例 如 弯 曲 等 等! 需 要 考 虑材料自然的弯曲性能$ 排样过程中还有一些其它的 某些约束条件!例如排样图案的方向约束!板材纹理的 方向性约束等等!都会影响到问题的复杂性和排样的 结果$