柱塞套机械加工工艺设计
柱塞工艺设计-ttqq92

一、机械加工工艺规程制订任务书任务要求:考虑毛坯选择、工艺路线、采用的设备、达到精度所采用的工装和定位方法。
1. 上述制定指定零件(或零件组)的机械加工工艺规程,编制机械加工工艺卡片,选择所用机床、夹具、刀具、量具、辅具;2. 对所制定的工艺进行必要的分析论证和计算;3. 确定毛坯制造方法及主要表面的总余量;4. 确定主要工序的加工余量、工序尺寸、公差和技术要求;5. 对主要工序进行工序设计,编制合理的机械加工工艺规程卡,画出的工序简图,选择切削用量;6. 定位基准的选择,设计某一工序的夹具,绘制夹具装配图和主要零件图;7. 编写设计说明书。
二、生产纲领和生产类型(《机械制造技术基础》P253 表5-5)生产类型纲领 单件生产成批生产 大量生产小批中批大批产品类型 重型机械 <5 5~100 100~300 300~1000 >1000 中型机械 <20 20~200 200~500 500~5000 >5000 轻型机械 <100 100~500500~50005000~5000>50000计算公式N=Q*n*(1+α%)*(1+b %),零件在每台产品中的数量n=1(件/台),年产量Q=40000(件/年),废品率α%=2%,备品率β%=2%,所以N=40000×1×(1+2%)×(1+2%)=41616(件),由于精密传动柱塞属于小型零件,根据N=41616可知此柱塞的生产为大批量生产。
1 柱塞105010 φ20φ102圆柱套筒三、主要功用和技术要求主要功用:精密传动柱塞是应用于油泵传动的重要零部件,柱塞和柱塞套的精密程度和质量决定了该油泵的质量,因此,做好精密传动柱塞的质量是柱塞泵的质量的关键环节。
柱塞和柱塞套是一对精密偶件,经配对研磨后不能互换,要求有高的精度和光洁度和好的耐磨性,其径向间隙2~3um。
柱塞头部圆柱面上切有斜槽,并通过径向孔、轴向孔与顶部相通,其目的是改变循环供油量;柱塞套上制有进、回油孔,均与泵上体内低压油腔相通,柱塞套装入泵上体后,应用定位螺钉定位。
柱塞套的成形设计
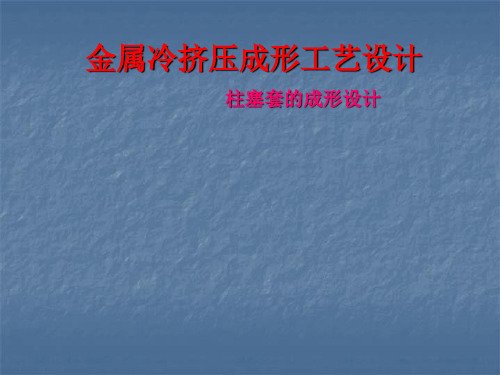
p 0 p 0
19.9
0.07 0 0.08 0
39.9
mm
0.15 0
mm
金属冷挤压成形工艺设计
柱塞套的成形设计
目录
三维模型 二维零件图的设计 工艺方案的选择及制定 尺寸计算 坯料的表面处理以及润滑 成形规律的分析 凸凹模的尺寸计算
挤压件的设计
三维图
挤压件的设计
工艺方案的选择及制定
下图为柱塞套零件图,在制造过程中,毛 坯一部分金属的流动方向与凸模的运动方 向相同,沿轴向运动;另一部分沿径向运 动,可以用镦粗成型。我们初步判断柱塞 套的上半部分采用正挤压,下半部分采取 镦挤压。
p
Dd 2 ( D1 ) 0 Dd 3 ( D1 )
p
19.90 0.07
p 0
39பைடு நூலகம்90 0.08
h1 100 0.15 mm h2 400 0.15 mm h3 50 0.15 mm
锥度为:30
上凹模尺寸为:
Dd 3 ( D1 ) Dd 4 ( D1 ) h3 20 h4 5
2.镦挤部分
A2
F1
A0 A2 314 618.56 100 0 0 97% A0 314
为零件的横断面积,建模后利用计算机可求得:
A2 618.55mm 2
变形力的计算
P cpA 1.3 2300Mpa 618.55mm 1849KN
2
p为平均挤压应力,查表后,取2300Mpa; A为凸模与毛坯直接接触表面在水平面上的 2 投影面积 618.55mm c为安全系数,取1.3
“精密传动柱塞”的加工精度设计

“精密传动柱塞”的加工精度设计一、目的、意义:1、通过对“精密传动柱塞”零部件的加工精度设计,所设计的零部件达到工作时规定的性能要求;2、精密传动柱塞,是通过圆柱套外壁定位并固定于装置,因此对圆柱套外壁有精度要求,以确保柱塞轴的位置和运动正确性;3、学习工艺规程的制定和掌握公差与配合知识的应用以及精度的控制与检验,并且培养学生分析综合能力、实验动手能力、数据处理能力及结合查阅文献进行总结的能力。
二、设计任务:“精密传动柱塞”部件,其结构如下图所示:1、标注配合尺寸公差、重要尺寸公差,包括:(1)根据部件工作性质,确定配合种类;(2)确定基孔制或基轴制;(3)根据要求,确定配合性质、精度要求、基本偏差;(4)求出极限偏差并标注;(5)重要尺寸的尺寸公差,按车床能加工达到的经济精度设计。
2、孔轴形位公差设计标注:(1)提出外圆柱圆的形位公差要求(控制外圆形状精度);(2)提出内圆柱的形位公差要求(确保内外圆柱共轴、内圆柱形状精度);(3)提出表面粗糙度要求(根据零件要求性质);(4)提出各轴颈的形位公差要求。
3、思考对所提出的尺寸精度要求和形位精度要求,如何在加工过程中保证,如何在加工过程中控制或检测。
三、分析、设计:通过参考《机械制造技术基础》、《画法几何与机械制图》、《机械设计》等书籍,配合Auto CAD 计算机绘图软件,完成了本次的机械加工精度设计任务。
在本人所学知识和查阅书籍的基础上认真思考、分析和计算,设计了以下精度的零部件。
下面是精密传动柱塞的主要技术要求和参数。
1、配合尺寸公差、重要尺寸公差:(1)柱塞与圆柱套的配合属于小动力传输的一般传动配合,孔与轴之间有相对运动,故采用属间隙配合。
(2)有两种配合,一是基孔制,另一个是基轴制;而采用基轴制的话,保证孔的精度比较困难,因此采用基孔制。
(3)轴的加工一般采用车床加工,使用精车的话精度可以达到IT7-IT8等级;而孔的加工使用精镗、精磨、铰等方法精度都可以达到IT7-IT9等级;按一般转速,考虑到柱塞需要一定的精度和加工的经济性,同时根据国家标准,尽量使用优先配合,可以选择H8/f7或H8/h7两种;又因为孔和轴之间有相对运动,属于间隙配合,因此选择H8/f7配合。
油泵柱塞套的热处理工艺制定详解

油泵柱塞套的热处理工艺制定详解油泵柱塞套是一种重要的零部件,它通常用于燃油喷射系统中,主要承担着油泵柱塞的工作。
为了保证油泵柱塞套的性能和使用寿命,需要对其进行热处理,以增加材料的硬度和耐磨性。
下面将详细阐述油泵柱塞套的热处理工艺制定过程。
首先需要选择合适的材料。
油泵柱塞套通常采用的是高强度合金钢,如20CrMoTi等。
该材料具有较好的机械性能和热处理可塑性,适合用于制作油泵柱塞套。
在选定材料后,第二步是进行前处理。
首先将材料进行锯割,并采用机械加工方法将其加工成为规定的尺寸和形状。
然后将材料进行去毛刺和酸洗处理,以去除表面的氧化物和杂质,保证后续加工和热处理的质量。
第三步是进行加热处理。
油泵柱塞套通常采用的是淬火+回火的工艺。
首先将材料放入加热炉中,进行均匀加热。
加热温度取决于材料的成分和机械性能要求,一般在800℃-860℃之间。
加热时间应保持足够长,以保证材料达到均匀的加热状态。
第四步是进行淬火处理。
在加热到适当温度后,将材料迅速放入淬火介质中,常用的淬火介质有油、水和盐水等。
淬火的目的是使材料迅速冷却,从而使其组织变为马氏体,增加硬度和耐磨性。
淬火介质的选择取决于材料的成分和机械性能要求,应根据具体情况进行合理选择。
第五步是进行回火处理。
淬火后的材料通常会出现内应力过大和脆性较高的问题,通过回火处理可以减轻内应力,并提高材料的韧性。
回火温度一般在150℃-350℃之间,根据具体要求进行合理选择。
回火时间应保持足够长,以保证材料达到均匀的回火状态。
最后一步是进行加工和表面处理。
经过热处理的油泵柱塞套需要进行加工,以达到精密加工的要求。
可以采用车削、铣削等机械加工方法。
加工后,还需要对表面进行处理,如研磨、抛光等,以保证表面的光洁度和平整度。
综上所述,油泵柱塞套的热处理工艺制定过程分为材料选择、前处理、加热处理、淬火处理、回火处理和加工表面处理等几个步骤。
每个步骤都需要根据材料的性能要求和具体情况进行合理选择,并进行严格的操作和控制,以保证油泵柱塞套的性能和使用寿命。
柱塞套机械加工工艺设计
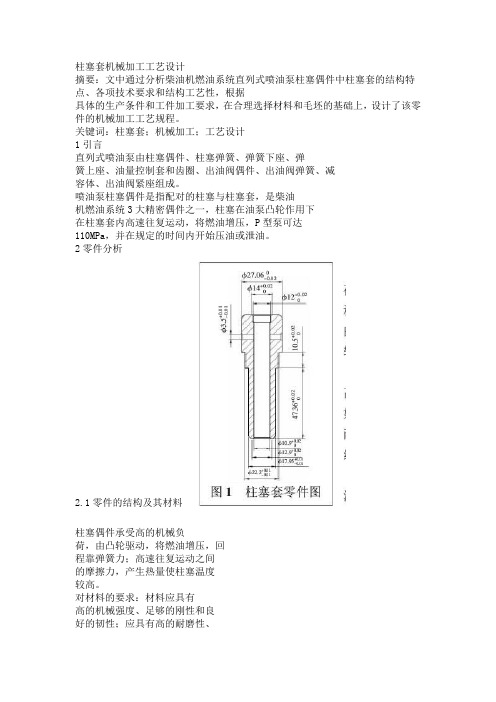
柱塞套机械加工工艺设计摘要:文中通过分析柴油机燃油系统直列式喷油泵柱塞偶件中柱塞套的结构特点、各项技术要求和结构工艺性,根据具体的生产条件和工件加工要求,在合理选择材料和毛坯的基础上,设计了该零件的机械加工工艺规程。
关键词:柱塞套;机械加工;工艺设计1引言直列式喷油泵由柱塞偶件、柱塞弹簧、弹簧下座、弹簧上座、油量控制套和齿圈、出油阀偶件、出油阀弹簧、减容体、出油阀紧座组成。
喷油泵柱塞偶件是指配对的柱塞与柱塞套,是柴油机燃油系统3大精密偶件之一,柱塞在油泵凸轮作用下在柱塞套内高速往复运动,将燃油增压,P型泵可达110MPa,并在规定的时间内开始压油或泄油。
2零件分析2.1零件的结构及其材料柱塞偶件承受高的机械负荷,由凸轮驱动,将燃油增压,回程靠弹簧力;高速往复运动之间的摩擦力,产生热量使柱塞温度较高。
对材料的要求:材料应具有高的机械强度、足够的刚性和良好的韧性;应具有高的耐磨性、耐蚀性和小的热膨胀系数,金相组织稳定及可加工性好。
常用材料:工具钢CrWMn;滚动轴承钢GCr15,硬度要求HRC62~65。
毛坯:棒料或模锻件。
2.2零件的工艺分析柱塞偶件的加工精度要求高,对密封性、滑动性、可靠性及寿命等性能有严格规定,从而使其加工工艺复杂,工艺装备精度要求高,夹具要求精密。
对中、小型喷油泵,柱塞偶件的径向配合间隙要求为1.5~4μm。
这样高的配合精度,很难达到完全互换的要求,因此,在实际生产中,是用放大偶件各自的制造公差,然后根据生产批量的大小,选用单位选配法或分组选配法来保证偶件的装配要求。
柱塞套的技术要求如图1所示,柱塞套内圆表面要求圆度和圆柱度公差小于0.0015mm,直线度小于0.001mm。
柱塞套与泵体配合的外圆表面对内圆表面轴线的径向圆跳动公差为0.03mm。
柱塞套内圆表面粗糙度为Ra0.2~Ra0.4。
3工艺规程设计3.1确定毛坯的制造形式毛坯选择的合理性对零件工艺过程的经济性有着很大影响。
柱塞生产工艺流程

柱塞生产工艺流程柱塞是一种常用的汽车发动机零部件,其生产工艺流程包括原料准备、铸造、机加工、热处理、精加工和检验等环节。
首先,柱塞的原材料准备包括铝合金、铁合金和一些特殊合金材料。
这些原材料需要经过进料检验,检查其化学成分、物理性能和外观质量是否符合要求。
然后,根据柱塞的设计图纸和相关技术要求,利用铸造工艺将铸锭铸成柱塞毛坯。
铸造过程中需要控制合金的熔化温度、浇注温度和浇注速度等参数,确保铸造成型的质量。
接下来,对柱塞毛坯进行机加工。
这一步骤包括车削、铣削、钻削、切割等工艺,将柱塞毛坯加工成精确尺寸和高精度的形状。
机加工过程中需要注意刀具的选择、切削参数的控制,以及灵活运用数控技术。
然后,对机加工后的柱塞进行热处理。
热处理是为了改善柱塞的内部组织结构和性能,通常包括退火、淬火、回火等工艺。
热处理过程中需要控制加热温度、保持时间和冷却速度等参数,以获得理想的热处理效果。
接着,对热处理后的柱塞进行精加工。
精加工包括研磨、抛光、镀膜等工艺,以提高柱塞的表面质量和装配性能。
精加工过程中需要使用一些专业的加工设备和工装,并进行质量检查,确保精加工的效果符合要求。
最后,对成品柱塞进行检验。
检验过程包括外观检查、尺寸测量、力学性能测试和化学成分分析等项目。
通过检验,确保柱塞的质量和可靠性达到设计要求,并对不合格品进行返工或报废处理。
总结起来,柱塞的生产工艺流程包括原料准备、铸造、机加工、热处理、精加工和检验等环节。
每个环节都需要严格控制各项工艺参数,确保柱塞质量稳定可靠。
这一流程的顺利完成,将为汽车发动机的性能和可靠性提供重要保障。
柱塞的工艺
柱塞的工艺
柱塞的工艺主要包括以下几个步骤:
1. 材料准备:选择合适的材料,通常是金属材料,如铝、铜等,根据产品要求制定合适的化学成分和物理性能,然后进行材料切割、磨削等加工步骤,得到合适的柱塞坯料。
2. 粗加工:通过车床、镗床等机械加工设备,对柱塞坯料进行初步的粗加工,如轮廓铣削、挖槽、车削等,以便后续进行细加工。
3. 热处理:将粗加工后的柱塞坯料进行热处理,主要包括退火、淬火等工艺,以改善柱塞的组织结构和性能,提高其硬度和耐磨性。
4. 细加工:对热处理后的柱塞进行进一步的精加工,包括精度加工、外表面抛光、孔加工等,以达到产品要求的尺寸和表面质量。
5. 表面处理:对柱塞的外表面进行处理,如阳极氧化、电镀等,以提高柱塞的抗腐蚀性和装饰性。
6. 检验和装配:对加工后的柱塞进行严格的检验,包括尺寸、表面质量、性能等方面,只合格的柱塞才能进入下一步的装配工序。
7. 包装和出货:将检验合格的柱塞进行包装,通常使用塑料袋、泡沫箱等包装材料,然后进行出货,送往客户或存放于仓库。
这是柱塞的一般工艺流程,具体的工艺可能会因产品类型、材料和生产设备等因素有所不同。
精密传动柱塞加工规程
目录一、柱塞机械加工工艺规程制订任务书二、计算生产纲领,确定生产类型三、零件主要功用与技术要求四、选择毛坯五、工艺分析六、工艺规程设计七、机械加工工艺过程卡八、机械加工工序卡片九、总结十、参考文献柱塞机械加工工艺规程制订任务书计算生产纲领,确定生产类型年产量4000个,备品率8%,机械加工废品率1%,年生产纲领N=Qn(1+a%)(1+b%)=4000×1×(1+8%+1%)=4360(件/年)呈现中批生产特点零件主要功用与技术要求1柱塞与圆柱套的配合属于小动力传输的一般传动配合,例如小电动机、泵一类传动与滑动配合。
2要求有经济性(普通润滑油或者滑脂润滑、温度影响较小)3有一定的精度4所设计的“精密传动柱塞”工作,是通过圆柱套外壁定位并固定于装置,因此对圆柱套外壁有精度要求,以确保柱塞轴的位置和运动正确性。
选择毛坯本零件的主要功用是传递动力,其工作时需承受较大冲击载荷,要求较高的强度和韧性,故毛坯应选择轧件。
工艺分析本零件为回转体零件,其主要加工面在柱塞的两个Φ=10的曲面,两者有较高的同轴度要求,,是加工工艺的重点。
工艺规程设计本零件结构简单,属于轴类零件范畴,可以采用粗车——精车——精磨加工。
加工工艺路线:柱塞:粗车端面-粗车外圆-切断掉头夹紧-粗车端面-粗车外圆-钻两端中心孔-精车一端配合面,及端面-调头,精车另一端配合面-修研中心孔-外圆磨套筒:粗车端面和外圆-精车端面和外圆-切断-粗车和精车端面-钻两端中心孔-扩孔-铰孔-内圆磨机械加工工艺过程卡柱塞机械加工工艺过程百分表000-5 机械加工工序卡片柱塞加工工序卡片机械加工工序卡片产品名称精密传动柱塞零件图号 1 共2页零件名称柱塞第1页材料牌号45钢毛坯种类轧制毛坯外形尺寸Ф25*100每毛坯件数 1每台件数1 备注工序号工序名称工步号工步内容工艺装备主轴转速/(r/min)切削速度/(m/min)进给量/(mm/r)切削深度/mm进给次数工时定额机动辅助夹紧 1三角卡盘夹紧长度30mm1粗车端面1 粗车圆柱端面1200 100 0.42 12粗车外圆1粗车圆柱外圆表面至Ф13,长601200 100 0.4 3 23 车断 1 车断,从未夹紧一450 ————————机械加工工序卡片产品名称精密传动柱塞零件图号 1 共2页零件名称套筒第2页材料牌号45钢毛坯种类轧制毛坯外形尺寸Ф25*100每毛坯件数 1每台件数1 备注工序号工序名称工步号工步内容工艺装备主轴转速/(r/min)切削速度/(m/min)进给量/(mm/r)切削深度/mm进给次数工时定额机动辅助夹紧 1三角卡盘夹紧长度30mm1 粗车端面1 粗车圆柱端面3600 150 0.32 12 粗车外圆1粗车圆柱外圆表面至Ф21长603600 150 0.3 2 13 精车端面1 精车外圆端面4600 150 0.3 0.5 14 精车外圆表面1精车外圆表面至夹紧处Ф10长604600 150 0.3 0.5 1总结这个任务是对于制造工程的知识的一次应用的。
柱塞套加工工艺设计
柱塞套加工工艺设计王德鹏【摘要】本文在加工之前进行柱塞套零件图分析,进而确定所用毛坯材料、尺寸。
然后分析零件的加工工艺流程,编写加工工艺路线进程和工序卡片、工艺过程卡片。
保证重要尺寸的表面质量和精度是柱塞套是否合格的重要问题,本文对加工过程中所选取的设备和工装也叫做简要的说明。
【期刊名称】《黑龙江科技信息》【年(卷),期】2015(000)012【总页数】2页(P90-91)【关键词】柱塞套;加工工艺;精度【作者】王德鹏【作者单位】贵州航天职业技术学院,贵州遵义 563000【正文语种】中文柱塞套的作用:柱塞套的作用:在机械加工的运动部件中,柱塞套能够起到滑动轴承的作用,柱塞套能够承受较小的轴向载荷以及轴套不能承受的载荷。
为了减少磨损,必须选用耐磨性较好,硬度低的材料作为毛坯进行加工,机械零件当中如果零件长期摩擦必然会引起磨损,当磨损到一定程度时,就不能达到配合条件。
如图1所示,对柱塞套的零件图进行结构分析,确定车削加工作为主要方式。
柱塞套的主要技术要求是孔和外圆的尺寸精度;外圆对内孔的平行度;台阶端面对外圆的垂直度,因此内孔需要进行精铰或精镗,外圆需要进行精车或磨削才能达到下述零件图上所要求的主要技术要求。
图1中以ø16的内孔为最高精度要求,且表面粗糙度为Ra0.8同时还要保证它的圆柱度为0.001。
几个端面倒角全部为 C1,零件表面粗糙度普遍较高,ø35.9755的外圆两个端面的平行度为0.03,并且与ø16的内孔垂直度为0.025。
由零件图分析,柱塞套所用材料为15Cr,选择棒料作为毛坯,毛坯余量部分均匀,打刀现象不会出现。
由图1表明该柱塞套的加工范畴属于回转体的轴类零件。
由(l/d=188/160<15)的比值可知零件的长径之比是小于临界值的,因此零件刚性满足要求,不属于细长轴,可以直接加工。
该零件上的外圆和外圆轴线为基准,则的外圆与的外圆有同轴度要求,则键槽与其有对称度要求,则与其端面有垂直度要求,表面粗糙度要求的最小数值为Ra0.4μm。
柱塞杆机械加工工艺
六、柱塞见图2-11。
图2-11 柱塞技术要求1、不同两点间硬度差值不超过三个数值。
4、两端不允许留中心孔。
2、探伤检查不得有裂纹、夹渣等缺陷。
5、热处理58~62HRC 。
3、尖角倒圆R0.5或0.5×45°。
6、材料GCr15。
1、零件图样分析1)柱塞φ2001.002.0--mm 切的圆柱度公差为0.005mm 。
2)端面对轴心线垂直度公差为0.006mm 。
3)柱塞与柱塞套的配合间隙为0.005~0.008mm.4)柱塞探伤检验,不允许有裂纹,夹渣等缺陷。
5)金相组织检查,应由隐晶、细小结晶马氏体和均匀分布的残留碳化物及少量残 留奥氏体组成,1~3级为合格组织。
6)热处理58~62HRC 。
7)材料GCr15。
2、柱塞机械加工工艺过程卡(表2-6)表2-6 柱塞杆机械加工工艺过程卡3、工艺分析1)因为柱塞的受力及耐磨性能较高,所以对材料的金相组织及化学成分都有相应的要求。
含碳(C)量为0.95%~1.05%,含硅(Si)量为0.15%~0.35%,含锰(Mn)量为0.20%~0.40%,含铬(Cr)量为1.3%~1.6%,含硫(S)量≤0.02,含磷(P)≤0.027%(均为质量分数)。
2)对材料进行正火处理,可消除应力,改善材料内部组织,改善加工性能。
3)由于柱塞与柱塞套为精密偶件,其配合间隙要求比较严格,在加工时应采用配作,其顺序应先完成柱塞套的加工(孔加工),再加工柱塞(外径加工)与之相配。
为了保证工件尺寸的稳定性,减小变形,淬火后必要进行冰冷处理,即零件淬火后冷却至室温。
经清洗后,在有液氮和干冰(-60~-80℃)的保温箱内保温1~1.5h,冷处理后,工件在空气中恢复到室温后,立即进行回火,中间停留时间不应超过4h。
4)因零件上不准留有中心孔,所以在下料时,要考虑留有工艺凸台,两端尺寸各加长8~10mm即可。
5)因零件的圆柱度和垂直度要求较高,所以需用高精度的磨床加工。
- 1、下载文档前请自行甄别文档内容的完整性,平台不提供额外的编辑、内容补充、找答案等附加服务。
- 2、"仅部分预览"的文档,不可在线预览部分如存在完整性等问题,可反馈申请退款(可完整预览的文档不适用该条件!)。
- 3、如文档侵犯您的权益,请联系客服反馈,我们会尽快为您处理(人工客服工作时间:9:00-18:30)。
柱塞套机械加工工艺设计
摘要:文中通过分析柴油机燃油系统直列式喷油泵柱塞偶件中柱塞套的结构特点、各项技术要求和结构工艺性,根据
具体的生产条件和工件加工要求,在合理选择材料和毛坯的基础上,设计了该零件的机械加工工艺规程。
关键词:柱塞套;机械加工;工艺设计
1引言
直列式喷油泵由柱塞偶件、柱塞弹簧、弹簧下座、弹
簧上座、油量控制套和齿圈、出油阀偶件、出油阀弹簧、减
容体、出油阀紧座组成。
喷油泵柱塞偶件是指配对的柱塞与柱塞套,是柴油
机燃油系统3大精密偶件之一,柱塞在油泵凸轮作用下
在柱塞套内高速往复运动,将燃油增压,P型泵可达
110MPa,并在规定的时间内开始压油或泄油。
2零件分析
2.1零件的结构及其材料
柱塞偶件承受高的机械负
荷,由凸轮驱动,将燃油增压,回
程靠弹簧力;高速往复运动之间
的摩擦力,产生热量使柱塞温度
较高。
对材料的要求:材料应具有
高的机械强度、足够的刚性和良
好的韧性;应具有高的耐磨性、
耐蚀性和小的热膨胀系数,金相
组织稳定及可加工性好。
常用材料:工具钢CrWMn;
滚动轴承钢GCr15,硬度要求
HRC62~65。
毛坯:棒料或模锻件。
2.2零件的工艺分析
柱塞偶件的加工精度要求高,对密封性、滑动性、可
靠性及寿命等性能有严格规定,从而使其加工工艺复
杂,工艺装备精度要求高,夹具要求精密。
对中、小型喷
油泵,柱塞偶件的径向配合间隙要求为1.5~4μm。
这样
高的配合精度,很难达到完全互换的要求,因此,在实际
生产中,是用放大偶件各自的制造公差,然后根据生产
批量的大小,选用单位选配法或分组选配法来保证偶件
的装配要求。
柱塞套的技术要求如图1所示,柱塞套内圆表面要求
圆度和圆柱度公差小于0.0015mm,直线度小于0.001mm。
柱塞套与泵体配合的外圆表面对内圆表面轴线的径向圆跳动公差为0.03mm。
柱塞套内圆表面粗糙度为Ra0.2~
Ra0.4。
3工艺规程设计
3.1确定毛坯的制造形式
毛坯选择的合理性对零件工艺过程的经济性有着很
大影响。
材料消耗、工序数量、加工工时等都在很大程度
上取决于所选择的毛坯。
同时,毛坯的质量对加工时工件
的定位、夹紧、加工质量也都有很大影响。
根据柱塞套的
工作条件和技术要求,毛坯采用棒料或者模锻件。
3.2制定工艺路线
柱塞套结构形状较为简单,但各表面精度要求较高。
加工分为3个阶段:粗加工、精加工及光整加工,中间有
热处理。
柱塞套加工工艺如下:粗车成型割断→以毛坯外
圆为定位基准车端面、端面外倒角、钻、扩、铰孔并内倒
角→清洗→中孔粗糙度及孔径检验→以中孔为定位基准
精车三级外圆→清洗→小端孔口倒角→清洗→铣定位定
位槽→以中孔为定位基准粗磨中外圆→清洗→以大外圆
及凸肩平面键槽为定位基准钻进油孔→清洗→以大外圆
及凸肩平面键槽为定位基准锪鱼眼→清洗→以大外圆及
凸肩平面键槽为定位基准扩进油孔→清洗。
3.3机械加工余量、工序尺寸、毛坯尺寸的确定
根据原始材料和加工工艺,查表,分别确定加工表面
的加工余量、工序尺寸公差,如表1。
3.4确定切削用量及基本工时
工序13,钻准10.9的孔。
(1)确定进给量f,按表f=(0.01~0.02)d0,考虑钻头直径小、刚性差,进给量宜选小值,取f=0.12mm/r,台式钻床没有自动进给系统,均采用手动进给;
(2)确定切削速度Vc,考虑到孔径小,钻削速度Vc可
选高些,故取Vc=22m/min;
(3)确定台式钻床主轴转速n
n=(1000×22/π×12)=583.9r/min
按表Z4006B台式钻床主轴转速取n=600r/min,实际
钻削速度Vc=22.6m/min
(4)计算基本时间Tm,准12孔深度为l=16mm,切入量
y=[d0cotΦ/2+(1~2)]=6.2~7.2mm
(式中d0为钻头直径,单位为mm,准为半顶角,常用
60°)取y=7mm,切出量△=7mm
Th=(l+y+△)/nf=(16+7+7)(/600×0.12)=0.4min (5)确定辅助时间Ta,查表,取工件装夹时间为0.5min,启动机床0.02min,取下工件0.2min,共计Ta=0.72min。